Dikey Tarım Endüstrisi için Kalın Ölçülü Termoform Çözümleri
Tarımsal yenilik ihtiyaçlarınızı karşılamak üzere özelleştirilmiş dikey tarım yapıları, tepsileri ve bileşenleri için dayanıklı, hafif ve uygun maliyetli çözümler.
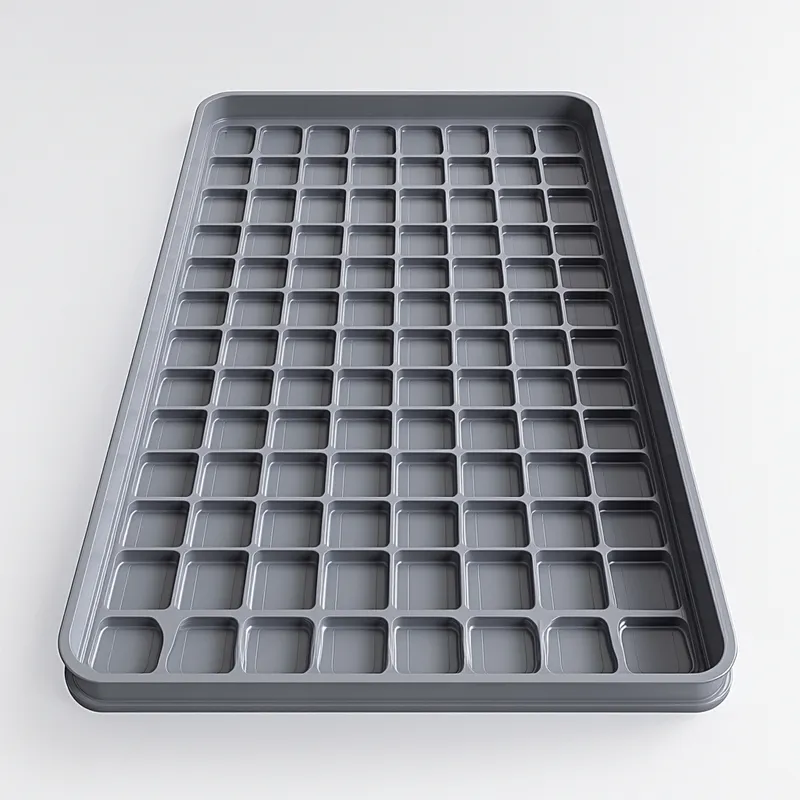
Dikey Tarım için Kalın Ölçülü Termoform Çözümleri
Dikey Tarım Nedir? Dikey Tarım VS. Geleneksel Tarım
Dikey tarım, hidroponik ve yapay ışıklar gibi kontrollü sistemler kullanarak, tipik olarak iç mekanlarda üst üste katmanlar halinde mahsul yetiştirir, yerden ve sudan tasarruf ederek ve hava koşullarından bağımsız olarak yıl boyunca hasat yapılmasını sağlayarak geleneksel tarımdan ayrılır.
Dikey tarım, büyümeyi optimize etmek için kontrollü ortamlar kullanarak mahsulleri üst üste katmanlar halinde, genellikle iç mekanlarda yetiştirmenin modern bir yöntemidir. Mahsulleri geniş yatay tarlalara yayan ve doğal hava koşullarına bağlı olan geleneksel tarımın aksine dikey tarım, yıl boyunca gıda üretmek için hidroponik, aeroponik ve LED aydınlatma gibi teknolojileri kullanır. Bu yaklaşım kentsel alanlarda gelişir, alanın az olduğu yerlerde taze ürün yetiştirmek için binaları veya nakliye konteynerlerini yeniden kullanır. Geleneksel yöntemlere kıyasla su kullanımını 98%'ye kadar azaltır, pestisit ihtiyacını azaltır ve çiftlikleri tüketicilere yaklaştırarak nakliye maliyetlerini düşürür. Geleneksel tarım mevsimler ve toprak kalitesiyle sınırlıyken, dikey tarım tutarlı verim ve ölçeklenebilirlik sunarak sürdürülebilir gıda üretimi için oyunun kurallarını değiştiriyor.
Dikey Tarımda Hangi Ekipman ve Yapılar Kullanılır?
Dikey tarım, mahsul katmanlarını dikey yönde istifleyerek arazi kullanım verimliliğini artıran yenilikçi bir tarımsal üretim modelidir. Bu modelde, kalın duvarlı ısıl şekillendirme süreci, ekipman ve yapısal bileşenlerin üretiminde kilit bir rol oynamaktadır.
1. Dikey Tarımda Yaygın Ekipman ve Yapısal Bileşenler:
① Yetiştirme Rafları veya Raf Üniteleri: Dikey tarım altyapısının bel kemiğini oluşturan yetiştirme rafları, verimi artırmak için mahsulleri birden fazla katman halinde istifleyerek alan kullanımını en üst düzeye çıkarır. Bu rafların bitkilerin, suyun ve ekipmanın ağırlığını taşıyacak kadar sağlam olması gerekir.
② Aydınlatma Sistemleri: Dikey çiftlikler genellikle yeterli doğal ışıktan yoksun olduğundan, yapay aydınlatma çok önemlidir. LED yetiştirme ışıkları, verimlilikleri ve uzun ömürleri nedeniyle yaygın olarak kullanılır ve bitki büyümesi için doğru ışık spektrumunu sağlar.
③ İklim Kontrol Sistemleri: İdeal sıcaklık ve nemin korunması bitki sağlığı için hayati önem taşır. HVAC sistemleri, nem kontrol cihazları ve CO₂ jeneratörleri, istikrarlı bir yetiştirme ortamı sağlamak için birlikte çalışır.
④ Sulama ve Besin Dağıtım Sistemleri: Hidroponik ve aeroponik gibi topraksız yetiştirme sistemlerinde, hassas sulama ve besin dağıtım sistemleri bitkilerin ihtiyaç duydukları su ve besinleri almalarını sağlar.
⑥ Yetiştirme Ortamı: Yetiştirme ortamı bitki kökleri için destek ve besin sağlar. Hidroponik sistemlerde, yaygın ortamlar arasında taş yünü ve genişletilmiş kil peletleri bulunur.
⑦ Fide Tepsileri ve Çoğaltma Ekipmanları: Fide tepsileri, tohum çimlenmesi ve erken evre bitki büyümesi için kullanılır ve sağlıklı gelişimi teşvik etmek için kontrollü bir ortam sağlar.
⑧ İzleme ve Kontrol Sistemleri: Sensörler ve kontrolörler sıcaklık, nem ve besin seviyeleri gibi çevresel parametreleri gerçek zamanlı olarak izler ve optimum büyüme koşullarını sağlamak için sistemleri otomatik olarak ayarlar.
⑨ Pompalar ve Tesisat: Hidroponik ve aeroponik sistemlerde, su ve besin solüsyonlarını sirküle etmek, eşit dağılım sağlamak ve bitki sağlığını geliştirmek için pompalar ve tesisat kullanılır.
⑩ CO₂ Jeneratörleri: Kapalı ortamlarda, CO₂ jeneratörleri fotosentezi artırmak ve bitki büyümesini hızlandırmak için karbondioksit seviyelerini artırır.
⑪ Güvenlik Ekipmanı: Bu, çalışanları kimyasallardan veya potansiyel tehlikelerden korumak için eldivenleri, maskeleri ve diğer koruyucu ekipmanları içerir.
⑫ Temizlik ve Sterilizasyon Araçları: Çevrenin temiz tutulması hastalıkların yayılmasını önler ve mahsullerin sağlıklı olmasını sağlar.
⑬ Hasat Araçları: Mahsulün türüne bağlı olarak, verimliliği artırmak ve bitki hasarını en aza indirmek için özel hasat aletleri kullanılır.
2. Dikey Tarımda Kalın Duvarlı Termoform Uygulamaları:
Kalın duvarlı termoform öncelikle yüksek mukavemet ve dayanıklılık gerektiren bileşenlerin üretiminde kullanılır. Dikey tarımda bu süreç genellikle aşağıdaki bileşenleri üretmek için kullanılır:
① Yetiştirme Tepsileri: Bitki köklerini tutmak için kullanılan bu tepsilerin, su ve besin çözeltilerine sürekli maruz kalmaya dayanacak kadar güçlü ve dayanıklı olması gerekir.
② Hidroponik Sistem Bileşenleri: Su depoları, borular ve konektörler gibi bu parçaların iyi bir korozyon direncine ve yapısal stabiliteye sahip olması gerekir.
③ Fide Tepsileri: Fide yetiştiriciliği için kullanılan bu tepsiler, bitki büyümesini destekleyecek kadar dayanıklı ve temizlenmesi kolay olmalıdır.
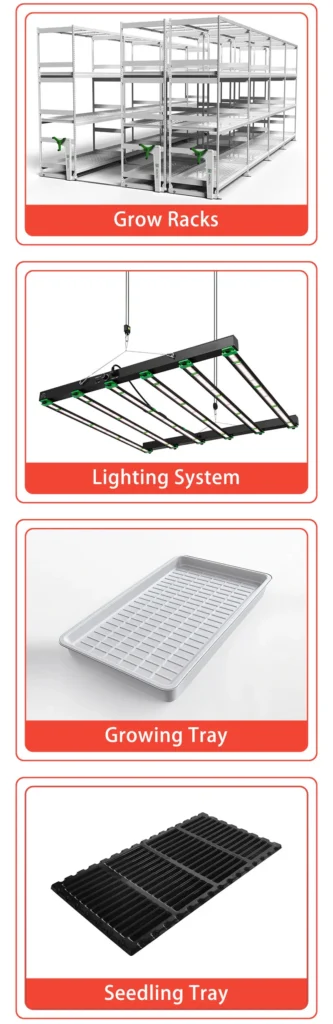
Dikey Tarım Sistemlerinde Yaygın Olarak Hangi Ürünler Yetiştirilir?
Dikey tarım sistemlerinde, yüksek alan kullanımı ve hassas çevre kontrolü sayesinde birçok farklı ürün türü başarıyla yetiştirilebilir. Aşağıda dikey tarımda en yaygın olarak yetiştirilen ürünlerden bazıları yer almaktadır:
1. Yapraklı Yeşillikler:
Marul, ıspanak, lahana ve roka gibi yapraklı yeşillikler dikey tarımda en yaygın ürünler arasındadır. Bu bitkiler hızlı büyür ve istikrarlı pazar talebi ile kontrollü ortamlar için çok uygundur.
2. Otlar:
Fesleğen, nane, kişniş ve maydanoz gibi otlar da dikey tarımda yaygın olarak bulunur. Yüksek pazar talepleri ve hızlı büyümeleri nedeniyle dikey tarım bu bitkiler için ideal bir yetiştirme ortamı sağlar.
3. Mikro yeşillikler:
Mikro fesleğen, turp filizi ve ayçiçeği filizi gibi mikro yeşillikler, kısa bir büyüme döngüsüne sahip besin açısından yoğun ürünlerdir. Üst düzey restoranlarda ve gurme yemeklerinde oldukça değerlidirler. Dikey çiftlikler, pazar talebini karşılamak için gereken yoğun ekim koşullarını sağlar.
4. Meyve Bitkileri:
Bazı dikey çiftlikler çilek, domates ve biber gibi meyve mahsullerini de denemektedir. Bu ürünler tipik olarak belirli büyüme koşulları ve alan desteği gerektirir, ancak dikey tarım, çevresel parametreleri hassas bir şekilde kontrol ederek bunları başarıyla yetiştirebilir.
5. Yenilebilir Çiçekler:
Aynısafa, kadife çiçeği ve hercai menekşe gibi bazı yenilebilir çiçekler de dikey çiftliklerde yetiştirilmektedir. Bu çiçekler genellikle mutfak dekorasyonu için veya bitkisel ürünlerde kullanılır. Dikey tarım, ürün kalitesini sağlayan kontrollü bir ortam sağlar.
6. Bodur Meyve Ağaçları:
Bazı büyük dikey çiftliklerde, bodur elma ve armut ağaçları gibi bodur meyve ağaçları da yetiştirilmektedir. Bu meyve ağaçları, özel sistemlerle dikey alanlarda büyüyebilir ve arazi kullanımını en üst düzeye çıkarabilir.
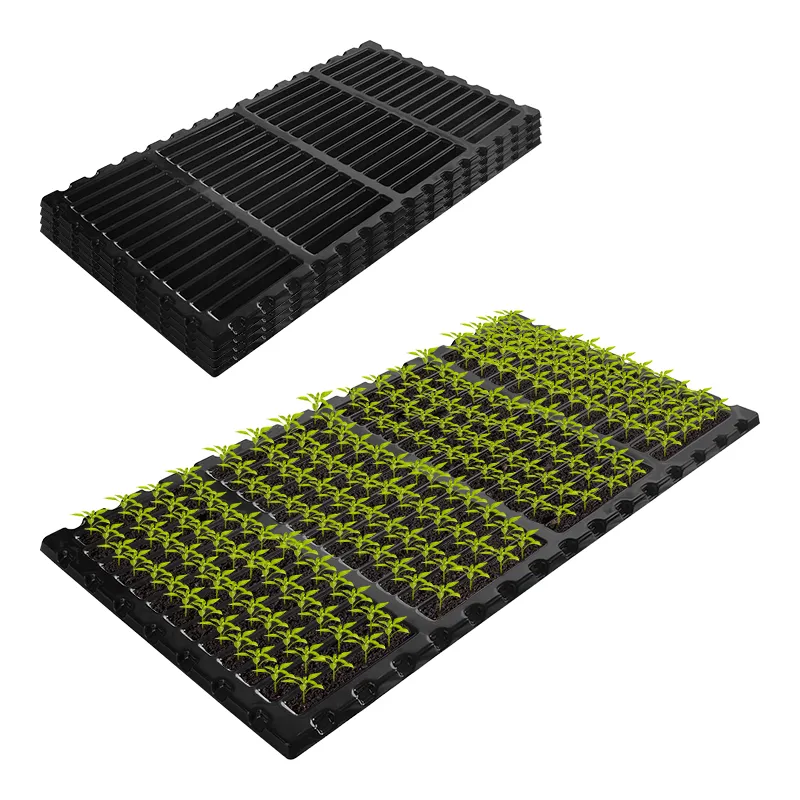
Dikey Tarımda Kalın Ölçülü Termoform Uygulamaları
Kalın ölçülü termoform, kalın plastik levhaların esnek bir duruma kadar ısıtıldığı ve daha sonra vakum veya basınç kullanılarak istenen şekle getirildiği bir üretim sürecidir. Dikey tarım endüstrisinde bu teknik, çeşitli dayanıklı ve işlevsel bileşenler üretmek için yaygın olarak kullanılmaktadır. Aşağıda bazı tipik uygulamalar yer almaktadır:
1. Yetiştirme Tepsileri:
Kalın kalibreli termoform, çeşitli ürünlerin yetiştirilmesi için gerekli olan sağlam, dayanıklı yetiştirme tepsilerinin üretiminde kullanılır. Geleneksel malzemelerle karşılaştırıldığında bu tepsiler hafif ve dayanıklıdır ve tarımsal verimliliği artırmaya yardımcı olur.
2. Fide Modülleri:
Fide modülleri genç bitkileri beslemek için kullanılır. Termoform işlemi, hassas boyutlara ve şekillere sahip modüllerin üretilmesini sağlayarak fidelerin sağlıklı bir şekilde büyümesini sağlar.
3. Hidroponik Konteynerler:
Hidroponik sistemlerde, bitkilerin topraksız bir ortamda sağlıklı bir şekilde büyümesini sağlamak için dayanıklılık ve korozyona karşı direnç gerektiren kaplar oluşturmak için kalın ölçülü termoform kullanılır.
4. Aydınlatma Paneli Kapakları:
Dikey tarım tesisleri genellikle özel aydınlatma koşulları gerektirir. Kalın kalibreli termoform, dayanıklı ve temizlenmesi kolay olmasının yanı sıra eşit ışık dağılımı sağlayan aydınlatma paneli kapakları üretmek için kullanılır.
5. Mühürlü Muhafazalar:
Elektronik cihazları nemden ve kirlenmeden korumak için, sızdırmaz muhafazalar oluşturmak üzere kalın kalibreli termoform kullanılır. Bu muhafazalar hafif ve dayanıklı kalırken gerekli korumayı sağlar.
Kalın Ölçülü Termoformun Avantajları:
① Yüksek Dayanıklılık: Kalın kalibreli termoform parçalar olağanüstü mukavemet ve darbe direncine sahiptir, bu da onları tarımda dayanıklılık gerektiren uygulamalar için uygun hale getirir.
② Tasarım Esnekliği: Süreç, belirli işlevsel ve estetik gereksinimleri karşılamak için karmaşık ve özelleştirilmiş şekillerin üretilmesine olanak tanır.
③ Maliyet Etkinliği: Diğer üretim yöntemleriyle karşılaştırıldığında, kalın ölçülü termoform tipik olarak daha düşük kalıp maliyetlerine ve daha kısa üretim döngülerine sahiptir, bu da onu büyük ölçekli üretim için uygun hale getirir.
Kalın Ölçülü Termoform Parçalar İçin Hangi Malzemeler Kullanılır?
Dikey tarım endüstrisinde, özellikle dayanıklı ve işlevsel plastik parçaların üretiminde kalın ölçülü termoform uygulaması yaygındır. Bu süreç, yüksek mukavemet, dayanıklılık ve tarımsal ortamın zorlu koşullarına dayanma yeteneği gerektiren parçalar için idealdir. Bu işlem için hangi malzemelerin yaygın olarak kullanıldığını daha iyi anlamak için, dikey tarım uygulamalarında son derece iyi performans gösteren malzemelere ilişkin ayrıntılı bir genel bakışı burada bulabilirsiniz.
1. ABS (Akrilonitril Bütadien Stiren):
ABS, yüksek mukavemet ve dayanıklılık gerektiren plastik parçaların üretiminde yaygın olarak kullanılan bir termoplastiktir. Mükemmel mekanik özellikleri ve darbe direnci, özellikle parçaların yapısal bütünlüğünü korumasını gerektiren uygulamalar için ideal bir seçimdir.
Avantajlar:
① Yüksek mukavemet ve iyi tokluk, dış kuvvetlere ve darbelere karşı dayanıklı.
② İşlenmesi ve şekillendirilmesi kolaydır, karmaşık şekilli parçalar için uygundur.
③ İyi kimyasal direnç, yaygın tarım kimyasallarına dayanabilir.
④ Hava koşullarına karşı mükemmel direnç, dış ortamlar için uygundur.
Uygulamalar:
① Seralarda sulama ekipmanı muhafazaları.
② Dikey tarım kurulumlarında konteynerler ve depolama sistemleri.
2. HIPS (Yüksek Etkili Polistiren):
HIPS, öncelikle iyi görünüm ve işlenebilirlik gerektiren parçalar için kullanılan yüksek etkili bir polistiren malzemedir. Pürüzsüz bir yüzeye sahiptir, renklendirilmesi ve basılması kolaydır ve mükemmel işleme performansı sunar.
Avantajlar:
① Estetik gereksinimleri karşılayan iyi yüzey kalitesi.
② Mükemmel işlenebilirlik, seri üretim için ideal.
③ İyi darbe direnci, hafif ve orta hizmet uygulamaları için uygundur.
Uygulamalar:
① Dikey tarımda dekoratif veya koruyucu muhafazalar.
② Dikim sistemlerinde yapısal destek ve bölme parçaları.
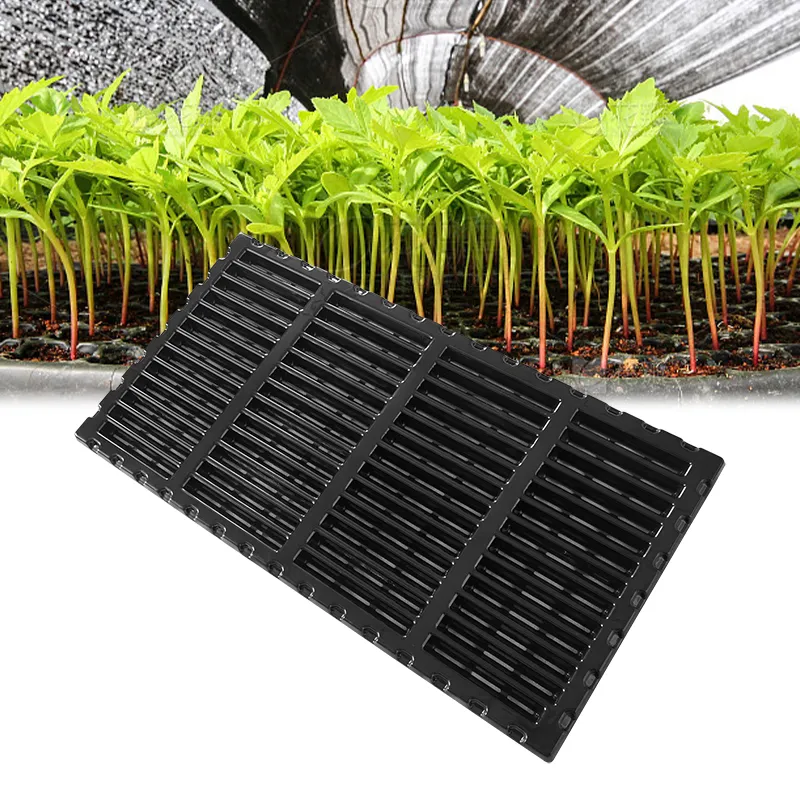
3. HDPE (Yüksek Yoğunluklu Polietilen):
HDPE, mükemmel kimyasal dirence ve darbe direncine sahip yüksek yoğunluklu bir polietilendir, bu da onu zorlu ortamlara maruz kalan parçalar için ideal hale getirir. Suya ve kimyasallara karşı güçlü bir dirence sahiptir, bu da onu neme veya kimyasallara maruz kalan tarımsal ortamlarda kullanım için son derece uygun hale getirir.
Avantajlar:
① Güçlü kimyasal direnç, çeşitli tarım kimyasallarına dayanabilir.
② Yüksek stres koşulları altında bütünlüğü koruyan mükemmel darbe direnci.
③ İyi hava direnci, dış mekan ve açık ortamlar için uygundur.
④ Yüksek geri dönüştürülebilirlik özelliği sayesinde çevre dostu bir seçenektir.
Uygulamalar:
① Hidroponik sistemlerdeki borular ve su tankları.
② Dikey tarımda su rezervuarları ve sulama sistemleri.
4. PVC (Polivinil Klorür):
PVC, iyi kimyasal direnci ve sertliği ile bilinen bir malzemedir. Özellikle suya ve diğer aşındırıcı maddelere maruz kalan parçalar olmak üzere, korozyon direnci ve sertlik gerektiren ürünler için yaygın olarak kullanılır.
Avantajlar:
① Mükemmel korozyon direnci, ıslak tarım ortamlarında kullanım için idealdir.
② Yüksek rijitlik ve sertlik, önemli basınca dayanabilir.
③ Kolay işlenebilir, karmaşık şekillerin oluşturulmasına olanak sağlar.
Uygulamalar:
① Boru sistemleri.
② Seralarda destek ve yapısal bileşenler.
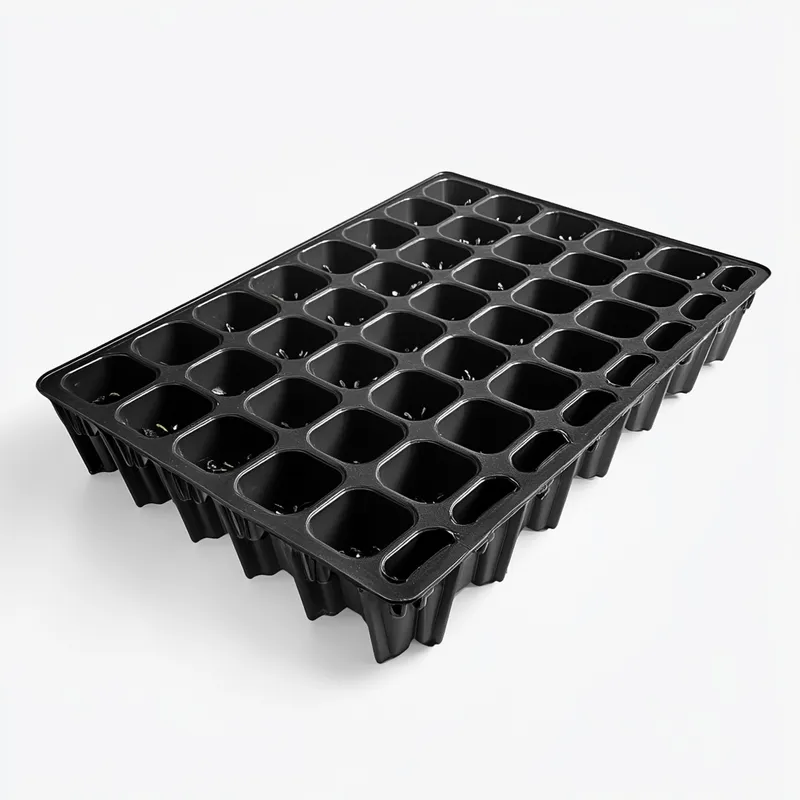
5. Polikarbonat (PC):
Polikarbonat, olağanüstü darbe direncine ve şeffaflığa sahip bir malzemedir. İyi bir optik netlik sunar, bu da onu şeffaf veya yarı şeffaf parçalar gerektiren uygulamalar için oldukça değerli kılar. Ayrıca, zorlu koşullarda bile uzun süreli dayanıklılık sağlayan mükemmel darbe direncine sahiptir.
Avantajlar:
① Yüksek şeffaflık, ışık geçirgenliği veya görsel inceleme gerektiren uygulamalar için idealdir.
② Yüksek darbe kuvvetlerine dayanabilen olağanüstü darbe direnci.
③ Çeşitli hava koşullarında stabilite sağlayan mükemmel hava direnci.
Uygulamalar:
① Dikey tarımda aydınlatma sistemleri için koruyucu kapaklar.
② Seralar için ışık geçirgenliğine izin veren çatı ve duvar malzemeleri.
6. PP (Polipropilen):
Polipropilen, mükemmel kimyasal dirence sahip hafif, dayanıklı bir termoplastiktir, bu da onu özellikle aşındırıcı maddeler içeren tarımsal ortamlar için ideal hale getirir. Ayrıca yüksek ısı direnci ve iyi yaşlanma direnci sunar.
Avantajlar:
① Çeşitli tarım kimyasallarına dayanabilen mükemmel kimyasal direnç.
② Üstün ısı direnci, yüksek sıcaklıklı ortamlarda kullanım için uygundur.
③ İyi yaşlanma direnci, uzun süreli kullanım için uygundur.
Uygulamalar:
① Tarımsal konteynerler ve depolama tankları.
② Tarım ekipmanları için taşıma sistemleri.
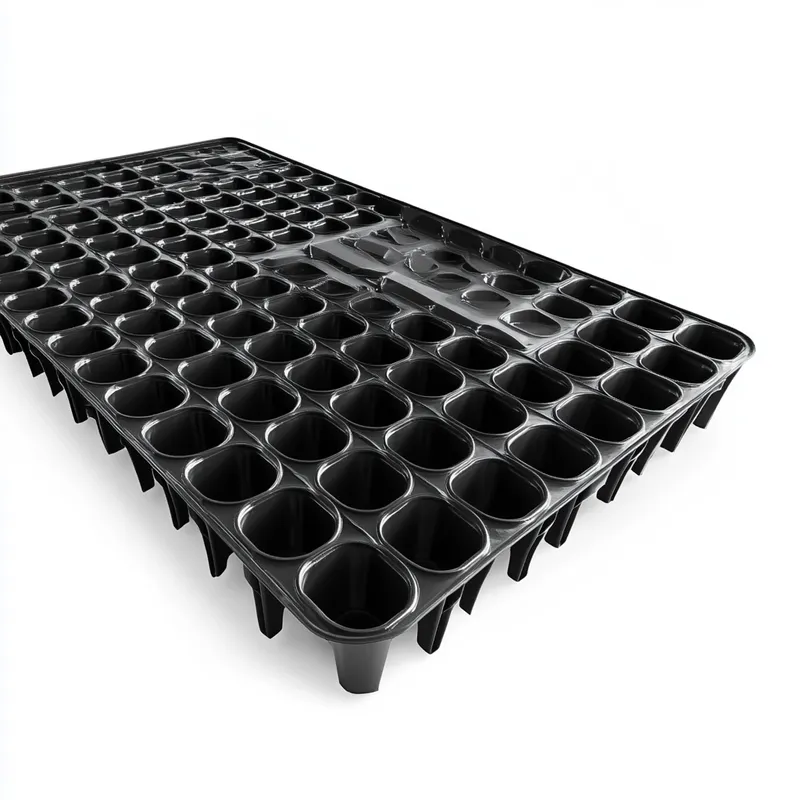
Doğru Malzeme Nasıl Seçilir?
Dikey tarımda kalın ölçülü termoform için malzeme seçerken şirketler birkaç kritik faktörü göz önünde bulundurmalıdır:
① Mukavemet ve Sertlik: Ağırlık veya yüksek basınç taşıması gereken parçalar için, daha yüksek mukavemetli bir malzeme seçmek çok önemlidir.
② Kimyasal Direnç: Tarımsal ortamlarda sıklıkla kimyasallar kullanıldığından, mükemmel kimyasal dirence sahip malzemelerin seçilmesi uzun ömür ve dayanıklılık sağlar.
③ Çevresel Uyumluluk: Farklı iklimlerde stabilite sağlamak için malzemenin hava koşullarına dayanıklılığını ve yüksek sıcaklık performansını göz önünde bulundurun.
④ Maliyet Etkinliği: Genel üretim maliyetlerini düşürmeye yardımcı olmak için teknik gereklilikleri karşılarken paranızın karşılığını veren malzemeleri tercih edin.
Neden Diğer Yöntemler Yerine Kalın Ölçülü Termoformu Seçmelisiniz?
Kalın ölçülü termoform, dayanıklı ve işlevsel tarım ekipmanları ve bileşenleri üretmek için dikey tarımda yaygın olarak kullanılmaktadır. Diğer üretim yöntemleriyle karşılaştırıldığında, kalın ölçülü termoform dikey tarımda kullanım için birkaç önemli avantaj sunar:
1. Üstün Dayanıklılık:
Kalın kalibreli termoform, yüksek mukavemet ve darbe direncine sahip parçalar üretir. Bu parçalar ağır yüklere ve zorlu ortamlara dayanabilir, bu da onları ekim tepsileri, konteynerler ve koruyucu kapaklar gibi tarım ekipmanları için ideal hale getirir.
2. Tasarım Esnekliği:
Bu süreç, ince ayrıntılara ve özelleştirme seçeneklerine sahip büyük ve karmaşık şekilli parçaların üretilmesine olanak tanır. Bu tasarım esnekliği, hassas boyutlara ve şekillere sahip ekim kapları gibi belirli tarımsal ihtiyaçları karşılayan parçaların üretilmesini mümkün kılar.
3. Maliyet-Etkinlik:
Enjeksiyon kalıplama gibi diğer üretim yöntemleriyle karşılaştırıldığında, kalın ölçülü termoform kalıp maliyetleri ve üretim döngüleri açısından belirgin avantajlar sunar. Daha düşük kalıp maliyetleri ve daha hızlı üretim zaman çizelgeleri, yüksek kaliteli tarımsal bileşenlerin üretilmesi için ekonomik olarak uygun bir seçimdir.
4. Malzeme Çok Yönlülüğü:
Kalın ölçülü termoform ABS, polikarbonat ve polietilen dahil olmak üzere çeşitli malzemelerle kullanılabilir. Bu malzeme çeşitliliği, üreticilerin kimyasal direnç, UV stabilitesi veya ısı yalıtımı gibi istenen performans özelliklerine göre en uygun malzemeyi seçmesine olanak tanır.
5. Estetik ve İşlevsellik:
Bu işlem, parçaların görünümünü ve işlevselliğini geliştirmek için özel yüzey kaplamaları, dokular ve renkler elde edebilir. Örneğin, ekim tepsileri için kaymaz yüzeyler oluşturulabilir veya bileşenler kolay tanımlama ve sıralama için renk kodlu olabilir.

Dikey Tarım için Özel Kalın Ölçülü Termoform Çözümleri
Dikey tarım endüstrisi için özel olarak tasarlanmış dayanıklı ve özel kalın ölçülü termoform çözümlerini keşfedin.
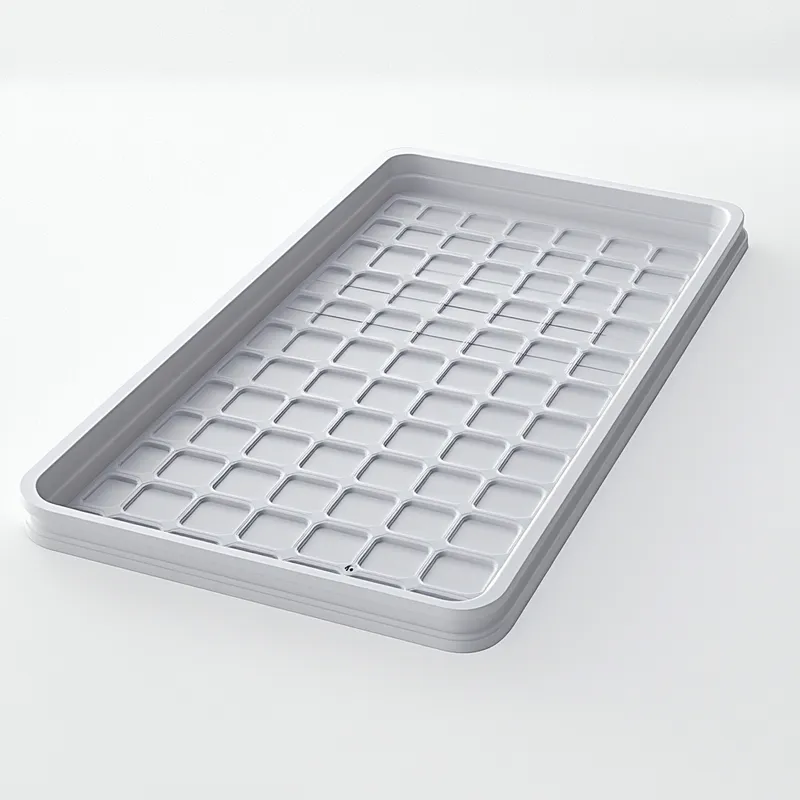
Dikey Tarım Endüstrisi için Kalın Ölçülü Termoform Çözümleri
- Termoform Parçalar UV, Nem ve Küfe Dayanıklı Olabilir mi?
- Kalın Ölçülü Termoformun Boyut Sınırlamaları Nelerdir?
- Dikey Tarım Uygulamaları için Sürdürülebilir Malzemeler
- Termoform Parçaların Uzun Süreli Dayanıklılığı Nasıl Sağlanır?
- Parça Tasarımı Dikey Tarımı Nasıl Etkiliyor?
- Yüksek Sıcaklık ve Yüksek Nemde Isıl Şekillendirilmiş Parçalar
Termoform Parçalar UV, Nem ve Küfe Dayanıklı Olabilir mi?
Dikey tarım endüstrisinde kalın ölçülü termoform uygulaması, ürünlerin sadece yapısal ve işlevsel yönlerine değil, aynı zamanda UV direnci, nem direnci ve küf direncinin artırılmasına da dikkat edilmesini gerektirir. Üreticiler, doğru malzemeleri seçerek ve gerekli kimyasal katkıları veya kaplamaları ekleyerek ürünlerinin zorlu çevre koşullarındaki performansını ve uzun ömürlülüğünü önemli ölçüde artırabilir. Bu iyileştirmeler, ürünlerin uzun kullanım süreleri boyunca istikrarlı ve güvenilir kalmasını sağlar.
1. UV Direnci:
UV radyasyonu, plastik ürünlerin kullanım ömrünü etkileyen başlıca faktörlerden biridir. Güneş ışığına maruz kalan plastikler, özellikle dikey tarım ekipmanlarındaki dış mekan uygulamaları için kırılgan hale gelebilir, solabilir ve hatta çatlayabilir. Kalın ölçülü termoform parçaların UV direncini artırmak için genellikle aşağıdaki önlemler alınır:
- UV Stabilizatörlerinin İlavesi: UV stabilizatörleri veya UV emiciler, UV radyasyonunu etkili bir şekilde absorbe etmek veya yansıtmak için plastik malzemelere eklenerek malzemenin yaşlanma sürecini yavaşlatır. Örneğin, Polikarbonat (PC) ve Polipropilen (PP) gibi polimerler doğal UV direncine sahiptir, ancak UV stabilizatörleri eklenerek daha da geliştirilebilir.
- UV Engelleyici Kaplamalar: Ürünün yüzeyine UV ışınlarından koruyan fiziksel bir bariyer oluşturan UV koruyucu bir film uygulanabilir. Bu kaplamalar tipik olarak şeffaftır ve UV ışınlarının nüfuz etmesini ve iç yapıyı bozmasını önleyerek etkili koruma sağlar.
2. Nem Direnci:
Dikey tarım ortamları genellikle yüksek neme sahiptir ve bu da plastik ürünlerin performansı açısından zorluk teşkil eder. Nem sadece malzemenin yaşlanmasını hızlandırmakla kalmaz, aynı zamanda küf oluşumuna da yol açabilir. Bu nedenle, ısıyla şekillendirilmiş parçalarda nem direncinin korunması çok önemlidir. Aşağıdaki önlemler nem direncini etkili bir şekilde artırabilir:
- Malzeme Seçimi: Polipropilen (PP) ve Yüksek Yoğunluklu Polietilen (HDPE) gibi bazı plastik malzemeler doğal olarak iyi nem direncine sahiptir. Bu malzemeler su girişini önler ve nemli ortamlarda kullanım için idealdir.
- Yüzey İşlemleri: Su girişini önleyen koruyucu bir tabaka oluşturmak için yüzey kaplamaları veya neme dayanıklı katkı maddeleri uygulanabilir. Örneğin, özel su geçirmez kaplamalar plastik yüzey üzerinde geçirimsiz bir bariyer oluşturarak ürünün dayanıklılığını artırabilir.
- Düşük Nem Emici Malzemeler: Uzun süre nemli koşullara maruz kalacak ürünler için nem emilimi düşük malzemelerin seçilmesi, su alımına bağlı genleşme ve deformasyonun önlenmesi açısından önemlidir.
3. Küf Direnci:
Küf oluşumu sadece plastiklerin görünümünü etkilemekle kalmaz, aynı zamanda ürünlere de zarar verebilir. Bu nedenle, dikey tarımda kullanılan kalın ölçülü termoform parçalar için küf direnci önemli bir husustur. Küf gelişimi tipik olarak nem ve sıcaklığın bir kombinasyonunu gerektirir ve küfe karşı uygun önlemlerin uygulanması bu sorunu önleyebilir.
- Antibakteriyel Katkı Maddeleri: Antibakteriyel katkı maddeleri, küf ve bakteri büyümesini engellemek için plastik malzemeye dahil edilebilir. Örneğin, gümüş iyonu bazlı katkı maddeleri küfü etkili bir şekilde öldürür ve plastik yüzeyde büyümesini önler.
- Küfe Dayanıklı Kaplamalar: İç katkı maddelerine ek olarak, ısıyla şekillendirilmiş parçaların yüzeyine küflenmeye karşı dayanıklı kaplamalar uygulanabilir. Bu kaplamalar sadece plastiği nemden korumakla kalmaz, aynı zamanda mantar oluşumunu önleyen küfe dayanıklı bir bariyer oluşturur.
- Antibakteriyel Katkı Maddeleri: Antibakteriyel katkı maddeleri, küf ve bakteri büyümesini engellemek için plastik malzemeye dahil edilebilir. Örneğin, gümüş iyonu bazlı katkı maddeleri küfü etkili bir şekilde öldürür ve plastik yüzeyde büyümesini önler.
- Küfe Dayanıklı Kaplamalar: İç katkı maddelerine ek olarak, ısıyla şekillendirilmiş parçaların yüzeyine küflenmeye karşı dayanıklı kaplamalar uygulanabilir. Bu kaplamalar sadece plastiği nemden korumakla kalmaz, aynı zamanda mantar oluşumunu önleyen küfe dayanıklı bir bariyer oluşturur.
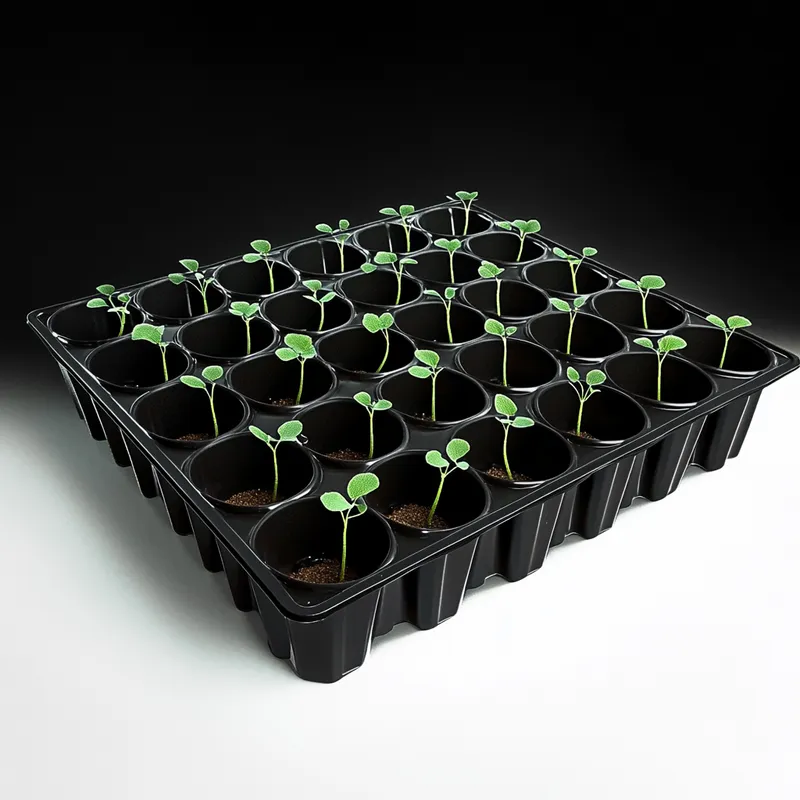
Kalın Ölçülü Termoformun Boyut Sınırlamaları Nelerdir?
Genellikle ağır ölçülü termoform olarak adlandırılan kalın ölçülü termoform, kalın bir plastik tabakayı ısıtan ve bir kalıp kullanarak dayanıklı bileşenlere dönüştüren çok yönlü bir üretim sürecidir. Bu teknik, sağlam ve özel parçalar yaratma kabiliyeti nedeniyle dikey tarım da dahil olmak üzere tüm sektörlerde yaygın olarak kullanılmaktadır. Peki bu parçalar ne kadar büyük olabilir? Aşağıda, bu sürecin boyut sınırlamalarını araştırıyor ve dikey tarım uygulamalarıyla ilgili içgörülerle büyük parçalar üretme kapasitesini doğruluyoruz.
1. Kalın Ölçülü Termoformun Boyut Sınırlamaları Nelerdir?
Ağır kalibreli ısıl şekillendirme yoluyla üretilen parçaların maksimum boyutu birkaç temel faktöre bağlıdır. Bu kısıtlamaları anlamak, sürecin dikey tarım ihtiyaçlarınıza uygun olup olmadığını belirlemenize yardımcı olur.
① Makine Kapasitesi: Termoform makinesinin boyutu, işleyebileceği plastik levha için üst sınırı belirler. Çoğu standart makine 2,5 metreye 3 metreye (8 feet'e 10 feet) kadar olan levhaları işler. Bununla birlikte, gelişmiş veya özel ekipmanlar, üreticiye bağlı olarak 3 metreye 4 metre (10 feet'e 13 feet) veya daha fazlası gibi daha büyük boyutları yönetebilir.
② Sac Kalınlığı: Ağır ölçülü termoform tipik olarak 1,5 mm (0,06 inç) ila 12,7 mm (0,5 inç) kalınlığında levhalarla çalışır. Daha kalın levhalar dayanıklılık sunar ancak daha uzun ısıtma süreleri gerektirebilir ve şekillendirme sırasında esnekliğin azalması nedeniyle karmaşık tasarımları sınırlayabilir.
③ Kalıp Boyutu ve Çekme Derinliği: Kalıp, makinenin şekillendirme alanına sığmalıdır. Daha büyük parçalar için kalıp tasarımı, bükülme gibi kusurları önlemek için eşit ısıtma ve soğutma sağlamalıdır. Çekme derinliği (parçanın genişliğine göre ne kadar derin olduğu) de önemlidir. Tipik bir çekme oranı 2:1'dir (yükseklik/genişlik), ancak bu akıllı kalıp mühendisliği ile değişebilir.
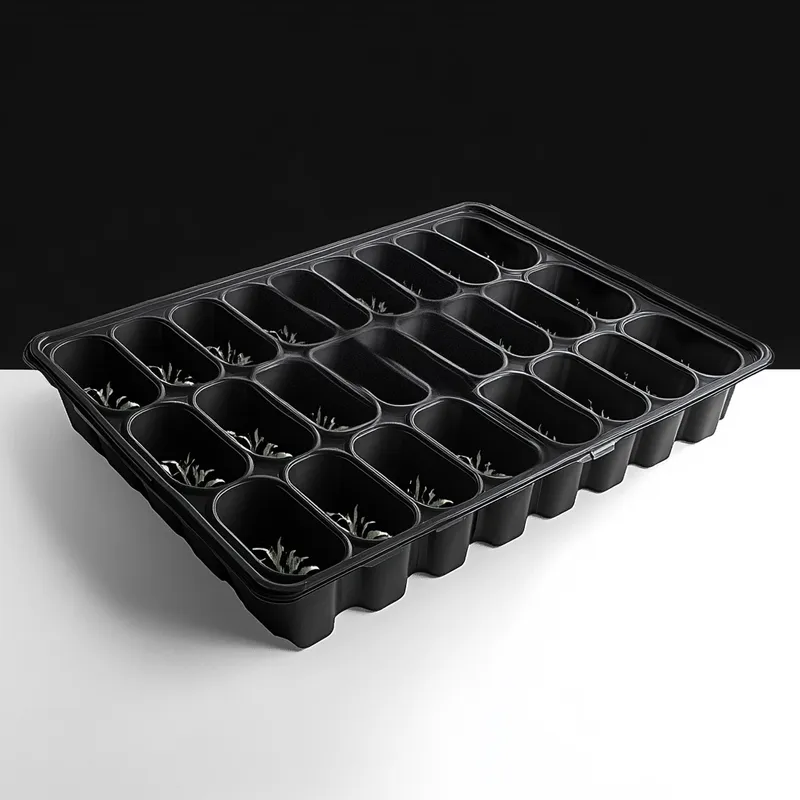
④ Malzeme Özellikleri: ABS, polikarbonat ve HDPE gibi plastikler kalın ölçülü termoformda popülerdir. Her malzeme farklı şekilde esneyerek bir parçanın incelmeden veya gücünü kaybetmeden ne kadar büyüklükte oluşturulabileceğini etkiler. Dikey tarımda büyük ölçekli uygulamalar için malzeme seçimi kritik önem taşır.
⑤ Pratik Kısıtlamalar: Teknik sınırların ötesinde, büyük boyutlu parçaların üretilmesi taşıma ve nakliye gibi lojistik zorluklar içerebilir veya maliyetleri artıran özel ekipman gerektirebilir. Bu faktörler boyutu doğrudan kısıtlamaz ancak fizibiliteyi etkiler.
2. Kalın Ölçülü Termoform Büyük Parçalar Üretebilir mi?
Evet, ağır kalibreli termoform büyük parçalar oluşturmada mükemmeldir ve bu da onu büyük, sağlam bileşenlere ihtiyaç duyan endüstriler için başvurulacak bir çözüm haline getirir. İşte dikey tarım için güçlü bir rakip olmasının nedeni:
① Kanıtlanmış Büyük Parça Kapasitesi: Bu süreç, doğru ekipmanla 3 metreye 4 metre (10 feet'e 13 feet) veya daha büyük parçalar üretebilir. Örnekler arasında otomotiv panelleri, cihaz muhafazaları ve hatta tekne gövdeleri yer almaktadır - bu da önemli boyutları işleme yeteneğini göstermektedir.
② Dikey Tarım Uygulamaları: Dikey tarımda, kalın ölçülü termoform büyük bileşenler için parlıyor:
- Yetiştirme Tepsileri: Birkaç metre uzunluğa kadar özel tepsiler veya paneller, kapsamlı bitki kurulumlarını destekleyebilir.
- Yapısal Muhafazalar: Ekipman için dayanıklı kapaklar veya çerçeveler, belirli sistem boyutlarına uyacak şekilde oluşturulabilir.
- Sulama Sistemleri: Su yönetimi için büyük, su geçirmez tepsiler verimli bir şekilde üretilebilir.
③ Temel Avantajlar:
- Uygun Fiyatlı Kalıplar: Enjeksiyon kalıplama ile karşılaştırıldığında, kalın ölçülü termoform kalıpları, özellikle büyük, düşük hacimli parçalar için uygun maliyetlidir.
- Malzeme Çok Yönlülüğü: Kalın plastikler, büyük parçalar için aşırı son işlem gerektirmeden güç ve dayanıklılık sağlar.
- Tasarım Özgürlüğü: Proses karmaşık şekilleri, dokuları ve alt kesimleri destekleyerek büyük çiftlik parçalarının işlevselliğini artırır.
④ Potansiyel Zorluklar:
- Kalınlık Tutarlılığı: Çok büyük veya derin parçalarda, gelişmiş kalıp tasarımları gerektiren düzensiz et kalınlığı görülebilir.
- Ekipman Erişimi: Tüm üreticilerin büyük boyutlu parçalar için makineleri yoktur, bu nedenle doğru tedarikçi ile ortaklık kurmak çok önemlidir.
- Lojistik: Büyük termoform parçaların taşınması ve montajı ekstra planlama gerektirebilir.
3. Bir Bakışta Boyut Yetenekleri:
Aspect | Tipik Aralık | Notlar |
---|---|---|
Sayfa Boyutu | 3m x 4m'ye (10ft x 13ft) kadar veya daha büyük | Daha büyük boyutlar özel makinelere bağlıdır. |
Sac Kalınlığı | 1,5 mm ila 12,7 mm (0,06 inç ila 0,5 inç) | Daha kalın tabakalar dayanıklılığı artırır ancak ayrıntıları sınırlayabilir. |
Çekme Derinliği | Genellikle 2:1 (yükseklik/genişlik) | Daha derin parçalar için kalıp tasarımı ile ayarlanabilir. |
Ortak Malzemeler | ABS, polikarbonat, HDPE | Boyut, güç ve çevresel ihtiyaçlara göre seçilmiştir. |
Dikey Tarım Uygulamaları için Sürdürülebilir Malzemeler
Sürdürülebilirlik artık sadece bir moda sözcük değil, üretim ve tarımda itici bir güç. Dikey tarım, daha az arazi kullanımı ve daha düşük su tüketimi gibi çevre dostu özellikleriyle zaten ünlüdür. Bununla birlikte, çevresel faydalarını en üst düzeye çıkarmak için endüstri, ağır ölçülü termoformda giderek daha fazla sürdürülebilir malzemelere yöneliyor.
Dikey tarımda, kalın levha termoform neme, ağırlığa ve değişen sıcaklıklara dayanması gereken temel bileşenleri oluşturur. Üreticiler sürdürülebilir malzemeleri entegre ederek, performanstan ödün vermeden bu sistemlerin çevre dostu olma özelliğini geliştirir.
Kalın Ölçülü Termoformda Sürdürülebilir Malzeme Türleri:
Dikey tarım için kalın ölçülü termoformda çeşitli sürdürülebilir malzemeler kullanılmaktadır. Aşağıda en öne çıkan seçeneklere genel bir bakış yer almaktadır:
① Geri dönüştürülmüş PET (rPET):
- Temel Özellikler: Yüksek mukavemet, dayanıklılık ve şeffaflık.
- Sürdürülebilirlik Avantajları: Plastik atıkları azaltır ve işlenmemiş PET üretimine göre 60%'ye kadar daha az enerji kullanır.
- Kullanım alanları: Tepsiler, konteynerler ve yapısal paneller.
② Polilaktik Asit (PLA):
- Temel Özellikler: Biyolojik olarak parçalanabilir, gübrelenebilir, orta güçte.
- Sürdürülebilirlik Avantajları: Fosil yakıt bağımlılığını azaltır ve kompostlanabilir bir kullanım ömrü sonu seçeneği sunar.
- Kullanım alanları: Fide tepsileri ve küçük kaplar.
③ Biyo-bazlı Polietilen (Bio-PE):
- Temel Özellikler: Geleneksel polietilenin gücü ve esnekliği ile eşleşir.
- Sürdürülebilirlik Avantajları: Fosil bazlı PE'ye kıyasla karbon ayak izini önemli ölçüde azaltır.
- Kullanım alanları: Sulama bileşenleri ve daha büyük paneller.
④ Geri Dönüştürülmüş Yüksek Yoğunluklu Polietilen (rHDPE):
- Temel Özellikler: Mükemmel dayanıklılık ve darbe direnci.
- Sürdürülebilirlik Avantajları: Yaygın olarak geri dönüştürülebilir ve atık birikimini azaltır.
- Kullanım alanları: Büyük konteynerler ve yapısal destekler.
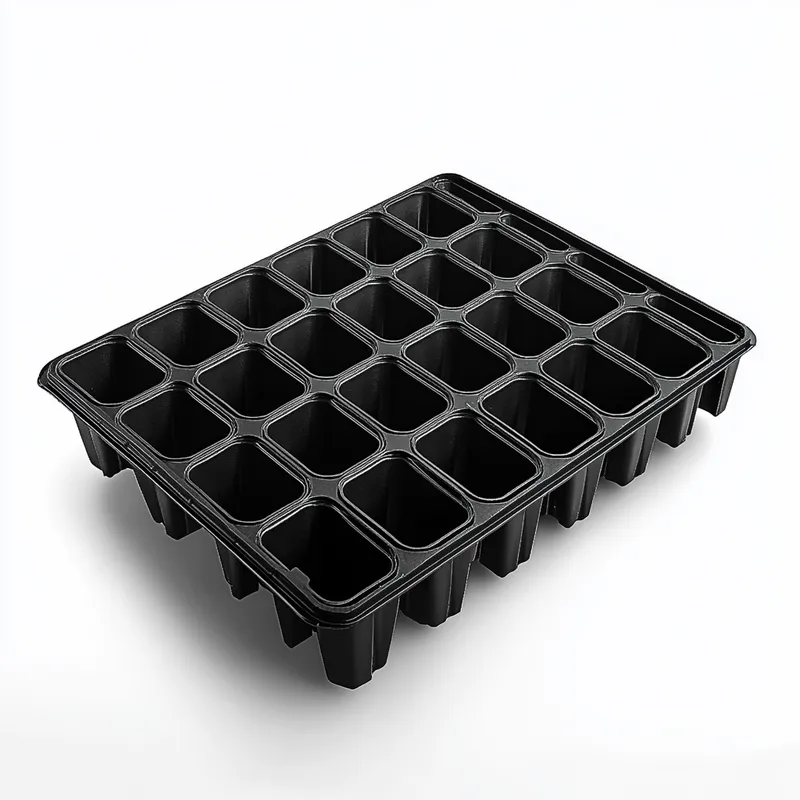
Malzeme | Kaynak | Biyobozunurluk | Güç | Maliyet | Çevresel Etki |
---|---|---|---|---|---|
rPET | Geri dönüştürülmüş plastik şişeler | Hayır | Yüksek | Orta | Düşük |
PLA | Mısır nişastası, şeker kamışı | Evet | Orta | Yüksek | Çok Düşük |
Bio-PE | Şeker Kamışı | Hayır | Yüksek | Orta | Düşük |
rHDPE | Geri dönüştürülmüş plastik atık | Hayır | Yüksek | Düşük | Düşük |
Termoform Parçaların Uzun Süreli Dayanıklılığı Nasıl Sağlanır?
Ağır ölçülü vakum şekillendirme veya sağlam plastik kalıplama olarak da bilinen kalın ölçülü termoform, dikey tarım gibi endüstriler için sağlam, uzun ömürlü bileşenler oluşturmak için yaygın olarak kullanılan güçlü bir üretim sürecidir. Tepsiler, paneller ve yapısal destekler gibi bu ürünler, eğilmeden veya çatlamadan neme, sıcaklık dalgalanmalarına ve mekanik gerilime dayanmalıdır. Peki, termoform ürünlerin zaman içinde dayanıklılıklarını korumalarını nasıl sağlayabilirsiniz? Aşağıda, bunu başarmak için dikey tarımın benzersiz taleplerine göre uyarlanmış kanıtlanmış stratejileri özetliyoruz.
1. Uzun Ömürlü Olması İçin Doğru Malzemeyi Seçin:
Uygun malzemenin seçilmesi, dayanıklı ağır ölçülü vakumlu şekillendirme ürünlerinin temelini oluşturur. Doğru termoplastik, dikey tarım kurulumlarında yaygın olan nem ve UV ışınlarına maruz kalma gibi çevresel zorluklara karşı koyabilir.
- ABS (Akrilonitril Bütadien Stiren): Mükemmel darbe direnci ve tokluk sunar, yük taşıyan parçalar için idealdir.
- PVC (Polivinil Klorür): Kimyasal direnci ile bilinir, gübre veya temizlik maddelerinin bulunduğu ortamlar için mükemmeldir.
- Polikarbonat: Olağanüstü güç ve UV direnci sağlar, dış mekan veya yarı açık tarım sistemleri için mükemmeldir.
- HDPE (Yüksek Yoğunluklu Polietilen): Neme karşı dayanıklıdır ve ıslak koşullarda bütünlüğünü korur, hidroponik kurulumlar için bir zorunluluktur.
İpucu: Malzemeyi özel ihtiyaçlarınızla eşleştirin. Örneğin, HDPE yüksek nemli dikey çiftliklerde üstünlük sağlarken, polikarbonat UV ışınlarına maruz kalan çatı sistemlerine uygundur.
2. Dayanıklılığı Göz Önünde Bulundurarak Tasarlayın:
Akıllı bir tasarım, kalın ölçülü termoform parçalarda eğilme veya çatlamaya yol açan gerilim birikimini önler.
- Yumuşak Geçişler: Stres yoğunluğunu azaltmak için keskin köşeleri yuvarlatılmış kenarlarla değiştirin.
- Takviyeler: Özellikle ağır bitkiler taşıyan tepsilerde yükleri eşit dağıtmak için nervür veya köşebentler ekleyin.
- Dengeli Çizim Oranı: Yapıyı zayıflatan incelmeyi önlemek için yükseklik/genişlik oranını (cer oranı) 2:1'in altında tutun.
Örnek: Yuvarlatılmış kenarlara ve takviye nervürlerine sahip bir tepsi, ağırlık altında deforme olmadan istiflenmiş ekicileri destekleyebilir.
3. Üretim Sürecinde Uzmanlaşın:
Sağlam plastik kalıplama sırasındaki hassasiyet, ürünün dayanıklılığı tehlikeye atabilecek kusurlardan arınmış olarak ortaya çıkmasını sağlar.
- Eşit Isıtma: Plastik levhayı eşit şekilde ısıtmak için kızılötesi ısıtıcılar kullanın ve bükülmeye neden olan sıcak noktaları önleyin.
- Kademeli Soğutma: İç gerilmeleri en aza indirmek için şekillendirilmiş parçayı fanlar veya su banyoları ile yavaşça soğutun.
- Uygun Şekillendirme Basıncı: Malzemeyi aşırı germeden şekillendirmek için tutarlı vakum veya basınç uygulayın.
Profesyonel ipucu: Tutarlı sonuçlar için hassas sıcaklık kontrollerine sahip modern termoform ekipmanlarına yatırım yapın.
4. Post-Processing Teknikleri ile Geliştirin:
Üretim sonrası adımlar, ağır ölçülü vakumla şekillendirilmiş ürünlerin ömrünü önemli ölçüde artırabilir.
- Tavlama: İç gerilimleri azaltmak için plastiğe ısıl işlem uygulayarak zaman içinde eğrilme riskini azaltır.
- Hassas Kırpma: Pürüzlü noktalarda çatlakların başlamasını önleyerek pürüzsüz kenarlar oluşturmak için CNC yönlendiriciler kullanın.
Fayda: Tavlama, özellikle dikey çiftliklerde dalgalanan sıcaklıklara maruz kalan polikarbonat parçalar için etkilidir.
5. Çevresel Stresörlere Karşı Koruyun:
Dikey tarım ortamları zorlu olabilir, bu nedenle kalın mastar ısıl şekillendirme işlemi sırasında bu koşulları planlayın.
- UV Koruması: Güneş ışığından kaynaklanan bozulmayı önlemek için ABS veya polikarbonat gibi malzemelere UV stabilizatörleri ekleyin.
- Sıcaklık Esnekliği: Ürünün çalışma aralığının çiftliğin iklimiyle eşleştiğinden emin olun; soğukta kırılganlıktan veya sıcakta yumuşamadan kaçının.
- Kimyasal Direnç: Gübre, su veya temizlik solüsyonlarına maruz kalmaya dayanıklı malzemeler seçin.
Örnek: UV ile stabilize edilmiş HDPE panel, güneş ışığı alan dikey bir çiftlikte solmaya ve çatlamaya karşı dayanıklıdır.
6. Bakım ve Denetime Öncelik Verin:
Düzenli bakım, sağlam plastik kalıplı bileşenlerin zaman içinde en iyi durumda kalmasını sağlar.
- Rutin Kontroller: Sorunları daha da kötüleşmeden ele almak için renk değişikliği veya hafif eğilme gibi erken stres belirtilerini arayın.
- Temizlik: Yüzeyi bozabilecek kir veya kimyasal birikintileri giderin.
Hızlı bilgi: Aylık basit bir denetim, sorunları erkenden yakalayarak termoform parçaların ömrünü uzatabilir.
7. Zorlu Koşullarda Daha Kalın Göstergeleri Tercih Edin:
Dikey tarım gibi zorlu uygulamalar için daha kalın malzemeler ekstra dayanıklılık sağlar.
- Standart Kalınlık: Kalın ölçülü termoform, 0,060 inç (1,5 mm) üzerinde levhalar kullanır ve doğal güç sunar.
- Ağır Hizmet Kullanımı: Raflar veya su kanalları gibi sabit yük altındaki bileşenler için kalınlığı artırın.
Kalınlık (inç) | Uygulama | Dayanıklılık Avantajı |
---|---|---|
0.060 - 0.120 | Işık tepsileri, kapaklar | Temel güç, hafif |
0.120 - 0.250 | Yapısal destekler, paneller | Yüksek yük direnci |
0.250+ | Ağır hizmet tipi raflar | Maksimum dayanıklılık |
8. Katkı Maddeleri ile Performansı Artırın:
Özel katkı maddeleri, belirli zorluklar için termoform ürünlerin özelliklerini geliştirir.
- Darbe Değiştiriciler: Çarpma veya düşme ihtimali olan parçalar için darbe direncini artırır.
- UV Stabilizatörleri: Güneş kaynaklı zayıflamayı önler, dış mekan dikey çiftlikleri için çok önemlidir.
- Antioksidanlar: Uzun süreli kullanımda oksijene bağlı gevrekleşmeye karşı korur.
Parça Tasarımı Dikey Tarımı Nasıl Etkiliyor?
Dikey tarım, mahsullerin genellikle kontrollü kapalı ortamlarda üst üste katmanlar halinde yetiştirilmesini sağlayarak tarımı dönüştürüyor. Bu yenilikçi yaklaşım, alan verimliliğini en üst düzeye çıkararak sınırlı araziye sahip kentsel ortamlar için idealdir. Bu sistemlerde kritik bir unsur, termoform parçaların kullanılmasıdır - ağır ölçülü termoform, kalın levha termoform veya yapısal termoform gibi işlemlerle üretilen plastik bileşenler. Tepsiler, konteynerler ve yapısal destekler de dahil olmak üzere bu parçalar, dikey tarım kurulumlarının işlevselliği ve verimliliği için çok önemlidir.
1. Termoform Parça Tasarımının Dikey Tarım Sistemleri Üzerindeki Temel Etkileri:
① Alan Verimliliği:
Alanı maksimize etmek dikey tarımın temel taşlarından biridir ve ısıyla şekillendirilmiş bileşenlerin tasarımı çok önemli bir rol oynar.
- Optimize Edilmiş İstifleme: Güvenli bir şekilde istiflenecek şekilde tasarlanan tepsiler, sınırlı bir alanda daha fazla yetiştirme katmanı sağlar.
- Yerleştirme Özellikleri: Kullanılmadığında, iç içe geçme özelliğine sahip tepsiler depolama alanını azaltır.
- Bitki Kapasitesi: Bir tepsinin şekli ve düzeni, kaç bitki tutabileceğini belirler. Örneğin ızgara desenli bir tepsi, bitki yoğunluğunu önemli ölçüde artırabilir.
② Su ve Besin Dağıtımı:
Verimli sulama ve besin dağıtımı sağlıklı mahsuller için hayati önem taşır ve termoform parçalar bu sistemleri geliştirmek üzere tasarlanabilir.
- Entegre Kanallar: Yerleşik oluklara sahip tepsiler, su ve besin maddelerinin her bitkiye eşit şekilde ulaşmasını sağlar.
- Drenaj Çözümleri: Eğimli yüzeyler veya delikler su birikmesini önleyerek kök çürümesi riskini azaltır.
- Modüler Tasarım: Parçalar damla sulama veya hidroponik sistemler için konektörler içerebilir.
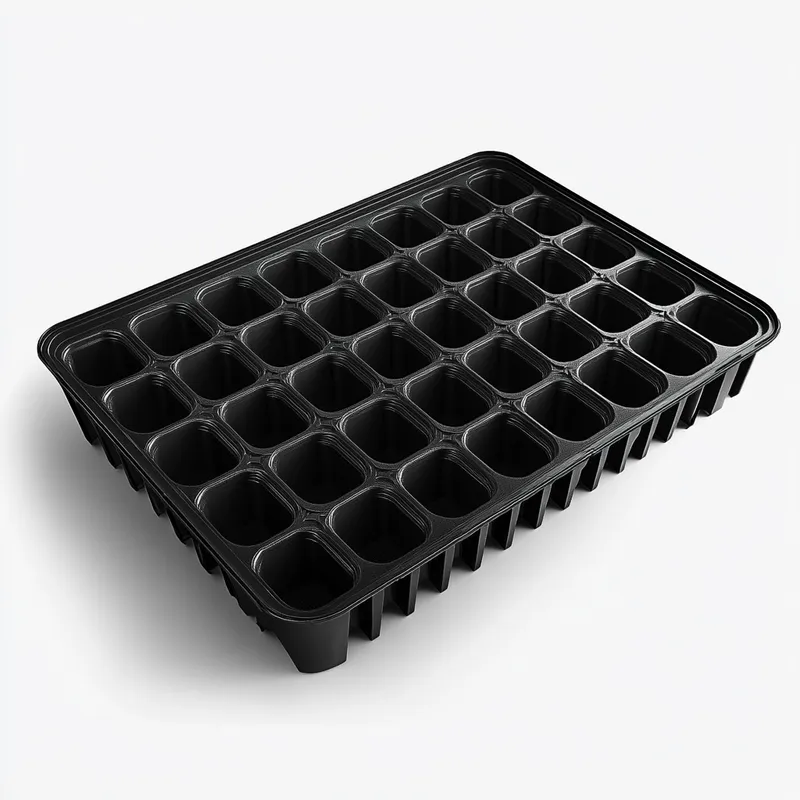
Özellik | Fayda |
Kanallar/Oluklar | Eşit besin maddesi dağılımı |
Drenaj Delikleri | Aşırı sulamayı ve kök hasarını önler |
Eğimli Tasarım | Suyu verimli bir şekilde köklere yönlendirir |
③ Işık Dağılımı:
Yapay aydınlatma dikey tarımda yaygındır ve ısıyla şekillendirilmiş parçaların tasarımı ışığın bitkilere ulaşma şeklini optimize edebilir.
- Yansıtıcı Yüzeyler: Parlak veya açık renkli yüzeylere sahip parçalar ışığı alt katmanlara yansıtarak genel pozlamayı iyileştirir.
- Malzeme Seçenekleri: Şeffaf veya yarı saydam plastikler, ışığın istiflenmiş seviyelerden geçmesine izin verir.
- Şekil Hususları: Kavisli kenarlar gölgeleri en aza indirebilir ve ışık homojenliğini artırabilir.
④ Dayanıklılık ve Bakım:
Dikey tarım ortamları genellikle nemli ve zorludur, bu da zaman içinde dayanıklı parçalar gerektirir.
- Malzeme Mukavemeti: ABS, polikarbonat veya HDPE gibi plastikler neme, kimyasallara ve aşınmaya karşı dayanıklıdır.
- Dikişsiz Yapı: Pürüzsüz, tek parça tasarımlar bakteri veya döküntülerin birikebileceği alanları azaltır.
- Temizlik Kolaylığı: Gözeneksiz yüzeyler sanitasyonu kolaylaştırarak hijyenik bir yetiştirme alanı sağlar.
⑤ Maliyet ve Ölçeklenebilirlik:
Termoform parçaların ekonomikliği ve uyarlanabilirliği, onları dikey tarım için pratik bir seçim haline getirmektedir.
- Düşük Kalıp Maliyetleri: Enjeksiyon kalıplama ile karşılaştırıldığında, termoform daha az pahalı kalıplar gerektirir ve küçük ila orta ölçekli çalışmalar için idealdir.
- Hafif Tasarım: Nakliye ve kurulum maliyetlerini azaltır.
- Ölçeklenebilir Üretim: Modüler parçalar, çiftlik büyüdükçe çoğaltılabilir veya ayarlanabilir.
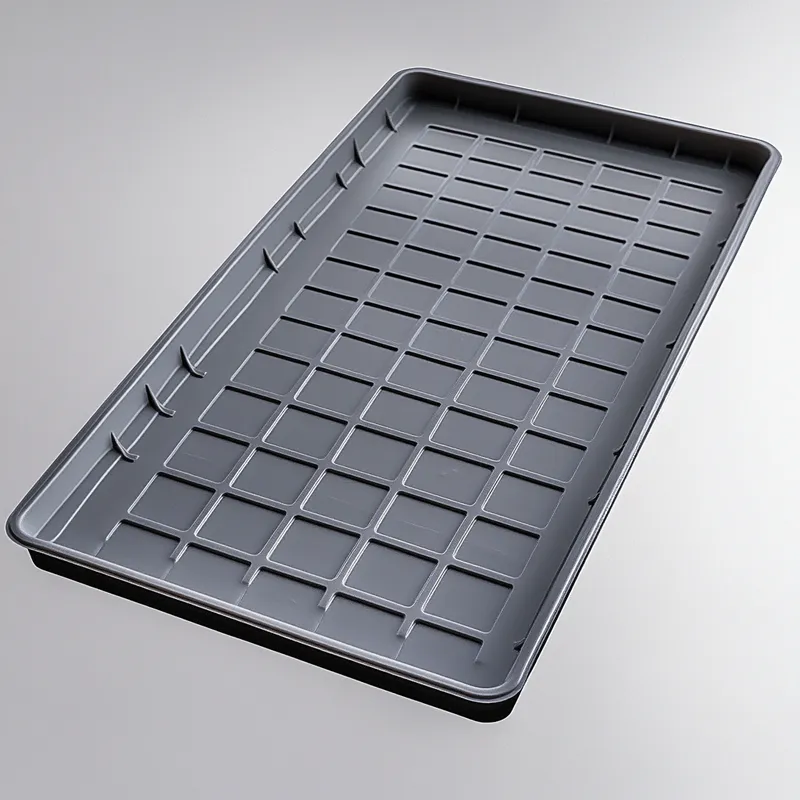
Süreç | Kalıp Maliyeti | Üretim Hızı | İdeal Kullanım Örneği |
Termoform | Düşük | Orta | Küçük ila orta ölçekli çalışmalar |
Enjeksiyon Kalıplama | Yüksek | Yüksek | Seri üretim |
3D Baskı | Orta | Düşük | Prototipleme |
2. Isıl Şekillendirilmiş Parçaların Çevresel Faydaları:
Sürdürülebilirlik, tarımda giderek artan bir önceliktir ve termoform parçalar buna olumlu katkıda bulunabilir.
- Geri Dönüştürülebilir Malzemeler: PET ve HDPE gibi plastikler geri dönüştürülebilir ve atıkları en aza indirir.
- Enerji Verimliliği: Ağır ölçülü termoform prosesi, fiberglas kalıplama gibi alternatiflere göre daha az enerji kullanır.
- Azaltılmış Kaynak Kullanımı: Optimize edilmiş tasarımlar su ve besin tüketimini azaltır.
Yüksek Sıcaklık ve Yüksek Nemde Isıl Şekillendirilmiş Parçalar
Kontrollü ortamların mahsul verimini en üst düzeye çıkarmanın anahtarı olduğu dikey tarım endüstrisinde, tepsiler, konteynerler ve yapısal paneller gibi kalın ölçülü termoform ürünler olağanüstü faydalar sağlar. Kalın plastik levhaların ısıtılması ve şekillendirilmesi işlemiyle oluşturulan bu ürünler, dikey çiftliklerin zorlu koşullarına, özellikle de yüksek sıcaklıklara ve yüksek neme dayanacak şekilde tasarlanmıştır. Hafif, tek kullanımlık ürünler üreten ince ölçülü termoformun aksine, kalın ölçülü termoform dikey çiftlikler gibi zorlu ortamlarda tekrar tekrar kullanılmak üzere tasarlanmış dayanıklı parçalar oluşturur.
1. Yüksek Sıcaklıklı Ortamlarda Faydaları:
Dikey çiftlikler genellikle yetiştirme ışıkları, ekipman veya dış iklim faktörlerinden kaynaklanan yüksek sıcaklıklarla karşı karşıya kalır. Kalın ölçülü termoform ürünler bu sıcak koşullarda çeşitli avantajlar sağlar:
① Şekil Tutma: Bu ürünler uzun süreli ısıya maruz kaldıklarında bile eğilmeye veya bükülmeye karşı dayanıklıdır. Bu, tepsilerin ve panellerin hizalı kalmasını sağlayarak yapısal bozulma olmadan tutarlı bitki büyümesini destekler.
② Uzun Ömürlü Dayanıklılık: Kırılganlaşmadan termal strese dayanırlar ve kullanım ömürlerini uzatırlar. Bu da değiştirme maliyetlerini azaltır ve çiftliğin sorunsuz çalışmasını sağlar.
③ Isıya Dayanıklı Malzemeler:
- Polikarbonat: 120°C'ye kadar sıcaklıkları tolere eder, sıcak bölgeler için mükemmeldir.
- Polipropilen: Isı altında sabit ve güçlü kalır, deformasyona karşı dirençlidir.
2. Yüksek Nemli Ortamlarda Faydaları:
Dikey çiftliklerde sulama ve bitki terlemesinden kaynaklanan yüksek nem yaygındır. Kalın ölçülü termoform ürünler burada da parlar:
① Nem Dayanımı: Suyu emmezler, çiftliğin kurulumunu bozabilecek şişme veya eğrilmeyi önlerler. Bu, bileşenlerin istiflenmiş veya modüler sistemlere mükemmel şekilde oturmasını sağlar.
② Hijyenik Özellikler: Pürüzsüz, gözeneksiz yüzeyleri küf ve bakteri oluşumuna karşı dirençlidir. Bu da daha temiz bir ortam yaratarak mahsuller için hastalık risklerini azaltır.
③ Akıllı Tasarım Özellikleri: Drenaj delikleri ve havalandırma kanalları gibi özellikler aşırı nemi yönetir. Bu da su birikimini önler ve sağlıklı kök koşullarını destekler.
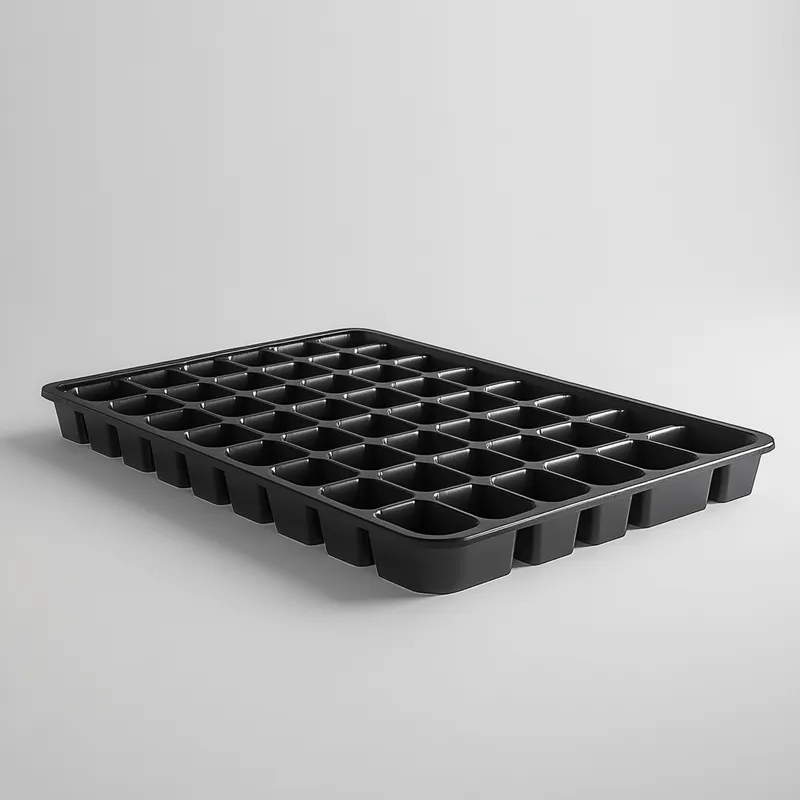
MÜŞTERİ İÇİN SSS
İle Başlarken Uplastech
Sorularınız mı var? Cevaplarımız var.
Ekstrüzyon, vakumlu şekillendirme, şişirme ve hassas kalıp yapımında uzmanlaşarak çeşitli üretim ihtiyaçlarınızı karşılamak için özelleştirilmiş çözümler sunuyoruz.
B2B ortaklıklarına odaklanarak ve ekstrüzyon, termoform, şişirme ve hassas kalıp yapımı alanlarında çözümler sunarak otomotiv, elektronik, tüketim malları ve ambalaj dahil olmak üzere çeşitli sektörlerle çalışıyoruz.
Evet, çözümlerimizi benzersiz gereksinimlerinize uyacak şekilde uyarlıyoruz.
İletişime Geçin
Fiyat teklifi almak için bize e-posta göndermekten veya aşağıdaki formu doldurmaktan çekinmeyin.
E-posta: uplastech@gmail.com