Perfis PE de alta qualidade para aplicações versáteis
Descubra os perfis PE de alta qualidade na UPlastech, concebidos para durabilidade e versatilidade em várias aplicações. Explore a nossa gama hoje mesmo!
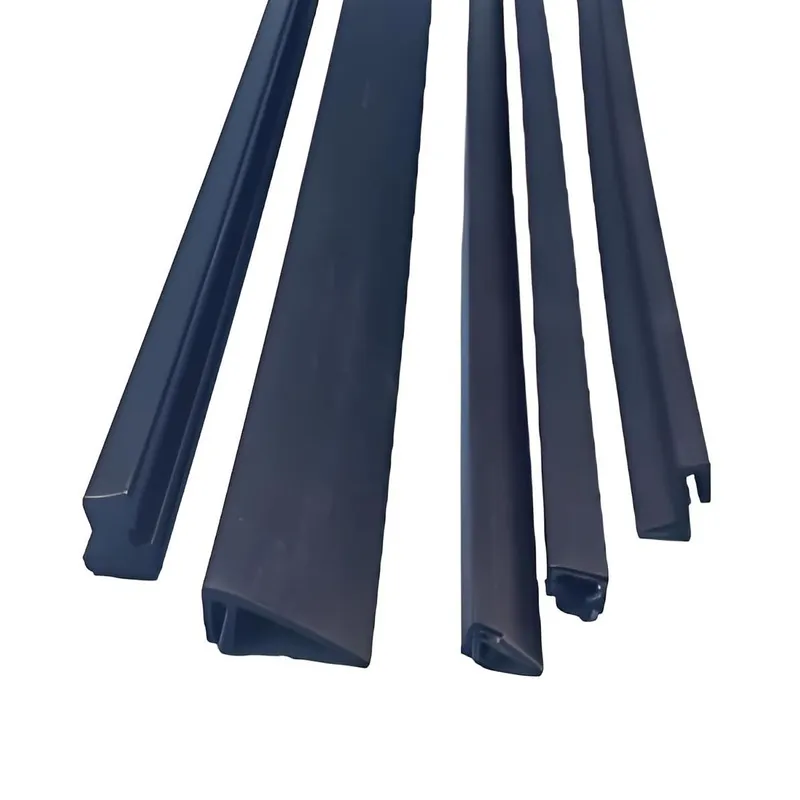
Faixa de desgaste da calha de guia PE
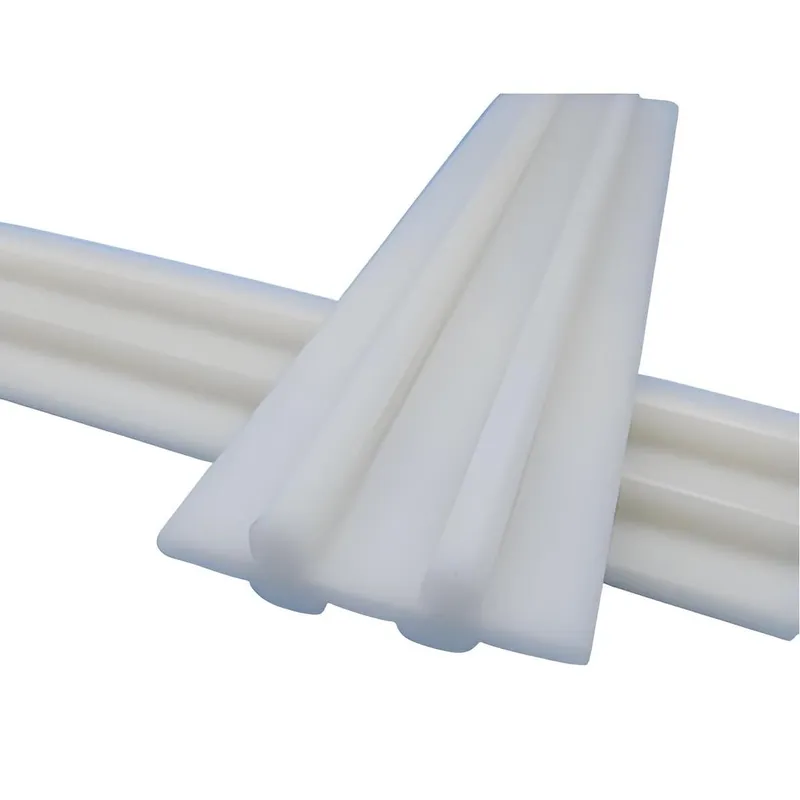
Perfil de calha de guia HDPE (tira de desgaste)
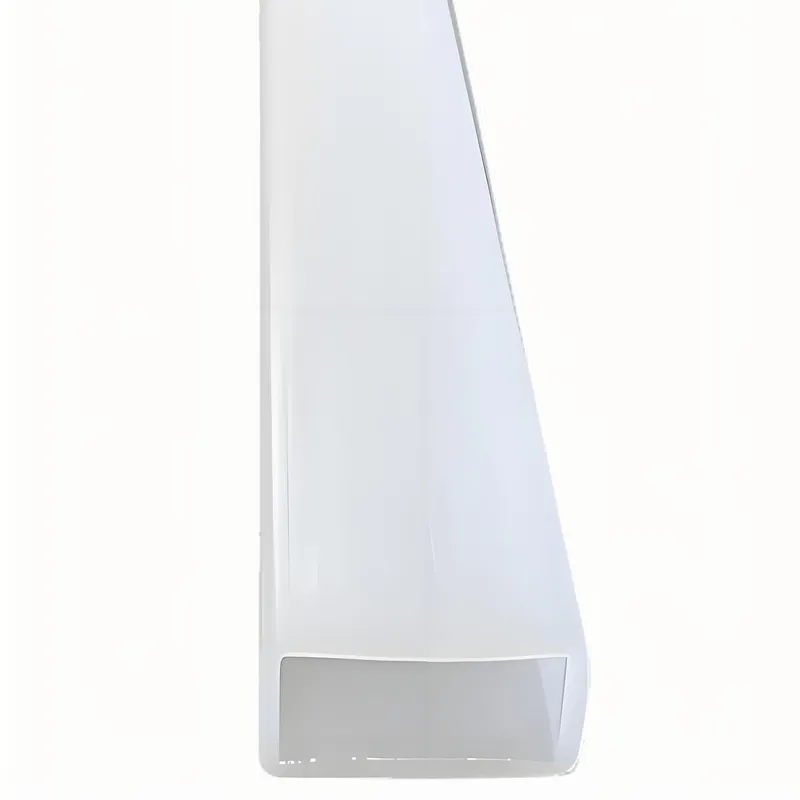
Tubo quadrado PE
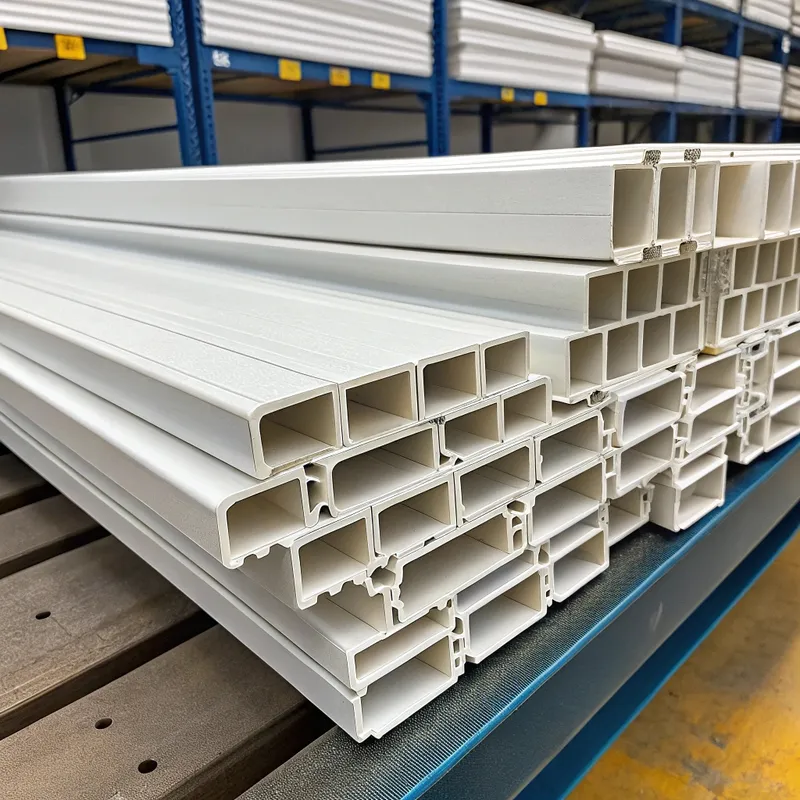
Guia para o fabrico de perfis de extrusão de PE personalizados
O que são perfis PE personalizados?
Os perfis PE personalizados referem-se a formas especializadas e contínuas fabricadas a partir de plástico de polietileno (PE) através do processo de extrusão, adaptadas para satisfazer os requisitos funcionais e de conceção específicos de uma determinada aplicação.
Nome técnico completo: Perfis extrudidos de polietileno.
Pseudónimos comuns: Formas extrudidas de PE, extrusões de polietileno personalizadas, secções de PE.
Princípios fundamentais: O princípio fundamental envolve a extrusão de termoplásticos. O polietileno, um polímero termoplástico, é aquecido até ao estado fundido e depois forçado (extrudido) através de uma matriz com uma forma específica. À medida que o plástico derretido sai da matriz, assume a forma da secção transversal da matriz. Esta forma contínua é então arrefecida, solidificada e cortada nos comprimentos desejados, resultando num "perfil".
Conceitos básicos:
- Polietileno (PE): Um polímero termoplástico versátil e amplamente utilizado, conhecido pela sua resistência química, propriedades de isolamento elétrico, baixo custo e facilidade de processamento. Existe em várias densidades, cada uma oferecendo propriedades diferentes.
- Perfil: Um produto de extrusão com uma secção transversal constante ao longo do seu comprimento. Os exemplos incluem formas em L, canais em U, secções em T, tubos, barras ou geometrias altamente complexas e únicas.
- Extrusão: Processo de fabrico em que um material é empurrado através de uma matriz com a secção transversal desejada.
- Morrer: Uma ferramenta especializada, normalmente feita de aço endurecido, com uma abertura maquinada para o negativo da forma de perfil desejada. É o coração do processo de extrusão de perfis.
- Extrusora: A máquina que funde a resina plástica e a força através da matriz. É normalmente constituída por uma tremonha (para entrada da matéria-prima), um cilindro aquecido, um parafuso rotativo (ou parafusos) e um sistema de acionamento.
- Calibração/dimensionamento: Processos pós-extrusão que garantem que o perfil cumpre especificações dimensionais precisas à medida que arrefece e solidifica.
- Termoplástico: Um tipo de polímero que se torna moldável a uma determinada temperatura elevada e solidifica após arrefecimento. Os termoplásticos podem ser fundidos e moldados repetidamente.
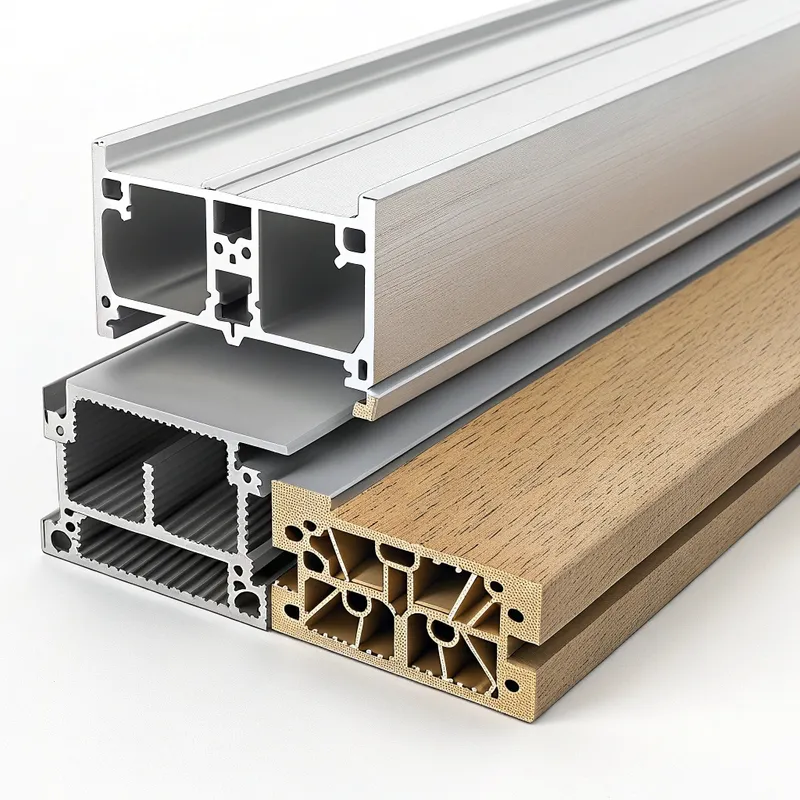
Classificação e tipo: Compreender as variedades de perfis PE
Os perfis PE personalizados podem ser classificados com base em vários factores, incluindo o tipo de resina de polietileno utilizada, a complexidade da forma do perfil e a área de aplicação pretendida.
1. Classificação com base no tipo de material de polietileno (PE):
Os diferentes tipos de polietileno oferecem um espetro de propriedades, tornando-os adequados para diversas aplicações:
① Perfis de polietileno de baixa densidade (LDPE):
- Caraterísticas: Suave, flexível, boa tenacidade, excelente resistência química, baixo ponto de fusão, boa processabilidade.
- Utilizações comuns: Tubos flexíveis, películas e componentes de embalagem, juntas, garrafas de compressão, isolamento de fios e cabos.
② Perfis de polietileno linear de baixa densidade (LLDPE):
- Caraterísticas: Maior resistência à tração, resistência ao impacto e resistência à perfuração em comparação com o LDPE. Oferece boa flexibilidade e resistência à fissuração por tensão.
- Utilizações comuns: Geomembranas, revestimentos, tubos flexíveis que exigem maior resistência, películas agrícolas.
③ Perfis de polietileno de média densidade (MDPE):
- Caraterísticas: Propriedades intermédias entre o PEBD e o PEAD. Boa resistência ao choque e à queda, melhor resistência à fissuração por tensão do que o PEAD.
- Utilizações comuns: Tubos e acessórios de gás, sacos, película retrátil.
④ Perfis de polietileno de alta densidade (HDPE):
- Caraterísticas: Mais rígido, mais forte e mais resistente à abrasão do que o LDPE. Excelente resistência química, boa resistência ao impacto mesmo a baixas temperaturas, baixa absorção de humidade.
- Utilizações comuns: Tubos (água, esgotos, industriais), recipientes para produtos químicos, tábuas de corte, tiras de desgaste, componentes para automóveis, componentes para barcos.
⑤ Perfis de polietileno de peso molecular ultra-elevado (UHMWPE):
- Caraterísticas: Resistência extremamente elevada à abrasão, coeficiente de atrito muito baixo, elevada resistência ao impacto, boa resistência química. Mais difícil de extrudir do que outros tipos de PE.
- Utilizações comuns: Calhas de guia, tiras de desgaste para transportadores, rolamentos, implantes médicos (graus específicos), revestimentos de calhas.
⑥ Perfis de polietileno reticulado (XLPE/PEX):
- Caraterísticas: Propriedades melhoradas, como melhor desempenho a altas temperaturas, força e resistência química, devido à reticulação das cadeias de polímeros. A extrusão é frequentemente seguida de um processo de reticulação pós-extrusão.
- Utilizações comuns: tubos de água quente (tubos PEX), tubos resistentes a produtos químicos, isolamento de cabos eléctricos.
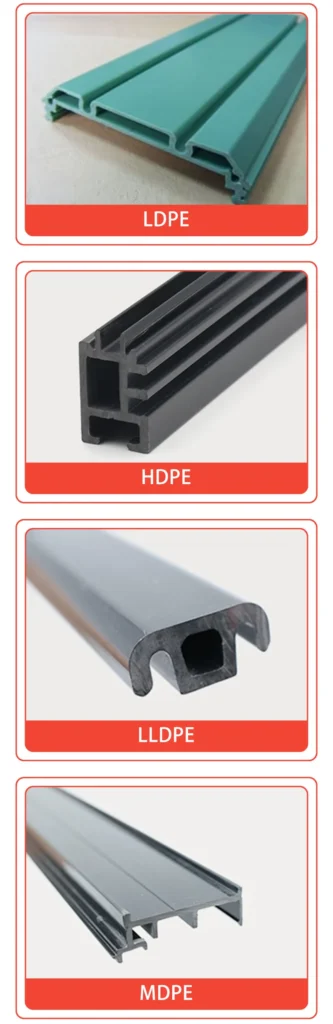
2. Classificação baseada na complexidade/forma do perfil:
① Perfis simples: Estes têm secções transversais geométricas básicas.
- Exemplos: Varões maciços, tubos ocos, tiras planas, barras quadradas, ângulos em L, canais em C.
② Perfis complexos: Estas envolvem geometrias complexas, múltiplas cavidades, espessuras de parede variáveis ou caraterísticas que requerem uma conceção avançada da matriz.
- Exemplos: Tubos multi-lúmenes, vidros de janelas, juntas personalizadas com caraterísticas pormenorizadas, perfis com dobradiças integradas.
③ Perfis co-extrudidos: São fabricados através da extrusão de dois ou mais materiais diferentes (ou cores do mesmo material) simultaneamente através de uma única matriz.
- Exemplos: Perfil de PE rígido com um lábio de vedação de PE flexível, um perfil com uma camada de cobertura colorida sobre um material de base, tubagem multicamada.
3. Classificação com base na área de aplicação geral:
Embora as aplicações pormenorizadas sejam discutidas mais adiante, uma classificação geral inclui:
- Perfis de construção: Utilizados na construção civil e em infra-estruturas.
- Perfis de embalagem: Utilizados para proteção e apresentação de produtos.
- Perfis para automóveis: Componentes para veículos.
- Perfis industriais: Peças para máquinas, equipamentos e infra-estruturas de instalações.
- Perfis de bens de consumo: Componentes para produtos de uso quotidiano.
- Perfis eléctricos: Para isolamento, condutas e gestão de cabos.
Cenários de aplicação/casos de utilização típicos para perfis PE personalizados
A versatilidade do polietileno, combinada com a adaptabilidade do processo de extrusão, permite que os perfis PE personalizados sirvam uma vasta gama de indústrias e aplicações.
1. Setor da construção:
① Componentes de janelas e portas: Contas de vidro, calafetagem, vedantes, componentes de caixilharia, espaçadores. (Frequentemente LDPE para flexibilidade, HDPE para peças mais rígidas).
② Tubagens e condutas: Tubos corrugados para drenagem, tubos lisos para água e gás (HDPE, MDPE), condutas eléctricas.
③ Protectores de bordos e guarnições: Proteção de cantos de paredes, mobiliário ou equipamento durante a construção ou em produtos acabados.
④ Juntas de dilatação e paragens de água: Vedação de fendas em estruturas de betão.
⑤ Componentes de decks e guarda-corpos: Alguns decks em compósito incorporam PE, e os perfis de PE puro podem ser utilizados para grades ou enchimento.
2. Soluções de embalagem:
① Tiras de vedação e fechos: Para sacos e contentores, que proporcionam vedações herméticas ou invioláveis. (LDPE, LLDPE).
② Bordadura de proteção e estendal: Amortecimento e proteção das mercadorias durante o transporte.
③ Componentes do ecrã: Molduras de exposição para pontos de venda, canais para sinalética.
④ Tubos para embalagem: Para cosméticos, adesivos industriais ou produtos alimentares.
3. Setor automóvel:
① Vedantes e juntas: Vedantes de janelas, vedantes de portas, vedantes contra intempéries. (Frequentemente TPE co-extrudido com PE, ou graus especializados de PE).
② Guarnições e molduras: Peças de remate decorativas ou funcionais, interiores e exteriores.
③ Tubagem: Para a transferência de fluidos (líquido de lavagem do para-brisas, drenagem do sistema AVAC), cablagens. (HDPE, MDPE).
④ Protectores de impacto e componentes do para-choques: Componentes de absorção de impactos menores.
⑤ Condutas de cabos e gestão de fios: Proteção da cablagem eléctrica.
4. Indústria e fabrico:
① Componentes do transportador: Tiras de desgaste, calhas de guia (especialmente UHMWPE pelo seu baixo atrito e elevada resistência ao desgaste), guias de corrente.
② Revestimentos de cisternas e revestimentos de calhas: Proteção de reservatórios contra produtos químicos corrosivos ou garantia de um fluxo suave em calhas de manuseamento de materiais (HDPE, UHMWPE).
③ Protectores de máquinas e barreiras de segurança: Protecções leves e resistentes ao impacto.
④ Sistemas de gestão de cabos: Condutas, canais e tubos para organizar e proteger os cabos.
⑤ Rolos e chumaceiras: (UHMWPE) para aplicações de baixa carga.
5. Bens de consumo:
① Borda e guarnição de móveis: Bordos decorativos e protectores para mesas, prateleiras.
② Componentes de brinquedos: Peças seguras, duradouras e coloridas para brinquedos.
③ Artigos de desporto: Componentes para esquis, pranchas de snowboard (camadas de base), equipamento de proteção.
④ Produtos hortícolas: Estacas para plantas, treliças, bordaduras para canteiros de jardim.
6. Eletricidade e eletrónica:
① Revestimento e isolamento do cabo: Isolamento primário ou bainha protetora exterior para fios e cabos eléctricos. (LDPE, HDPE, XLPE).
② Conduta eléctrica: Proteção da cablagem eléctrica em edifícios e instalações industriais.
③ Isolamento do barramento: Perfis de isolamento para sistemas de distribuição eléctrica.
7. Medicina e cuidados de saúde (utilizando PE específico de grau médico):
① Tubagem: Para a transferência de fluidos, cateteres (embora muitas vezes sejam utilizados polímeros mais especializados ou silicone para dispositivos de internamento). O PE é comum para tubagens não críticas.
② Conectores e acessórios: Componentes extrudidos simples.
8. Agricultura e aquicultura:
① Tubagem de irrigação e linhas de gotejamento: (LDPE, LLDPE) para uma distribuição eficiente da água.
② Perfis de estufas: Componentes para estruturas de estufas, perfis de fixação de películas.
③ Componentes da rede e da gaiola: Para piscicultura ou proteção das culturas.
Comparação das vantagens e desvantagens dos perfis PE personalizados
Como qualquer combinação de material e processo, os perfis PE personalizados oferecem um conjunto distinto de vantagens e limitações.
1. Vantagens dos perfis PE personalizados:
- Custo-eficácia: As resinas de polietileno encontram-se geralmente entre os plásticos de base mais baratos, tornando os perfis de PE uma escolha económica para muitas aplicações. O próprio processo de extrusão também é eficiente para a produção de grandes volumes de comprimentos contínuos.
- Versatilidade: A disponibilidade de diferentes tipos de PE (LDPE, HDPE, UHMWPE, etc.) permite obter uma vasta gama de propriedades (flexibilidade, rigidez, resistência ao desgaste).
- Excelente resistência química: O PE é altamente resistente a um amplo espetro de ácidos, bases, solventes e outros produtos químicos, o que o torna adequado para ambientes agressivos.
- Bom isolamento elétrico: O PE possui uma elevada resistência dieléctrica e resistividade volumétrica, o que o torna um material ideal para o isolamento elétrico e o revestimento de cabos.
- Coeficiente de atrito baixo: O HDPE e especialmente o UHMWPE apresentam um atrito muito baixo, o que os torna excelentes para aplicações de deslizamento, como faixas de desgaste e calhas de guia.
- Resistência à humidade: O PE tem uma absorção de água muito baixa, garantindo a estabilidade dimensional e a retenção de propriedades em condições húmidas ou molhadas.
- Facilidade de processamento: O PE tem geralmente boas caraterísticas de fluxo de fusão, tornando-o relativamente fácil de extrudir em formas complexas.
- Leve: Os perfis PE são leves, reduzindo o consumo de material, os custos de transporte e facilitando o manuseamento e a instalação.
- Reciclabilidade: O polietileno é um termoplástico e é amplamente reciclado (códigos #2 para HDPE, #4 para LDPE/LLDPE), contribuindo para os esforços de sustentabilidade.
- Personalização: O aspeto "personalizado" significa que os perfis podem ser adaptados com precisão a formas, tamanhos e cores específicos e podem incorporar aditivos (estabilizadores de UV, retardadores de chama, agentes anti-estáticos) para satisfazer as exigências da aplicação.
- Boa resistência ao impacto: O PEAD, em particular, oferece uma boa resistência ao impacto, mesmo a baixas temperaturas.
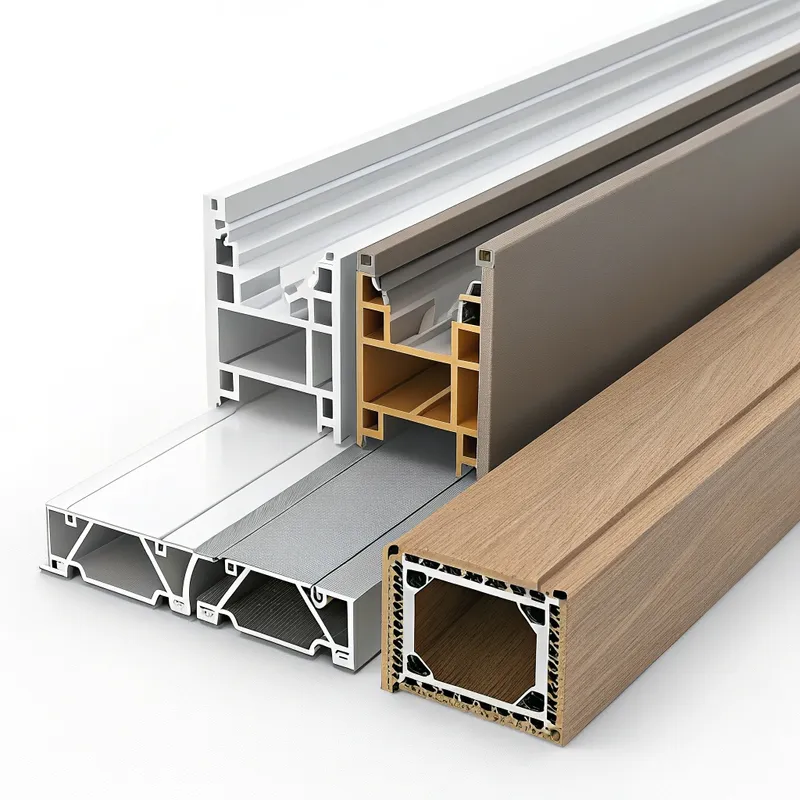
2. Desvantagens dos perfis PE personalizados:
- Menor resistência e rigidez (em comparação com plásticos de engenharia ou metais): Os perfis de PE não são normalmente adequados para aplicações de suporte de cargas estruturais elevadas, onde materiais como o aço, o alumínio ou os plásticos de engenharia (por exemplo, policarbonato, nylon) seriam preferidos.
- Resistência limitada à temperatura: Os tipos de PE padrão têm pontos de fusão e temperaturas de serviço relativamente baixos (normalmente até 60-80°C para uso contínuo, embora alguns tipos como XLPE ou UHMWPE possam tolerar um pouco mais). Não são adequados para ambientes de alta temperatura.
- Suscetibilidade à degradação por UV: O PE não estabilizado pode degradar-se quando exposto à luz solar prolongada (radiação UV), provocando fragilidade e descoloração. Os estabilizadores UV devem ser adicionados para aplicações no exterior.
- Potencial de fissuração por stress ambiental (ESC): Alguns tipos de PE podem ser susceptíveis de fissurar quando expostos a produtos químicos específicos (por exemplo, detergentes, álcoois) sob tensão. A seleção do material é fundamental para atenuar este problema.
- Fraca aderência e capacidade de impressão: A superfície cerosa e não polar do PE dificulta a colagem com adesivos ou a impressão sem tratamentos de superfície especializados (por exemplo, corona, chama, tratamento de plasma).
- Inflamabilidade: O PE é combustível e arderá se não forem incorporados aditivos retardadores de chama, o que pode afetar outras propriedades e o custo.
- Custos de ferramentas: O custo inicial de conceção e fabrico de uma matriz de extrusão personalizada pode ser significativo, especialmente para perfis complexos. Este custo é geralmente amortizado ao longo do volume de produção.
- Expansão térmica: O PE tem um coeficiente de expansão térmica relativamente elevado, o que significa que se expandirá e contrairá significativamente com as alterações de temperatura. Este facto deve ser tido em conta na conceção, especialmente para perfis ou conjuntos longos.
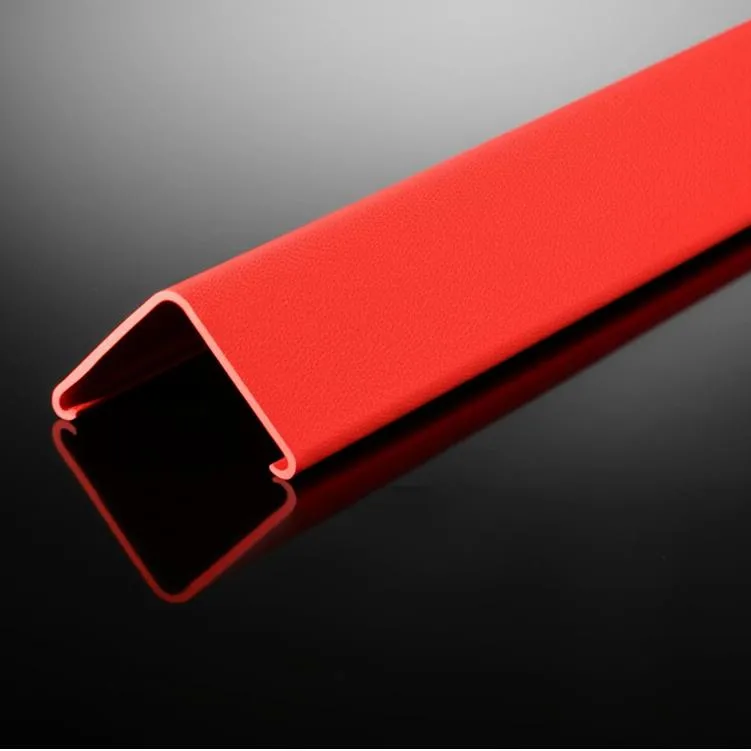
3. Breve comparação com outras tecnologias/métodos conexos:
① vs. PVC (Polyvinyl Chloride) Perfis:
- PE: geralmente mais flexível (LDPE), melhor resistência química a certas substâncias, melhor impacto a baixa temperatura.
- PVC: Pode ser mais rígido (uPVC), inerentemente retardador de chama, boa resistência às intempéries, frequentemente mais fácil de colar.
② vs. Extrusão de alumínio:
- PE: Menor custo, menor peso, isolante elétrico, resistente à corrosão sem acabamento.
- Alumínio: Muito maior resistência e rigidez, maior resistência à temperatura, melhor estabilidade dimensional, condutor.
③ vs. Moldagem por Injeção:
- Extrusão de PE: Ideal para comprimentos contínuos de secção transversal constante, menor custo de ferramentas para perfis simples, elevadas taxas de produção para peças lineares.
- Moldagem por injeção: Adequado para produzir peças tridimensionais discretas e frequentemente complexas. Custos de ferramentas mais elevados, mas pode produzir caraterísticas complexas que não são possíveis com a extrusão. Se forem necessárias peças PE curtas e discretas com geometria 3D complexa, a moldagem por injeção é preferível ao corte de perfis extrudidos.
④ vs. Extrusão de silicone:
- PE: Custo mais baixo, perfil de resistência química diferente, gama de temperaturas mais baixa.
- Silicone: Gama de temperaturas muito mais alargada (alta e baixa), excelente flexibilidade e elasticidade, biocompatibilidade para aplicações médicas, custo mais elevado. A extrusão de silicone é comum para vedantes e tubos que requerem estas propriedades.
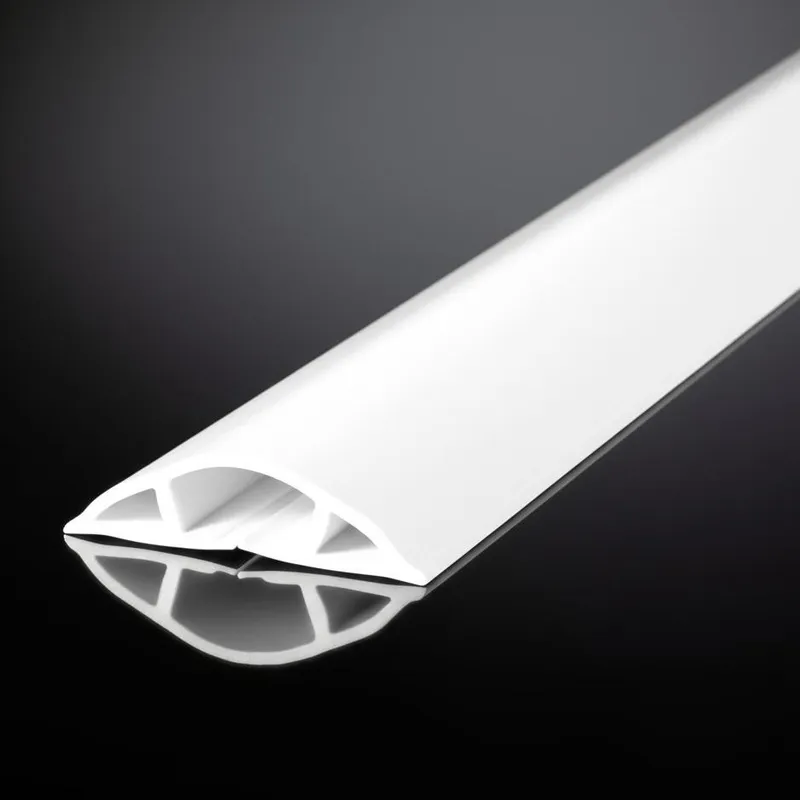
Principais caraterísticas do PE (relevantes para a extrusão e perfis)
As propriedades do polietileno são fundamentais para o seu desempenho, tanto durante a extrusão como na aplicação final.
1. Índice de fluxo de fusão (MFI) / Caudal de fusão (MFR):
- Descrição: Medida da facilidade de escoamento do plástico fundido. É expressa como o peso do polímero (em gramas) que flui em 10 minutos através de um capilar de diâmetro e comprimento específicos por uma pressão aplicada através de pesos gravimétricos alternativos prescritos para temperaturas alternativas prescritas.
- Significado: Crucial para a extrudabilidade. Um MFI mais elevado significa geralmente um fluxo mais fácil, mas potencialmente uma menor resistência na peça final. Os tipos de extrusão têm normalmente um MFI mais baixo do que os tipos de moldagem por injeção para uma melhor resistência à fusão.
2. Densidade:
- Descrição: Massa por unidade de volume. O PE é classificado pela sua densidade (LDPE, MDPE, HDPE).
- Significado: Influencia diretamente a rigidez, a dureza, a resistência à tração, a resistência química e o ponto de fusão. Uma densidade mais elevada significa geralmente uma maior rigidez e resistência.
3. Peso molecular (MW) e distribuição do peso molecular (MWD):
- Descrição: MW refere-se à massa média de uma cadeia de polímero. MWD descreve a gama de pesos moleculares dentro do polímero.
- Significado: Um MW mais elevado melhora geralmente a tenacidade, a resistência ao impacto e a resistência à fissuração por tensão, mas torna o processamento mais difícil (maior viscosidade). Um MWD estreito pode levar a propriedades e comportamento de processamento mais uniformes. O UHMWPE tem um peso molecular excecionalmente elevado.
4. Cristalinidade:
- Descrição: O grau de ordem estrutural num polímero. O PE é um polímero semi-cristalino.
- Significado: Afecta a densidade, a rigidez, a resistência à tração, a opacidade (maior cristalinidade = mais opaco) e a retração. A taxa de arrefecimento durante a extrusão influencia o grau de cristalinidade.
5. Resistência à tração e alongamento na rutura:
- Descrição: A resistência à tração é a tensão máxima que um material pode suportar ao ser esticado ou puxado antes de se romper. O alongamento é a medida de quanto pode ser esticado antes de quebrar.
- Significado: Propriedades mecânicas essenciais que indicam a capacidade do perfil para resistir a forças de tração.
6. Resistência ao impacto (por exemplo, Izod ou Charpy):
- Descrição: A capacidade do material para resistir a uma carga ou choque súbito.
- Significado: Importante para aplicações em que o perfil pode sofrer impactos. O HDPE e o UHMWPE têm uma excelente resistência ao impacto.
7. Dureza (por exemplo, Shore D):
- Descrição: Resistência do material à indentação permanente ou ao risco.
- Significado: Indica a durabilidade da superfície. O PEAD é mais duro do que o PEBD.
8. Propriedades térmicas:
- Ponto de fusão (Tm): Temperatura à qual as regiões cristalinas do PE fundem.
- Ponto de amolecimento Vicat / Temperatura de deflexão térmica (HDT): Indica a temperatura à qual o material começa a amolecer significativamente sob uma carga.
- Coeficiente de Expansão Térmica (CTE): Mede a mudança de tamanho por mudança de grau na temperatura. O PE tem um CTE relativamente elevado.
9. Propriedades eléctricas:
- Resistência dieléctrica: A força máxima do campo elétrico que o PE pode suportar sem se romper.
- Resistividade volumétrica: Uma medida da sua resistência à fuga de corrente através do seu corpo.
10. Resistência química:
- Descrição: Capacidade de resistir à degradação quando exposto a vários produtos químicos.
- Significado: O PE é geralmente excelente, mas a resistência específica varia consoante o tipo de PE e o produto químico. O PEAD é frequentemente mais resistente do que o PEBD.
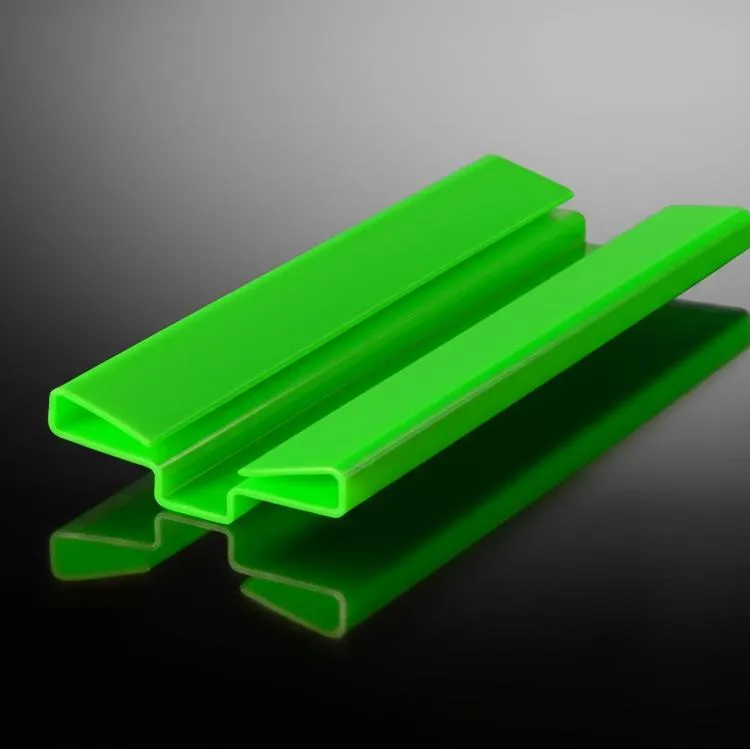
Processo central/fluxo/princípio de trabalho: Perfis PE
O processo de extrusão de plástico para perfis de PE é uma operação contínua que envolve várias fases-chave:
1. Manuseamento e preparação de materiais:
① Seleção da resina: Seleção do tipo de PE adequado (LDPE, HDPE, etc.) com base nos requisitos da aplicação. Aditivos como corantes, estabilizadores de UV, retardadores de chama, auxiliares de processamento ou cargas são frequentemente pré-compostos na resina ou adicionados como masterbatch.
② Secagem (se necessário): Embora o PE não seja altamente higroscópico (absorve pouca humidade), a humidade excessiva da superfície pode causar defeitos como vazios ou saliências no extrudado. A secagem pode ser necessária em condições de humidade ou para tipos específicos, embora seja menos crítica do que para plásticos como o nylon ou o PET.
③ Mistura: Se forem utilizados masterbatches ou componentes múltiplos, estes são cuidadosamente misturados antes de serem introduzidos na extrusora para garantir a homogeneidade.
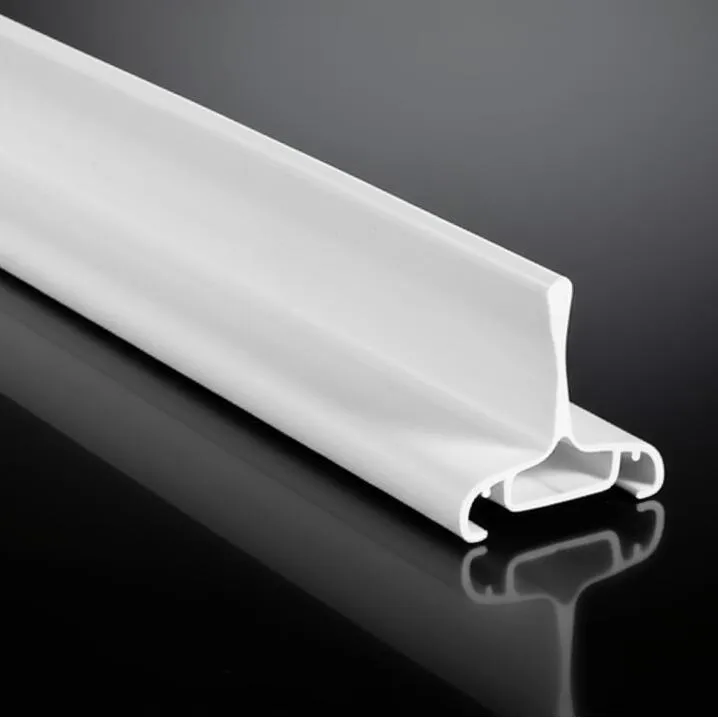
2. Extrusão:
① Alimentação: Os granulados (ou pó) de PE são alimentados por gravidade a partir de uma tremonha para o tambor da extrusora.
② Fusão, Mistura e bombagem: Isto ocorre dentro do barril da extrusora, principalmente por um parafuso rotativo (normalmente um parafuso único para perfis PE).
- Zona de alimentação: O parafuso recolhe os granulados da tremonha e transporta-os para o barril aquecido.
- Zona de transição (zona de compressão): A profundidade do canal do parafuso diminui, comprimindo o material. O calor de fricção da rotação do parafuso (aquecimento por cisalhamento) e os aquecedores externos no cilindro derretem o PE.
- Zona de dosagem: A parte mais superficial do parafuso, concebida para homogeneizar o polímero fundido, assegurar uma temperatura consistente e criar pressão suficiente para forçar a fusão através da matriz.
③ Perfil de temperatura: O tambor está equipado com várias zonas de aquecimento/arrefecimento, permitindo um controlo preciso do perfil de temperatura ao longo do seu comprimento, crucial para uma fusão adequada e para a qualidade da fusão.
④ Design do parafuso: Os principais parâmetros incluem o rácio comprimento/diâmetro (L/D, normalmente 24:1 a 32:1 para PE), o rácio de compressão e a geometria específica do parafuso (por exemplo, elementos de mistura).
⑤ Conjunto de ecrãs e placa de rutura: Localizado entre a ponta do parafuso e a matriz. O conjunto de filtros (várias camadas de malha de arame) filtra os contaminantes e as partículas não fundidas. A placa separadora suporta o conjunto de filtros e ajuda a converter o fluxo em espiral da massa fundida do parafuso num fluxo mais linear. Ambos contribuem para aumentar a contrapressão, melhorando a homogeneidade da massa fundida.
3. Moldagem de matrizes:
① Forçando a matriz: O PE fundido homogeneizado e pressurizado é forçado através da matriz de extrusão concebida à medida. O orifício da matriz tem a forma negativa do perfil desejado.
② Desenho da matriz: Este é um aspeto crítico e complexo. Os projectistas devem ter em conta:
- Caraterísticas do fluxo de material: Assegurar um fluxo uniforme em todas as partes do perfil para evitar distorções.
- Comprimento do terreno: O comprimento da secção paralela na saída da matriz, que influencia o acabamento da superfície e a estabilidade dimensional.
- Estiramento: O estiramento do extrudado à medida que é puxado para fora da matriz. A abertura da matriz é normalmente feita ligeiramente maior do que as dimensões finais do perfil para ter em conta este facto.
- Inchaço da matriz: A tendência do extrudado para se expandir na secção transversal à medida que sai da matriz devido ao relaxamento das tensões moleculares. Isto também deve ser compensado na conceção da matriz.
③ As matrizes podem ser fabricadas a partir de vários aços, muitas vezes endurecidos e polidos para uma maior longevidade e superfícies de perfil lisas.
- Comprimento do terreno: O comprimento da secção paralela na saída da matriz, que influencia o acabamento da superfície e a estabilidade dimensional.
- Estiramento: O estiramento do extrudado à medida que é puxado para fora da matriz. A abertura da matriz é normalmente feita ligeiramente maior do que as dimensões finais do perfil para ter em conta este facto.
- Inchaço da matriz: A tendência do extrudado para se expandir na secção transversal à medida que sai da matriz devido ao relaxamento das tensões moleculares. Isto também deve ser compensado na conceção da matriz.
③ As matrizes podem ser fabricadas a partir de vários aços, muitas vezes endurecidos e polidos para uma maior longevidade e superfícies de perfil lisas.
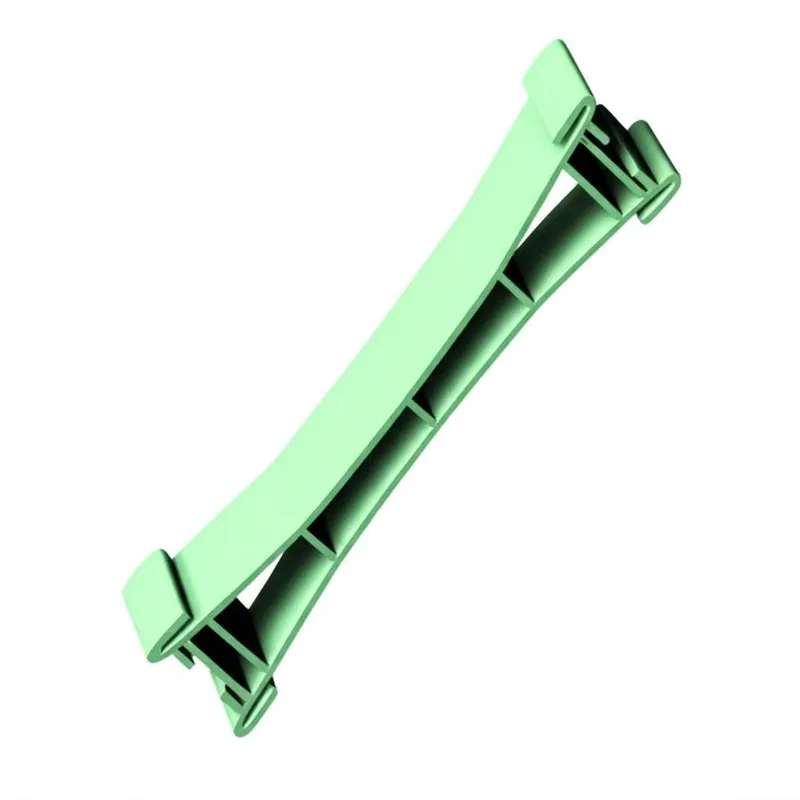
4. Dimensionamento e calibração:
① Objetivo: Para arrefecer o extrudado e solidificá-lo na forma e dimensões exactas desejadas. O perfil ainda está quente e maleável quando sai da matriz.
② Métodos:
- Banhos de água: O perfil passa por um ou mais tanques cheios de água refrigerada ou à temperatura ambiente.
- Arrefecimento por ar: Para alguns perfis ou em conjunto com o arrefecimento a água, podem ser utilizados fluxos de ar.
- Rolos refrigerados: Utilizados para folhas ou películas, menos comuns para perfis complexos.
③ A taxa de arrefecimento controlada é importante para gerir a cristalinidade, minimizar as tensões internas e evitar deformações.
5. Arrefecimento:
① Objetivo: Para solidificar completamente o perfil e reduzir a sua temperatura de manuseamento.
② Métodos:
- Banhos de água: O perfil passa por um ou mais tanques cheios de água refrigerada ou à temperatura ambiente.
- Arrefecimento por ar: Para alguns perfis ou em conjunto com o arrefecimento a água, podem ser utilizados fluxos de ar.
- Rolos refrigerados: Utilizados para folhas ou películas, menos comuns para perfis complexos.
③ A taxa de arrefecimento controlada é importante para gerir a cristalinidade, minimizar as tensões internas e evitar deformações.
6. Puxar (Haul-Off):
① Objetivo: Para extrair o perfil da matriz e através do equipamento de calibragem e arrefecimento a uma velocidade constante.
② Equipamento: São comuns os extractores de lagarta (que utilizam duas ou mais correias móveis) ou os extractores de correia com grampos.
③ A velocidade do dispositivo de extração deve ser sincronizada com precisão com a taxa de saída da extrusora para manter dimensões de perfil consistentes e evitar a retirada excessiva ou a acumulação de material.
7. Acabamento em linha (opcional):
Dependendo dos requisitos, podem ser efectuadas várias operações em linha com o processo de extrusão:
- Corte em comprimento: Serras (de corte rápido, de deslocamento) ou cortadores para produzir comprimentos discretos.
- Impressão/marcação: Para marcas, números de peças ou especificações.
- Gravação em relevo: Criar superfícies texturadas.
- Aplicação de fita adesiva: Para perfis que necessitam de ser auto-adesivos.
- Perfuração: Criação de furos ou ranhuras.
- Bobinagem/enrolamento: Para perfis flexíveis como tubos ou pequenas juntas.
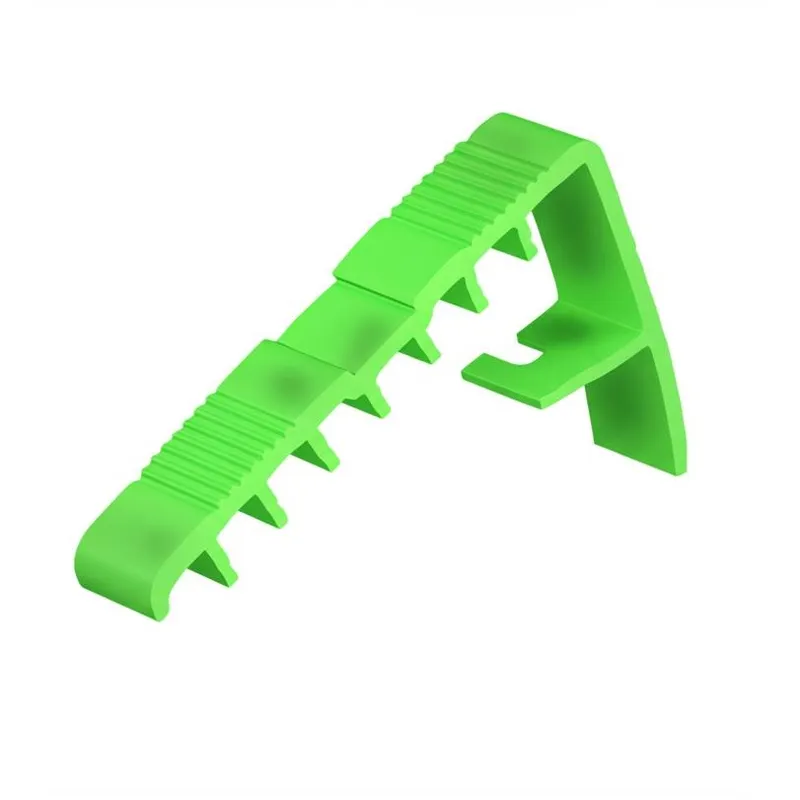
8. Controlo de qualidade e inspeção:
Durante todo o processo e nas peças acabadas, são efectuados controlos de qualidade:
- Medições dimensionais (com paquímetros, comparadores ópticos, medidores laser).
- Inspeção do acabamento da superfície (para defeitos como linhas de matriz, suavidade).
- Verificações da consistência da cor.
- Ensaio das propriedades mecânicas (se necessário, em peças de amostra).
Perfis de PE personalizados: O guia definitivo para a extrusão de plástico
Desbloqueie perfis PE personalizados com o nosso guia completo sobre extrusão de plástico. Saiba mais sobre os tipos de PE, aplicações, design, pormenores técnicos e melhores práticas.
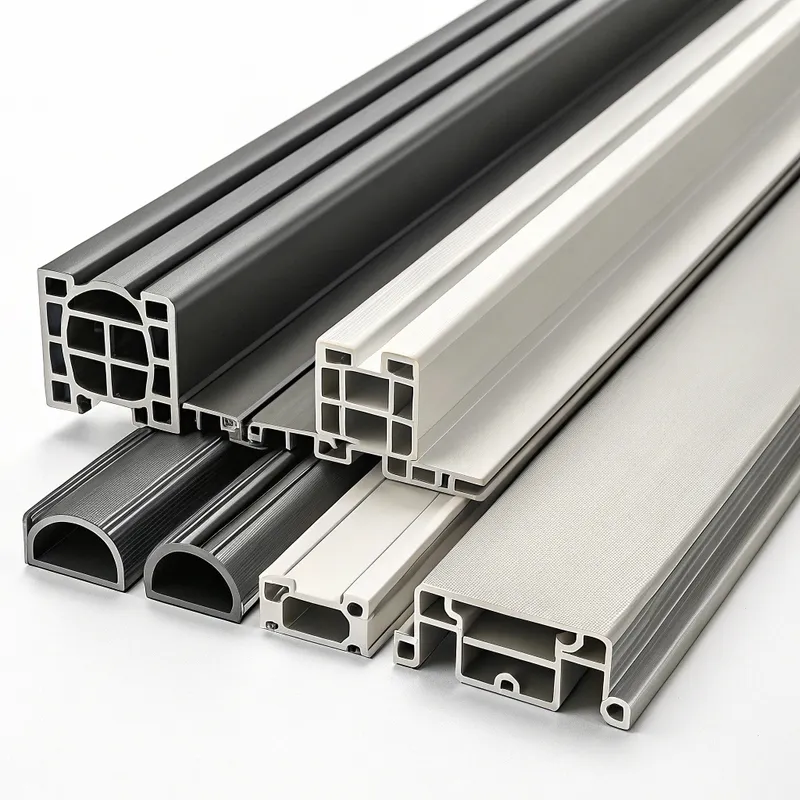
Guia para o fabrico de perfis de extrusão de PE personalizados
- Principais considerações sobre a extrusão de perfis PE personalizados
- Guia de conceção/implementação/melhores práticas para perfis PE personalizados
- Problemas comuns e soluções na extrusão de perfis PE
- Formulações avançadas de PE e perfis de especialidade
- Métodos de controlo de qualidade e normas relevantes para perfis PE
- Sustentabilidade na produção de perfis PE personalizados
Principais considerações sobre a extrusão de perfis PE personalizados
Vários factores são críticos para o sucesso da conceção, produção e utilização de perfis PE personalizados:
1. Seleção do material:
- Corresponder o tipo específico de PE (LDPE, LLDPE, MDPE, HDPE, UHMWPE) e quaisquer aditivos necessários (estabilizadores UV, corantes, retardadores de chama, auxiliares de processamento) aos requisitos mecânicos, químicos, térmicos, eléctricos e ambientais da aplicação.
- Considerando as caraterísticas do fluxo da massa fundida para a extrudabilidade da complexidade do perfil desejado.
2. Complexidade da conceção do perfil:
- Desenhos altamente complexos, paredes muito finas, cantos internos afiados ou grandes variações na espessura da parede podem ser difíceis de extrudir de forma consistente.
- Os desenhos mais simples e uniformes conduzem geralmente a uma maior estabilidade do processo e a menores custos de ferramentas.
3. Conceção e fabrico de matrizes:
- Este é, sem dúvida, o elemento mais crítico. A conceção adequada da matriz assegura um fluxo de material equilibrado, uma forma de perfil correta, um bom acabamento da superfície e tem em conta a dilatação e a redução da matriz.
- Os projectistas e fabricantes de ferramentas experientes são essenciais para perfis complexos.
- A escolha do material para a matriz (por exemplo, aço D2 para ferramentas, aço inoxidável) e o acabamento da superfície (por exemplo, polimento, revestimentos) têm impacto na vida útil da matriz e na qualidade do perfil.
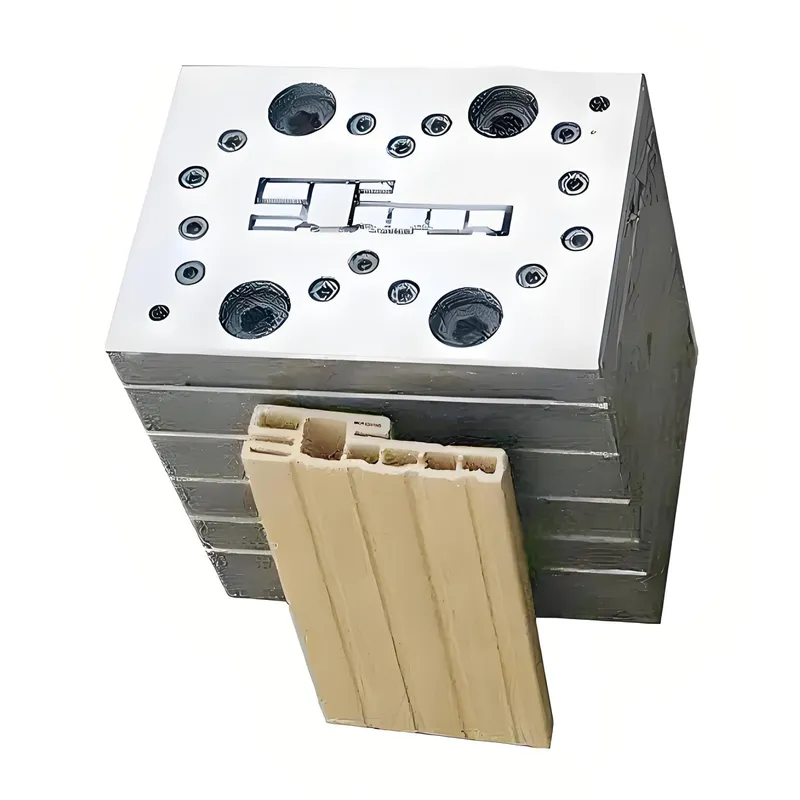
3. Parâmetros de processamento:
- O controlo preciso das temperaturas do cilindro da extrusora, da velocidade do parafuso, da temperatura da massa fundida, da temperatura da matriz, da velocidade do extrator e das condições de arrefecimento é vital.
- Estes parâmetros são interdependentes e devem ser optimizados para cada tipo específico de PE e conceção de perfil.
4. Técnicas de arrefecimento e dimensionamento:
- A eficiência e a uniformidade do arrefecimento têm um impacto significativo na estabilidade dimensional, nas tensões internas, na cristalinidade e no potencial de deformação.
- A conceção correta da ferramenta de dimensionamento e os níveis de vácuo (se utilizados) são cruciais para obter tolerâncias apertadas.
5. Tolerâncias:
- Compreender as tolerâncias dimensionais possíveis para a extrusão de PE. Estas dependem do material, da dimensão e complexidade do perfil e do controlo do processo. As normas da indústria (por exemplo, do Plastic Pipe Institute ou de associações de extrusão personalizadas) podem fornecer orientações.
- As tolerâncias demasiado apertadas e não funcionais aumentam os custos e as dificuldades.
6. Encolhimento:
- O polietileno, especialmente o HDPE, tem uma taxa de contração relativamente elevada e não uniforme à medida que arrefece do estado fundido para o estado sólido. Este facto deve ser previsto com precisão e compensado na conceção da matriz.
7. Factores de custo:
- Custo da resina: Varia consoante o grau de PE e os aditivos.
- Custo das ferramentas: Conceção e fabrico de matrizes, mais ferramentas de dimensionamento. Pode ser substancial, mas é um custo único amortizado pelo volume da peça.
- Volume de produção: Volumes mais elevados conduzem geralmente a custos unitários mais baixos.
- Complexidade: Perfis mais complexos requerem ferramentas mais sofisticadas e taxas de produção mais lentas, aumentando o custo.
- Operações secundárias: Todas as etapas de acabamento pós-extrusão aumentam o custo.
8. Requisitos das operações secundárias:
- Se o perfil exigir corte, perfuração, puncionamento, impressão, montagem ou outras operações a jusante, estas devem ser consideradas durante a fase inicial de conceção para garantir a compatibilidade.
9. Considerações ambientais:
- O PE é reciclável, mas é necessário dispor de infra-estruturas de recolha e de reprocessamento.
- Consumo de energia do processo de extrusão.
- Utilização de aditivos e seu impacto ambiental.
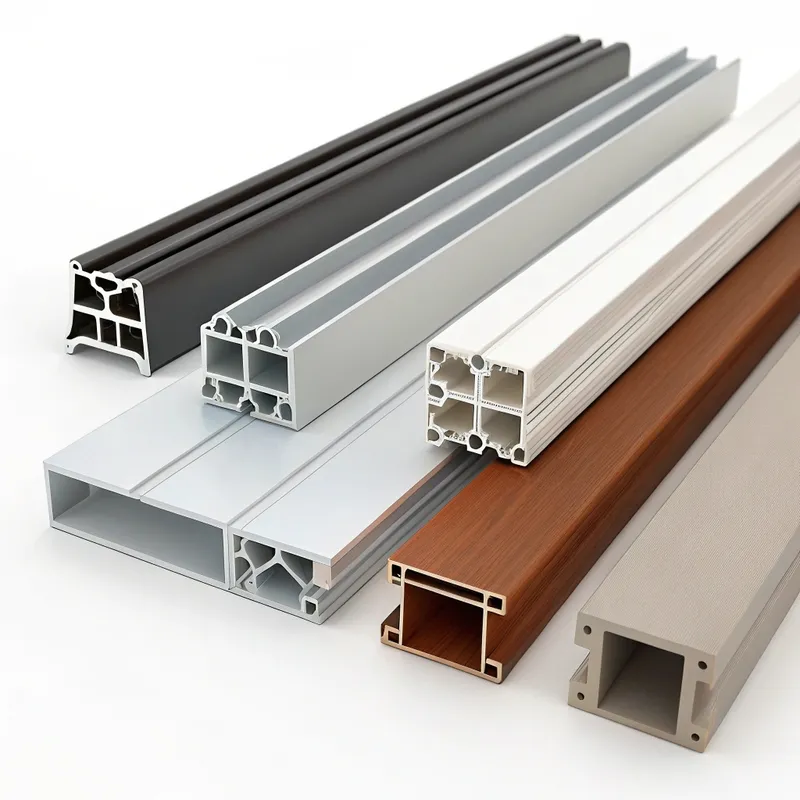
Guia de conceção/implementação/melhores práticas para perfis PE personalizados
O cumprimento destas orientações pode conduzir a projectos de perfis PE personalizados mais bem sucedidos e rentáveis:
1. Envolvimento precoce do fornecedor (ESI):
Colabore com uma extrusora de PE personalizada experiente no início da fase de conceção. Os seus conhecimentos especializados na seleção de materiais, DFM (Design for Manufacturability para extrusão) e ferramentas podem evitar redesenhos dispendiosos e garantir a viabilidade.
2. Simplificar a conceção do perfil sempre que possível:
Evite caraterísticas desnecessariamente complexas, cantos internos afiados (utilize raios) e variações extremas ou abruptas na espessura da parede. Os projectos mais simples são mais fáceis de trabalhar, funcionam de forma mais consistente e são geralmente menos dispendiosos.
3. O objetivo é obter uma espessura de parede consistente:
Uma espessura uniforme da parede promove um fluxo uniforme do material, um arrefecimento uniforme, reduz as tensões internas e minimiza o empeno ou a distorção. Se for necessário variar as espessuras, as transições devem ser graduais.
4. Incorporar raios generosos:
Utilizar raios em todos os cantos internos e externos em vez de arestas vivas. Isto melhora o fluxo de material na matriz, reduz as concentrações de tensão na peça final e pode melhorar a vida útil da matriz.
5. Considerar a dinâmica do fluxo de materiais:
Conceber caraterísticas que promovam um fluxo equilibrado do plástico fundido através da matriz. Evitar secções grossas isoladas alimentadas por secções finas.
6. Especificar as tolerâncias realistas e funcionais:
Compreender as limitações do processo de extrusão de PE para o material escolhido e a complexidade do perfil. Especificar tolerâncias apertadas apenas em dimensões funcionais verdadeiramente críticas. O excesso de tolerância aumenta significativamente os custos.
7. Definir claramente todos os requisitos funcionais:
Fornecer à extrusora informações completas sobre a utilização final do perfil, incluindo:
- Dimensões e caraterísticas funcionais críticas.
- Propriedades mecânicas necessárias (rigidez, flexibilidade, resistência ao impacto).
- Ambiente de funcionamento (gama de temperaturas, exposição a produtos químicos, exposição aos raios UV).
- Requisitos estéticos (cor, acabamento da superfície, transparência).
- Detalhes da montagem ou da peça de acoplamento.
8. Seleção de materiais com base na utilização final e não apenas no custo:
Embora o PE seja rentável, selecione o tipo (LDPE, HDPE, etc.) e quaisquer aditivos com base nas exigências de desempenho da aplicação. Uma subespecificação pode levar a falhas prematuras.
9. Cuidado com a retração e a dilatação da matriz:
Embora seja principalmente da responsabilidade da extrusora compensar estes factores na conceção da matriz, os projectistas devem compreender que a abertura da matriz não será idêntica às dimensões da peça final.
10. Conceção para montagem e operações secundárias:
Se o perfil tiver de ser montado, soldado ou sujeito a outras operações, incorporar caraterísticas que facilitem estes processos (por exemplo, canais para fixadores, superfícies planas para colagem).
11. Investir na criação de protótipos para perfis complexos:
Para projectos novos ou complexos, a criação de ferramentas de protótipo (frequentemente mais simples e menos dispendiosas) pode validar o projeto, a escolha do material e a processabilidade antes de se comprometer com ferramentas de produção dispendiosas.
12. Comunicar a quantidade e as expectativas ao longo da vida:
O conhecimento do volume anual previsto e do ciclo de vida do produto ajuda a extrusora a otimizar o planeamento das ferramentas e da produção.
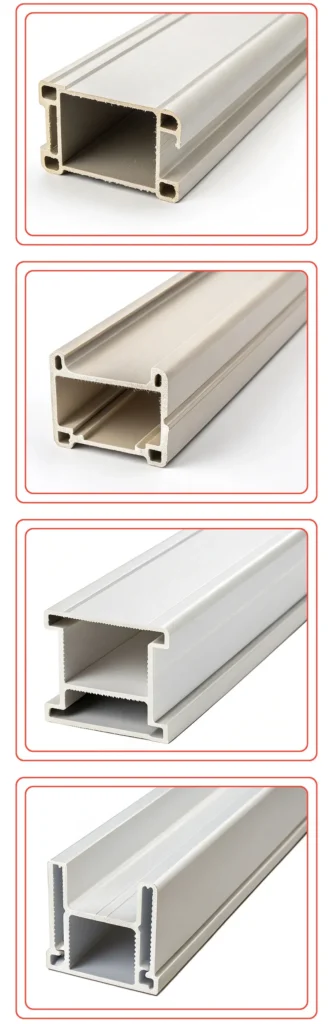
Problemas comuns e soluções na extrusão de perfis PE
Mesmo com um planeamento cuidadoso, podem surgir problemas durante a extrusão de perfis PE. Eis alguns problemas comuns e as suas potenciais soluções:
1. Instabilidade dimensional (empeno, arqueamento, torção):
- Problema: Taxas de arrefecimento desiguais, tensões internas devido à espessura não uniforme da parede, velocidade inconsistente do extrator, apoio insuficiente após a saída da matriz.
- Solução: Otimizar o arrefecimento (ajustar a temperatura da água, o caudal ou os padrões de pulverização), garantir uma espessura uniforme da parede na conceção, verificar a velocidade e a tensão consistentes do extrusor, fornecer um suporte adequado para o extrudado quente, ajustar as temperaturas da fusão ou da matriz, considerar o recozimento pós-extrusão para alívio das tensões.
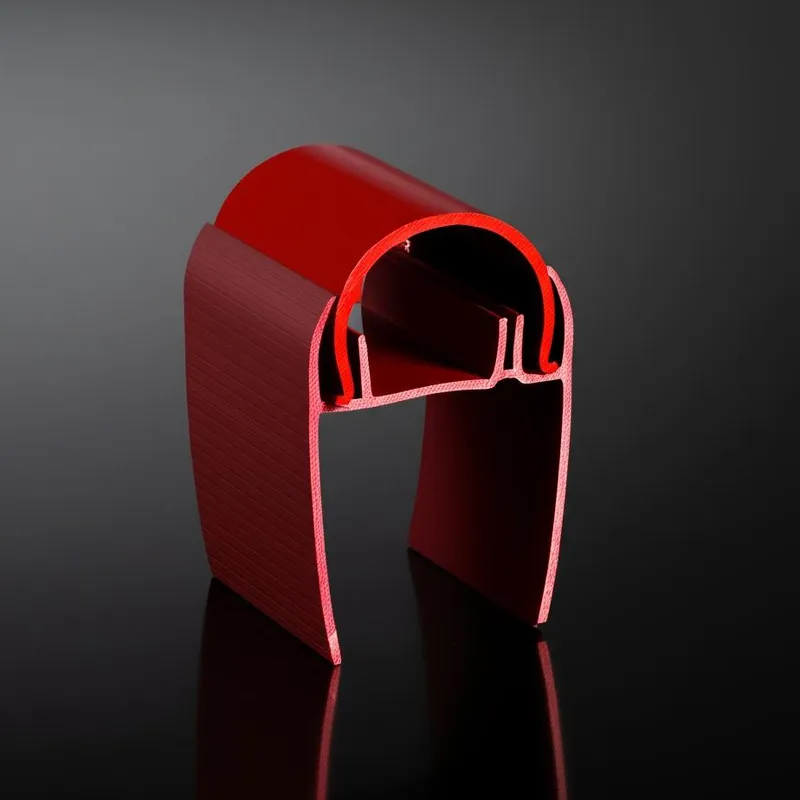
2. Defeitos de superfície:
① Linhas de matriz (estrias ao longo da direção de extrusão):
- Problema: Riscos ou imperfeições nas superfícies da matriz, material contaminado, acumulação de matriz.
- Solução: Polir ou reparar as superfícies da matriz, melhorar a filtragem da fusão, limpar a matriz regularmente.
② Pele de tubarão (superfície rugosa e mate com sulcos perpendiculares ao fluxo):
- Problema: Tensão excessiva na saída da matriz, frequentemente a taxas de produção mais elevadas. Fusão demasiado fria.
- Solução: Aumentar a temperatura da matriz/derretimento, utilizar auxiliares de processamento (por exemplo, fluoropolímeros), reduzir a taxa de produção, redesenhar a geometria da saída da matriz (por exemplo, aumentar o comprimento do terreno, chanfrar o lábio da matriz).
③ Fratura por fusão (distorção grosseiramente irregular ou helicoidal):
- Problema: Tensão de cisalhamento excessiva na matriz, fusão demasiado fria ou taxa de fluxo demasiado elevada para a geometria da matriz.
- Solução: Reduzir a taxa de produção, aumentar a temperatura da fusão/da matriz, redesenhar a matriz para um fluxo mais suave (por exemplo, entrada cónica), utilizar um tipo de PE de menor viscosidade, se possível.
3. Espessura de parede inconsistente:
- Problema: Fluxo desequilibrado no molde (má conceção do molde ou danos), sobretensão da extrusora, velocidade inconsistente do extrator, molde não centrado (para tubagem).
- Solução: Ajuste a matriz (por exemplo, parafusos de centragem para matrizes de tubos, limitadores para matrizes planas), investigue e corrija a causa do pico (ver abaixo), assegure um funcionamento consistente do extrator, inspeccione a matriz quanto a desgaste ou danos.
4. Bolhas, vazios ou porosidade no perfil:
- Problema: Humidade na resina (menos comum no PE, mas possível), ar retido, degradação do polímero que liberta voláteis, contaminantes.
- Solução: Assegurar que a resina está seca, se necessário, otimizar a conceção do parafuso para desvolatilização (se aplicável), verificar a existência de fugas de ar na tremonha/garganta de alimentação, reduzir a temperatura de fusão se houver suspeita de degradação, melhorar a filtragem da fusão.
5. Fragilidade ou baixa resistência ao impacto:
- Problema: Degradação do polímero (calor excessivo ou cisalhamento), tipo de material incorreto, arrefecimento insuficiente antes do manuseamento/esforço, demasiada trituração.
- Solução: Otimizar o perfil de temperatura e a velocidade do parafuso para reduzir o cisalhamento, verificar se é utilizado o tipo correto de PE, assegurar um arrefecimento adequado, limitar a percentagem de material reciclado.
6. Riscas de cor ou cor inconsistente:
- Problema: Má dispersão do masterbatch de cor, suporte de masterbatch incompatível, mistura insuficiente na extrusora.
- Solução: Utilizar um masterbatch de alta qualidade com boa compatibilidade, aumentar a contrapressão para uma melhor mistura, utilizar um parafuso com melhores elementos de mistura, assegurar um rácio de descarga adequado do masterbatch.
7. Surgimento (saída pulsante ou instável da extrusora):
- Problema: Alimentação inconsistente de pellets (formação de pontes na tremonha, transporte deficiente de sólidos na zona de alimentação), perfil de temperatura incorreto (por exemplo, zona de alimentação demasiado quente), problemas de conceção do parafuso, parafuso/barril gasto.
- Solução: Verificar a tremonha quanto a problemas de fluxo, ajustar a temperatura da zona de alimentação (frequentemente mais fria ajuda), otimizar o perfil geral de temperatura, verificar o parafuso e o tambor quanto a desgaste, garantir propriedades consistentes do material.
8. Inchaço ou contração excessivos da matriz:
- Problema: Propriedade inerente ao material, condições de processamento incorrectas.
- Solução: A conceção da matriz é a principal preocupação, mas a otimização da temperatura de fusão e das taxas de arrefecimento pode ter alguma influência. Assegurar a consistência para obter resultados previsíveis.
Formulações avançadas de PE e perfis de especialidade
Embora os tipos de PE padrão cubram muitas aplicações, as exigências específicas de desempenho requerem formulações avançadas ou tipos de perfis especializados:
1. Perfis de espuma de PE:
① Descrição: Estes perfis incorporam um núcleo celular ou espumado, quer através de agentes de expansão químicos misturados com a resina, quer através de espumação física (injeção de gás como CO2 ou N2 na massa fundida). Isto resulta num perfil que é mais leve do que um perfil sólido com as mesmas dimensões.
② Propriedades: Consumo reduzido de material (poupança de custos), menor peso, melhor isolamento térmico e acústico, boas propriedades de amortecimento. A resistência mecânica é normalmente inferior à dos perfis maciços.
③ Aplicações: Embalagens de proteção (protectores de bordos, amortecedores), tiras de isolamento térmico, componentes estruturais leves (quando a elevada resistência não é fundamental), auxiliares de flutuação, acabamentos decorativos com um toque mais suave.
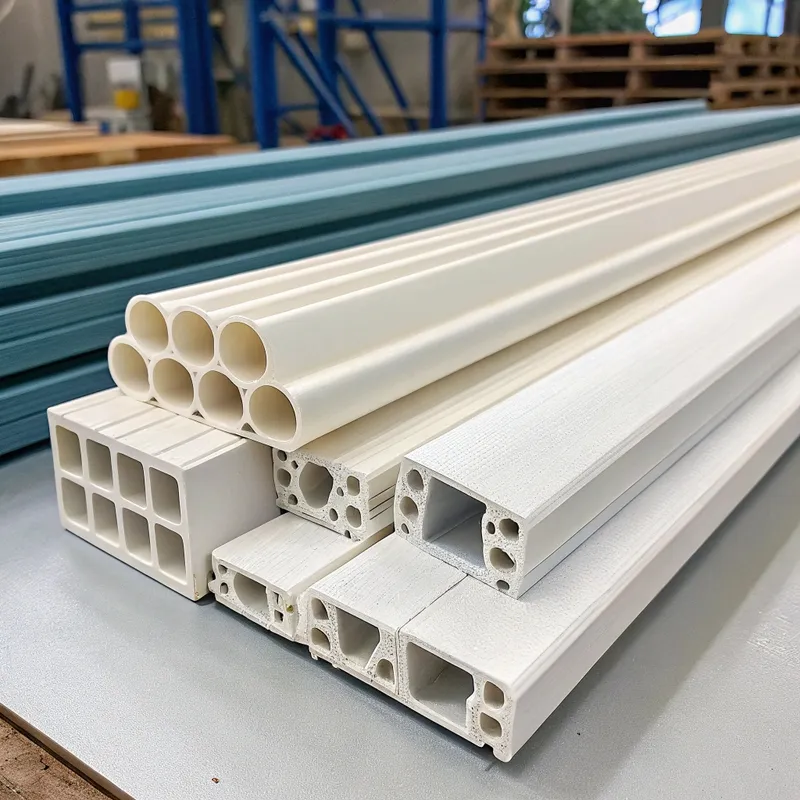
2. Perfis PE condutores/anti-estáticos:
① Descrição: O PE normal é um excelente isolante. Para aplicações que exijam a dissipação de eletricidade estática (por exemplo, no manuseamento de componentes electrónicos ou em ambientes explosivos), são incorporados na resina de PE cargas condutoras como o negro de carbono, fibras de carbono ou polímeros condutores inerentes (ICPs).
② Propriedades: Proporcionam um caminho controlado para a dissipação da carga estática, evitando danos causados por descargas electrostáticas (ESD) ou a atração de poeiras. Os valores da resistividade da superfície ou da resistividade do volume definem a sua eficácia (por exemplo, anti-estático: 10^9-10^12 ohms/sq; condutor: <10^6 ohms/sq).
③ Aplicações: Tabuleiros e canais para a manipulação de componentes electrónicos sensíveis, perfis para ambientes de sala limpa, componentes para equipamentos utilizados em atmosferas explosivas, peças de transporte na montagem de eletrónica.
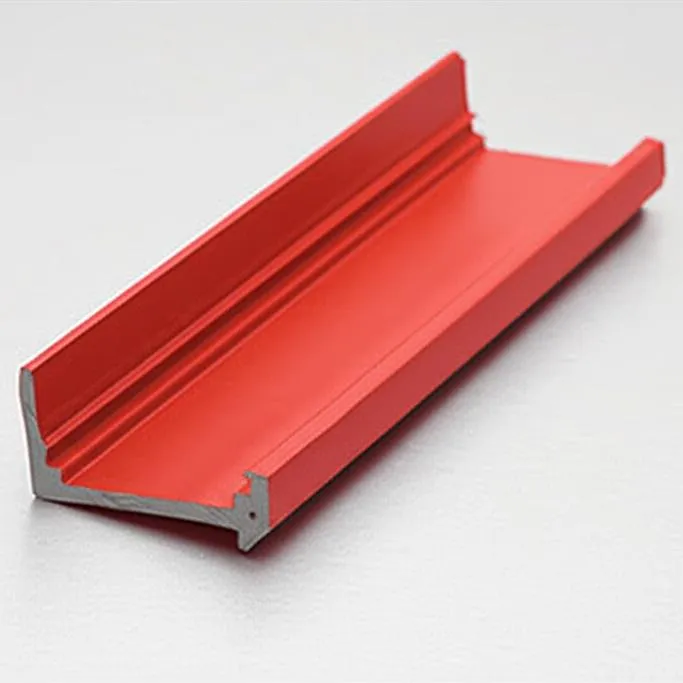
3. Perfis PE preenchidos:
① Descrição: Incorporação de cargas inorgânicas (por exemplo, carbonato de cálcio, talco, mica, fibras de vidro, farinha de madeira) na matriz de PE para modificar as suas propriedades.
② Propriedades:
- Carbonato de cálcio/Talco: Pode aumentar a rigidez, melhorar a estabilidade dimensional, reduzir o custo e melhorar a capacidade de impressão. Pode reduzir a resistência ao impacto.
- Fibras de vidro (curtas ou longas): Aumentam significativamente a resistência à tração, a rigidez e a temperatura de deflexão térmica. Podem tornar o material mais abrasivo para o equipamento de processamento.
- Farinha de madeira/fibras naturais (compósitos de madeira-plástico - WPC): Oferecem um aspeto e toque semelhantes aos da madeira e maior rigidez. Normalmente utilizado com PE para decks, vedações e perfis exteriores. Requer uma formulação cuidadosa para garantir uma boa ligação e resistência à humidade.
③ Aplicações: Componentes automóveis que requerem uma maior rigidez, pavimentos e grades de WPC, componentes industriais que necessitam de propriedades mecânicas melhoradas, redução de custos em aplicações não críticas.
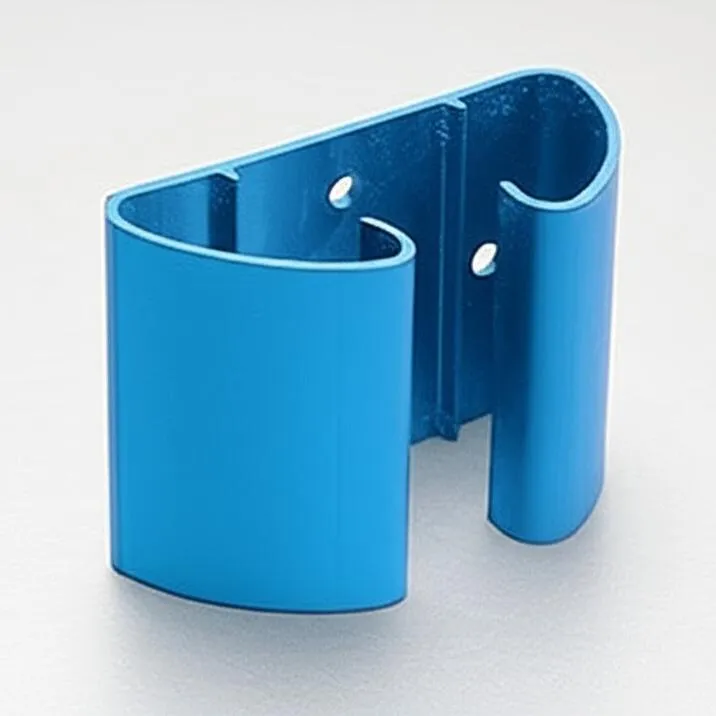
4. Perfis de PE de elevada resistência/elevado módulo (por exemplo, PE orientado):
① Descrição: Através de técnicas de processamento especializadas, como a trefilagem ou a laminagem pós-extrusão, as cadeias moleculares de PE podem ser altamente orientadas na direção da extrusão, conduzindo a propriedades mecânicas significativamente melhoradas ao longo desse eixo.
② Propriedades: Aumento drástico da resistência à tração e do módulo, por vezes próximo do de alguns plásticos de engenharia.
③ Aplicações: Cintas, fitas de reforço, fibras especializadas, cordas de alto desempenho, elementos estruturais potencialmente leves em que a resistência unidirecional é fundamental. As fibras UHMWPE são um exemplo extremo.
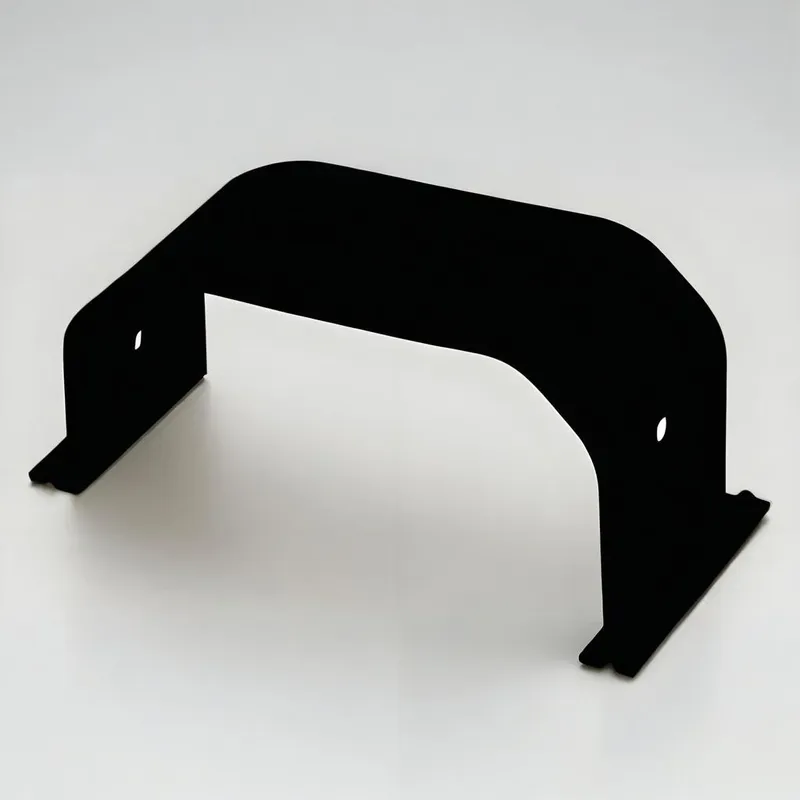
5. Perfis de PE retardadores de chama:
① Descrição: O PE normal é inflamável. Os aditivos retardadores de chama (FR) (por exemplo, compostos halogenados, muitas vezes com trióxido de antimónio, ou sistemas sem halogéneos, como hidratos minerais ou à base de fósforo, como ATH ou MDH) são incorporados para cumprir classificações de inflamabilidade específicas (por exemplo, UL 94 V-0, V-1, V-2).
② Propriedades: Inflamabilidade reduzida, caraterísticas de auto-extinção. Os aditivos de FR podem afetar as propriedades mecânicas, o processamento e o custo. As opções sem halogéneos são cada vez mais preferidas devido a preocupações ambientais com alguns FRs halogenados.
③ Aplicações: Condutas eléctricas, revestimento de fios e cabos na construção civil, componentes para aparelhos e eletrónica, aplicações de transporte que exigem segurança contra incêndios.
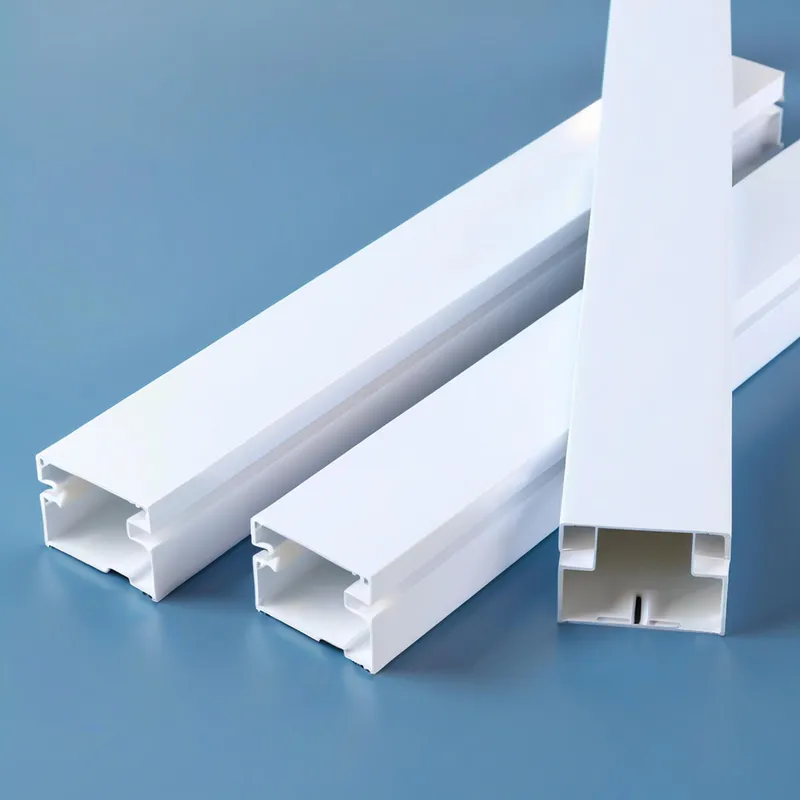
Métodos de controlo de qualidade e normas relevantes para perfis PE
Garantir que os perfis PE personalizados cumprem as especificações requer um programa robusto de controlo de qualidade (CQ), frequentemente orientado por normas da indústria.
1. Inspeção dimensional:
Métodos: Crucial para verificar se o perfil cumpre as tolerâncias do desenho.
- Ferramentas manuais: Paquímetros, micrómetros, calibradores de pinos, calibradores de raios, transferidores para medições básicas.
- Comparadores ópticos/Projectores de perfis: Ampliam a secção transversal do perfil e projectam-na num ecrã com uma sobreposição das dimensões nominais e tolerâncias para verificações rápidas ou medições detalhadas.
- Sistemas de visão sem contacto: Sistemas automatizados que utilizam câmaras e software para medir rapidamente várias dimensões.
- Scanners/medidores laser: Podem fornecer medições contínuas em linha ou fora de linha das dimensões do perfil.
- Máquinas de medição por coordenadas (CMMs): Para medições 3D altamente precisas de perfis complexos ou secções de amostras.
2. Ensaios de propriedades dos materiais (frequentemente efectuados em lotes de matérias-primas ou em placas/amostras de ensaio extrudidas em condições semelhantes):
Verificação do índice de fluxo de fusão (MFI) (ASTM D1238): Confirma que as caraterísticas de fluxo da resina estão dentro da especificação, crucial para um processamento consistente e propriedades finais.
- Densidade (ASTM D792, ASTM D1505): Verifica se está a ser utilizado o grau de PE correto e pode indicar problemas com a cristalinidade ou o teor de vazios.
- Propriedades de tração (ASTM D638): Mede a resistência à tração, o alongamento e o módulo de elasticidade. Fornece informações sobre a resistência e a ductilidade do material.
- Resistência ao impacto (Izod ASTM D256, Charpy ASTM D6110): Avalia a capacidade do perfil para resistir a um impacto súbito, importante para muitas aplicações.
- Dureza (Shore D - ASTM D2240): Mede a resistência à indentação.
- Calorimetria Exploratória Diferencial (DSC) (ASTM D3418): Pode determinar pontos de fusão, temperaturas de cristalização e grau de cristalinidade, úteis para verificar o grau do material e a consistência do processamento.
- Temperatura de deflexão térmica (HDT) (ASTM D648) / Ponto de amolecimento Vicat (ASTM D1525): Indica a temperatura à qual o material amolece sob carga.
3. Controlos do acabamento e do aspeto da superfície:
- Inspeção visual: Verificação de defeitos como linhas de matriz, pele de tubarão, fratura de fusão, descoloração, vazios, contaminação da superfície ou inconsistências. Frequentemente comparada com padrões visuais aprovados ou amostras limite.
- Correspondência de cores: Utilizando espectrofotómetros ou comparação visual em condições de iluminação normalizadas (por exemplo, cabina de luz) em relação a placas de cores ou padrões principais (por exemplo, Pantone, RAL).
- Medição do brilho (ASTM D523): Quantifica o nível de brilho da superfície, se especificado.
4. Ensaios de aplicações específicas:
- Resistência à fissuração por stress ambiental (ESCR) (ASTM D1693): Importante para os tipos de PE expostos a determinados produtos químicos sob tensão.
- Normas de ensaio de tubos (por exemplo, ASTM D3350 para materiais de tubos PE, ISO 4427 para tubos PE para abastecimento de água): Envolvem ensaios de pressão, resistência à rutura, resistência hidrostática a longo prazo.
- Teste de inflamabilidade (por exemplo, UL 94): Para perfis que requerem propriedades retardadoras de chama.
5. Normas relevantes do sector (categorias gerais):
- ASTM International: Publica numerosas normas para testes de plásticos, especificações de materiais e desempenho de produtos.
- ISO (International Organization for Standardization): Normas globais que abrangem áreas semelhantes às da ASTM, frequentemente harmonizadas.
- Normas específicas do sector: Tais como as do Instituto de Tubos de Plástico (PPI), da Associação Nacional de Fabricantes Eléctricos (NEMA) ou das normas automóveis (SAE).
- Também são comuns as normas e especificações específicas do cliente.
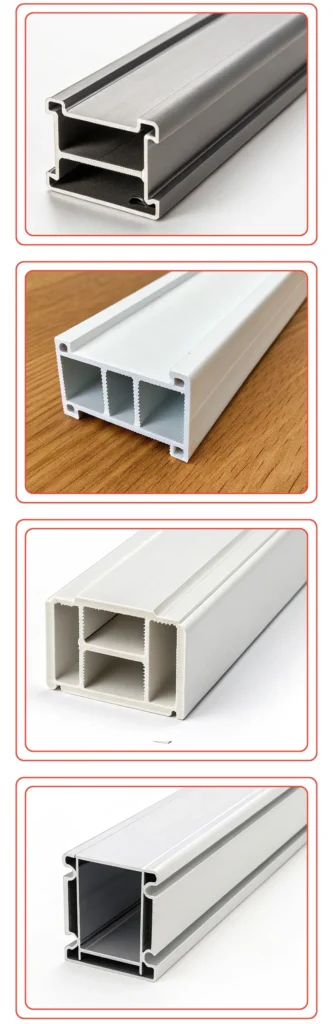
Sustentabilidade na produção de perfis PE personalizados
O impacto ambiental dos plásticos é uma preocupação global significativa, e a indústria de perfis de PE está ativamente envolvida em iniciativas de sustentabilidade.
1. Reciclabilidade inerente do polietileno:
- O PE é um termoplástico, o que significa que pode ser derretido e reprocessado várias vezes. O HDPE (código de identificação da resina #2) e o LDPE/LLDPE (código de identificação da resina #4) são amplamente reciclados.
- Conteúdo Reciclado Pós-Consumo (PCR): Incorporação de PE recuperado de fluxos de resíduos domésticos ou comerciais em novos perfis. A qualidade e a consistência do PCR podem ser difíceis, mas estão a melhorar.
- Conteúdo Reciclado Pós-Industrial (PIR) / Regrind: Utilização de sucata e material fora de especificação gerado na fábrica de extrusão ou de outras fontes industriais. Esta é uma prática comum e ajuda a minimizar os resíduos.
2. Utilização de conteúdo reciclado em perfis PE:
- Muitas aplicações não críticas podem utilizar facilmente perfis de PE com percentagens elevadas de conteúdo reciclado.
- Os desafios incluem potenciais variações de cor, uma ligeira redução das propriedades mecânicas e a garantia de um fornecimento consistente de matéria-prima reciclada de qualidade.
- Os avanços nas tecnologias de triagem e limpeza estão a melhorar a qualidade do PE reciclado.
3. Opções de polietileno de base biológica e renovável:
- Bio-PE: Quimicamente idêntico ao PE à base de combustíveis fósseis, mas derivado de recursos renováveis como a cana-de-açúcar (etanol convertido em etileno). É um substituto "drop-in", processável no equipamento de extrusão existente.
- Benefício: Reduz a dependência de combustíveis fósseis e pode ter uma pegada de carbono mais baixa (dependendo das práticas agrícolas e da utilização dos solos).
- Consideração: O custo é normalmente mais elevado e a disponibilidade pode ser limitada em comparação com o PE convencional. Não é inerentemente biodegradável, exceto se for especificamente concebido para o ser (a maior parte do bio-PE é durável).
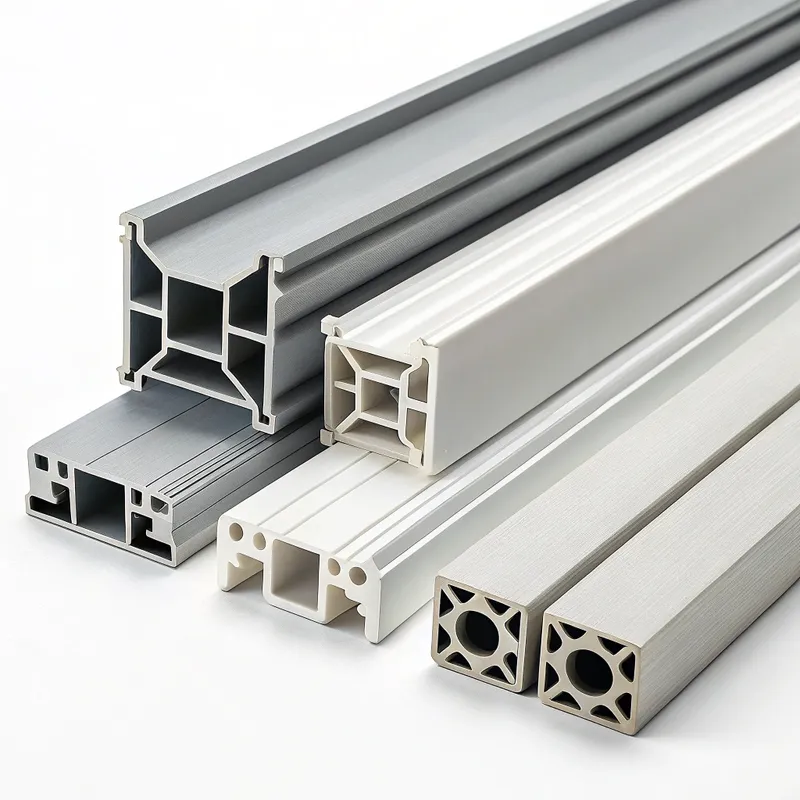
4. Princípios de conceção para o ambiente (DfE) / conceção para a reciclagem:
- Seleção de materiais: Escolher graus de PE que sejam facilmente recicláveis. Evitar perfis multimateriais complexos em que os materiais não possam ser facilmente separados se a reciclagem for um objetivo principal (a menos que a combinação seja também reciclável como um composto).
- Minimizar os aditivos: Utilizar apenas os aditivos necessários e evitar aqueles que podem contaminar os fluxos de reciclagem (por exemplo, certos enchimentos ou pigmentos problemáticos).
- Facilidade de desmontagem: Se o perfil fizer parte de um produto maior, deve ser concebido de forma a ser facilmente removido e separado.
- Aligeiramento: Otimizar a conceção do perfil para utilizar menos material sem comprometer a função (por exemplo, perfis espumados, espessuras de parede optimizadas).
5. Eficiência energética no processo de extrusão:
- As extrusoras modernas com motores energeticamente eficientes (por exemplo, accionamentos vectoriais AC), melhor isolamento do tambor e designs optimizados dos parafusos consomem menos energia.
- A otimização do processo para reduzir os tempos de arranque e as taxas de refugo também contribui para a poupança global de energia.
6. Redução de resíduos:
- Minimizar os resíduos durante o arranque, a paragem e as mudanças de produto.
- Reciclagem eficiente de sucata interna (regrind).
- Otimizar a embalagem dos perfis acabados para reduzir os resíduos.
7. Desafios e oportunidades:
- Contaminação: Assegurar que os fluxos reciclados estão isentos de contaminantes que afectam a qualidade do perfil.
- Perceção do consumidor: Criar confiança no desempenho dos perfis fabricados com conteúdos reciclados.
- Infra-estruturas: Expansão da infraestrutura de recolha e reprocessamento de PE a nível mundial.
- Oportunidade: A procura crescente de produtos sustentáveis está a impulsionar a inovação em materiais reciclados e alternativas de base biológica.
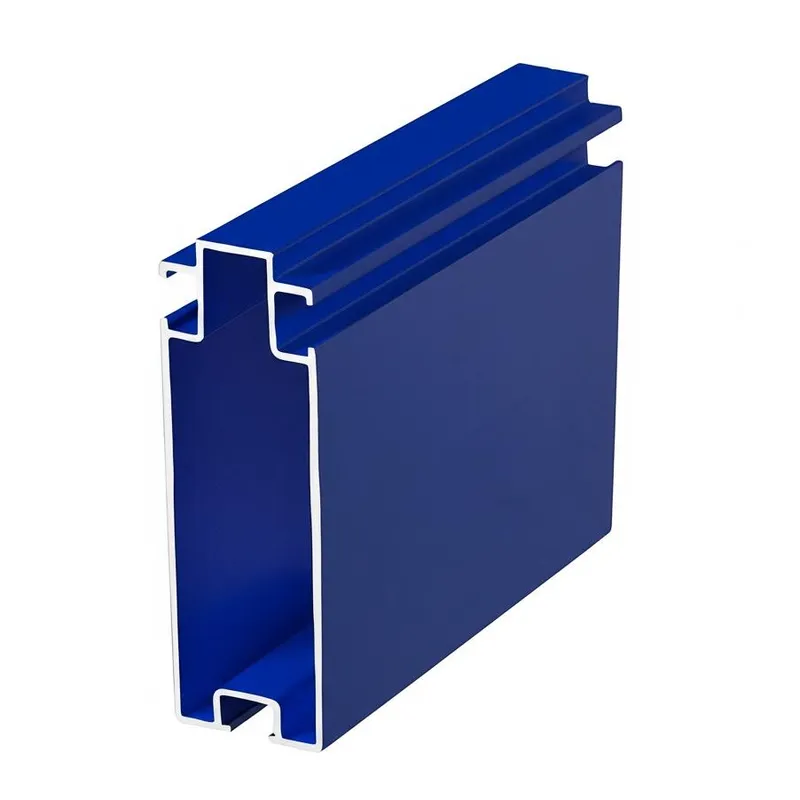
FAQs PARA O CLIENTE
Introdução ao Uplastech
Tem perguntas? Nós temos as respostas.
Somos especializados em extrusão, moldagem por vácuo, moldagem por sopro e fabrico de moldes de precisão, oferecendo soluções personalizadas para satisfazer as suas diversas necessidades de fabrico.
Trabalhamos com várias indústrias, incluindo a automóvel, eletrónica, bens de consumo e embalagens, concentrando-nos em parcerias B2B e fornecendo soluções de extrusão, termoformagem, moldagem por sopro e fabrico de moldes de precisão.
Sim, adaptamos as nossas soluções às suas necessidades específicas.
Entrar em contacto
Não hesite em enviar-nos um e-mail ou preencher o formulário abaixo para obter um orçamento.
Correio eletrónico: uplastech@gmail.com