Innowacyjne rozwiązania w zakresie wytłaczania z rozdmuchiwaniem
Odkryj innowacyjne usługi UPlasTech w zakresie wytłaczania z rozdmuchiwaniem. Specjalistyczne rozwiązania dla trwałych, wysokiej jakości produktów z tworzyw sztucznych.
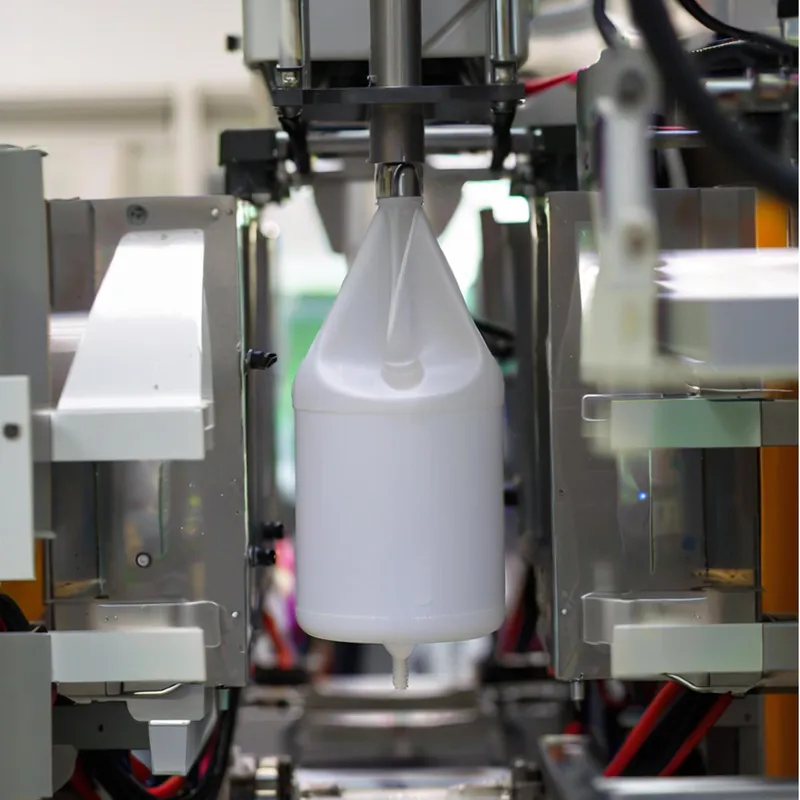
Przewodnik po niestandardowych rozwiązaniach w zakresie wytłaczania z rozdmuchiwaniem
Co to jest wytłaczanie z rozdmuchiwaniem?
Wytłaczanie z rozdmuchiwaniem (EBM) to proces produkcyjny mający na celu tworzenie pustych w środku przedmiotów z tworzyw sztucznych poprzez nadmuchiwanie stopionej plastikowej rurki, znanej jako parison, wewnątrz formy. Wywodzący się z technik podobnych do dmuchania szkła, EBM stał się podstawą w przemyśle tworzyw sztucznych od czasu jego opracowania na początku XX wieku. Proces rozpoczyna się od stopienia żywicy termoplastycznej, która jest następnie wytłaczana do formy. Ta część jest przechwytywana przez schłodzoną metalową formę, do której wdmuchiwane jest sprężone powietrze, zmuszając plastik do rozszerzenia się i dopasowania do kształtu formy. Po schłodzeniu forma otwiera się, a gotowa część jest wyrzucana, często wymagając przycięcia w celu usunięcia nadmiaru materiału lub wypływki.
EBM wyróżnia się zdolnością do wytwarzania dużych ilości lekkich, trwałych przedmiotów przy stosunkowo niskich kosztach, co czyni go idealnym do produkcji masowej. Jest ona powszechnie stosowana w branżach takich jak opakowaniowa - do produkcji butelek na wodę i pojemników na szampon - oraz motoryzacyjna, do produkcji komponentów takich jak kanały powietrzne i zbiorniki paliwa. Możliwość dostosowania do różnych kształtów i rozmiarów, w połączeniu z niższymi kosztami formowania w porównaniu do innych metod, ugruntowała jego rolę w nowoczesnej produkcji.
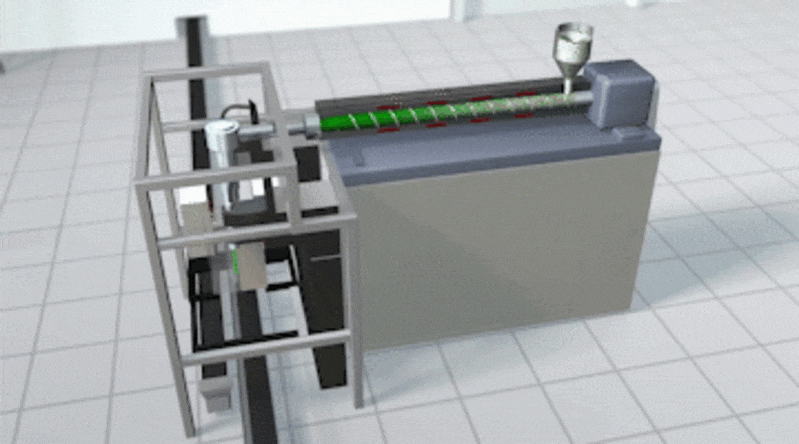
Jak działa wytłaczanie z rozdmuchiwaniem?
Wytłaczanie z rozdmuchiwaniem (EBM) to proces produkcyjny wykorzystywany do tworzenia pustych w środku części z tworzyw sztucznych, takich jak butelki, pojemniki i części samochodowe. Obejmuje on topienie żywicy z tworzywa sztucznego, formowanie jej w strukturę przypominającą rurkę zwaną parisonem, napełnianie jej wewnątrz formy sprężonym powietrzem w celu uzyskania pożądanego kształtu, chłodzenie, a następnie wyrzucanie gotowej części. Poniżej znajduje się szczegółowe wyjaśnienie, jak działa ten proces, z podziałem na kluczowe etapy.
1. Proces krok po kroku:
① Topienie i wytłaczanie tworzyw sztucznych:
- Podawanie materiału: Proces rozpoczyna się od granulatu z tworzywa sztucznego, zazwyczaj termoplastycznego, takiego jak polietylen o wysokiej gęstości (HDPE), polipropylen (PP) lub politereftalan etylenu (PET), podawanego do wytłaczarki przez lej zasypowy.
- Topienie: Wewnątrz wytłaczarki obracający się ślimak przesuwa granulki przez rozgrzaną beczkę. Ciepło i działanie mechaniczne topią tworzywo sztuczne w jednolity stopiony stan.
- Wytłaczanie: Stopione tworzywo sztuczne jest przeciskane przez matrycę, tworząc ciągłą pustą rurkę zwaną parisonem. Matryca kształtuje średnicę i grubość ścianki parisona, które są krytyczne dla produktu końcowego.
② Formacja Parison: Parison to wydrążona rura z centralnym otworem, przez który później przepływa powietrze. W przypadku prostych części, parison ma jednolitą grubość, ale w przypadku złożonych kształtów, programator parisona może dostosować szczelinę matrycy, aby dynamicznie zmieniać grubość podczas wytłaczania parisona.
③ Zamknięcie formy: Parison jest umieszczany między dwiema połówkami chłodzonej metalowej formy, często wykonanej z aluminium ze względu na jego przewodność cieplną. Forma zamyka się wokół parisona, uszczelniając go na dole (a czasem na górze), aby uwięzić plastik i przygotować go do nadmuchania.
④ Dmuchanie: Sprężone powietrze jest wdmuchiwane do parisona przez trzpień lub igłę. Ciśnienie powietrza napełnia parison, powodując jego rozszerzenie i dopasowanie do kształtu wnętrza formy. Ciśnienie musi być dokładnie kontrolowane, aby upewnić się, że tworzywo sztuczne wypełnia formę bez pękania lub pozostawiania cienkich plam.
⑤ Chłodzenie: Forma, wyposażona w kanały chłodzące (zwykle cyrkulujące schłodzoną wodę), szybko chłodzi napompowany plastik, aby go zestalić. Ten etap zapewnia, że część zachowuje swój kształt i może być przenoszona bez deformacji. Czas chłodzenia zależy od grubości części i użytego materiału.
⑥ Wyrzucenie: Gdy tworzywo sztuczne stwardnieje, forma otwiera się, a gotowa część jest wyrzucana, często za pomocą powietrza lub mechanicznych wyrzutników. Na tym etapie część może mieć nadmiar materiału, znany jako flash, nadal dołączony.
⑦ Przycinanie: Wypływka - nadmiar tworzywa sztucznego z linii podziału formy lub obszarów ściskania - jest usuwana ręcznie za pomocą narzędzi lub automatycznie za pomocą ostrzy lub innego sprzętu. Ten etap finalizuje kształt części, a dodatkowe wykończenie (takie jak etykietowanie) może nastąpić w zależności od zastosowania.
2. Kluczowe czynniki sukcesu:
① Kontrola temperatury: Tworzywo sztuczne musi być równomiernie stopione, a forma skutecznie schłodzona, aby zapobiec wadom, takim jak wypaczenia lub nierówna grubość.
② Kontrola parowania: Grubość i stabilność parisona są kluczowe dla uzyskania jednolitej grubości ścianki w produkcie końcowym, szczególnie w przypadku złożonych kształtów.
③ Ciśnienie powietrza: Odpowiednie ciśnienie zapewnia pełne napompowanie parisona bez wydmuchiwania lub niekompletnego formowania.
④ Konstrukcja formy: Forma musi pasować do geometrii części i umożliwiać łatwe wyrzucanie.
3. Warianty procesu:
① Wytłaczanie ciągłe: Parison jest wytłaczany stabilnie, a formy wychwytują jego sekcje podczas ruchu. Jest to idealne rozwiązanie do wysokonakładowej produkcji mniejszych części, takich jak butelki na napoje.
② Wytłaczanie przerywane: Wytłaczanie zatrzymuje się między cyklami, aby zapewnić bardziej precyzyjną kontrolę, często stosowaną w przypadku większych lub złożonych części. Obejmuje to:
③ Metoda śruby tłokowej: Śruba porusza się do tyłu, aby zebrać stopiony plastik, a następnie do przodu, aby wytłoczyć parison.
④ Metoda akumulatora: Roztopiony plastik jest przechowywany w akumulatorze i szybko wytłaczany, co nadaje się do dużych elementów, takich jak zbiorniki paliwa.
Jakie są różne rodzaje wytłaczania z rozdmuchiwaniem?
Wytłaczanie z rozdmuchiwaniem to proces produkcyjny wykorzystywany do wytwarzania pustych w środku części z tworzyw sztucznych, takich jak butelki, pojemniki i komponenty samochodowe, poprzez wytłaczanie rurki ze stopionego tworzywa sztucznego (zwanej parisonem) i nadmuchiwanie jej wewnątrz formy. Istnieje kilka różnych rodzajów wytłaczania z rozdmuchiwaniem, z których każdy jest dostosowany do różnych potrzeb produkcyjnych i wymagań dotyczących części. Poniżej znajdują się główne typy:
1. Ciągłe wytłaczanie z rozdmuchiwaniem:
W tym typie parison jest wytłaczany w sposób ciągły z maszyny, a formy przechwytują jego sekcje w celu uformowania części. Metoda ta jest idealna do wysokonakładowej produkcji małych i średnich przedmiotów, takich jak plastikowe butelki i pojemniki, ze względu na jej szybkość i wydajność. Odmiany wytłaczania ciągłego obejmują:
- Shuttle Blow Molding: Formy poruszają się tam i z powrotem (wahadłowo), aby uchwycić parison, umożliwiając elastyczność produkcji.
- Obrotowe koło do formowania z rozdmuchiwaniem: Wiele form jest zamontowanych na obracającym się kole, umożliwiając szybką, zautomatyzowaną produkcję.
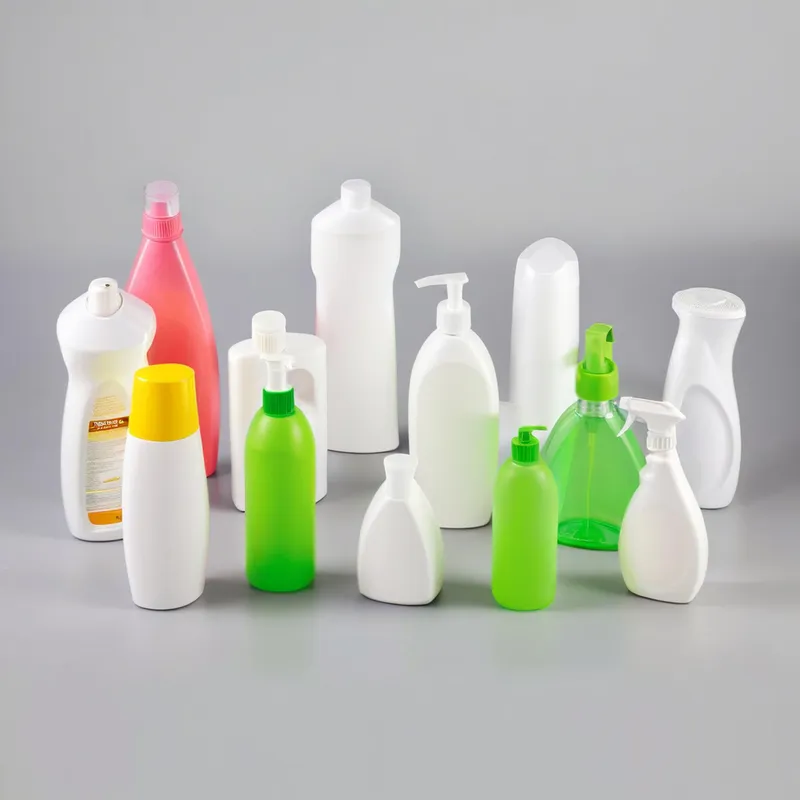
2. Formowanie z rozdmuchiwaniem z przerywanym wytłaczaniem:
W przypadku wytłaczania przerywanego parison jest wytłaczany w dyskretnych cyklach, a nie w sposób ciągły, co zapewnia większą kontrolę nad jego formowaniem. Ten typ jest odpowiedni dla większych lub bardziej złożonych części. Można go dalej podzielić na dwie metody:
Metoda śruby tłokowej: Śruba w wytłaczarce porusza się do tyłu, aby zgromadzić stopiony plastik, a następnie do przodu, aby wytłoczyć parison. Metoda ta jest zwykle stosowana w przypadku części średniej wielkości i zapewnia dobrą precyzję.
- Metoda akumulatora: Stopione tworzywo sztuczne jest przechowywane w akumulatorze, a następnie szybko wytłaczane w celu uformowania parisona. Jest to idealne rozwiązanie w przypadku bardzo dużych lub skomplikowanych części, takich jak samochodowe zbiorniki paliwa, gdzie szybko potrzebna jest znaczna ilość materiału.
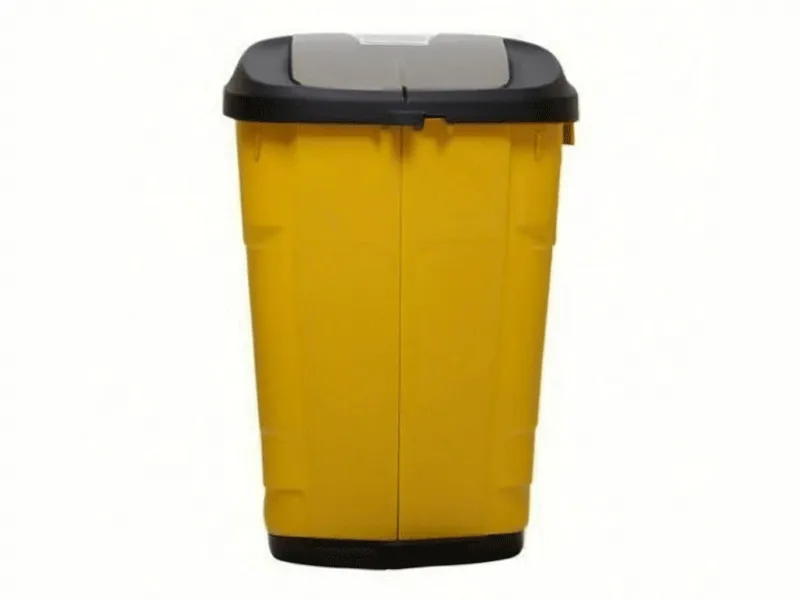
3. Współwytłaczanie z rozdmuchiwaniem:
Współwytłaczanie z rozdmuchiwaniem polega na wykorzystaniu wielu wytłaczarek do tworzenia parisonu z kilkoma warstwami różnych materiałów. Ten rodzaj zwiększa właściwości produktu końcowego, takie jak poprawa odporności na barierę (np. w przypadku opakowań na żywność) lub połączenie estetyki z wytrzymałością. Współwytłaczanie może być stosowane zarówno w procesach wytłaczania ciągłego, jak i przerywanego, co sprawia, że jest to raczej wszechstronna odmiana niż całkowicie odrębna kategoria, choć często jest wymieniana jako odrębny typ ze względu na swoje znaczenie.
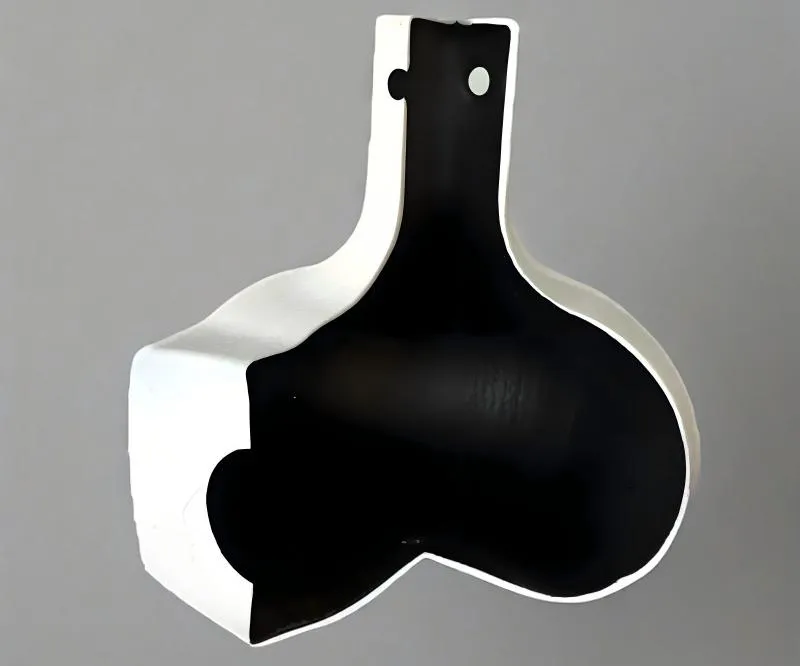
Jakie materiały są używane w procesie wytłaczania z rozdmuchiwaniem?
Wytłaczanie z rozdmuchiwaniem (EBM) to proces produkcyjny wykorzystywany do tworzenia pustych w środku plastikowych części, takich jak butelki, pojemniki i części samochodowe. W tym procesie żywica z tworzywa sztucznego jest topiona, wytłaczana w strukturę przypominającą rurkę zwaną parisonem, a następnie nadmuchiwana wewnątrz formy w celu uformowania pożądanego kształtu. Materiały stosowane w EBM to głównie tworzywa termoplastyczne - tworzywa, które można wielokrotnie topić, kształtować i chłodzić bez znaczącej degradacji chemicznej.
1. Typowe materiały stosowane w wytłaczaniu z rozdmuchiwaniem:
Następujące tworzywa termoplastyczne są szeroko stosowane w EBM ze względu na ich wszechstronność i kompatybilność z procesem:
① Polietylen o wysokiej gęstości (HDPE): Znany ze swojej trwałości i odporności chemicznej, HDPE jest najpopularniejszym materiałem w EBM. Jest on powszechnie stosowany do produkcji dzbanków na mleko, butelek na detergenty i zbiorników na paliwo. Możliwość recyklingu sprawia, że jest to zrównoważony wybór.
② Polipropylen (PP): PP oferuje odporność na ciepło i elastyczność, dzięki czemu idealnie nadaje się do produkcji części samochodowych, takich jak kanały powietrzne, a także pojemniki wielokrotnego użytku. Jego kluczową zaletą jest odporność na powtarzające się naprężenia.
③ Politereftalan etylenu (PET): Chociaż PET jest bardziej typowy dla formowania wtryskowego z rozdmuchiwaniem, jest stosowany w EBM do produkcji przezroczystych, mocnych butelek na napoje i opakowań na żywność. Wymaga wstępnego suszenia, aby uniknąć degradacji podczas przetwarzania.
④ Polichlorek winylu (PVC): PVC jest sztywny i odporny na chemikalia, często używany do produkcji rur, kształtek i izolacji kabli. Może być również elastyczny do zastosowań takich jak rurki medyczne.
⑤ Polistyren (PS): Lekki i łatwy do formowania materiał PS jest używany do produkcji przedmiotów jednorazowego użytku, takich jak kubki i tace na żywność. Jest opłacalny, ale mniej trwały niż inne opcje.
2. Specjalistyczne i nowe materiały:
Oprócz powszechnie stosowanych materiałów, EBM wykorzystuje również specjalistyczne tworzywa termoplastyczne i zrównoważone alternatywy dla konkretnych potrzeb:
① Poliwęglan (PC): Dzięki wysokiej udarności i przezroczystości PC jest stosowany do produkcji dużych pojemników i części samochodowych, takich jak butelki do chłodziarek. Jest droższy, ale doskonale sprawdza się w wymagających zastosowaniach.
② Nylon (poliamid): Nylon zapewnia wytrzymałość i odporność na temperaturę, dzięki czemu nadaje się do przewodów paliwowych i kolektorów dolotowych powietrza w warunkach przemysłowych. Jego zastosowanie jest ograniczone kosztami.
③ Biotworzywa: Nowe materiały, takie jak kwas polimlekowy (PLA) lub polietylen na bazie biologicznej, są biodegradowalne i wykorzystywane do produkcji ekologicznych opakowań. Zyskują one na popularności jako zrównoważone opcje.
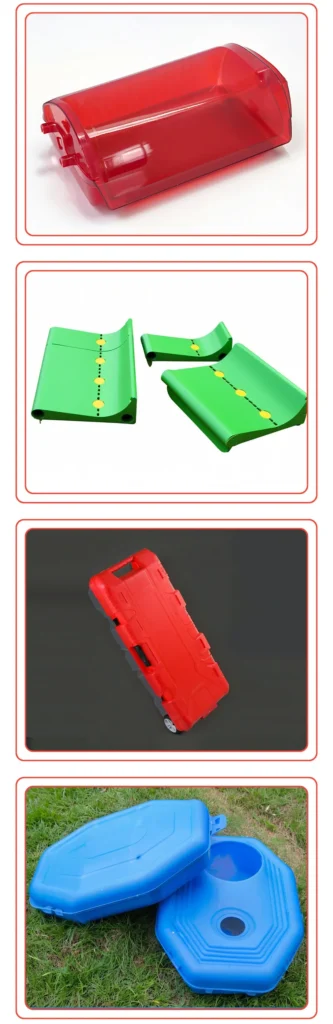
3. Tabela materiałów:
Materiał | Typowe zastosowania | Kluczowe właściwości |
---|---|---|
HDPE | Butelki, zbiorniki paliwa | Trwały, odporny na chemikalia |
PP | Części samochodowe, pojemniki | Odporny na wysoką temperaturę, elastyczny |
PET | Butelki na napoje | Wyraźny, mocny |
PVC | Rury, złączki | Sztywny, odporny na chemikalia |
PS | Jednorazowe kubki, tace | Lekki, łatwy do formowania |
Poliwęglan | Butelki do chłodzenia wodą | Wysoka udarność, przezroczystość |
Nylon | Przewody paliwowe, kolektory | Mocny, odporny na temperaturę |
Biotworzywa | Zrównoważone opakowania | Biodegradowalny, przyjazny dla środowiska |
Jakie są główne zastosowania wytłaczania z rozdmuchiwaniem?
Wytłaczanie z rozdmuchiwaniem (EBM) jest szeroko stosowanym procesem produkcyjnym, który tworzy puste w środku plastikowe części poprzez nadmuchiwanie stopionej plastikowej rurki, znanej jako parison, wewnątrz formy. Technika ta jest ceniona za swoją wszechstronność, opłacalność i zdolność do wytwarzania lekkich, trwałych produktów o złożonych kształtach. Od przedmiotów codziennego użytku, takich jak butelki na wodę, po specjalistyczne komponenty przemysłowe, EBM stał się kamieniem węgielnym nowoczesnej produkcji w wielu branżach.
1. Przemysł spożywczy i napojów:
Sektor żywności i napojów w dużym stopniu polega na EBM w zakresie produkcji bezpiecznych, praktycznych i opłacalnych rozwiązań opakowaniowych.
- Butelki i pojemniki: EBM jest używany do produkcji butelek na wodę, dzbanków na mleko, pojemników na sok i butelek na przyprawy. Produkty te są lekkie, odporne na stłuczenia i zaprojektowane tak, aby zachować zawartość i wydłużyć okres przydatności do spożycia.
- Opakowania na żywność: Przedmioty takie jak kubki na jogurt, pojemniki na margarynę i pojemniki do przechowywania są wykonane z EBM, często posiadają ergonomiczne kształty lub uchwyty dla wygody użytkownika.
Użyte materiały:
- Polietylen o wysokiej gęstości (HDPE) i polipropylen (PP) są popularnym wyborem ze względu na ich właściwości bezpieczne dla żywności, odporność chemiczną i możliwość recyklingu.
Dlaczego EBM?
- Jego zdolność do produkcji hermetycznych, szczelnych opakowań na dużą skalę sprawia, że idealnie nadaje się do towarów łatwo psujących się. Ponadto EBM wspiera trendy zrównoważonego rozwoju, umożliwiając wykorzystanie tworzyw sztucznych pochodzących z recyklingu.
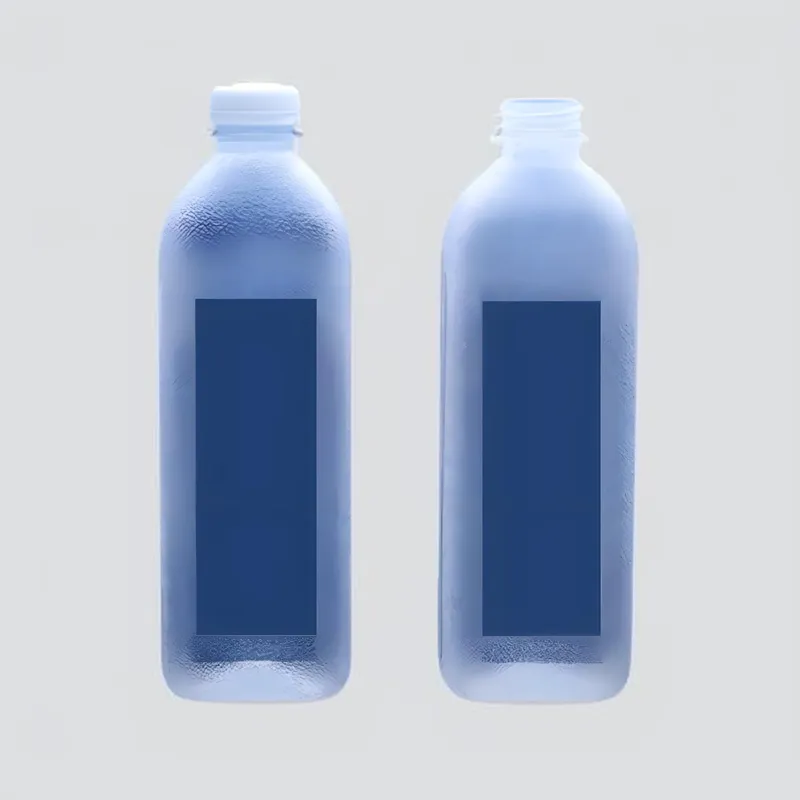
2. Produkty gospodarstwa domowego i higieny osobistej:
EBM to proces tworzenia funkcjonalnych i atrakcyjnych wizualnie pojemników na artykuły gospodarstwa domowego i higieny osobistej.
- Butelki na detergenty i środki czyszczące: Wytrzymałe, odporne na chemikalia butelki na detergenty do prania, wybielacze i spraye czyszczące są wykonane z EBM, często z uchwytami ułatwiającymi użytkowanie.
- Pojemniki na kosmetyki i środki higieny osobistej: Butelki szamponów, dozowniki balsamów, dezodoranty w sztyfcie i słoiki kosmetyczne korzystają ze zdolności EBM do tworzenia skomplikowanych wzorów, takich jak wytłaczane logo lub teksturowane powierzchnie.
Użyte materiały:
HDPE i polietylen o niskiej gęstości (LDPE) oferują elastyczność i trwałość, podczas gdy politereftalan etylenu (PET) zapewnia przejrzystość produktów premium.
Dlaczego EBM?
Proces ten pozwala na bezpośrednie formowanie złożonych kształtów i elementów marki, zwiększając atrakcyjność produktu. Opcje współwytłaczania wielowarstwowego poprawiają również właściwości barierowe, wydłużając okres przydatności do spożycia.
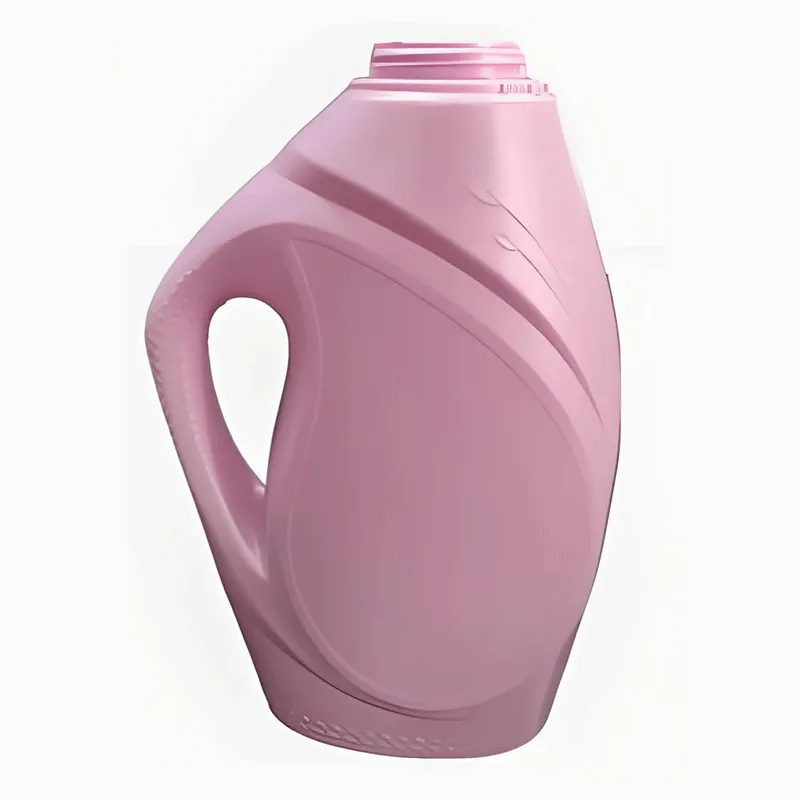
3. Przemysł farmaceutyczny i opieka zdrowotna:
W służbie zdrowia EBM dostarcza bezpieczne, precyzyjne i sterylne opakowania i komponenty, które spełniają rygorystyczne standardy.
- Butelki farmaceutyczne: Butelki na tabletki, syropy i płynne leki są produkowane z EBM, często z zakrętkami zabezpieczającymi przed manipulacją lub zamknięciami zabezpieczającymi przed dziećmi.
- Komponenty urządzeń medycznych: Elastyczne, puste w środku części, takie jak mieszki, ściskacze i maski oddechowe, są wytwarzane przy użyciu EBM do zastosowań medycznych.
Użyte materiały:
PP i HDPE zapewniają sterylność i odporność chemiczną, podczas gdy elastomery termoplastyczne (TPE) zapewniają elastyczność przewodów i uszczelek.
Dlaczego EBM?
Jego precyzja zapewnia stałą jakość, co ma krytyczne znaczenie dla zgodności z przepisami, i obsługuje funkcje, takie jak stopniowane oznaczenia dla dokładnego dozowania.
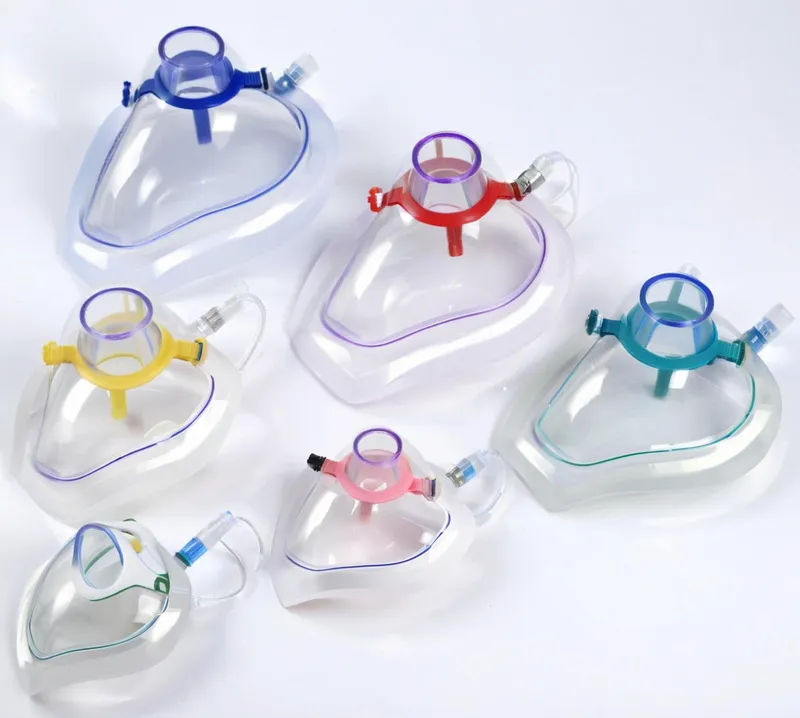
4. Przemysł motoryzacyjny:
EBM przyczynia się do zwiększenia wydajności i osiągów pojazdów poprzez produkcję lekkich i wytrzymałych komponentów.
- Kanały powietrzne i komponenty HVAC: Złożone, wydrążone części, które kierują powietrze w pojazdach, są wykonane przy użyciu EBM, zmniejszając wagę i poprawiając wydajność paliwową.
- Zbiorniki paliwa i zbiorniki płynów: Małe zbiorniki paliwa (np. do motocykli) i zbiorniki płynu do spryskiwaczy lub płynu chłodzącego są wykonane z EBM w celu zapewnienia szczelności.
Użyte materiały:
HDPE i PP zapewniają odporność na ciepło, a wielowarstwowe współwytłaczanie dodaje bariery zapobiegające przenikaniu paliwa.
Dlaczego EBM?
Produkuje duże, złożone kształty ze zintegrowanymi funkcjami, takimi jak punkty montażowe, obniżając koszty montażu i wspierając koncentrację branży na lekkości.
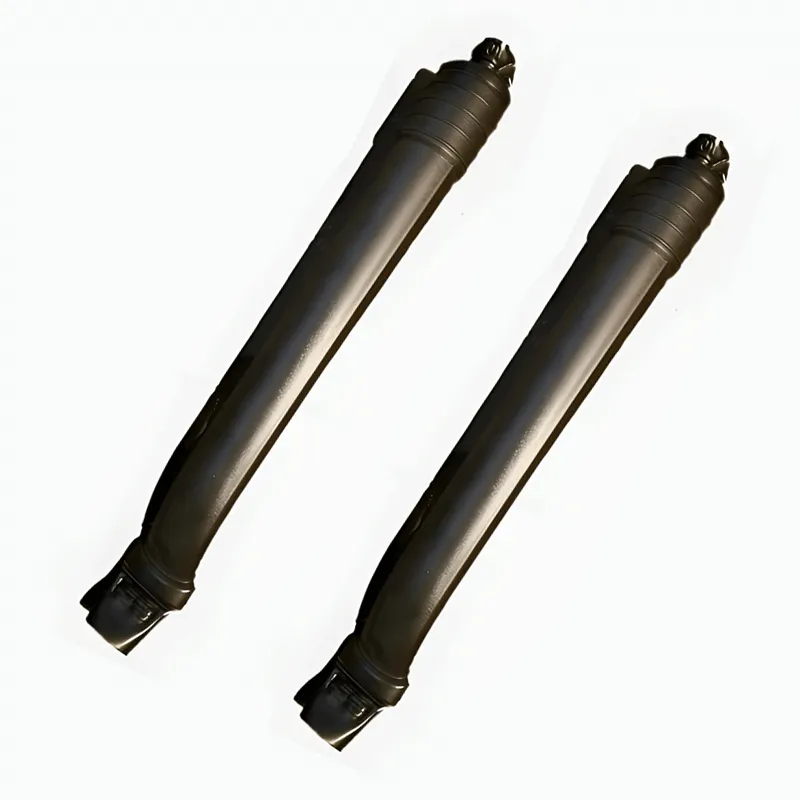
5. Zastosowania przemysłowe i rolnicze:
EBM wyróżnia się w tworzeniu solidnych, wielkogabarytowych pojemników i komponentów do zastosowań przemysłowych i rolniczych.
- Bębny i zbiorniki przemysłowe: Duże pojemniki, takie jak 55-galonowe beczki na chemikalia lub smary, są wykonane z EBM, aby wytrzymać trudne warunki.
- Produkty rolne: Konewki, opryskiwacze do pestycydów i pojemniki na nawozy mają ergonomiczną konstrukcję, którą umożliwia EBM.
Użyte materiały:
HDPE zapewnia odporność na uderzenia i stabilność chemiczną, podczas gdy PVC oferuje sztywność dostosowaną do konkretnych potrzeb.
Dlaczego EBM?
Jego zdolność do produkcji grubościennych, jednolitych części zapewnia trwałość, a zintegrowane funkcje, takie jak gwintowane szyjki, zwiększają funkcjonalność.
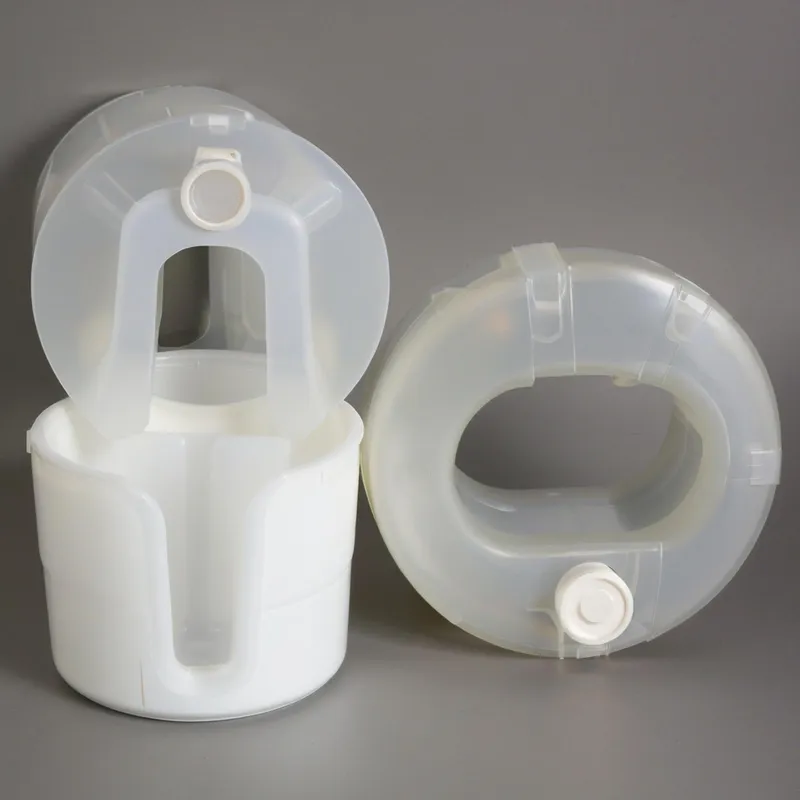
6. Zabawki i produkty rekreacyjne:
EBM jest szeroko stosowany do tworzenia bezpiecznych, trwałych i zabawnych produktów dla dzieci i aktywności na świeżym powietrzu.
- Zabawki: Puste plastikowe zabawki, takie jak piłki, domki do zabawy i pojazdy jeżdżące, są wykonane z EBM, co zapewnia gładkie, bezpieczne krawędzie i żywe kolory.
- Artykuły sportowe: Kajaki, sanki i wyposażenie placów zabaw wykorzystują zdolność EBM do produkcji dużych, bezszwowych i lekkich konstrukcji.
Użyte materiały:
LDPE i HDPE zapewniają elastyczność, bezpieczeństwo i odporność na uderzenia.
Dlaczego EBM?
Elastyczność projektu pozwala na kreatywne kształty ze zintegrowanymi funkcjami, a zastosowanie nietoksycznych materiałów nadających się do recyklingu spełnia normy bezpieczeństwa i ochrony środowiska.
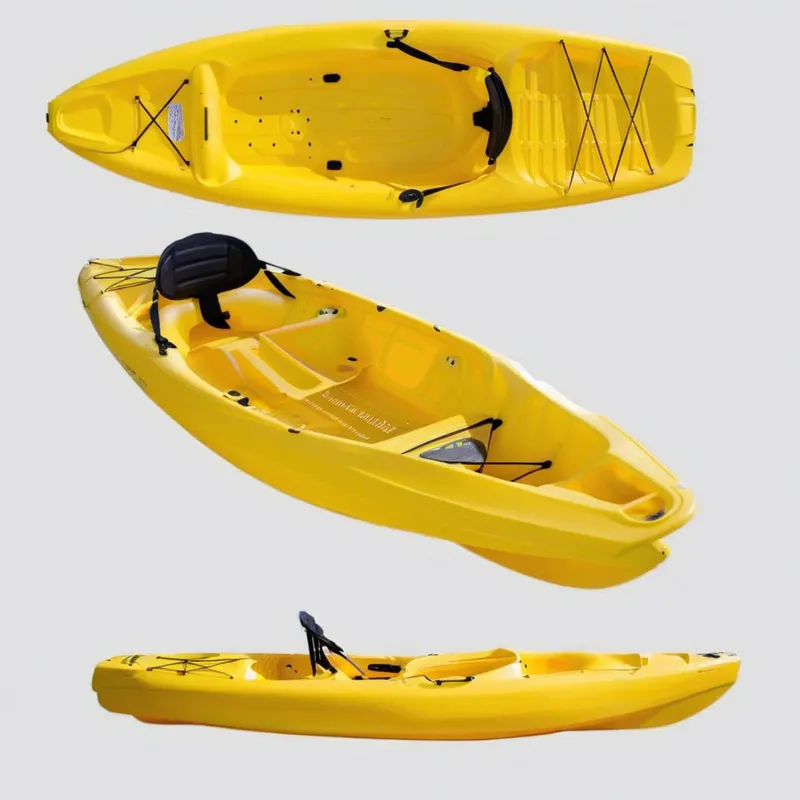
7. Budownictwo i infrastruktura:
EBM wspiera budownictwo poprzez produkcję trwałych, odpornych na warunki atmosferyczne komponentów.
- Rury i kanały: Kanały wentylacyjne, rury drenażowe i osłony ochronne są wykonane z EBM, co zapewnia lekkość i wytrzymałość.
- Bariery i sprzęt bezpieczeństwa: Pachołki drogowe, bariery bezpieczeństwa i przenośne zbiorniki toaletowe korzystają z możliwości EBM na dużą skalę.
Użyte materiały:
HDPE i PVC zapewniają odporność na warunki atmosferyczne i trwałość.
Dlaczego EBM?
Szybko dostarcza jednolite, spójne części, spełniając wysokie wymagania i potrzeby strukturalne projektów budowlanych.
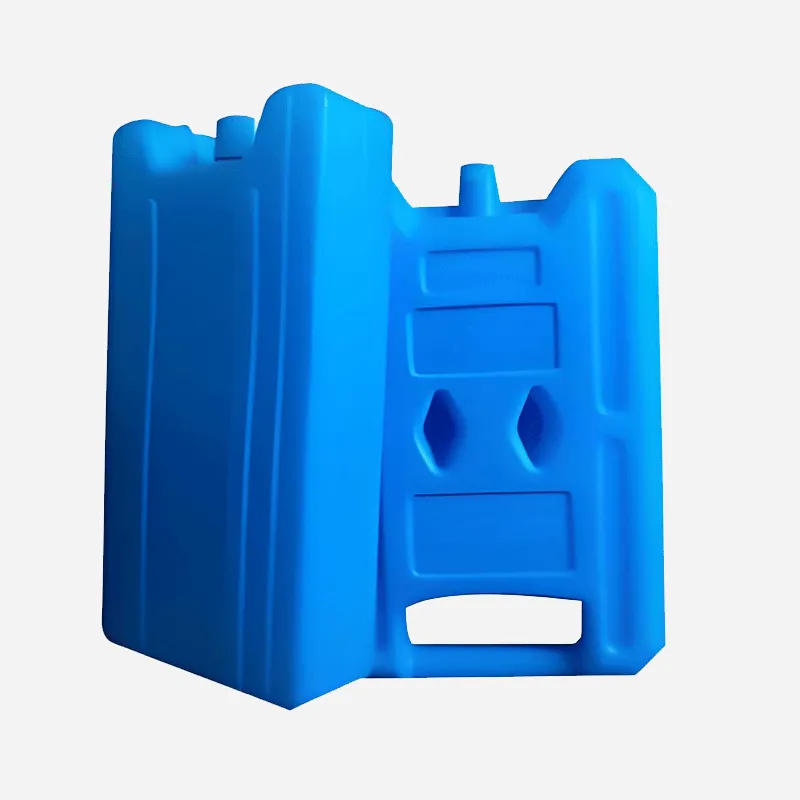
Zalety i ograniczenia wytłaczania z rozdmuchiwaniem
Zalety:
Opłacalność: Niższe koszty form i sprzętu sprawiają, że jest to idealne rozwiązanie do produkcji na dużą skalę.
② Elastyczność projektowania: Łatwe tworzenie złożonych kształtów poprzez dostosowanie form lub ustawień parison.
③ Wszechstronność materiałowa: Współpracuje z różnymi tworzywami termoplastycznymi, zapewniając dostosowane właściwości.
Lekkie produkty: Tworzy trwałe, lekkie produkty, redukując koszty materiałów i wysyłki.
Ograniczenia:
① Odpady materiałowe: Wytwarza więcej złomu (flash) niż inne metody, wpływając na wydajność.
② Operacje dodatkowe: Wymaga przycinania, co zwiększa czas i koszty.
③ Problemy z wypełnianiem narożników: Cienkie parisony zmagają się z ostrymi narożnikami, ryzykując defekty.
④ Wykwalifikowana obsługa: Wymaga przeszkolonego personelu do zarządzania zmiennymi procesowymi.
Rozwiązania do wytłaczania z rozdmuchiwaniem
Odkryj specjalistyczne rozwiązania w zakresie wytłaczania z rozdmuchiwaniem niestandardowych produktów z tworzyw sztucznych. Dowiedz się więcej o materiałach, procesach, rozważaniach projektowych i zrównoważonych metodach produkcji, aby zaspokoić swoje potrzeby produkcyjne.
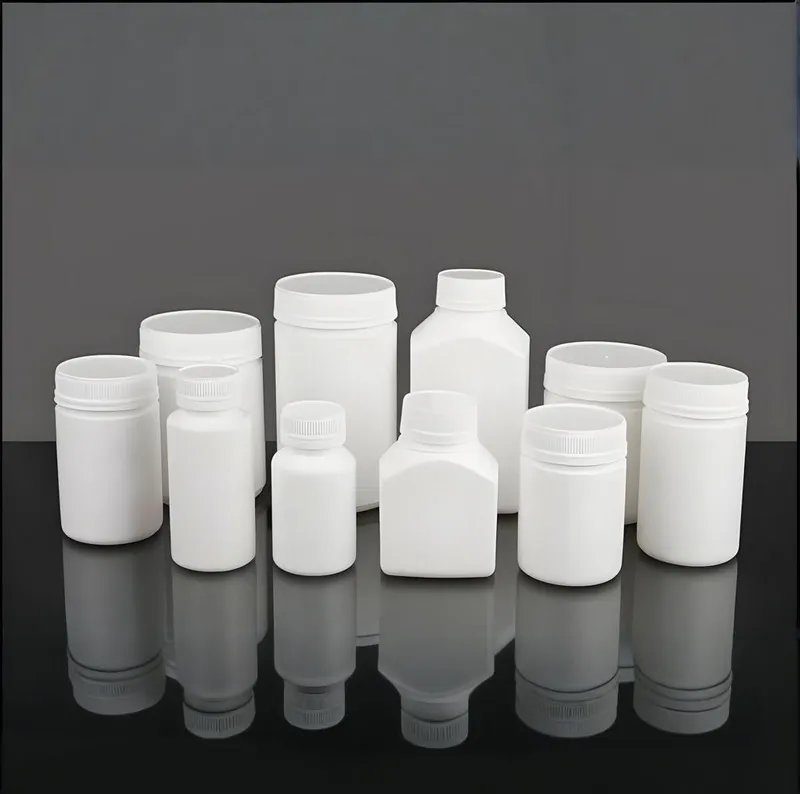
Przewodnik po niestandardowych rozwiązaniach w zakresie wytłaczania z rozdmuchiwaniem
- Maszyny i urządzenia do wytłaczania z rozdmuchiwaniem
- Kluczowe kwestie projektowe w wytłaczaniu z rozdmuchiwaniem
- Wytłaczanie z rozdmuchiwaniem w porównaniu do innych procesów formowania
- Jakie są najczęstsze wady wytłaczania z rozdmuchiwaniem?
- Prototypowanie i produkcja małoseryjna w EBM
- Zrównoważony rozwój i recykling w wytłaczaniu z rozdmuchiwaniem
Jakie maszyny i urządzenia są używane w procesie wytłaczania z rozdmuchiwaniem?
Wytłaczanie z rozdmuchiwaniem (EBM) to proces produkcyjny, który tworzy puste w środku plastikowe części, takie jak butelki i pojemniki, poprzez topienie plastiku, formowanie go w rurkę (parison), nadmuchiwanie go wewnątrz formy i chłodzenie do ostatecznego kształtu. Zaangażowane maszyny i urządzenia są wyspecjalizowane, aby skutecznie obsługiwać te etapy. Oto szczegółowy podział:
1. Wytłaczarka:
Wytłaczarka jest głównym elementem, w którym granulki tworzyw sztucznych (np. HDPE, PP) są podawane do leja zasypowego, topione i mieszane. Wewnątrz podgrzewanej beczki znajduje się obracający się ślimak, który topi tworzywo sztuczne i przesuwa je w kierunku matrycy. Nowoczesne wytłaczarki często posiadają precyzyjną kontrolę temperatury i prędkości, aby zapewnić spójne stopienie.
2. Forma do wytłaczania:
Matryca kształtuje stopiony plastik w wydrążoną rurkę zwaną parisonem. Jej konstrukcja kontroluje średnicę i grubość ścianki, które mają kluczowe znaczenie dla jakości produktu końcowego. Regulowane matryce lub systemy programowania parison umożliwiają regulację grubości w czasie rzeczywistym, szczególnie w przypadku złożonych części.
3. Forma rozdmuchowa:
Zazwyczaj wykonana z aluminium ze względu na jego opłacalność i przewodność cieplną, forma składa się z dwóch połówek, które zamykają się wokół parisona, tworząc ostateczny kształt części. Formy często mają zintegrowane kanały chłodzące i otwory wentylacyjne, aby zapewnić prawidłowe krzepnięcie i ucieczkę powietrza podczas napełniania.
4. Zawleczka:
Trzpień rozdmuchowy dostarcza sprężone powietrze do parisona, nadmuchując go do ścianek formy. Jego położenie i przepływ powietrza muszą być precyzyjne, aby uniknąć wad, takich jak nierówna grubość lub wydmuchiwanie. W niektórych konfiguracjach trzpień rozdmuchowy pomaga również w przycinaniu nadmiaru materiału.
5. Jednostka zaciskowa:
System ten zabezpiecza połówki formy podczas napełniania i chłodzenia, przeciwdziałając ciśnieniu powietrza wewnątrz. Może być hydrauliczny lub mechaniczny, z wystarczającą siłą, aby zapobiec wyciekom lub niewspółosiowości, które mogą prowadzić do wypalenia lub wadliwych części.
6. Układ chłodzenia:
Chłodzenie odbywa się poprzez kanały wodne wewnątrz formy, cyrkulujące schłodzoną wodę w celu szybkiego zestalenia tworzywa sztucznego. Wydajne chłodzenie skraca czas cyklu i zapobiega wypaczaniu, a niektóre systemy obejmują chłodzenie powietrzem w celu dodatkowej kontroli.
7. Stacja przycinania:
Po wyrzuceniu nadmiar tworzywa sztucznego (wypływka) utworzony na linii podziału formy lub w obszarach zaciskania jest usuwany na stacji przycinania. Może to obejmować narzędzia ręczne, zautomatyzowane ostrza lub lasery, w zależności od skali produkcji i potrzeb w zakresie precyzji.
8. Dodatkowe wyposażenie:
① Urządzenia programujące Parison: Dynamiczna regulacja ustawień matrycy w celu uzyskania jednolitej grubości ścianki.
Głowice akumulatorowe: Przechowują stopione tworzywo sztuczne do wytłaczania przerywanego, idealne do dużych lub złożonych części.
Systemy automatyzacji: Roboty lub przenośniki obsługują części w konfiguracjach o dużej objętości, zwiększając wydajność.
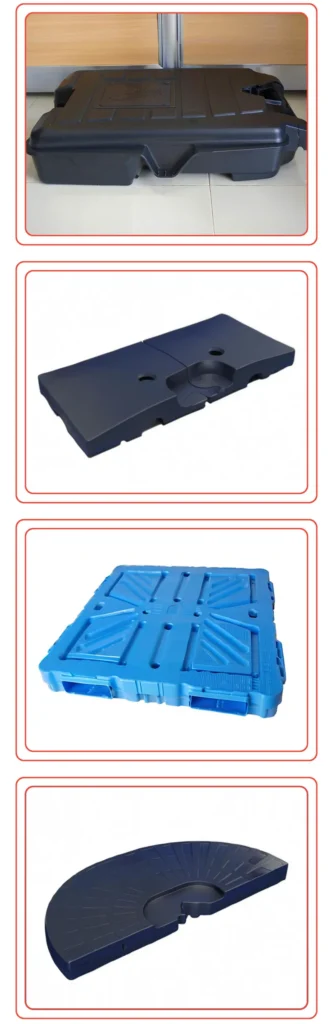
Jakie są kluczowe kwestie projektowe w wytłaczaniu z rozdmuchiwaniem?
Projektowanie pod kątem EBM wymaga zrównoważenia funkcjonalności, estetyki i możliwości produkcyjnych części. Oto kluczowe kwestie, które zostały szczegółowo wyjaśnione:
1. Jednorodność grubości ścianki:
Stała grubość ścianki zapewnia wytrzymałość i wydajność. Tendencja parisona do opadania pod wpływem grawitacji może powodować przerzedzanie, dlatego projektanci używają programowania parisona do dostosowywania grubości podczas wytłaczania, zapewniając, że krytyczne obszary (np. narożniki) mają wystarczającą ilość materiału.
2. Konstrukcja formy:
Forma musi pasować do geometrii części, w tym złożonych elementów, takich jak uchwyty lub podcięcia. Potrzebuje odpowiedniego odpowietrzenia, aby uwolnić uwięzione powietrze, kanałów chłodzących dla jednolitego krzepnięcia oraz konstrukcji, która umożliwia łatwe wyrzucanie części bez uszkodzeń.
3. Wybór materiału:
Wybór tworzywa termoplastycznego (np. HDPE dla trwałości, PP dla odporności na ciepło, PET dla przejrzystości) zależy od wymagań części - wytrzymałości mechanicznej, odporności chemicznej lub wyglądu. Lepkość materiału wpływa również na to, jak rozciąga się on podczas pompowania.
4. Umieszczenie linii podziału:
Linia podziału, w miejscu styku połówek formy, wpływa na powstawanie wypływek i łatwość przycinania. Umieszczenie jej w niekrytycznych lub mniej widocznych obszarach zmniejsza konieczność obróbki końcowej i poprawia estetykę, zapewniając jednocześnie, że obszary funkcjonalne pozostaną nienaruszone.
5. Współczynnik nadmuchu:
Zdefiniowany jako stosunek średnicy wnęki formy do średnicy parisona, współczynnik rozdmuchu wpływa na rozkład grubości. Zbyt wysoki stosunek (np. >3:1) grozi przerzedzeniem; zbyt niski powoduje marnowanie materiału. Optymalne proporcje (od 1,5:1 do 3:1) są obliczane na podstawie rozmiaru i kształtu części.
6. Kąty i promienie zanurzenia:
Lekkie stożki (kąty pochylenia) i zaokrąglone krawędzie (promienie) ułatwiają usuwanie części, zmniejszają punkty naprężeń i poprawiają przepływ materiału podczas napełniania, minimalizując wady, takie jak pękanie lub nierówne ściany.
7. Konstrukcja typu Pinch-Off:
Zacisk uszczelnia dno parisona, tworząc linię zgrzewu. Mocne ściśnięcie zapobiega wyciekom, zmniejsza wypływ i zapewnia stabilność (np. w przypadku butelek stojących), wymagając precyzyjnego ustawienia formy i ciśnienia.
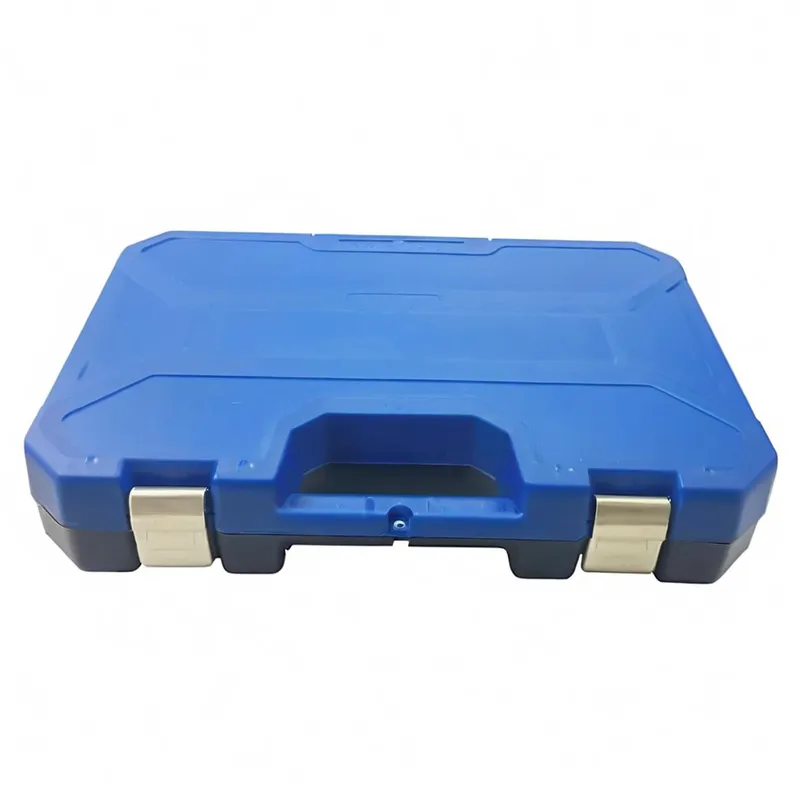
Wytłaczanie z rozdmuchiwaniem w porównaniu do innych procesów formowania
EBM doskonale sprawdza się w przypadku dużych, wydrążonych części, w przeciwieństwie do formowania wtryskowego z rozdmuchiwaniem (IBM), które nadaje się do małych, precyzyjnych elementów, lub formowania rotacyjnego (RM), idealnego do bardzo dużych części, ale wolniejszego i droższego. Patrz tabela poniżej:
Proces | Najlepsze dla | Zalety | Ograniczenia |
---|---|---|---|
EBM | Duże, puste w środku części | Opłacalność, elastyczność | Odpady, etapy wtórne |
IBM | Małe, precyzyjne części | Wysoka precyzja | Wyższe koszty, ograniczenia rozmiaru |
RM | Bardzo duże części | Jednolita grubość | Powolny, drogi |
Jakie są najczęstsze wady wytłaczania z rozdmuchiwaniem?
Usterki w EBM mogą negatywnie wpływać na jakość, ale można sobie z nimi poradzić dzięki odpowiednim dostosowaniom. Oto lista typowych problemów i ich rozwiązań:
1. Nierówna grubość ścianki:
Przyczyna: Zwisający parison, niespójne ustawienia matrycy lub złe programowanie.
Poprawka: Wdrożenie programowania parisona w celu zmiany grubości w zależności od potrzeb lub użycie systemów wsparcia (np. pierścieni powietrznych) w celu ustabilizowania parisona podczas wytłaczania.
2. Blowouts:
Przyczyna: Nadmierne ciśnienie powietrza lub słabe obszary parisona spowodowane nierównomiernym ogrzewaniem.
Poprawka: Obniż ciśnienie nadmuchu, zapewnij jednolitą temperaturę topnienia lub zmień materiał na bardziej wytrzymały, aby wytrzymać nadmuchiwanie.
3. Lampa błyskowa:
Przyczyna: Nadmiar materiału na linii podziału spowodowany niewspółosiowością lub zużyciem formy.
Poprawka: Precyzyjne wyrównywanie form, konserwacja lub wymiana zużytych komponentów i regulacja siły zacisku w celu uniknięcia nadmiernego pakowania.
4. Wypaczenie:
Przyczyna: Nierównomierne chłodzenie powodujące wewnętrzne naprężenia i odkształcenia.
Poprawka: Zoptymalizuj chłodzenie poprzez dostosowanie przepływu wody lub temperatury formy i zapewnij stałą grubość ścianki, aby zrównoważyć szybkość krzepnięcia.
5. Linie spawania:
Przyczyna: Słabe szwy w punktach zaciskania spowodowane niskim ciśnieniem lub słabym stopieniem materiału.
Poprawka: Popraw konstrukcję zacisku, zwiększ siłę zacisku lub dostosuj temperaturę stopu, aby uzyskać lepszy przepływ i wiązanie.
6. Wady powierzchni (np. smugi, pęcherzyki):
Przyczyna: Zanieczyszczenia, wilgoć w żywicy lub nieprawidłowe topienie.
Poprawka: Używaj suchych, czystych materiałów i dostosuj ustawienia ekstrudera (prędkość ślimaka, ciepło bębna), aby uzyskać płynniejsze topienie.
Prototypowanie i produkcja małoseryjna w EBM
Prototypowanie i produkcja małoseryjna w EBM dostosowują proces do małych ilości, koncentrując się na kosztach i elastyczności. Oto jak to osiągnąć:
1. Mniejsze maszyny:
Stosowane są kompaktowe maszyny EBM, wymagające mniej energii i czasu konfiguracji niż systemy pełnowymiarowe. Są idealne do testowania lub produkcji ograniczonych serii bez dużych inwestycji.
2. Formy drukowane 3D:
Szybkie prototypowanie z wykorzystaniem form drukowanych 3D skraca czas realizacji i obniża koszty. Chociaż są one mniej trwałe niż formy metalowe, wystarczają do wstępnych projektów lub małych partii, umożliwiając szybkie iteracje.
3. Wytłaczanie przerywane:
Ta metoda, często wykorzystująca głowice akumulatorowe, przechowuje stopiony plastik i uwalnia go w razie potrzeby, oferując precyzyjną kontrolę nad formowaniem parisonów - idealna do małych, szczegółowych serii lub prototypów.
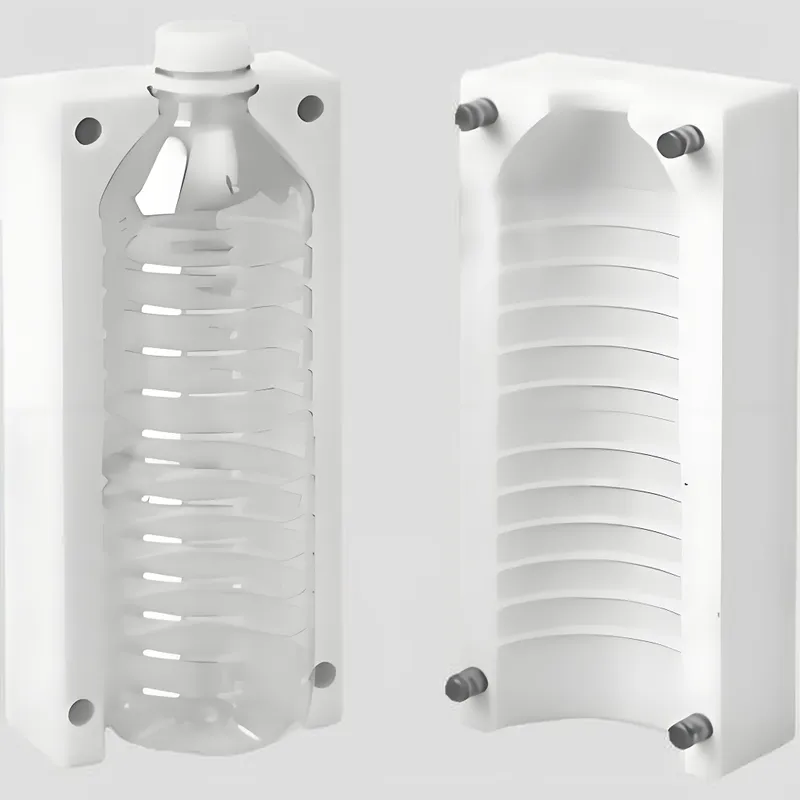
4. Uproszczone oprzyrządowanie:
Formy jednogniazdowe lub podstawowe oprzyrządowanie zmniejszają koszty w porównaniu z konfiguracjami wielogniazdowymi, umożliwiając niedrogie testowanie koncepcji przed zwiększeniem skali.
5. Elastyczne regulacje:
Regulowane parametry EBM (np. temperatura, ciśnienie) i wszechstronność materiału umożliwiają eksperymentowanie z różnymi żywicami lub ustawieniami w celu skutecznego udoskonalania prototypów.
Zrównoważony rozwój i recykling w wytłaczaniu z rozdmuchiwaniem
EBM przyczynia się do zrównoważonego rozwoju i recyklingu poprzez innowacyjne praktyki, które zmniejszają wpływ na środowisko. Oto w jaki sposób:
1. Materiały z recyklingu:
Wykorzystanie poużytkowych tworzyw sztucznych pochodzących z recyklingu (np. rHDPE) w EBM zmniejsza zależność od żywic pierwotnych. Wiele produktów, takich jak opakowania, zawiera obecnie do 50% materiałów pochodzących z recyklingu, zachowując wydajność przy jednoczesnym zmniejszeniu ilości odpadów.
2. Biodegradowalne tworzywa sztuczne:
Postępy w dziedzinie biodegradowalnych tworzyw termoplastycznych dla EBM oferują przyjazne dla środowiska alternatywy, rozkładające się naturalnie i zmniejszające długoterminowe zanieczyszczenie, zwłaszcza w zastosowaniach jednorazowego użytku.
3. Optymalizacja projektu:
Cieńsze ścianki, opływowe kształty i zredukowane wypływki dzięki lepszemu projektowaniu form zmniejszają zużycie materiału i ilość odpadów, zwiększając wydajność bez poświęcania jakości.
4. Energooszczędne maszyny:
Nowoczesny sprzęt EBM wyposażony jest w energooszczędne technologie, takie jak napędy o zmiennej prędkości i ulepszone ogrzewanie, obniżające ślad węglowy procesu.
5. Recykling w obiegu zamkniętym:
Złom produkcyjny (np. Flash) jest ponownie mielony i wykorzystywany na miejscu, minimalizując ilość odpadów i wspierając gospodarkę o obiegu zamkniętym w procesie produkcyjnym.
6. Lekkość:
Tworzenie lżejszych części zmniejsza zużycie materiałów i energii transportowej, co jest zgodne z celami zrównoważonego rozwoju przy jednoczesnym spełnieniu standardów wydajności.
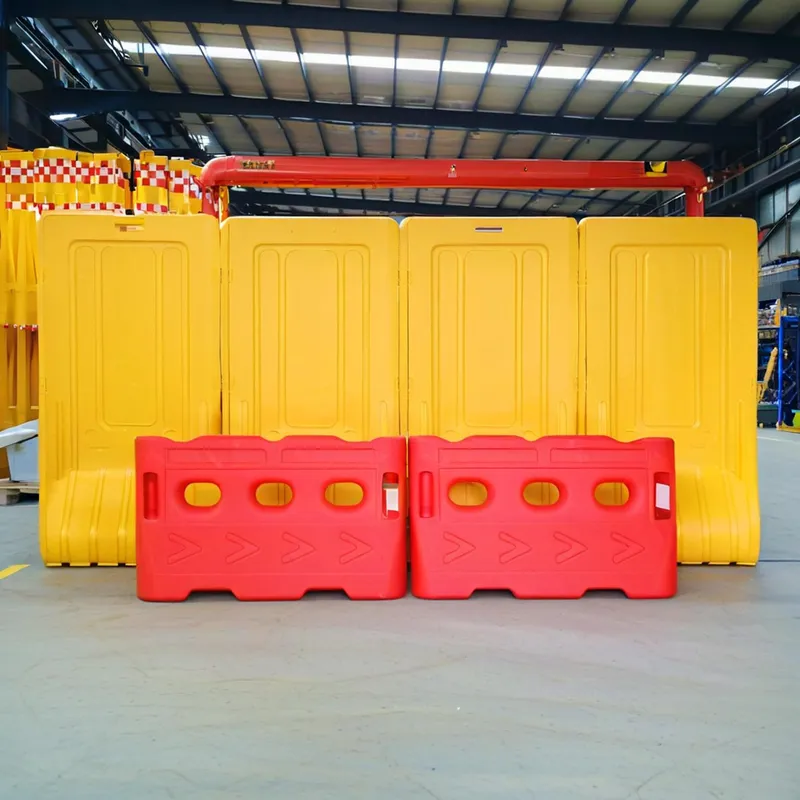
najczęściej zadawane pytania dla klientów
Pierwsze kroki z Uplastech
Masz pytania? Mamy odpowiedzi.
Specjalizujemy się w wytłaczaniu, formowaniu próżniowym, rozdmuchiwaniu i precyzyjnym wytwarzaniu form, oferując niestandardowe rozwiązania spełniające różnorodne potrzeby produkcyjne.
Współpracujemy z różnymi branżami, w tym motoryzacyjną, elektroniczną, dóbr konsumpcyjnych i opakowań, koncentrując się na partnerstwie B2B i dostarczaniu rozwiązań w zakresie wytłaczania, termoformowania, rozdmuchiwania i precyzyjnego formowania.
Tak, dostosowujemy nasze rozwiązania do Twoich unikalnych wymagań.
Skontaktuj się
Napisz do nas lub wypełnij poniższy formularz, aby uzyskać wycenę.
E-mail: uplastech@gmail.com