Wydajne rozwiązania do formowania wtryskowego z rozdmuchiwaniem
Odkryj najwyższej klasy techniki formowania wtryskowego z rozdmuchiwaniem w Uplastech. Zwiększ wydajność produkcji dzięki naszym innowacyjnym rozwiązaniom do różnych zastosowań.
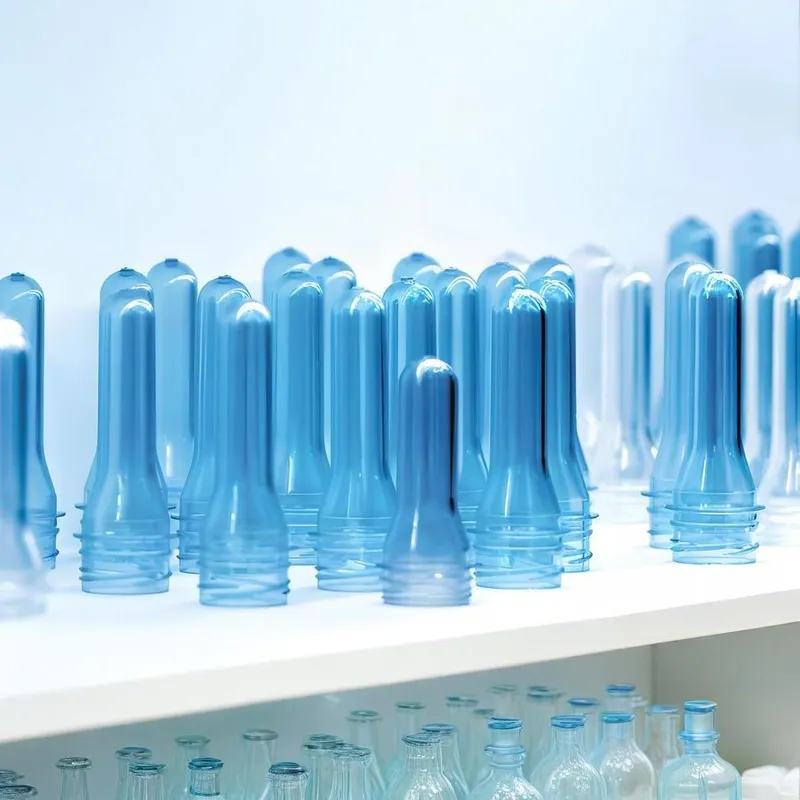
Przewodnik po niestandardowych rozwiązaniach do formowania wtryskowego z rozdmuchiwaniem
Co to jest formowanie wtryskowe z rozdmuchiwaniem?
Formowanie wtryskowe z rozdmuchiwaniem (IBM) to technika produkcji wykorzystywana do wytwarzania pustych w środku przedmiotów z tworzyw sztucznych, takich jak butelki i pojemniki, poprzez integrację formowania wtryskowego i rozdmuchiwania. Proces rozpoczyna się od wstrzyknięcia stopionego tworzywa sztucznego do formy w celu uformowania preformy - małego, przypominającego rurkę kształtu z zamkniętym końcem. Preforma ta jest następnie przenoszona do stacji formowania z rozdmuchiwaniem, gdzie jest nadmuchiwana sprężonym powietrzem, aby przybrać kształt ostatecznej formy. Po schłodzeniu produkt jest wyrzucany i gotowy do użycia. IBM jest ceniony za zdolność do tworzenia cienkościennych, wysokiej jakości produktów o jednolitej grubości i przejrzystości, co czyni go najlepszym wyborem dla branż takich jak opakowania i farmaceutyki.
IBM działa w dwóch głównych wariantach: proces jednoetapowy, w którym preforma jest formowana i rozdmuchiwana w jednym ciągłym cyklu, oraz proces dwuetapowy, w którym preformy są formowane, chłodzone i przechowywane przed ponownym podgrzaniem i późniejszym rozdmuchaniem. Ta elastyczność sprawia, że IBM nadaje się zarówno do małych, jak i dużych serii produkcyjnych. Proces ten wyróżnia się wytwarzaniem w pełni gotowych produktów bez nadmiaru materiału (flash), oferując czyste i wydajne rozwiązanie dla przedmiotów wymagających precyzji, takich jak butelki na napoje, słoiki kosmetyczne i pojemniki medyczne.
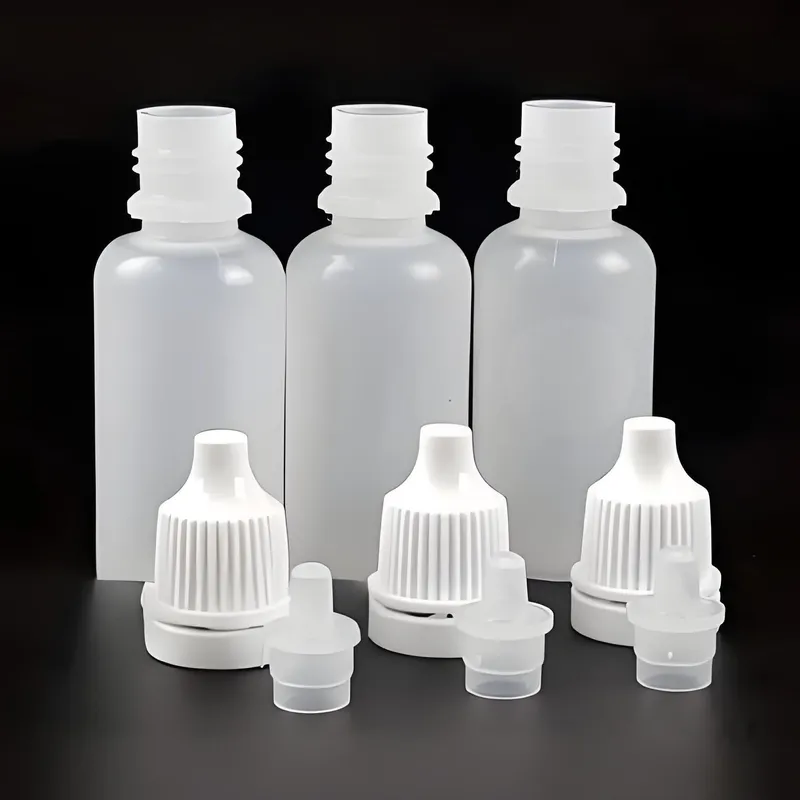
Jak działa formowanie wtryskowe z rozdmuchiwaniem? Przewodnik krok po kroku
Formowanie wtryskowe z rozdmuchiwaniem (IBM) to proces produkcyjny, który łączy precyzję formowania wtryskowego z wydajnością formowania z rozdmuchiwaniem w celu wytworzenia wysokiej jakości pustych w środku produktów z tworzyw sztucznych, takich jak butelki, słoiki i pojemniki. Metoda ta jest szeroko stosowana w branżach takich jak farmaceutyczna, kosmetyczna i opakowań żywności ze względu na jej zdolność do tworzenia małych, złożonych części o doskonałej konsystencji i minimalnej ilości odpadów. Poniżej znajduje się szczegółowy przewodnik krok po kroku, jak działa formowanie wtryskowe z rozdmuchiwaniem.
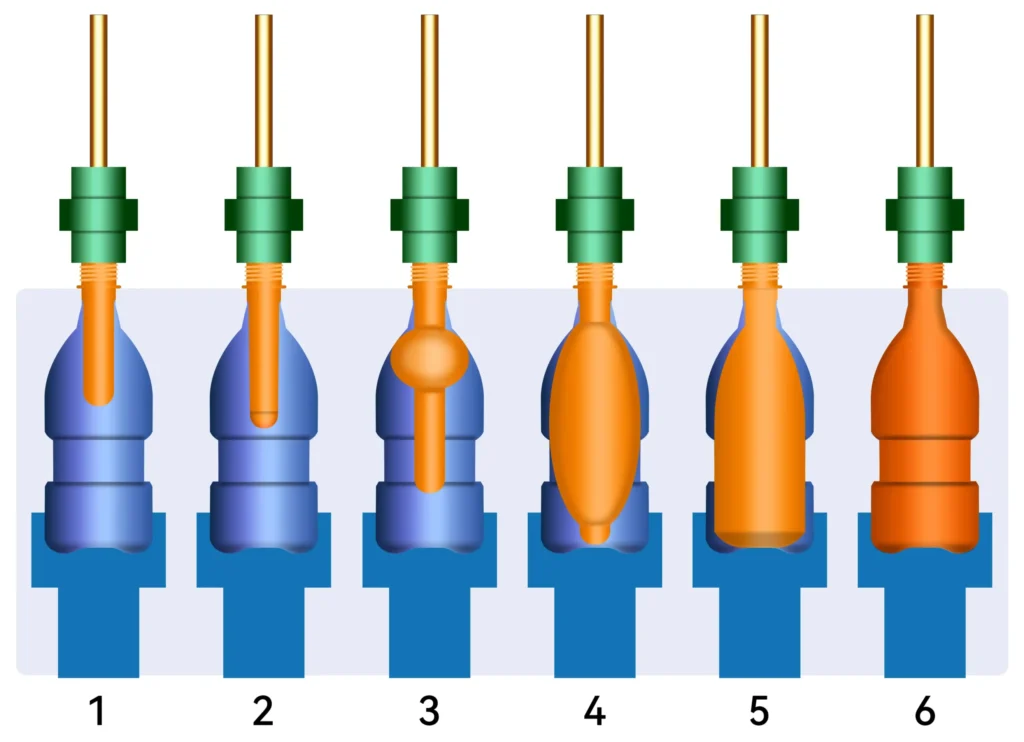
Krok 1: Formowanie wtryskowe (tworzenie preform):
Proces rozpoczyna się od formowania wtryskowego. Plastikowe granulki, takie jak politereftalan etylenu (PET) lub polietylen o wysokiej gęstości (HDPE), są podawane do wtryskarki. Tworzywo sztuczne jest podgrzewane do momentu stopienia, a następnie wtryskiwane pod wysokim ciśnieniem do gniazda formy. Forma ta kształtuje stopione tworzywo sztuczne w preformę - małą, przypominającą rurkę strukturę z wykończoną szyjką (np. gwintem zakrętki butelki) i grubą ścianką, która zostanie później rozciągnięta podczas etapu rozdmuchiwania.
- Preforma zawiera dokładną ilość tworzywa sztucznego potrzebną do wytworzenia produktu końcowego, co zmniejsza ilość odpadów.
- Wykończenie szyjki jest w pełni uformowane na tym etapie i pozostaje niezmienione przez cały proces.
Krok 2: Przeniesienie do stacji formowania z rozdmuchiwaniem:
Po utworzeniu preformy jest ona przenoszona do stacji rozdmuchiwania. Może się to odbywać ręcznie lub automatycznie, w zależności od konfiguracji. W systemach zautomatyzowanych stół obrotowy lub chwytak sprawnie przesuwa preformę, zachowując jej kształt.
- W procesie jednoetapowym preforma jest przenoszona natychmiast, gdy jest jeszcze ciepła.
- W dwuetapowym procesie preformy są chłodzone, przechowywane i ponownie podgrzewane w celu rozdmuchania.
Krok 3: Podgrzewanie preformy:
Na stanowisku formowania z rozdmuchiwaniem preforma jest podgrzewana do określonej temperatury, w której staje się miękka i giętka, ale nie w pełni stopiona. Przygotowuje to tworzywo sztuczne do rozciągania podczas etapu rozdmuchiwania.
- Na przykład preformy PET są zwykle podgrzewane do temperatury 90-110°C.
- Równomierne nagrzewanie ma kluczowe znaczenie dla zapewnienia równomiernego rozciągania i uniknięcia wad, takich jak nierówna grubość ścianki.
Krok 4: Nadmuchiwanie preformy:
Podgrzana preforma jest zaciskana w formie rozdmuchowej, która odpowiada kształtowi produktu końcowego. Wprowadzany jest trzpień lub igła, a sprężone powietrze (zwykle o ciśnieniu 2-4 MPa lub 290-580 psi) jest wdmuchiwane do preformy. Ciśnienie powietrza powoduje, że preforma rozszerza się i rozciąga, dopasowując się do wewnętrznych ścian formy.
- Tworzywo sztuczne rozciąga się dwuosiowo (promieniowo i osiowo), rozrzedzając się, tworząc ścianki produktu.
- Szyja, już ukończona, pozostaje niezmieniona.
Krok 5: Chłodzenie formy:
Po tym, jak preforma przyjmie kształt formy, jest ona chłodzona w celu zestalenia tworzywa sztucznego. W tym celu przez kanały w formie zazwyczaj przepływa zimna woda.
- Równomierne chłodzenie zapobiega wypaczeniom i zniekształceniom.
- Czas chłodzenia zależy od materiału i grubości ścianki, ale jest zoptymalizowany pod kątem wydajności.
Krok 6: Wyrzucenie gotowego produktu:
Po stwardnieniu tworzywa sztucznego forma otwiera się, a gotowy produkt jest wyrzucany. Jest on teraz gotowy do pakowania lub dodatkowego przetwarzania, takiego jak etykietowanie lub napełnianie.
- IBM produkuje w pełni wykończone produkty bez nadmiaru materiału, eliminując etapy przycinania.
- Proces ten zapewnia wysoką powtarzalność i stałą jakość.
Jakie materiały są powszechnie stosowane w formowaniu wtryskowym z rozdmuchiwaniem?
Formowanie wtryskowe z rozdmuchiwaniem powszechnie wykorzystuje materiały termoplastyczne, takie jak PET, HDPE, PP i PVC, z których każdy jest wybierany ze względu na swoje specyficzne właściwości, które są zgodne z potrzebami produktu końcowego. PET (politereftalan etylenu) jest preferowany do butelek na napoje ze względu na jego przejrzystość i właściwości bariery gazowej, podczas gdy HDPE (polietylen o wysokiej gęstości) jest wybierany ze względu na jego trwałość i odporność chemiczną, idealny do butelek na detergenty. PP (polipropylen) oferuje odporność na ciepło i elastyczność dla pojemników na żywność, a PVC (polichlorek winylu) zapewnia wszechstronność dla opakowań kosmetycznych.
Wybór materiału ma wpływ na wydajność, koszt i wygląd produktu. Na przykład, przezroczystość PET sprawia, że jest on idealny do prezentacji zawartości, podczas gdy wytrzymałość HDPE nadaje się do zastosowań przemysłowych. Inne materiały, takie jak ABS, polistyren lub poliwęglan, mogą być używane do specjalistycznych potrzeb, takich jak odporność na promieniowanie UV lub zwiększona wytrzymałość. Poniżej znajduje się tabela podsumowująca te materiały i ich kluczowe atrybuty:
Materiał | Kluczowe właściwości | Typowe zastosowania |
---|---|---|
PET | Przejrzystość, bariera gazowa, lekkość | Butelki na napoje |
HDPE | Trwałość, odporność chemiczna | Dzbanki na mleko, butelki na detergenty |
PP | Odporność na ciepło, elastyczność | Pojemniki na żywność, urządzenia medyczne |
PVC | Elastyczność, przejrzystość | Butelki kosmetyczne, rurki |
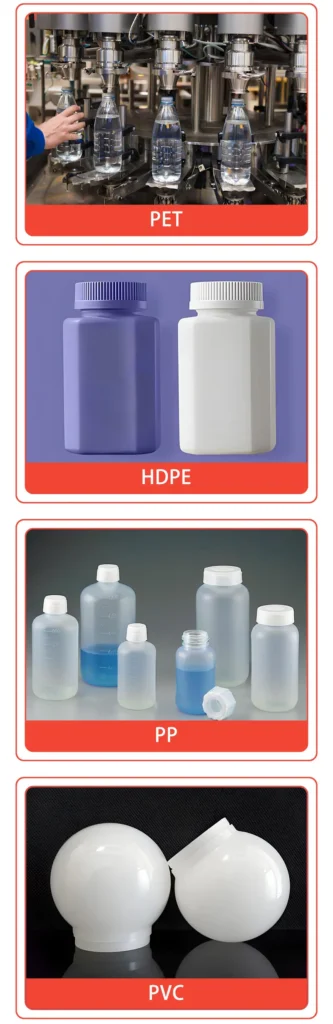
Zalety i wady formowania wtryskowego z rozdmuchiwaniem
Formowanie z rozdmuchiwaniem oferuje wyraźne zalety, w tym produkcję wysokiej jakości, cienkościennych produktów o stałej grubości i bez wypływek, dzięki czemu idealnie nadaje się do małych i średnich pojemników, takich jak butelki i słoiki. Ma jednak wady, takie jak wyższe koszty ze względu na złożone maszyny i wolniejsze tempo produkcji w niektórych zastosowaniach w porównaniu z alternatywami, takimi jak wytłaczanie z rozdmuchiwaniem.
Zalety:
① Najwyższa jakość: Produkuje przedmioty o doskonałej przejrzystości, jednolitych ściankach i precyzyjnych wymiarach.
② No Flash: Eliminuje nadmiar materiału, zmniejszając ilość odpadów i obróbkę końcową.
Wszechstronność: Nadaje się zarówno do wąskich, jak i szerokich otworów.
Wady:
① Koszt: Wymaga drogiego sprzętu i form, co zwiększa początkową inwestycję.
② Szybkość: Może być wolniejsza niż wytłaczanie z rozdmuchiwaniem w przypadku dużych serii.
Ograniczenie rozmiaru: Najlepsze dla mniejszych pojemników, a nie dużych części przemysłowych.
Jakie są typowe zastosowania formowania wtryskowego z rozdmuchiwaniem?
Formowanie wtryskowe z rozdmuchiwaniem jest szeroko stosowane do tworzenia pustych w środku produktów z tworzyw sztucznych, takich jak butelki na napoje, pojemniki na żywność, opakowania farmaceutyczne i słoiki kosmetyczne, wykorzystując jego zdolność do produkcji lekkich, trwałych i atrakcyjnych wizualnie przedmiotów. Jego precyzja i jakość sprawiają, że jest niezastąpiony w branżach wymagających niezawodnych rozwiązań opakowaniowych.
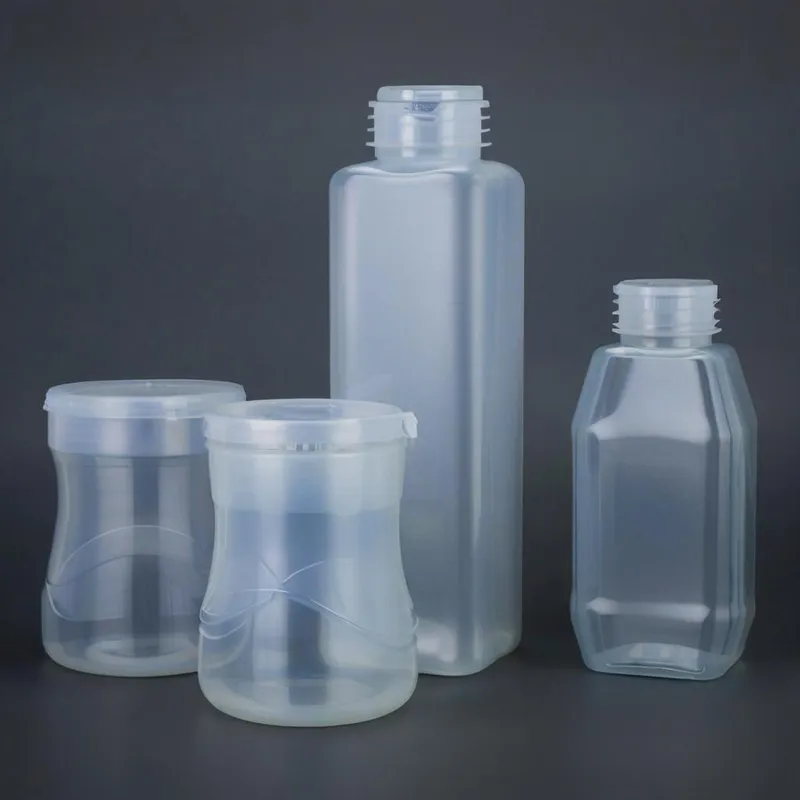
Butelki na napoje:
Butelki PET na wodę i napoje gazowane korzystają z wytrzymałości i przejrzystości IBM.
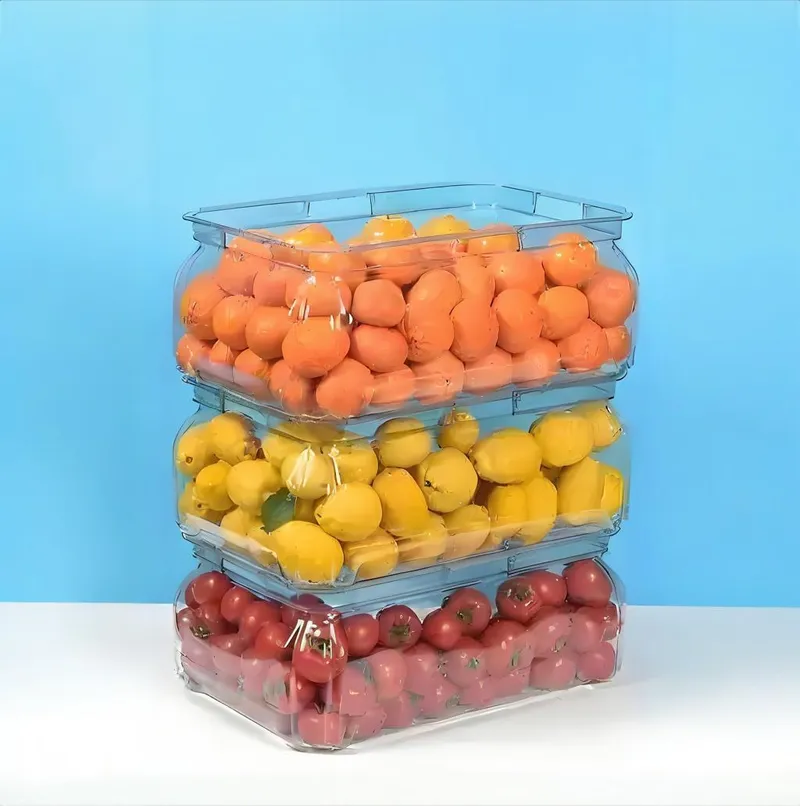
Pojemniki na żywność:
Słoiki na sosy lub żywność dla niemowląt zazwyczaj wykorzystują PP do hermetycznego i bezpiecznego przechowywania.
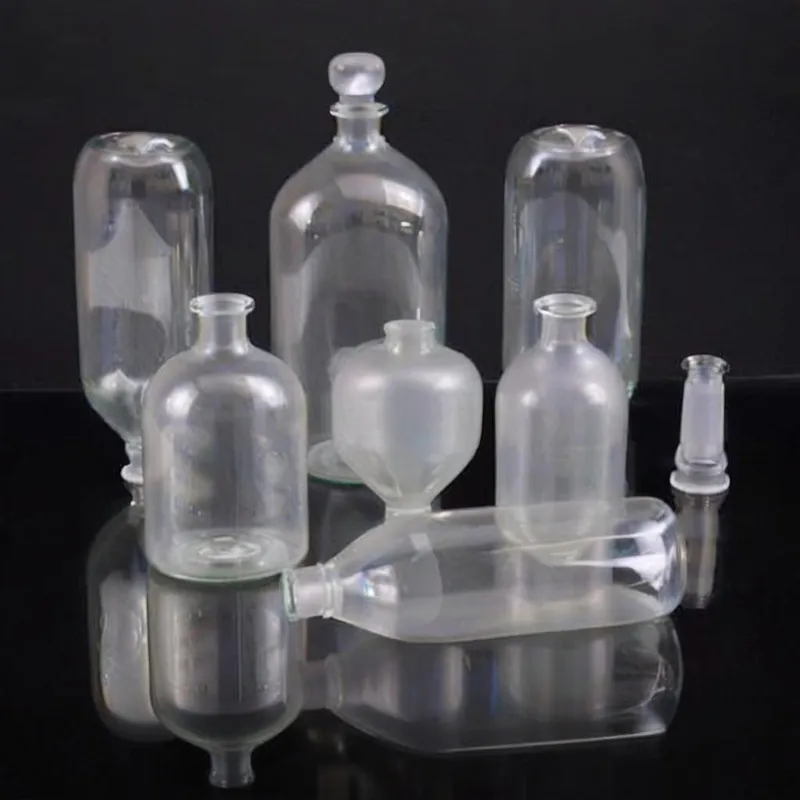
Opakowania medyczne:
Przezroczyste, sterylne pojemniki na leki zapewniają bezpieczeństwo i widoczność.
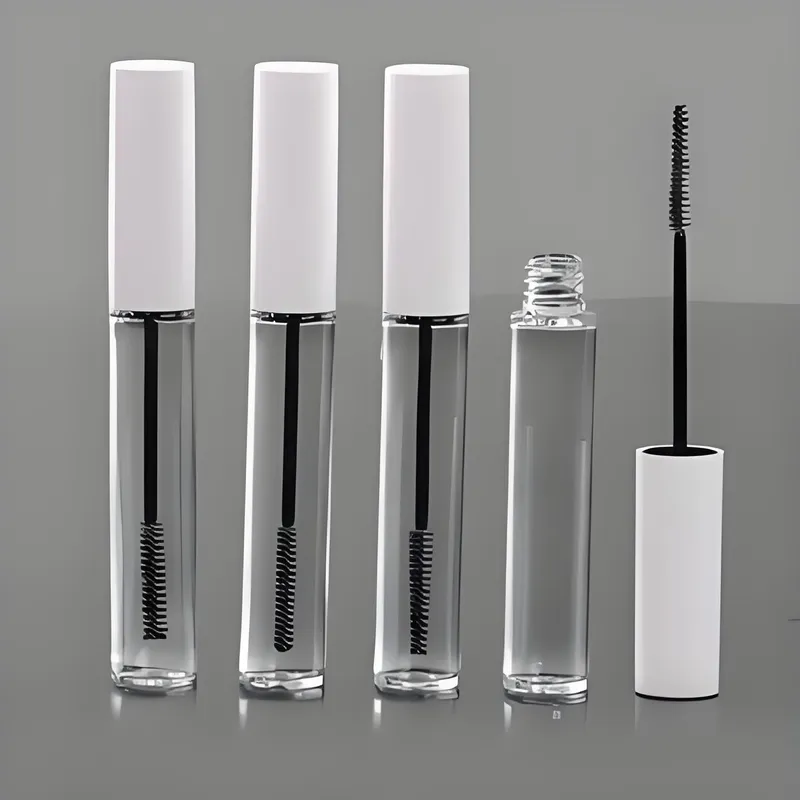
Pojemniki na kosmetyki:
Stylowe butelki na kremy i balsamy pokazują elastyczność projektową IBM.
Formowanie wtryskowe z rozdmuchiwaniem w porównaniu do innych technik formowania
Formowanie wtryskowe z rozdmuchiwaniem wyróżnia się w produkcji pustych, cienkościennych produktów o wysokiej precyzji, w przeciwieństwie do zwykłego formowania wtryskowego, które jest lepsze dla części pełnych, lub formowania wtryskowego z rozdmuchiwaniem, które przedkłada szybkość nad dokładność. IBM wyróżnia się tam, gdzie jakość i estetyka mają kluczowe znaczenie, podczas gdy alternatywy mogą odpowiadać różnym potrzebom.
1. Vs. Wytłaczanie z rozdmuchiwaniem (EBM): EBM jest szybszy i tańszy w przypadku dużych serii, ale produkuje mniej precyzyjne elementy z lampą błyskową. IBM oferuje lepszą jakość i brak konieczności przycinania.
2. Vs. Zwykłe formowanie wtryskowe: Formowanie wtryskowe jest idealne dla części pełnych, ale nie może skutecznie tworzyć pustych konstrukcji, takich jak IBM.
Technika | Najlepsze dla | Plusy | Wady |
---|---|---|---|
IBM | Puste, cienkościenne części | Wysoka precyzja, brak błysku | Wyższy koszt, wolniejsze działanie |
EBM | Duże, proste pojemniki | Szybkość i opłacalność | Mniej precyzyjny, flash |
Formowanie wtryskowe | Części stałe | Wysoka szczegółowość, szybkość | Ograniczone do solidnych konstrukcji |
Formowanie wtryskowe z rozdmuchiwaniem: Kompleksowy przewodnik
Odkryj formowanie wtryskowe z rozdmuchiwaniem: jego proces, zastosowania i zalety w porównaniu z innymi technikami formowania. Idealne rozwiązanie dla producentów poszukujących precyzji i wydajności.
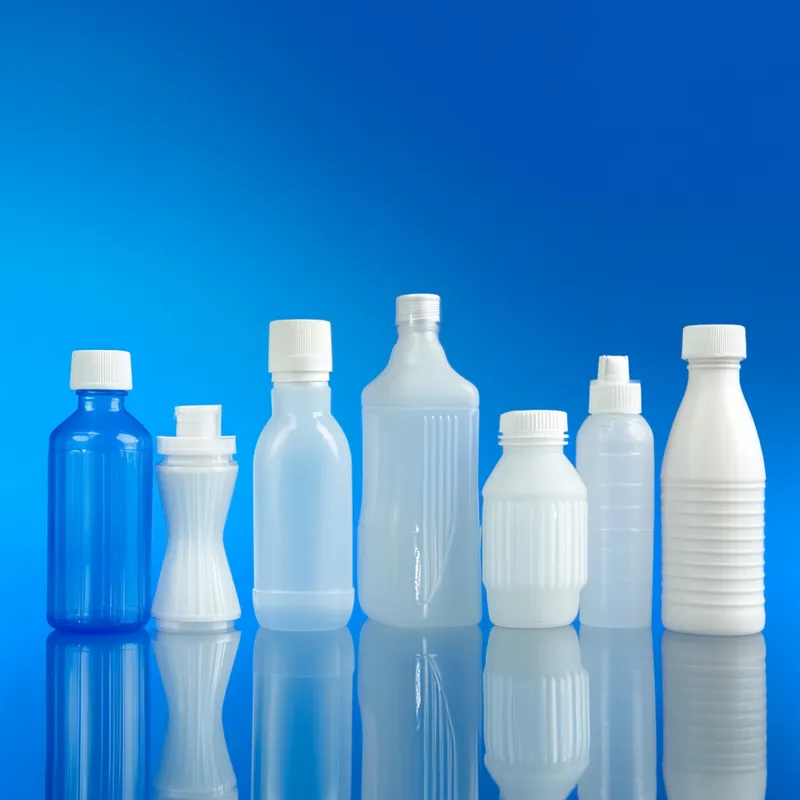
Przewodnik po niestandardowych rozwiązaniach do formowania wtryskowego z rozdmuchiwaniem
- Jaki sprzęt jest wymagany do formowania wtryskowego z rozdmuchiwaniem?
- Jakie są kluczowe wskazówki projektowe dotyczące formowania wtryskowego z rozdmuchiwaniem?
- Jakie są typowe wady formowania wtryskowego z rozdmuchiwaniem?
- Jak można zoptymalizować formowanie wtryskowe z rozdmuchiwaniem?
- Jakie czynniki środowiskowe należy wziąć pod uwagę?
- Jak wybrać odpowiedni materiał do formowania wtryskowego z rozdmuchiwaniem?
Jaki sprzęt jest wymagany do formowania wtryskowego z rozdmuchiwaniem?
Formowanie wtryskowe z rozdmuchiwaniem (IBM) to precyzyjny proces produkcyjny, który łączy formowanie wtryskowe i rozdmuchiwanie w celu wytworzenia wysokiej jakości pustych w środku produktów z tworzyw sztucznych, takich jak butelki i pojemniki. Aby to osiągnąć, wymaganych jest kilka specjalistycznych urządzeń, z których każde odgrywa kluczową rolę w procesie. Oto szczegółowe spojrzenie na niezbędny sprzęt:
1. Maszyna do formowania wtryskowego:
Jest to serce procesu IBM, odpowiedzialne za tworzenie preformy - małego, przypominającego rurkę kształtu z tworzywa sztucznego, który służy jako punkt wyjścia dla produktu końcowego. Maszyna topi żywicę z tworzywa sztucznego (np. PET lub HDPE) i wtryskuje ją do formy pod wysokim ciśnieniem. Składa się z jednostki wtryskowej, która kontroluje przepływ stopionego tworzywa sztucznego, oraz systemu zaciskowego do bezpiecznego mocowania formy. Precyzja tej maszyny zapewnia, że preforma ma spójne wymiary i rozkład materiału, które są niezbędne do późniejszego równomiernego rozdmuchiwania.
2. Stacja formowania z rozdmuchiwaniem:
Po uformowaniu preformy jest ona przenoszona do stacji rozdmuchiwania, gdzie jest nadmuchiwana do ostatecznego kształtu. Stacja ta obejmuje formę rozdmuchową, która definiuje zewnętrzne kontury produktu oraz system dostarczania sprężonego powietrza (zazwyczaj 2-4 MPa lub 290-580 psi). Powietrze rozszerza podgrzaną preformę, aż dopasuje się ona do wnętrza formy, tworząc pusty obiekt. Stacja formowania z rozdmuchiwaniem musi utrzymywać precyzyjne ciśnienie i czas, aby uniknąć wad, takich jak niepełne rozprężenie.
3. Formy:
IBM wymaga dwóch różnych form: formy wtryskowej do kształtowania preformy i formy rozdmuchowej do formowania produktu końcowego. Formy te są zwykle wykonane z trwałych materiałów, takich jak stal lub aluminium, zaprojektowanych tak, aby wytrzymywały wysokie temperatury i ciśnienia. Forma wtryskowa tworzy krytyczne elementy, takie jak wykończenie szyjki, podczas gdy forma rozdmuchowa określa kształt korpusu. Konstrukcja i jakość formy bezpośrednio wpływają na spójność produktu i wydajność produkcji.
4. Sprzęt kondycjonujący (opcjonalnie):
W niektórych konfiguracjach IBM, szczególnie w procesach jednoetapowych, stacja kondycjonowania jest używana do regulacji temperatury preformy przed rozdmuchiwaniem. Zapewnia to, że tworzywo sztuczne jest wystarczająco miękkie, aby równomiernie się rozciągać, ale nie tak gorące, że odkształca się w niekontrolowany sposób. Kondycjonowanie może obejmować strefy ogrzewania lub chłodzenia, w zależności od materiału i wymagań produktu, i ma kluczowe znaczenie dla uzyskania przejrzystości i wytrzymałości produktów takich jak butelki PET.
5. Mechanizm transferu:
Aby przemieszczać preformę między stacjami, systemy IBM wykorzystują mechanizm przenoszenia, taki jak stół obrotowy, system indeksowania lub pręty rdzeniowe. W maszynach wielostanowiskowych pręty rdzeniowe przytrzymują preformę, gdy przechodzi ona od wtrysku przez kondycjonowanie (jeśli dotyczy) do rozdmuchu. Ta automatyzacja zapewnia ciągły przepływ pracy, minimalizując opóźnienia i utrzymując wyrównanie w celu precyzyjnego formowania.
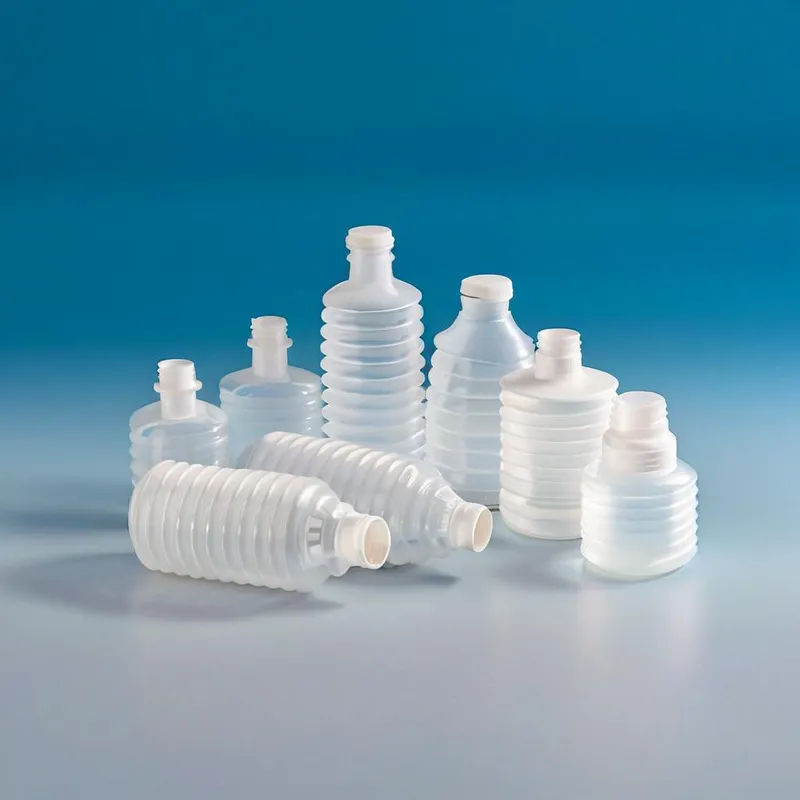
Jakie są kluczowe wskazówki projektowe dotyczące formowania wtryskowego z rozdmuchiwaniem?
Projektowanie dla formowania wtryskowego z rozdmuchiwaniem wymaga starannego planowania, aby proces przebiegał płynnie, a produkt końcowy spełniał standardy jakości i funkcjonalności. Kluczowe kwestie obejmują projekt preformy, wybór materiału i określone czynniki geometryczne. Poniżej przedstawiamy najważniejsze aspekty projektowania:
1. Konstrukcja preformy:
Preforma jest kamieniem węgielnym IBM, a jej konstrukcja określa sposób, w jaki tworzywo sztuczne rozciąga się podczas rozdmuchiwania. Preforma musi być dostosowana do kształtu produktu końcowego, z precyzyjną kontrolą jej długości, średnicy i grubości ścianek. Źle zaprojektowana preforma może prowadzić do nierównomiernego rozciągania, powodując powstawanie cienkich miejsc lub nadmiaru materiału. Na przykład butelka o szerokim korpusie wymaga preformy o grubszych ściankach w obszarach, które będą się bardziej rozciągać, zapewniając jednolitą grubość gotowego produktu.
2. Wykończenie szyjki:
Szyjka produktu - często zawierająca gwinty, elementy zatrzaskowe lub powierzchnie uszczelniające - jest formowana na etapie wtrysku i pozostaje niezmieniona podczas rozdmuchiwania. Wymaga to wysokiej precyzji formy wtryskowej, aby zapewnić dopasowanie szyjki do nakrętek lub zamknięć. Projektanci muszą wziąć pod uwagę tolerancje i skurcz, aby uniknąć wycieków lub problemów z kompatybilnością, szczególnie w zastosowaniach takich jak butelki na napoje.
3. Wybór materiału:
Wybór tworzywa sztucznego wpływa zarówno na przetwarzalność, jak i wydajność produktu. Typowe materiały IBM obejmują politereftalan etylenu (PET), polietylen o wysokiej gęstości (HDPE) i polipropylen (PP), wybrane ze względu na ich rozciągliwość i wytrzymałość. Materiał musi mieć odpowiedni wskaźnik płynięcia i właściwości termiczne, aby wytrzymać wtryskiwanie i rozdmuchiwanie bez degradacji. Na przykład PET jest preferowany ze względu na swoją przejrzystość i właściwości barierowe w opakowaniach.
4. Grubość ścianki i współczynnik wydmuchu:
Osiągnięcie jednolitej grubości ścianki jest głównym celem IBM. Współczynnik rozdmuchu - stosunek średnicy produktu końcowego do średnicy preformy - musi być zoptymalizowany (zwykle od 1,5 do 3), aby zapobiec nadmiernemu rozrzedzeniu lub niepełnemu rozszerzeniu. Projektanci obliczają to na podstawie kształtu produktu i właściwości materiału, odpowiednio dostosowując preformę.
5. Kąty zanurzenia i zwolnienie części:
Uwzględnienie w projekcie niewielkich kątów pochylenia (1-2 stopnie) ułatwia wyjmowanie produktu z formy. Bez tych kątów tworzywo sztuczne może się przykleić, prowadząc do uszkodzenia powierzchni lub opóźnień w produkcji. Jest to szczególnie ważne w przypadku głębokich lub złożonych kształtów.
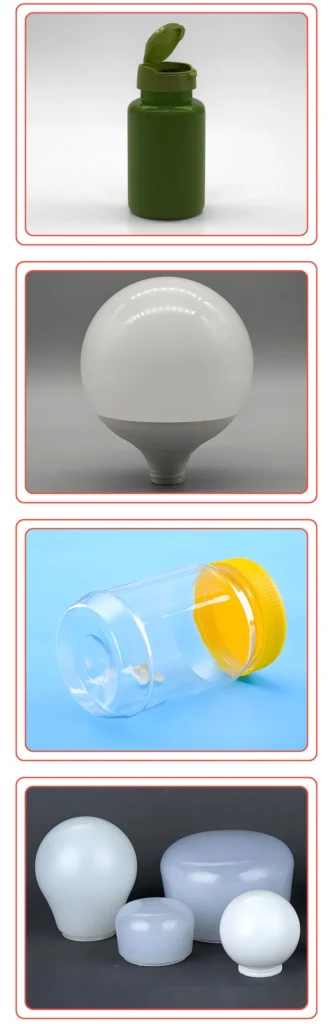
Jakie są typowe wady formowania wtryskowego z rozdmuchiwaniem?
Formowanie wtryskowe z rozdmuchiwaniem może wytwarzać wyjątkowe produkty, ale może pojawić się kilka typowych wad, jeśli proces nie jest dokładnie kontrolowany. Zrozumienie tych kwestii, ich przyczyn i metod zapobiegania jest kluczem do utrzymania jakości. Oto najczęstsze wady:
1. Nierówna grubość ścianki:
Dzieje się tak, gdy preforma rozciąga się nierównomiernie, powodując powstawanie cienkich lub grubych miejsc. Przyczyny obejmują niewłaściwą konstrukcję preformy (np. nieprawidłowy rozkład grubości ścianek), nierównomierne nagrzewanie lub nieoptymalne ciśnienie rozdmuchu. Cienkie obszary osłabiają produkt, podczas gdy grube obszary zwiększają koszty materiału. Regularna kalibracja ustawień temperatury i ciśnienia może złagodzić ten problem.
3. Wypaczenie:
Wypaczenie ma miejsce, gdy produkt zniekształca się po wyrzuceniu, często z powodu nierównomiernego chłodzenia lub naprężeń szczątkowych w tworzywie sztucznym. Na przykład, jeśli jedna strona stygnie szybciej niż druga, produkt może się wygiąć. Aby temu zapobiec, należy zapewnić równomierne chłodzenie w całej formie i zapewnić odpowiedni czas chłodzenia przed wyjęciem.
3. Niekompletny nadmuch:
Wada ta powoduje zniekształcenie produktu, ponieważ preforma nie rozszerza się w pełni, aby wypełnić formę. Może to wynikać z niewystarczającego ciśnienia powietrza, zatkanego kanału powietrznego lub zbyt niskiej temperatury preformy. Sprawdzenie systemów dostarczania powietrza i temperatury preformy może rozwiązać ten problem.
4. Niedoskonałości powierzchni:
Pęcherzyki, smugi lub szorstkie plamy na powierzchni produktu mogą wynikać z zanieczyszczonej żywicy, nadmiernej wilgoci lub słabej wentylacji formy. Wady te wpływają na estetykę, a w niektórych przypadkach także na funkcjonalność. Używanie czystych, suchych materiałów i utrzymywanie form z odpowiednimi otworami wentylacyjnymi może wyeliminować problemy z powierzchnią.
Jak można zoptymalizować formowanie wtryskowe z rozdmuchiwaniem?
Optymalizacja procesu formowania wtryskowego z rozdmuchiwaniem zwiększa wydajność, obniża koszty i poprawia jakość produktu. Wiąże się to z dostrajaniem parametrów procesu, modernizacją sprzętu i wdrażaniem inteligentnych technologii. Oto jak osiągnąć optymalizację:
1. Kontrola temperatury:
Precyzyjne zarządzanie temperaturą ma kluczowe znaczenie na każdym etapie. Podczas wtrysku tworzywo sztuczne musi być równomiernie stopione, podczas gdy preforma musi mieć optymalną temperaturę (np. 90-110°C dla PET) do rozdmuchiwania. Przegrzanie może spowodować degradację materiału, podczas gdy niedogrzanie uniemożliwia prawidłowe rozciąganie. Nowoczesne systemy z czujnikami temperatury w czasie rzeczywistym zapewniają spójność.
2. Regulacja ciśnienia nadmuchu:
Ciśnienie powietrza używanego do nadmuchiwania preformy musi odpowiadać materiałowi i konstrukcji produktu. Zbyt wysokie ciśnienie grozi rozerwaniem preformy, podczas gdy zbyt niskie ciśnienie powoduje niepełne nadmuchanie. Dokładne dostrojenie ciśnienia (zazwyczaj 2-4 MPa) w oparciu o próbne uruchomienia może osiągnąć idealną grubość ścianki i kształt.
3. Skrócenie czasu cyklu:
Skrócenie czasu każdego etapu - wtrysku, transferu, rozdmuchu i chłodzenia - zwiększa wydajność produkcji. Jednak musi to być zrównoważone z jakością; na przykład zbytnie skrócenie czasu chłodzenia może spowodować wypaczenie. Wydajne systemy chłodzenia form (np. kanały wodne) pomagają utrzymać jakość przy szybszych cyklach.
4. Optymalizacja formy:
Ulepszona konstrukcja formy z ulepszonymi kanałami chłodzenia, lepszą wentylacją i trwałymi materiałami skraca czas cyklu i zmniejsza liczbę defektów. Na przykład formy z wkładkami z miedzi berylowej poprawiają transfer ciepła, przyspieszając chłodzenie bez uszczerbku dla precyzji.
5. Zaawansowane technologie:
Wdrożenie oprogramowania do monitorowania procesów lub zautomatyzowanych systemów kontroli jakości umożliwia wprowadzanie korekt w czasie rzeczywistym i wczesne wykrywanie wad. Narzędzia te analizują dane, takie jak trendy ciśnienia i temperatury, dynamicznie optymalizując proces.
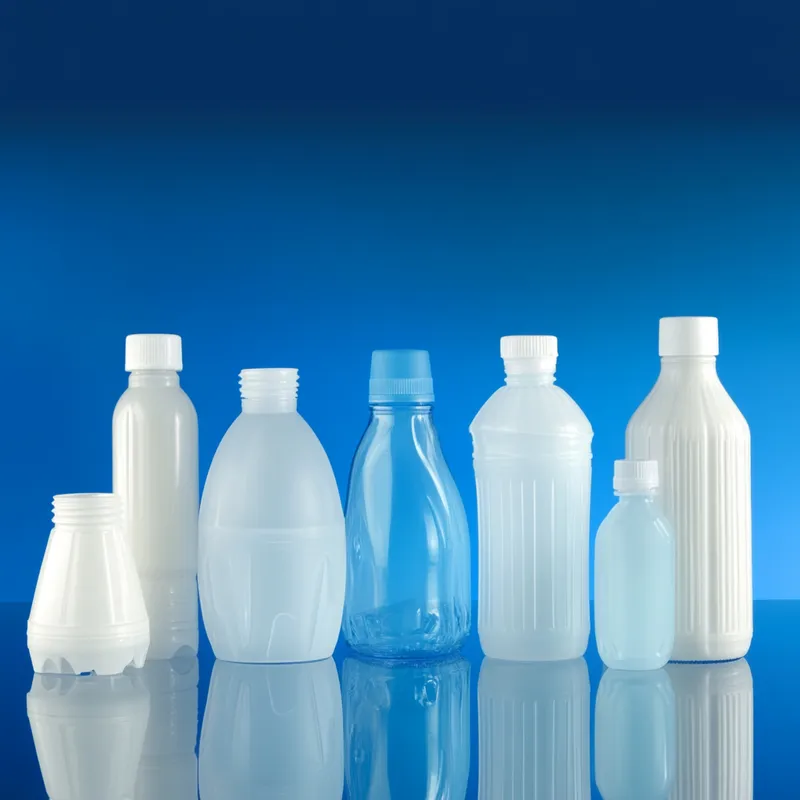
Jakie czynniki środowiskowe należy wziąć pod uwagę?
Zrównoważony rozwój jest coraz ważniejszy w produkcji, a formowanie wtryskowe z rozdmuchiwaniem musi uwzględniać wpływ na środowisko związany z materiałami, energią i odpadami. Oto kluczowe czynniki, które należy wziąć pod uwagę:
1. Materiały z recyklingu:
Korzystanie z tworzyw sztucznych pochodzących z recyklingu, takich jak rPET, zmniejsza zależność od zasobów pierwotnych i wspiera cele zrównoważonego rozwoju. Przykładowo, wiele butelek PET zawiera obecnie 25-50% materiału pochodzącego z recyklingu bez utraty jakości. Zapewnienie, że materiał pochodzący z recyklingu jest czysty i kompatybilny z IBM ma kluczowe znaczenie dla uzyskania spójnych wyników.
2. Zużycie energii:
Urządzenia IBM, w szczególności stacje wtrysku i rozdmuchu, mogą być energochłonne. Przejście na energooszczędne maszyny z napędami o zmiennej prędkości lub systemami odzyskiwania ciepła obniża zużycie energii. Optymalizacja czasów cyklu i temperatur również zmniejsza zapotrzebowanie na energię bez wpływu na wydajność.
3. Zarządzanie odpadami:
IBM produkuje minimalną ilość odpadów, ponieważ tworzy gotowe produkty bez nadmiaru błysku. Jednak ilość odpadów pochodzących z wadliwych części lub rozruchu można jeszcze bardziej zminimalizować, poddając je recyklingowi. Systemy o obiegu zamkniętym zbierają i ponownie przetwarzają ten materiał, zmniejszając ilość odpadów trafiających na wysypiska.
4. Zgodność z przepisami:
Przestrzeganie norm środowiskowych, takich jak ISO 14001 lub regionalnych przepisów dotyczących recyklingu, zapewnia zrównoważone praktyki. Wytyczne te mogą dyktować wybór materiałów, limity emisji lub metody utylizacji odpadów, dostosowując IBM do ekologicznych trendów.
Jak wybrać odpowiedni materiał do formowania wtryskowego z rozdmuchiwaniem?
Wybór materiału formy w IBM wpływa na wydajność produkcji, jakość produktu i koszty. Typowe opcje obejmują stal, aluminium i miedź berylową, z których każda ma unikalne właściwości dostosowane do różnych potrzeb. Oto jak wybrać właściwą:
1. Stal:
Formy stalowe, często z hartowanej stali nierdzewnej lub stali narzędziowej, są wybierane do produkcji wielkoseryjnej. Oferują niezrównaną trwałość, odporność na zużycie w tysiącach cykli i precyzję przy skomplikowanych projektach. Wiążą się one jednak z wyższym kosztem początkowym i dłuższym czasem obróbki, co czyni je mniej idealnymi dla małych serii.
2. Aluminium:
Formy aluminiowe są lżejsze, tańsze i szybsze w produkcji, co czyni je idealnymi do prototypowania lub projektów niskonakładowych. Ich doskonała przewodność cieplna przyspiesza chłodzenie, skracając czas cyklu. Zużywają się one jednak szybciej niż stal, co ogranicza ich zastosowanie w produkcji długoterminowej.
3. Miedź berylowa:
Materiał ten wyróżnia się doskonałym rozpraszaniem ciepła, często stosowanym do wkładek form lub kanałów chłodzących, a nie całych form. Jest idealny do zastosowań wymagających szybkiego chłodzenia, aby zapobiec defektom, takim jak wypaczanie. Jego wyższy koszt ogranicza go do określonych obszarów o wysokiej wydajności.
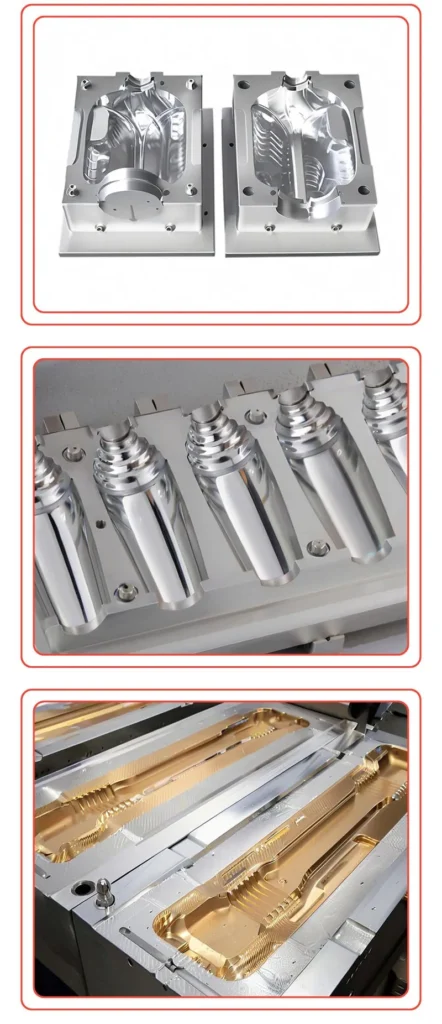
Kryteria wyboru:
① Wielkość produkcji: Wybierz stal do produkcji masowej (np. miliony cykli) i aluminium do krótkich serii (np. tysiące cykli).
② Budżet: Aluminium zapewnia oszczędność kosztów z góry, podczas gdy trwałość stali uzasadnia jej koszt w czasie.
③ Złożoność produktu: Skomplikowane projekty lub wąskie tolerancje sprzyjają precyzji stali; prostsze kształty mogą pasować do aluminium.
najczęściej zadawane pytania dla klientów
Pierwsze kroki z Uplastech
Masz pytania? Mamy odpowiedzi.
Specjalizujemy się w wytłaczaniu, formowaniu próżniowym, rozdmuchiwaniu i precyzyjnym wytwarzaniu form, oferując niestandardowe rozwiązania spełniające różnorodne potrzeby produkcyjne.
Współpracujemy z różnymi branżami, w tym motoryzacyjną, elektroniczną, dóbr konsumpcyjnych i opakowań, koncentrując się na partnerstwie B2B i dostarczaniu rozwiązań w zakresie wytłaczania, termoformowania, rozdmuchiwania i precyzyjnego formowania.
Tak, dostosowujemy nasze rozwiązania do Twoich unikalnych wymagań.
Skontaktuj się
Napisz do nas lub wypełnij poniższy formularz, aby uzyskać wycenę.
E-mail: uplastech@gmail.com