Rozwiązania do formowania próżniowego grubych ścianek
Precyzyjne termoformowanie do ciężkich zastosowań. Poznaj wspierane przez ekspertów usługi formowania próżniowego grubych ścianek do zastosowań przemysłowych, motoryzacyjnych i lotniczych.
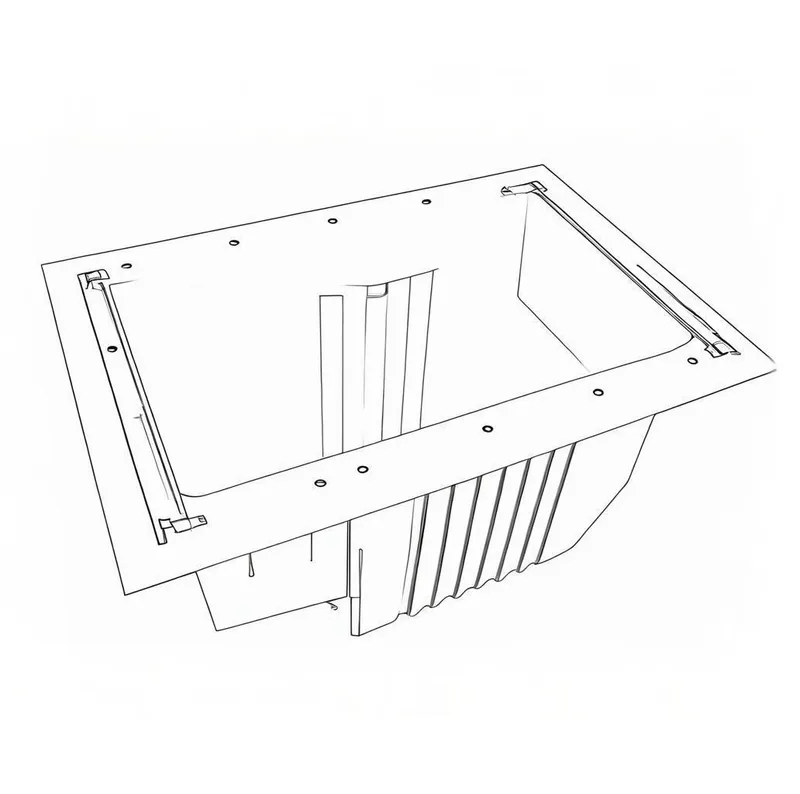
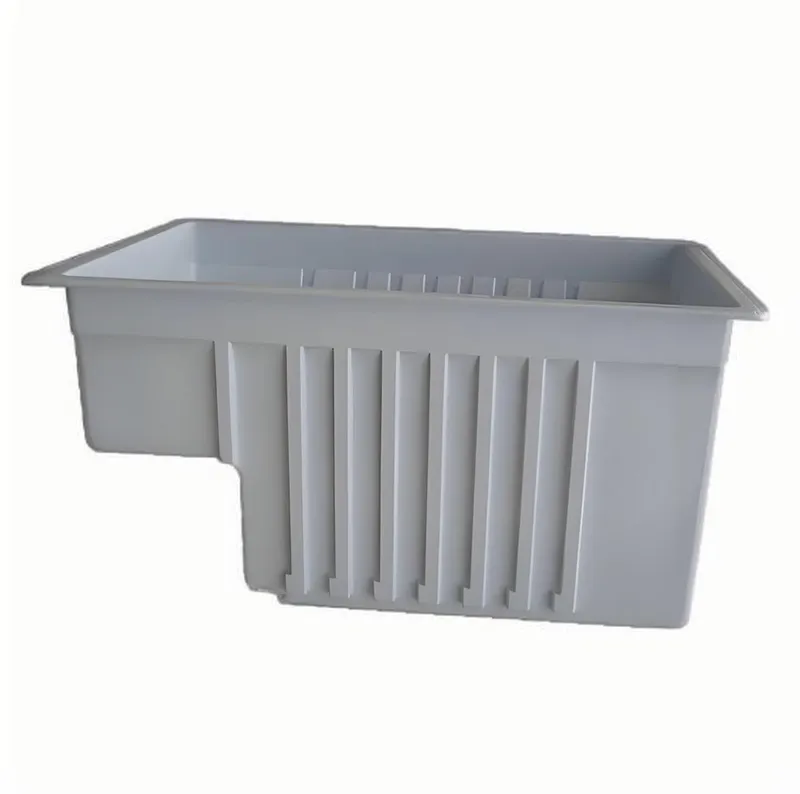
Przewodnik po niestandardowym formowaniu próżniowym grubych ścianek (Heavy Gauge)
Czym jest formowanie próżniowe grubościenne?
Grubościenne formowanie próżniowe (znane również jako Heavy-Gauge Thermoforming lub Thick-Sheet Vacuum Forming) to specjalistyczny proces produkcji tworzyw sztucznych przeznaczony do kształtowania grubych arkuszy tworzyw sztucznych (zwykle ≥2 mm) w trwałe, wytrzymałe komponenty. Proces ten obejmuje:
- Ogrzewanie: Arkusze tworzyw sztucznych (ABS, PC, PP itp.) są zmiękczane za pomocą promienników podczerwieni lub ceramicznych do stanu giętkości (np. 160-180°C dla ABS).
- Formowanie: Podgrzany arkusz jest nakładany na formę, a ciśnienie próżni (do 25-28 inHg) przyciąga go ściśle do powierzchni formy, aby odtworzyć skomplikowane geometrie.
- Chłodzenie i przycinanie: Szybkie chłodzenie (za pomocą powietrza lub mgły wodnej) zestala kształt, po czym następuje przycinanie CNC w celu uzyskania precyzyjnych krawędzi.
Metoda ta jest idealna dla dużych, strukturalnych części wymagających solidności, takich jak panele samochodowe, obudowy przemysłowe lub oznakowanie 3D.
Warianty procesu:
① Formowanie ciśnieniowe: Łączy podciśnienie i sprężone powietrze (3-6 barów) w celu uzyskania ostrzejszych detali na grubych blachach.
② Formowanie podwójnych arkuszy: Łączy dwa formowane arkusze dla pustych struktur (np. palet przemysłowych).
③ Formowanie obłożenia: Wspomagane grawitacyjnie zwisanie podgrzanych arkuszy nad męskimi formami w celu uzyskania jednolitej grubości.
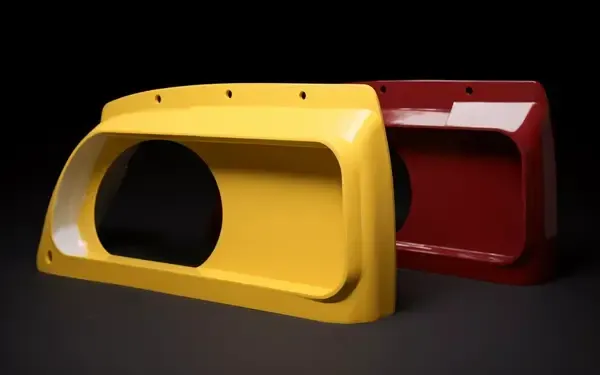
Przewodnik wyboru materiałów: ABS, PC, HDPE i inne
Łącząc specyfikacje techniczne z norm przemysłowych i praktycznych zastosowań, przedstawiamy kompleksową analizę doboru materiałów do grubościennego formowania próżniowego:
1. ABS (akrylonitryl-butadien-styren):
① Aplikacje:
- Komponenty motoryzacyjne (deski rozdzielcze, skrzynki narzędziowe).
- Obudowy elektroniczne (obudowy urządzeń przemysłowych).
- Powłoki urządzeń medycznych.
② Kluczowe zalety:
- Wysoka odporność na uderzenia (idealna do części konstrukcyjnych).
- Doskonała stabilność wymiarowa podczas formowania grubych blach (zakres grubości 1-20 mm).
- Łatwa obróbka końcowa (malowanie, galwanizacja).
③ Rozważania dotyczące procesu:
- Wymaga ogrzewania w temperaturze 180-220°C w celu optymalnego formowania próżniowego.
- Kompatybilny z powierzchniami teksturowanymi (np. wzory skóry we wnętrzach samochodów).
④ Przykład przypadku:
- Ognioodporne osłony maszyn formowane próżniowo z ABS (certyfikat UL94 V-0).
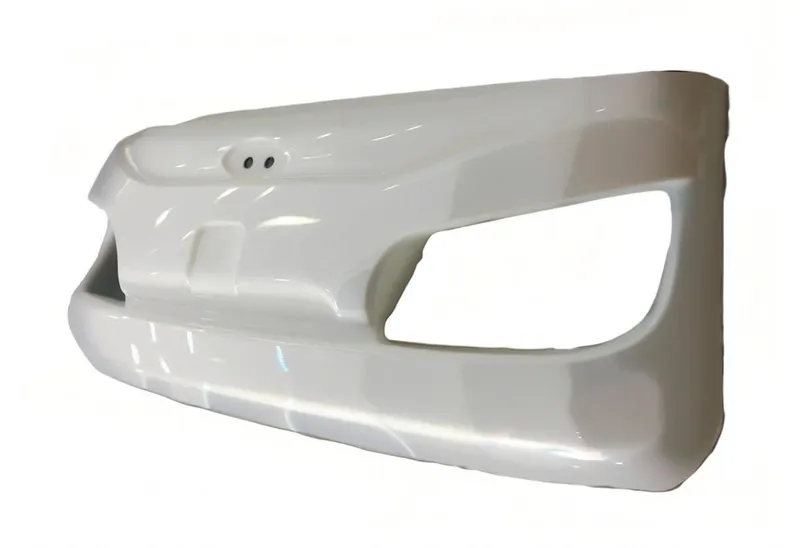
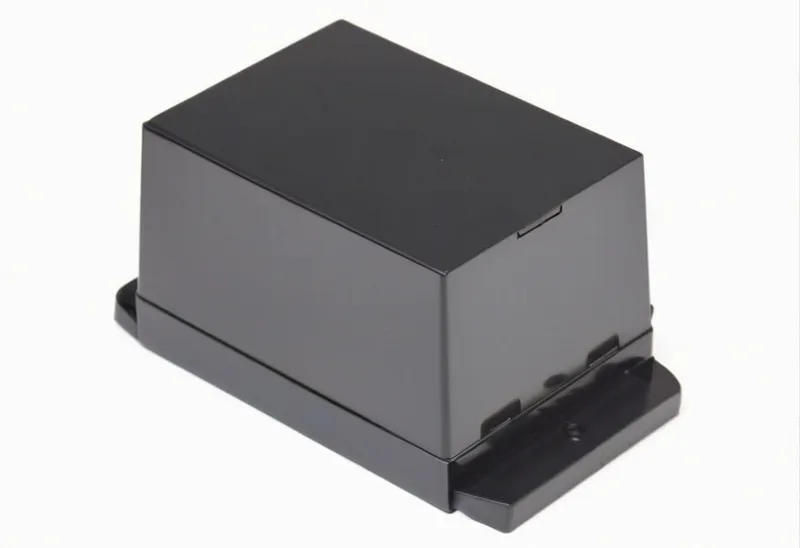
2. PC (poliwęglan):
① Aplikacje:
- Przezroczyste osłony ochronne (sprzęt medyczny, osłony maszyn).
- Komponenty wewnętrzne dla przemysłu lotniczego.
② Kluczowe zalety:
- Przejrzystość zbliżona do szkła (przepuszczalność światła >88%).
- Odporność na temperaturę do 135°C.
③ Rozważania dotyczące procesu:
- Wymagana ścisła kontrola temperatury (wąskie okno formowania: 190-210°C).
- Niezbędne suszenie wstępne (zawartość wilgoci <0,02%).
④ Przykład przypadku:
- Odporne na promieniowanie UV panele kabinowe z PC (grubość 3-6 mm).
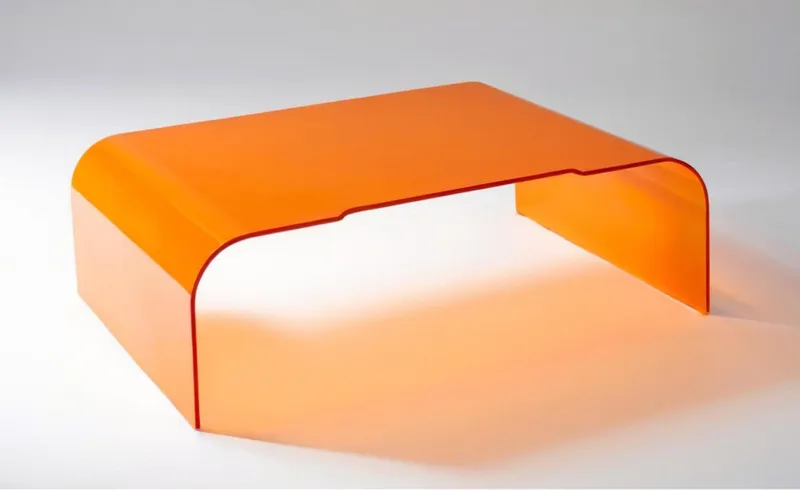
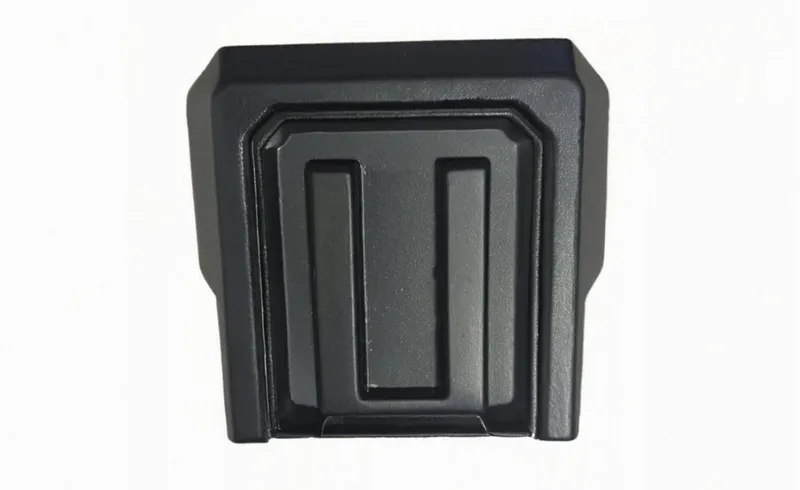
3. HDPE (polietylen o wysokiej gęstości):
① Aplikacje:
- Pojemniki odporne na chemikalia (przemysłowe zbiorniki magazynowe).
- Wytrzymałe palety i systemy transportu materiałów.
② Kluczowe zalety:
- Doskonała odporność na pęknięcia naprężeniowe (ponad 500 godzin w testach ASTM D1693).
- Opłacalność w przypadku produkcji na dużą skalę (30-50% niższy koszt materiału w porównaniu z ABS).
③ Rozważania dotyczące procesu:
- Optymalna grubość formowania: 4-12 mm.
- Wymaga specjalistycznego chłodzenia, aby zapobiec wypaczeniu.
④ Przykład przypadku:
- Tace antystatyczne HDPE do produkcji elektroniki.
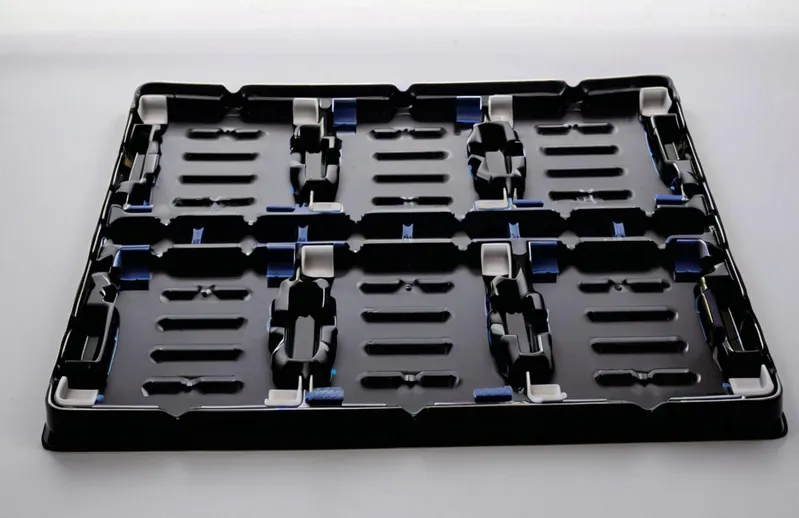
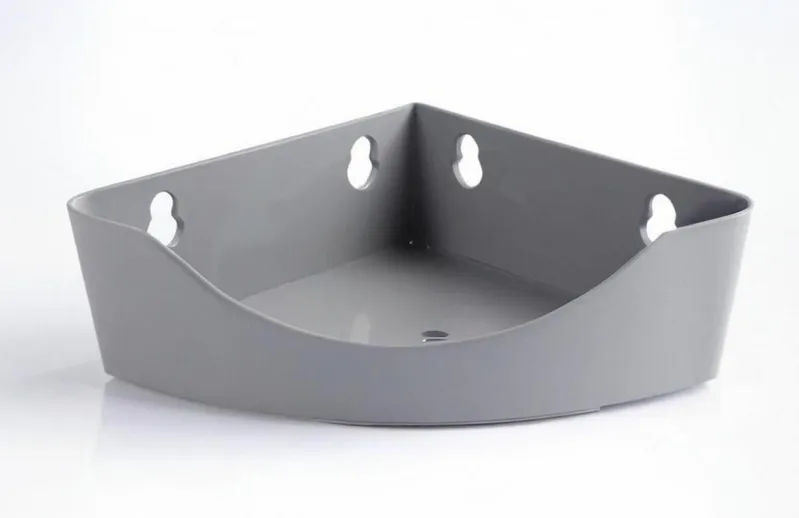
4. PETG (PET modyfikowany glikolem):
① Aplikacje:
- Opakowania dopuszczone do kontaktu z żywnością (pojemniki zgodne z FDA).
- Systemy ekspozycji detalicznej.
② Kluczowe zalety:
- Łączy formowalność PVC z odpornością chemiczną PET.
- Niska temperatura formowania (110-130°C).
③ Przykład przypadku:
- Przezroczyste tacki PETG na narzędzia medyczne (sterylizowane promieniami γ).
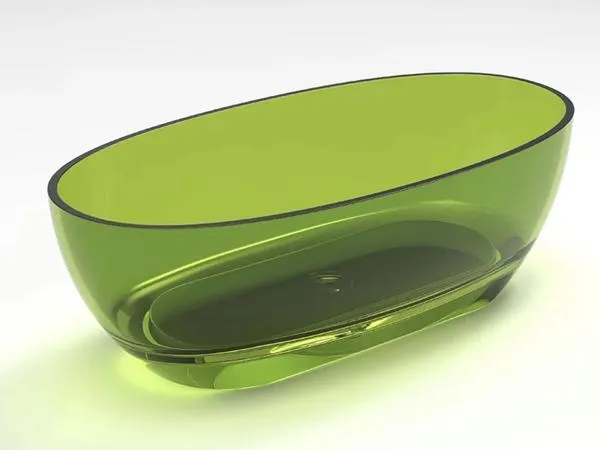
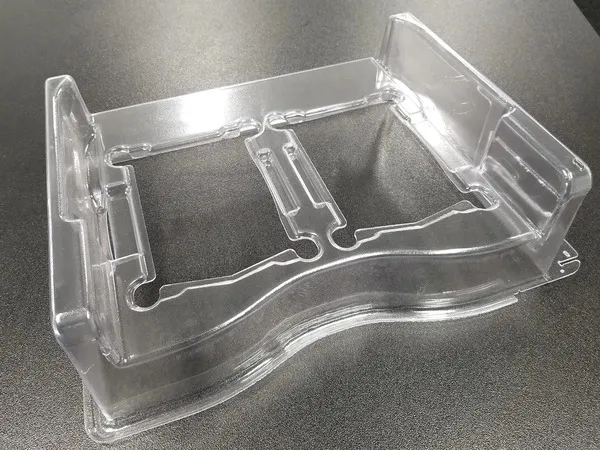
5. PP (polipropylen):
① Aplikacje:
- Opakowania na żywność (kubeczki na jogurt, pojemniki nadające się do mikrofalówki).
- Medyczne produkty jednorazowego użytku (strzykawki, butelki do kroplówek, tace do sterylizacji).
- Pojemniki przemysłowe (pojemniki do przechowywania chemikaliów, zbiorniki rolnicze).
② Kluczowe zalety:
- Lekkość i odporność na zmęczenie: Idealny do cienkościennych konstrukcji z powtarzającym się zginaniem (np. żywe zawiasy na kapslach butelek).
- Obojętność chemiczna: Odporność na kwasy, zasady i rozpuszczalniki organiczne.
- Autoklawowalny: Wytrzymuje sterylizację parową (121°C+) w zastosowaniach medycznych.
- Opłacalność: Niski koszt surowców i wysoka zdolność do recyklingu.
③ Wyzwania związane z grubymi ścianami:
- Skłonność do kurczenia się i wypaczania w sekcjach o dużej grubości (>3 mm).
- Wymaga kontroli temperatury formy (40-80°C) w celu poprawy stabilności wymiarowej.
④ Przykład przypadku:
- Jednorazowe tacki medyczne: Sterylizowane promieniami gamma, zgodne z wymogami FDA, ze zintegrowanymi zatrzaskowymi zamknięciami.
- Przemysłowe pojemniki IBC: Pojemniki PP o grubości 8-12 mm do transportu cieczy korozyjnych.
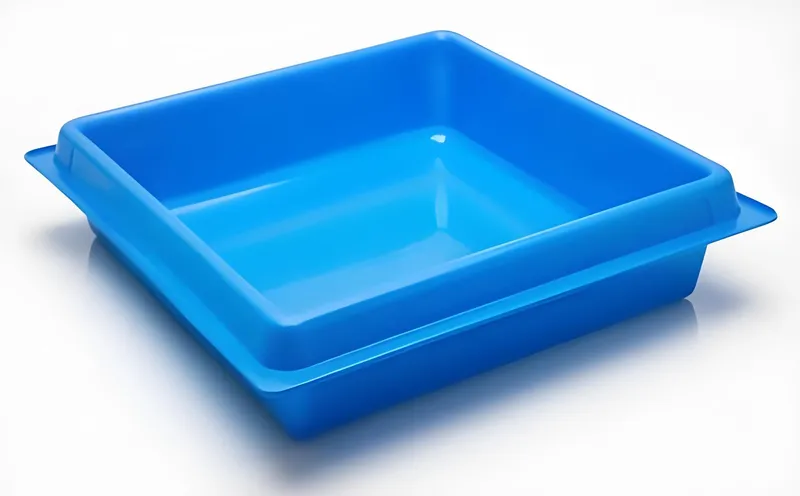
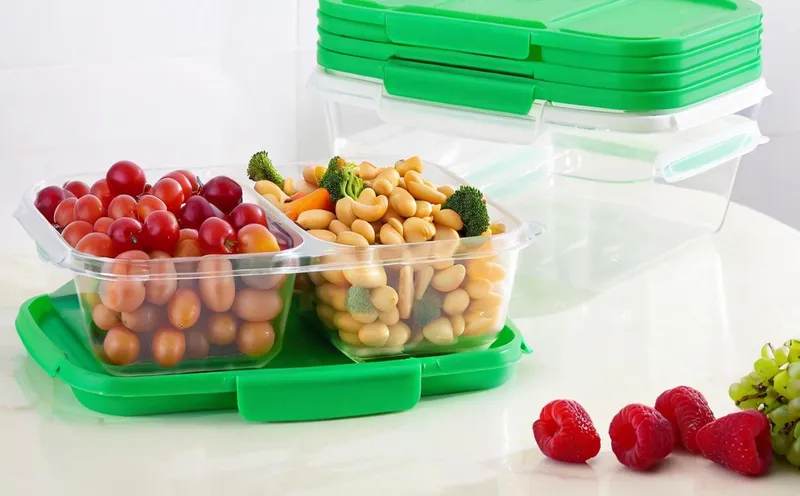
Materiał | Zastosowania | Kluczowe właściwości | Przydatność do termoformowania grubościennego | Przykładowe przypadki użycia |
---|---|---|---|---|
ABS | Części samochodowe, elektronika | Wysoka wytrzymałość, odporność na uderzenia | (Złożone kształty) | Skrzynki narzędziowe |
PC | Przezroczyste osłony, urządzenia medyczne | Wysoka przezroczystość, odporność na ciepło | (Wymaga precyzyjnej kontroli temperatury) | Osłony maszyn |
HDPE | Pojemniki przemysłowe, palety | Odporność chemiczna, możliwość recyklingu | (Jednolita grubość ścianki) | Tace antystatyczne |
PETG | Opakowania na żywność, ekspozytory | Zatwierdzona przez FDA, wysoka wytrzymałość | (Formowanie precyzyjne) | Przezroczyste pojemniki na żywność |
PP | Przedmioty cienkościenne, tace medyczne | Lekkość, odporność na zmęczenie | (Skłonność do kurczenia się w grubych ścianach) | Tacki farmaceutyczne |
Kluczowe etapy procesu: Od arkusza tworzywa sztucznego do produktu końcowego
Kluczowe etapy procesu i punkty techniczne grubościennego formowania próżniowego (grubościenne termoformowane / ciężkie formowanie próżniowe).
1. Wybór materiału i obróbka wstępna:
① Wybór materiału arkusza:
- Popularne materiały: ABS (o grubości 4 mm lub większej i powierzchni o wysokim połysku), HDPE (doskonała odporność na zużycie, odpowiedni do palet obrotowych), PVDF (odporność na wysoką temperaturę i korozję chemiczną, odpowiedni do scenariuszy przemysłowych).
- Obróbka wstępna materiału: Czyste i suche grube arkusze (4 - 6 mm), aby zapobiec wpływowi zanieczyszczeń na jakość formowania.
② Ogrzewanie i zmiękczanie:
- Kontrola temperatury: Ustaw zakres ogrzewania zgodnie z charakterystyką materiału (np. ABS wymaga 200-220°C, a HDPE 150-170°C), aby zapewnić równomierne zmiękczanie.
- Metoda ogrzewania: Należy używać promienników podczerwieni lub kwarcowych, aby uniknąć miejscowego przegrzania, które może spowodować deformację arkusza.
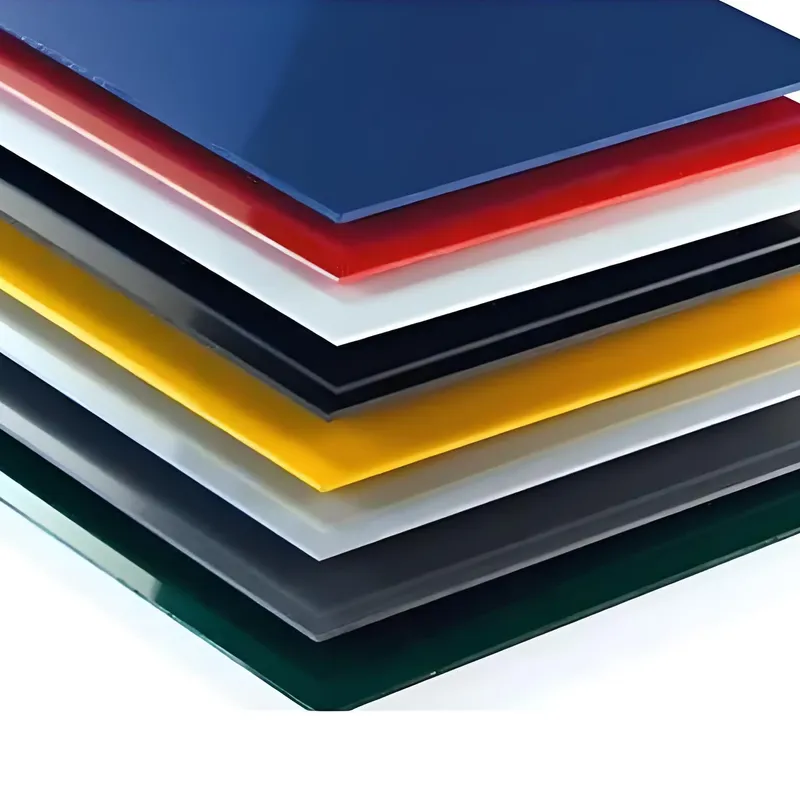
2. Projektowanie form i proces formowania:
① Wybór typu formy:
- Formy jednostronne (męskie/żeńskie): Formy męskie nadają się do produktów z głębokimi wgłębieniami, podczas gdy formy żeńskie mogą poprawić dokładność powierzchni.
- Formy specjalne: Formy z litego aluminium (o wysokim wykończeniu powierzchni) są zalecane do produktów przezroczystych, a w przypadku produktów o złożonej strukturze wymagane są pomocnicze tłoki.
② Formowanie próżniowe i ciśnieniowe:
- Adsorpcja próżniowa: Użyj podciśnienia, aby docisnąć zmiękczony arkusz do konturu formy. Stopień podciśnienia musi być precyzyjnie kontrolowany (wartość referencyjna: ≥0,08 MPa).
- Pomocnicze ciśnienie powietrza: Zastosuj sprężone powietrze (ciśnienie 0,3 - 0,6 MPa), aby przyspieszyć rozciąganie materiału i zredukować pęcherzyki powietrza.
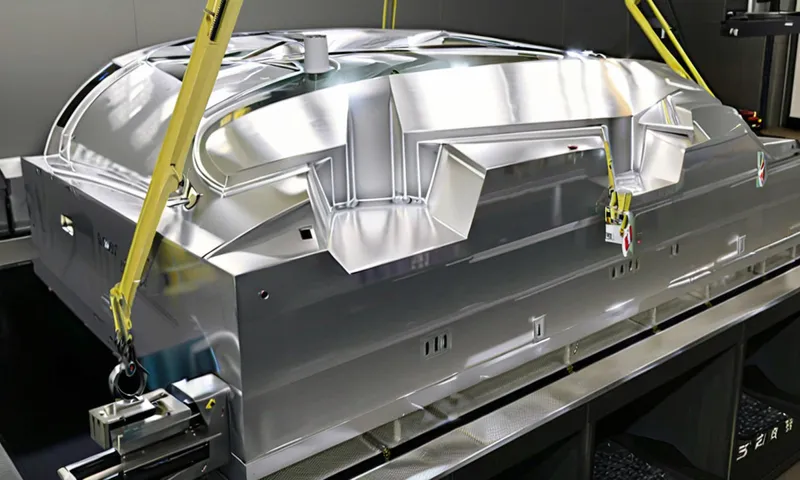

3. Optymalizacja chłodzenia i rozformowywania:
① Chłodzenie i kształtowanie:
- Metoda chłodzenia: Należy stosować systemy chłodzenia powietrzem lub wodą, aby kontrolować szybkość chłodzenia i uniknąć pękania naprężeniowego.
- Zarządzanie gradientem temperatury: Najpierw należy schłodzić stronę stykającą się z formą, aby zmniejszyć nierównomierny skurcz części o grubych ściankach.
② Obróbka rozformowująca:
- Konstrukcja stożka rozformowującego: Zwężenie ≥0,5° dla gładkich powierzchni i ≥1,5° dla chropowatych powierzchni zapewnia płynne rozformowywanie.
- Zautomatyzowane rozformowywanie: W pełni zautomatyzowane maszyny do termoformowania grubych arkuszy są wyposażone w mechanizmy rozformowywania w celu ograniczenia interwencji ręcznej.
4. Przetwarzanie końcowe i kontrola jakości:
① Przycinanie i przetwarzanie wtórne:
- Cięcie krawędzi: Do usuwania nadmiaru zadziorów należy używać wycinarek CNC lub laserowych.
- Obróbka funkcjonalna: Wiercenie otworów, polerowanie lub nakładanie powłok powierzchniowych (np. powłok fluorowęglowych PVDF w celu zwiększenia odporności na warunki atmosferyczne).
② Kontrola jakości:
- Kontrola grubości ścianki: Użyj ultradźwiękowego miernika grubości, aby zweryfikować jednorodność (błąd docelowy <5%).
- Testowanie wytrzymałości: Symulacja rzeczywistego środowiska obciążenia w celu sprawdzenia odporności na uderzenia i zużycie.
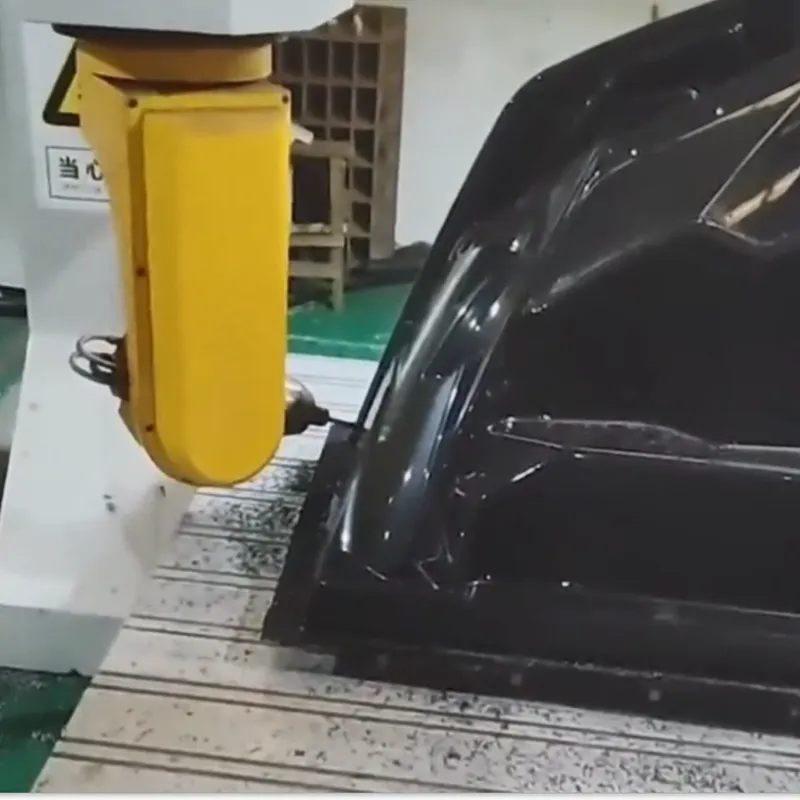
Zastosowania w różnych branżach: Motoryzacja, medycyna i inne
Grubościenne formowanie próżniowe (znane również jako termoformowanie grubościenne, termoformowanie grubościenne lub termoformowanie grubych arkuszy) jest wszechstronnym procesem produkcyjnym szeroko stosowanym w branżach wymagających trwałych elementów o złożonych kształtach. Poniżej znajdują się kluczowe zastosowania w głównych sektorach:
1. Przemysł motoryzacyjny:
Grubościenne formowanie próżniowe ma kluczowe znaczenie dla lekkości i funkcjonalności samochodów:
- Elementy wewnętrzne: Panele deski rozdzielczej, okładziny drzwi i konsole środkowe wykonane z arkuszy ABS lub PP, oferujące wysoką wytrzymałość i konfigurowalne tekstury.
- Części zewnętrzne: Zderzaki, błotniki i aerodynamiczne panele nadwozia wykonane z materiałów odpornych na uderzenia, takich jak HDPE lub mieszanki ABS+TPU.
- Systemy oświetlenia: Obudowy reflektorów i tylnych świateł o precyzyjnej przejrzystości optycznej, często wykonane z PMMA lub PC.
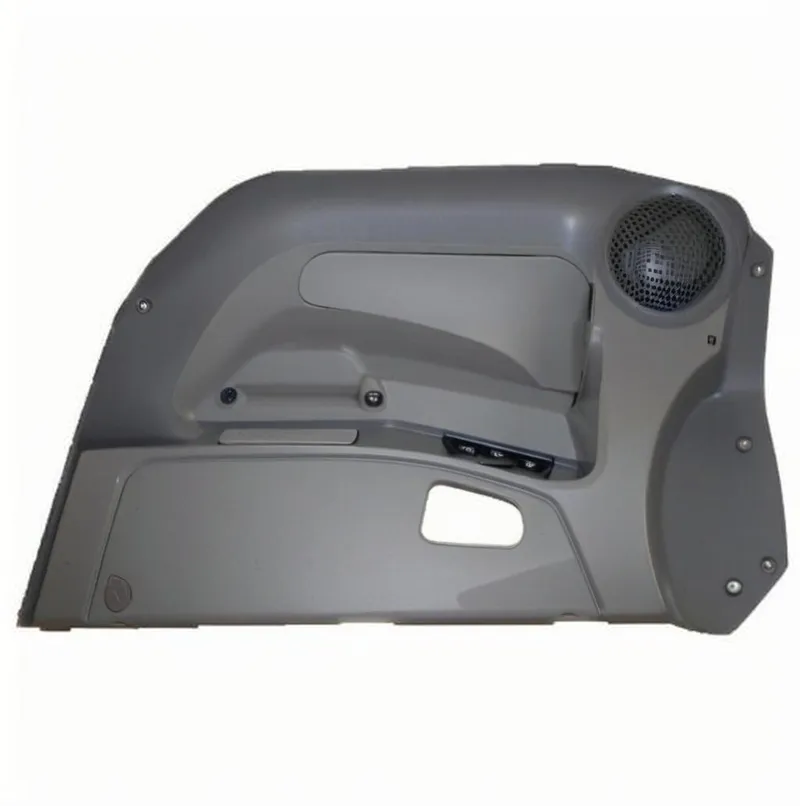
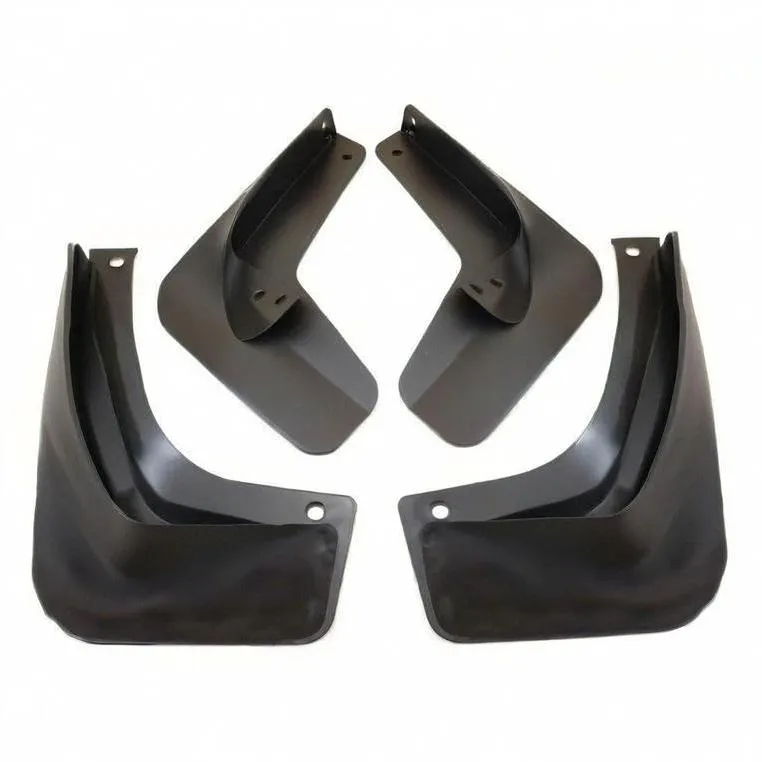
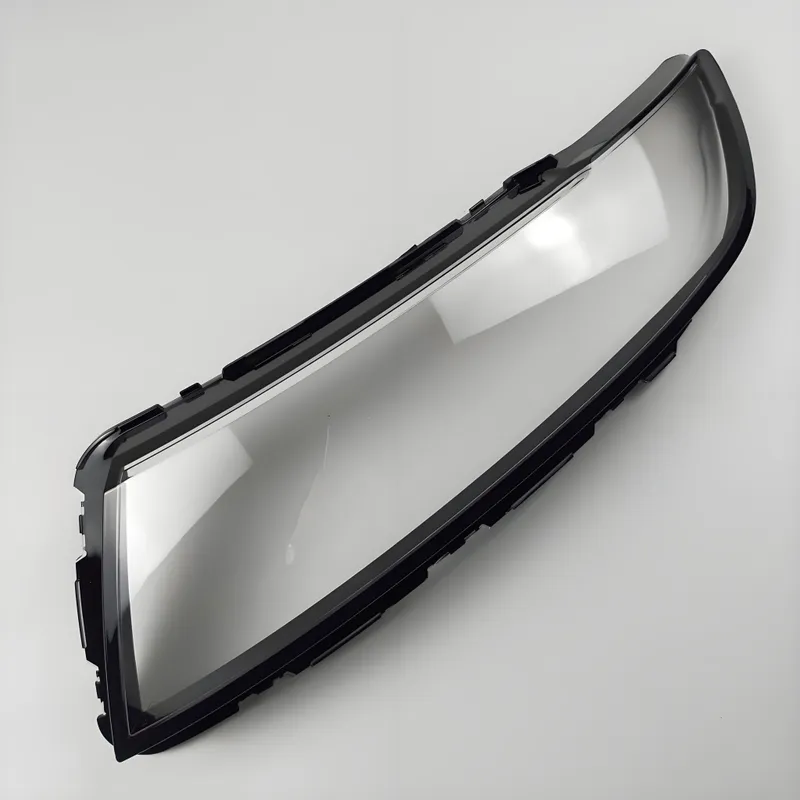
2. Przemysł medyczny:
W zastosowaniach medycznych priorytetem jest higiena, trwałość i precyzja:
- Obudowy urządzeń: Pokrywy urządzeń do rezonansu magnetycznego, obudowy instrumentów chirurgicznych i obudowy respiratorów wykonane z materiałów nadających się do sterylizacji, takich jak PETG lub ABS klasy medycznej.
- Tace: Elementy aparatury rentgenowskiej i tace na sprzęt laboratoryjny o właściwościach antystatycznych.
- Opakowanie niestandardowe: Opakowania wielokrotnego użytku na narzędzia chirurgiczne (grubość 3-5 mm) do sterylizacji tlenkiem etylenu

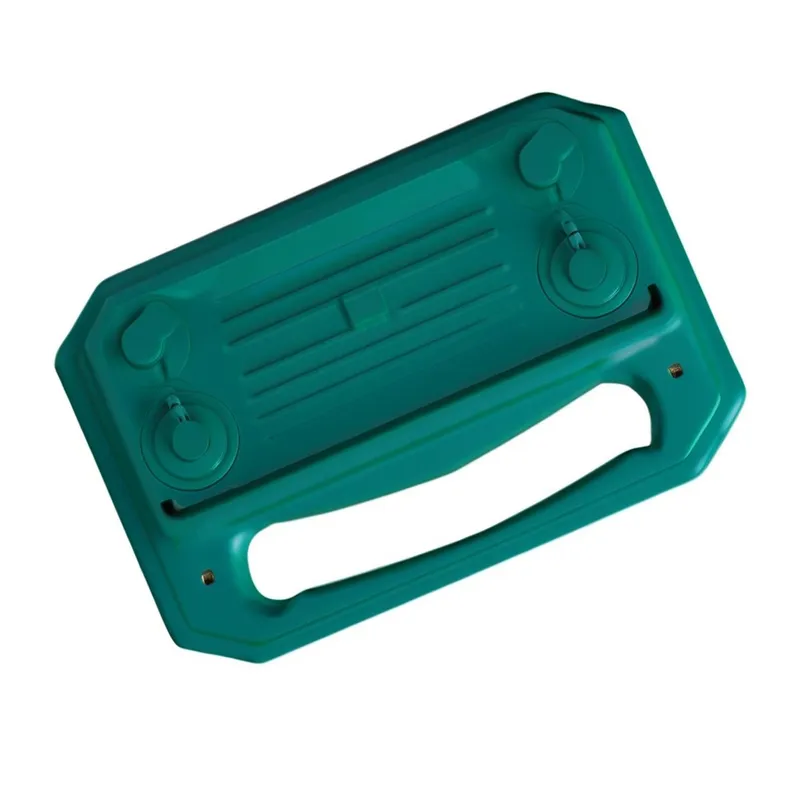
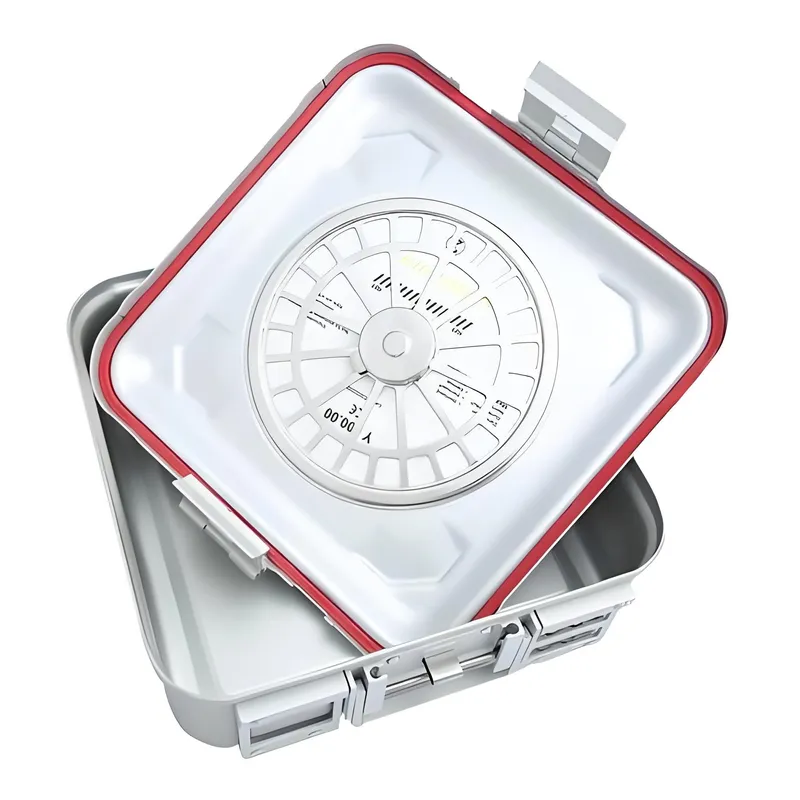
3. Elektronika użytkowa i sprzęt AGD:
- Urządzenia gospodarstwa domowego: Wkłady do lodówek, pokrywy pralek i elementy zmywarek wykorzystujące PP lub HDPE w celu zapewnienia odporności chemicznej.
- Obudowy elektroniki: Panele tylne telewizorów, obudowy komputerów i panele sterowania z trudnopalnego tworzywa ABS lub PC.
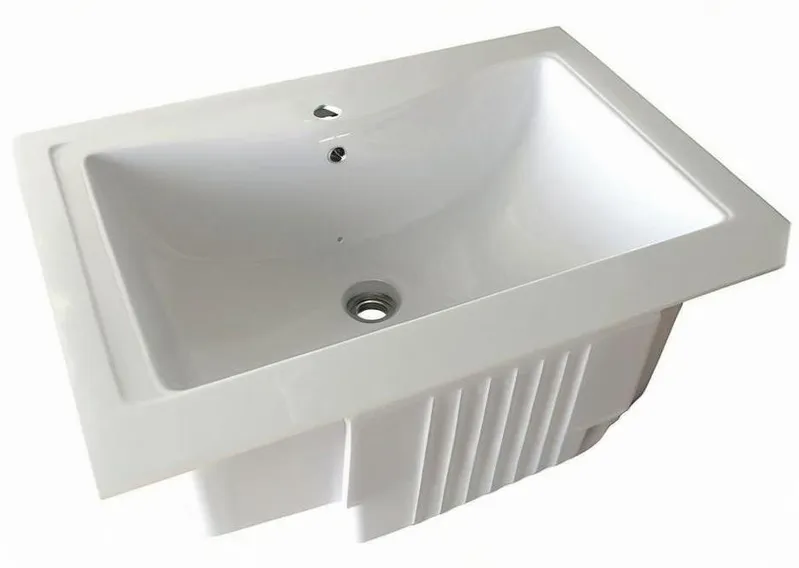
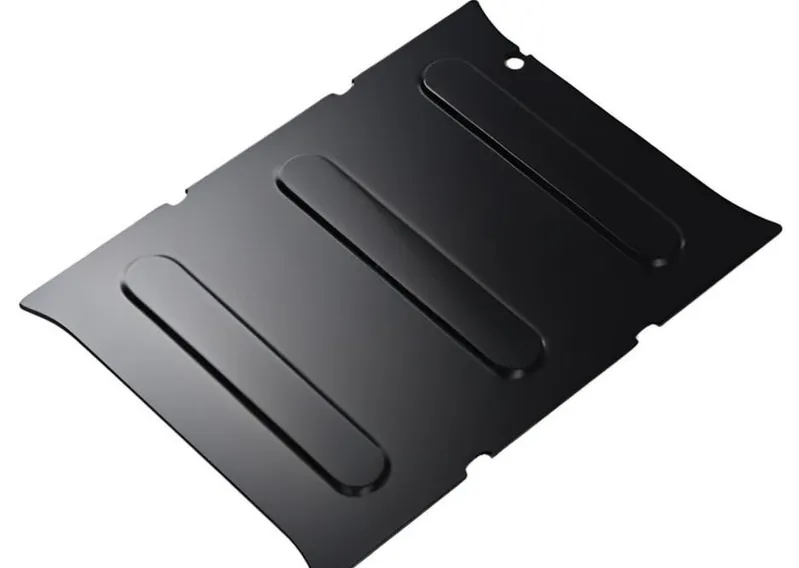
4. Lotnictwo i transport:
- Wnętrza samolotów: Pojemniki nad głową, panele oparć siedzeń i wykładziny kabiny wykonane z lekkich, trudnopalnych kompozytów.
- Komponenty kolejowe: Podstawy foteli i okładziny wewnętrzne wykonane z materiałów o wysokiej wytrzymałości i niskiej wadze.
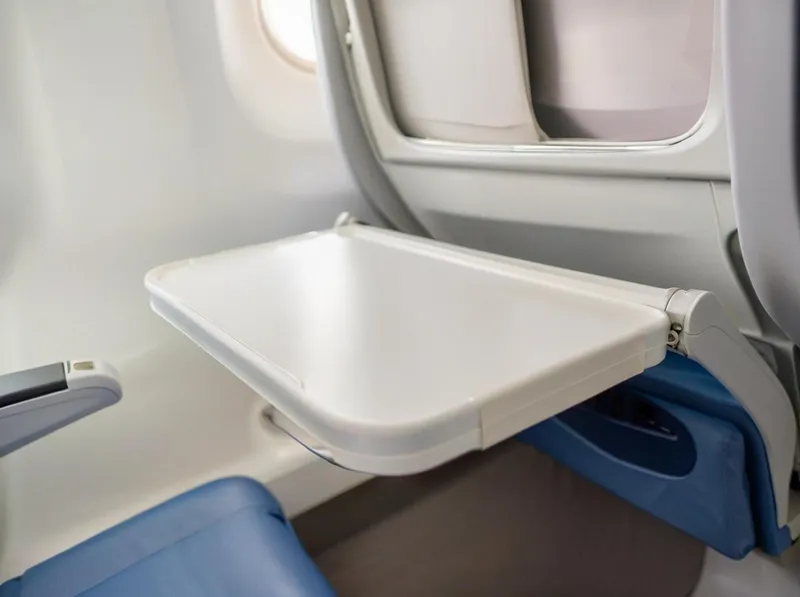
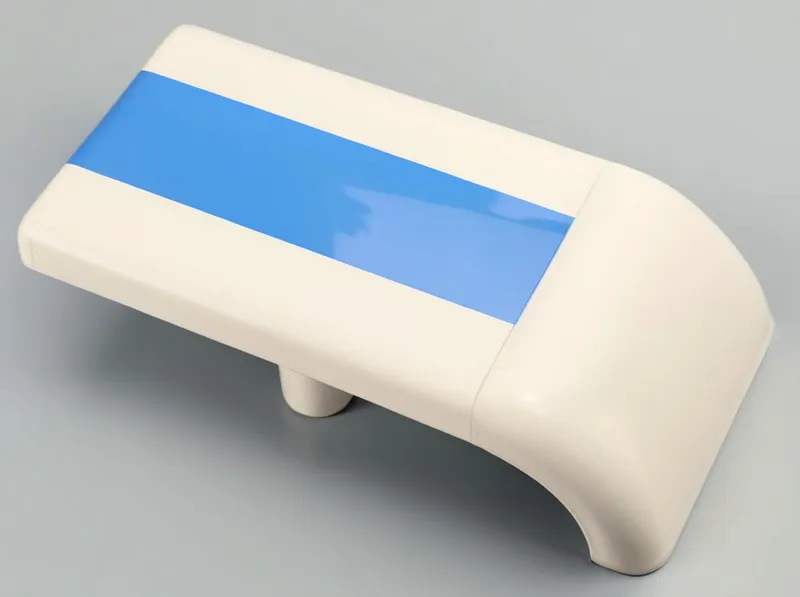
5. Rozwiązania przemysłowe i opakowaniowe:
- Niestandardowe oprzyrządowanie: Wytrzymałe tace i pokrywy ochronne na części maszyn.
- Wyświetlacze detaliczne: Trwałe oznakowanie, stojaki na produkty i jednostki w punktach sprzedaży z teksturowanymi powierzchniami do brandingu.
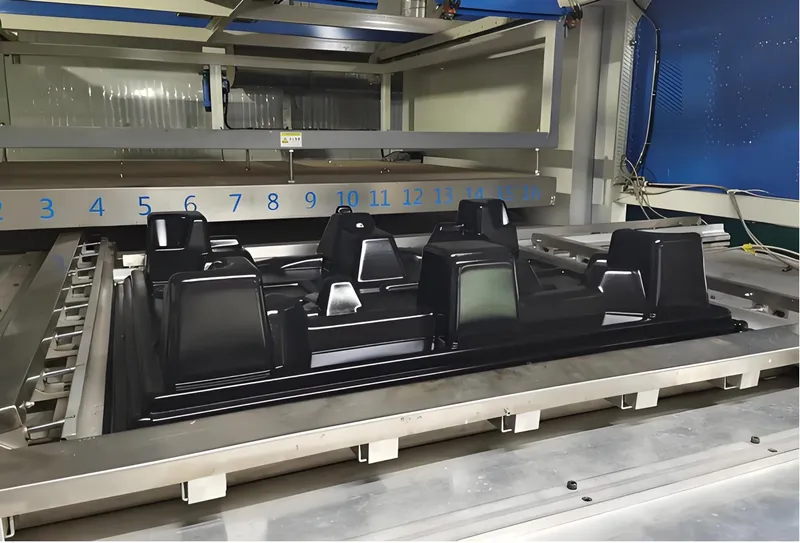
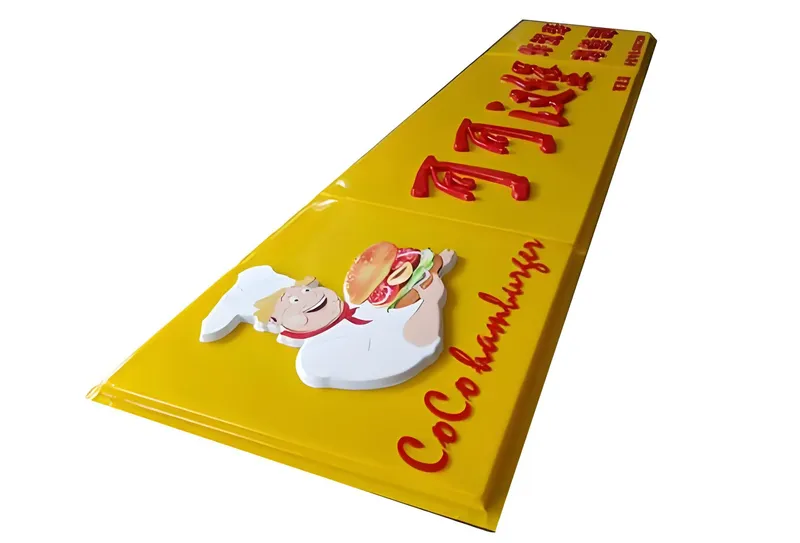
Zalety w porównaniu z formowaniem wtryskowym
Poniżej przedstawiono pięć głównych zalet formowania próżniowego grubościennego w porównaniu z formowaniem wtryskowym, analizowanych w połączeniu z cechami technicznymi i zastosowaniami przemysłowymi:
1. Koszt formy i elastyczność produkcji:
Formy do grubościennego formowania próżniowego są zwykle wykonane z aluminium lub materiałów kompozytowych. Mają prostą strukturę i niskie koszty produkcji (około 10% - 30% form wtryskowych). Ta cecha sprawia, że są one bardziej ekonomiczne w przypadku produkcji małoseryjnej lub opracowywania prototypów. Natomiast formowanie wtryskowe wymaga precyzyjnych form stalowych, które nadają się do produkcji wielkoseryjnej, ale wymagają wysokich inwestycji początkowych.
2. Wykorzystanie materiałów i kontrola odpadów:
Formowanie próżniowe polega na podgrzewaniu jednowarstwowego arkusza tworzywa sztucznego i nadawaniu mu kształtu. Skrawki można poddać recyklingowi, co skutkuje mniejszą ilością odpadów materiałowych. W przypadku formowania wtryskowego stopiony plastik musi wypełnić całą wnękę formy. W przypadku części o grubych ściankach nierównomierny skurcz może prowadzić do nadmiaru materiału, a recykling odpadów jest trudniejszy.
3. Jednorodność struktury grubościennej i kontrola naprężeń:
Formowanie próżniowe może zmniejszyć naprężenia wewnętrzne poprzez równomierne rozciąganie i chłodzenie części o grubych ściankach, unikając typowych problemów związanych z formowaniem wtryskowym, takich jak wgniecenia i wypaczenia. Na przykład, w przypadku części samochodowych o grubości ścianki przekraczającej 5 mm, formowanie próżniowe może utrzymać płaskość powierzchni, podczas gdy formowanie wtryskowe może powodować wewnętrzne puste przestrzenie z powodu niewystarczającego ciśnienia pakowania.
4. Możliwość dostosowania do dużych i złożonych struktur geometrycznych:
Formowanie próżniowe doskonale sprawdza się w produkcji dużych części o grubych ściankach (takich jak obudowy sprzętu lotniczego lub tace na sprzęt medyczny). Rozmiar pojedynczej części może sięgać kilku metrów i ma dużą zdolność adaptacji do złożonych zakrzywionych powierzchni. Formowanie wtryskowe jest ograniczone przez otwieranie i zamykanie formy oraz wydajność wtryskarki, co utrudnia produkcję ponadwymiarowych lub bardzo grubych części.
5. Ochrona środowiska i energia:
Proces formowania próżniowego ma niższe zużycie energii i nie wymaga wysokociśnieniowego systemu wtrysku, co jest zgodne z trendem ekologicznej produkcji. Z kolei procesy topienia i wysokiego ciśnienia w formowaniu wtryskowym zużywają więcej energii. Produkty o grubych ściankach wymagają dłuższego cyklu chłodzenia, co dodatkowo zwiększa zużycie energii.
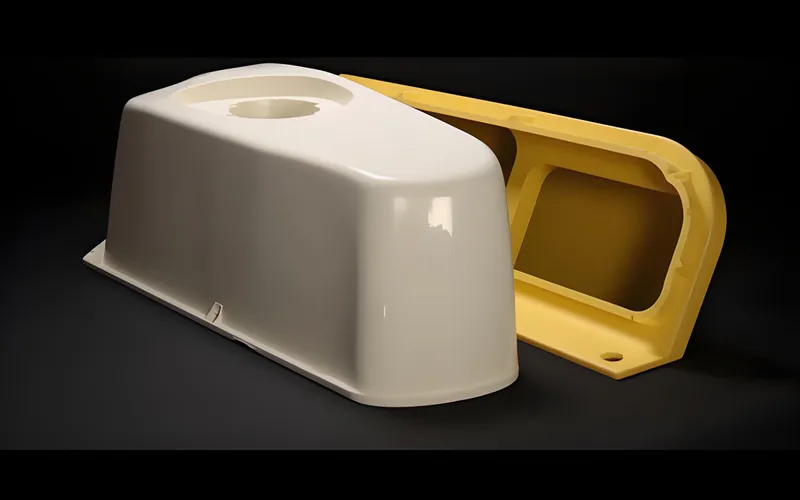
Wyzwania związane z formowaniem próżniowym grubościennym
Formowanie próżniowe grubościenne stanowi wyjątkowe wyzwanie w porównaniu ze standardowymi procesami termoformowania. Czynniki takie jak przepływ materiału, kontrola temperatury, złożoność oprzyrządowania i czas cyklu znacząco wpływają na jakość i wydajność. Zarządzanie naprężeniami szczątkowymi, defektami powierzchni i ograniczeniami materiałowymi ma kluczowe znaczenie dla uzyskania wysokowydajnych, stabilnych wymiarowo części.
1. Przepływ materiału i jednorodność:
Formowanie próżniowe grubych ścianek wymaga precyzyjnej kontroli nad przepływem materiału, aby uniknąć nierównej grubości ścianek. Termoformowanie grubościenne często zmaga się z niepełnym rozciąganiem z powodu ograniczonej mobilności polimeru, co prowadzi do słabych punktów lub koncentracji naprężeń w produktach końcowych.
2. Kontrola temperatury:
Termoformowanie grubych arkuszy wymaga ścisłego zarządzania temperaturą. Nadmierne ciepło może degradować łańcuchy polimerowe, podczas gdy niewystarczające ogrzewanie powoduje kruchość. Równoważenie gradientów temperatury w grubych sekcjach (np. ≥6 mm) ma kluczowe znaczenie dla zapobiegania wypaczaniu lub rozwarstwianiu.
3. Złożoność narzędzi i form:
Złożone geometrie w grubościennym formowaniu próżniowym wymagają precyzyjnych form z zaawansowanymi systemami chłodzenia. Formy o dużej grubości muszą być odporne na długotrwałe działanie wysokich temperatur i dużych sił zaciskających, co zwiększa koszty projektowania i konserwacji.
4. Czas cyklu i efektywność energetyczna:
Przetwarzanie grubych materiałów (np. ABS, HDPE) wiąże się z wydłużonymi cyklami ogrzewania/chłodzenia, co zwiększa zużycie energii. Kluczowym wyzwaniem pozostaje optymalizacja czasu cyklu bez uszczerbku dla integralności strukturalnej.
5. Naprężenie szczątkowe i stabilność wymiarowa:
Części formowane termicznie o grubych ściankach często zachowują naprężenia szczątkowe z powodu nierównomiernego chłodzenia, co prowadzi do zniekształceń po formowaniu. Zarządzanie szybkością skurczu i zapewnienie dokładności wymiarowej ma kluczowe znaczenie dla funkcjonalnych zastosowań.
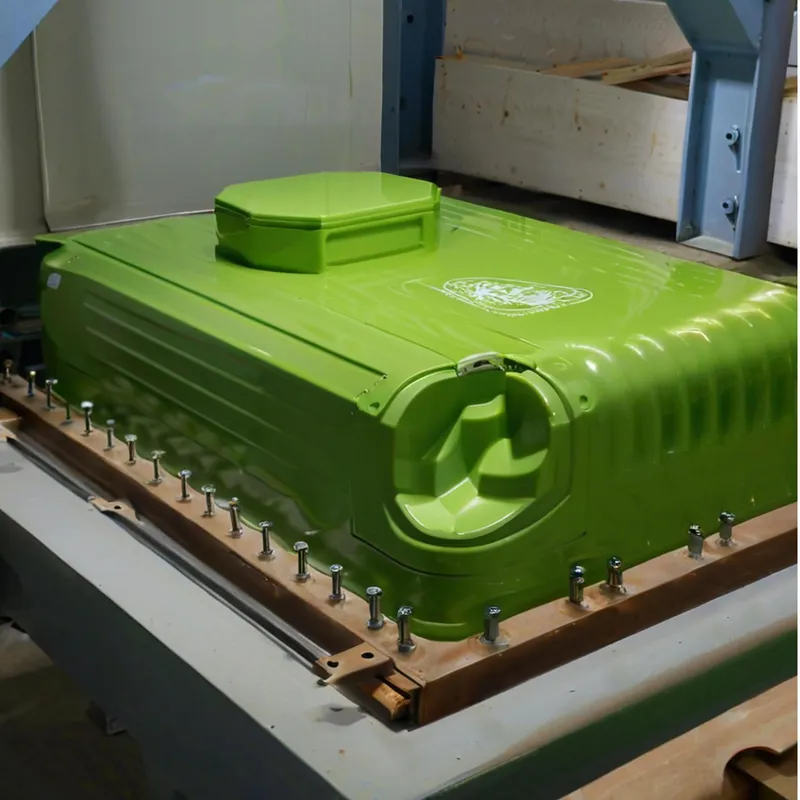
6. Wady powierzchni:
Termoformowanie o dużej grubości może powodować niedoskonałości powierzchni, takie jak tekstury skórki pomarańczowej lub uwięzienie powietrza, szczególnie w głęboko tłoczonych sekcjach. Konstrukcja kanału próżniowego i techniki wstępnego rozciągania materiału mają kluczowe znaczenie dla złagodzenia tego zjawiska.
7. Ograniczenia w wyborze materiałów:
Nie wszystkie polimery nadają się do grubościennego formowania próżniowego. Preferowane są materiały o wysokiej wytrzymałości (np. usieciowany PE), ale opcje są ograniczone w porównaniu do termoformowania cienkościennego, co ogranicza elastyczność projektowania.
Rozwiązania do formowania próżniowego grubych ścianek
Odkryj trwałe, wysoce precyzyjne rozwiązania do termoformowania z niestandardowym wsparciem projektowym i wszechstronnością materiałów. Poproś o wycenę już dziś!
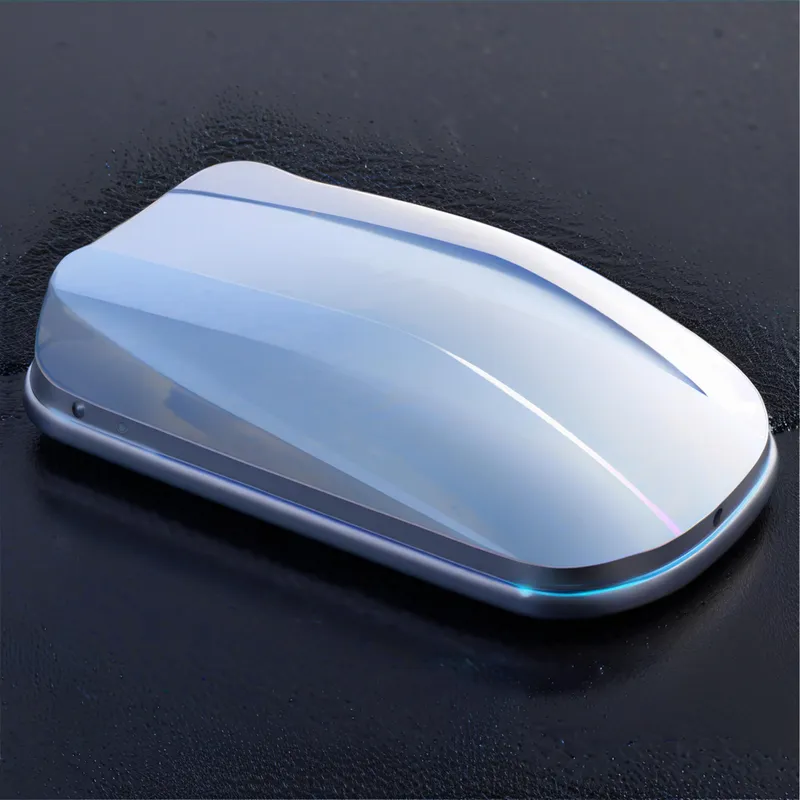
Przewodnik po niestandardowym formowaniu próżniowym grubych ścianek (Heavy Gauge)
- Rozważania projektowe dotyczące integralności strukturalnej
- Kontrola jakości: Grubość ścianki i wykończenie powierzchni
- Studia przypadków: Formowanie próżniowe grubościenne
- Formowanie próżniowe grubościenne a formowanie próżniowe cienkościenne
- Opcje dostosowywania: Tekstury i przetwarzanie końcowe
- Nasz kompleksowy przepływ usług
Rozważania projektowe dotyczące integralności strukturalnej
Oto kluczowe kwestie projektowe dotyczące integralności strukturalnej w procesach termoformowania grubościennego:
1. Wybór materiału i obróbka wstępna:
Wysokowydajne polimery: Priorytetem jest PVDF (np. seria Solvay PVDF 20808), zmodyfikowany ABS lub PC dla stabilności termicznej i odporności na promieniowanie UV w grubościennym formowaniu próżniowym.
② Kontrola jednorodności arkusza: Utrzymanie tolerancji grubości ≤±5% poprzez wstępne suszenie (np. 105°C/4h) w celu wyeliminowania mikropustek spowodowanych wilgocią w termoformowaniu o dużej grubości.
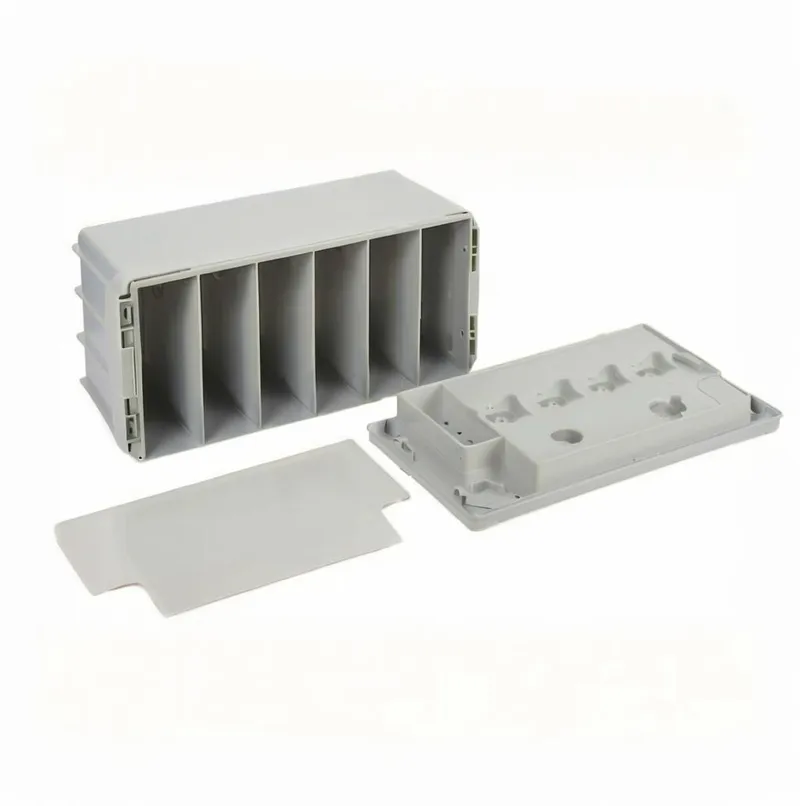
2. Projekt gradientu grubości ścianki:
① Optymalizacja przejścia: Stosuj stożkowe lub zakrzywione przejścia (promień ≥3× grubość ścianki, R≥3T), aby uniknąć pęknięć naprężeniowych. Przykład: Kąt przejścia 45° dla samochodowych desek rozdzielczych ze zmianami grubości 8→4 mm.
② Minimalne standardy grubości:
- Małe części (≤200 mm): ≥2 mm
- Duże części (≥400 mm): ≥3 mm + żebra wzmacniające.
3. Inżynieria form i kompatybilność procesów:
① Wybór typu formy:
- Formy żeńskie: Idealne do płytkich wnęk (głębokość ≤3× grubość), np. obudowy urządzeń medycznych.
- Formy męskie: W przypadku wysokiej precyzji wymiarów wewnętrznych (np. pojemniki przemysłowe), ale należy ograniczyć grubość dna do <15%.
Kąty zanurzenia: ≥3° (≥5° dla części przezroczystych); zwiększać o 0,5° na każde 0,1 mm głębokości tekstury.
4. Parametry procesu termicznego:
Parametr | Zakres grubościenny | Zakres cienkościenny |
---|---|---|
Temperatura ogrzewania | 210-290°C (sterowane strefowo) | 180-240°C |
Ciśnienie próżni | ≥95 kPa (wielostopniowy) | ≥90 kPa |
Szybkość chłodzenia | 2-4°C/s (chłodzenie mgłą) | 5-8°C/s (chłodzenie powietrzem) |
Czas utrzymywania | Grubość (mm) ×1,2-1,5s | Grubość (mm) ×0,8s |
5. Strategie wzmocnienia strukturalnego:
① Wzór żebra:
- Wysokość ≤5T, grubość korzenia 0,6-0,8T, końcówka ≥0,4T
- Przykład: rozstaw żeber 80 mm dla obudów o długości 400 mm.
② Otwory wentylacyjne: Dodaj otwory Φ3-30 mm nie przenoszące obciążeń, aby zmniejszyć opór podciśnienia i ułatwić wyrównanie montażu.
6. Zarządzanie stresem:
① Chłodzenie stopniowe:
- Szybkie chłodzenie do Tg+20°C (eliminacja naprężeń formujących)
- Powolne chłodzenie do Tg-10°C (uwolnienie naprężeń orientacji molekularnej)
- Wymuszone chłodzenie do temperatury otoczenia.
② Wyżarzanie: 2-4h w Tg-30°C dla części o grubości >8mm (np. tworzywa konstrukcyjne).
Kontrola jakości: Grubość ścianki i wykończenie powierzchni
W przypadku grubościennych produktów termoformowanych (określanych również jako termoformowanie grubych blach lub termoformowanie grubych arkuszy), utrzymanie stałej grubości ścianek i wykończenia powierzchni ma kluczowe znaczenie. Poniżej przedstawiono kluczowe strategie kontroli jakości w tych procesach:
1. Kontrola grubości ścianki:
① Równomierność podgrzewania materiału: Zapewnienie równomiernego nagrzewania arkusza termoplastycznego w celu uniknięcia miejscowego przerzedzenia lub zgrubienia podczas formowania. Zaawansowane systemy monitorowania temperatury mogą zoptymalizować cykle podgrzewania wstępnego.
② Optymalizacja projektu formy: Używaj precyzyjnie zaprojektowanych form z regulowanym ciśnieniem powietrza i ustawieniami podciśnienia, aby regulować dystrybucję materiału. Symulacje (np. analiza elementów skończonych) pomagają przewidzieć wzorce przepływu dla części o grubych ściankach.
③ Monitorowanie grubości w czasie rzeczywistym: Wdrożenie czujników inline (np. ultradźwiękowych lub laserowych) do pomiaru grubości podczas formowania. Dynamiczne dostosowywanie parametrów w oparciu o informacje zwrotne.
④ Kontrola po formowaniu: Użyj próbek QC, aby zweryfikować spójność grubości w różnych partiach. Statystyczna kontrola procesu (SPC) może zidentyfikować odchylenia w trendach produkcyjnych.
2. Zapewnienie wykończenia powierzchni:
① Jakość powierzchni formy: Polerowanie form do wysokiej jakości wykończenia (np. standard SPI A1) w celu zminimalizowania niedoskonałości powierzchni produktu końcowego.
② Wybór materiału: Wybierz żywice o wysokiej czystości i niskiej lepkości, aby zredukować defekty powierzchni, takie jak skórka pomarańczowa lub linie przepływu, powszechne w grubościennym formowaniu próżniowym.
③ Kontrolowane prędkości chłodzenia: Stopniowe chłodzenie zapobiega nieregularnościom powierzchni spowodowanym naprężeniami. Stacje chłodzące o kontrolowanej temperaturze lub noże powietrzne zapewniają równomierne krzepnięcie.
Techniki przetwarzania końcowego: Procesy wtórne (np. szlifowanie, powlekanie) mogą poprawić jakość powierzchni w zastosowaniach wymagających estetycznej precyzji.
3. Systematyczne ramy jakości:
① Przyjęcie standardów ISO 9001: Wdrożenie systemu zarządzania jakością (QMS) obejmującego zaopatrzenie w materiały, walidację procesów i kontrole końcowe.
② Łączenie protokołów QA/QC: Integracja zapewniania jakości (np. audyty procesów) z kontrolą jakości w czasie rzeczywistym (np. zautomatyzowane wykrywanie usterek) w celu uwzględnienia zarówno ryzyka systemowego, jak i operacyjnego.
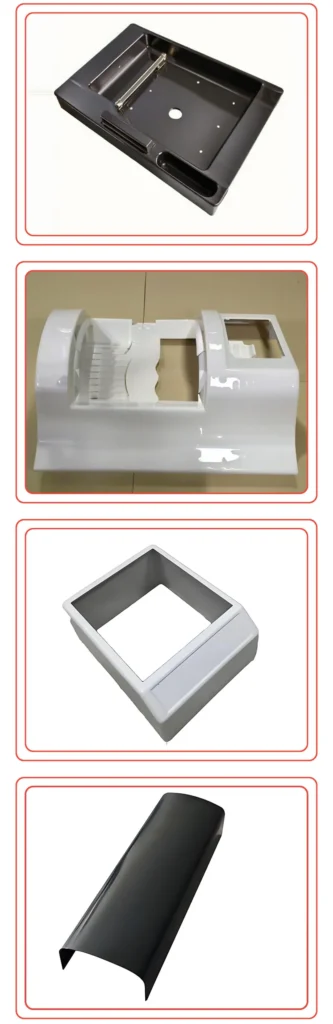
Studia przypadków: Formowanie próżniowe grubościenne
Formowanie próżniowe grubych ścianek (alternatywnie nazywane termoformowaniem grubych ścianek lub formowaniem ciśnieniowym grubych arkuszy) stanowi transformacyjną metodę przetwarzania polimerów do produkcji elementów konstrukcyjnych o grubości ścianek przekraczającej 3 mm. Technika ta termicznie kształtuje tworzywa termoplastyczne klasy inżynieryjnej, takie jak ABS, HDPE i PVC, w złożone geometrie poprzez formowanie próżniowe / ciśnieniowe, osiągając precyzyjne tolerancje tak wąskie, jak ±0,25 mm w przypadku radomów lotniczych.
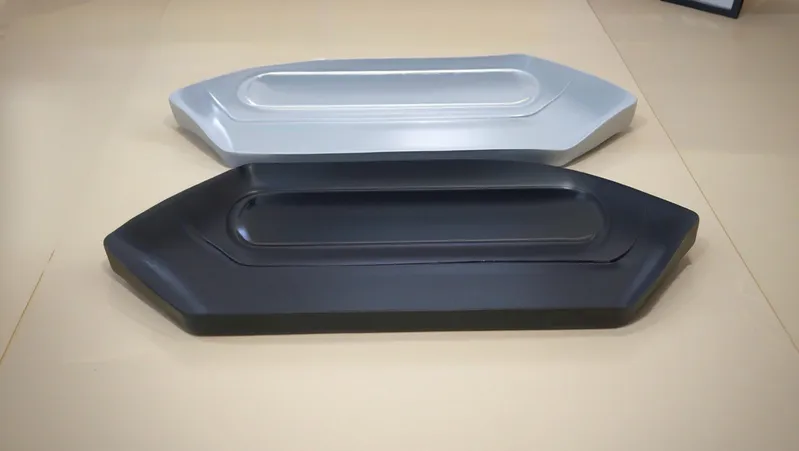
1. Produkcja komponentów lotniczych:
W pracach nad systemem UAV, formowanie próżniowe grubościennych arkuszy ABS o grubości 3-6 mm umożliwiło produkcję lekkich radomów. Proces wspomagany ciśnieniowo osiągnął dokładność krzywizny ±0,25 mm przy jednoczesnym obniżeniu kosztów oprzyrządowania o 60% w porównaniu z metodami formowania kompozytów, pokazując, w jaki sposób formowanie obciągów o dużej grubości rozwiązuje wyzwania związane z precyzją w produkcji obudów lotniczych.
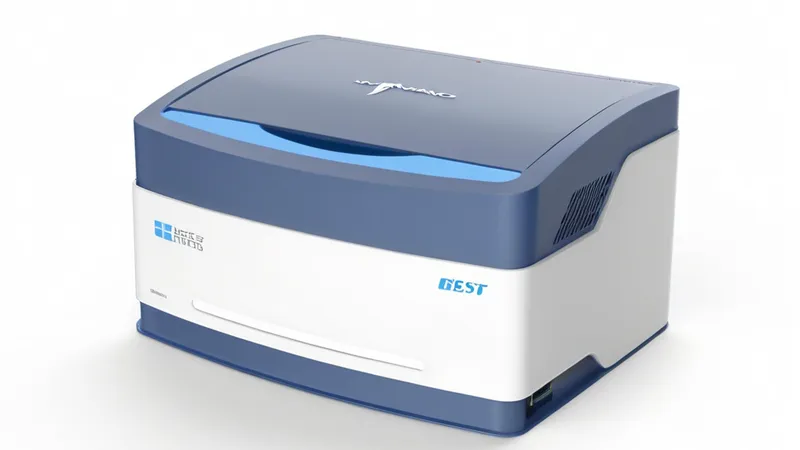
2. Ochrona sprzętu medycznego:
Sterylizowalne obudowy do przenośnych urządzeń MRI zostały opracowane przy użyciu termoformowania grubych arkuszy 4 mm PVC klasy medycznej. Podejście to, wdrożone zgodnie ze standardami pomieszczeń czystych ISO klasy 8, skróciło cykle produkcyjne z 12 tygodni (tradycyjna produkcja metalowa) do 3 tygodni przy zachowaniu kompatybilności z autoklawem, pokazując zalety termoformowania grubych blach.
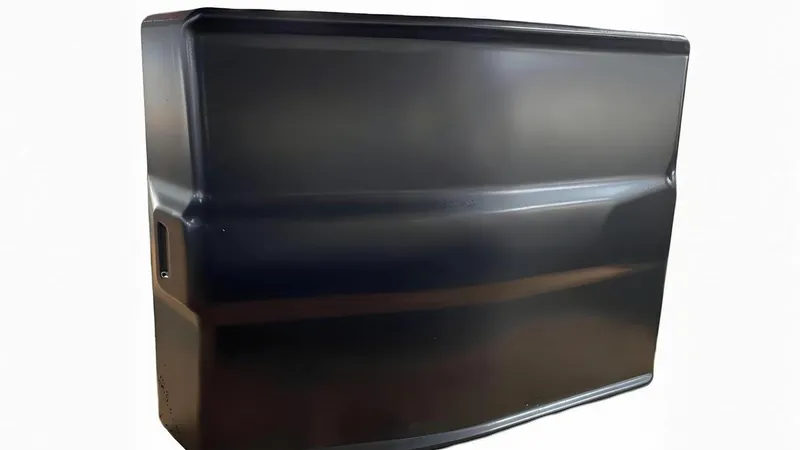
3. Rozwiązania do magazynowania energii w motoryzacji:
Grubościenne, termoformowane, 8-milimetrowe, ognioodporne obudowy akumulatorów z HDPE przeszły testy upadku z wysokości 1,5 metra, osiągając przy tym redukcję masy o 30% w porównaniu z metalowymi alternatywami. Zintegrowana konstrukcja żeber poprzez formowanie próżniowe o dużej grubości zapewniła wzmocnienie strukturalne bez dodatkowego montażu, stanowiąc przykład rozwiązań odpornych na zderzenia w produkcji komponentów EV.
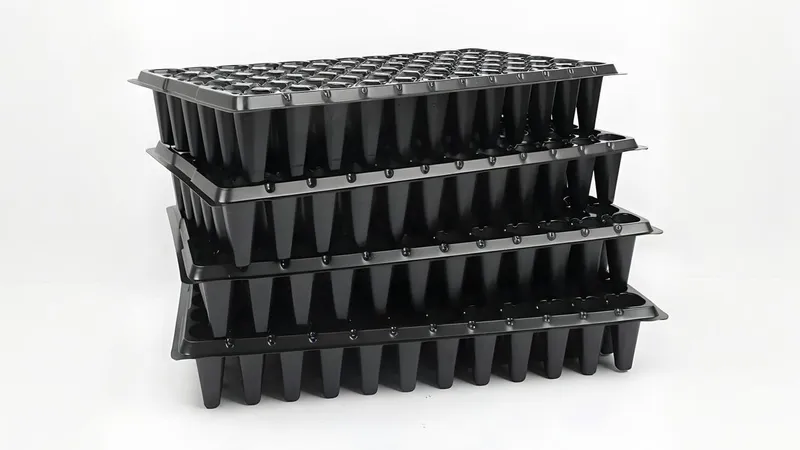
4. Systemy upraw rolnych:
Wielokrotnego użytku tace na sadzonki z HDPE o grubości 5 mm o właściwościach odpornych na nawozy zostały wyprodukowane w procesie wieloetapowego formowania grubościennego. Wyposażone w zazębiające się krawędzie i sieci drenażu korzeni, tace te obsługują ponad 200 cykli wzrostu w pionowych operacjach rolniczych, ilustrując rolę grubościennego formowania ciśnieniowego w zrównoważonym sprzęcie rolniczym.
Wskazówki:
Zmienność procesu | Kluczowe cechy charakterystyczne |
---|---|
Formowanie obłożenia o dużej grubości | Umożliwia głębokie tłoczenie geometrii >150 mm |
Formowanie z grubym pęcherzem | Idealny do replikacji tekstury powierzchni |
Formowanie ciśnieniowe grubych arkuszy | Poprawia definicję szczegółów na materiałach o grubości 5-12 mm |
Wielostopniowe formowanie próżniowe | Nadaje się do złożonych narzędzi wielogniazdowych |
Porównanie: Formowanie próżniowe grubościenne a formowanie próżniowe cienkościenne
Przy wyborze między grubościennym a cienkościennym formowaniem próżniowym, zrozumienie różnic między nimi ma kluczowe znaczenie dla wyboru odpowiedniej metody produkcji. Grubościenne formowanie próżniowe, często stosowane w przypadku elementów konstrukcyjnych, oferuje zwiększoną trwałość i odporność na uderzenia, dzięki czemu idealnie nadaje się do ciężkich zastosowań, takich jak obudowy akumulatorów i obudowy przemysłowe. Z kolei cienkościenne formowanie próżniowe jest preferowane w przypadku lekkiej produkcji wielkoseryjnej, powszechnie stosowanej w opakowaniach i towarach konsumpcyjnych.
1. Podstawowe definicje:
Formowanie próżniowe z grubym miernikiem:
- Grubość materiału: 2-15 mm (tworzywa konstrukcyjne, takie jak ABS, PC, akryl).
- Proces: Wymaga półautomatycznego sprzętu; często konieczne jest przycinanie lub wiercenie CNC po formowaniu. Formy aluminiowe są powszechne.
- Zastosowania: Obudowy przemysłowe (drony, urządzenia medyczne), panele samochodowe, duże oznakowania.
Cienkogabarytowe formowanie próżniowe:
- Grubość materiału: 0,14-2 mm (rolki PVC, PET, PS).
- Proces: Wykorzystuje szybkie zautomatyzowane maszyny z wykrawaniem krawędzi. Rodzaje form obejmują miedź lub aluminium.
- Zastosowania: Opakowania na żywność, blistry, tacki kosmetyczne.
2. Kluczowe porównanie:
Aspekt | Miernik grubości | Thin-Gauge |
---|---|---|
Rodzaje materiałów | ABS, PC, arkusze akrylowe | Rolki PVC, PET, PS |
Wydajność produkcji | Niższa wydajność (dłuższy czas cyklu na część) | Wysoka przepustowość (dziesiątki części na minutę) |
Koszt pleśni | Drogie formy aluminiowe | Tanie formy do miedzi i matryc |
Wytrzymałość produktu | Wysoka odporność na uderzenia, trwałość przy dużych obciążeniach | Lekkie, niekonstrukcyjne zastosowania |
Zrównoważony rozwój | Nadające się do recyklingu, ale energochłonne | Energooszczędne; niektóre biodegradowalne (np. PET) |
3. Zalety i ograniczenia:
Zalety grubego miernika:
- Ekonomiczna alternatywa dla formowania wtryskowego.
- Obsługuje złożone tekstury 3D i zakrzywione struktury.
- Wytrzymałość do użytku zewnętrznego/przemysłowego.
Wady grubego miernika:
- Wysokie zużycie energii i wymagania dotyczące przetwarzania końcowego.
- Zadziory na krawędziach wymagające dodatkowego przycięcia.
Zalety cienkich grubości:
- Efektywność kosztowa dla produkcji masowej.
- Elastyczna obróbka powierzchni (nadruk, flokowanie).
Wady cienkogabarytowe:
- Kruche ze względu na cienkie ścianki i nierówną grubość.
- Ograniczona wytrzymałość strukturalna.
Opcje dostosowywania: Tekstury i przetwarzanie końcowe
Osiągnięcie idealnego wykończenia powierzchni i integralności strukturalnej w produkcji tworzyw sztucznych wymaga zaawansowanych technik dostosowywania. Począwszy od wytłaczania i wyboru materiału, aż po ulepszenia po obróbce, takie jak powłoki i przycinanie CNC, metody te zapewniają optymalną wydajność w różnych branżach, w tym motoryzacyjnej, architektonicznej i dóbr konsumpcyjnych.
1. Opcje dostosowywania tekstur:
① Wytłaczanie i tekstury powierzchni:
- Wzory 3D: Osiągalne dzięki projektowaniu form, w tym wzorów geometrycznych, logo marki lub efektów reliefowych. Formy aluminiowe są powszechnie używane do tworzenia precyzyjnych tekstur.
- Wykończenie powierzchni: Dostępne są wykończenia błyszczące, matowe, teksturowane lub półprzezroczyste. Materiały takie jak ABS i PVC są preferowane w przypadku skomplikowanych tekstur, podczas gdy PMMA (akryl) nadaje się do projektów rozpraszających światło.
② Kompatybilność materiałowa:
- ABS i PVC są idealne do wytłaczania o wysokiej szczegółowości ze względu na ich stabilność termiczną i formowalność. PMMA jest zalecany do zastosowań wymagających przejrzystości optycznej (np. panele oświetleniowe).
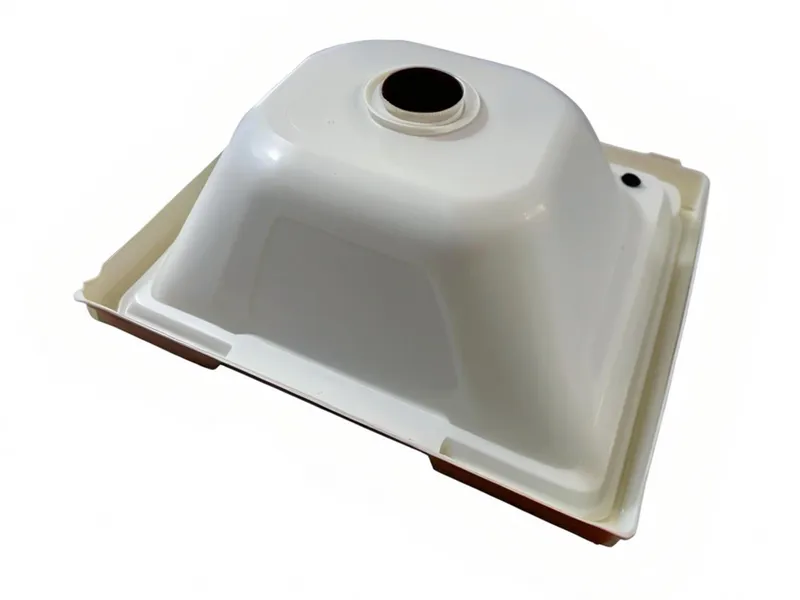
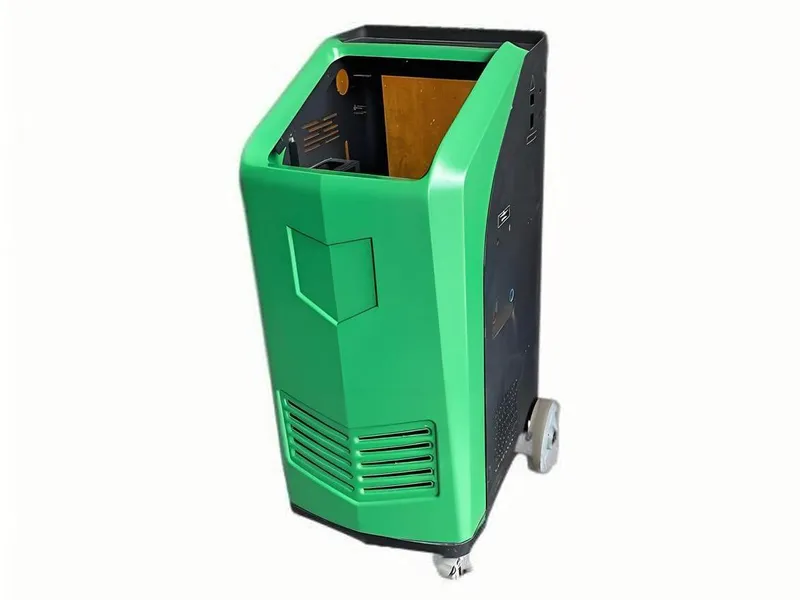
2. Techniki przetwarzania końcowego:
① Powłoki powierzchniowe i drukowanie:
- Malowanie natryskowe: Farby klasy samochodowej z dopasowaniem kolorów Pantone i odpornością na promieniowanie UV zapewniają trwałość na zewnątrz.
- Sitodruk: Obsługuje logo lub tekst o rozdzielczości do 0,3 mm, odpowiedni do oznakowania i brandingu.
- Ochrona przed zarysowaniami i promieniowaniem UV: Dodatki takie jak stabilizatory UV lub środki zmniejszające palność zwiększają wydajność w trudnych warunkach (np. części samochodowe, panele budowlane).
② Ulepszenia strukturalne i funkcjonalne:
- Przycinanie CNC: Zapewnia gładkie krawędzie i precyzyjną dokładność wymiarową, co ma kluczowe znaczenie dla komponentów gotowych do montażu.
- Platerowanie metali/grawerowanie laserowe: Dodaje metaliczne wykończenia lub trwałe oznaczenia w celach estetycznych lub funkcjonalnych.
3. Proces projektowania i produkcji:
① Prototypowanie i DFM (Design for Manufacturability):
- Akceptuje pliki 3D lub próbki fizyczne do replikacji. Zespoły inżynierów optymalizują projekty pod kątem formowania próżniowego, uwzględniając podcięcia i kąty pochylenia.
② Certyfikaty i kontrola jakości:
- Zgodność z normami ISO, certyfikaty materiałowe (np. zgodność z FDA dla PET dopuszczonego do kontaktu z żywnością) i testy próbek pod kątem odporności na uderzenia i warunki atmosferyczne.
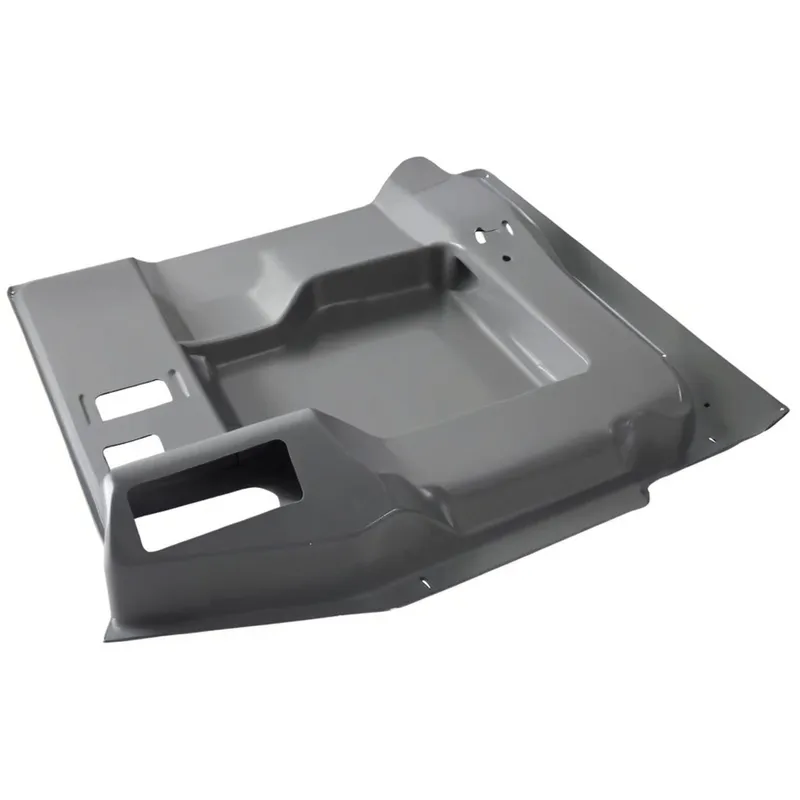
4. Kluczowe zastosowania:
① Motoryzacja:
- Grubościenne zderzaki ABS z wytłoczonymi teksturami i powłokami zapobiegającymi zarysowaniom.
② Architektura:
- Panele ścienne z PVC z powłokami ognioodpornymi i matowymi wykończeniami do namiotów lub przestrzeni przemysłowych.
Towary konsumpcyjne:
- Tacki PET z powłokami antybakteryjnymi do pakowania żywności.
Nasz kompleksowy przepływ usług
1. Przegląd koncepcji
Uzgadnianie specyfikacji, materiałów (PVC/PET/PP) i szkiców z działem sprzedaży/inżynierii. Ocena kosztów, funkcji i wykonalności termoformowania.
2. Projektowanie 3D
Twórz modele 3D wnęk, optymalizując grubość i przepływ materiału. Symulacje zapewniają odporność na naprężenia i możliwość masowej produkcji.
3. Prototypowanie
Tworzenie prototypów drukowanych CNC/3D w celu przetestowania dopasowania, estetyki i uszczelnienia. Dostosowanie tolerancji w celu zapewnienia kompatybilności ze zautomatyzowanymi maszynami.
4. Produkcja form
Finalizacja form aluminiowych/kompozytowych z analizą DFM. Integracja kanałów chłodzących i testy trwałości w celu uzyskania wysokiej wydajności cyklicznej.
5. Formowanie próżniowe
Podgrzewanie plastikowych arkuszy do stanu giętkości; formowanie próżniowe nad formami. Monitorowanie parametrów (temperatura, ciśnienie) w celu zapobiegania defektom, takim jak wypaczanie.
6. Przycinanie
Przycinanie nadmiaru materiału za pomocą precyzyjnych ostrzy/wykrawarek. Dodawanie perforacji lub wygładzanie krawędzi w celu bezproblemowej integracji opakowania.
7. Wykończenie
Ulepsza produkty formowane próżniowo poprzez malowanie, powlekanie UV, teksturowanie lub wytrawianie laserowe w celu uzyskania wykończeń (matowych, błyszczących, metalicznych).
8. Kontrola jakości i pakowanie
Przeprowadzanie testów szczelności, kontroli wymiarów i inspekcji wizualnych. Montaż opakowań typu clamshell i pakowanie w kartony/kody kreskowe klasy eksportowej.
najczęściej zadawane pytania dla klientów
Pierwsze kroki z Uplastech
Masz pytania? Mamy odpowiedzi.
Specjalizujemy się w wytłaczaniu, formowaniu próżniowym, rozdmuchiwaniu i precyzyjnym wytwarzaniu form, oferując niestandardowe rozwiązania spełniające różnorodne potrzeby produkcyjne.
Współpracujemy z różnymi branżami, w tym motoryzacyjną, elektroniczną, dóbr konsumpcyjnych i opakowań, koncentrując się na partnerstwie B2B i dostarczaniu rozwiązań w zakresie wytłaczania, termoformowania, rozdmuchiwania i precyzyjnego formowania.
Tak, dostosowujemy nasze rozwiązania do Twoich unikalnych wymagań.
Skontaktuj się
Napisz do nas lub wypełnij poniższy formularz, aby uzyskać wycenę.
E-mail: uplastech@gmail.com