Rozwiązania do formowania próżniowego cienkościennego
Poznaj wydajne rozwiązania do formowania próżniowego cienkościennego. Odblokuj innowacyjność i precyzję na potrzeby wtrysku tworzyw sztucznych.
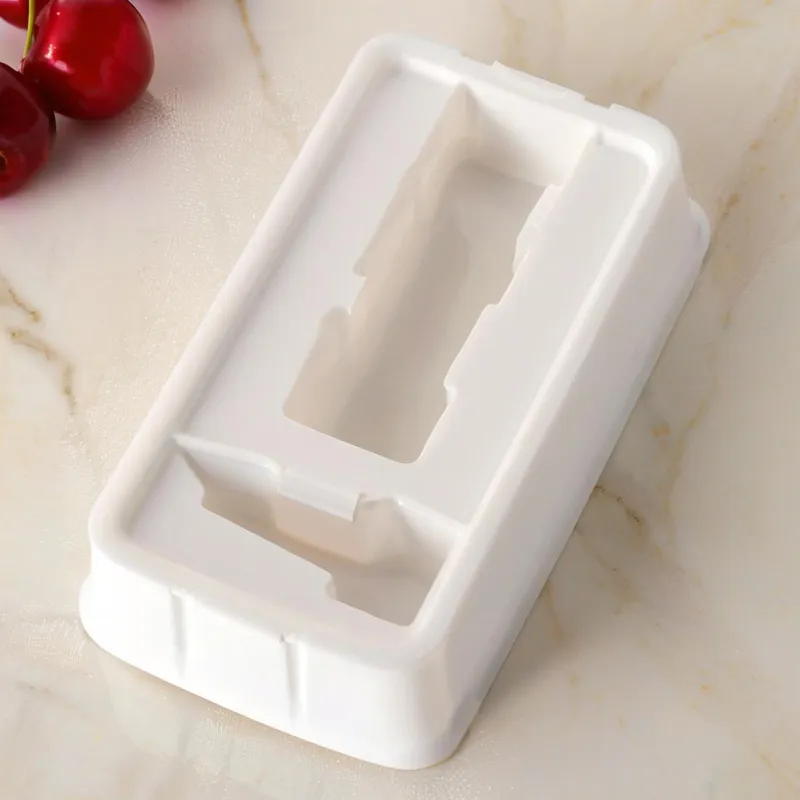
Przewodnik po niestandardowym formowaniu próżniowym cienkościennym (cienkościennym)
Wprowadzenie do formowania próżniowego cienkościennego
Formowanie próżniowe cienkościenne to proces produkcyjny, w którym podgrzany arkusz tworzywa sztucznego jest kształtowany nad formą przy użyciu ciśnienia próżniowego, w wyniku czego powstają części o stosunkowo cienkich ściankach. Metoda ta jest szczególnie odpowiednia do prototypowania i produkcji nisko- i średnioseryjnej, oferując równowagę kosztów i szybkości.
Formowanie próżniowe, często nazywane formowaniem próżniowym cienkościennym, gdy koncentruje się na produkcji części o cieńszych ściankach, jest techniką termoformowania, która podgrzewa arkusz tworzywa sztucznego, aż stanie się giętki, a następnie wykorzystuje próżnię do ścisłego przyciągnięcia go do powierzchni formy. Proces ten jest ceniony za swoją prostotę i przystępną cenę, tworząc lekkie komponenty o ogólnie jednolitej grubości, które mogą być przezroczyste lub nieprzezroczyste w zależności od materiału. Jest to doskonały wybór dla producentów, którzy potrzebują wydajnej produkcji cienkościennych elementów, takich jak tace do pakowania, panele samochodowe lub osłony urządzeń medycznych, zwłaszcza gdy skomplikowane maszyny lub narzędzia wysokociśnieniowe nie są wykonalne.
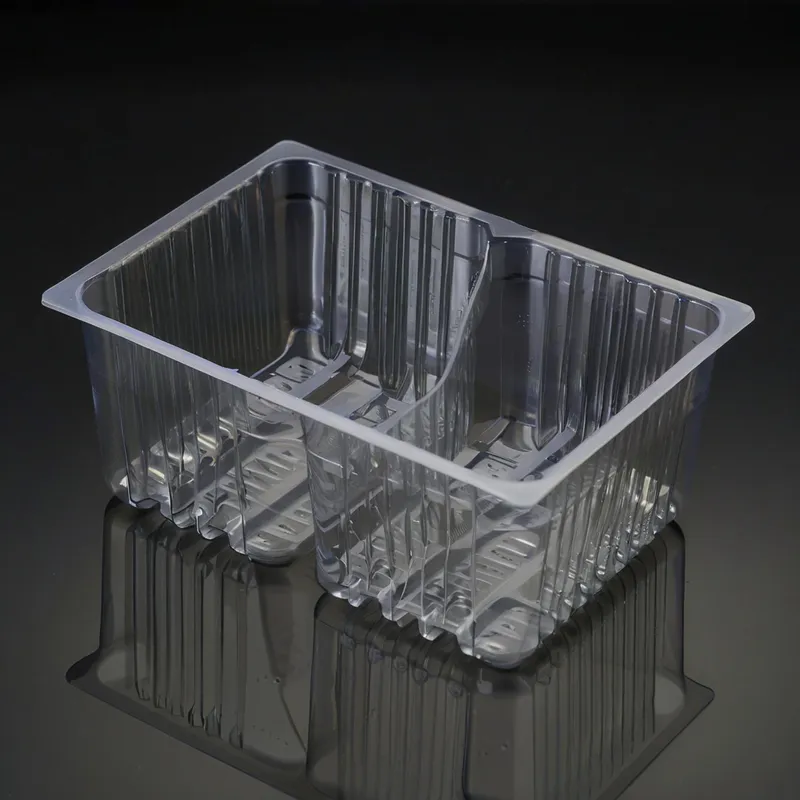
W przeciwieństwie do bardziej skomplikowanych metod, takich jak formowanie wtryskowe, formowanie próżniowe wyróżnia się niższymi barierami wejścia, wymagającymi tańszego oprzyrządowania i prostszego sprzętu. Sprawia to, że jest to idealne rozwiązanie dla małych firm, startupów lub każdego, kto prototypuje nowe projekty bez ponoszenia z góry kosztów produkcji na dużą skalę.
Jak krok po kroku przetwarzać cienkościenne formowanie próżniowe?
Proces formowania próżniowego cienkich ścianek to usprawniona, ale precyzyjna sekwencja kroków dostosowana do produkcji części o cienkich, jednolitych ściankach. Oto szczegółowy podział:
1. Ogrzewanie:
Cienki arkusz tworzywa sztucznego, takiego jak ABS lub polistyren, jest podgrzewany w temperaturze od 120°C do 180°C, dzięki czemu staje się miękki i elastyczny.
2. Pozycjonowanie formy:
Podgrzany arkusz jest ostrożnie umieszczany na formie wykonanej z aluminium lub polimerów drukowanych w 3D, zapewniając precyzję.
3. Zastosowanie próżniowe:
Próżnia mocno przyciąga tworzywo sztuczne do formy, kształtując je i zapobiegając nadmiernemu rozciągnięciu, które mogłoby osłabić część.
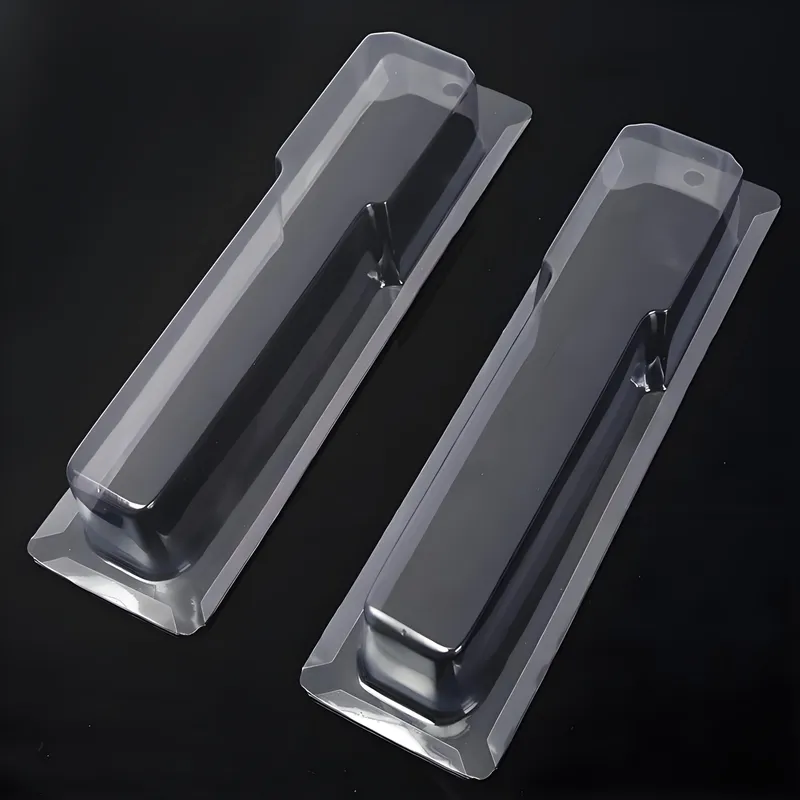
5. Przycinanie:
Nadmiar materiału jest usuwany za pomocą routerów CNC lub cięcia ręcznego, a następnie szlifowany w celu uzyskania gładkiego i wypolerowanego wykończenia.
4. Chłodzenie:
Wentylatory lub mgiełka szybko schładzają tworzywo sztuczne, zapewniając prawidłowe uformowanie kształtu, minimalizując jednocześnie wszelkie wypaczenia.
Proces ten jest wydajny, często zajmuje tylko kilka minut na cykl, ale wymaga starannej uwagi na etapach ogrzewania i próżni, aby utrzymać pożądaną cienkość i wytrzymałość. Oto tabela podsumowująca poszczególne etapy:
Krok | Opis |
---|---|
Ogrzewanie | Cienki arkusz tworzywa sztucznego jest podgrzewany do stanu giętkiego (120°C-180°C). |
Pozycjonowanie formy | Podgrzany arkusz jest wyrównywany nad formą (aluminiową lub wydrukowaną w 3D). |
Aplikacja próżniowa | Próżnia przyciąga arkusz do formy, tworząc cienkie ścianki (0,5 mm-2 mm). |
Chłodzenie | Część jest chłodzona za pomocą wentylatorów lub mgły, aby zestalić cienkościenną strukturę. |
Przycinanie | Nadmiar materiału jest usuwany, a krawędzie są wykańczane w celu uzyskania końcowej cienkościennej części. |
Zalety i ograniczenia formowania próżniowego cienkościennego
Formowanie próżniowe cienkościenne oferuje wyraźne korzyści, ale wiąże się również z wyzwaniami, które należy wziąć pod uwagę. Oto szczegółowe spojrzenie:
1. Zalety:
① Efektywność kosztowa: Koszty oprzyrządowania są stosunkowo niskie, dzięki czemu jest to przystępne cenowo rozwiązanie do produkcji cienkościennych części w małych i średnich ilościach (250-3000 sztuk).
Lekkie części: Dzięki wykorzystaniu minimalnej ilości materiału, proces ten pozwala na tworzenie wyjątkowo lekkich komponentów, idealnych do zastosowań, w których redukcja wagi poprawia wydajność, takich jak deski rozdzielcze w samochodach lub części kabin lotniczych.
③ Szybka produkcja: Cykle są szybkie - często poniżej 10 minut od nagrzania do przycięcia - umożliwiając szybką realizację prototypów lub pilnych potrzeb produkcyjnych.
④ Wydajność materiałowa: Cienkościenne formowanie próżniowe minimalizuje zużycie plastiku, zmniejszając zarówno koszty, jak i ilość odpadów, a odpady często nadają się do recyklingu.
2. Ograniczenia:
① Spójność grubości ścianki: Utrzymanie jednolitej grubości w głębszych sekcjach może być trudne, potencjalnie prowadząc do cienkich plam lub słabości strukturalnych, jeśli nie jest starannie zarządzane.
② Tylko proste geometrie: Proces ten doskonale radzi sobie z podstawowymi kształtami, ale ma trudności ze złożonymi projektami, takimi jak te z podcięciami lub skomplikowanymi detalami, co ogranicza jego wszechstronność.
③ Nie dla dużych wolumenów: Chociaż jest to ekonomiczne w przypadku mniejszych serii, staje się mniej konkurencyjne w przypadku produkcji na dużą skalę w porównaniu z metodami takimi jak formowanie wtryskowe ze względu na konieczność ręcznego wykańczania.
④ Wykończenie wtórne: Przycinanie i wygładzanie cienkościennych części często wymaga dodatkowego nakładu pracy, co zwiększa całkowity czas i koszty.
3. Porównanie:
Zalety | Ograniczenia |
---|---|
Niskie koszty oprzyrządowania | Trudność w zapewnieniu jednolitej grubości ścianki |
Lekkie komponenty | Ograniczone do prostych kształtów |
Szybkie cykle produkcyjne | Mniejsza wydajność przy dużych nakładach |
Zmniejszona ilość odpadów materiałowych | Wymaga dodatkowego przycinania i wykańczania |
Jakie materiały są stosowane w formowaniu próżniowym cienkościennym?
W procesie formowania próżniowego cienkościennych profili powszechnie stosuje się różne materiały termoplastyczne ze względu na ich zdolność do podgrzewania, rozciągania i formowania w precyzyjne kształty. Kluczowe materiały obejmują:
Materiały | Właściwości i zastosowania |
---|---|
ABS (akrylonitryl-butadien-styren) | Trwałe, odporne na uderzenia i łatwe do formowania. Idealny do części samochodowych, towarów konsumpcyjnych i obudów elektronicznych. |
HIPS (polistyren wysokoudarowy) | Lekki, ekonomiczny i dobry do opakowań, pojemników jednorazowych i prototypów. Mniej odporny na ciepło niż ABS. |
PVC (polichlorek winylu) | Opcje sztywne lub elastyczne. Odporny na chemikalia i trudnopalny; stosowany w sprzęcie medycznym, oznakowaniu i budownictwie. |
PETG (glikol politereftalanu etylenu) | Łączy w sobie przejrzystość, wytrzymałość i odporność chemiczną. Powszechnie stosowane w opakowaniach żywności, urządzeniach medycznych i wyświetlaczach. |
Poliwęglan (PC) | Wysoka wytrzymałość, przezroczystość i odporność na ciepło. Stosowany w osłonach ochronnych, oświetleniu i komponentach lotniczych. |
Polipropylen (PP) | Elastyczny, odporny na chemikalia i zmęczenie materiału. Nadaje się do żywych zawiasów, pojemników i części samochodowych. |
Akryl (PMMA) | Doskonała przejrzystość optyczna i odporność na promieniowanie UV. Idealny do wyświetlaczy, soczewek i przedmiotów dekoracyjnych. |
HDPE (polietylen o wysokiej gęstości) | Sztywny, odporny na chemikalia i wilgoć. Używany do produkcji pojemników przemysłowych i części technicznych. |
Czynniki wyboru:
Wybór materiału zależy od wymagań aplikacji, takich jak wytrzymałość, elastyczność, stabilność termiczna, odporność chemiczna i koszt. Formowanie cienkościenne często stawia na materiały o dobrej charakterystyce płynięcia (np. PETG, ABS), aby uzyskać precyzyjne, lekkie części bez rozdzierania.
Kluczowe kwestie projektowe dotyczące formowania próżniowego cienkościennego
Projektowanie pod kątem cienkościennego formowania próżniowego wymaga określonych wytycznych, aby zapewnić, że cienkościenne części będą zarówno funkcjonalne, jak i możliwe do wyprodukowania:
① Kąty zanurzenia: Kąty 5°-10° dla form żeńskich i 3°-5° dla form męskich umożliwiają łatwe wyjmowanie bez uszkadzania cienkich ścianek.
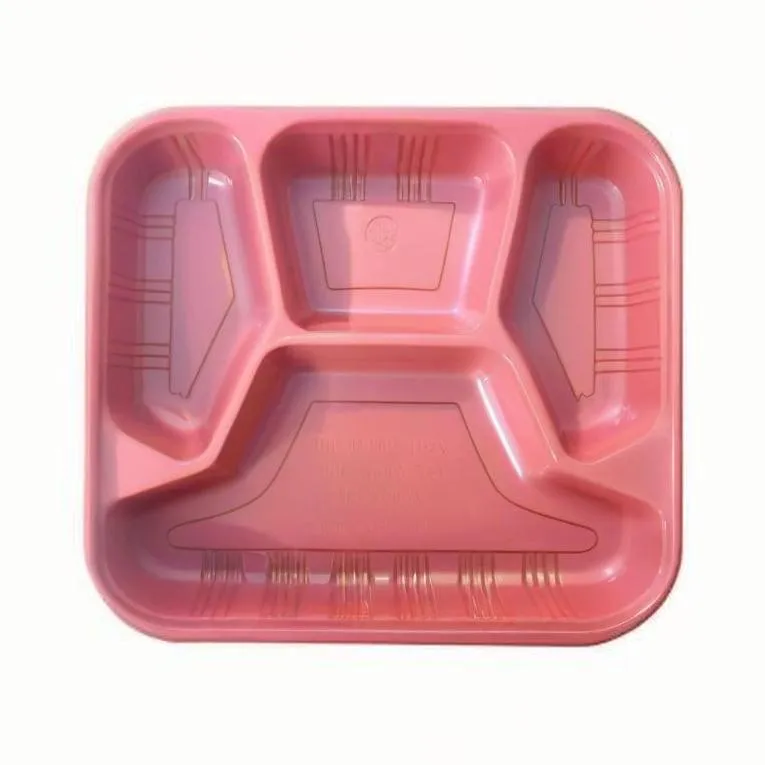
② Grubość ścianki: Celuj w jednolitą grubość (0,5 mm-2 mm), aby uniknąć słabych punktów; nierównomierne rozciąganie może wystąpić, jeśli nie zostanie starannie zaplanowane.
③ Unikaj głębokich zaciągnięć: Głębokość rysowania powinna być niewielka - najlepiej mniejsza niż 75% najmniejszej szerokości górnej części - aby zapobiec nadmiernemu przerzedzeniu lub rozdarciu.
Zaokrąglone funkcje: Należy stosować duże promienie (minimum 3 mm) i gładkie narożniki w celu zmniejszenia naprężeń i pęknięć w cienkich ściankach.
⑤ Podcięcia graniczne: Zminimalizuj podcięcia lub zwisy, ponieważ komplikują one uwalnianie formy i mogą wymagać dodatkowego oprzyrządowania.
Zastosowania formowania próżniowego cienkościennego
Cienkościenne formowanie próżniowe to wszechstronny i opłacalny proces produkcyjny wykorzystywany do wytwarzania lekkich, trwałych i precyzyjnych elementów z tworzyw sztucznych. Jego zastosowania obejmują różne branże ze względu na wydajność w tworzeniu złożonych kształtów przy minimalnych stratach materiału. Kluczowe zastosowania obejmują:
1. Opakowanie:
Opakowania na żywność: Tacki, pojemniki z klapką i kubki jednorazowe.
Opakowania blistrowe: Dla farmaceutyków, elektroniki lub towarów konsumpcyjnych.
Opakowania detaliczne: Niestandardowe pojemniki na kosmetyki, zabawki lub elektronikę.
2. Towary konsumpcyjne:
Jednorazowa zastawa stołowa: Talerze, miski i sztućce.
Artykuły gospodarstwa domowego: Pojemniki do przechowywania, wkłady do lodówek lub panele prysznicowe.
Pojemniki na kosmetyki: Cienkościenne słoiki, pokrywki i pojemniki kompaktowe.
3. Medycyna i opieka zdrowotna:
Sterylne tacki: Do pakowania narzędzi chirurgicznych lub urządzeń medycznych.
② Elementy jednorazowego użytku: Pojemniki na próbki, organizery na tabletki lub osłony ochronne.
4. Rolnictwo:
Tace do sadzonek: Cienkościenne tace do rozmnażania roślin wielokrotnego użytku.
② Osłony ochronne: Dla sprzętu lub upraw.
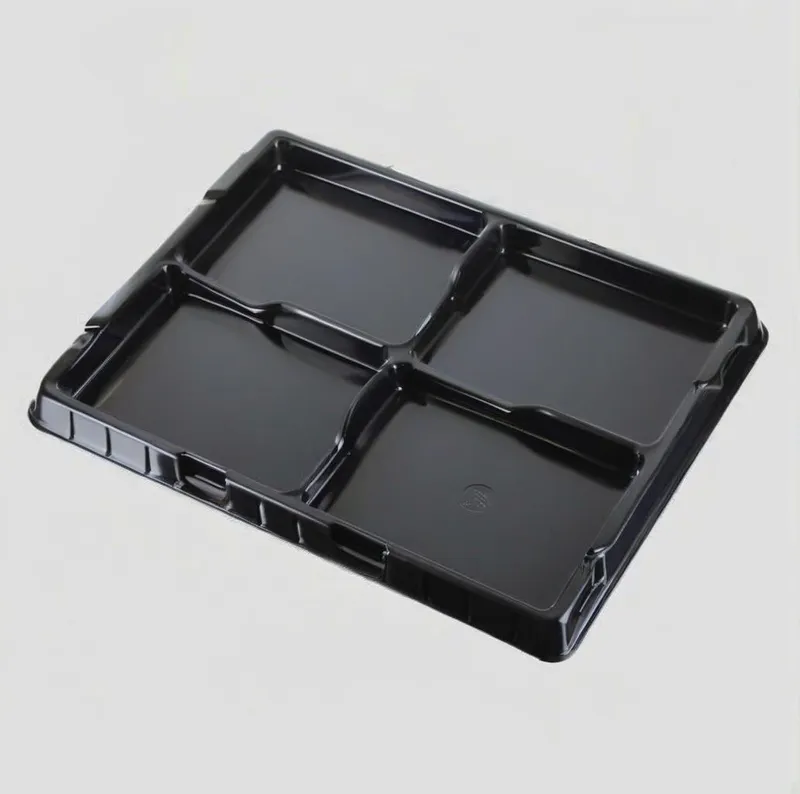
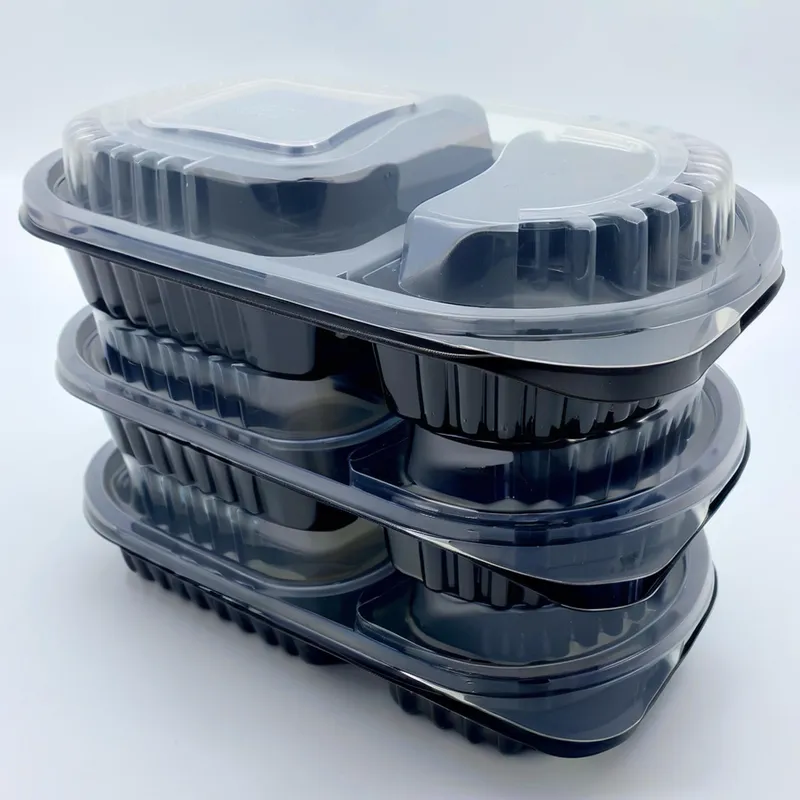
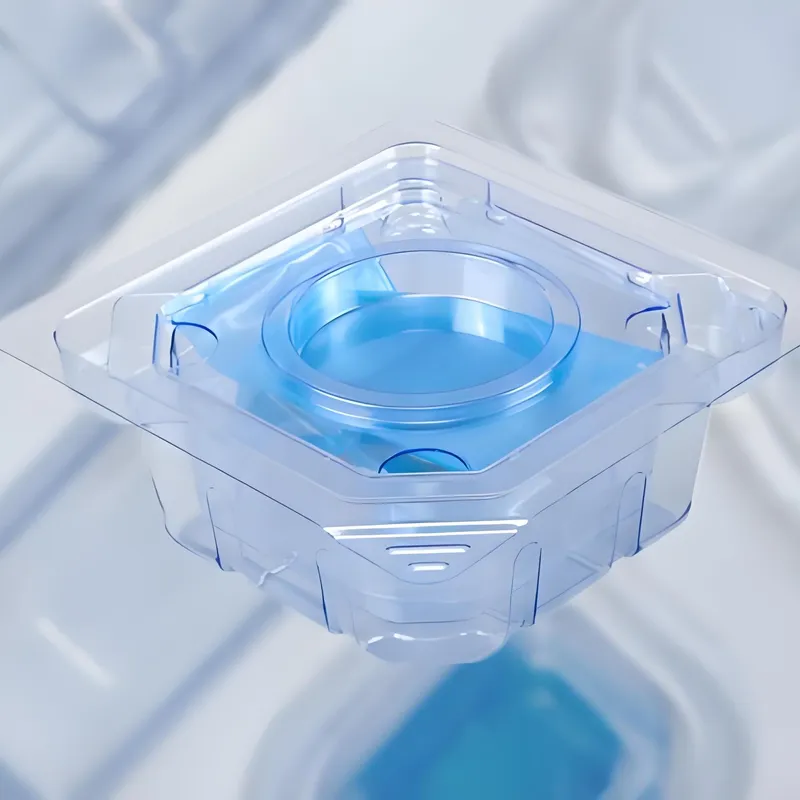

Rozwiązania do formowania próżniowego cienkościennego
Odkryj trwałe, wysoce precyzyjne rozwiązania do termoformowania z niestandardowym wsparciem projektowym i wszechstronnością materiałów. Poproś o wycenę już dziś!
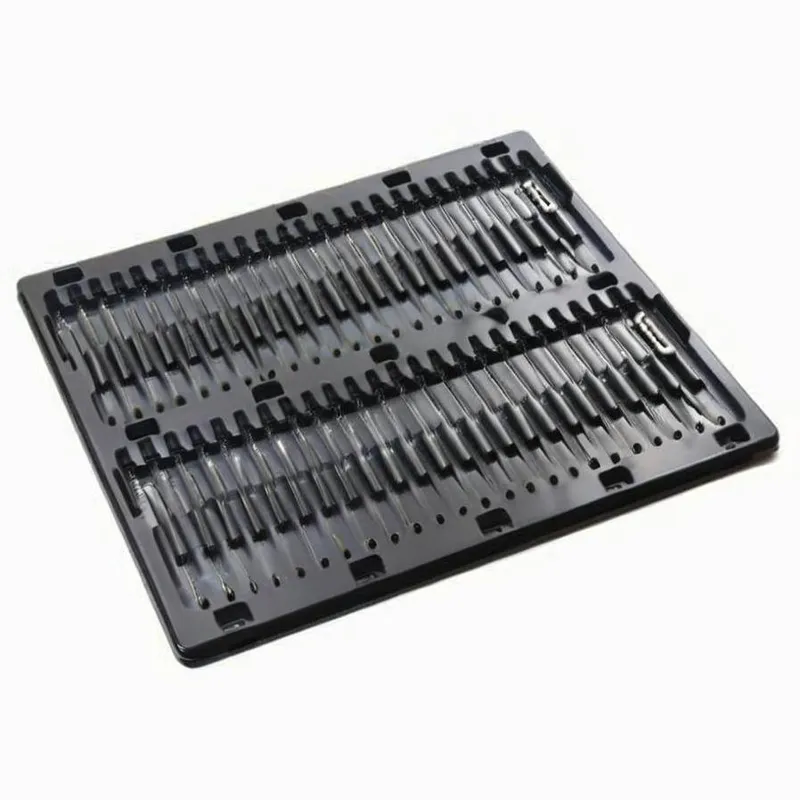
Przewodnik po niestandardowym formowaniu próżniowym cienkościennym (cienkościennym)
- Automatyzacja formowania próżniowego cienkościennego
- Wyzwania i rozwiązania w formowaniu próżniowym cienkościennym
- Jak skalować produkcję za pomocą formowania próżniowego cienkościennego?
- Formowanie próżniowe cienkogabarytowe a formowanie próżniowe ciężkogabarytowe
- Wysokiej jakości, spójne formy do termoformowania cienkościennego
- Jakie są rodzaje cienkościennych form do termoformowania?
Automatyzacja formowania próżniowego cienkościennego
Automatyzacja przekształca formowanie próżniowe cienkościenne, zwiększając wydajność i spójność. Oto jak nowoczesna technologia jest zintegrowana z procesem:
① Zrobotyzowana obsługa materiałów: Roboty ładują plastikowe arkusze do maszyny i wyjmują gotowe części, ograniczając pracę ręczną i przyspieszając czas cyklu.
② Przycinanie CNC: Po formowaniu, maszyny sterowane numerycznie (CNC) precyzyjnie przycinają nadmiar materiału z cienkościennych części, zapewniając czyste krawędzie i powtarzalność.
③ Kontrole jakości na linii produkcyjnej: Zautomatyzowane czujniki monitorują temperaturę arkusza, ciśnienie próżni i wymiary części w czasie rzeczywistym, sygnalizując problemy przed ich eskalacją.
④ Programowalne sterowniki logiczne (PLC): Systemy te zarządzają całym procesem - ogrzewaniem, formowaniem i chłodzeniem - przy użyciu wstępnie ustawionych parametrów, minimalizując błędy ludzkie.
W przypadku średniej wielkości serii 1000 części automatyzacja może skrócić czas produkcji o 20-30%, jednocześnie poprawiając jednorodność, co czyni ją przełomem w branżach o wysokim popycie.
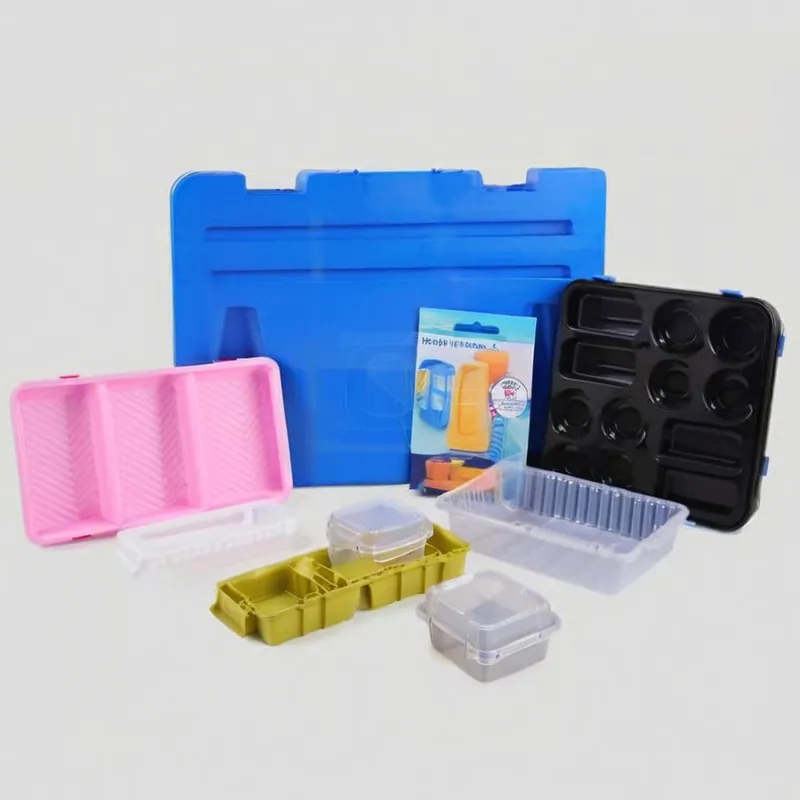
Wyzwania i rozwiązania w formowaniu próżniowym cienkościennym
Podczas gdy formowanie próżniowe cienkościenne oferuje wiele korzyści, wiąże się ono z wyzwaniami, którym producenci muszą sprostać:
1. Nierównomierne przerzedzenie:
Wyzwanie: Głębokie rysowanie może zbytnio rozciągnąć materiał, osłabiając niektóre obszary.
Rozwiązanie: Należy używać narzędzi wspomagających, które wstępnie równomiernie rozciągają arkusz, zanim podciśnienie wciągnie go do formy.
2. Wypaczenie:
① Wyzwanie: Cienkie części mogą odkształcać się podczas chłodzenia z powodu naprężeń wewnętrznych.
Rozwiązanie: Zoptymalizuj szybkość chłodzenia za pomocą wentylatorów lub mgły wodnej i użyj uchwytów, aby utrzymać kształt części podczas chłodzenia.
3. Ograniczona szczegółowość:
Wyzwanie: Formowanie próżniowe zmaga się ze skomplikowanymi elementami w porównaniu do formowania wtryskowego.
Rozwiązanie: Połączenie z formowaniem ciśnieniowym lub obróbką po procesie w celu uzyskania dokładniejszych detali.
Jak skalować produkcję za pomocą formowania próżniowego cienkościennego?
Skalowanie od prototypu do pełnej produkcji w zakresie formowania próżniowego cienkościennych elementów wymaga strategicznego planowania. Oto, w jaki sposób producenci płynnie przechodzą do tego procesu:
① Prototypowanie: Zacznij od niedrogich form drukowanych w 3D lub drewnianych do testowania projektów. Pojedyncza prototypowa forma może kosztować zaledwie $150.
② Małe nakłady: Przejdź na formy aluminiowe dla partii 100-500 sztuk. Formy te są trwałe, a jednocześnie przystępne cenowo, równoważąc koszty i jakość.
③ Produkcja wielkoseryjna: W przypadku ponad 1000 sztuk, formy wielogniazdowe (tworzące kilka części jednocześnie) zwiększają wydajność. Koszty oprzyrządowania rosną, ale koszty jednostkowe znacznie spadają.
④ Optymalizacja procesów: Precyzyjnie dostosuj czas nagrzewania, siłę próżni i przycinanie, aby zmaksymalizować wydajność bez utraty jakości.
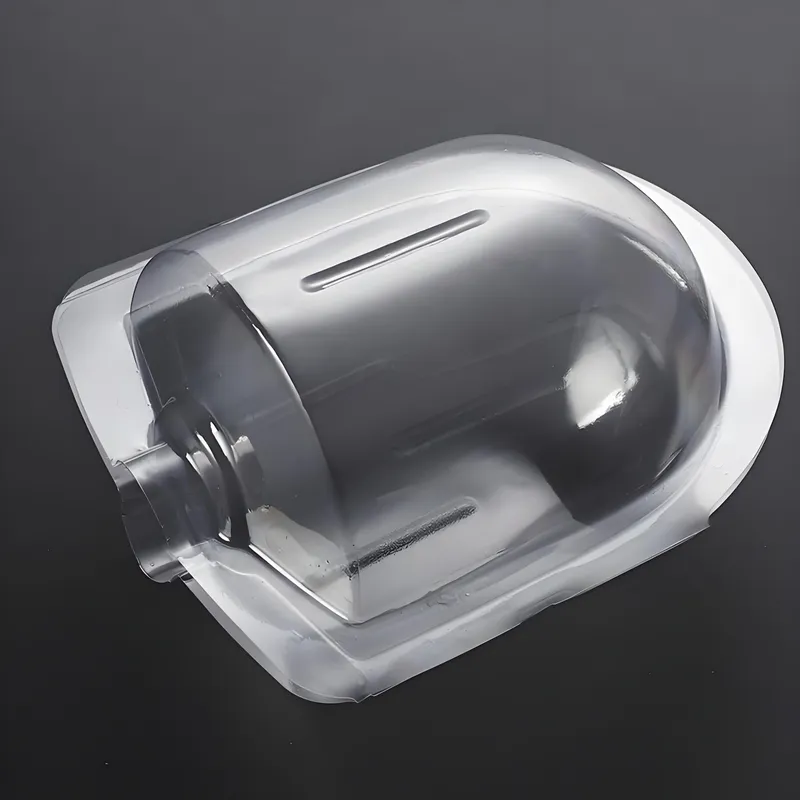
Formowanie próżniowe cienkogabarytowe a formowanie próżniowe ciężkogabarytowe
Formowanie próżniowe cienkowarstwowe i formowanie próżniowe grubowarstwowe to dwie odmiany procesu termoformowania, różniące się przede wszystkim grubością używanych arkuszy tworzyw sztucznych i ich zastosowaniami.
1. Grubość materiału:
① Thin Gauge: Obejmuje arkusze z tworzywa sztucznego cieńsze niż 0,060 cala (1,5 mm), często dostarczane w rolkach do ciągłego przetwarzania.
② Heavy Gauge: Wykorzystuje arkusze o grubości od 0,060 cala (1,5 mm) do 0,500 cala (12,7 mm) lub grubsze, zazwyczaj cięte na wymiar i podawane pojedynczo.
2. Zastosowania:
① Thin Gauge: Powszechnie stosowane w lekkich produktach jednorazowego użytku o dużej objętości, takich jak tacki do pakowania, opakowania typu clamshell, blistry i pojemniki na żywność.
② Heavy Gauge: Stosowany do trwałych, strukturalnych części, takich jak komponenty samochodowe (np. deski rozdzielcze), obudowy urządzeń medycznych i osłony przemysłowe.
3. Charakterystyka procesu:
① Thin Gauge: Charakteryzuje się krótszym czasem cyklu dzięki właściwościom szybkiego nagrzewania i chłodzenia cienkiego materiału. Często integruje zautomatyzowane przycinanie i układanie w stosy w celu zwiększenia wydajności.
② Heavy Gauge: Wymaga dłuższych okresów nagrzewania i chłodzenia, co skutkuje wolniejszą produkcją, ale umożliwia uzyskanie bardziej złożonych kształtów i większej wytrzymałości części.
4. Zalety i wady:
① Thin Gauge:
- Zalety: Opłacalny przy masowej produkcji, lekki i generuje minimalną ilość odpadów.
- Wady: Ograniczone do prostszych konstrukcji i mniej wytrzymałych części.
② Heavy Gauge:
- Zalety: Wytwarza solidne, trwałe części o większej elastyczności projektowej (np. podcięcia, szczegółowe tekstury).
- Wady: Wyższe koszty materiałów i narzędzi, wolniejsze tempo produkcji.
Wysokiej jakości, spójne formy do termoformowania cienkościennego
Osiągnięcie wysokiej jakości i spójności form do termoformowania cienkościennego ma kluczowe znaczenie dla produkcji jednolitych części, zwłaszcza w przypadku dużych serii. Kluczowe czynniki wpływające na jakość form obejmują:
1. Wybór materiału:
① Aluminium: Preferowany do form produkcyjnych ze względu na swoją trwałość, doskonałą przewodność cieplną i zdolność do zachowania wąskich tolerancji przez tysiące cykli.
② Kompozyt / żywica epoksydowa: Używany do prototypów lub krótkich serii, oferując mniej trwałą, ale bardziej przystępną cenowo alternatywę.
2. Precyzja projektu:
Narzędzia CAD/CAM: Formy są projektowane za pomocą wspomagania komputerowego (CAD) i obrabiane za pomocą wspomagania komputerowego (CAM) w celu zapewnienia dokładności i powtarzalności.
② Kąty i promienie zanurzenia: Kąty pochylenia (3-5 stopni) i gładkie promienie zapewniają łatwe uwalnianie części i zapobiegają przerzedzaniu materiału.
3. Systemy chłodzenia:
① Kanały chłodzące: Zintegrowane kanały zapewniają jednolitą kontrolę temperatury, skracając czas cyklu i zapewniając stałą jakość części.
② Zarządzanie temperaturą: Skuteczne chłodzenie zapobiega wypaczaniu i utrzymuje stabilność wymiarową cienkich części.
4. Wykończenie powierzchni:
① Polerowana/Teksturowana: Polerowana forma daje błyszczące części, podczas gdy teksturowane powierzchnie tworzą matowe lub wzorzyste wykończenia.
② Wentylacja: Strategicznie rozmieszczone otwory wentylacyjne umożliwiają ucieczkę powietrza, zapewniając pełne dopasowanie tworzywa sztucznego do formy bez wad.
5. Techniki produkcji:
① Obróbka CNC: Precyzyjna obróbka zapewnia dokładne odwzorowanie cech formy, co ma kluczowe znaczenie dla spójności w dużych seriach.
② Konstrukcje modułowe: Wymienne wkładki umożliwiają szybką zmianę projektu bez konieczności wymiany całej formy.
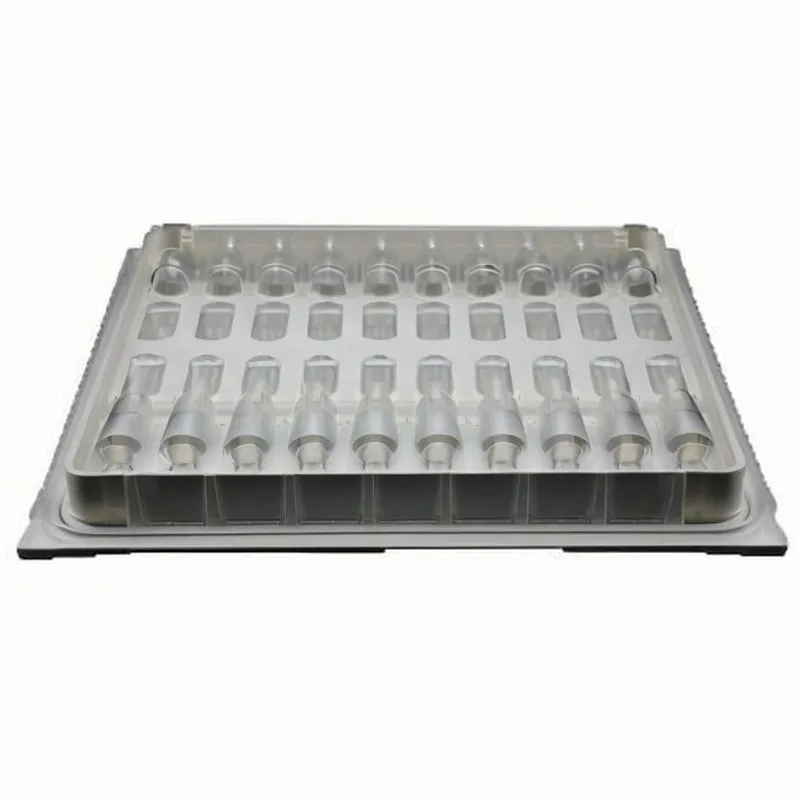
Jakie są rodzaje cienkościennych form do termoformowania?
Istnieje kilka rodzajów cienkościennych form do termoformowania, z których każdy jest dostosowany do konkretnych potrzeb produkcyjnych, budżetu i wymagań dotyczących części:
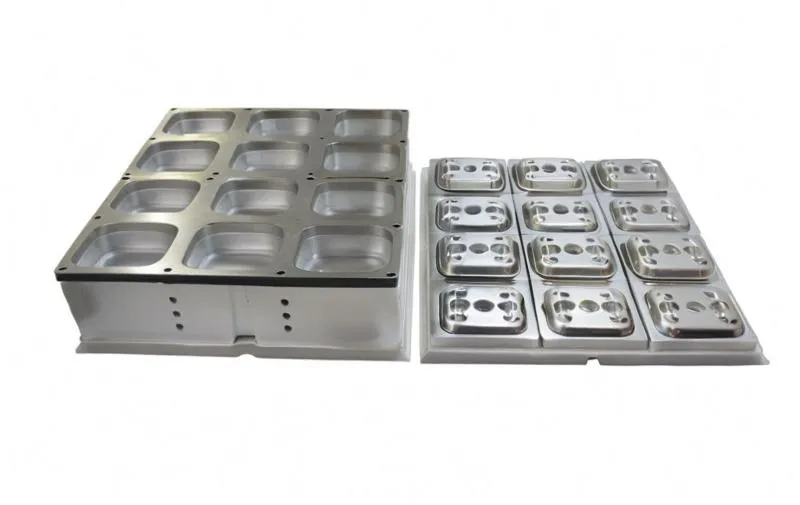
1. Formy aluminiowe:
Wykonane z wysokiej jakości aluminium, są najlepszym wyborem dla form produkcyjnych.
- Zastosowanie: Wysokonakładowa produkcja opakowań, tacek i pojemników.
- Zalety: Trwałe, doskonałe przenoszenie ciepła i możliwość odwzorowania najdrobniejszych szczegółów.
- Wady: Wyższy koszt początkowy.
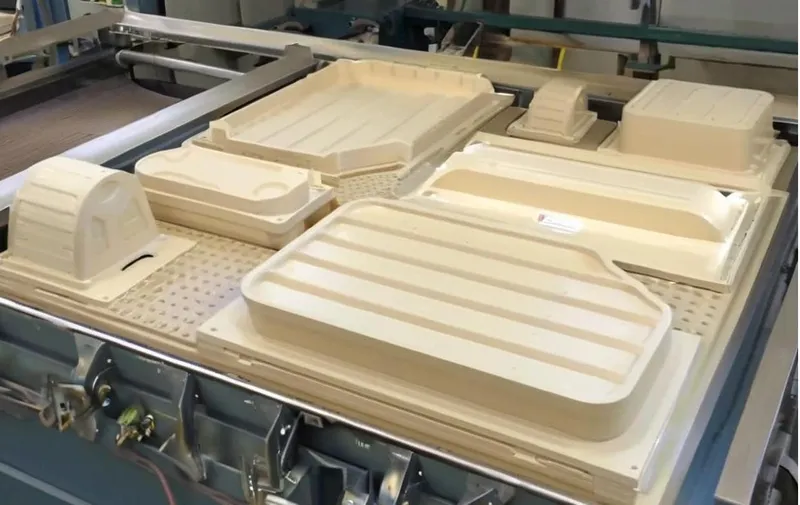
2. Formy kompozytowe:
Wykonane z żywicy epoksydowej lub włókna szklanego, formy te są lżejsze i tańsze.
- Zastosowania: Prototypowanie lub produkcja krótkoseryjna.
- Zalety: Przystępna cena i szybkość produkcji.
- Wady: Mniejsza trwałość, zazwyczaj 100-500 cykli.
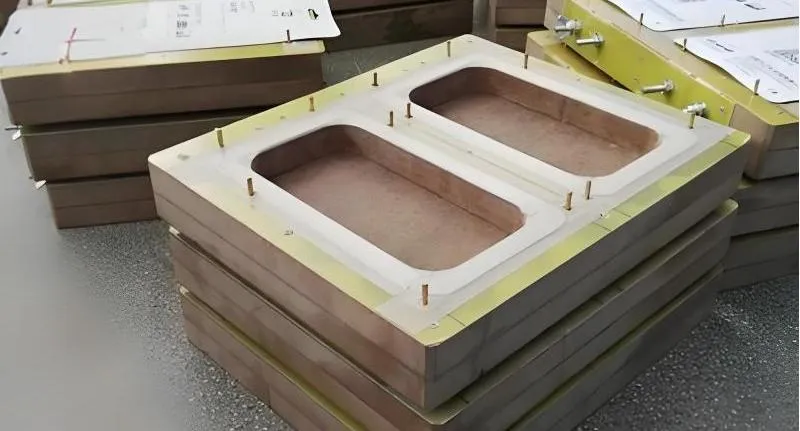
3. Drewniane formy:
Zbudowany z twardego drewna lub sklejki dla podstawowych potrzeb formowania.
- Zastosowania: Jednorazowe części lub wczesne prototypy.
- Plusy: Niedrogie i szybkie do stworzenia.
- Wady: Podatne na zużycie i nie nadają się do produkcji.
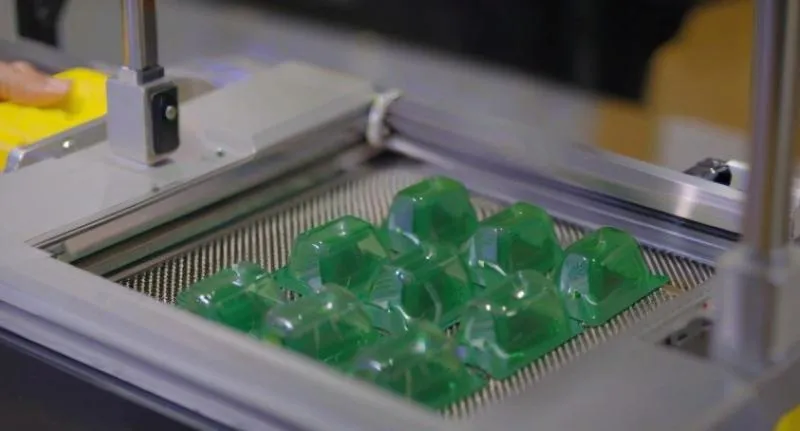
4. Formy drukowane 3D:
Produkowane przy użyciu odpornych na ciepło polimerów lub żywic za pomocą druku 3D.
- Zastosowania: Szybkie prototypowanie lub niestandardowe części o małej objętości.
- Zalety: Szybka produkcja i elastyczność projektowania.
- Wady: Ograniczona trwałość i odporność na ciepło.
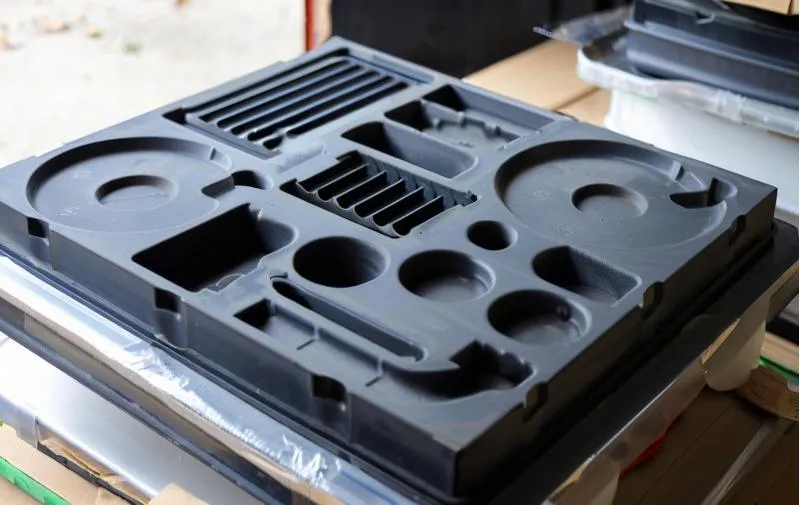
5. Formy wielokomorowe:
Wiele wgłębień umożliwia jednoczesne formowanie kilku części z jednego arkusza.
- Zastosowanie: Produkcja wielkoseryjna zapewniająca wydajność.
- Zalety: Zwiększa wydajność i obniża koszty jednostkowe.
- Wady: Złożony i kosztowny projekt.
najczęściej zadawane pytania dla klientów
Pierwsze kroki z Uplastech
Masz pytania? Mamy odpowiedzi.
Specjalizujemy się w wytłaczaniu, formowaniu próżniowym, rozdmuchiwaniu i precyzyjnym wytwarzaniu form, oferując niestandardowe rozwiązania spełniające różnorodne potrzeby produkcyjne.
Współpracujemy z różnymi branżami, w tym motoryzacyjną, elektroniczną, dóbr konsumpcyjnych i opakowań, koncentrując się na partnerstwie B2B i dostarczaniu rozwiązań w zakresie wytłaczania, termoformowania, rozdmuchiwania i precyzyjnego formowania.
Tak, dostosowujemy nasze rozwiązania do Twoich unikalnych wymagań.
Skontaktuj się
Napisz do nas lub wypełnij poniższy formularz, aby uzyskać wycenę.
E-mail: uplastech@gmail.com