Dikke wand vacuümvormen
Precisie-dieptrekken voor zware toepassingen. Ontdek de deskundige diensten op het gebied van dikwandig vacuümvormen voor industriële, auto- en ruimtevaarttoepassingen.
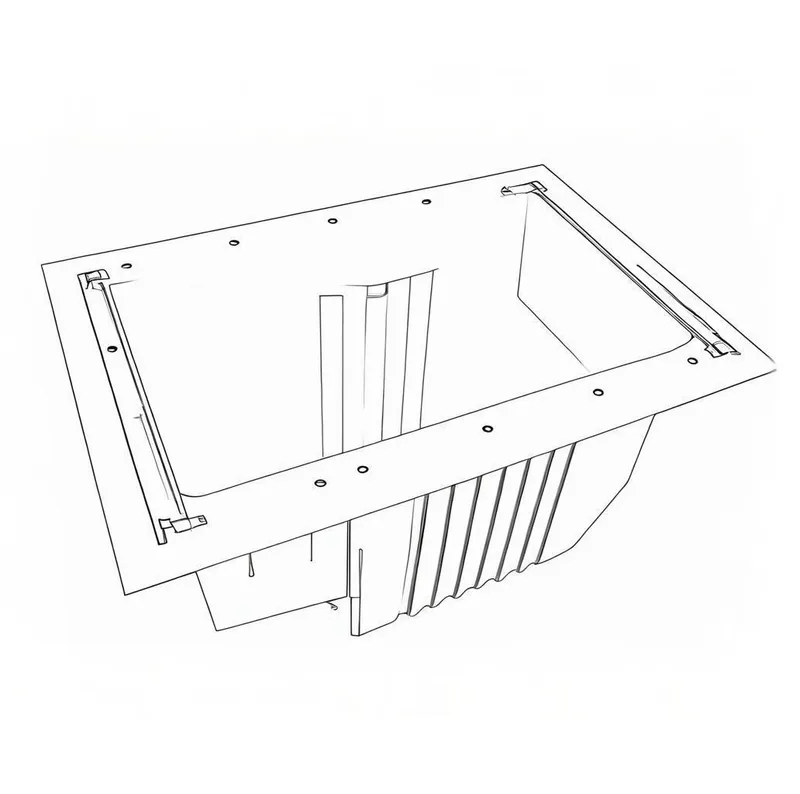
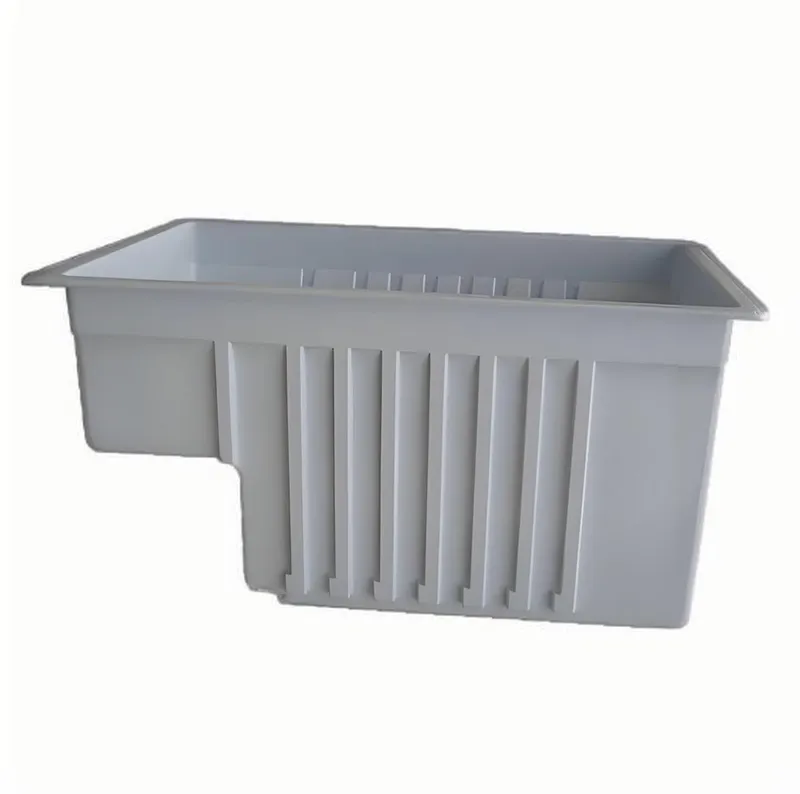
Gids voor vacuümvormen van dikke wanden (heavy gauge) op maat
Wat is dikwandig vacuümvormen?
Dikwandig vacuümvormen (ook bekend als thermovormen met hoge diktemaat of dikwandig vacuümvormen) is een gespecialiseerd kunststof productieproces dat ontworpen is om dikke kunststofplaten (meestal ≥2 mm) te vormen tot duurzame onderdelen met een hoge sterkte. Het proces omvat:
- Verwarming: Kunststofplaten (ABS, PC, PP, enz.) worden zacht gemaakt met infrarood of keramische verwarmingselementen tot ze buigzaam zijn (bv. 160-180°C voor ABS).
- Vormen: Het verwarmde vel wordt over een mal gedrapeerd en vacuümdruk (tot 25-28 inHg) trekt het strak tegen het oppervlak van de mal om ingewikkelde geometrieën na te bootsen.
- Koelen en trimmen: Snelle koeling (via lucht of waternevel) stolt de vorm, gevolgd door CNC-bewerking voor precisieranden.
Deze methode is ideaal voor grote, structurele onderdelen die robuustheid vereisen, zoals autopanelen, industriële behuizingen of 3D-bewegwijzering.
Procesvariaties:
Drukvormen: Combineert vacuüm en perslucht (3-6 bar) voor scherpere details op dikke platen.
Twin-Sheet Forming: Lijmt twee voorgevormde platen voor holle structuren (bijv. industriële pallets).
Drape Forming: Zakken van verwarmde platen over mannelijke mallen met behulp van zwaartekracht voor een uniforme dikte.
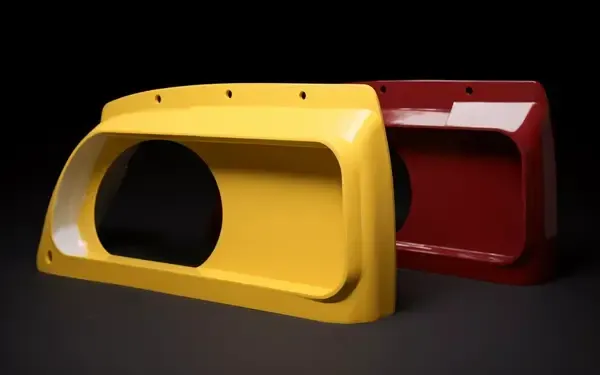
Gids voor materiaalselectie: ABS, PC, HDPE & verder
Door technische specificaties van industriële normen en praktische toepassingen te combineren, volgt hier een uitgebreide analyse van de materiaalselectie voor dikwandig vacuümvormen:
1. ABS (Acrylonitril Butadieen Styreen):
Toepassingen:
- Auto-onderdelen (dashboards, gereedschapskisten).
- Elektronicabehuizingen (behuizingen voor industriële apparatuur).
- Omhulsels van medische hulpmiddelen.
Belangrijkste voordelen:
- Hoge slagvastheid (ideaal voor structurele onderdelen).
- Uitstekende dimensionale stabiliteit tijdens het vormen van dikke profielen (diktebereik 1-20 mm).
- Eenvoudige nabewerking (verven, galvaniseren).
③ Procesoverwegingen:
- Moet 180-220°C verwarmd worden voor optimaal vacuümvormen.
- Compatibel met gestructureerde oppervlakken (zoals lederen nerfpatronen voor auto-interieurs).
④ Praktijkvoorbeeld:
- Brandvertragende ABS vacuümgevormde machinekappen (UL94 V-0 gecertificeerd).
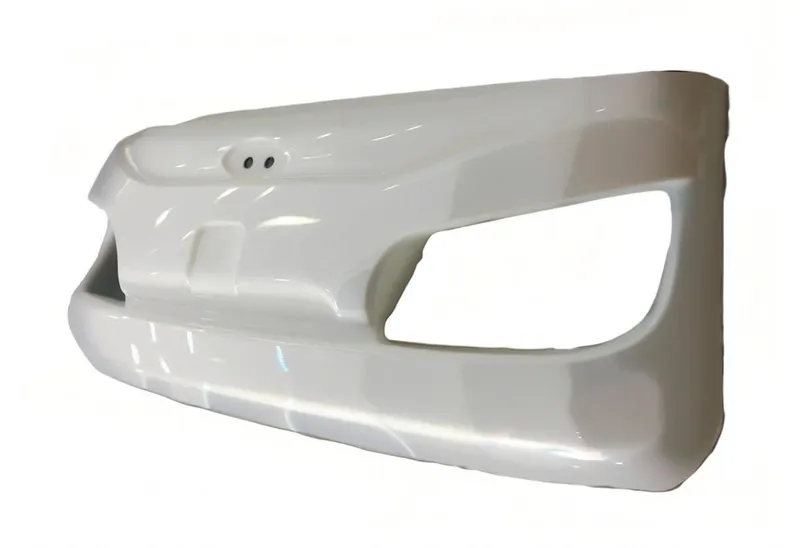
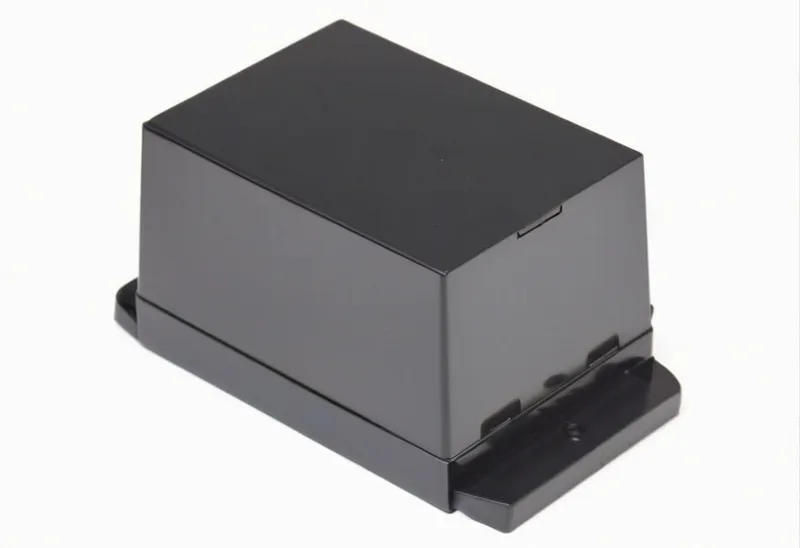
2. PC (polycarbonaat):
Toepassingen:
- Transparante beschermkappen (medische apparatuur, machineafschermingen).
- Interieuronderdelen voor de ruimtevaart.
Belangrijkste voordelen:
- Glasachtige helderheid (lichttransmissie >88%).
- Hittebestendigheid tot 135°C.
③ Procesoverwegingen:
- Strikte temperatuurregeling vereist (smal vormvenster: 190-210°C).
- Voordrogen essentieel (vochtgehalte <0,02%).
④ Praktijkvoorbeeld:
- UV-bestendige PC vliegtuigcabine panelen (3-6mm dik).
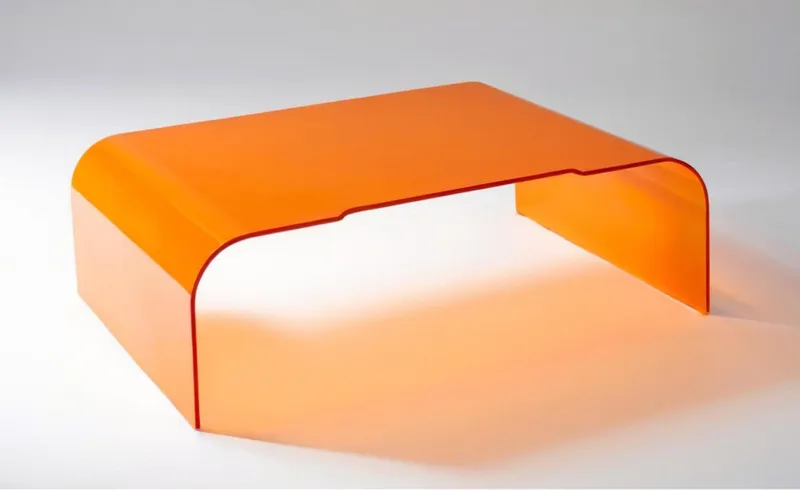
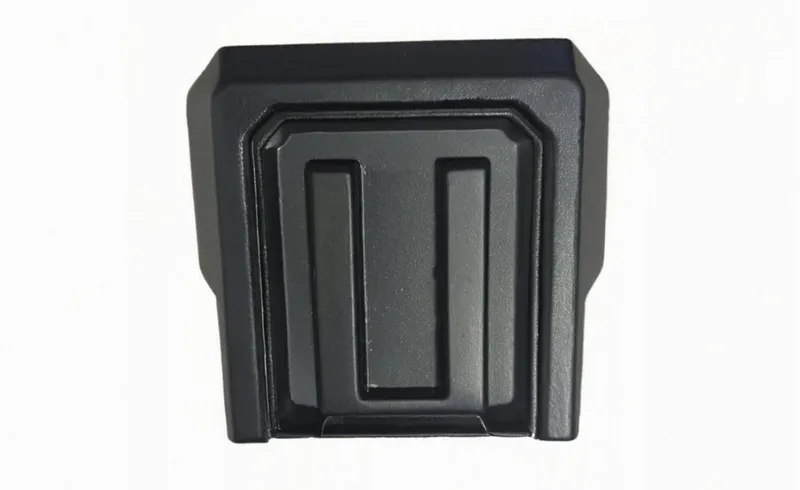
3. HDPE (polyethyleen met hoge dichtheid):
Toepassingen:
- Chemicaliënbestendige containers (industriële opslagtanks).
- Pallets en material-handlingsystemen voor zwaar gebruik.
Belangrijkste voordelen:
- Superieure weerstand tegen spanningsscheuren (meer dan 500 uur in ASTM D1693-tests).
- Rendabel voor productie op grote schaal (30-50% lagere materiaalkosten in vergelijking met ABS).
③ Procesoverwegingen:
- Optimale vormdikte: 4-12 mm.
- Vereist speciale koeling om kromtrekken te voorkomen.
④ Praktijkvoorbeeld:
- Antistatische HDPE-bakken voor de productie van elektronica.
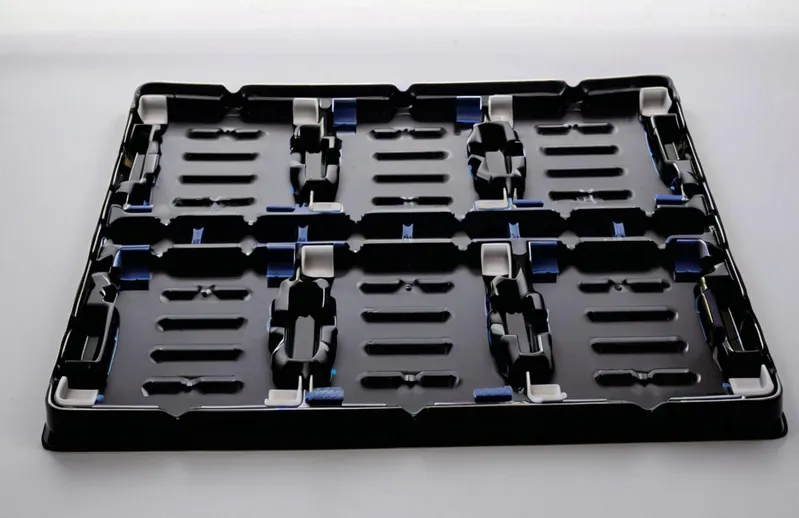
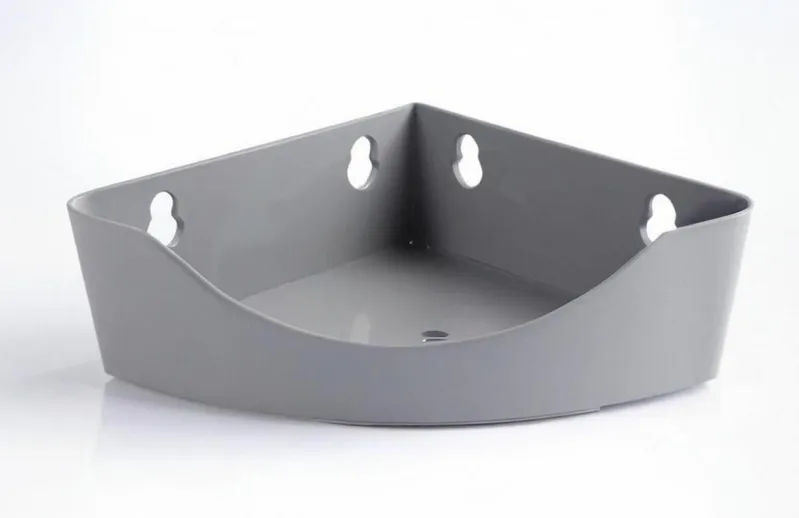
4. PETG (met glycol gemodificeerd PET):
Toepassingen:
- Voedselveilige verpakking (FDA-conforme containers).
- Displaysystemen voor de detailhandel.
Belangrijkste voordelen:
- Combineert de vervormbaarheid van PVC met de chemische weerstand van PET.
- Lage vervormingstemperatuur (110-130°C).
③ Praktijkvoorbeeld:
- Transparante PETG medische instrumentenschalen (γ-straalsteriliseerbaar).
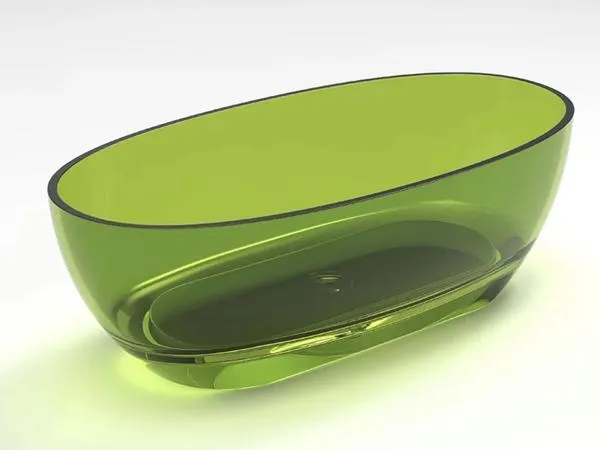
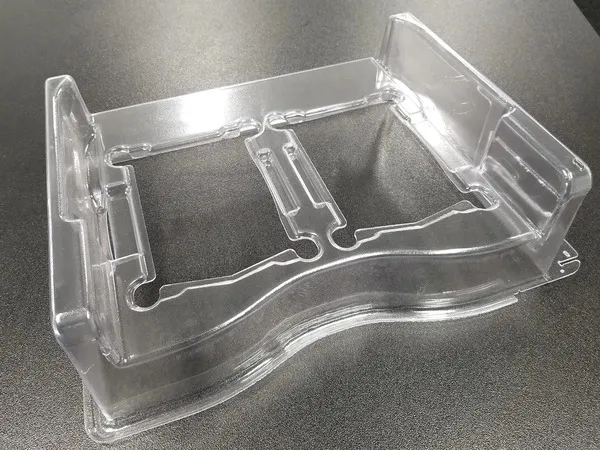
5. PP (polypropyleen):
Toepassingen:
- Voedselverpakking (yoghurtbekers, magnetronbestendige bakjes).
- Medische wegwerpproducten (spuiten, infuusflessen, sterilisatietrays).
- Industriële containers (chemische opslagbakken, landbouwtanks).
Belangrijkste voordelen:
- Lichtgewicht en weerstand tegen vermoeidheid: Ideaal voor dunwandige ontwerpen met herhaald buigen (bijv. levende scharnieren op flessendoppen).
- Chemische inertie: Bestand tegen zuren, alkaliën en organische oplosmiddelen.
- Autoclaveerbaar: Bestand tegen stoomsterilisatie (121°C+) voor medische toepassingen.
- Kosteneffectief: Lage grondstofkosten en hoge recyclebaarheid.
③ Dikke-muur-uitdagingen:
- Gevoelig voor krimpen en kromtrekken in zware profielen (>3 mm).
- Geregelde matrijstemperatuur (40-80°C) vereist om de maatvastheid te verbeteren.
④ Praktijkvoorbeeld:
- Medische trays voor eenmalig gebruik: Met gammastralen steriliseerbare, FDA-conforme ontwerpen met geïntegreerde kliksluitingen.
- Industriële IBC-voeringen: 8-12 mm dikke PP containers voor corrosief vloeistoftransport.
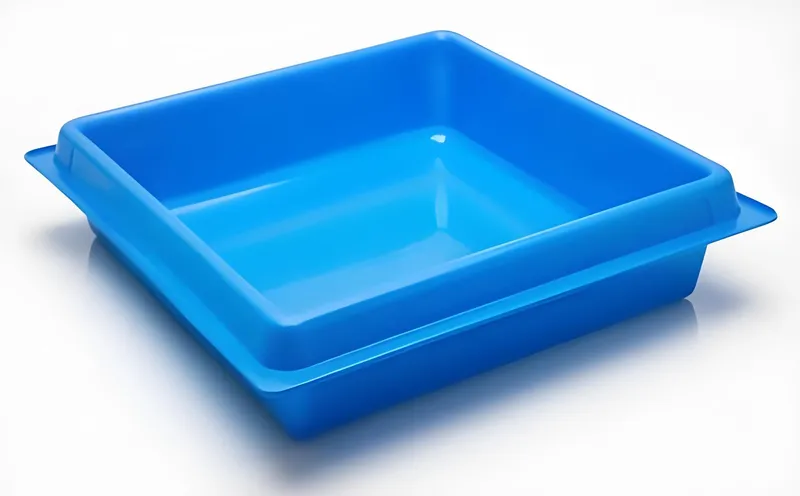
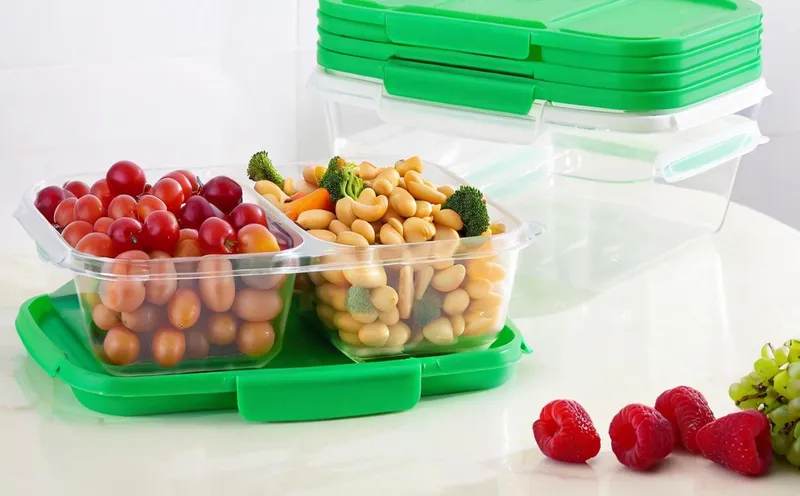
Materiaal | Toepassingen | Essentiële eigenschappen | Geschikt voor dikwandig thermovormen | Voorbeeldgebruiksgevallen |
---|---|---|---|---|
ABS | Auto-onderdelen, elektronica | Hoge sterkte, slagvast | (Complexe vormen) | Gereedschapskist schelpen |
PC | Transparante afdekkingen, medische hulpmiddelen | Hoge transparantie, hittebestendigheid | (Vereist nauwkeurige temperatuurregeling) | Machinebescherming |
HDPE | Industriële containers, pallets | Chemische weerstand, recycleerbaarheid | (Uniforme wanddikte) | Antistatische trays |
PETG | Voedselverpakking, displays | FDA-goedgekeurd, hoge taaiheid | (Precisiegieten) | Transparante voedselcontainers |
PP | Dunwandige artikelen, medische trays | Lichtgewicht, weerstand tegen vermoeidheid | (gevoelig voor krimp in dikke muren) | Farmaceutische trays |
Belangrijkste processtappen: Van kunststof plaat tot eindproduct
Belangrijkste processtappen en technische punten van dikwandig vacuümvormen (dikwandig thermovormen/zwaarspannend vacuümvormen).
1. Materiaalkeuze en voorbehandeling:
① Selectie van plaatmateriaal:
- Gangbare materialen: ABS (met een dikte van 4 mm of meer en een hoogglanzend oppervlak), HDPE (uitstekende slijtvastheid, geschikt voor omzetpallets), PVDF (bestand tegen hoge temperaturen en chemische corrosie, geschikt voor industriële scenario's).
- Materiaal voorbehandeling: Schone en droge dikke platen (4 - 6 mm) om te voorkomen dat onzuiverheden de vormkwaliteit beïnvloeden.
Verwarmen en verzachten:
- Temperatuurregeling: Stel het verwarmingsbereik in volgens de materiaaleigenschappen (ABS heeft bijvoorbeeld 200 - 220°C nodig en HDPE 150 - 170°C) voor een gelijkmatige verweking.
- Verwarmingsmethode: Gebruik infrarood- of kwartsverwarmers om plaatselijke oververhitting te voorkomen die plaatvervorming kan veroorzaken.
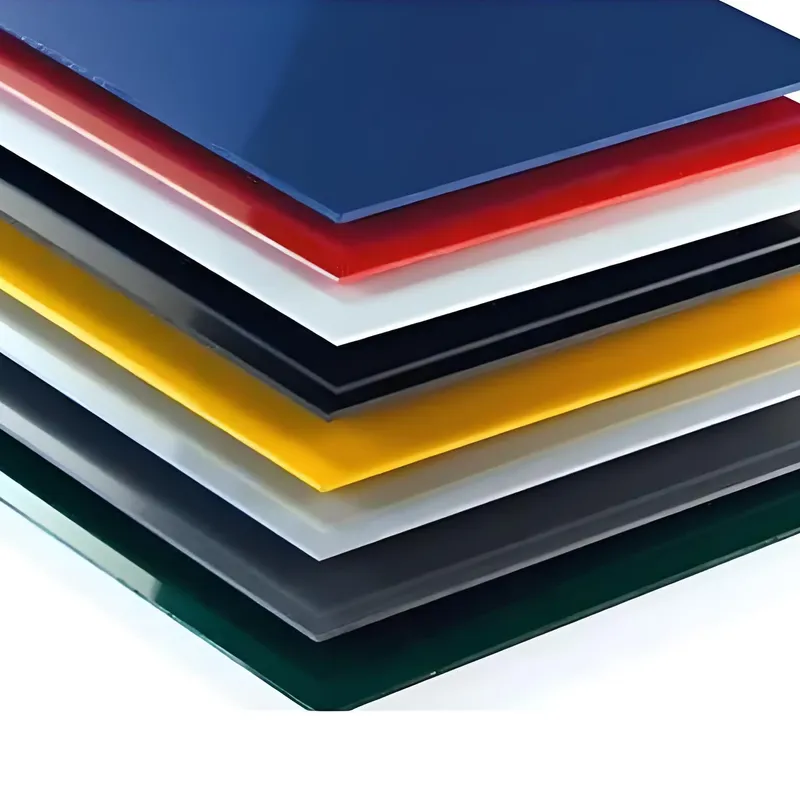
2. Vormontwerp en vormproces:
Vormtypeselectie:
- Enkelzijdige mallen (mannelijke/vrouwelijke mallen): Mannelijke mallen zijn geschikt voor producten met diepe holtes, terwijl vrouwelijke mallen de oppervlaktefijnheid kunnen verbeteren.
- Speciale mallen: Voor transparante producten worden massieve aluminium mallen (met een hoge oppervlakteafwerking) aanbevolen en voor producten met een complexe structuur zijn extra plunjers nodig.
Vacuüm- en drukvormen:
- Vacuümabsorptie: Gebruik negatieve druk om het zacht geworden vel tegen de vormcontour te drukken. De vacuümgraad moet nauwkeurig worden geregeld (referentiewaarde: ≥0,08MPa).
- Hulpluchtdruk: Gebruik perslucht (druk van 0,3 - 0,6MPa) om het materiaal sneller uit te rekken en luchtbellen te verminderen.
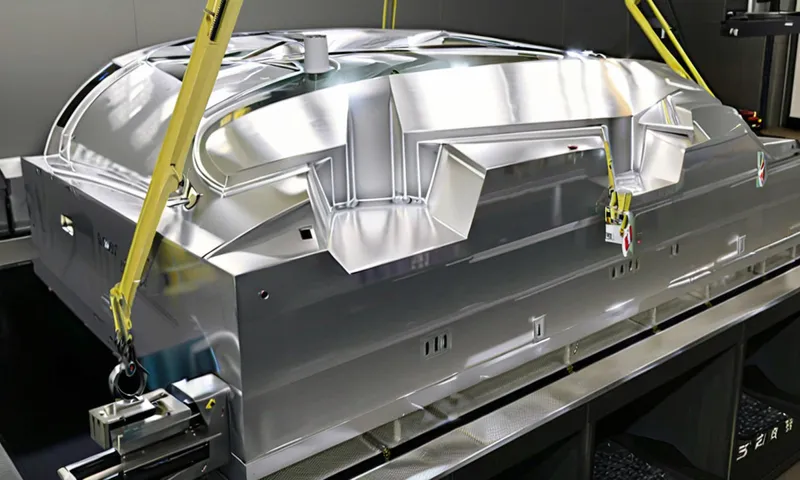

3. Optimalisatie van koelen en ontvouwen:
Koelen en vormen:
- Koelmethode: Gebruik lucht- of waterkoelsystemen om de koelsnelheid te regelen en spanningsscheuren te voorkomen.
- Temperatuurgradiëntbeheer: Koel de kant die in contact komt met de matrijs het eerst om ongelijkmatige krimp van onderdelen met een dikke wand te verminderen.
Ontvouwbehandeling:
- Ontwerp met conische vorm: Een conus van ≥0,5° voor gladde oppervlakken en ≥1,5° voor ruwe oppervlakken zorgt voor soepel ontvouwen.
- Geautomatiseerd ontvouwen: Volautomatische dieptrekmachines voor dikke platen zijn uitgerust met ontvormmechanismen om handmatige interventie te verminderen.
4. Nabewerking en kwaliteitscontrole:
① Bijwerken en secundaire verwerking:
- Snijden van randen: Gebruik CNC- of lasersnijders om overtollige bramen te verwijderen.
- Functionele verwerking: Gaten boren, polijsten of oppervlaktecoatings aanbrengen (bijv. PVDF-fluorkoolstofcoatings om de weerbestendigheid te verbeteren).
Kwaliteitsinspectie:
- Wanddikte inspecteren: Gebruik een ultrasone diktemeter om de uniformiteit te controleren (richtfout <5%).
- Sterkte testen: Simuleren de werkelijke belastingsomgeving om de schokbestendigheid en slijtvastheid te controleren.
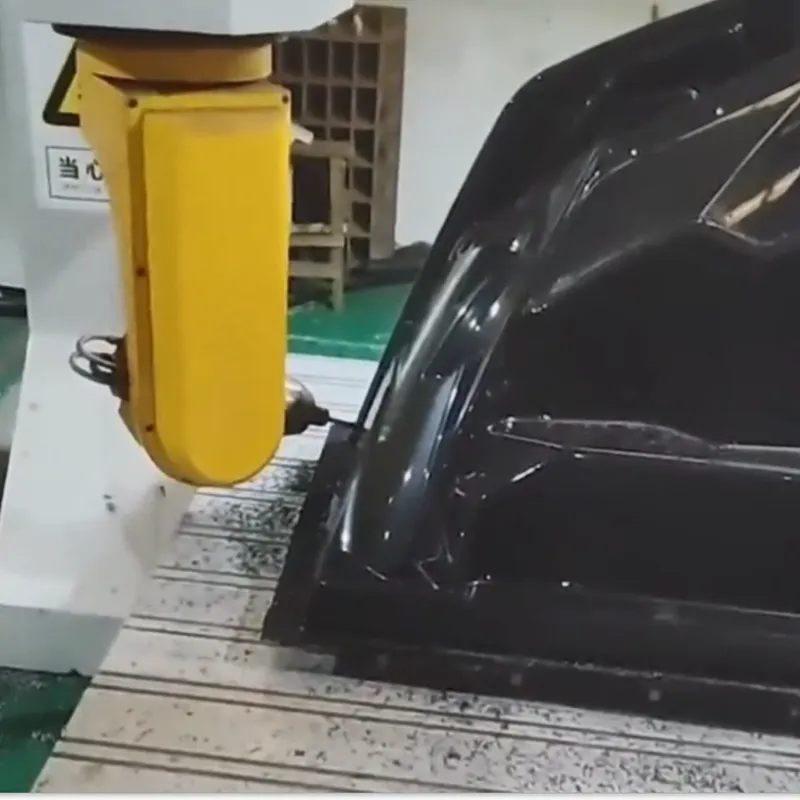
Toepassingen in verschillende bedrijfstakken: Auto's, medisch & meer
Dikwandig vacuümvormen (ook bekend als thermovormen van zware profielen, thermovormen van dikke profielen of thermovormen van dikke platen) is een veelzijdig productieproces dat veel wordt gebruikt in industrieën die duurzame, complex gevormde onderdelen nodig hebben. Hieronder vindt u de belangrijkste toepassingen in de belangrijkste sectoren:
1. Auto-industrie:
Dikwandig vacuümvormen is essentieel voor het lichtgewicht en functioneel ontwerp van auto's:
- Interieuronderdelen: Dashboardpanelen, deurbekledingen en middenconsoles van ABS- of PP-platen met hoge sterkte en aanpasbare texturen.
- Exterieurdelen: Bumpers, spatborden en aerodynamische carrosseriepanelen met slagvaste materialen zoals HDPE of ABS+TPU mengsels.
- Verlichtingssystemen: Behuizingen voor koplampen en achterlichten met precieze optische helderheid, vaak gemaakt van PMMA of PC.
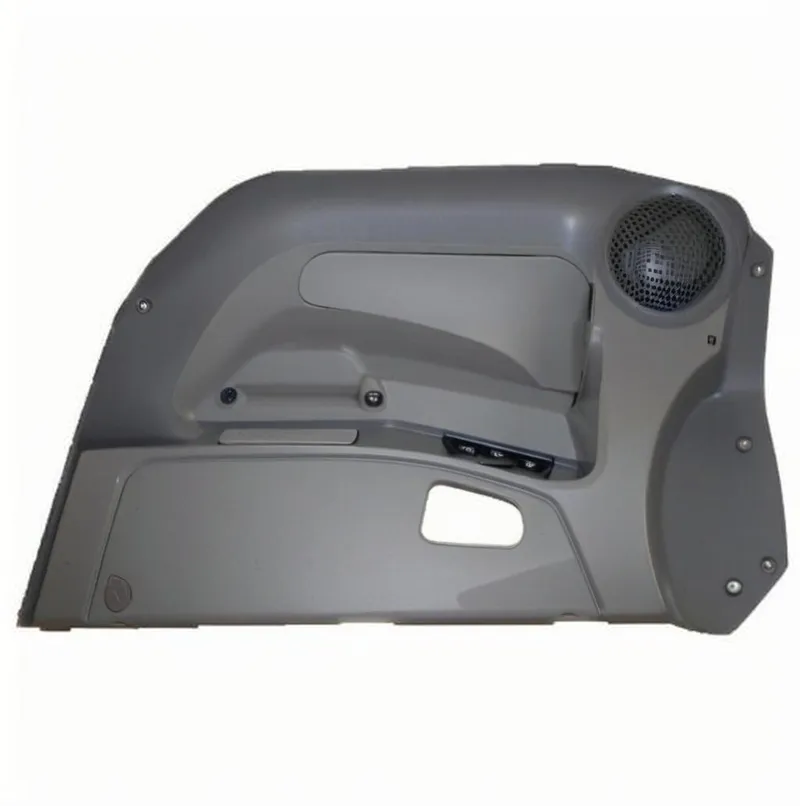
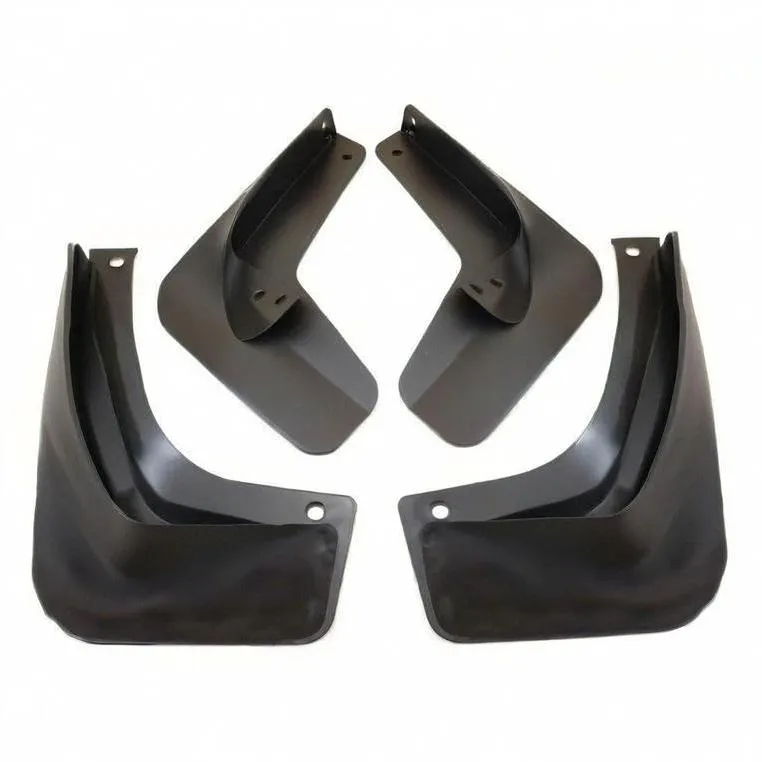
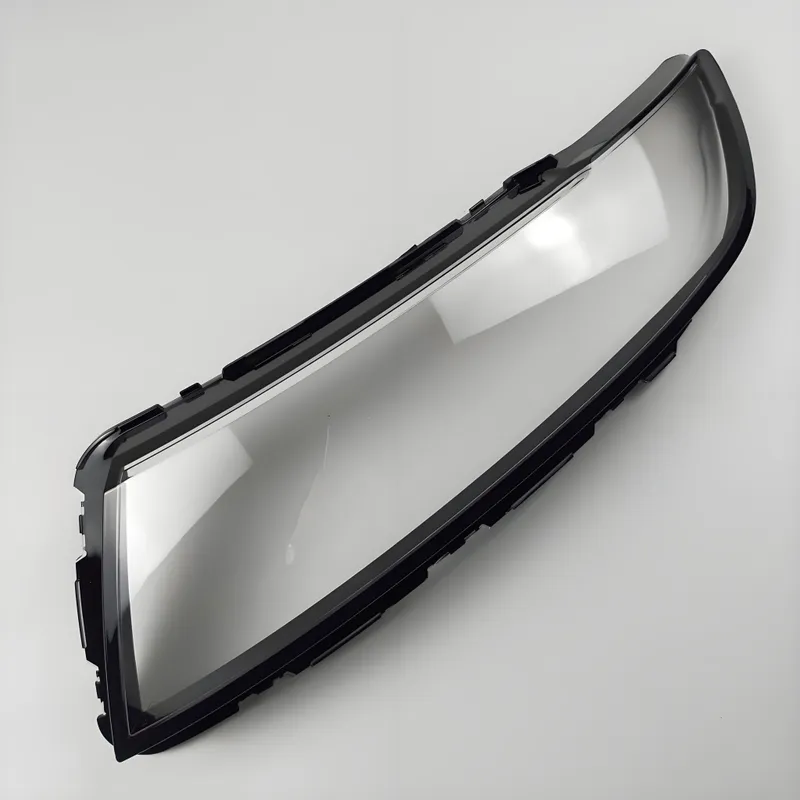
2. Medische industrie:
Bij medische toepassingen staan hygiëne, duurzaamheid en precisie voorop:
- Apparatuurbehuizingen: MRI-machineafdekkingen, behuizingen voor chirurgische instrumenten en behuizingen voor ventilatoren met steriliseerbare materialen zoals PETG of ABS van medische kwaliteit.
- Dienbladen: Onderdelen voor röntgenapparaten en trays voor laboratoriumapparatuur met antistatische eigenschappen.
- Aangepaste verpakking: Herbruikbare verpakking voor chirurgisch gereedschap (dikte 3-5 mm) voor ethyleenoxide sterilisatie

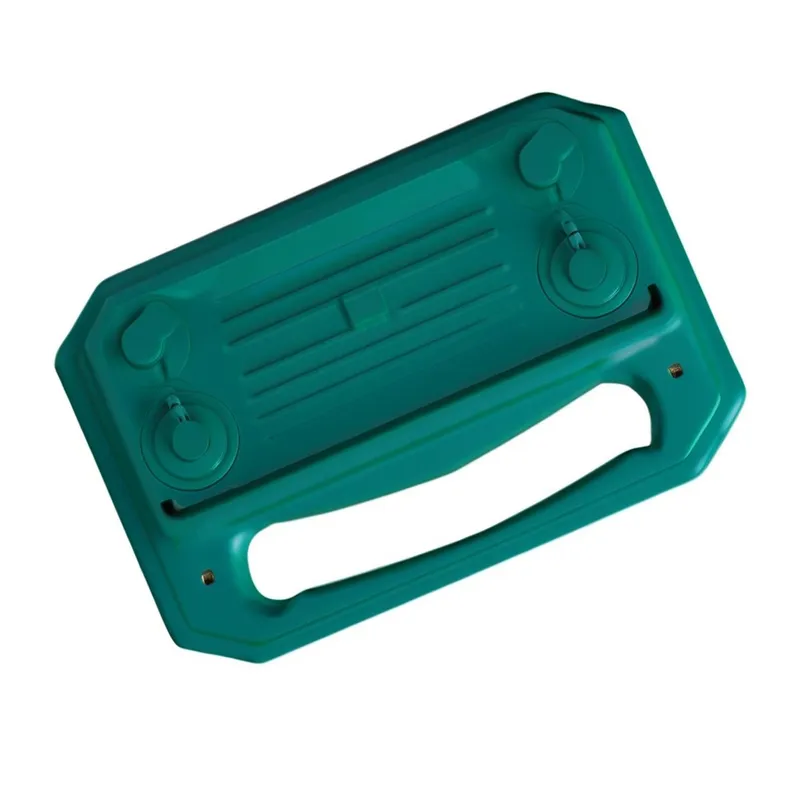
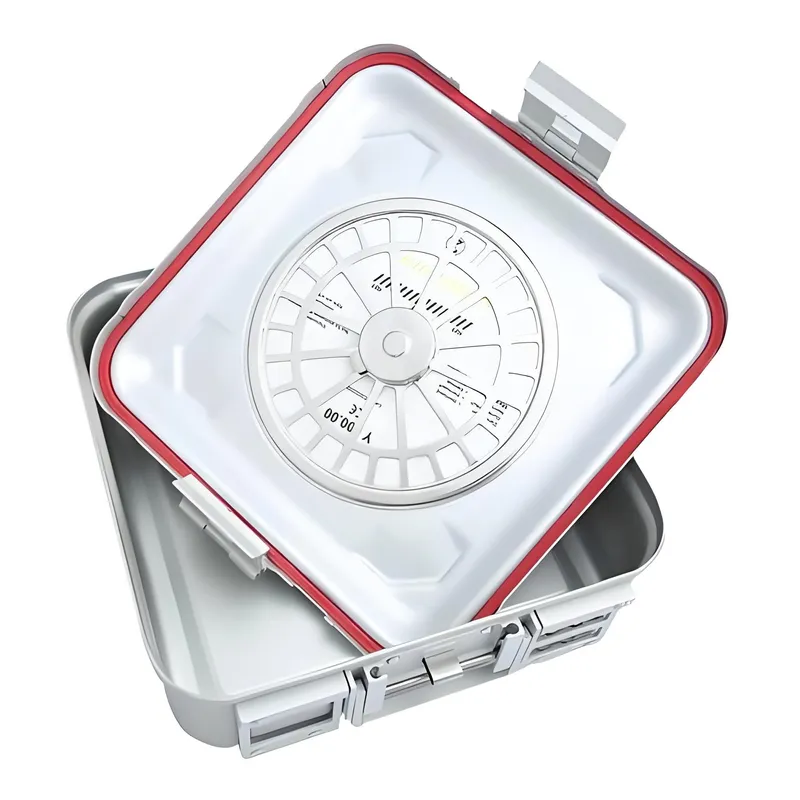
3. Consumentenelektronica en -apparaten:
- Huishoudelijke apparaten: Koelkastvoeringen, wasmachinedeksels en vaatwasseronderdelen die PP of HDPE gebruiken voor chemische weerstand.
- Elektronicabehuizingen: TV-achterpanelen, computerbehuizingen en bedieningspanelen met vlamvertragende ABS of PC.
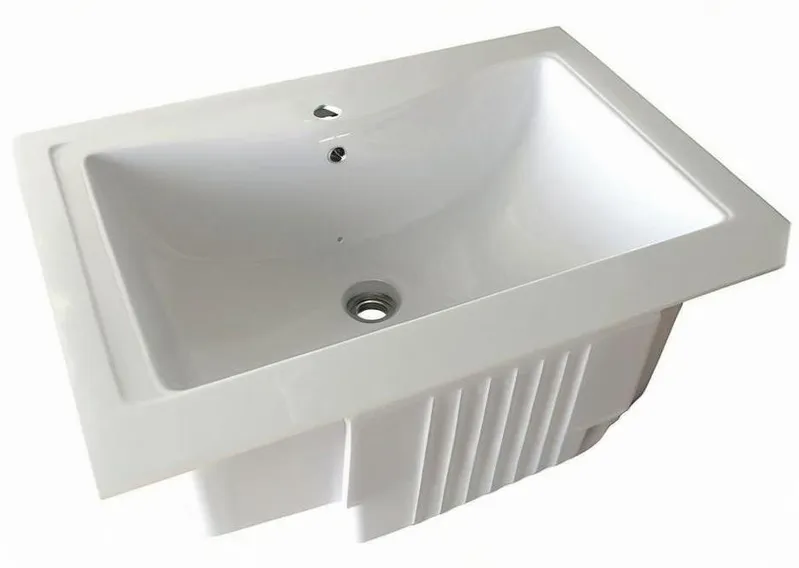
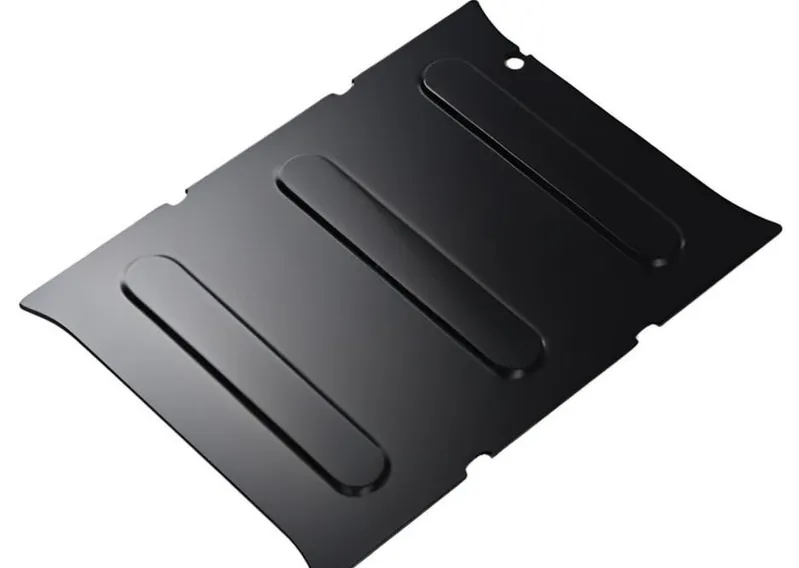
4. Ruimtevaart en transport:
- Vliegtuiginterieurs: Bovenkastjes, rugleuningpanelen en binnenbekleding van lichtgewicht, vlamvertragend composietmateriaal.
- Spoorwegonderdelen: Train stoelonderstellen en interieurbekleding met gebruik van zeer sterke, lichtgewicht materialen.
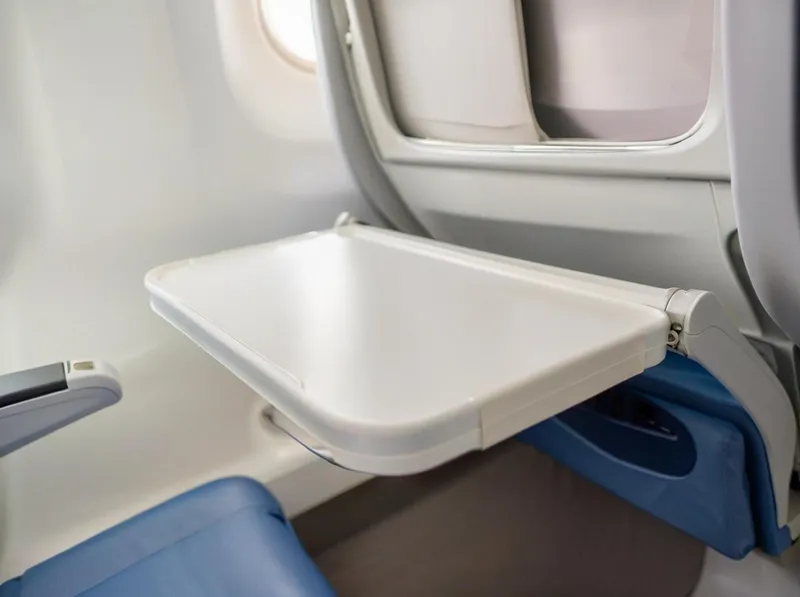
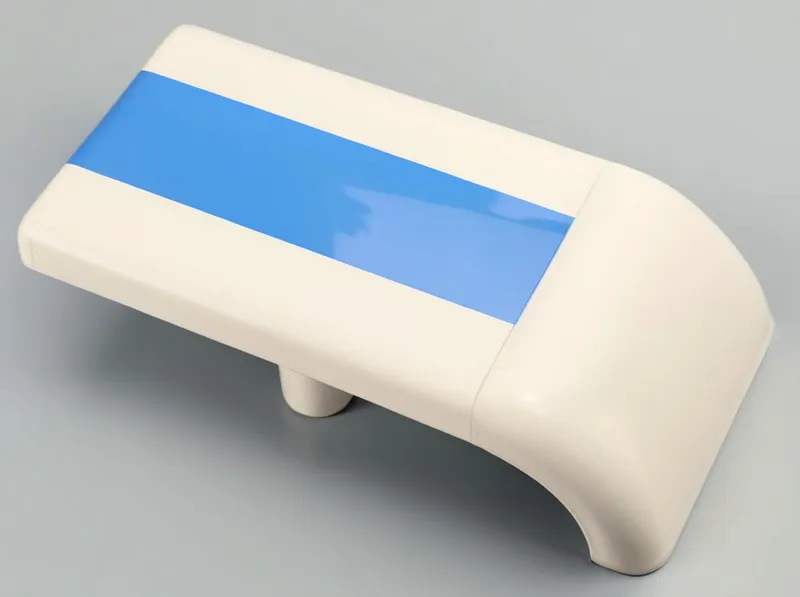
5. Industriële & verpakkingsoplossingen:
- Gereedschap op maat: Heavy-duty trays en beschermhoezen voor machineonderdelen.
- Displays in de detailhandel: Duurzame bewegwijzering, productstandaards en verkooppuntunits met gestructureerde oppervlakken voor branding.
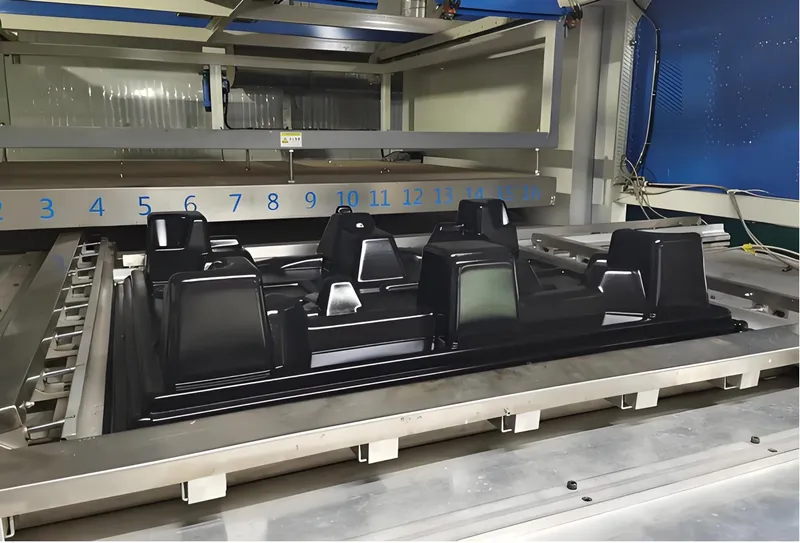
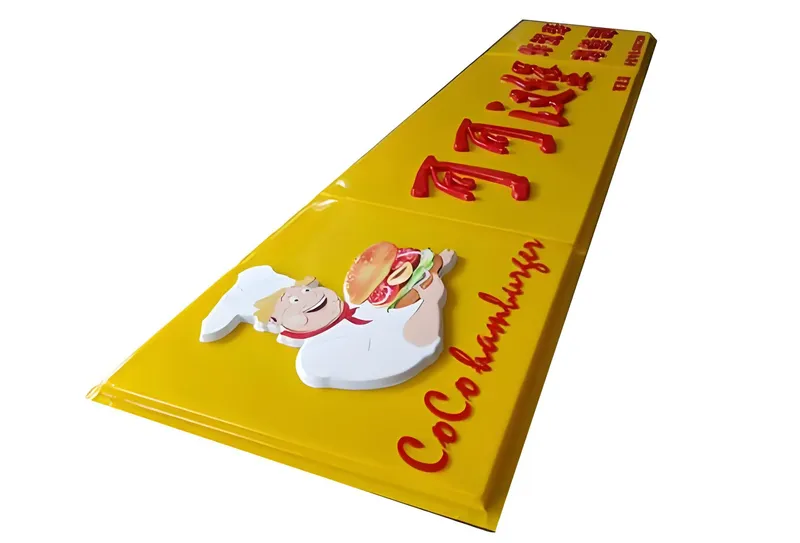
Voordelen ten opzichte van spuitgieten
Hieronder volgen de vijf belangrijkste voordelen van dikwandig vacuümvormen ten opzichte van spuitgieten, geanalyseerd in combinatie met technische kenmerken en industriële toepassingen:
1. Matrijskosten en productieflexibiliteit:
De mallen voor dikwandig vacuümvormen zijn meestal gemaakt van aluminium of composietmaterialen. Ze hebben een eenvoudige structuur en lage productiekosten (ongeveer 10% - 30% van spuitgietmatrijzen). Deze eigenschap maakt het voordeliger voor kleine batchproductie of prototypeontwikkeling. Voor spuitgieten zijn daarentegen stalen precisiematrijzen nodig, die geschikt zijn voor de productie van grote batches, maar hoge initiële investeringen vereisen.
2. Materiaalgebruik en afvalbeheersing:
Bij vacuümvormen wordt een kunststofplaat met één laag verwarmd en in vorm geadsorbeerd. De resten kunnen worden gerecycled, waardoor er minder materiaal wordt verspild. Bij spuitgieten moet gesmolten kunststof de volledige vormholte vullen. Voor dikwandige onderdelen kan ongelijkmatige krimp leiden tot overtollig materiaal en is het moeilijker om het afval te recycleren.
3. Uniformiteit van de structuur van dikke wanden en spanningscontrole:
Vacuümvormen kan de inwendige spanning verminderen door gelijkmatig rekken en koelen in dikwandige onderdelen, waardoor veelvoorkomende problemen bij spuitgieten zoals deuken en kromtrekken vermeden worden. Voor interieuronderdelen voor auto's met een wanddikte van meer dan 5 mm bijvoorbeeld, kan vacuümvormen de vlakheid van het oppervlak behouden, terwijl spuitgieten interne holtes kan veroorzaken door onvoldoende verpakkingsdruk.
4. Aanpassingsvermogen aan grootschalige en complexe geometrische structuren:
Vacuümvormen blinkt uit in het produceren van grote dikwandige onderdelen (zoals behuizingen voor luchtvaartapparatuur of trays voor medische apparatuur). De grootte van een enkel onderdeel kan enkele meters bereiken en het heeft een sterk aanpassingsvermogen aan complexe gebogen oppervlakken. Spuitgieten wordt beperkt door het openen en sluiten van de matrijs en de capaciteit van de spuitgietmachine, waardoor het moeilijk is om extra grote of ultradikke onderdelen te maken.
5. Milieubescherming en energie:
Het vacuümvormproces heeft een lager energieverbruik en vereist geen injectiesysteem onder hoge druk, wat in overeenstemming is met de trend van groene productie. Daarentegen verbruiken de smelt- en hogedrukprocessen bij spuitgieten meer energie. Dikwandige producten vereisen een langere koelcyclus, waardoor het energieverbruik verder toeneemt.
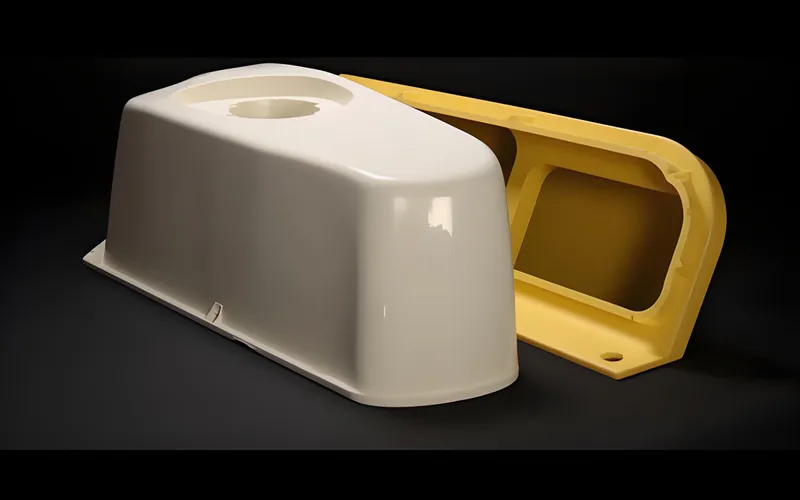
Uitdagingen in vacuümvormen van dikke wanden
Dikwandig vacuümvormen brengt unieke uitdagingen met zich mee in vergelijking met standaard thermovormprocessen. Factoren zoals materiaalstroom, temperatuurregeling, complexiteit van de tooling en cyclustijd hebben een aanzienlijke invloed op de kwaliteit en efficiëntie. Het beheersen van restspanningen, oppervlaktedefecten en materiaalbeperkingen is van cruciaal belang om hoogwaardige, vormstabiele onderdelen te maken.
1. Materiaalstroom en uniformiteit:
Vacuümvormen van dikke wanden vereist een nauwkeurige controle over de materiaalstroom om ongelijkmatige wanddikte te voorkomen. Thermovormen van zware wanden heeft vaak moeite met onvolledig uitrekken door de beperkte beweeglijkheid van polymeren, wat leidt tot zwakke plekken of spanningsconcentraties in eindproducten.
2. Temperatuurregeling:
Thermovormen van dikke platen vereist een strikt thermisch beheer. Overmatige warmte kan polymeerketens aantasten, terwijl onvoldoende warmte broosheid veroorzaakt. Het in evenwicht houden van temperatuurgradiënten over dikke secties (bijv. ≥6 mm) is essentieel om kromtrekken of delaminatie te voorkomen.
3. Gereedschaps- en matrijscomplexiteit:
Complexe geometrieën in dikwandig vacuümvormen vereisen zeer nauwkeurige matrijzen met geavanceerde koelsystemen. Matrijzen met zware afmetingen moeten bestand zijn tegen langdurige blootstelling aan hitte en hoge klemkrachten, waardoor de ontwerp- en onderhoudskosten toenemen.
4. Cyclustijd en energie-efficiëntie:
Het verwerken van dikke materialen (bijv. ABS, HDPE) gaat gepaard met lange opwarm-/koelcycli, waardoor het energieverbruik toeneemt. Het optimaliseren van de cyclustijden zonder de structurele integriteit in gevaar te brengen, blijft een belangrijke uitdaging.
5. Restspanning en dimensionale stabiliteit:
Diepgetrokken onderdelen met een dikke wand behouden vaak restspanning door ongelijkmatige afkoeling, wat leidt tot vervormingen na het gieten. Het beheersen van krimpsnelheden en het waarborgen van de maatnauwkeurigheid zijn essentieel voor functionele toepassingen.
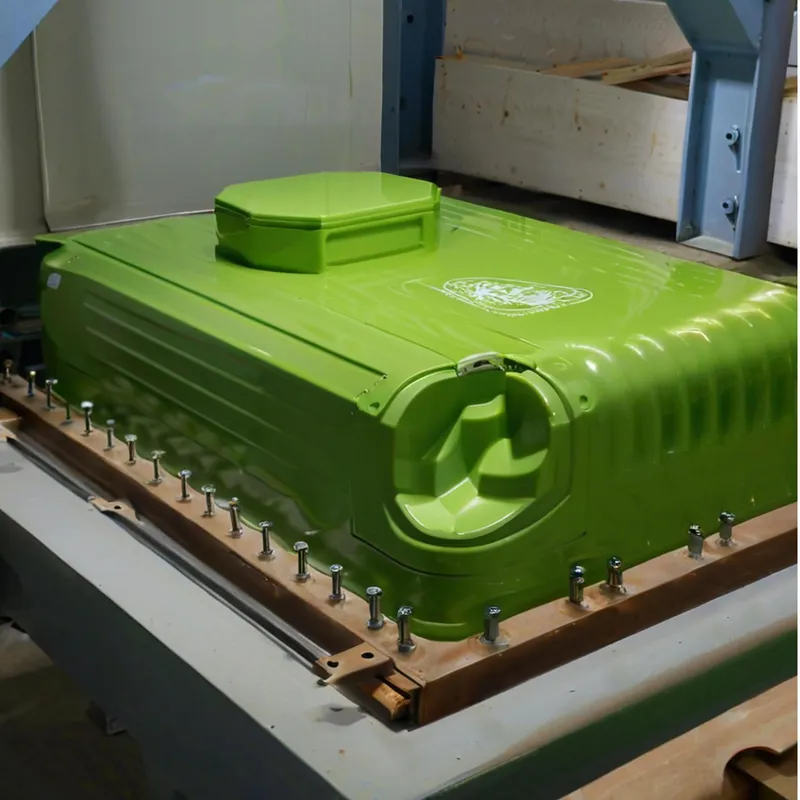
6. Oppervlaktegebreken:
Het thermovormen van zware profielen kan leiden tot imperfecties aan het oppervlak, zoals sinaasappelhuidtexturen of luchtinsluitingen, vooral bij diepgetrokken profielen. Het ontwerp van vacuümkanalen en technieken voor het voorrekken van materiaal zijn van vitaal belang om dit te beperken.
7. Beperkingen in materiaalselectie:
Niet alle polymeren zijn geschikt voor dikwandig vacuümvormen. Materialen met een hoge smeltsterkte (bv. vernet PE) genieten de voorkeur, maar de opties zijn beperkt in vergelijking met thermovormen met dunne wand, wat de ontwerpflexibiliteit beperkt.
Dikke wand vacuümvormen
Ontdek duurzame, zeer nauwkeurige thermovormoplossingen met ondersteuning voor aangepaste ontwerpen en veelzijdige materialen. Vraag vandaag nog een offerte aan!
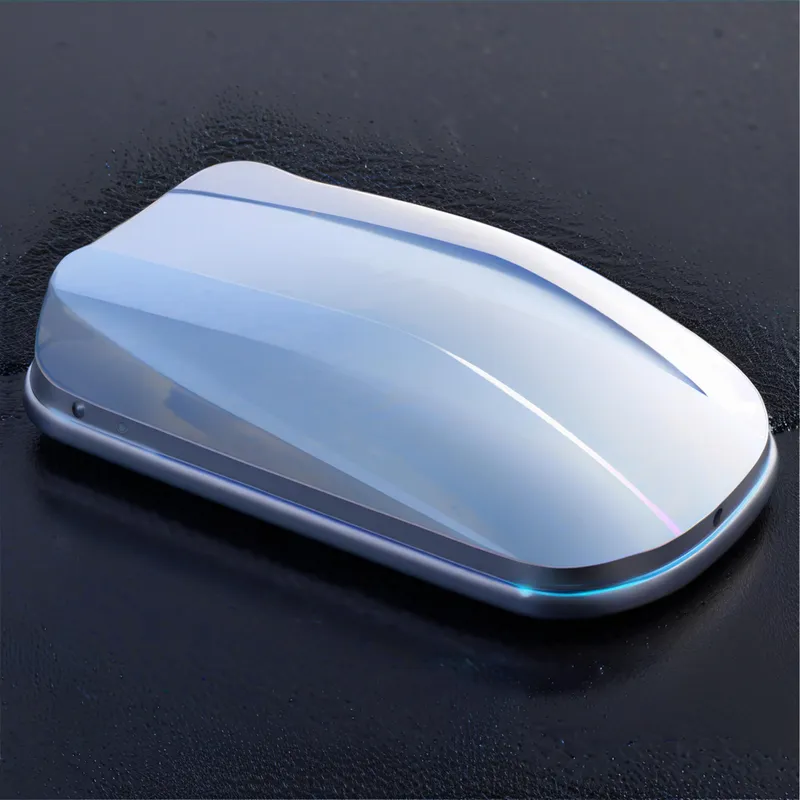
Gids voor vacuümvormen van dikke wanden (heavy gauge) op maat
Ontwerpoverwegingen voor structurele integriteit
Hier volgen de belangrijkste ontwerpoverwegingen voor structurele integriteit in thermovormprocessen met dikke wanden:
1. Materiaalkeuze en voorbehandeling:
① Hoogwaardige polymeren: Geef de voorkeur aan PVDF (bijv. Solvay PVDF 20808 serie), gemodificeerd ABS of PC voor thermische stabiliteit en UV-bestendigheid bij dikwandig vacuümvormen.
② Controle van de plaatuniformiteit: Handhaaf diktetolerantie ≤±5% door voordrogen (bijv. 105°C/4u) om door vocht veroorzaakte microvoids te elimineren bij thermovormen met zware dikte.
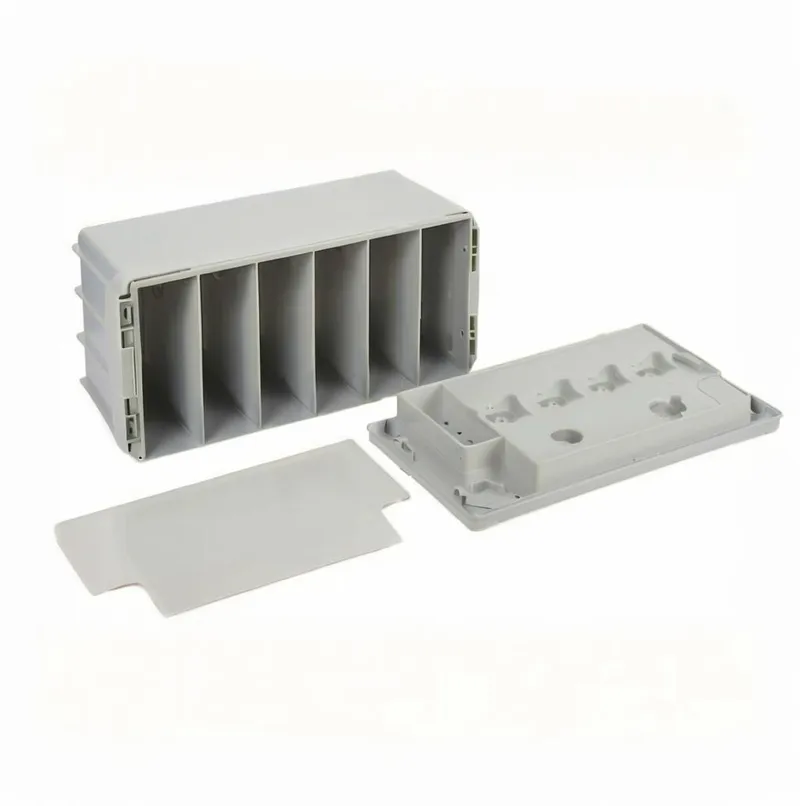
2. Ontwerp wanddiktegradiënt:
Overgangsoptimalisatie: Gebruik conische of gebogen overgangen (straal ≥3× wanddikte, R≥3T) om spanningsscheuren te voorkomen. Voorbeeld: Overgangshoek van 45° voor dashboards in auto's met dikteveranderingen van 8→4 mm.
② Minimumdiktestandaarden:
- Kleine onderdelen (≤200mm): ≥2mm
- Grote delen (≥400 mm): ≥3 mm + verstevigingsribben.
3. Matrijstechniek en procescompatibiliteit:
Vormtypeselectie:
- Vrouwelijke mallen: Ideaal voor ondiepe holtes (diepte ≤3× dikte), bijv. behuizingen voor medische apparatuur.
- Mannelijke mallen: Voor hoge inwendige dimensionale precisie (bijv. industriële containers), maar beperk bodemdunning tot <15%.
Ontwerphoeken: ≥3° (≥5° voor transparante delen); verhoog 0,5° per 0,1 mm textuurdiepte.
4. Thermische procesparameters:
Parameter | Dikwandig assortiment | Dunwandig bereik |
---|---|---|
Verwarmingstemperatuur | 210-290°C (zoneregeling) | 180-240°C |
Vacuümdruk | ≥95 kPa (meertraps) | ≥90 kPa |
Koeling | 2-4°C/s (nevelkoeling) | 5-8°C/s (luchtkoeling) |
Wachttijd | Dikte (mm) ×1.2-1.5s | Dikte (mm) ×0.8s |
5. Strategieën voor structurele versterking:
① Ribontwerp:
- Hoogte ≤5T, worteldikte 0,6-0,8T, top ≥0,4T
- Voorbeeld: 80 mm ribafstand voor kasten van 400 mm lang.
② Ontluchtingsgaten: Voeg Φ 3-30 mm niet-dragende gaten toe om de vacuümweerstand te verminderen en de assemblage uit te lijnen.
6. Stressmanagement:
Gefaseerde koeling:
- Snel afkoelen tot Tg+20°C (vormspanning elimineren)
- Langzaam afkoelen tot Tg-10°C (moleculaire oriëntatiestress loslaten)
- Geforceerde koeling tot omgevingstemperatuur.
Gloeien: 2-4 uur bij Tg-30°C voor onderdelen met een dikte >8 mm (bijv. technische kunststoffen).
Kwaliteitscontrole: Wanddikte & oppervlakteafwerking
Voor dikwandige thermovormproducten (ook wel heavy-gauge thermovormen of thick sheet thermoforming genoemd) is het van cruciaal belang om een consistente wanddikte en oppervlakteafwerking te behouden. Hieronder staan de belangrijkste strategieën voor kwaliteitscontrole in deze processen:
1. Wanddiktecontrole:
① Materiaal Voorverwarmingsuniformiteit: Zorg ervoor dat het thermoplastische blad gelijkmatig wordt verwarmd om te voorkomen dat het tijdens het vormen plaatselijk dunner of dikker wordt. Geavanceerde temperatuurbewakingssystemen kunnen voorverwarmingscycli optimaliseren.
Optimalisatie van matrijsontwerp: Gebruik precisie ontworpen mallen met instelbare luchtdruk en vacuüminstellingen om de materiaalverdeling te regelen. Simulaties (bijv. eindige elementenanalyse) helpen stromingspatronen voorspellen voor onderdelen met dikke wanden.
③ Real-Time Diktecontrole: Implementeer inline sensoren (bv. ultrasoon of laser) om de dikte te meten tijdens het vormen. Pas parameters dynamisch aan op basis van feedback.
Inspectie na vervorming: Gebruik QC-monsters om de dikteconsistentie van verschillende batches te controleren. Statistische procescontrole (SPC) kan afwijkingen in productietrends identificeren.
2. Borging van de oppervlakteafwerking:
Kwaliteit van het maloppervlak: Polijst matrijzen tot een hoogwaardige afwerking (bijv. SPI A1 standaard) om oppervlakte-onvolkomenheden op het eindproduct te minimaliseren.
Materiaalkeuze: Kies voor hoogzuivere harsen met een lage viscositeit om oppervlaktedefecten zoals sinaasappelschil of vloeilijnen, die vaak voorkomen bij dikwandig vacuümvormen, te verminderen.
Gecontroleerde koelsnelheden: Geleidelijk afkoelen voorkomt door spanning veroorzaakte onregelmatigheden in het oppervlak. Koelstations met temperatuurregeling of luchtmessen zorgen voor een gelijkmatige stolling.
Technieken voor nabewerking: Secundaire processen (bv. schuren, coaten) kunnen de oppervlaktekwaliteit verbeteren voor toepassingen die esthetische precisie vereisen.
3. Systematische kwaliteitskaders:
① ISO 9001-normen aannemen: Een kwaliteitsmanagementsysteem (QMS) implementeren dat materiaalinkoop, procesvalidatie en eindinspecties omvat.
② QA/QC-protocollen combineren: Integreer kwaliteitsborging (bijv. procesaudits) met real-time kwaliteitscontrole (bijv. geautomatiseerde detectie van defecten) om zowel systemische als operationele risico's aan te pakken.
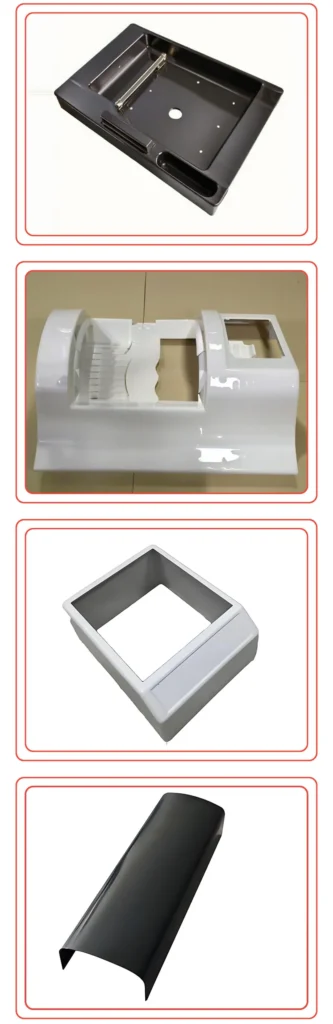
Praktijkvoorbeelden: Dikke wand vacuümvormen
Dikwandig vacuümvormen (ook wel heavy-gauge thermoforming of thick-sheet pressure forming genoemd) is een transformatieve polymeerverwerkingsmethode voor de productie van structurele componenten met wanddiktes van meer dan 3 mm. Met deze techniek worden technisch hoogwaardige thermoplasten zoals ABS, HDPE en PVC thermisch gevormd tot complexe geometrieën door middel van vacuüm/druk-ondersteund gieten, waarbij precisietoleranties van ±0,25 mm op radarkoepels voor de ruimtevaart worden bereikt.
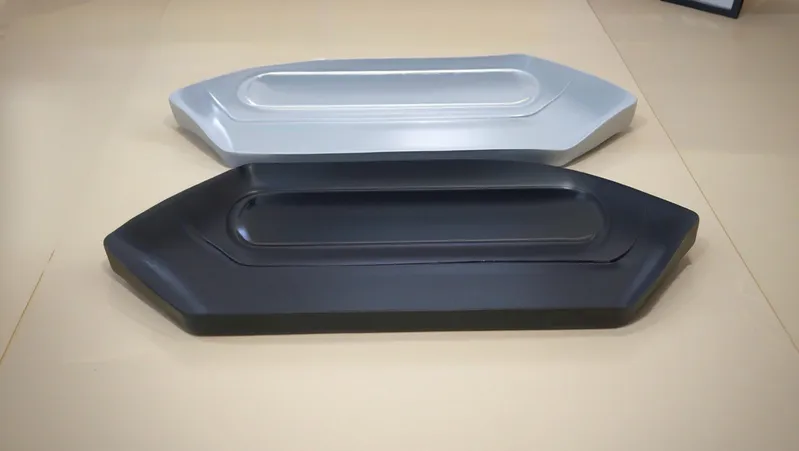
1. Productie van onderdelen voor de lucht- en ruimtevaart:
Bij de ontwikkeling van UAV-systemen maakte dikwandig vacuümvormen met 3-6 mm slagvaste ABS-platen de productie van lichtgewicht radarkoepels mogelijk. Het drukgestuurde proces bereikte een krommingsnauwkeurigheid van ±0,25 mm en verminderde de gereedschapskosten met 60% in vergelijking met composietvormen. Dit bewijst hoe het vormen van dikwandige draperieën precisie-uitdagingen oplost in de productie van luchtvaartbehuizingen.
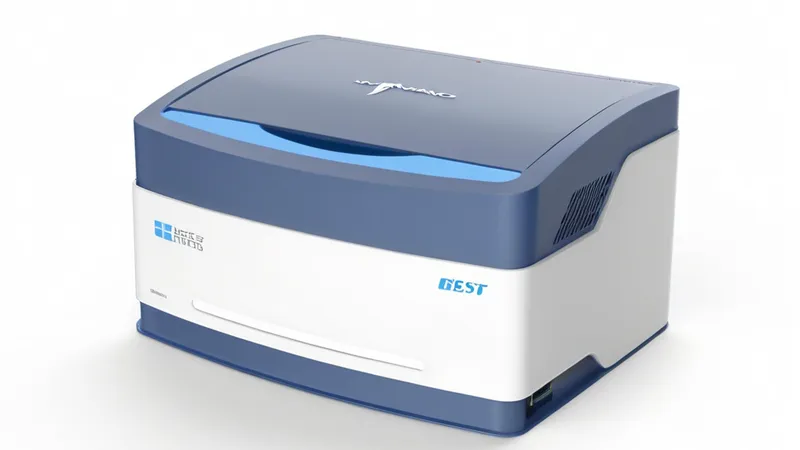
2. Bescherming van medische apparatuur:
Steriliseerbare behuizingen voor draagbare MRI-units werden ontwikkeld met behulp van dikplaatthermoforming van 4 mm PVC van medische kwaliteit. Deze aanpak werd geïmplementeerd onder ISO klasse 8 cleanroomnormen en verkortte de productiecycli van 12 weken (traditionele metaalproductie) tot 3 weken met behoud van de autoclaafcompatibiliteit.
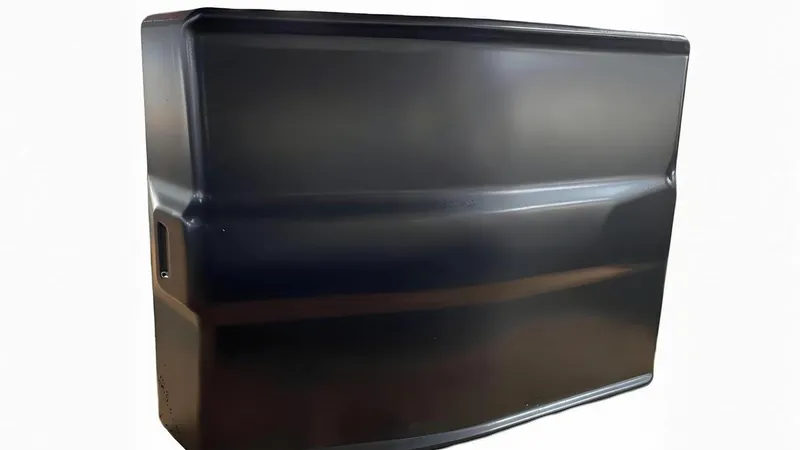
3. Oplossingen voor energieopslag in de auto-industrie:
Dikwandige thermogevormde 8mm vlamvertragende HDPE-batterijomhulsels doorstonden valtests van 1,5 m en een gewichtsbesparing van 30% ten opzichte van metalen alternatieven. Het geïntegreerde ribontwerp door middel van vacuümvormen van zware dikte zorgde voor structurele versterking zonder secundaire assemblage, wat een voorbeeld is van crashbestendige oplossingen in de productie van EV-onderdelen.
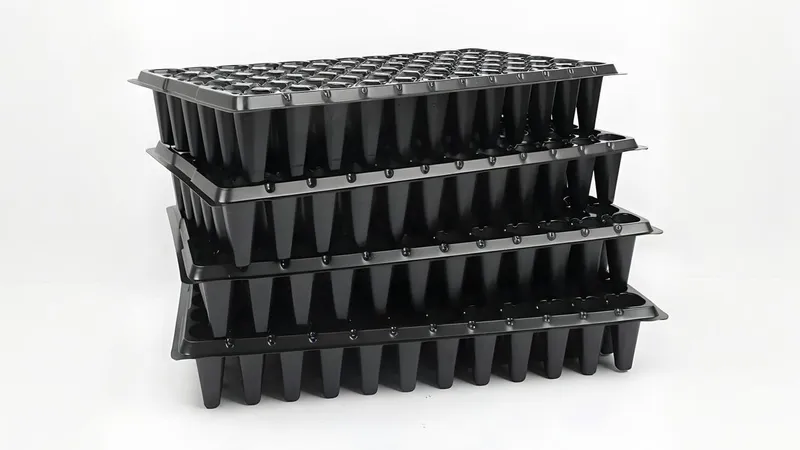
4. Agrarische teeltsystemen:
Herbruikbare 5 mm HDPE zaailingtrays met kunstmestbestendige eigenschappen werden geproduceerd door middel van meervoudig dikwandig vervormen. Met in elkaar grijpende randen en worteldrainagenetwerken ondersteunen deze trays meer dan 200 groeicycli in verticale kweek, wat de rol van dikwandig drukvormen in duurzame landbouwapparatuur illustreert.
Tips:
Procesvariatie | Belangrijkste kenmerken |
---|---|
Zware drapering | Maakt dieptrekken van geometrie >150 mm mogelijk |
Dikke blaarvorming | Ideaal voor het repliceren van oppervlaktestructuren |
Drukvormen van dikke platen | Verbetert de detaildefinitie op materialen van 5-12 mm |
Meertraps vacuümvormen | Geschikt voor complexe gereedschappen met meerdere caviteiten |
Vergelijking: Dikke wand vacuümvormen vs dunne wand vacuümvormen
Bij de keuze tussen dikwandig en dunwandig vacuümvormen is het cruciaal om de verschillen te begrijpen en de juiste productiemethode te kiezen. Dikwandig vacuümvormen, vaak gebruikt voor structurele componenten, biedt een verbeterde duurzaamheid en slagvastheid, waardoor het ideaal is voor zware toepassingen zoals behuizingen voor batterijen en industriële behuizingen. Dunwandig vacuümvormen daarentegen heeft de voorkeur voor lichtgewicht productie in grote volumes, zoals in verpakkingen en consumentengoederen.
1. Basisdefinities:
Vacuümvormen met dikke meter:
- Materiaaldikte: 2-15 mm (technische kunststoffen zoals ABS, PC, acryl).
- Proces: Vereist semi-automatische apparatuur; na het vormen is vaak CNC-bewerking of boren nodig. Aluminium mallen zijn gebruikelijk.
- Toepassingen: Industriële behuizingen (drones, medische apparatuur), autopanelen, grote bewegwijzering.
Dunwandig vacuümvormen:
- Materiaaldikte: 0,14-2 mm (PVC, PET, PS rollen).
- Proces: Gebruikt geautomatiseerde hogesnelheidsmachines met stansvormen voor randen. Mallen zijn van koper of aluminium.
- Toepassingen: Voedselverpakking, blisterverpakkingen, cosmetische trays.
2. Belangrijkste vergelijking:
Aspect | Dikspoor | Dunspoor |
---|---|---|
Materiaalsoorten | ABS, PC, acrylplaten | PVC, PET, PS rollen |
Productie-efficiëntie | Lagere output (langere cyclustijden per onderdeel) | Hoge verwerkingscapaciteit (tientallen onderdelen/minuut) |
Schimmelkosten | Dure aluminium mallen | Goedkope koper/die mallen |
Productsterkte | Hoge slagvastheid, duurzaam voor zware ladingen | Lichtgewicht, niet-structurele toepassingen |
Duurzaamheid | Recyclebaar maar energie-intensief | Energiezuinig; sommige biologisch afbreekbaar (bijv. PET) |
3. Voordelen en beperkingen:
Dikke maat Pro's:
- Rendabel alternatief voor spuitgieten.
- Ondersteunt complexe 3D-texturen en gebogen structuren.
- Duurzaam voor buiten/industrieel gebruik.
Dikke Minpunten:
- Hoog energieverbruik en vereisten voor nabewerking.
- Randbramen die bijgesneden moeten worden.
Thin-Gauge Pros:
- Kostenefficiënt voor massaproductie.
- Flexibele oppervlaktebehandelingen (printen, flocken).
Dunprofiel Cons:
- Breekbaar door dunne wanden en ongelijke dikte.
- Beperkte structurele sterkte.
Aanpassingsopties: Texturen en nabewerking
Om de perfecte oppervlakteafwerking en structurele integriteit te bereiken bij de productie van kunststof zijn geavanceerde aanpassingstechnieken nodig. Van reliëfdruk en materiaalselectie tot nabewerkingen zoals coatings en CNC-afwerking, deze methoden zorgen voor optimale prestaties in verschillende industrieën, waaronder de auto-industrie, architectuur en consumentengoederen.
1. Aanpassingsopties voor textuur:
Embossing en oppervlaktestructuren:
- 3D-patronen: Bereikbaar via matrijsontwerp, inclusief geometrische patronen, merkspecifieke logo's of reliëfeffecten. Aluminium mallen worden vaak gebruikt voor texturen met hoge precisie.
- Afwerking oppervlak: Glanzende, matte, getextureerde of semi-transparante afwerkingen behoren tot de opties. Materialen zoals ABS en PVC hebben de voorkeur voor ingewikkelde texturen, terwijl PMMA (acryl) geschikt is voor lichtverspreidende ontwerpen.
② Materiaal compatibiliteit:
- ABS en PVC zijn ideaal voor zeer gedetailleerd reliëfdrukwerk vanwege hun thermische stabiliteit en vervormbaarheid. PMMA wordt aanbevolen voor toepassingen die optische helderheid vereisen (bijv. verlichtingspanelen).
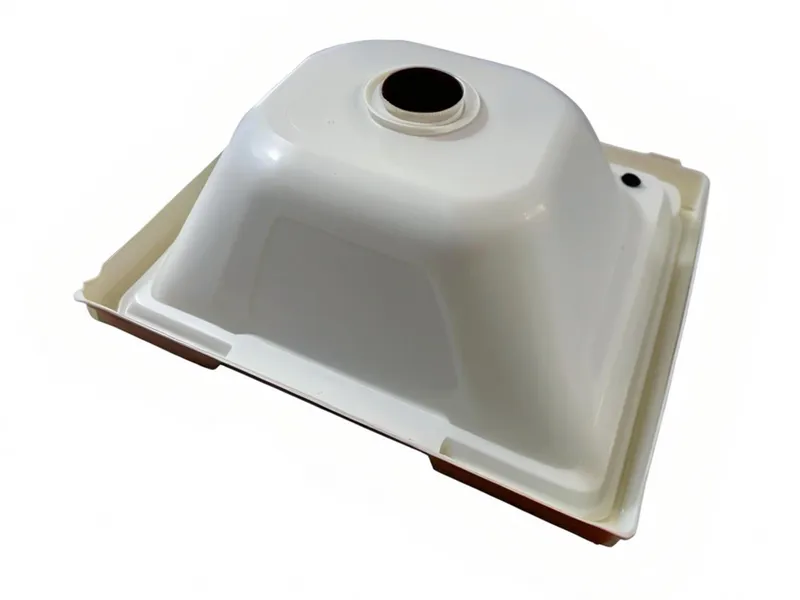
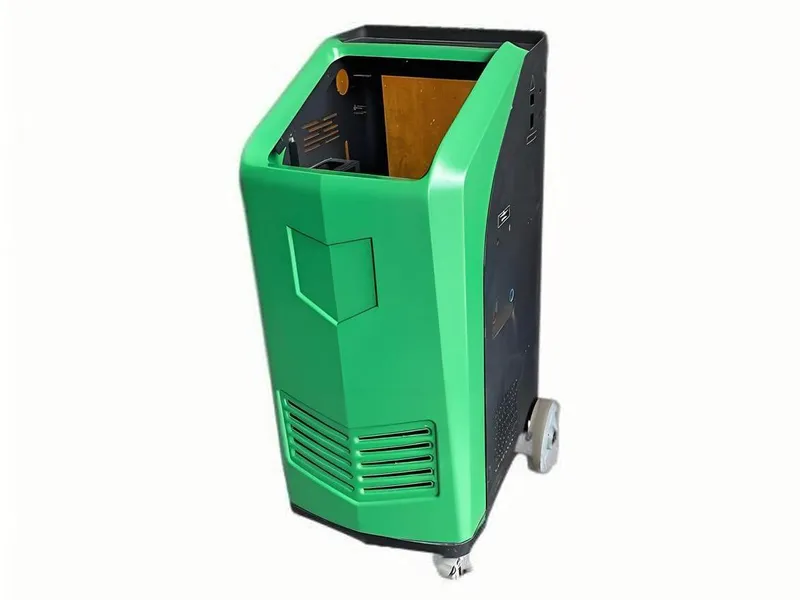
2. Technieken voor nabewerking:
① Oppervlaktecoatings & afdrukken:
- Spuiten: Verf van Automotive-kwaliteit met Pantone-kleurmatching en UV-bestendigheid voor duurzaamheid buitenshuis.
- Zeefdruk: Ondersteunt logo's of tekst met een resolutie tot 0,3 mm, geschikt voor bewegwijzering en branding.
- Bescherming tegen krassen/UV: Additieven zoals UV-stabilisatoren of vlamvertragers verbeteren de prestaties in ruwe omgevingen (bijv. auto-onderdelen, bouwpanelen).
Structurele en functionele verbeteringen:
- CNC snijwerk: Zorgt voor gladde randen en precieze maatnauwkeurigheid, essentieel voor componenten die klaar zijn voor assemblage.
- Metalen platen/lasergraveren: Voegt metalen afwerkingen of permanente markeringen toe voor esthetische of functionele doeleinden.
3. Ontwerp en productie workflow:
Prototyping & DFM (Design for Manufacturability):
- Accepteert 3D-bestanden of fysieke monsters voor reproductie. Engineeringteams optimaliseren ontwerpen voor vacuümvormen, met aandacht voor ondersnijdingen en ontwerphoeken.
Certificeringen en kwaliteitscontrole:
- Voldoet aan ISO-normen, met materiaalcertificeringen (bijv. FDA-conformiteit voor PET van voedselkwaliteit) en tests voor schokbestendigheid en weerbestendigheid.
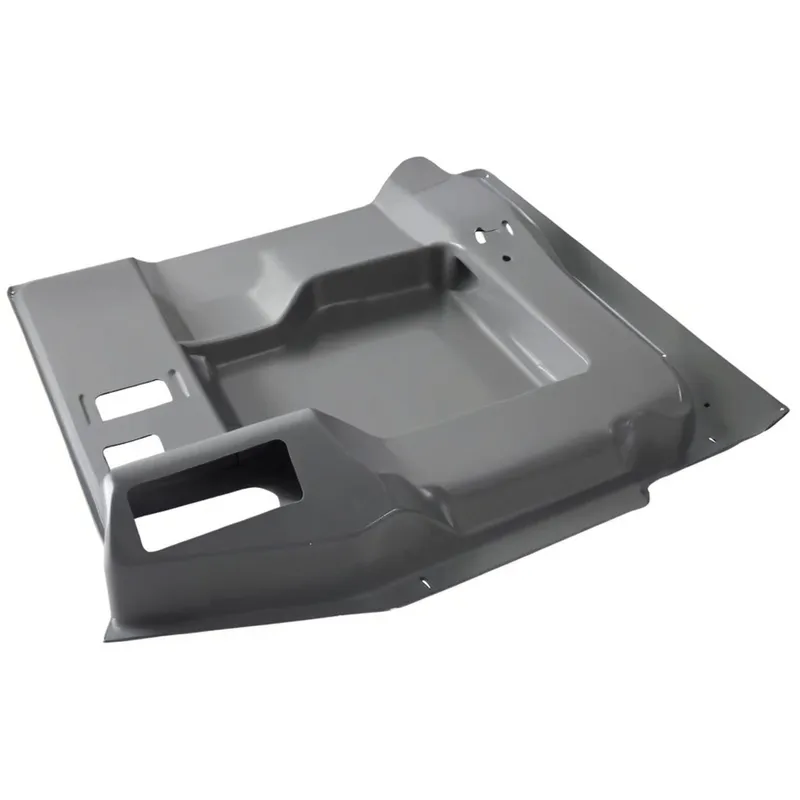
4. Belangrijkste toepassingen:
Auto:
- ABS-bumpers met dikke wand, reliëfstructuur en antikraslaag.
Architectuur:
- Pvc-wandpanelen met brandvertragende coatings en matte afwerkingen voor tenten of industriële ruimtes.
Consumptiegoederen:
- PET trays met antimicrobiële coatings voor voedselverpakking.
Onze end-to-end servicestroom
1. Conceptbespreking
Stem specificaties, materialen (PVC/PET/PP) en schetsen af met verkoop/engineering. Kosten, functie en haalbaarheid van thermovormen beoordelen.
2. 3D-ontwerp
3D caviteitsmodellen maken, dikte en materiaalstroom optimaliseren. Simulaties garanderen spanningsbestendigheid en haalbaarheid voor massaproductie.
3. Prototypering
CNC/3D-geprinte prototypes maken om pasvorm, esthetiek en afdichting te testen. Toleranties aanpassen voor compatibiliteit met geautomatiseerde machines.
4. Vorm Fabricage
Voltooi aluminium/samengestelde matrijzen met DFM-analyse. Integreer koelkanalen en duurzaamheidstests voor hoge cyclusprestaties.
5. Vacuümvormen
Verwarm plastic platen tot ze buigzaam zijn; vacuümvormen over mallen. Parameters controleren (temperatuur, druk) om defecten zoals kromtrekken te voorkomen.
6. Trimmen
Knip overtollig materiaal weg met behulp van precisiemessen/stansmessen. Voeg perforaties of gladgestreken randen toe voor naadloze integratie in de verpakking.
7. Afwerking
Verbetert vacuümgevormde producten door verven, UV-coaten, textureren of lasermarkeren voor afwerkingen (mat, glanzend, metallic).
8. QA en verpakking
Lektests, dimensionale controles en visuele inspecties uitvoeren. Assembleer clamshells en verpak ze met exportdozen/barcodes.
veelgestelde vragen voor klanten
Aan de slag met Uplastech
Heb je vragen? Wij hebben antwoorden.
We zijn gespecialiseerd in extrusie, vacuümvormen, blazen en precisievormen en bieden oplossingen op maat om te voldoen aan uw uiteenlopende productiebehoeften.
We werken met verschillende industrieën, waaronder de auto-industrie, elektronica, consumentengoederen en verpakkingsindustrie. We richten ons op B2B-partnerschappen en leveren oplossingen op het gebied van extrusie, thermovormen, blazen en precisievormen.
Ja, we passen onze oplossingen aan uw unieke vereisten aan.
Neem contact op
Stuur ons een e-mail of vul onderstaand formulier in voor een offerte.
E-mail: uplastech@gmail.com