Ontwerp en productie van plastic extrusiemallen
Ontdek deskundige ontwerp- en productiediensten voor kunststofextrusiematrijzen, afgestemd op uw behoeften. We leveren duurzame matrijzen van hoge kwaliteit voor diverse industrieën en garanderen precisie en efficiëntie bij elk project. Neem vandaag nog contact met ons op voor een consultatie!
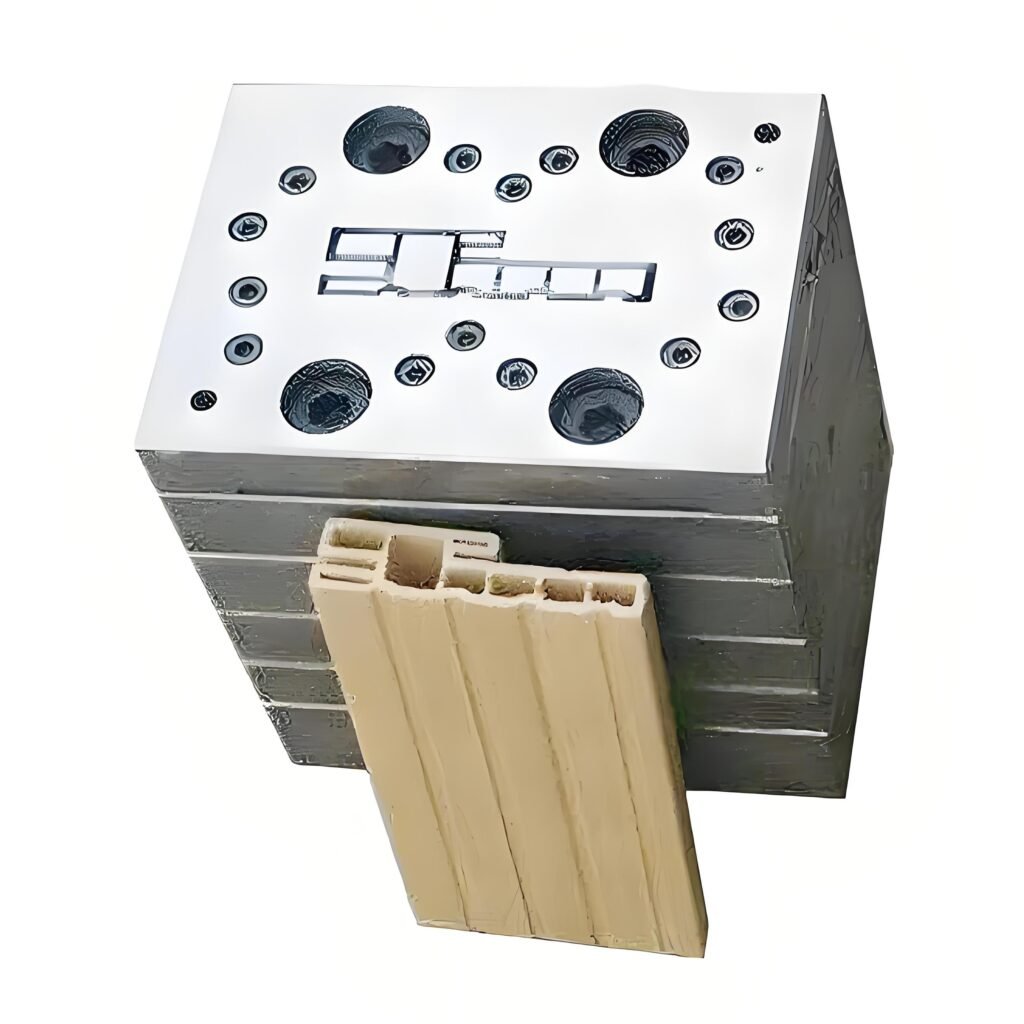
De complete gids voor het ontwerpen en produceren van extrusiemallen
Wat zijn extrusiemallen en hoe werken ze?
Kunststof extrusiemallen, ook wel matrijzen genoemd, zijn superbelangrijk in het kunststof extrusieproces. Kunststof extrusie is een manier om lange vormen te maken van kunststof. Het wordt gebruikt om dingen als buizen, platen en aangepaste vormen te maken. Mensen gebruiken het in de bouw, verpakking en auto's.
Wat zijn plastic extrusiemallen?
Een kunststof extrusiematrijs is een metalen gereedschap dat gesmolten kunststof vormt tot een specifiek doorsnedeprofiel. Deze matrijzen zijn gemaakt van staal of aluminium en kunnen de hoge temperaturen en druk van het extrusieproces aan.
Het ontwerp van de matrijs, of matrijs, bepaalt de uiteindelijke vorm van het geëxtrudeerde product, waardoor het een kritieke factor is in het bereiken van de gewenste afmetingen en kwaliteit.
Onderdelen van kunststof extrusiemallen
De doeltreffendheid van een extrusiesysteem hangt af van verschillende kritieke onderdelen:
Trechter: Voert grondstoffen in de extruder.
Schroef: Draait om het plastic materiaal in het vat te transporteren en te smelten.
Vat: Verwarmt het plastic tot het smeltpunt en houdt het in gesmolten toestand.
Matrijs (extrusievorm): Vormt de gesmolten kunststof tot een doorlopend profiel wanneer het de extruder verlaat.
Koelsysteem: Zorgt voor een goede stolling van het geëxtrudeerde materiaal.
Trekker of transportsysteem: Handhaaft een constante snelheid om vervorming tijdens het koelen te voorkomen.
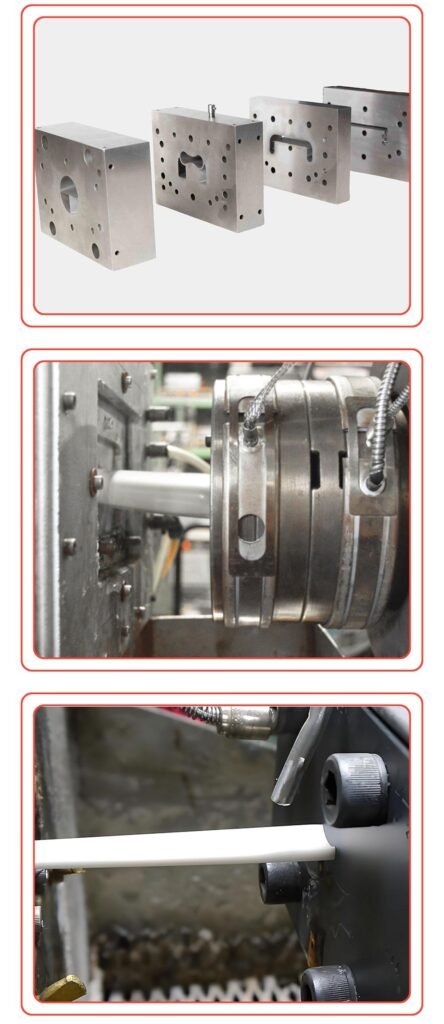
Hoe werken plastic extrusiemallen?
Het plastic extrusieproces maakt van ruwe plastic materialen afgewerkte producten door ze te verhitten, te vormen en af te koelen. Dit is hoe het werkt:
1. Materiaaltoevoer:
Ruw plastic, meestal in de vorm van korrels of granulaat, wordt in een trechter geladen. In dit stadium kunnen additieven zoals kleurstoffen, stabilisatoren of vulstoffen worden toegevoegd om eigenschappen zoals kleur, sterkte of UV-bestendigheid te verbeteren.
2. Smelten:
Het plastic materiaal wordt dan in een verwarmd vat gevoerd, waar een draaiende schroef het smelt. De warmte wordt gegenereerd door de wrijving van de schroef en door externe verwarmingselementen. De temperatuur van het vat wordt meestal ingesteld tussen 200 en 275 graden Celsius, afhankelijk van het type kunststof.
3. Vormgeven:
Het gesmolten plastic wordt door een matrijs geduwd, ook wel de extrusiematrijs genoemd. Deze matrijs geeft het materiaal de gewenste vorm. Het extrusieproces biedt veel flexibiliteit, waardoor verschillende vormen mogelijk zijn, zoals buizen, platen of aangepaste ontwerpen.
4. Koeling:
Zodra het plastic de matrijs verlaat, wordt het snel afgekoeld door lucht, waterbaden of koelwalsen. Dit snelle afkoelingsproces stolt het materiaal en zet het vast in de beoogde vorm.
5. Snijden:
Het afgekoelde en gestolde geëxtrudeerde materiaal wordt vervolgens op de gewenste lengte gesneden. Afhankelijk van de toepassing kan het in specifieke afmetingen worden gesneden of op rollen worden gewikkeld.
6. Afwerking:
Na het snijden kunnen aanvullende processen zoals oppervlaktebehandeling, bijsnijden of verder vormgeven worden uitgevoerd, afhankelijk van het beoogde gebruik en de specificaties van het product.
Wat zijn de verschillende soorten extrusiemallen?
Er zijn veel verschillende soorten plastic extrusiemallen, elk ontworpen voor specifieke industriële en productbehoeften. Deze mallen zijn cruciaal voor het vormen van ruw plastic tot precieze profielen, vellen of folies. Hier volgt een overzicht van de verschillende soorten kunststof extrusiemallen:
1. Matrijzen met één schroef:
Matrijzen met één schroef zijn de meest voorkomende extrusiemallen. Ze zijn perfect voor het maken van pijpen, buizen en profielen. Ze zijn goedkoop en kunnen gebruikt worden voor het extruderen van veel verschillende kunststoffen zoals PVC, PE, PP en ABS. Hierdoor zijn ze ideaal voor grote productieseries.
2. Dubbele schroefmatrijzen:
Matrijzen met twee schroeven gebruiken twee schroeven voor intens mengen en smelten, waardoor ze goed zijn voor het maken van complexe vormen of producten met veel vulstof. Deze matrijzen worden vaak gebruikt in toepassingen zoals buizen met meerdere lumen of medische hulpmiddelen zoals katheters, waarbij je het materiaal heel goed wilt controleren.
3. Co-Extrusiematrijzen:
Co-extrusiematrijzen zijn ontworpen om meerdere lagen kunststof tegelijk te extruderen. Hierdoor kun je producten maken met speciale eigenschappen zoals barrièrelagen of isolatie. Mensen gebruiken deze matrijzen veel voor verpakkingsmaterialen. Ze kunnen kunststoffen met verschillende smeltpunten of eigenschappen samenvoegen om dingen beter te laten werken.
4. Micro-Extrusiematrijzen:
Micro-extrusiematrijzen zijn ontworpen om kleine, precieze onderdelen te maken, zoals medische apparatuur en elektronica. Ze maken onderdelen die zeer nauwkeurig zijn en worden vaak gebruikt met speciale kunststoffen zoals PEEK en Teflon. Ze zijn ideaal voor het maken van onderdelen met zeer kleine afmetingen en vormen.
5. Vlakke film en vellen matrijzen:
Matrijzen voor vlakke folies en vellen maken brede, dunne vellen of folies, die vaak worden gebruikt in verpakkingen, laminaten en thermovormen. Deze matrijzen zorgen voor een gelijkmatige dikte via instelbare stroomkanalen en werken met materialen zoals PET, PE en PVC.
6. Geblazen film matrijzen:
Matrijzen voor blaasfolie worden gebruikt om buisvormige folies te maken die met lucht worden opgeblazen. Deze zijn ideaal voor het maken van plastic zakken, krimpfolie en rekfolie. Omdat ze rond zijn, is de folie rondom even dik. Ze kunnen LDPE, HDPE en PP maken.
7. Pijp- en buismatrijzen:
Pijp- en buismatrijzen worden gemaakt om holle cilindrische profielen te maken, zoals loodgietersbuizen en medische buizen. Ze hebben verstelbare matrijsspleten om de wanddikte te veranderen. Ze werken met materialen zoals PVC, HDPE en PP.
8. Profiel extrusiematrijzen:
Matrijzen voor de extrusie van profielen worden gebruikt om complexe vormen te maken, zoals raamkozijnen en sierlijsten voor auto's. Ze zijn ideaal voor het maken van nauwkeurige mallen met ingewikkelde doorsneden. Ze zijn ideaal voor het maken van precieze mallen met ingewikkelde doorsneden en werken goed met materialen zoals ABS, PVC en TPE, die worden gebruikt in industriële en bouwtoepassingen.
9. Coatingmatrijzen voor draad en kabel:
Matrijzen voor draad- en kabelcoating worden gebruikt om draden of kabels te omhullen met beschermende plastic lagen, die isolatie bieden voor elektrische bedrading en glasvezel. Deze matrijzen zijn ontworpen om materialen met een hoge temperatuur te verwerken, zoals PVC en XLPE, terwijl ze zorgen voor een gladde en duurzame afwerking.
10. Extrusieblaasvormen:
Extrusieblaasmallen maken holle verpakkingen zoals flessen en brandstoftanks door een gesmolten kunststof parison te vormen en op te blazen. Met een nauwkeurige temperatuurregeling om ervoor te zorgen dat de wanden rondom even dik zijn, werken ze uitstekend met PET, HDPE en PP.
11. Ringvormige matrijzen:
Ringvormige matrijzen maken ronde vormen zoals ringen en holle buizen. Ze zijn goed voor dingen als pakkingen en afdichtingen. Ze maken dingen die de juiste maat hebben. Ze zijn goed voor sterke kunststoffen zoals nylon en versterkt PP.
12. Plaatbekledingsmatrijzen:
Matrijzen voor vellencoating worden gebruikt om dunne kunststoflagen aan te brengen voor lamineer- of coatingdoeleinden. Ze worden gebruikt in decoratieve films en barrièretoepassingen. Deze matrijzen zijn zeer nauwkeurig en compatibel met materialen zoals TPU, EVA en PE. Ze zorgen ervoor dat de coatings gelijkmatig zijn en lang meegaan.
13. Meerlagige extrusiematrijzen:
Matrijzen voor meerlaagse extrusie worden gebruikt om meerdere materialen in één proces te combineren, waardoor producten met verbeterde eigenschappen ontstaan, zoals verpakkingsfolie of autopanelen. Deze matrijzen zijn uitstekend in het combineren van geavanceerde materialen zoals EVOH, Nylon en PE, wat zorgt voor betere prestaties voor gespecialiseerde toepassingen.
Richtlijnen voor het ontwerp van extrusiematrijzen
Een effectief ontwerp van extrusiematrijzen is essentieel om consistent en efficiënt kunststofproducten van hoge kwaliteit te produceren. Hieronder volgt een geconsolideerde en gedetailleerde reeks richtlijnen die alle aspecten van het ontwerpen van extrusiematrijzen behandelt:
1. Principes voor matrijsontwerp:
Consistentie en efficiëntie: De matrijs produceert een uniform en consistent product, minimaliseert materiaalverspilling en vermindert productiestilstand.
Duurzaamheid: Ontwerp om bestand te zijn tegen bedrijfsbelastingen, waaronder hoge temperaturen en druk, voor een lange levensduur en betrouwbaarheid.
2. Materiaalkeuze:
Duurzaamheid en weerstand: Gebruik hoogwaardige materialen zoals gehard staal of wolfraamcarbide voor slijtvastheid en thermische stabiliteit.
Corrosiebestendigheid: Kies materialen die bestand zijn tegen corrosieve omgevingen, vooral voor het verwerken van agressieve kunststoffen zoals PVC.
3. Geometrie van de matrijs en ontwerp van het stromingskanaal:
Gestroomlijnd ontwerp: Stromingskanalen moeten symmetrisch en glad zijn, stagnerende gebieden vermijden om een gelijkmatige materiaalverdeling te garanderen en defecten zoals kromtrekken of ongelijke dikte te verminderen.
Geleidelijke overgangen: Zorg voor geleidelijke overgangen in de matrijsvorm om de materiaalspanning te minimaliseren en defecten in het geëxtrudeerde product te voorkomen.
4. Landlengte en doorgang:
Optimale landlengte: Houd een landlengte aan die ongeveer 10 keer zo groot is als de landafstand om de stroming te stabiliseren en consistente afmetingen te garanderen.
Uniforme doorsnede: De matrijs moet een constante dwarsdoorsnede hebben om diktevariaties in het extrudaat te voorkomen.
5. Afstelling matrijzenafstand:
Aanpasbaar ontwerp: Voorzien van instelbare openingen voor fijnafstelling van de materiaaldikte tijdens gebruik, voor verschillende viscositeiten en productievereisten.
6. Thermisch beheer en koelsystemen:
Temperatuurregeling: Gelijkmatige verwarmings- en koelzones voorkomen thermische gradiënten en kromtrekken, waardoor de productintegriteit behouden blijft.
Geïntegreerde koeling: Gebruik koelsystemen op basis van water of lucht om de matrijstemperatuur te stabiliseren en oververhitting te voorkomen.
7. Ontluchtingssystemen:
Ontluchting: Voeg ontluchtingskanalen toe om ingesloten lucht te verwijderen, een glad oppervlak te garanderen en defecten zoals holtes of luchtzakken te voorkomen.
8. Oppervlakteafwerking en coating:
Gladde binnenoppervlakken: Breng oppervlaktebehandelingen aan (bijv. verchromen of nitreerlagen) en zorg voor een spiegelende afwerking om wrijving te verminderen, de materiaalstroom te verbeteren en de levensduur van de matrijs te verlengen.
9. Modulair en onderhoudsvriendelijk ontwerp:
Onderhoudsgemak: Gebruik modulaire ontwerpen voor eenvoudigere demontage, reiniging en vervanging van onderdelen, waardoor stilstand tot een minimum wordt beperkt.
Duurzame onderdelen: Met vervangbare slijtdelen om de onderhoudskosten op lange termijn te verlagen.
10. Simulatie en testen:
CFD-simulatie: Gebruik geavanceerde simulatiesoftware om stromingspatronen te analyseren, geometrieën te optimaliseren en prestaties te voorspellen.
Prototype testen: Voer grondige tests uit om potentiële problemen te identificeren en te verhelpen voordat de productie op volledige schaal plaatsvindt.
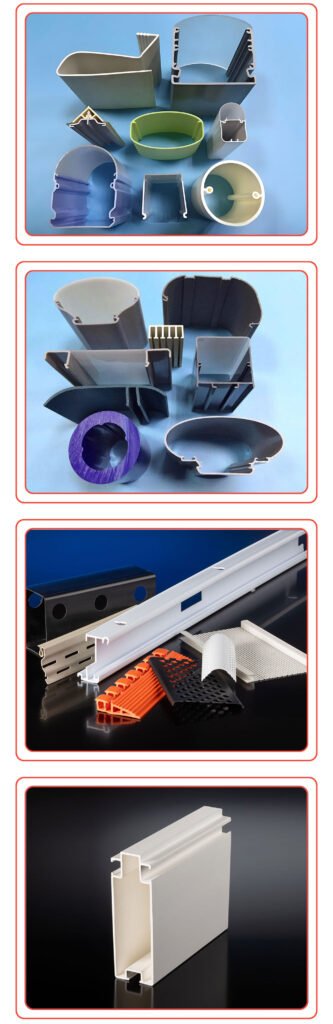
11. Matrijs uitlijnen:
Nauwkeurige uitlijning: Zorg voor de juiste uitlijning tussen de matrijs, extruder en nageschakelde apparatuur om materiaalverspilling, ongelijkmatige stroming en productdefecten te voorkomen.
12. Ontwerp voor maakbaarheid:
Vereenvoudigd ontwerp: Vermijd al te complexe geometrieën die assemblage en kalibratie bemoeilijken. Eenvoudige ontwerpen verbeteren de produceerbaarheid en betrouwbaarheid.
Pasvorm en integratie: Test aangepaste extrusies op compatibiliteit met andere onderdelen om een naadloze integratie te garanderen.
13. Overwegingen met betrekking tot reiniging en onderhoud:
Eenvoudige reinigingssystemen: Ontwerp matrijzen met toegankelijke reinigingsmechanismen om resten te verwijderen en verontreiniging te voorkomen.
Gepland onderhoud: Stel regelmatige inspectie- en reinigingsschema's op om optimale prestaties van de matrijs en productkwaliteit te garanderen.
14. Geavanceerde ontwerppraktijken:
Duidelijke ontwerpfilosofie: Focus op eenvoud, efficiëntie en het minimaliseren van afval.
② Gebruik van software: Gebruik gespecialiseerde software om aan specifieke productvereisten te voldoen en prestaties onder verschillende omstandigheden te simuleren.
Wat zijn de meest gebruikte materialen voor extrusiemallen?
Extrusiegieten is een veelzijdig productieproces om thermoplastische producten te maken. De matrijsmaterialen die in dit proces worden gebruikt, spelen een grote rol bij het bepalen van hoe goed het eindproduct is. Hier volgt een overzicht van de meest gebruikte materialen voor kunststof extrusiematrijzen en waar je aan moet denken als je het beste materiaal voor jouw toepassing kiest.
1. Staal:
Staal is het meest gebruikte materiaal voor extrusiemallen en staat bekend om zijn uitzonderlijke sterkte, duurzaamheid en slijtvastheid. Koudwerkstaal van hoge kwaliteit biedt een uitstekende hardheid, waardoor het ideaal is voor hoogvolume productiemallen, terwijl warmwerkstaal bestand is tegen extreme temperaturen, waardoor het lang meegaat in omgevingen met thermische belasting. Gelegeerd gereedschapsstaal biedt een balans van taaiheid, slijtvastheid en bewerkbaarheid, waardoor het veelzijdig is voor verschillende toepassingen, waaronder matrijzen voor PVC, HDPE en ABS.
2. Aluminiumlegeringen:
Aluminiumlegeringen zijn een lichtgewicht en kosteneffectieve optie die veel gebruikt wordt voor prototypes en korte productieruns. Hun uitstekende thermische geleidbaarheid helpt de koeltijden te verkorten en de efficiëntie te verbeteren. Hoewel aluminium gemakkelijker te bewerken is dan staal, heeft het een lagere hardheid en slijtvastheid, waardoor het alleen gebruikt kan worden voor toepassingen met een lage belasting. Het is het meest geschikt voor matrijzen met eenvoudige geometrieën en productie in kleine aantallen.
3. Koper en koperlegeringen:
Koper en koperlegeringen, vooral beryllium-koper, worden gewaardeerd om hun superieure thermische geleidbaarheid en corrosiebestendigheid. Deze materialen zijn bijzonder effectief voor matrijzen die een nauwkeurige temperatuurregeling vereisen, waardoor kromtrekken en defecten in complexe extrusieprofielen worden voorkomen. Matrijzen op basis van koper worden vaak gebruikt in toepassingen die een afwerking van hoge kwaliteit en een consistent temperatuurbeheer vereisen.
4. Titaanlegeringen:
Titaanlegeringen staan bekend om hun indrukwekkende sterkte-gewichtsverhouding en uitstekende corrosiebestendigheid. Ze zijn bijzonder geschikt voor mallen met hoge precisie en gespecialiseerde toepassingen waarbij strikte toleranties essentieel zijn. Het lichtgewicht van titanium maakt het ook een goede keuze voor matrijzen die worden gebruikt in industrieën zoals de medische en luchtvaartindustrie.
5. Keramische materialen:
Keramische materialen worden gekozen vanwege hun uitzonderlijke hardheid en weerstand tegen hoge temperaturen. Deze eigenschappen maken ze ideaal voor matrijzen die worden gebruikt in extreme omstandigheden, zoals toepassingen onder hoge druk of bij hoge temperaturen. Keramiek is echter bros, wat het gebruik ervan kan beperken in toepassingen die mechanische schokbestendigheid vereisen.
6. Kunststoffen en composietmaterialen:
Gespecialiseerde kunststoffen en composieten worden soms gebruikt als matrijsmateriaal wanneer lichtgewicht structuren of chemische weerstand vereist zijn. PTFE (Teflon) wordt vaak gekozen vanwege de antikleefeigenschappen, waardoor het gemakkelijk te ontvouwen is in toepassingen met een lage productie. Deze materialen zijn kosteneffectief en bieden unieke voordelen voor specifieke toepassingen, maar zijn over het algemeen beperkt tot omgevingen met lage druk.
7. Messing en andere koperlegeringen:
Messing, een legering van koper en zink, wordt vaak gekozen vanwege de bewerkbaarheid en corrosiebestendigheid. Het levert een oppervlakteafwerking van hoge kwaliteit en is geschikt voor matrijzen die in kleine tot middelgrote productievolumes worden gebruikt. De combinatie van precisie en betaalbaarheid maakt het een aantrekkelijke optie voor bepaalde toepassingen.
8. Glas en siliconen:
Glas en silicone zijn gespecialiseerde materialen die worden gebruikt in nichetoepassingen die een hoge mate van precisie, flexibiliteit of unieke oppervlakteafwerking vereisen. Siliconenmallen zijn ideaal voor ingewikkelde ontwerpen en bieden een uitstekende flexibiliteit, terwijl glazen mallen een superieure maatnauwkeurigheid leveren, maar duur en breekbaar zijn, wat hun wijdverspreide gebruik beperkt.
Overwegingsfactoren bij het kiezen van matrijsmaterialen
Productievolume:
Matrijzen voor hoogvolume productie vereisen materialen zoals gereedschapsstaal voor duurzaamheid, terwijl voor laagvolume productie aluminium of composietmaterialen kunnen worden gebruikt.
Thermische prestaties:
Materialen zoals aluminium of koperlegeringen hebben de voorkeur vanwege hun thermische geleidbaarheid, waardoor efficiënte koelcycli worden gegarandeerd.
③ Afwerking oppervlak:
Messing of roestvrij staal is uitstekend voor hoogwaardige afwerkingen, terwijl keramiek ideaal is voor precisie.
Corrosiebestendigheid:
Roestvrij staal, titanium en koperlegeringen zijn bestand tegen corrosie, wat essentieel is voor medische toepassingen of toepassingen in de voedingsmiddelenindustrie.
Kosten en onderhoud:
Aluminium is kosteneffectief voor prototyping, terwijl voorgeharde staalsoorten de bewerkingstijd en -kosten verminderen voor duurzame productiemallen.
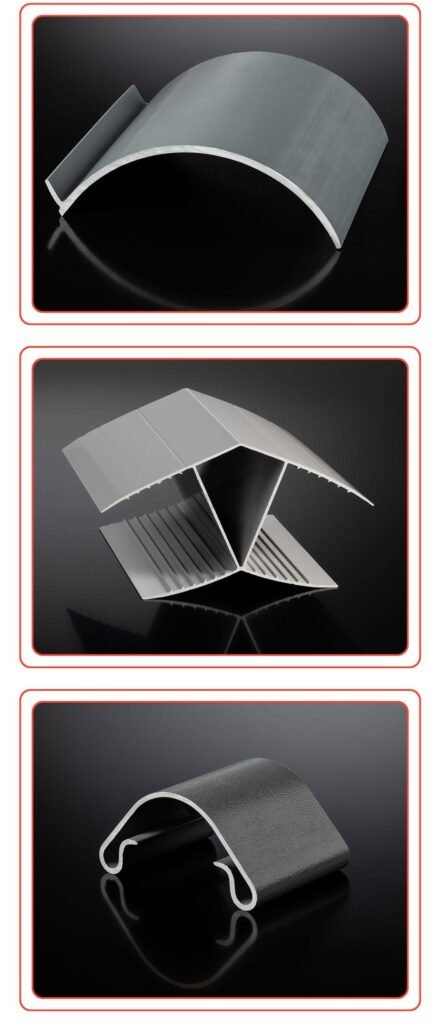
Welke invloed hebben de eigenschappen van matrijsmaterialen op het ontwerp van matrijzen?
De eigenschappen van matrijsmaterialen zijn fundamenteel voor het ontwerp, de prestaties en de levensduur van matrijzen die worden gebruikt in spuitgiet- en extrusieprocessen. Ze beïnvloeden factoren zoals thermisch beheer, duurzaamheid, productkwaliteit en productie-efficiëntie. Hier is een uitgebreide gids over hoe deze eigenschappen het matrijsontwerp beïnvloeden:
1. Warmtegeleidingsvermogen:
Impact: Materialen met een hoge thermische geleidbaarheid (bijv. aluminium, koper) voeren warmte efficiënt af, waardoor de koeltijden korter worden en problemen zoals kromtrekken of vervorming in spuitgietproducten worden voorkomen. Omgekeerd kunnen materialen zoals staal, met een lager warmtegeleidingsvermogen, extra koelsystemen nodig hebben.
Ontwerpoverwegingen: Gebruik hooggeleidende materialen voor mallen met prioriteit voor snelheid en gelijkmatige koeling, maar zorg voor balans met structurele versterking voor duurzaamheid.
2. Thermische uitzetting:
Impact: Variaties in thermische uitzettingssnelheden kunnen leiden tot onnauwkeurigheden in de maatvoering bij temperatuurveranderingen. Materialen zoals staal of keramiek, met een lage thermische uitzetting, bieden een grotere maatvastheid.
Ontwerpoverwegingen: Selecteer voor processen bij hoge temperaturen of nauwe toleranties materialen met minimale uitzetting om de precisie te behouden.
3. Sterkte en duurzaamheid:
Impact: Sterke materialen (bijv. gehard staal, titanium) zijn bestand tegen de hoge druk en temperaturen van spuitgieten of extrusie. Deze materialen zijn bestand tegen vervorming en garanderen een consistente productkwaliteit tijdens lange productiecycli.
Ontwerpoverwegingen: Gebruik duurzame materialen voor matrijzen met complexe geometrieën of grote volumes. Overweeg gereedschapsstaal zoals P20 of H13 vanwege de balans tussen sterkte en bewerkbaarheid.
4. Slijtvastheid:
Impact: Voortdurend gebruik en schurende materialen kunnen matrijsoppervlakken aantasten. Slijtvaste materialen verminderen de onderhoudsfrequentie en verlengen de levensduur van de matrijs.
Ontwerpoverwegingen: Kies voor coatings (bijv. nitreren, verchromen) of hardere materialen bij het gieten van abrasieve of met glas gevulde kunststoffen.
5. Corrosiebestendigheid:
Impact: Blootstelling aan vocht, chemicaliën of corrosieve additieven in bepaalde kunststoffen kan matrijzen aantasten, wat de productkwaliteit beïnvloedt. Roestvrijstalen en gecoate mallen bieden meer weerstand.
Ontwerpoverwegingen: Gebruik corrosiebestendige materialen voor mallen die worden blootgesteld aan reactieve omgevingen, of pas beschermende oppervlaktebehandelingen toe voor een langere levensduur.
6. Bewerkbaarheid:
Impact: Gemakkelijker te bewerken materialen zoals aluminium verlagen de productietijd en -kosten, maar missen mogelijk de duurzaamheid van staal of titanium.
Ontwerpoverwegingen: Voor prototype-mallen of kleine series besparen bewerkbare materialen tijd. Productiemallen kunnen de hogere bewerkingskosten van duurzame materialen rechtvaardigen.
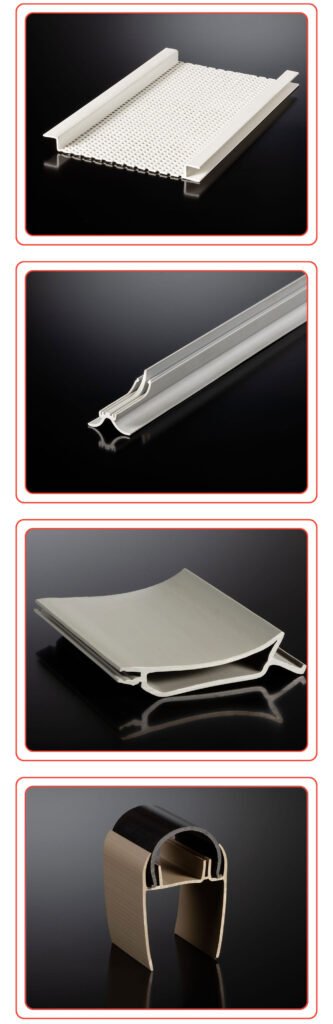
7. Afwerking oppervlak:
Impact: De oppervlaktekwaliteit van de matrijs beïnvloedt de esthetiek van het eindproduct en het gemak waarmee het loskomt. Afwerkingen van hoge kwaliteit minimaliseren defecten en verkorten de cyclustijden.
Ontwerpoverwegingen: Kies materialen met een gladde afwerking, zoals gereedschapsstaal, voor onderdelen met kritieke esthetische of functionele vereisten.
8. Chemische weerstand:
Impact: Bepaalde kunststoffen of additieven kunnen matrijsoppervlakken aantasten. Materialen zoals roestvrij staal of titanium zijn bestand tegen chemische blootstelling, waardoor de integriteit van de matrijs behouden blijft.
Ontwerpoverwegingen: Geef bij mallen die gebruikt worden met chemisch agressieve harsen voorrang aan resistente materialen of beschermende coatings.
9. Kosten:
Impact: Hoogwaardige materialen zoals gehard staal of titanium verhogen de initiële kosten, maar verlagen de onderhouds- en vervangingskosten na verloop van tijd.
Ontwerpoverwegingen: Breng de materiaalkosten in balans met het verwachte productievolume en de operationele eisen om het rendement op investering te optimaliseren.
Technieken voor de productie van kunststof extrusiemallen
Kunststof extrusiematrijzen, ook wel extrusiematrijzen genoemd, worden gemaakt met behulp van een breed scala aan technieken om de gewenste vorm, grootte en functionaliteit te bereiken. Hieronder volgt een uitgebreid overzicht van de meest gebruikte productietechnieken, met belangrijke details voor een beter begrip:
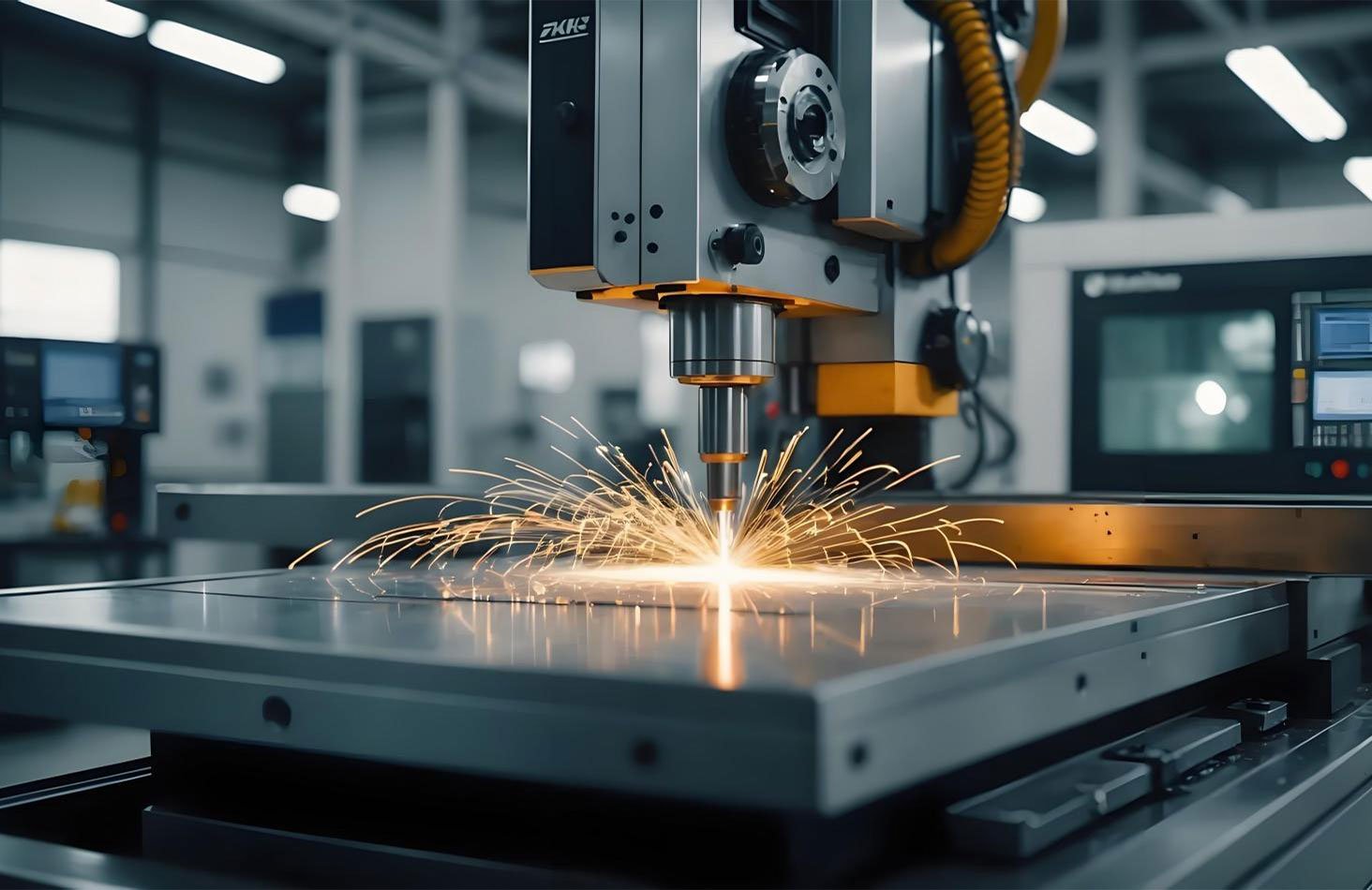
1. CNC-bewerking:
CNC-bewerking maakt gebruik van computergestuurde snijgereedschappen om matrijsmaterialen zoals staal of aluminium nauwkeurig vorm te geven. Het is zeer nauwkeurig en kan nauwe toleranties bereiken, waardoor het ideaal is voor het maken van primaire matrijsonderdelen en externe geometrieën met precisie en consistentie.
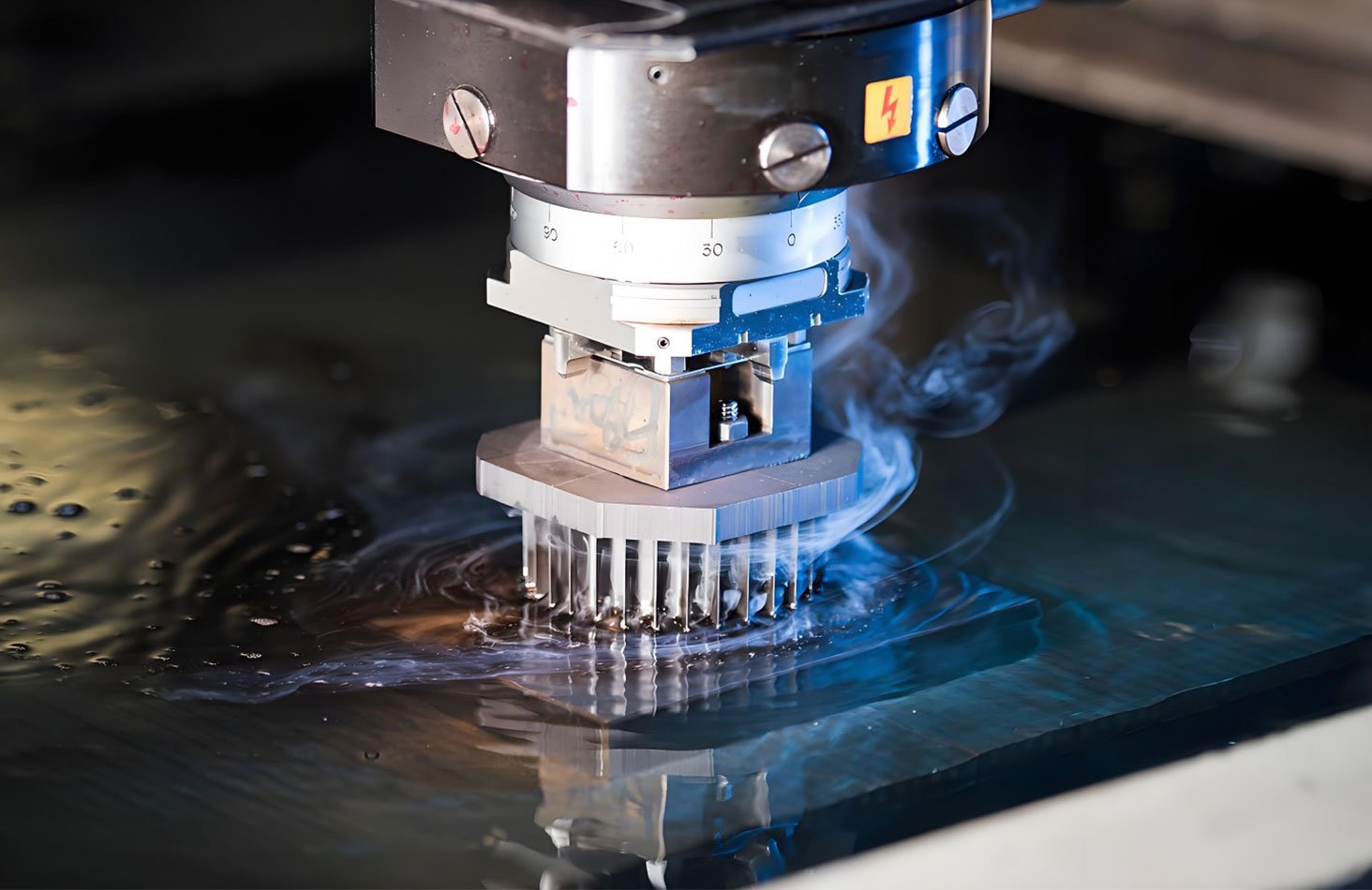
2. EDM:
EDM maakt gebruik van elektrische ontladingen om materiaal te eroderen, waardoor complexe vormen, diepe holtes en ingewikkelde interne geometrieën kunnen worden gecreëerd. Het omvat varianten zoals zinkvonkmachines voor gedetailleerde holtes en draadvonkmachines voor nauwkeurig snijden, waardoor het geschikt is voor smalle stromingskanalen en scherpe hoeken.
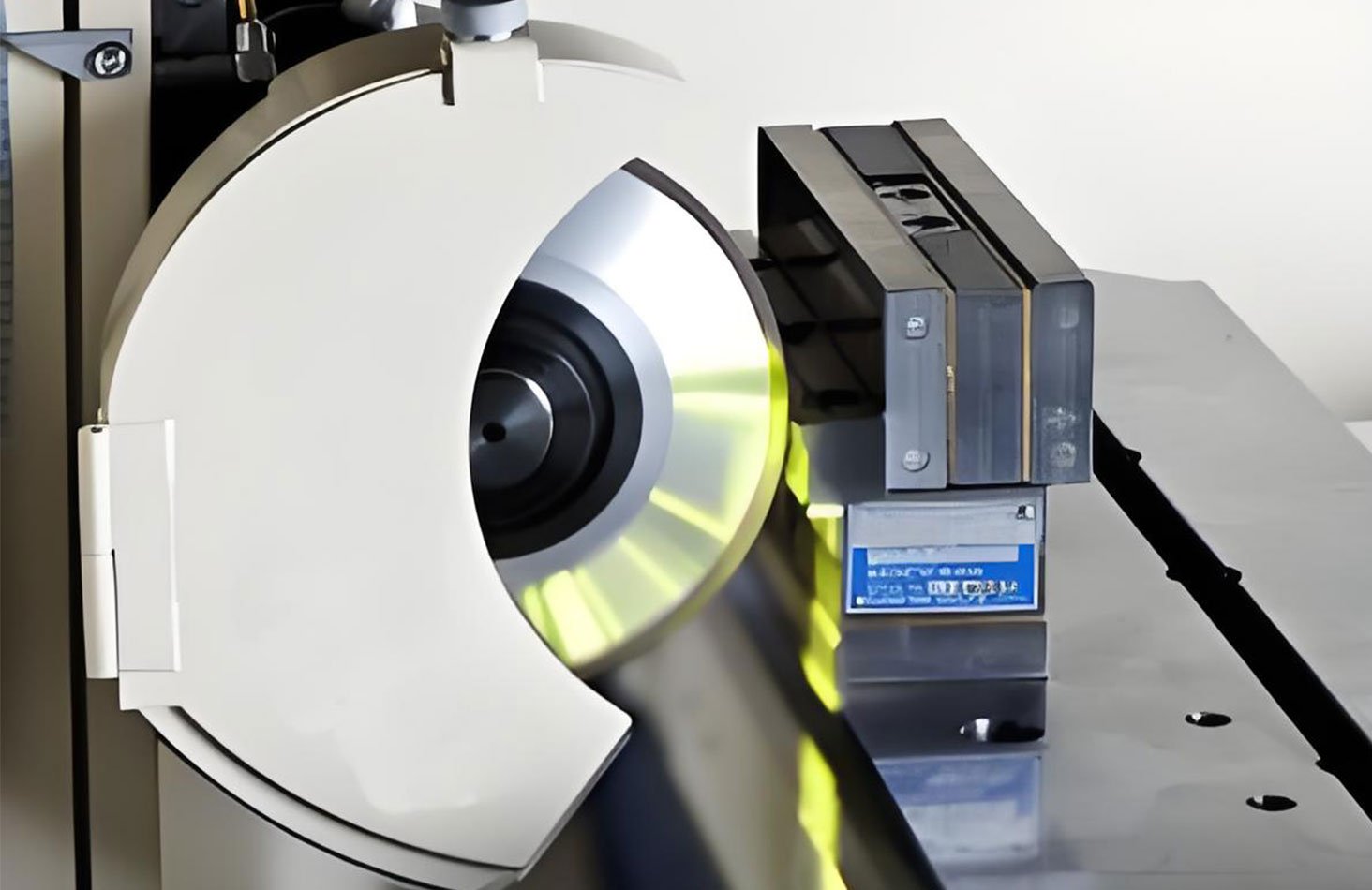
3. Malen:
Slijpen wordt gebruikt om de oppervlakteafwerking en precisie van matrijsonderdelen te verbeteren door kleine hoeveelheden materiaal te verwijderen door middel van schurende werking. Het wordt vaak gebruikt in de laatste stadia van het maken van mallen om gladde oppervlakken te verkrijgen en te voldoen aan strakke maattoleranties.
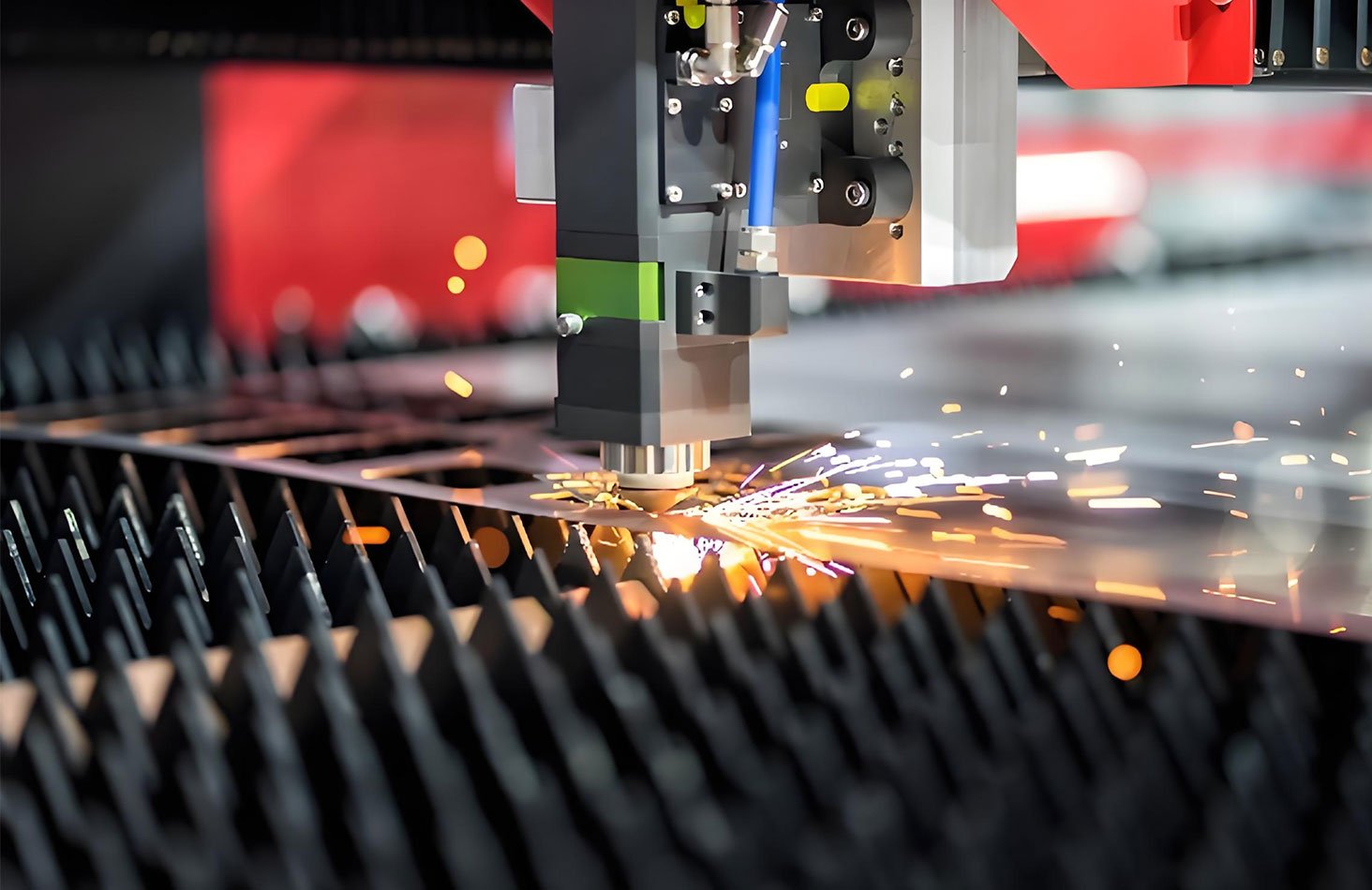
4. Lasersnijden:
Lasersnijden maakt gebruik van een krachtige laserstraal om vormmateriaal met een uitstekende precisie te snijden en te vormen. Het wordt vaak gebruikt voor dunne platen of om ingewikkelde patronen te maken in matrijsonderdelen en biedt een snelle en efficiënte snijoplossing.
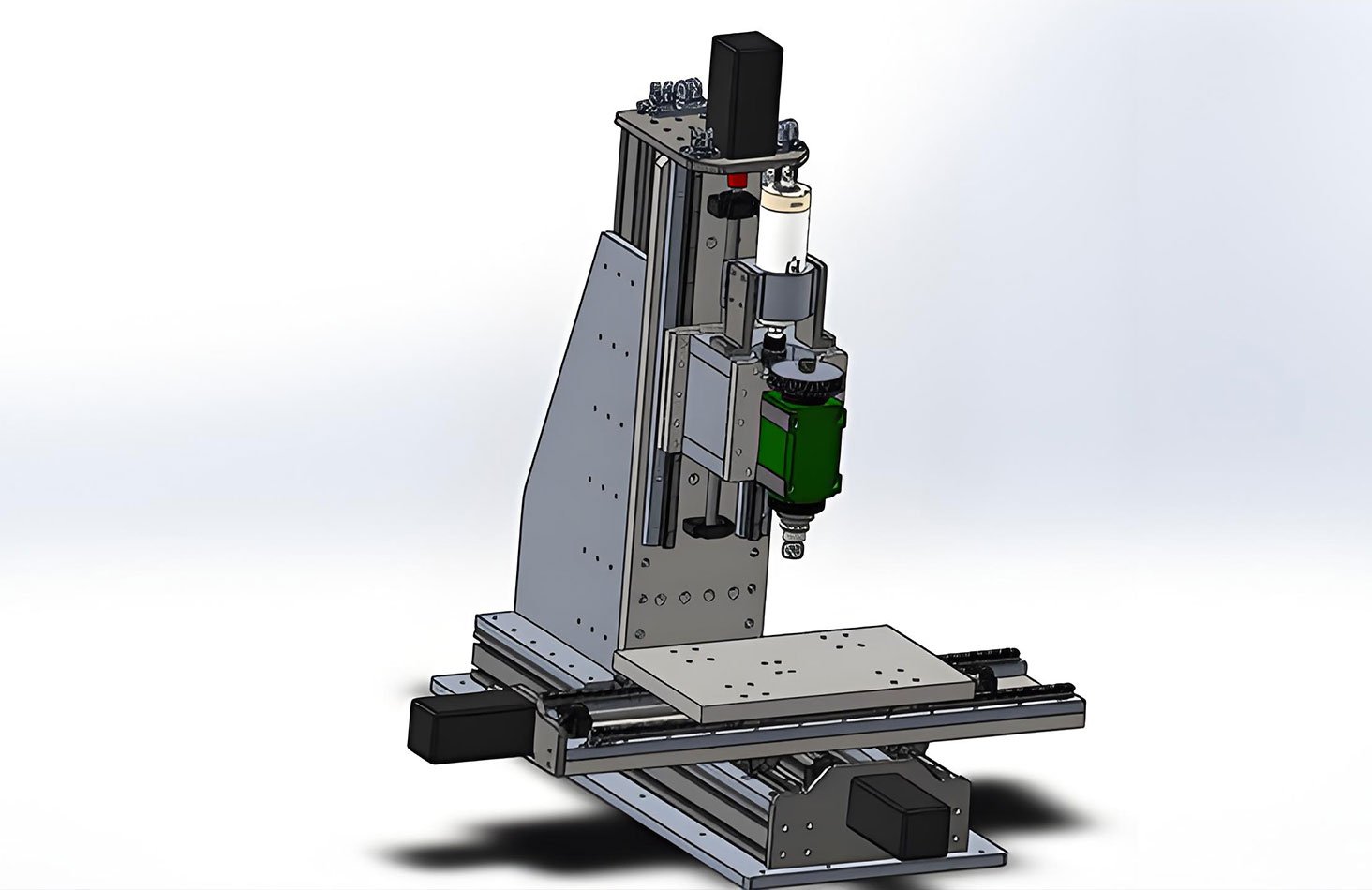
5. Frezen:
Bij frezen wordt een roterend snijgereedschap, of frees, gebruikt om materiaal van een werkstuk te verwijderen. Deze techniek is ideaal voor het bewerken van grote, vlakke oppervlakken met hoge nauwkeurigheid, maar ook voor het maken van sleuven, contouren en andere complexe vormen in matrijsonderdelen.
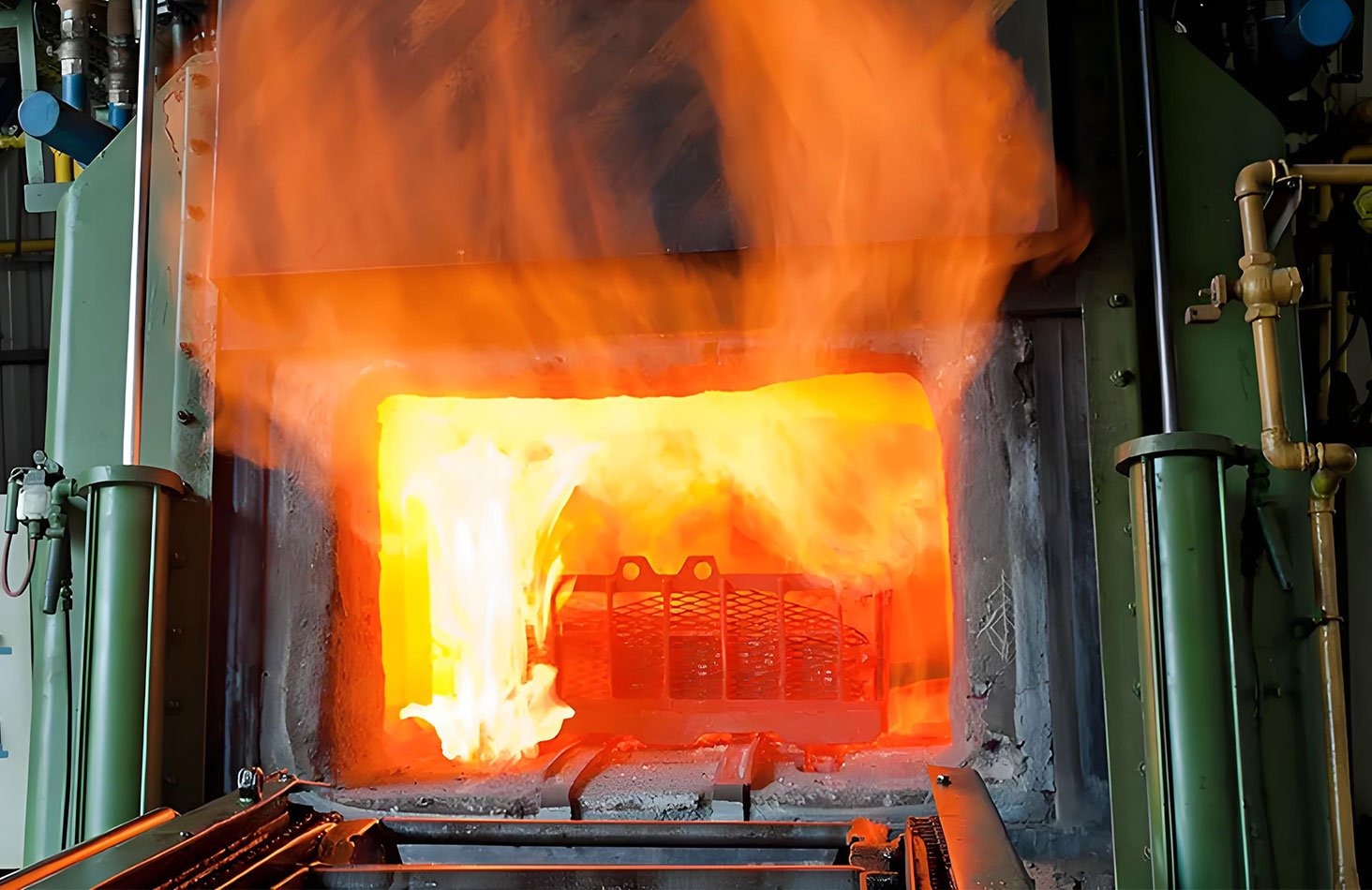
6. Warmtebehandeling:
Warmtebehandelingsprocessen zoals afschrikken, ontlaten en oppervlakteharden worden gebruikt om de eigenschappen van matrijsmaterialen te verbeteren. Deze behandelingen verbeteren de duurzaamheid, slijtvastheid en sterkte van matrijzen, zodat ze voldoen aan de eisen van hoogwaardige toepassingen.
Wat zijn de productieprocessen van kunststof extrusiemallen?
Bij de productie van kunststof extrusiematrijzen komen verschillende processen kijken die grondstoffen omzetten in functionele matrijzen voor kunststofextrusie. Hieronder vind je een gedetailleerd overzicht van deze processen, met zowel algemene stappen als specifieke overwegingen om de hoogste kwaliteit en prestaties te garanderen:
Stap 1: Ontwerp en engineering:
De ontwerp- en engineeringfase is de eerste stap in de productie van matrijzen voor kunststofextrusie. Er worden gedetailleerde ontwerpen gemaakt met CAD-software (Computer-Aided Design) en er worden simulaties uitgevoerd om er zeker van te zijn dat de matrijs aan de productspecificaties kan voldoen en de materiaalstroom en thermische spanningen aankan. Tijdens deze fase wordt onder andere rekening gehouden met het type kunststof, de viscositeit, productafmetingen, toleranties en compatibiliteit met de extrusiemachine. Het uiteindelijke ontwerp moet defecten minimaliseren en het productieproces optimaliseren, zodat de productie efficiënt en soepel verloopt.
Stap 2: Materiaalkeuze:
Het kiezen van het juiste materiaal voor de matrijs is cruciaal om duurzaamheid, slijtvastheid en het vermogen om de hoge druk en temperaturen tijdens extrusie te weerstaan, te garanderen. Veelgebruikte materialen zijn gereedschapsstaal zoals P20, H13 of roestvrij staal. Bij het kiezen van materialen moet rekening worden gehouden met factoren zoals de bedrijfstemperatuur en -druk, het type kunststof dat wordt gebruikt en de balans tussen kosten en prestaties. Hoogwaardige materialen zorgen voor een lange levensduur en stabiliteit van de matrijs onder veeleisende omstandigheden.
Stap 3: Bewerking:
Nadat het ontwerp en de materiaalselectie zijn afgerond, komt de matrijs in de bewerkingsfase. Er worden zeer nauwkeurige bewerkingstechnieken, zoals CNC frezen, draaien, boren en EDM (Electrical Discharge Machining) gebruikt om de onderdelen van de mal te maken. Deze methoden zorgen ervoor dat de matrijs voldoet aan de eisen voor maatnauwkeurigheid, waarbij EDM vooral nuttig is voor ingewikkelde details. Het is essentieel om een glad oppervlak te verkrijgen om de plastic hechting tijdens extrusie te minimaliseren en een efficiënte productie te garanderen.
Stap 4: Warmtebehandeling:
Warmtebehandeling is een cruciale stap om de sterkte en slijtvastheid van de matrijs te verbeteren. Veel voorkomende warmtebehandelingen zijn afschrikken, ontlaten en nitreren, die de hardheid van de matrijs verbeteren en hem bestand maken tegen hoge druk en temperaturen tijdens het extrusieproces. Het is essentieel om een evenwicht te vinden tussen hardheid en taaiheid om broosheid te voorkomen. Het minimaliseren van vervorming tijdens het behandelingsproces is de sleutel tot het behouden van de precisie van de mal.
Stap 5: Polijsten en afwerken:
Na de warmtebehandeling wordt de mal gepolijst en afgewerkt. Interne oppervlakken worden gepolijst om de plastic stroom en de kwaliteit van het productoppervlak te verbeteren. Coatings zoals chroom of nikkel kunnen ook worden aangebracht om de weerstand tegen corrosie en slijtage te verbeteren. De gladheid van het oppervlak van de matrijs heeft een directe invloed op de prestaties en de levensduur, terwijl de coating corrosie en slijtage helpt voorkomen, zodat de matrijs gedurende de hele levenscyclus duurzaam blijft.
Stap 6: Montage:
Als alle onderdelen zijn bewerkt en afgewerkt, wordt de mal zorgvuldig geassembleerd. Dit omvat het uitlijnen van matrijsholten, inzetstukken en andere onderdelen om ervoor te zorgen dat alles goed in elkaar past. Bevestigingen en afdichtingen worden aangebracht om ervoor te zorgen dat de mal lekvrij is en de integriteit van de stromingstrajecten tijdens de extrusie behoudt. Het is belangrijk om tijdens de assemblage strakke toleranties aan te houden om problemen tijdens de productie te voorkomen en ervoor te zorgen dat de matrijs onder operationele omstandigheden goed functioneert.
Stap 7: Testen en valideren:
Na assemblage wordt de matrijs getest onder werkelijke extrusieomstandigheden met voorbeeldmaterialen. Het doel van het testen is om eventuele problemen te identificeren, zoals ongelijkmatige vloei, lekken of onnauwkeurigheden in de afmetingen. Als er problemen worden ontdekt, worden het matrijsontwerp of de procesparameters aangepast om ze op te lossen. Door rigoureus testen en verfijnen wordt de matrijs gevalideerd om te voldoen aan de productievereisten, waardoor een consistente en hoogwaardige productie wordt gegarandeerd.
Stap 8: Onderhoud en documentatie:
Om ervoor te zorgen dat de mal na verloop van tijd betrouwbaar presteert, wordt een onderhoudsschema opgesteld. Regelmatige reiniging, smering en inspecties zijn essentieel en versleten onderdelen moeten onmiddellijk worden vervangen. Gedetailleerde documentatie van ontwerpbestanden, bewerkingsparameters en onderhoudsgegevens wordt ook bijgehouden voor toekomstig gebruik. Goede onderhoudspraktijken helpen de stilstandtijd te minimaliseren en de levensduur van de matrijs te verlengen, waardoor een langdurige, efficiënte productie wordt gegarandeerd.
Hoe worden extrusiemallen gebruikt in verschillende sectoren?
Extrusiemallen zijn een veelzijdig en essentieel hulpmiddel in veel industrieën voor het maken van een breed scala aan producten. Door materialen door een matrijs te persen, maken extrusiemallen de efficiënte en continue productie van artikelen met complexe doorsnedeprofielen mogelijk. Hieronder wordt gedetailleerd beschreven hoe extrusiemallen in verschillende sectoren worden gebruikt.
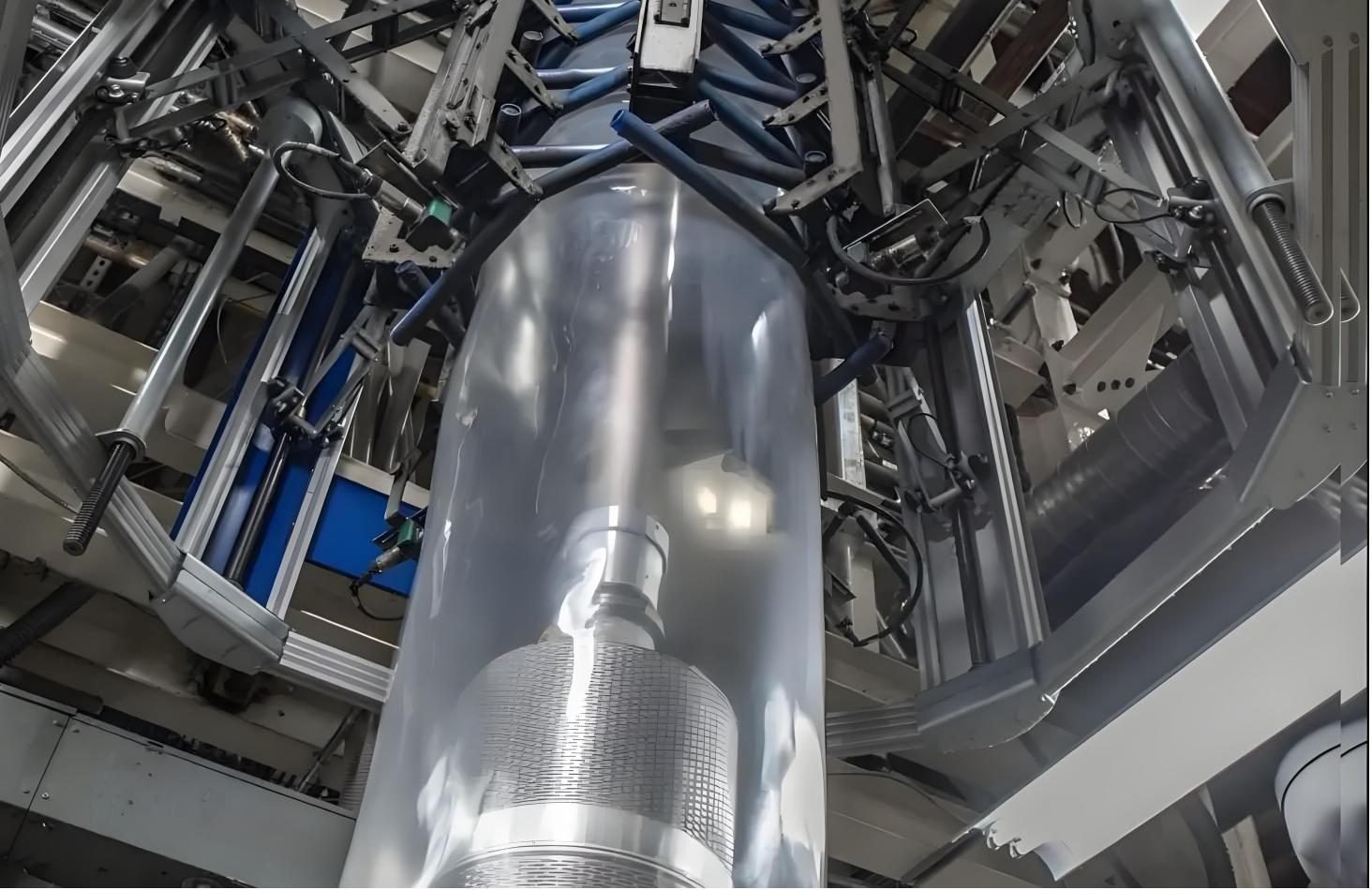
1. Verpakkingsindustrie:
In de verpakkingsindustrie worden extrusiemallen gebruikt om verschillende kunststof verpakkingsmaterialen te produceren, waaronder flessen, verpakkingen en tubes voor voedsel, dranken en persoonlijke verzorgingsproducten. Gangbare materialen zijn polyethyleen (PE), polypropyleen (PP) en PET, die ideaal zijn voor het maken van lichtgewicht, flexibele en kosteneffectieve verpakkingsoplossingen. Het extrusieproces garandeert de productie van grote volumes met een minimum aan afval, wat tegemoet komt aan de vraag van de industrie naar in massa geproduceerde artikelen met een consistente kwaliteit.
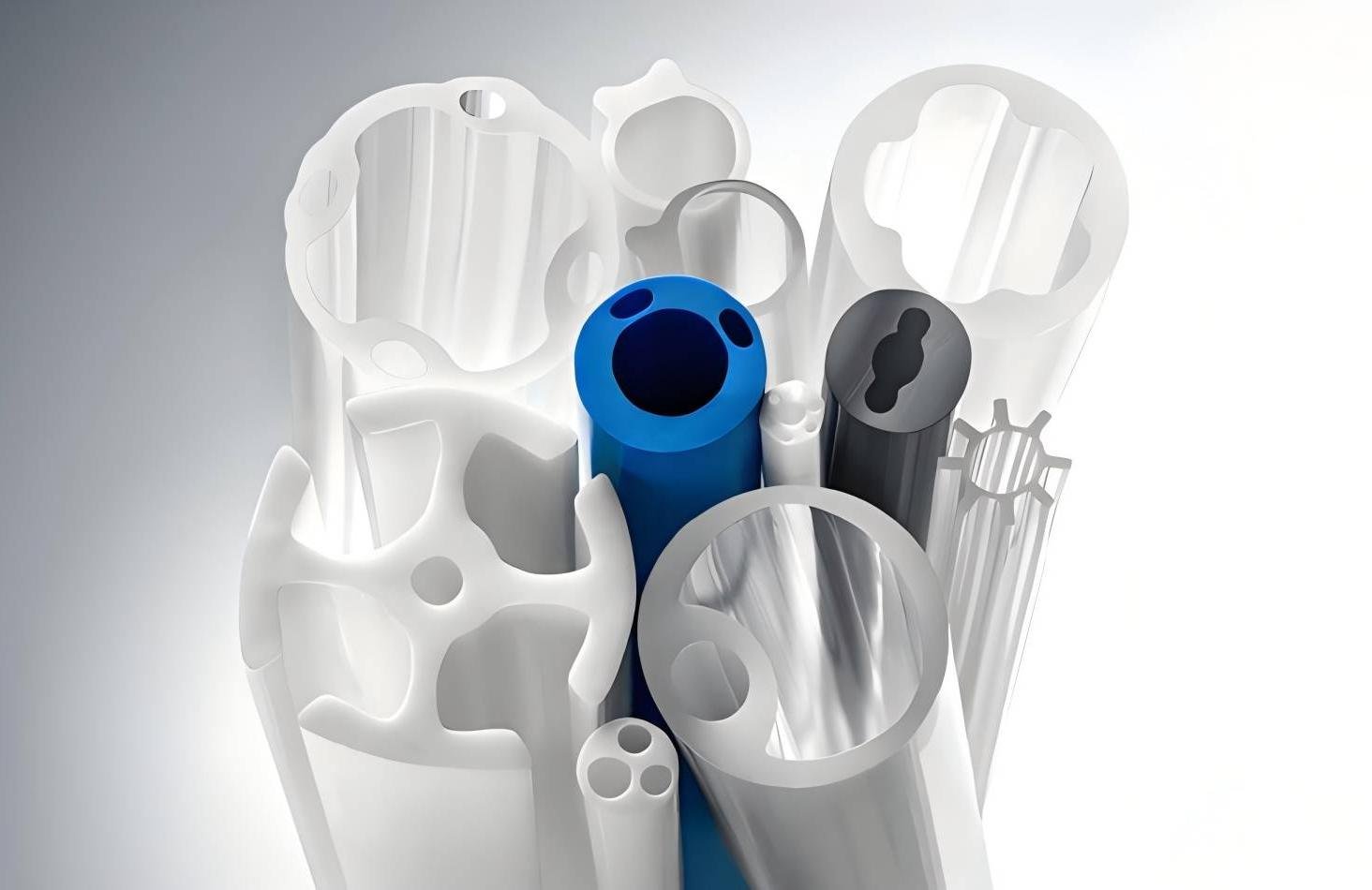
2. Medische industrie:
Extrusiemallen zijn essentieel in de medische industrie voor de productie van hulpmiddelen zoals katheters, voerdraden, chirurgische slangen en implanteerbare hulpmiddelen. Materialen zoals PVC, polyethyleen (PE) en polypropyleen (PP) worden vaak gebruikt vanwege hun biocompatibiliteit en duurzaamheid. De precisie van extrusie zorgt ervoor dat medische componenten voldoen aan de strenge wettelijke normen voor veiligheid, hygiëne en prestaties, waardoor ze cruciaal zijn voor de productie van betrouwbare medische producten van hoge kwaliteit.
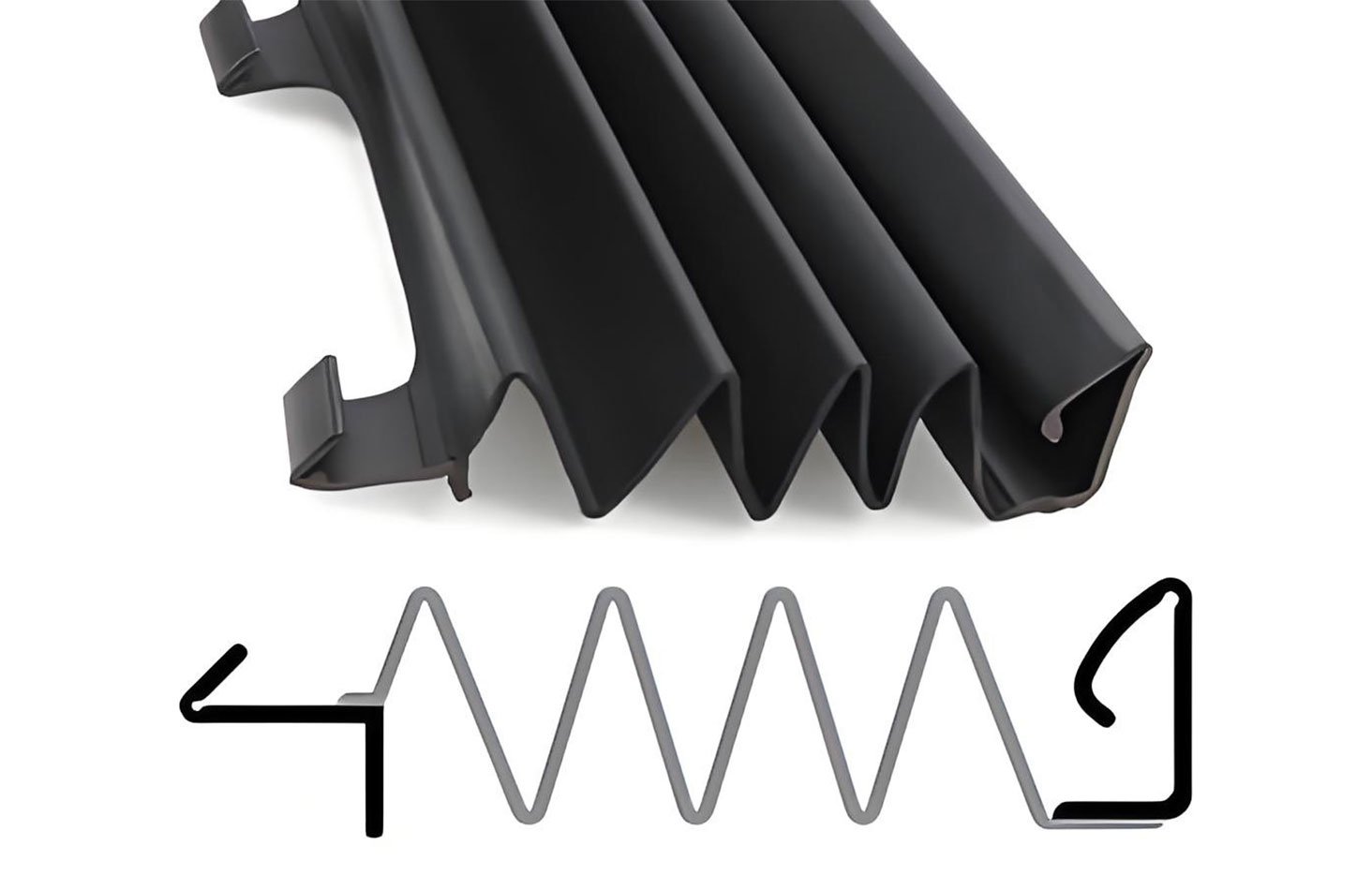
3. Auto-industrie:
In de automobielsector worden extrusiemallen gebruikt om lichtgewicht maar duurzame onderdelen te maken, zoals brandstofleidingen, remleidingen, luchtkanalen, raamkozijnen en afdichtingen. De gebruikte materialen zijn aluminium, PVC en verschillende thermoplasten. Deze materialen zijn sterk bij een laag gewicht, wat de prestaties en brandstofefficiëntie van voertuigen verbetert. Het extrusieproces maakt de productie mogelijk van onderdelen met ingewikkelde vormen en profielen, essentieel voor moderne auto-ontwerpen.
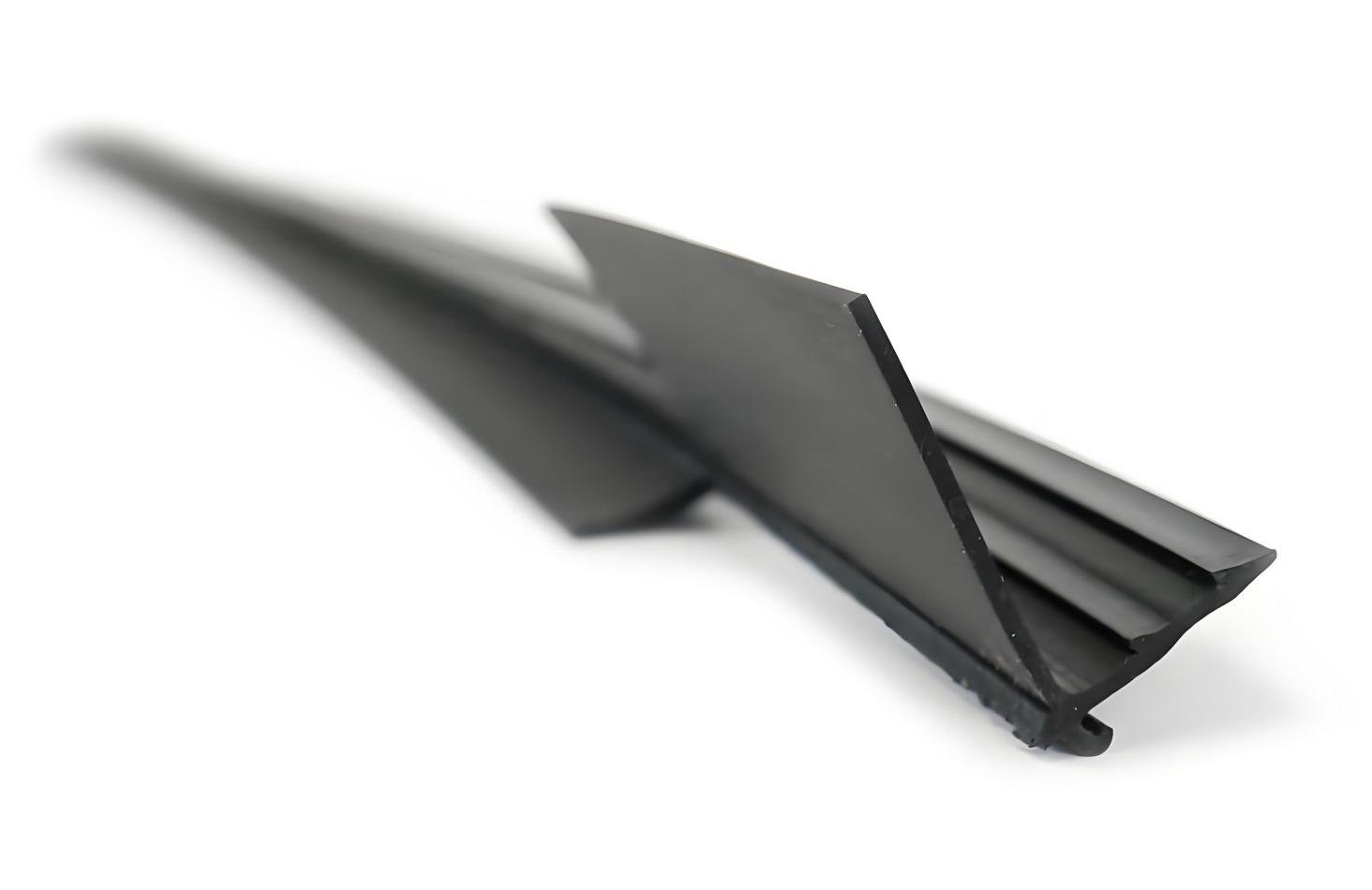
4. Lucht- en ruimtevaartindustrie:
Extrusiematrijzen in de luchtvaartindustrie worden gebruikt om lichtgewicht componenten met hoge sterkte te maken, zoals brandstofleidingen, hydraulische leidingen en structurele elementen. Materialen zoals aluminium, titaniumlegeringen en gespecialiseerde polymeren worden gebruikt om te voldoen aan de strenge prestatievereisten van luchtvaarttoepassingen. De precisie en betrouwbaarheid van het extrusieproces zorgen ervoor dat ruimtevaartonderdelen zowel licht als duurzaam zijn, wat bijdraagt aan een verbeterde efficiëntie en veiligheid bij het ontwerpen van vliegtuigen.

5. Consumentengoederenindustrie:
Extrusiemallen worden veel gebruikt in de consumptiegoederenindustrie voor de productie van alledaagse producten zoals speelgoed, huishoudelijke artikelen, meubelonderdelen en verpakkingsfolie. Meestal worden materialen als PVC, PET en polystyreen (PS) gebruikt, die een balans bieden tussen duurzaamheid, flexibiliteit en kosteneffectiviteit. Het extrusieproces maakt massaproductie mogelijk van lichtgewicht, duurzame en esthetisch diverse consumptiegoederen, waarmee tegemoet wordt gekomen aan de grote vraag naar consistente kwaliteit en design.
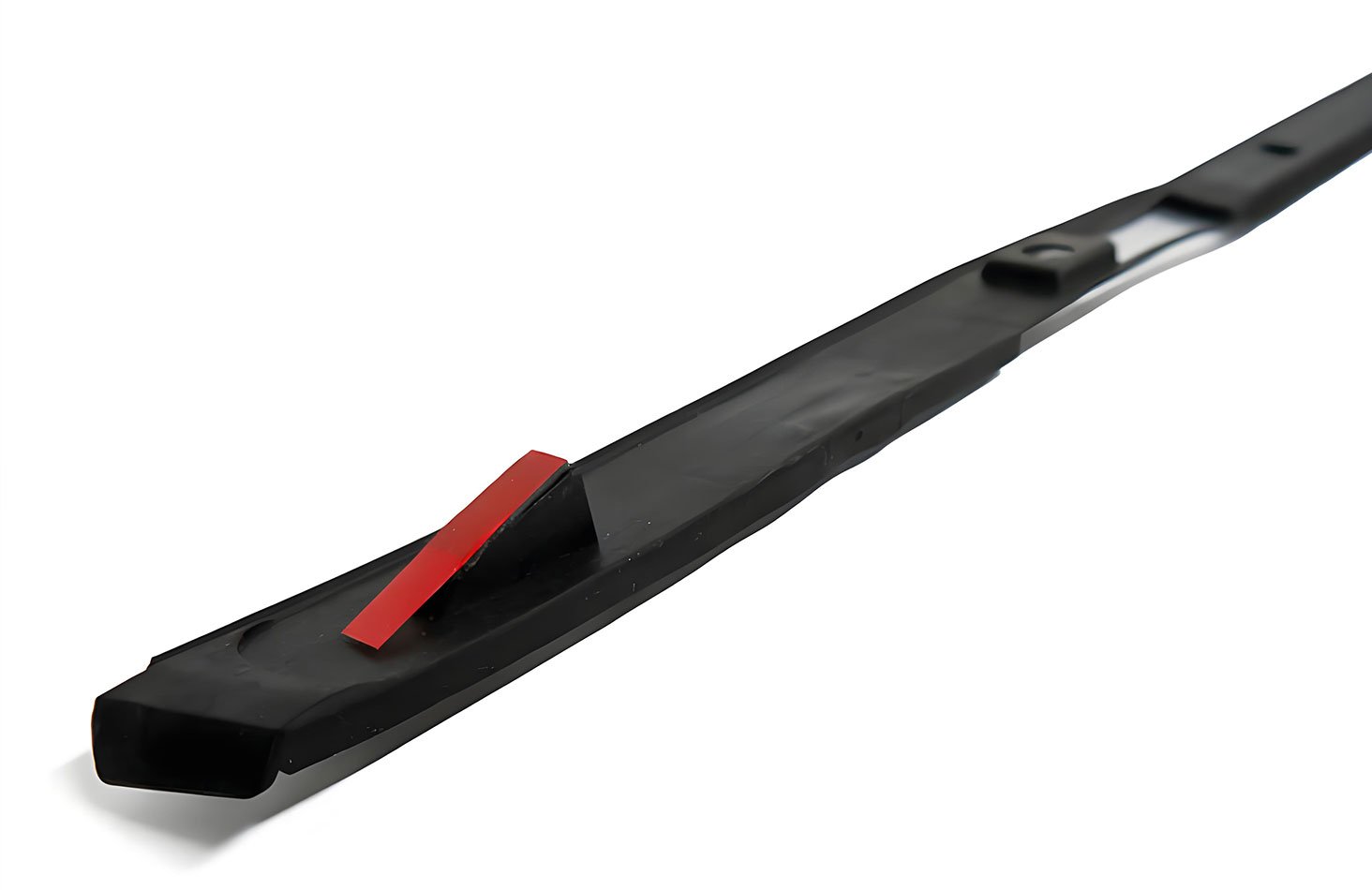
6. Textielindustrie:
In textiel creëren extrusiemallen synthetische vezels, garens en stoffen die worden gebruikt in kleding, bekleding en industrieel textiel. Materialen zoals polyethyleentereftalaat (PET), nylon en acryl worden vaak gebruikt vanwege hun sterkte, flexibiliteit en vermogen om tot fijne draden te worden gesponnen. Het extrusieproces zorgt voor een continue productie van vezels en stoffen, die geweven of gebreid kunnen worden tot veelzijdige en duurzame textielproducten.
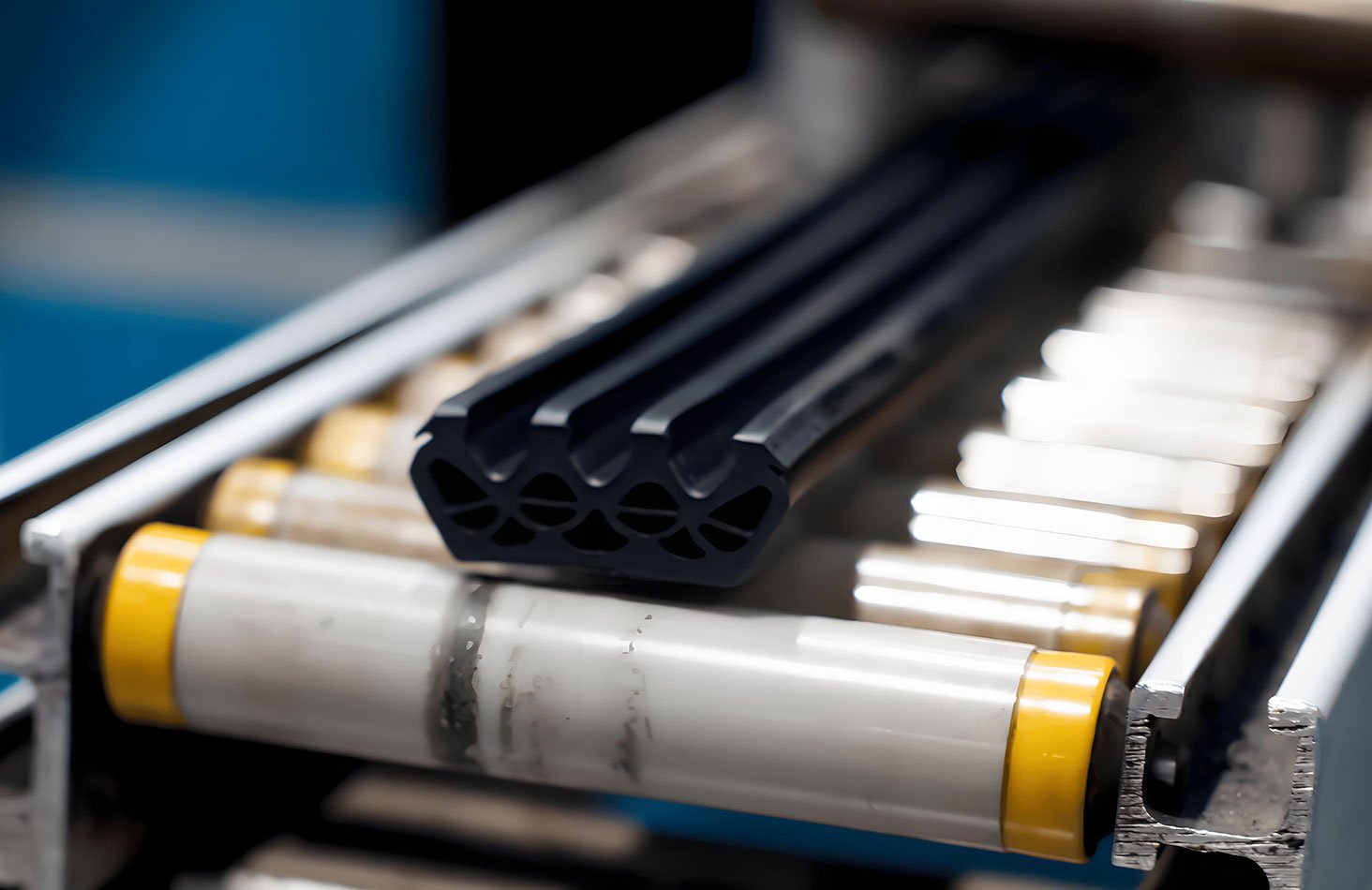
7. Mariene industrie:
In de scheepvaartindustrie worden extrusiemallen gebruikt om onderdelen te maken zoals sanitair, ventilatiesystemen en structurele onderdelen voor boten en schepen. Materialen zoals corrosiebestendig aluminium worden vaak gebruikt om het ruwe maritieme milieu te weerstaan. Het extrusieproces biedt een duurzame, lichtgewicht oplossing voor het maken van onderdelen die moeten worden blootgesteld aan water en andere moeilijke omstandigheden.
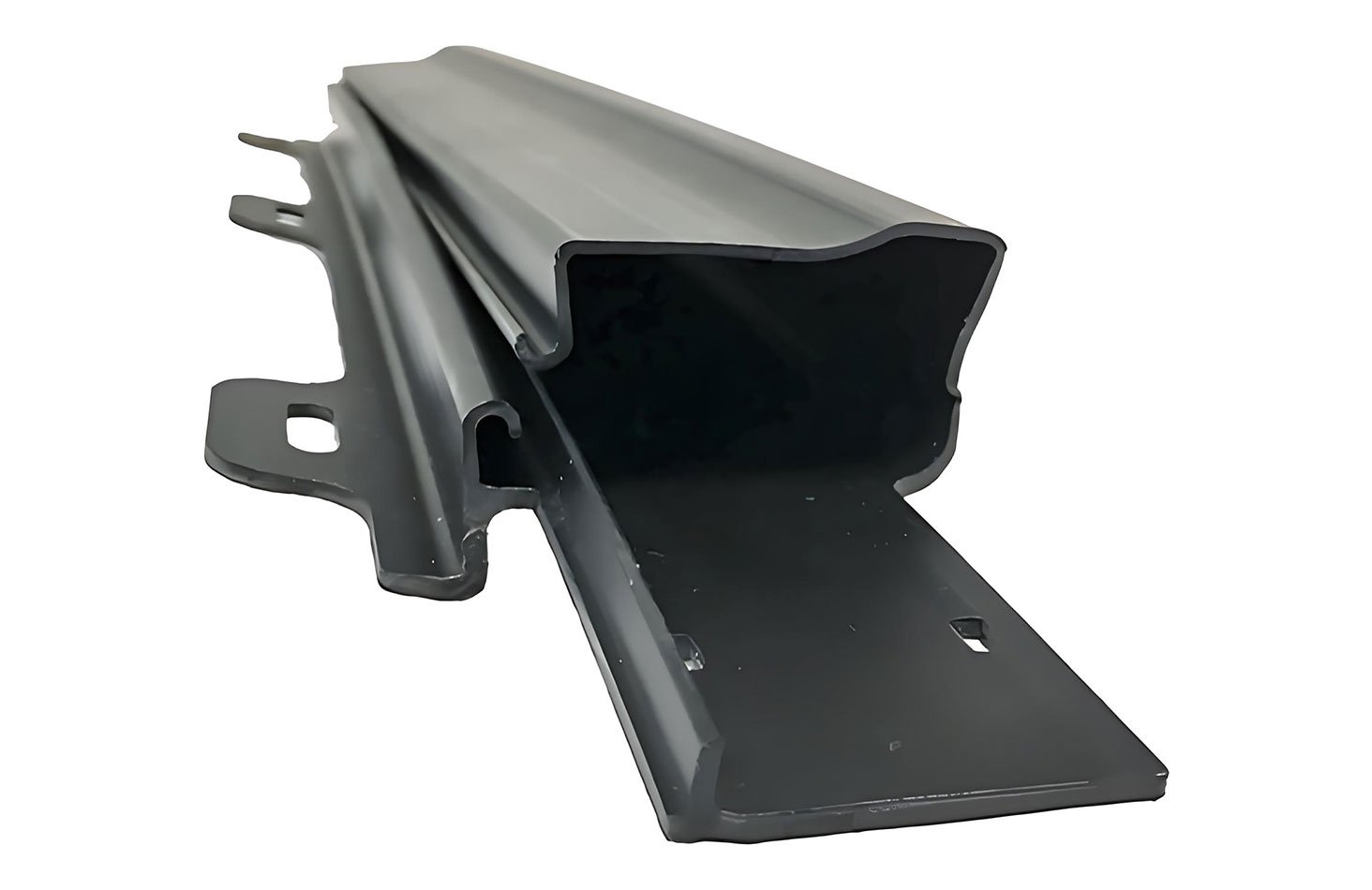
8. Bouwsector:
In de bouw worden extrusiemallen gebruikt om materialen te produceren zoals buizen, raamkozijnen, deurkozijnen en structurele onderdelen zoals balken en kanalen. Veelgebruikte materialen zijn PVC, aluminium en staal. Het extrusieproces maakt de productie mogelijk van lange, doorlopende secties met aangepaste profielen, waardoor het ideaal is voor het maken van bouwonderdelen die zowel sterk als duurzaam moeten zijn, en voor het minimaliseren van materiaalafval tijdens de productie.
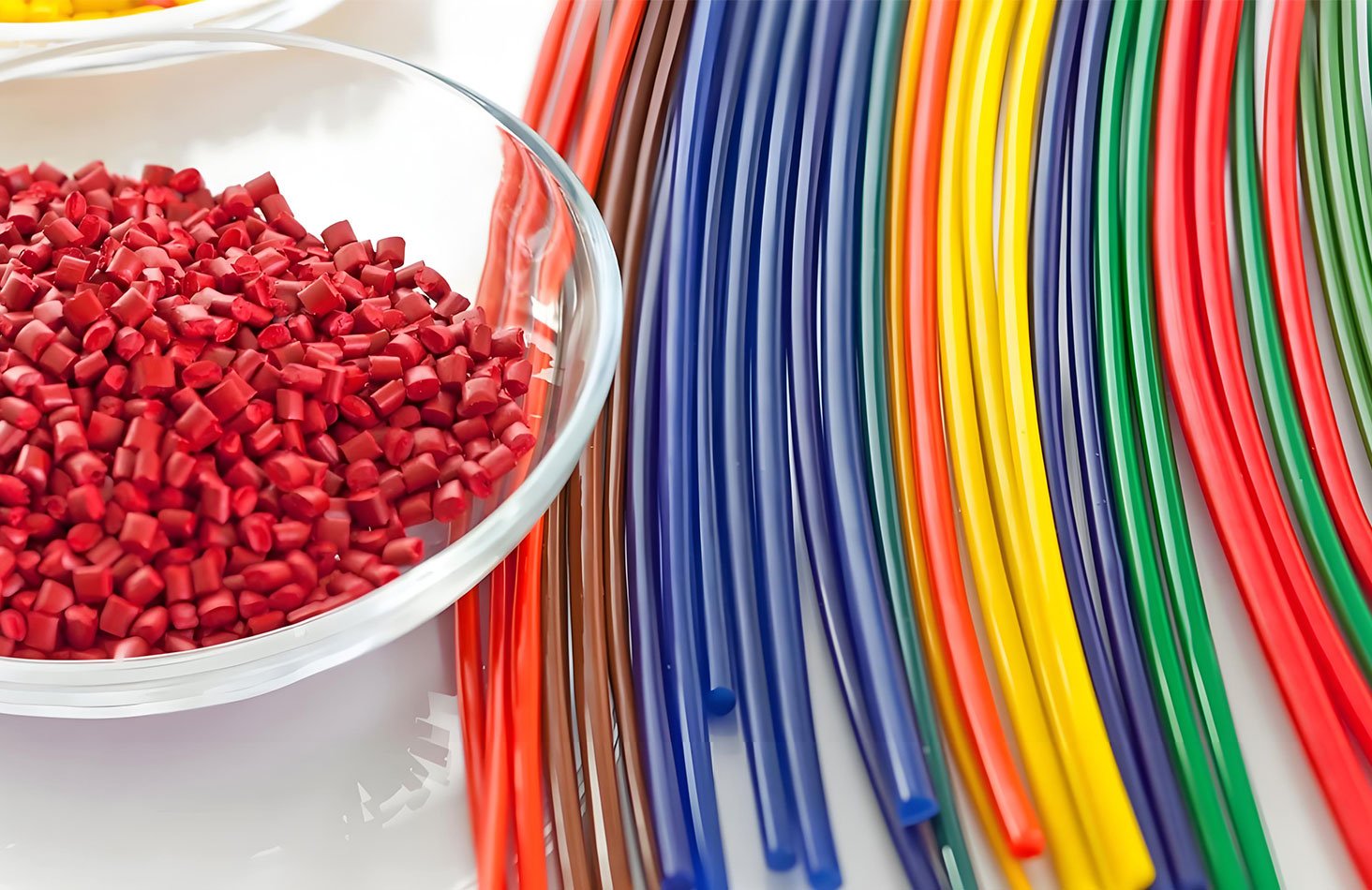
9. Elektrische en elektronische industrie:
Extrusiemallen spelen een cruciale rol in de elektrische en elektronische industrie, waar ze worden gebruikt om onderdelen te maken zoals koellichamen, draadisolatie, kabelmantels en behuizingen voor elektronische apparaten. Materialen zoals thermoplasten en aluminium worden vaak gebruikt om duurzaamheid, flexibiliteit en elektrische isolatie te garanderen. De precisie van extrusie zorgt ervoor dat deze componenten uniform worden geproduceerd en voldoen aan de vereiste specificaties voor prestaties en veiligheid in elektrische systemen.

10. Farmaceutische industrie:
In de farmaceutische industrie worden extrusiemallen gebruikt om producten als tabletomhulsels, capsules en spuiten te maken. De gebruikte materialen zijn thermoplasten zoals PVC, die de nodige eigenschappen hebben om producten van medische kwaliteit te maken. Het extrusieproces is essentieel om ervoor te zorgen dat farmaceutische componenten zeer nauwkeurig worden geproduceerd en voldoen aan strenge hygiëne- en veiligheidsnormen, zodat elk product betrouwbaar en veilig is voor medisch gebruik.
veelgestelde vragen voor klanten
Aan de slag met Uplastech
Heb je vragen? Wij hebben antwoorden.
We zijn gespecialiseerd in extrusieprocessen en het maken van precisiemallen en bieden oplossingen op maat om aan uw productiebehoeften te voldoen.
We werken met verschillende industrieën, waaronder de auto-industrie, elektronica en consumentengoederen, en richten ons op B2B-partnerschappen.
Ja, we passen onze oplossingen aan uw unieke vereisten aan.
Neem contact op
Stuur ons een e-mail of vul onderstaand formulier in voor een offerte.
E-mail: uplastech@gmail.com