プラスチック押出金型設計・製造
お客様のニーズに合わせた専門的なプラスチック押出成形金型の設計と製造サービスをご覧ください。弊社は様々な業界に高品質で耐久性のある金型を提供し、すべてのプロジェクトで精度と効率を保証します。今すぐご相談ください!
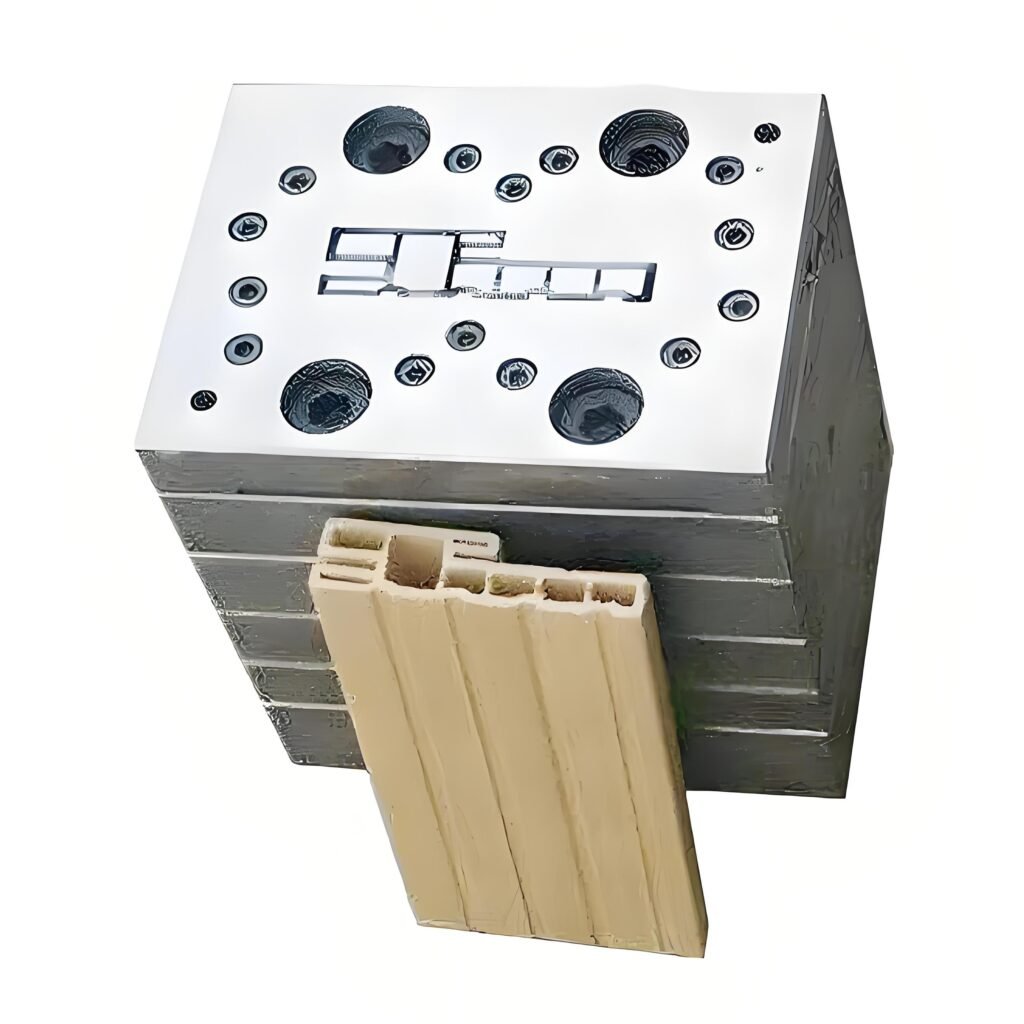
押出成形金型設計・製造完全ガイド
押出成形金型とその仕組みとは?
プラスチック押出成形用金型は、ダイスとも呼ばれ、プラスチック押出成形プロセスにおいて超重要である。プラスチック押出成形は、プラスチックから長い形状を作る方法です。パイプやシート、特注の形状などを作るのに使われます。建築、包装、自動車などに利用されている。
プラスチック押出成形金型とは?
プラスチック押出成形用金型は、溶融プラスチックを特定の断面形状に成形する金属製工具です。これらの金型は鋼鉄かアルミニウムからなされ、放出のプロセスの高温そして圧力を扱うことができる。
金型(ダイ)の設計は、押出製品の最終的な形状を決定するため、所望の寸法と品質を達成するための重要な要素となる。
プラスチック押出成形金型の構成部品
押出システムの有効性は、いくつかの重要な構成要素に依存する:
ホッパー原料を押出機に投入する。
スクリュー:スクリュー:回転し、バレル内のプラスチック材料を搬送・溶融する。
バレル:プラスチックを融点まで加熱し、溶融状態を維持する。
ダイ(押出成形用金型):押出機から出てきた溶融プラスチックを連続した形状に成形する。
冷却システム:押出材料の適切な凝固を確保する。
プーラーまたはコンベアシステム:冷却中の変形を防ぐため、一定の速度を保つ。
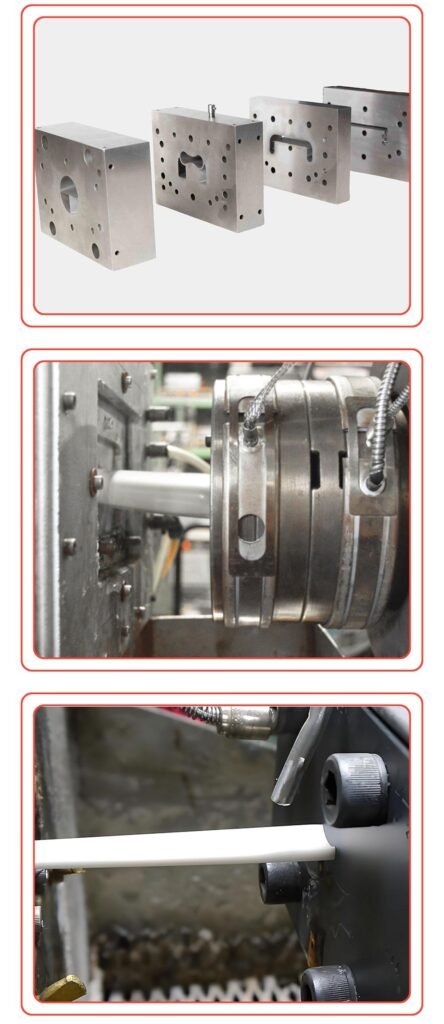
プラスチック押出成形金型の仕組み
プラスチック押出工程は、原料のプラスチックを加熱、成形、冷却することによって最終製品にする工程である。その仕組みはこうだ:
1.材料の供給:
原料プラスチックは、一般的にペレットや顆粒の形で、ホッパーに投入される。この段階で、色、強度、耐紫外線性などの特性を向上させるために、着色剤、安定剤、充填剤などの添加剤が混合されることがある。
2.溶ける:
その後、プラスチック材料は加熱されたバレルに供給され、回転するスクリューによって溶かされる。熱はスクリューの摩擦と外部ヒーターの両方で発生する。バレルの温度は、プラスチックの種類にもよるが、一般的に200~275℃に設定される。
3.シェーピング:
溶けたプラスチックは、押出成形用金型とも呼ばれるダイに押し込まれる。この金型によって、材料は希望の形状になる。押出成形は非常に柔軟性が高く、パイプ、シート、カスタムデザインなど、さまざまな形状にすることができます。
4.冷却:
プラスチックが金型から出ると、空気、水槽、冷却ロールによって急速に冷却される。この急速冷却プロセスにより、材料は固化し、意図した形状に固定されます。
5.カッティング:
冷却され固化した押出材は、次に必要な長さに切断される。用途に応じて、特定のサイズに切断したり、ロール状に巻いたりします。
6.仕上げ:
切断後、製品の用途や仕様に応じて、表面処理、トリミング、さらなる成形などの追加工程が行われることもある。
押出金型の種類とは?
プラスチック押出成形用金型には多くの種類があり、それぞれ特定の産業や製品のニーズに合わせて設計されています。これらの金型は、生のプラスチックを精密なプロファイル、シート、またはフィルムに成形するために重要です。ここでは、様々な種類のプラスチック押出成形用金型の概要を説明します:
1.シングルスクリュー金型:
シングルスクリューダイは、最も一般的な押出成形用金型です。パイプ、チューブ、プロファイルの製造に最適です。安価で、PVC、PE、PP、ABSなどさまざまなプラスチックの押出成形に使用できます。そのため、大量生産に適しています。
2.ツインスクリュー金型:
二軸スクリューダイは、2本のスクリューを使用して激しい混合と溶融を行うため、複雑な形状や充填材の多い製品の製造に適しています。これらのダイは、マルチルーメンチューブやカテーテルのような医療機器など、材料を厳密に制御したい用途でよく使用されます。
3.共押出ダイス:
共押出ダイは、複数のプラスチック層を同時に押出すように設計されています。これにより、バリア層や断熱材のような特殊な機能を持つ製品を作ることができます。これらの金型は、包装材料によく使用されます。融点や特性の異なるプラスチックを組み合わせることで、より効果的に機能させることができます。
4.マイクロ押し出しダイス
マイクロ押し出しダイスは、医療機器や電子機器のような小型で精密な部品を作るために設計されています。非常に精度の高い部品を作ることができ、PEEKやテフロンのような特殊プラスチックによく使用されます。非常に小さなサイズや形状の部品を作るのに最適です。
5.フラットフィルムとシート金型
平らなフィルムやシートの金型は、幅の広い薄いシートやフィルムを作ることができ、包装、ラミネート、熱成形によく使用されます。これらの金型は、調整可能な流路によって均一な厚みを実現し、PET、PE、PVCなどの素材に対応します。
6.ブローフィルムダイ
ブローフィルムダイは、空気で吹き上げるチューブ状フィルムの製造に使用される。ビニール袋やシュリンク、ストレッチフィルムなどを作るのに適しています。丸いので、フィルムの厚みが同じになります。LDPE、HDPE、PPを作ることができる。
7.パイプおよびチューブ金型
パイプ・チューブ用ダイスは、配管用パイプや医療用チューブのような中空円筒形プロファイルを製造するために作られます。ダイの隙間は調整可能で、肉厚を変えることができます。PVC、HDPE、PPなどの材料に対応します。
8.プロファイル押出ダイス
プロファイル押し出しダイスは、窓枠や自動車トリムなどの複雑な形状を作るために使用されます。複雑な断面の精密な金型を作るのが得意で、ABS、PVC、TPEなど、工業用や建築用の材料に適しています。
9.電線・ケーブル被覆金型
電線・ケーブル被覆用金型は、電線やケーブルを保護プラスチック層で覆い、電気配線や光ファイバーの絶縁を行うために使用されます。これらの金型は、PVCやXLPEのような高温材料を扱うように設計されており、滑らかで耐久性のある仕上げを保証します。
10.押出ブロー金型
押出ブロー金型は、溶融したプラスチックのパリソンを成形して吹き上げることで、ボトルや燃料タンクのような中空容器を作ります。PET、HDPE、PPを使用し、正確な温度制御により、壁の厚さを同じにすることができます。
11.環状ダイス:
環状ダイは、リングや中空チューブのような円形形状を作ります。ガスケットやシールなどに適しています。適切なサイズのものを作ります。ナイロンや強化PPのような強いプラスチックに適しています。
12.シートコーティング金型
シートコーティングダイは、ラミネートやコーティングの目的で薄いプラスチック層を塗布するために使用されます。装飾フィルムやバリア用途に使用されます。これらのダイは高精度で、TPU、EVA、PEなどの素材に対応しています。コーティングが均一で長持ちすることを保証します。
13.多層押出ダイス:
多層押出ダイは、複数の素材を1つの工程で組み合わせるために使用され、包装用フィルムや自動車用パネルなどの特性を向上させた製品を作り出します。これらのダイは、EVOH、ナイロン、PEなどの高度な材料を組み合わせることに優れており、特殊な用途でより優れた性能を発揮します。
押出金型設計ガイドライン
高品質なプラスチック製品を一貫して効率よく生産するためには、効果的な押出成形用金型の設計が不可欠です。以下に、押出金型設計のあらゆる側面を網羅する、統合された詳細なガイドラインを示します:
1.金型設計の原則:
一貫性と効率:金型が均一で一貫性のある製品を生産し、材料の無駄を最小限に抑え、生産のダウンタイムを削減します。
耐久性:耐久性:高温・高圧などの使用上のストレスに耐える設計により、長寿命と信頼性を確保。
2.材料の選択:
耐久性と耐性:耐摩耗性と熱安定性のために、硬化鋼やタングステンカーバイドのような高品質の材料を使用します。
耐腐食性:特にPVCのような腐食性の強いプラスチックの加工には、腐食環境に耐性のある材料を選択する。
3.金型形状と流路設計
流線型のデザイン:流路は対称的で滑らかであるべきで、淀み部分を避け、均一な材料分配を確保し、反りや不均一な厚みなどの欠陥を減らす。
段階的な移行:材料応力を最小化し、押出製品の欠陥を防止するために、ダイス形 状に緩やかな遷移を取り入れる。
4.土地の長さとクリアランス:
最適な土地の長さ:流れを安定させ、一定の寸法を確保するため、土地の長さは土地のクリアランスの約10倍を維持する。
均一な断面:均一な断面:押出材の厚みのばらつきを避けるため、ダイスの断面を一定に保つ必要がある。
5.ダイギャップの調整:
調整可能な設計:調整可能なギャップを組み込むことで、運転中に材料の厚さを微調整でき、さまざまな粘度や生産要件に対応できます。
6.熱管理と冷却システム
温度制御:均一な加熱・冷却ゾーンにより、熱勾配や反りを防ぎ、製品の完全性を維持。
統合冷却:ダイの温度を安定させ、過熱を防ぐために、水冷または空冷システムを使用する。
7.換気システム:
エア抜き:ベント・チャンネルを追加することで、閉じ込められた空気を排除し、滑らかな表面仕上げを確保し、ボイドやエアポケットなどの欠陥を防ぐ。
8.表面仕上げとコーティング:
滑らかな内面:表面処理(クロムメッキや窒化物コーティングなど)を施し、鏡面仕上げにすることで、摩擦を減らし、材料の流れを良くし、金型の寿命を延ばします。
9.モジュール式でメンテナンスしやすい設計:
メンテナンスの容易さ:分解、清掃、部品交換が容易なモジュール設計を採用し、ダウンタイムを最小限に抑えます。
耐久性のある部品:交換可能な磨耗部品を使用し、長期的なメンテナンスコストを削減。
10.シミュレーションとテスト:
CFDシミュレーション:高度なシミュレーションソフトウェアを使用して、流れのパターンを解析し、形状を最適化し、性能を予測します。
試作品テスト:試作品テスト:本格的な生産に入る前に、潜在的な問題を特定し、修正するための徹底的なテストを実施する。
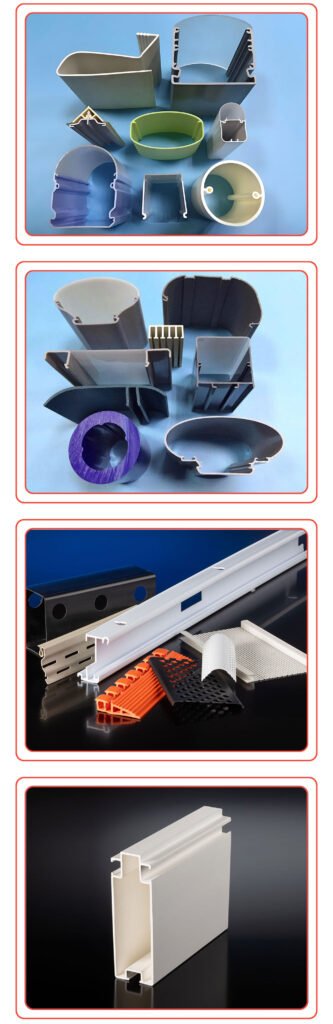
11.ダイ・アライメント:
精密アライメント:ダイ、押出機、および下流装置の間で適切なアライメントを確保し、材料の無駄、不均一な流れ、および製品の欠陥を回避します。
12.製造可能な設計:
シンプルな設計:組立や校正を複雑にする複雑すぎる形状は避ける。シンプルな設計は製造性と信頼性を向上させます。
適合と統合:シームレスな統合を保証するために、他のコンポーネントとの互換性をカスタム押出テストを行います。
13.クリーニングとメンテナンスに関する注意事項:
簡単な洗浄システム:残留物を除去し、汚染を防ぐために、アクセス可能な洗浄機構を含むように金型を設計する。
定期メンテナンス:金型の最適な性能と製品品質を確保するため、定期的な点検と清掃のスケジュールを設定します。
14.アドバンスト・デザイン・プラクティス
明確なデザイン哲学:シンプルさ、効率性、無駄の最小化に重点を置く。
ソフトウェアの活用:ソフトウェアの活用:特定の製品要件に対応し、さまざまな条件下での性能をシミュレートするために、専用のソフトウェアを活用する。
押出成形金型によく使われる材料とは?
押出成形は、熱可塑性プラスチック製品を作るための多用途な製造工程である。この工程で使用される金型材料は、最終製品の出来栄えを左右する大きな役割を果たします。ここでは、プラスチック押出成形用金型に使用される最も一般的な材料の概要と、用途に最適な材料を選ぶ際に考えなければならないことを説明します。
1.スチール:
スチールは押出成形用金型に最も広く使用されている材料で、その卓越した強度、耐久性、耐摩耗性で知られています。高品質の冷間工具鋼は優れた硬度を持ち、大量生産金型に最適です。一方、熱間工具鋼は極端な温度にも耐えることができるため、熱応力のかかる環境でも長持ちします。合金工具鋼は、靭性、耐摩耗性、機械加工性のバランスが取れており、PVC、HDPE、ABS用の金型を含む様々な用途に汎用性があります。
2.アルミニウム合金:
アルミニウム合金は軽量で費用対効果の高い選択肢であり、試作品や短納期生産に広く使用されています。その優れた熱伝導性は、冷却時間の短縮と効率の向上に役立ちます。アルミニウムは鋼鉄よりも機械加工が容易ですが、硬度と耐摩耗性が低いため、低応力用途に限定されます。単純な形状の金型や少量生産に最適です。
3.銅および銅合金:
銅とその合金、特にベリリウム銅は、その優れた熱伝導性と耐食性が評価されています。これらの素材は、正確な温度管理が必要な金型に特に効果的で、複雑な押出成形プロファイルの反りや欠陥を防ぐのに役立ちます。銅ベースの金型は、高品質な仕上げと一貫した温度管理が要求される用途でよく使用されます。
4.チタン合金:
チタン合金は、その驚異的な強度対重量比と優れた耐食性で知られています。特に高精度の金型や、厳しい公差が要求される特殊な用途に適しています。また、チタンは軽量であるため、医療や航空宇宙製造などの産業で使用される金型にも適しています。
5.セラミック材料:
セラミック材料は、その卓越した硬度と高温に対する耐性から選ばれます。これらの特性は、高圧または高温用途のような極限状態で使用される金型に理想的です。しかし、セラミックは脆いため、機械的な耐衝撃性を必要とする用途では使用が制限されることがあります。
6.プラスチックと複合材料
軽量構造や耐薬品性が要求される場合、特殊なプラスチックや複合材料が金型材料として使用されることがある。PTFE(テフロン)は、その非粘着性の特性からしばしば選択され、生産量の少ない用途での脱型を容易にします。これらの材料はコスト効率が高く、特定の使用例に対して独自の利点をもたらしますが、一般的には低応力環境に限定されます。
7.黄銅およびその他の銅合金:
銅と亜鉛の合金である真鍮は、その加工性と耐食性からよく選ばれている。真鍮は高品質の表面仕上げを実現し、低~中程度の生産量で使用される金型に適しています。その精度と手頃な価格の組み合わせは、特定の用途にとって魅力的な選択肢となります。
8.ガラスとシリコーン:
ガラスとシリコーンは、高度な精度、柔軟性、または独特の表面仕上げを必要とするニッチな用途に使用される特殊な材料です。シリコーン型は複雑なデザインに理想的で、優れた柔軟性を提供します。一方、ガラス型は優れた寸法精度を提供しますが、コストが高く壊れやすいため、広く使用されるには限界があります。
金型材料を選択する際に考慮すべき要素
生産量:
大量生産の金型には、耐久性のために工具鋼のような材料が必要だが、少量生産ではアルミニウムや複合材料を利用することができる。
熱性能:
アルミニウムや銅合金のような素材は熱伝導率が高く、効率的な冷却サイクルを確保できるため好まれる。
表面仕上げ:
真鍮やステンレススチールは高品質な仕上げに優れ、セラミックは精密な仕上げに最適です。
耐食性:
ステンレス鋼、チタン、銅合金は腐食に強く、医療用や食品用の用途には不可欠です。
コストとメンテナンス:
アルミニウムはプロトタイピングに費用対効果が高く、プリハードン鋼は耐久性のある量産金型の加工時間とコストを削減します。
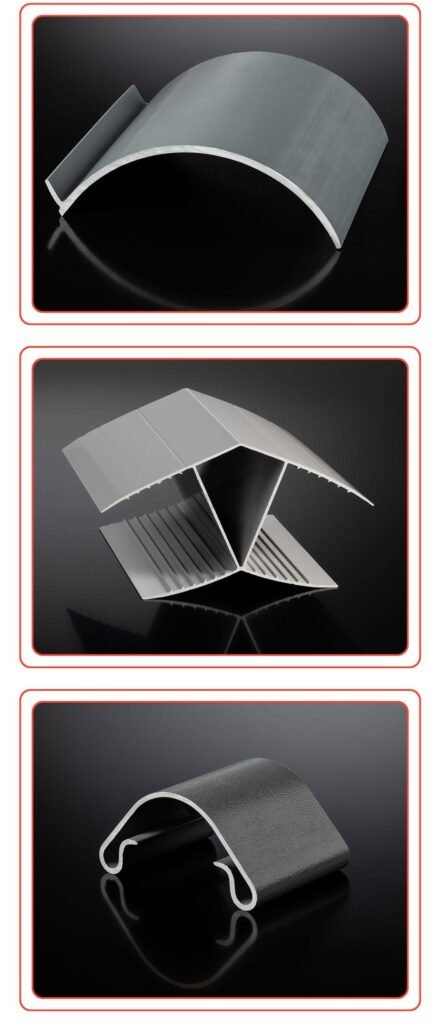
金型材料の特性は金型設計にどう影響するか?
金型材料の特性は、射出成形や押出成形で使用される金型の設計、性能、寿命の基本です。熱管理、耐久性、製品品質、製造効率などの要素に影響を与えます。ここでは、これらの特性が金型設計にどのような影響を与えるかについて、包括的なガイドを示します:
1.熱伝導率:
衝撃:熱伝導率の高い材料(アルミニウム、銅など)は効率よく熱を放散するため、冷却時間が短縮され、成形部品の反りや歪みなどの問題を防ぐことができる。逆に、熱伝導率の低い鋼鉄のような材料は、追加の冷却システムを必要とする場合がある。
設計上の考慮点:設計上の考慮点:金型には、スピードと均一な冷却を優先して導電性の高い素材を使用するが、耐久性のために構造補強とのバランスをとる。
2.熱膨張:
影響:熱膨張率のばらつきは、温度変化時の寸法の不正確さにつながる。スチールやセラミックのような熱膨張率の低い材料は、寸法安定性が高い。
設計上の考慮点:設計上の考慮点: 高温プロセスや厳しい公差では、精度を維持するため に膨張の少ない材料を選択する。
3.強度と耐久性:
衝撃:高強度材料(硬化鋼、チタンなど)は、射出成形や押出成形の高圧・高温に耐えます。これらの材料は変形しにくく、長期の生産サイクルにわたって安定した部品品質を保証します。
設計上の考慮点:複雑な形状の金型や大量生産の金型には、耐久性のある素材を使用する。強度と加工性のバランスから、P20やH13のような工具鋼を検討する。
4.耐摩耗性:
衝撃:継続的な使用や研磨材は金型表面を劣化させます。耐摩耗性材料はメンテナンス頻度を減らし、金型寿命を延ばします。
設計上の考慮点:設計上の考慮点:研磨材入りプラスチックやガラス繊維入りプラスチックの成形には、コーティング(窒化処理、クロムメッキなど)や硬い材料を選択する。
5.耐食性:
影響:湿気、化学薬品、プラスチックに含まれる腐食性添加物などにさらされると、金型が劣化し、製品の品質に影響を与えることがあります。ステンレス鋼やコーティングされた金型は耐性を向上させる。
設計上の考慮点:設計上の留意点:反応環境にさらされる金型には耐腐食性材料を使用するか、長寿命化のために表面保護処理を施す。
6.機械加工性:
衝撃:アルミニウムのような加工しやすい材料は、生産時間とコストを削減するが、鋼やチタンの耐久性に欠ける可能性がある。
設計上の考慮点:設計上の考慮点:試作金型や少量生産の場合、機械加工が可能な材 料は時間を節約できる。量産金型では、耐久性のある材料の高い加工コストを正当化できるかもしれない。
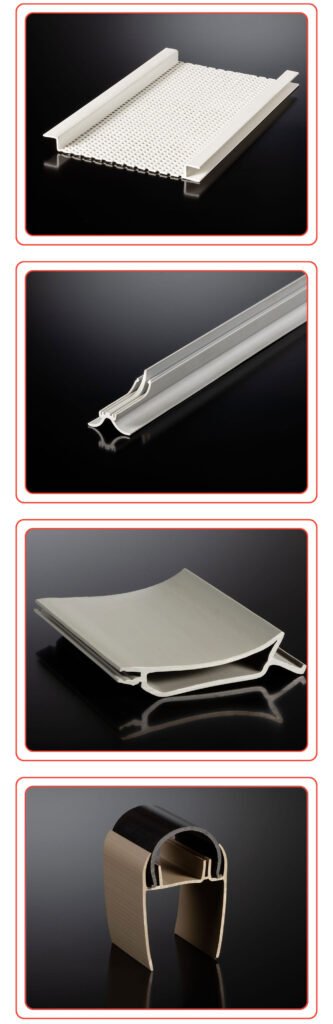
7.表面仕上げ:
影響:金型の表面品質は、最終製品の美観と離型のしやすさに影響する。高品質な仕上げは、不良を最小限に抑え、サイクルタイムを短縮する。
設計上の考慮点:設計上の考慮点:美観や機能面で重要な要件がある部 品には、工具鋼のように滑らかな仕上げが可能な材 料を選択する。
8.耐薬品性:
衝撃:ある種のプラスチックや添加剤は金型表面を劣化させる。ステンレスやチタンのような素材は、化学物質への暴露に耐え、金型の完全性を保ちます。
設計上の考慮点:設計上の考慮点:化学的侵食性の高い樹脂を使用する金型は、耐性のある材料や保護コ ーティングを優先すること。
9.コスト
インパクト:硬化鋼やチタンのような高級素材は、初期費用は増加するが、長期的なメンテナンスと交換費用を削減する。
設計上の考慮点:設計上の考慮点:材料費と予想される生産量および運用上の要求とのバランスをとり、投資対効果を最適化する。
プラスチック押出成形金型の製造技術
プラスチック押出成形用金型は、押出成形用金型とも呼ばれ、所望の形状、サイズ、機能を実現するために、さまざまな技術を駆使して作られます。以下は、最も一般的に使用される製造技術の包括的な概要であり、理解を深めるために重要な詳細を組み合わせています:
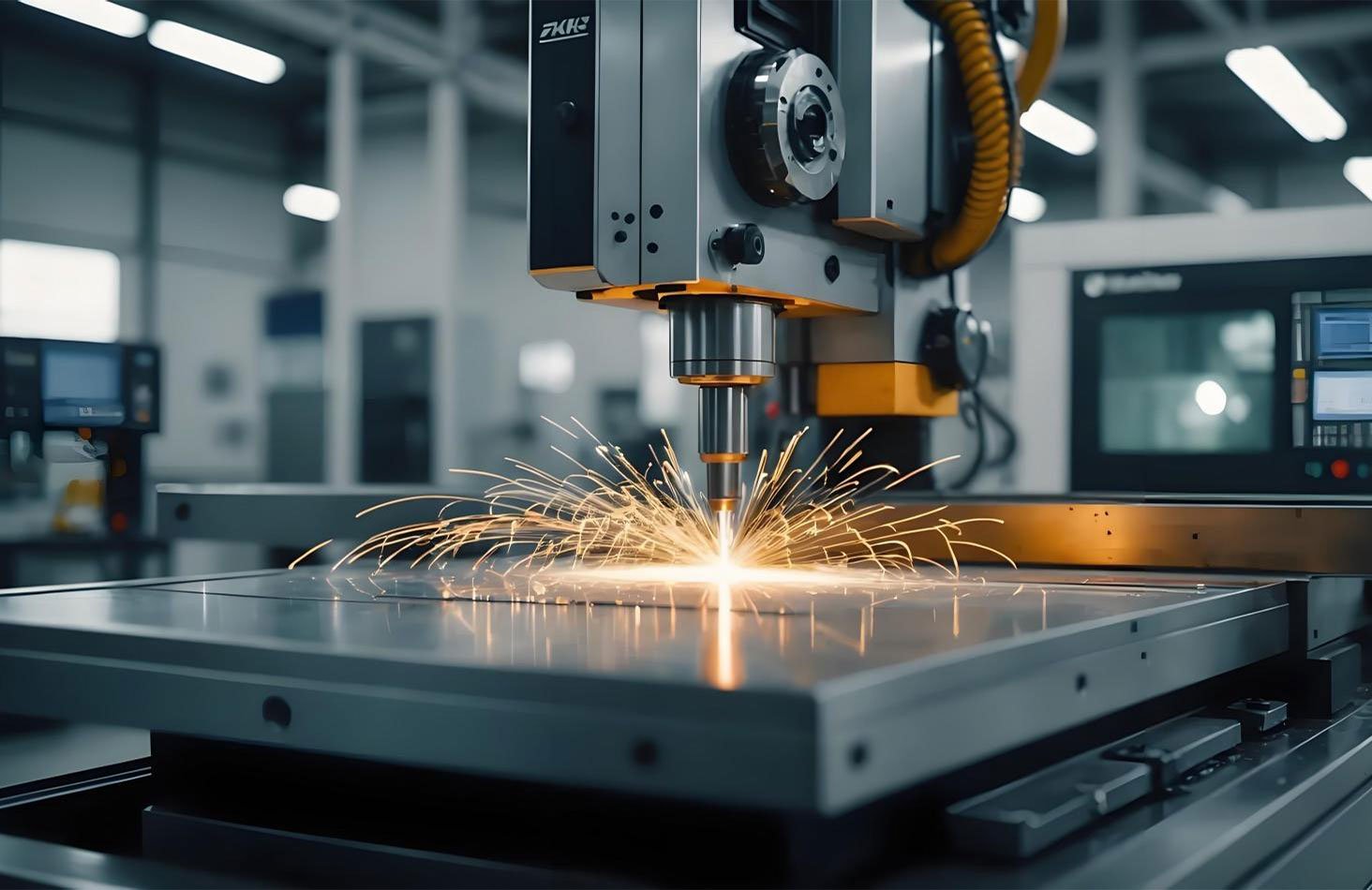
1.CNC加工:
CNCマシニングは、コンピューター制御の切削工具を使用して、スチールやアルミニウムなどの金型材料を精密に成形します。精度が高く、厳しい公差を実現できるため、精密で一貫性のある一次金型部品や外形形状を作成するのに理想的です。
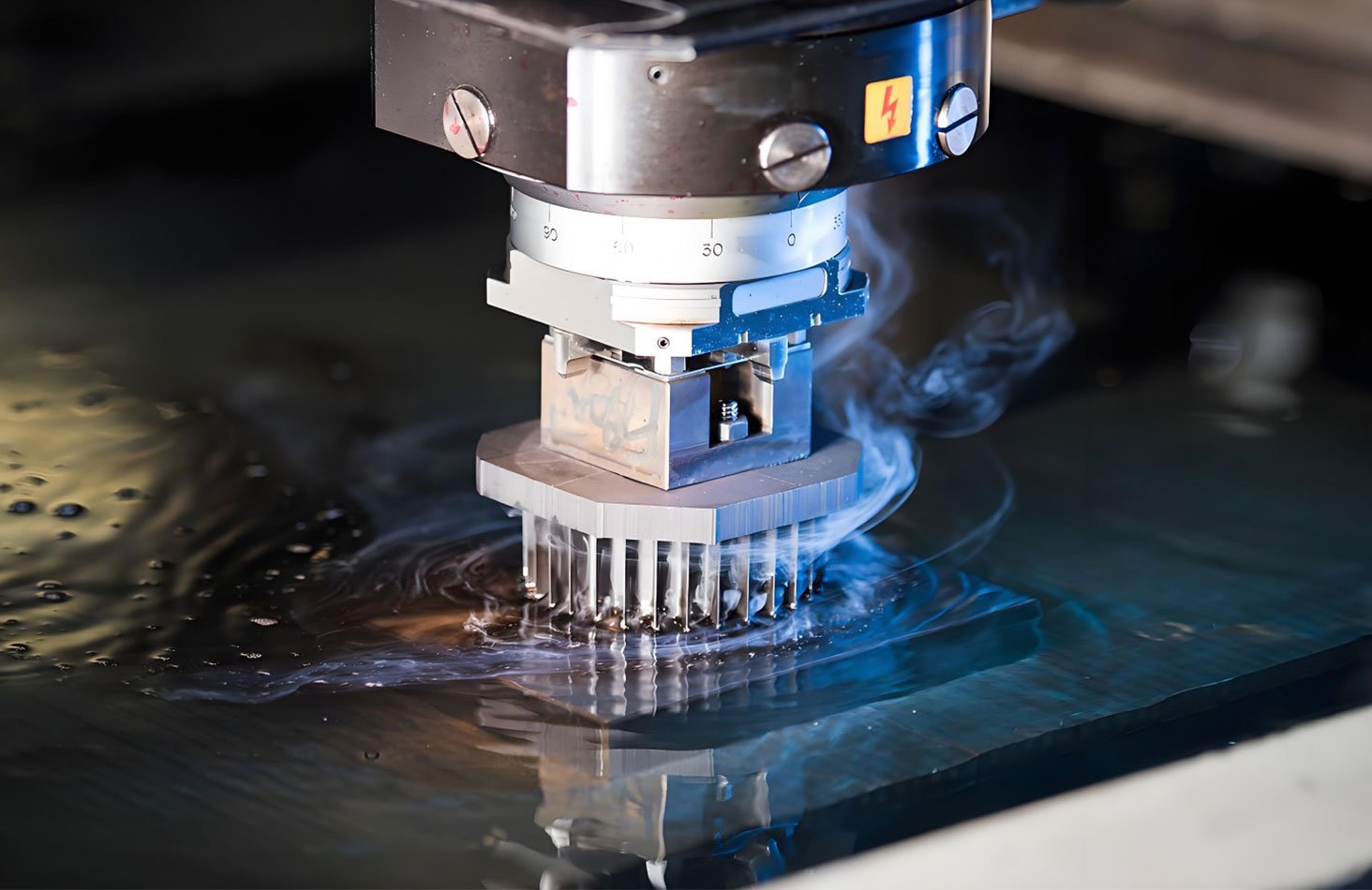
2.EDM:
放電加工は、放電により材料を侵食し、複雑な形状、深い空洞、複雑な内部形状を作り出すことができる。この放電加工には、細かい空洞を作るための型彫り放電加工や、精密な切断を行うワイヤー放電加工などの種類があり、狭い流路や鋭い角に適しています。
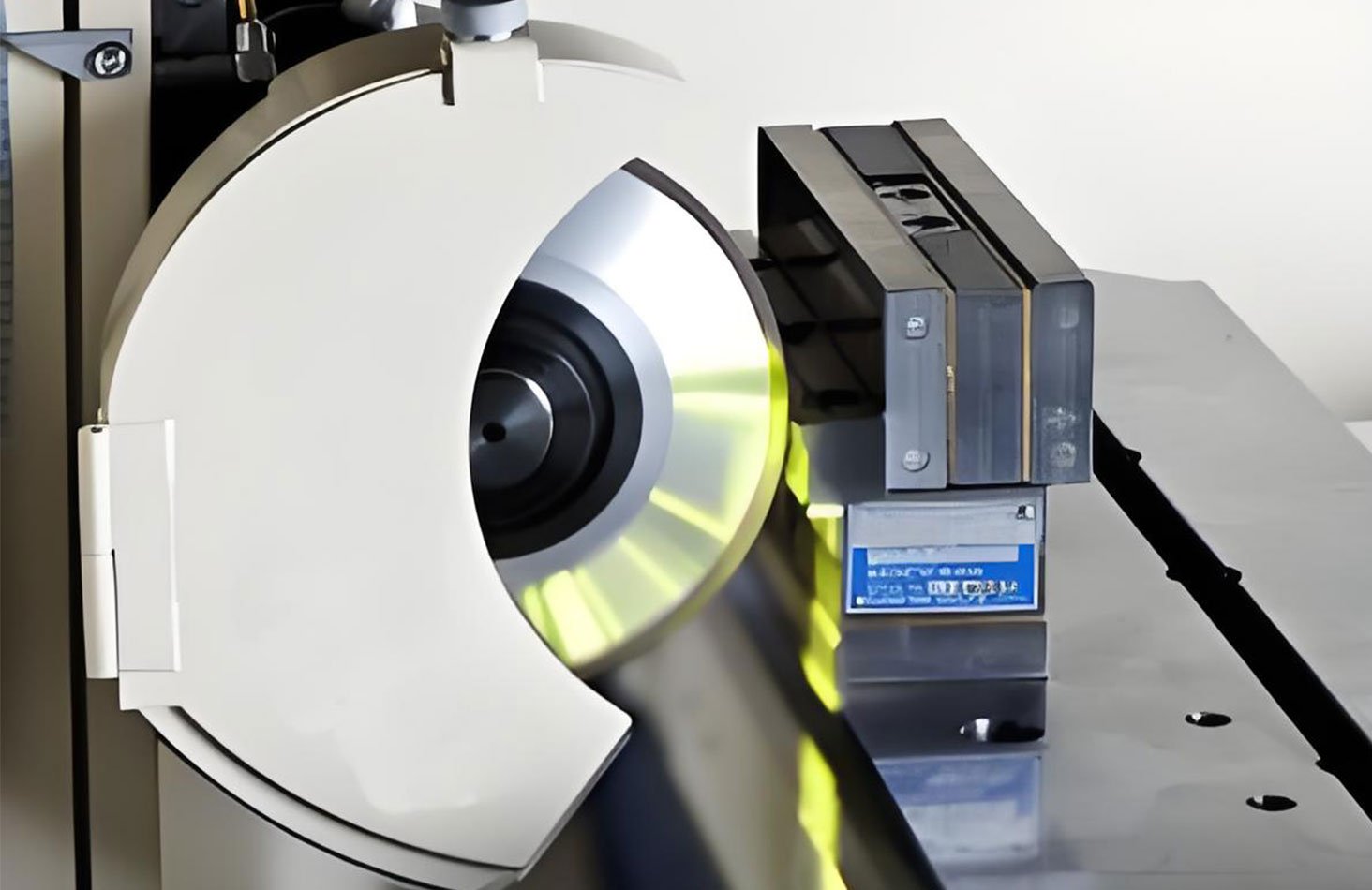
3.研磨:
研削は、研磨作用によって少量の材料を除去することにより、金型部品の表面仕上げと精度を向上させるために使用されます。滑らかな表面を実現し、厳しい寸法公差を満たすために、金型製造の最終段階で一般的に使用されます。
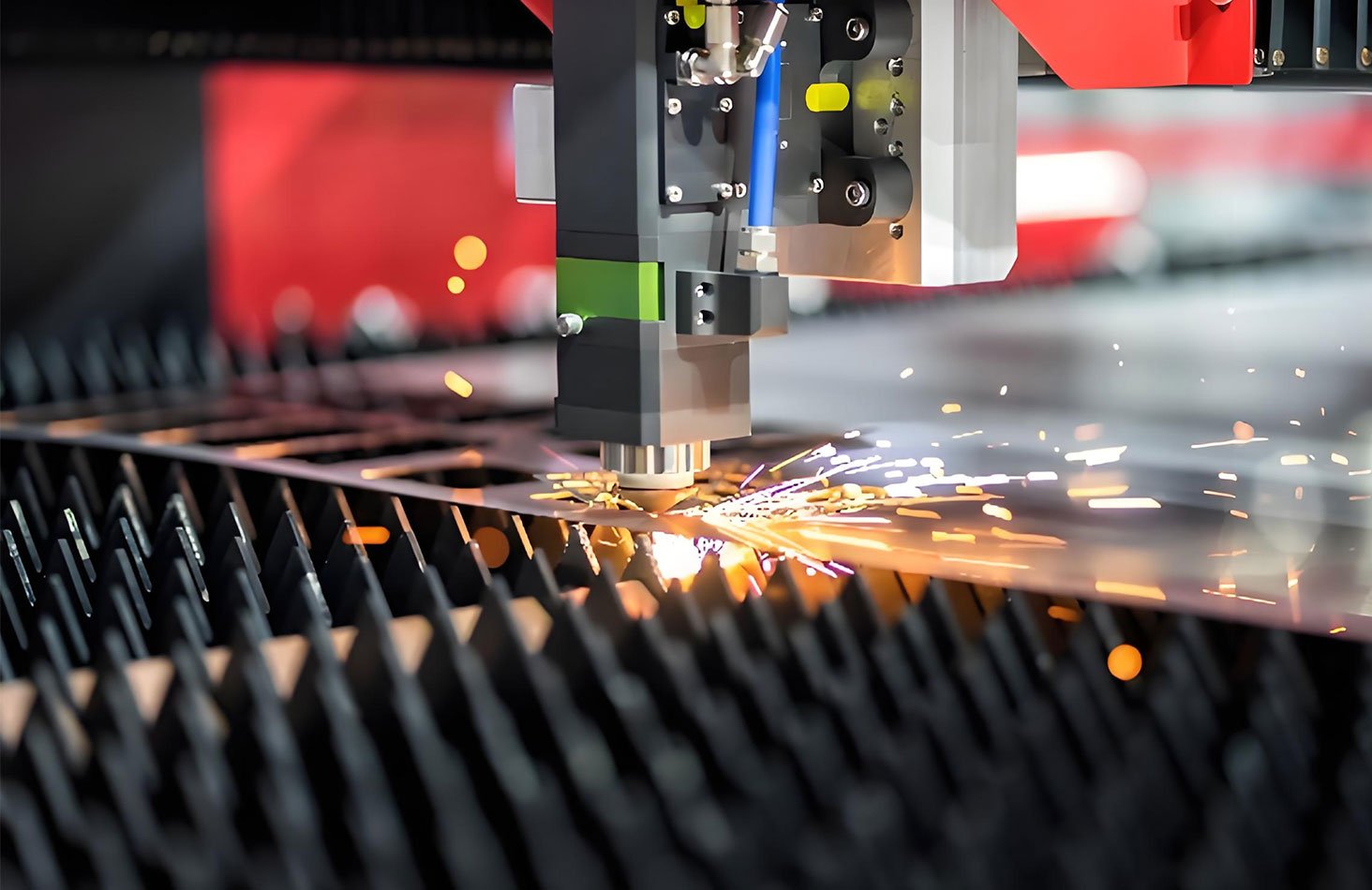
4.レーザー切断:
レーザー切断は、高出力のレーザービームを利用して、金型材料を優れた精度で切断・成形します。一般的に薄い板や金型部品の複雑なパターンを作成するために使用され、高速で効率的な切断ソリューションを提供します。
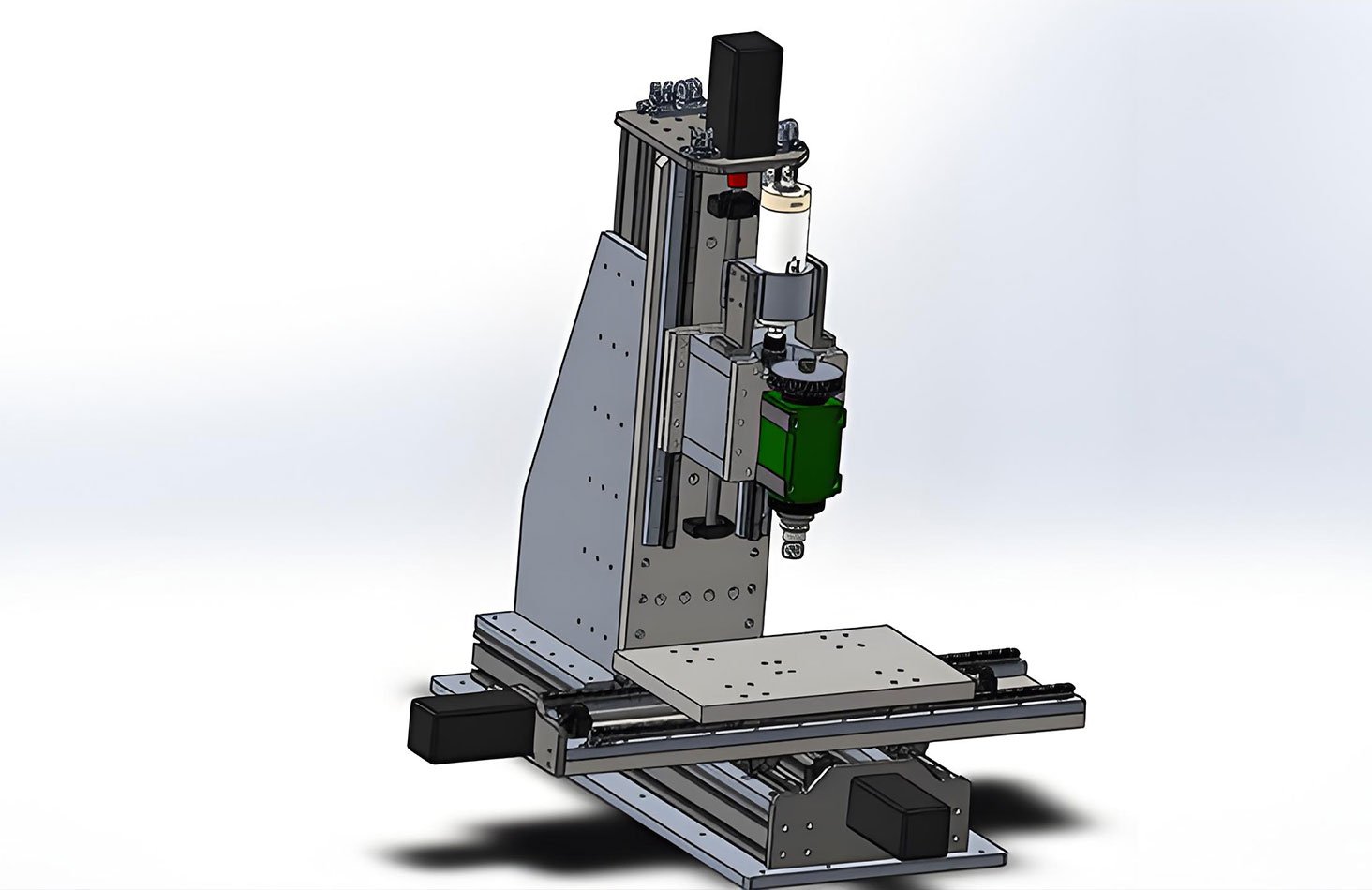
5.製粉:
フライス加工では、回転する切削工具(フライスカッター)を使用して、ワークピースから材料を除去します。この技術は、大きく平らな面を高精度で加工したり、金型部品に溝や輪郭などの複雑な形状を作ったりするのに理想的である。
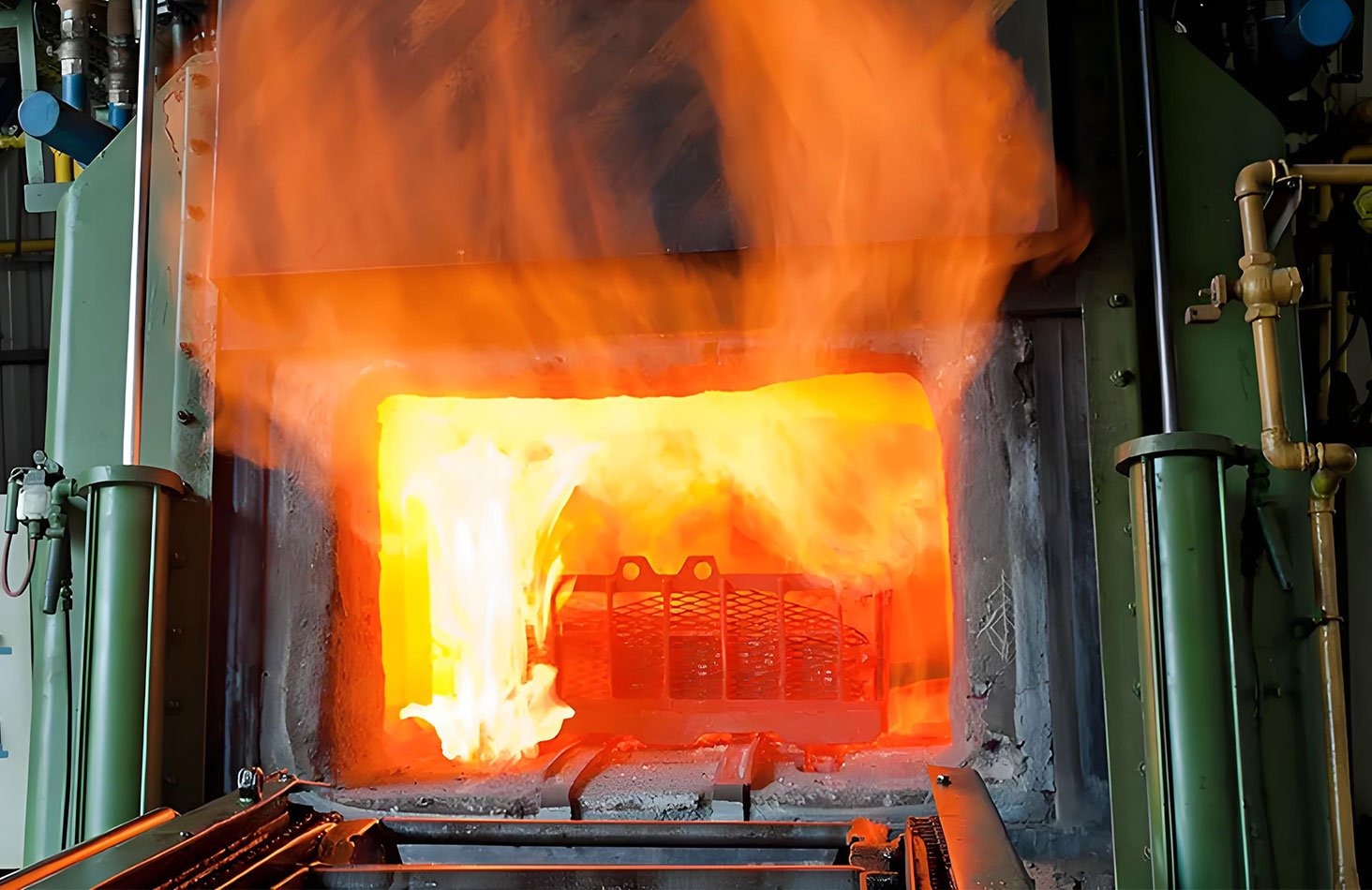
6.熱処理:
焼入れ、焼戻し、表面硬化などの熱処理工程は、金型材料の特性を向上させるために使用されます。これらの処理は、金型の耐久性、耐摩耗性、強度を向上させ、高性能なアプリケーションの要求を満たすことを保証します。
プラスチック押出成形金型の製造工程とは?
プラスチック押出成形用金型の製造には、原材料をプラスチック押出成形用の機能的な金型に変えるいくつかの重要な工程があります。以下は、これらのプロセスの詳細な内訳であり、最高の品質と性能を確保するための一般的な手順と特定の考慮事項の両方を兼ね備えています:
ステップ1:デザインとエンジニアリング:
設計とエンジニアリングの段階は、プラスチック押出成形金型製造の最初のステップです。CAD(コンピュータ支援設計)ソフトウェアを使用して詳細設計を作成し、金型が製品仕様を満たし、材料の流れや熱応力に対応できることを確認するためにシミュレーションを行います。この段階で考慮されるのは、プラスチックの種類、粘度、製品寸法、公差、押出成形機との適合性などです。最終的な設計では、欠陥を最小限に抑え、製造工程を最適化し、効率的でスムーズな製造を実現する必要があります。
ステップ2:素材の選択:
金型に適切な材料を選択することは、耐久性、耐摩耗性、および押出成形中に遭遇する高圧と高温に耐える能力を確保するために非常に重要です。一般的に使用される材料には、P20、H13、ステンレス鋼などの工具鋼があります。材料を選ぶ際には、使用温度や圧力、使用するプラスチックの種類、コストと性能のバランスなどの要素を考慮する必要があります。高品質の材料は、厳しい条件下での金型の寿命と安定性を保証します。
ステップ3:機械加工:
設計と材料の選択が完了すると、金型は機械加工の段階に入る。金型部品の製造には、CNCフライス加工、旋盤加工、ドリル加工、放電加工(EDM)などの高精度加工技術が使用される。これらの方法は、金型が寸法精度の要件を満たすことを保証し、放電加工は特に複雑な細部に有効です。押し出し時のプラスチックの付着を最小限に抑え、効率的な生産を確保するためには、滑らかな表面仕上げを実現することが不可欠です。
ステップ4:熱処理:
熱処理は、金型の強度と耐摩耗性を高めるための重要なステップです。一般的な熱処理には、焼入れ、焼戻し、窒化処理などがあり、金型の硬度を向上させ、押出工程での高圧や高温に耐えられるようにします。脆くならないよう、硬度と靭性のバランスをとることが重要です。金型の精度を維持するには、処理工程での歪みを最小限に抑えることが重要です。
ステップ5:研磨と仕上げ:
熱処理後、金型は研磨と表面仕上げを行う。内部表面は、プラスチックの流れや製品の表面品質を向上させるために研磨される。また、耐腐食性や耐摩耗性を高めるために、クロムやニッケルなどのコーティングを施すこともある。金型表面の平滑性は金型の性能と寿命に直接影響し、コーティングは腐食や磨耗の防止に役立つため、金型はライフサイクルを通じて耐久性を維持することができます。
ステップ6:組み立て:
すべての部品の機械加工と仕上げが終わると、金型を慎重に組み立てます。これには、金型のキャビティ、インサート、その他の部品の位置合わせを行い、すべてが正しく収まるようにします。ファスナーやシールは、金型が漏れないようにし、押し出し中の流路の完全性を維持するために適用されます。生産中の問題を回避し、金型が稼動条件下で適切に機能するようにするためには、組み立て時に厳しい公差を守ることが重要です。
ステップ7:テストと検証:
組み立て後、金型はサンプル材料を用いて実際の押出条件でテストを受けます。テストの目的は、不均一な流れ、漏れ、寸法の不正確さなどの問題を特定することです。問題が検出された場合は、金型設計や工程パラメータを調整して解決します。厳格な試験と改良を通じて、金型が生産要件を満たすことが検証され、一貫した高品質の生産が保証されます。
ステップ8:メンテナンスと文書化
金型が長期間にわたって確実に機能するように、メンテナンス・スケジュールを作成する。定期的な清掃、潤滑、点検は不可欠であり、摩耗した部品は速やかに交換しなければならない。設計ファイル、加工パラメーター、メンテナンス記録などの詳細な文書も、将来の参考のために保管します。優れたメンテナンスの実践は、ダウンタイムを最小限に抑え、金型の寿命を延ばし、長期的で効率的な生産を保証します。
押出成形用金型はさまざまな産業でどのように使用されているか?
押出成形用金型は、さまざまな製品を製造するために、多くの産業で多用途かつ不可欠なツールです。ダイを通して材料を成形することで、押出成形金型は複雑な断面形状を持つ製品の効率的かつ連続的な生産を可能にします。以下では、押出成形用金型がさまざまな分野でどのように使用されているかを詳しくご紹介します。
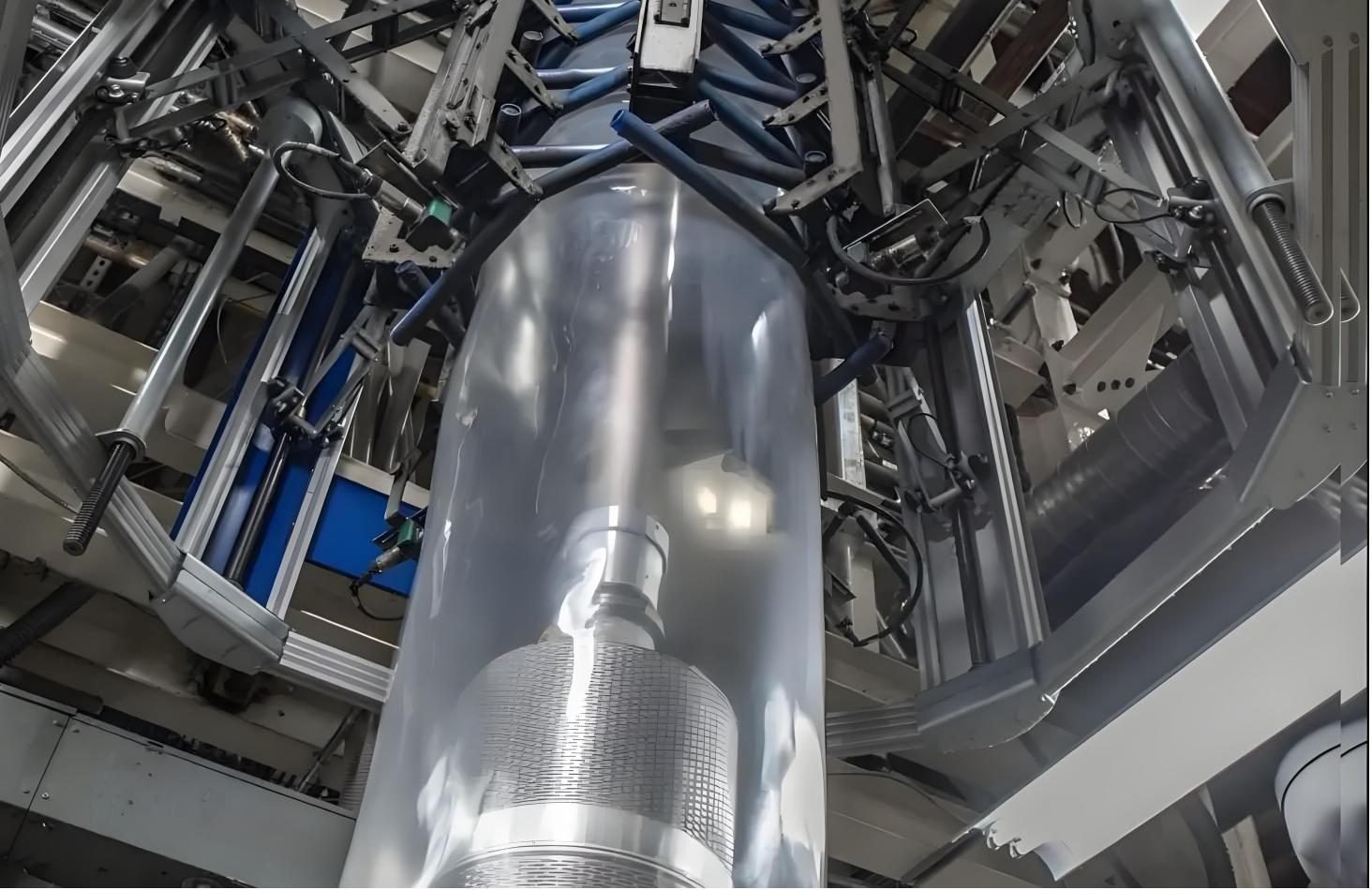
1.包装業界:
包装業界では、食品、飲料、パーソナルケア製品用のボトル、容器、チューブなど、さまざまなプラスチック包装材料の製造に押出成形用金型が使用されています。一般的な材料には、ポリエチレン(PE)、ポリプロピレン(PP)、PETなどがあり、軽量で柔軟性があり、費用対効果の高いパッケージング・ソリューションの製造に最適です。押出成形プロセスにより、無駄を最小限に抑えた大量生産が可能になり、安定した品質の大量生産品に対する業界の需要に応えている。
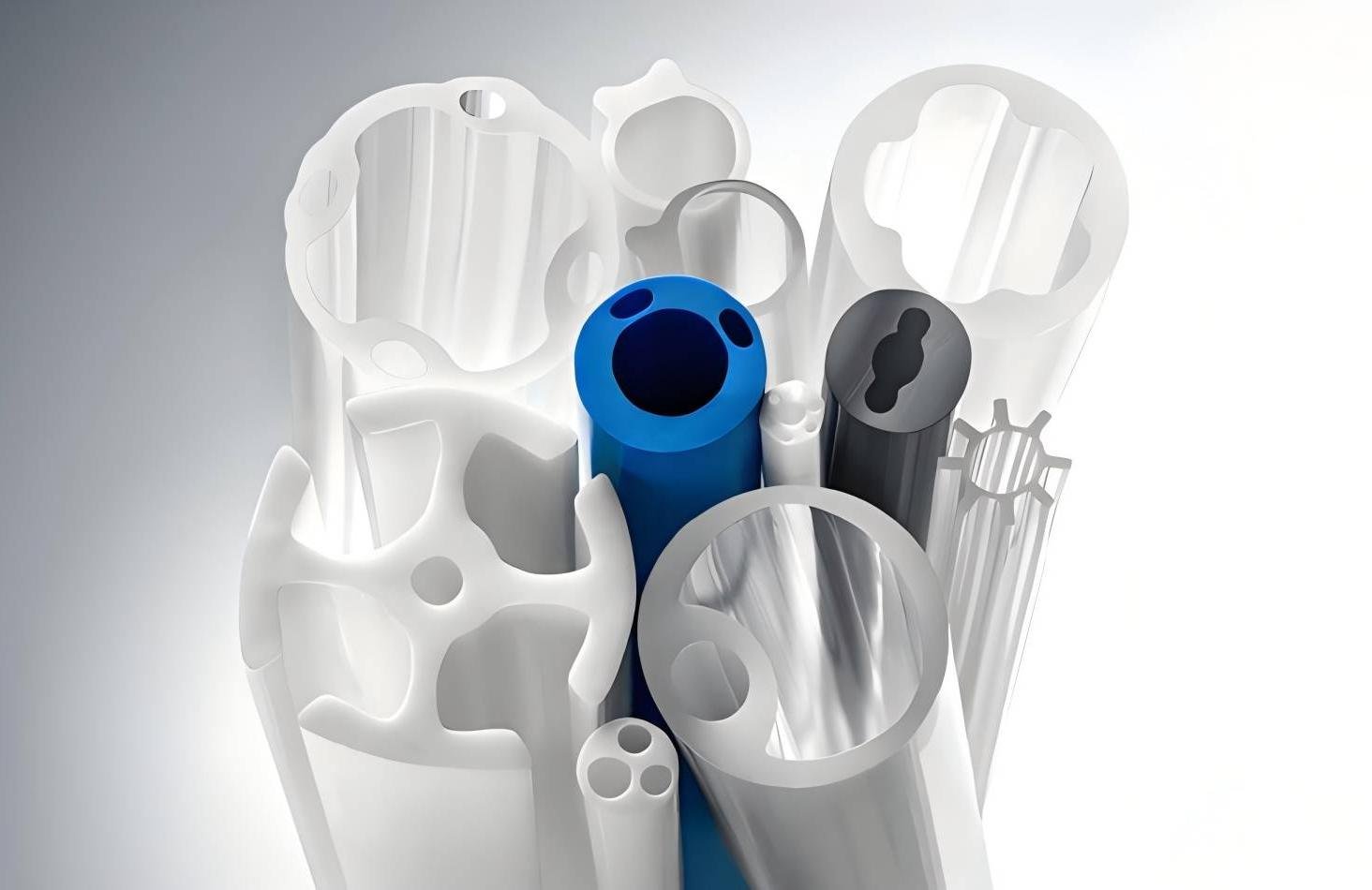
2.医療業界:
押出成形用金型は、カテーテル、ガイドワイヤー、手術用チューブ、埋め込み型器具などの器具を製造する医療業界では不可欠なものです。PVC、ポリエチレン(PE)、ポリプロピレン(PP)などの素材は、生体適合性と耐久性に優れているため、一般的に使用されています。押出成形の精度は、医療用部品が安全性、衛生性、性能に関する厳しい規制基準を満たすことを保証し、信頼性の高い高品質の医療製品の生産に欠かせないものとなっている。
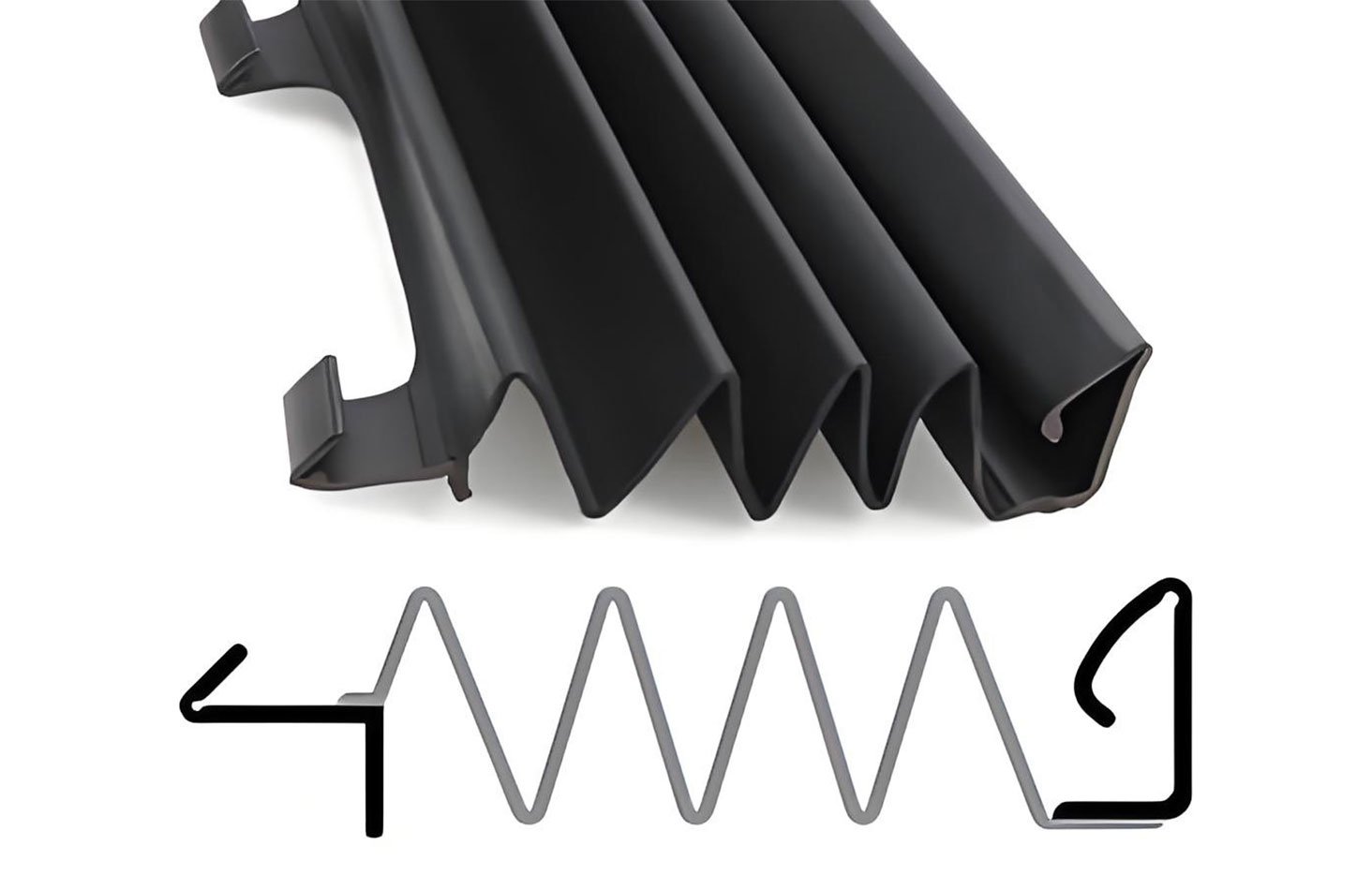
3.自動車産業:
自動車分野では、燃料ライン、ブレーキライン、エアダクト、窓枠、ウェザーシールなど、軽量かつ耐久性のある部品の製造に押出成形用金型が使用されている。使用される材料には、アルミニウム、PVC、各種熱可塑性プラスチックなどがある。これらの材料は、軽量でありながら強度があり、自動車の性能と燃費を向上させます。押出成形は、最新の自動車設計に不可欠な複雑な形状やプロファイルを持つ部品の製造を可能にする。
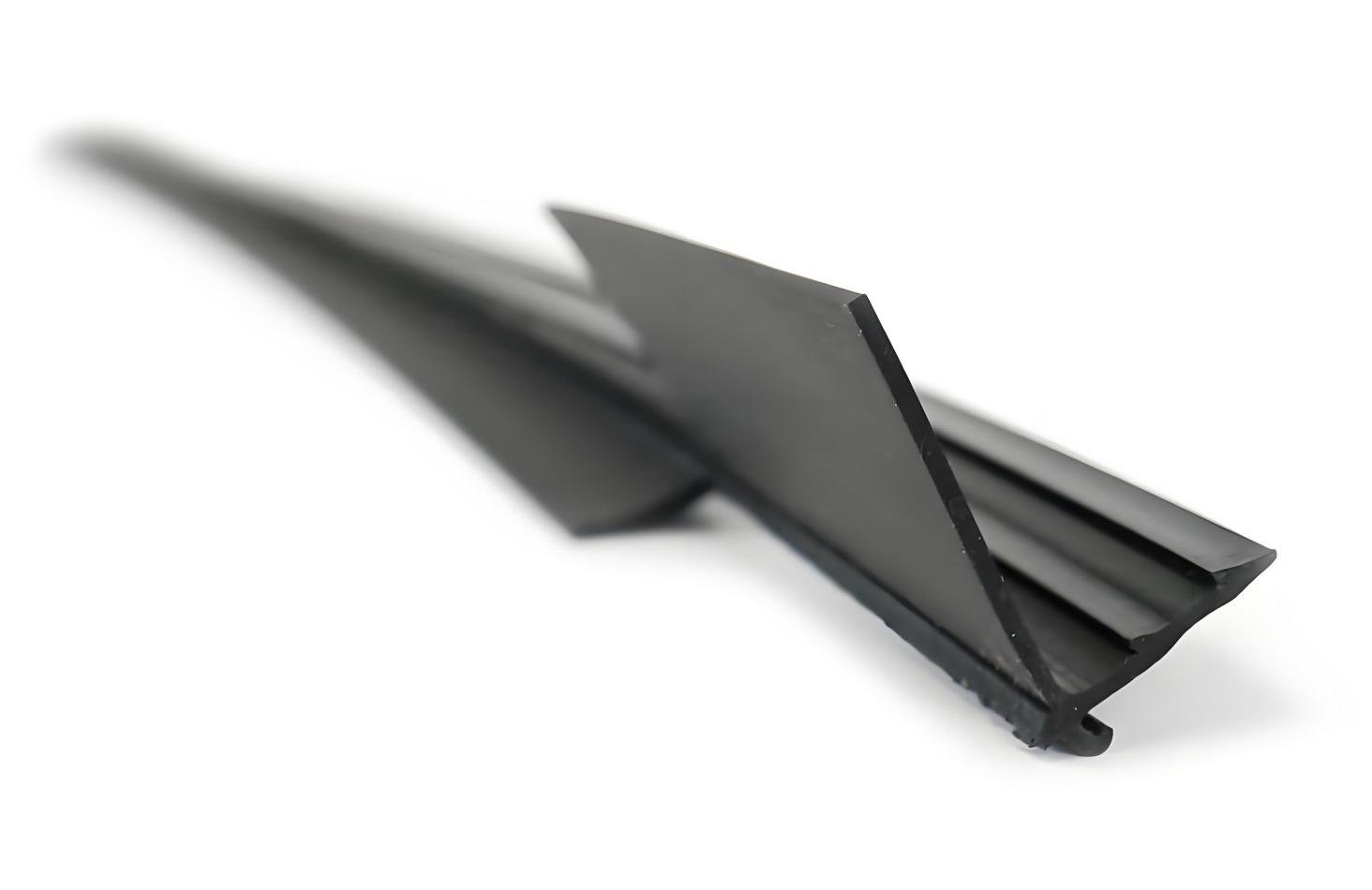
4.航空宇宙産業:
航空宇宙産業における押出成形金型は、燃料ライン、油圧ライン、構造要素などの軽量で高強度の部品を製造するために採用されています。航空宇宙用途の厳しい性能要件を満たすために、アルミニウム、チタン合金、特殊ポリマーなどの材料が使用されます。押出成形プロセスの精度と信頼性により、航空宇宙部品は軽量かつ耐久性に優れ、航空機設計の効率と安全性の向上に貢献します。

5.消費財産業:
押出成形用金型は、玩具、家庭用品、家具部品、包装フィルムなどの日用品を生産する消費財産業で広く使用されている。PVC、PET、ポリスチレン(PS)などの素材が一般的に使用され、耐久性、柔軟性、費用対効果のバランスが取れています。押出成形プロセスは、軽量で耐久性があり、美的にも多様な消費財の大量生産を可能にし、一貫した品質とデザインに対する高い需要に応えている。
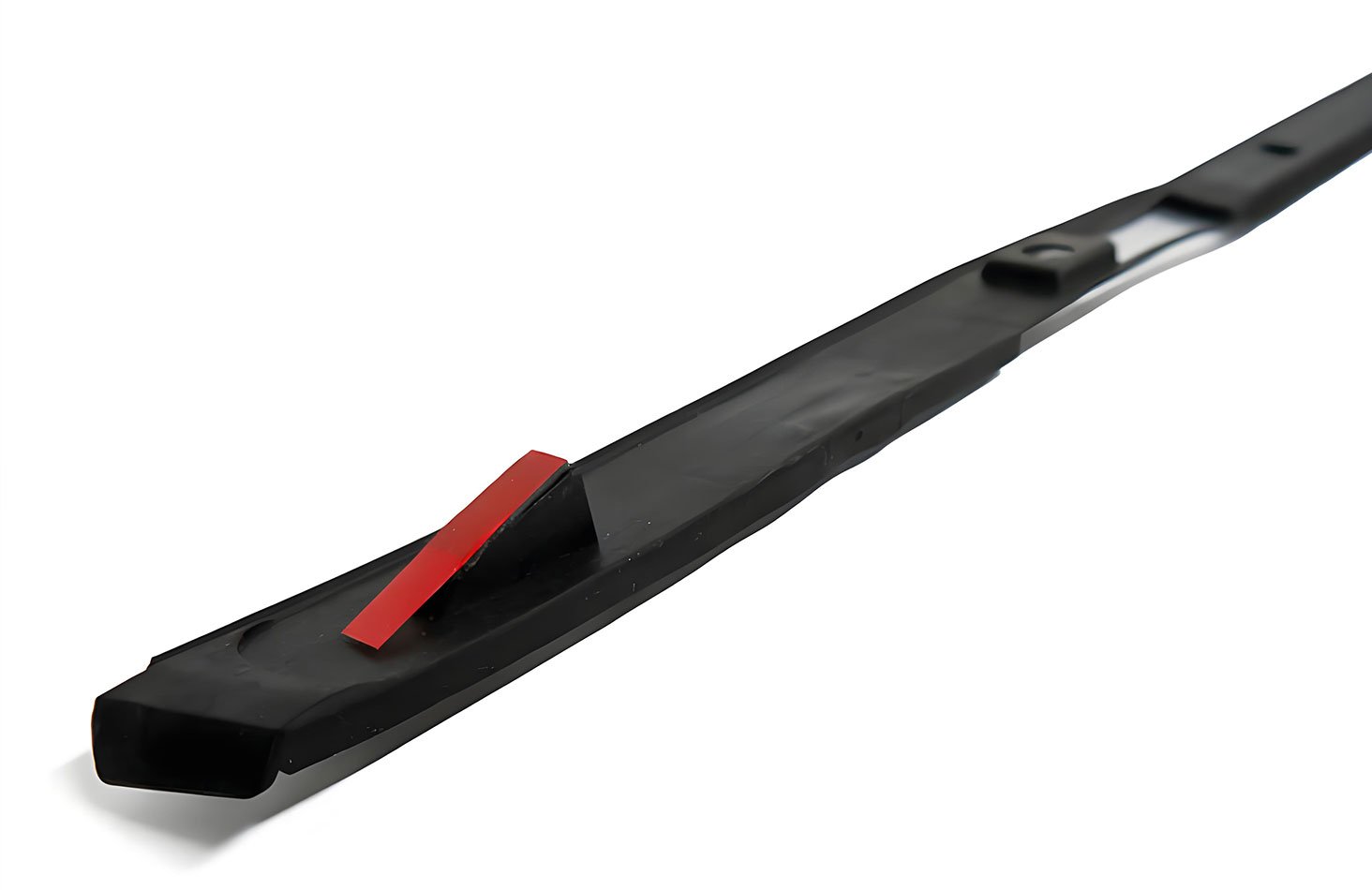
6.繊維産業:
繊維製品では、衣類、椅子張り、工業用繊維に使われる合成繊維、糸、織物を押出成形金型で作る。ポリエチレンテレフタレート(PET)、ナイロン、アクリルなどの素材は、その強度、柔軟性、細い糸に紡ぐ能力から、一般的に使用されている。押し出し工程は、繊維や織物の連続生産を保証し、織ったり編んだりして、多用途で耐久性のある繊維製品を作ることができる。
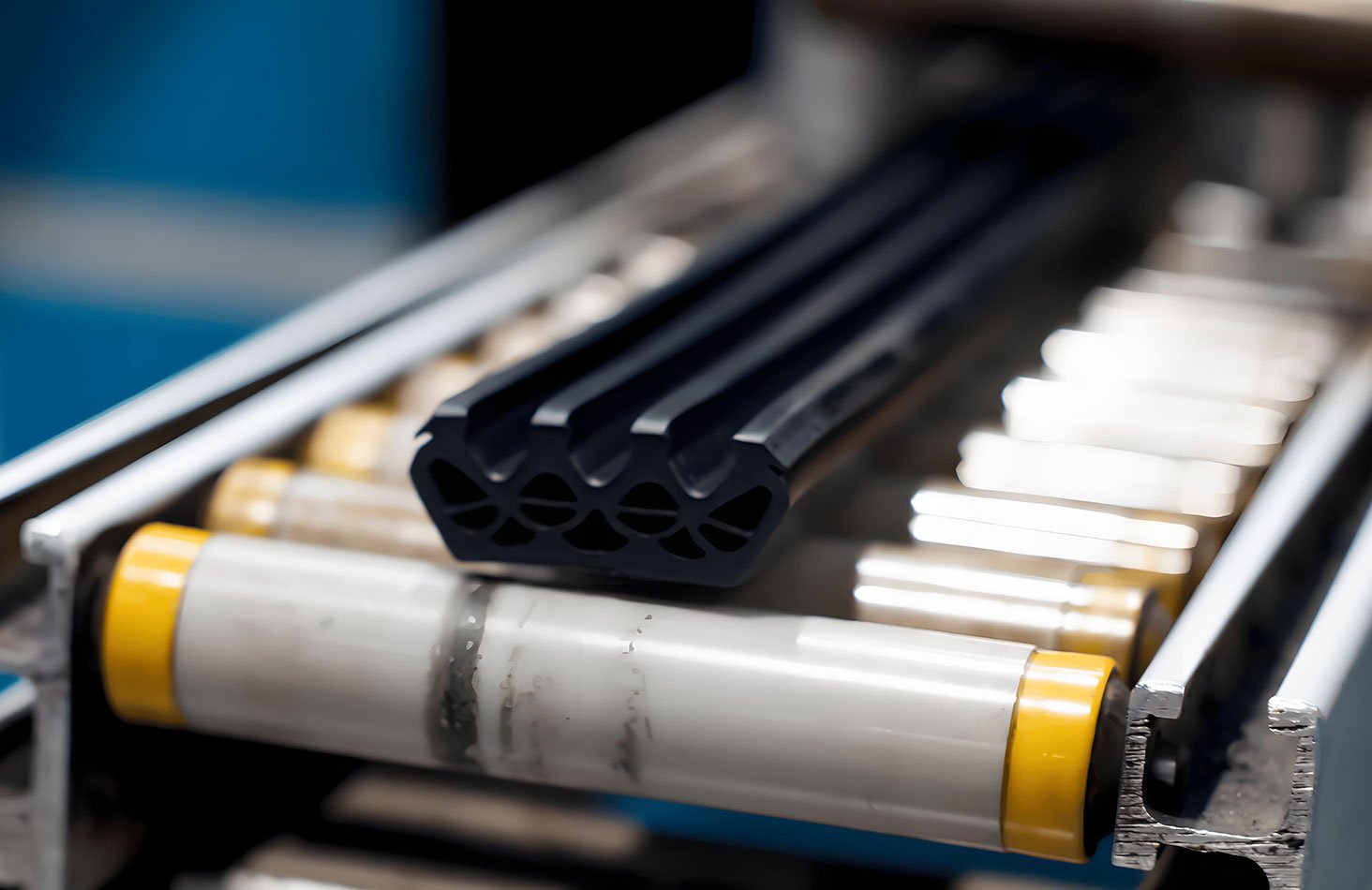
7.海洋産業:
海洋産業では、配管設備、換気システム、ボートや船舶の構造部品などの部品を作るために押出成形金型が使用されています。過酷な海洋環境に耐えるため、耐腐食性アルミニウムなどの材料が一般的に使用されています。押出成形は、水やその他の厳しい条件への曝露に耐えなければならない部品を作るための耐久性のある軽量なソリューションを提供します。
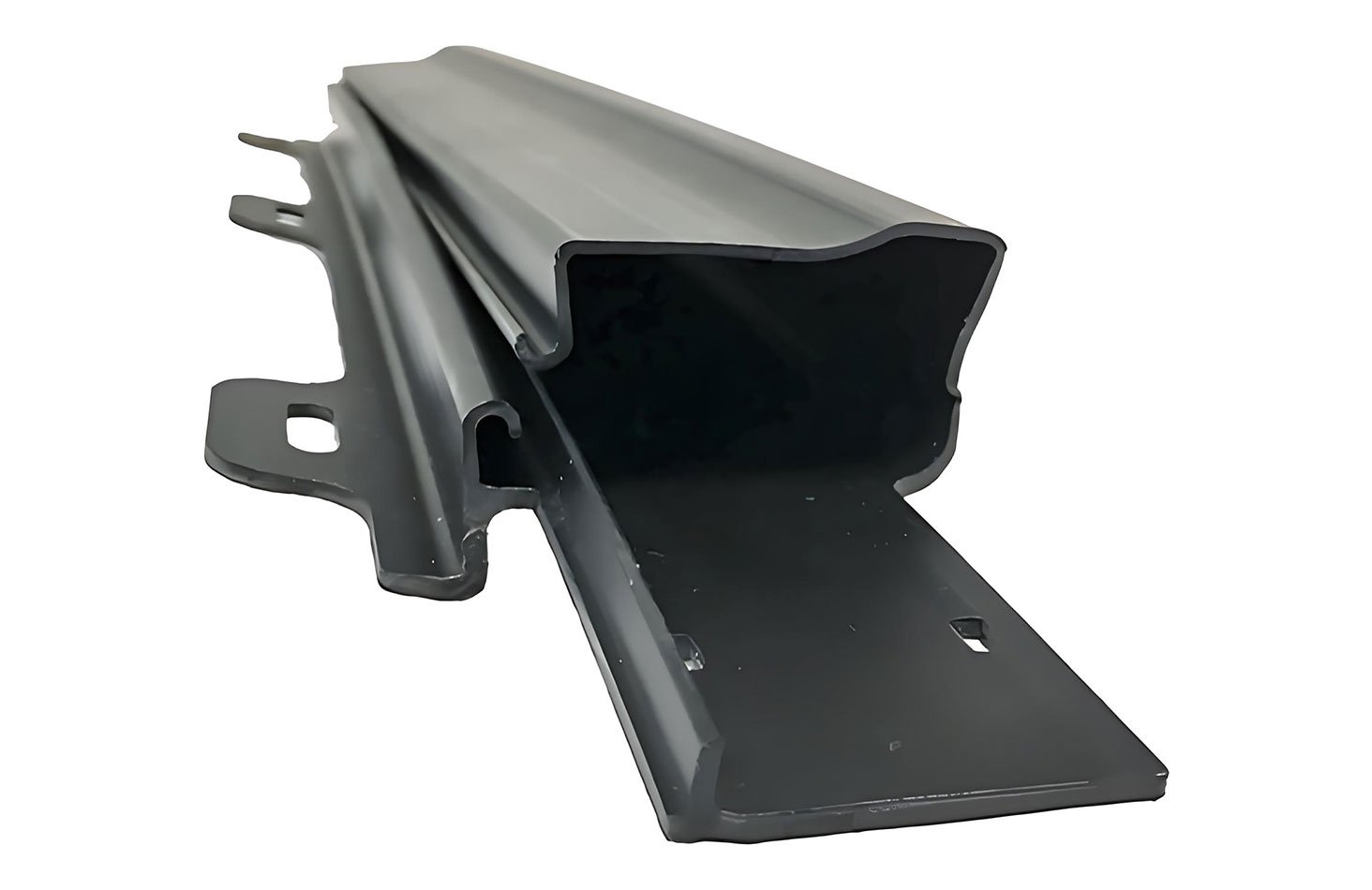
8.建設業界:
建築では、パイプ、窓枠、ドア枠、梁やチャンネルなどの構造部品などの材料を製造するために押出成形用金型が使用される。一般的に使用される材料は、PVC、アルミニウム、スチールなどである。押出成形は、長尺で連続した断面をカスタム・プロファイルで製造できるため、強度と耐久性の両方が求められる建築部材の製造に最適で、製造時の材料の無駄も最小限に抑えることができます。
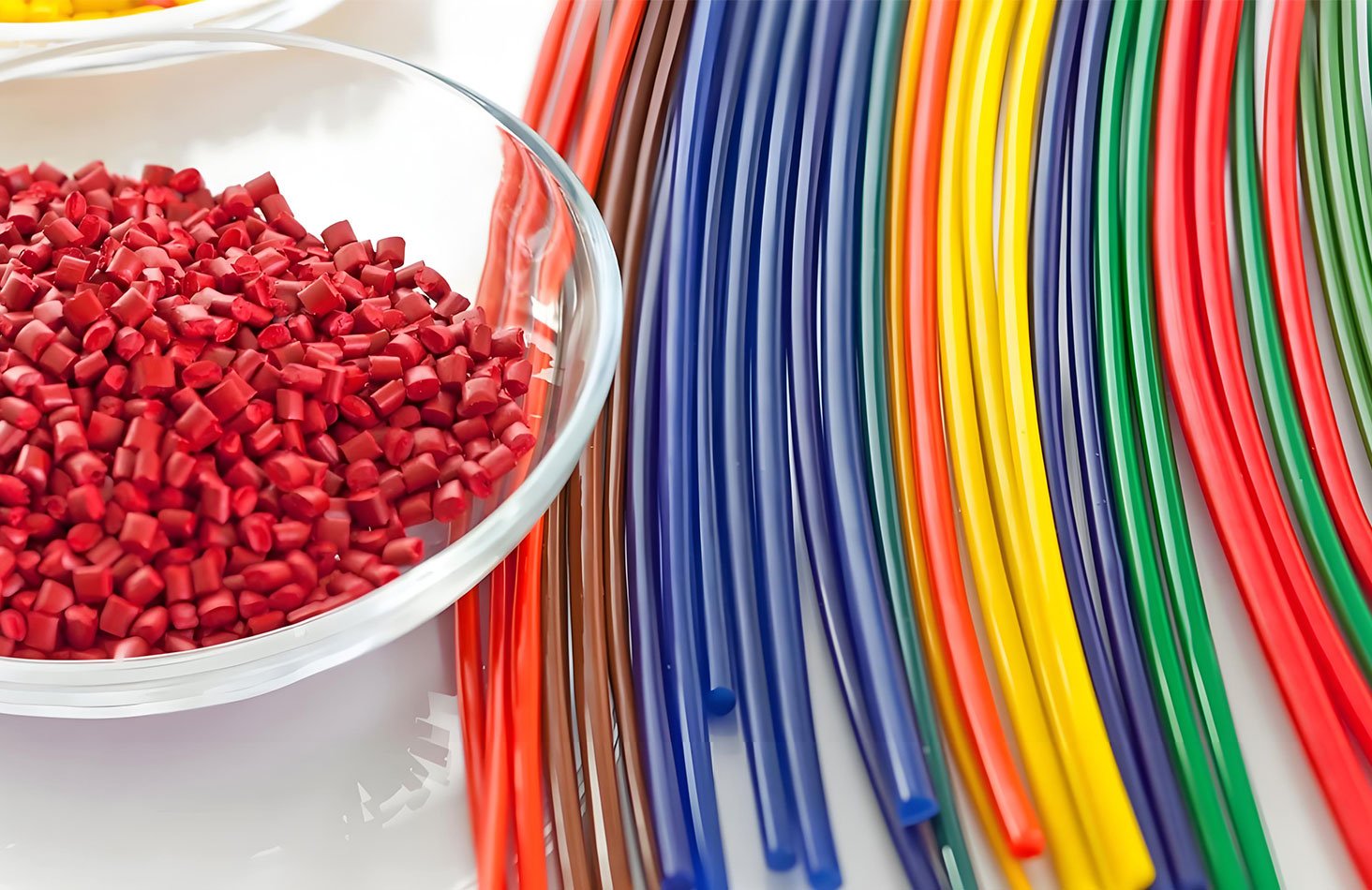
9.電気・電子産業
押出成形用金型は、ヒートシンク、ワイヤー絶縁体、ケーブルジャケット、電子機器用エンクロージャーなどの部品を製造する電気・電子産業で重要な役割を果たしています。耐久性、柔軟性、電気絶縁性を確保するために、熱可塑性プラスチックやアルミニウムなどの材料が一般的に使用されています。押し出し成形の精度は、これらの部品が均一に製造され、電気システムの性能と安全性に必要な仕様を満たすことを保証します。

10.製薬業界:
製薬業界では、錠剤のケーシング、カプセル、シリンジなどの製品を製造するために押出成形用金型が使用されます。使用される材料にはPVCなどの熱可塑性プラスチックがあり、医療グレードの製品を製造するのに必要な特性を備えています。押出成形工程は、医薬品部品が高い精度で製造され、厳しい衛生・安全基準を満たしていることを保証するために不可欠であり、各製品が医療用として信頼性が高く安全であることを保証します。
よくあるご質問
入門編 アップラステック
質問がありますか?私たちがお答えします。
弊社は押出加工と精密金型製作を専門としており、お客様の製造ニーズに合わせてカスタマイズされたソリューションを提供しています。
B2Bパートナーシップを中心に、自動車、エレクトロニクス、消費財などさまざまな業界と提携しています。
はい、お客様独自の要件に合わせてソリューションをカスタマイズします。
お問い合わせ
お見積もりはメールまたは下記フォームからお気軽にお問い合わせください。
Eメール:uplastech@gmail.com