Progettazione e produzione di stampi per estrusione di plastica
Scoprite i servizi di progettazione e produzione di stampi per estrusione di plastica su misura per le vostre esigenze. Forniamo stampi durevoli e di alta qualità per diversi settori industriali, garantendo precisione ed efficienza in ogni progetto. Contattateci oggi stesso per una consulenza!
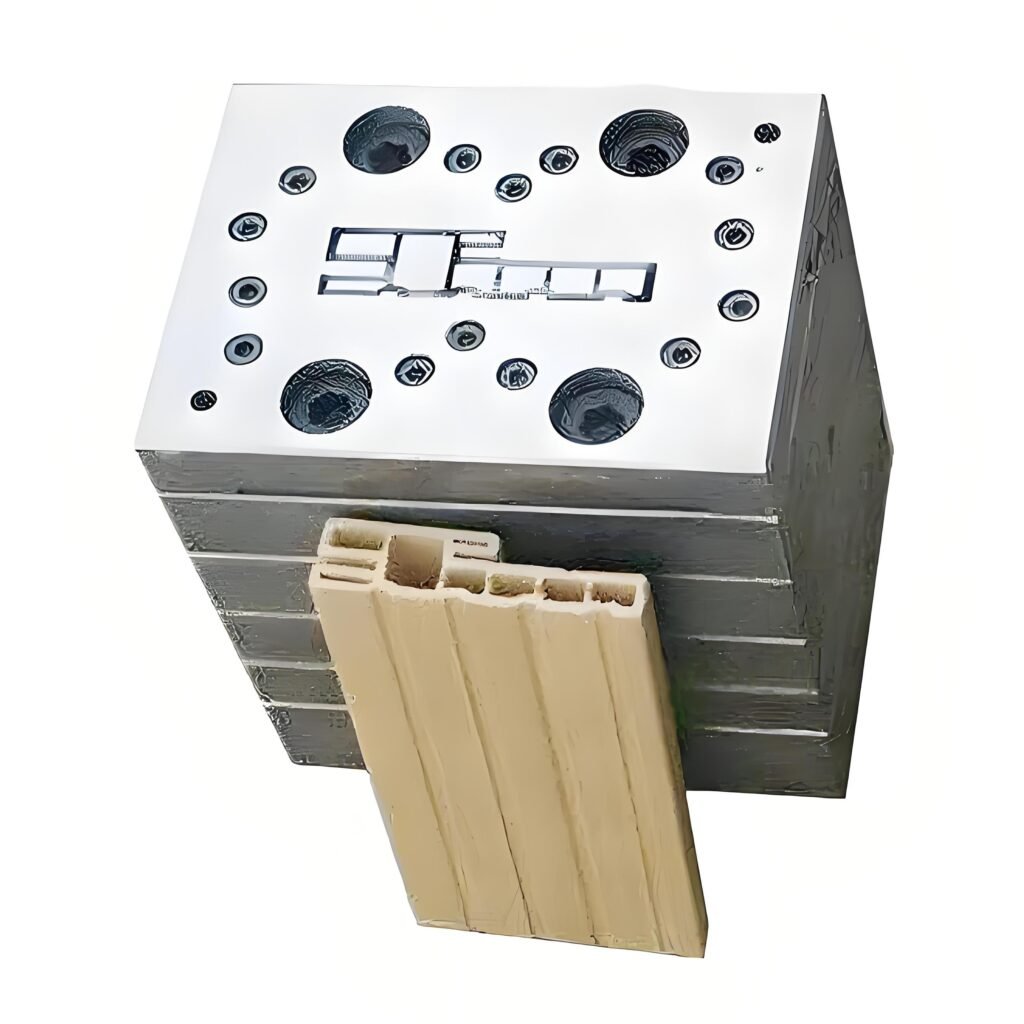
Guida completa alla progettazione e alla produzione di stampi per estrusione
Cosa sono gli stampi per estrusione e come funzionano?
Gli stampi per estrusione di plastica, noti anche come matrici, sono importantissimi nel processo di estrusione della plastica. L'estrusione di plastica è un modo per ottenere forme lunghe dalla plastica. Viene utilizzata per realizzare oggetti come tubi, lastre e forme personalizzate. La si usa nell'edilizia, negli imballaggi e nelle automobili.
Cosa sono gli stampi per estrusione di plastica?
Uno stampo per estrusione di plastica è uno strumento metallico che modella la plastica fusa in uno specifico profilo trasversale. Questi stampi sono realizzati in acciaio o alluminio e possono sopportare le alte temperature e le pressioni del processo di estrusione.
La progettazione dello stampo, o matrice, determina la forma finale del prodotto estruso e rappresenta quindi un fattore critico per il raggiungimento delle dimensioni e della qualità desiderate.
Componenti degli stampi per estrusione di plastica
L'efficacia di un sistema di estrusione dipende da diversi componenti critici:
Tramoggia: Alimenta le materie prime nell'estrusore.
Vite ②: Ruota per trasportare e fondere il materiale plastico all'interno del cilindro.
③ Barile: Riscalda la plastica fino al punto di fusione e la mantiene allo stato fuso.
④ Stampo (stampo per estrusione): Forma la plastica fusa in un profilo continuo quando esce dall'estrusore.
Sistema di raffreddamento: Assicura la corretta solidificazione del materiale estruso.
⑥ Estrattore o sistema di trasporto: Mantiene una velocità costante per evitare la deformazione durante il raffreddamento.
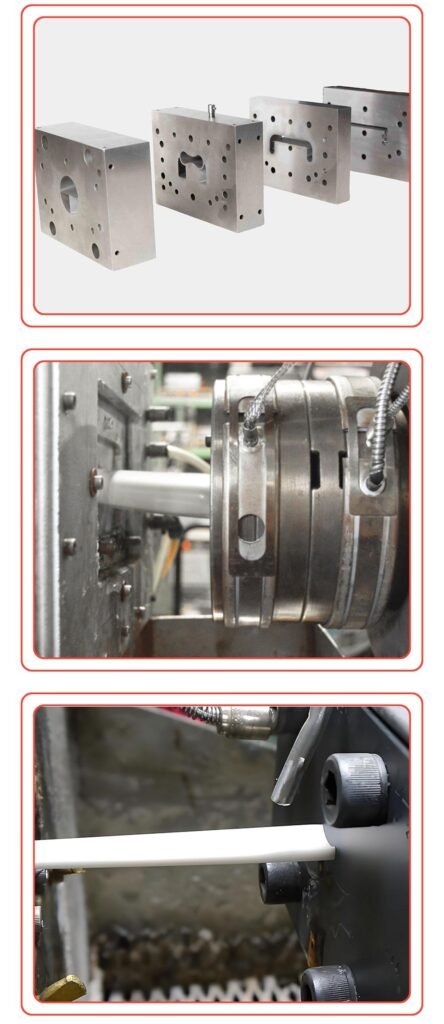
Come funzionano gli stampi per estrusione di plastica?
Il processo di estrusione della plastica prende i materiali plastici grezzi e li trasforma in prodotti finiti riscaldandoli, modellandoli e raffreddandoli. Ecco come funziona:
1. Alimentazione del materiale:
La plastica grezza, in genere sotto forma di pellet o granuli, viene caricata in una tramoggia. In questa fase, possono essere miscelati additivi come coloranti, stabilizzatori o riempitivi per migliorare proprietà come il colore, la forza o la resistenza ai raggi UV.
2. Fusione:
Il materiale plastico viene quindi introdotto in un barile riscaldato, dove una vite rotante lo fonde. Il calore è generato sia dall'attrito della vite sia da riscaldatori esterni. La temperatura del barile è generalmente impostata tra i 200 e i 275 gradi Celsius, a seconda del tipo di plastica.
3. Modellazione:
La plastica fusa viene spinta attraverso uno stampo, noto anche come stampo di estrusione. Questo stampo conferisce al materiale la forma desiderata. Il processo di estrusione offre una grande flessibilità, consentendo di ottenere forme diverse, come tubi, lastre o design personalizzati.
4. Raffreddamento:
Una volta uscita dallo stampo, la plastica viene raffreddata rapidamente con aria, bagni d'acqua o rulli di raffreddamento. Questo rapido processo di raffreddamento solidifica il materiale e lo blocca nella forma desiderata.
5. Taglio:
Il materiale estruso raffreddato e solidificato viene poi tagliato alla lunghezza desiderata. Può essere tagliato in dimensioni specifiche o avvolto in rotoli, a seconda dell'applicazione.
6. Finitura:
Dopo il taglio, possono essere eseguiti ulteriori processi come il trattamento superficiale, la rifilatura o l'ulteriore sagomatura, a seconda dell'uso e delle specifiche del prodotto.
Quali sono i diversi tipi di stampi per estrusione?
Esistono diversi tipi di stampi per estrusione di plastica, ciascuno progettato per specifiche esigenze industriali e di prodotto. Questi stampi sono fondamentali per modellare la plastica grezza in profili, lastre o pellicole precise. Ecco una sintesi dei vari tipi di stampi per estrusione di plastica:
1. Filiere a vite singola:
Le matrici monovite sono gli stampi per estrusione più comuni. Sono perfetti per la produzione di tubi e profilati. Sono economiche e possono essere utilizzate per estrudere diverse materie plastiche come PVC, PE, PP e ABS. Per questo motivo sono ideali per le grandi produzioni.
2. Filiere a doppia vite:
Gli stampi bivite utilizzano due viti per un'intensa miscelazione e fusione, il che li rende adatti alla produzione di forme complesse o di prodotti con molto riempimento. Questi stampi sono spesso utilizzati in applicazioni come tubi multi-lume o dispositivi medici come i cateteri, dove si desidera controllare molto bene il materiale.
3. Stampi per co-estrusione:
Le matrici per co-estrusione sono progettate per estrudere più strati di plastica contemporaneamente. Ciò consente di realizzare prodotti con caratteristiche speciali, come strati barriera o isolanti. Questi stampi sono molto utilizzati per i materiali da imballaggio. Possono mettere insieme plastiche con punti di fusione o proprietà diverse per migliorare il funzionamento dei prodotti.
4. Stampi per microestrusione:
Le matrici per microestrusione sono progettate per realizzare pezzi piccoli e precisi come dispositivi medici ed elettronici. Realizzano pezzi molto accurati e sono spesso utilizzati con plastiche speciali come il PEEK e il Teflon. Sono ideali per realizzare pezzi di dimensioni e forme molto piccole.
5. Stampi per pellicole e lastre piatte:
Gli stampi per film e lastre piane producono lastre o film larghi e sottili, spesso utilizzati per imballaggi, laminati e termoformatura. Questi stampi offrono uno spessore uniforme grazie a canali di flusso regolabili e funzionano con materiali come PET, PE e PVC.
6. Mortai a film soffiato:
Gli stampi per film soffiato sono utilizzati per produrre film tubolari che vengono gonfiati con aria. Sono ideali per la produzione di sacchetti di plastica, film termoretraibili e film estensibili. Essendo di forma rotonda, il film ha lo stesso spessore su tutto il perimetro. Possono produrre LDPE, HDPE e PP.
7. Stampi per tubi:
Gli stampi per tubi sono realizzati per produrre profili cilindrici cavi come tubi idraulici e tubi medici. Sono dotate di spazi tra gli stampi regolabili per modificare lo spessore della parete. Lavorano con materiali come PVC, HDPE e PP.
8. Stampi per l'estrusione di profili:
Le matrici per l'estrusione di profili sono utilizzate per realizzare forme complesse come i telai delle finestre e le finiture per autoveicoli. Sono ottime per realizzare stampi precisi con sezioni trasversali complicate e funzionano bene con materiali come ABS, PVC e TPE, utilizzati in applicazioni industriali e di costruzione.
9. Stampi per il rivestimento di fili e cavi:
Gli stampi per il rivestimento di fili e cavi sono utilizzati per avvolgere fili o cavi in strati protettivi di plastica, che garantiscono l'isolamento di cavi elettrici e fibre ottiche. Questi stampi sono progettati per gestire materiali ad alta temperatura come il PVC e l'XLPE, garantendo al contempo finiture lisce e durevoli.
10. Stampi per estrusione e soffiaggio:
Gli stampi a soffiaggio per estrusione producono contenitori cavi come bottiglie e serbatoi di carburante formando e soffiando un parison di plastica fusa. Grazie a un preciso controllo della temperatura per garantire che le pareti abbiano lo stesso spessore su tutto il perimetro, funzionano benissimo con PET, HDPE e PP.
11. Filiere anulari:
Le matrici anulari realizzano forme circolari come anelli e tubi cavi. Sono adatte per guarnizioni e sigilli. Producono oggetti della giusta dimensione. Sono adatte a materiali plastici resistenti come il nylon e il PP rinforzato.
12. Stampi per il rivestimento delle lastre:
Le fustelle per il rivestimento delle lastre sono utilizzate per applicare sottili strati di plastica a scopo di laminazione o rivestimento. Sono utilizzate per film decorativi e applicazioni barriera. Questi stampi sono altamente precisi e compatibili con materiali come TPU, EVA e PE. Assicurano che i rivestimenti siano uniformi e duraturi.
13. Stampi per estrusione multistrato:
Le matrici per estrusione multistrato sono utilizzate per combinare più materiali in un unico processo, creando prodotti con proprietà migliorate, come film per imballaggi o pannelli automobilistici. Queste matrici sono eccellenti per combinare materiali avanzati come EVOH, Nylon e PE, garantendo migliori prestazioni per applicazioni specializzate.
Linee guida per la progettazione degli stampi di estrusione
Una progettazione efficace degli stampi di estrusione è essenziale per produrre prodotti plastici di alta qualità con costanza ed efficienza. Qui di seguito viene presentata una serie consolidata e dettagliata di linee guida che coprono tutti gli aspetti della progettazione degli stampi di estrusione:
1. Principi di progettazione degli stampi:
Consistenza ed efficienza: Garantire che lo stampo produca un prodotto uniforme e coerente, ridurre al minimo gli sprechi di materiale e i tempi di inattività della produzione.
② Durata: Progettato per resistere alle sollecitazioni operative, comprese le alte temperature e le pressioni, garantendo longevità e affidabilità.
2. Selezione del materiale:
① Durata e resistenza: Utilizzare materiali di alta qualità come l'acciaio temprato o il carburo di tungsteno per garantire la resistenza all'usura e la stabilità termica.
② Resistenza alla corrosione: Scegliere materiali resistenti agli ambienti corrosivi, soprattutto per la lavorazione di materie plastiche aggressive come il PVC.
3. Geometria dello stampo e progettazione del canale di flusso:
① Design snello: I canali di flusso devono essere simmetrici e lisci, evitando le aree di ristagno per garantire una distribuzione uniforme del materiale e ridurre difetti come deformazioni o spessori non uniformi.
② Transizioni graduali: Incorporare transizioni graduali nella forma della matrice per ridurre al minimo le sollecitazioni del materiale e prevenire i difetti nel prodotto estruso.
4. Lunghezza e distanza dal suolo:
Lunghezza ottimale del terreno: Mantenere una lunghezza del terreno pari a circa 10 volte l'altezza del terreno per stabilizzare il flusso e garantire dimensioni costanti.
Sezione trasversale uniforme: La matrice deve mantenere una sezione trasversale costante per evitare variazioni di spessore nell'estruso.
5. Regolazione dello spazio tra gli stampi:
Design regolabile: Incorporano spazi regolabili per consentire la regolazione fine dello spessore del materiale durante il funzionamento, adattandosi a viscosità e requisiti di produzione variabili.
6. Gestione termica e sistemi di raffreddamento:
Controllo della temperatura: Le zone di riscaldamento e raffreddamento uniformi impediscono gradienti termici e deformazioni, mantenendo l'integrità del prodotto.
② Raffreddamento integrato: Utilizzare sistemi di raffreddamento ad acqua o ad aria per stabilizzare la temperatura dello stampo ed evitare il surriscaldamento.
7. Sistemi di ventilazione:
Rilascio dell'aria: Aggiungere canali di sfiato per eliminare l'aria intrappolata, garantendo una finitura superficiale liscia e prevenendo difetti come vuoti o sacche d'aria.
8. Finitura superficiale e rivestimento:
Superfici interne lisce: Applicare trattamenti superficiali (ad esempio, cromatura o rivestimenti al nitruro) e ottenere una finitura a specchio per ridurre l'attrito, migliorare il flusso del materiale e prolungare la durata dello stampo.
9. Design modulare e di facile manutenzione:
Facilità di manutenzione: Utilizza design modulari per facilitare lo smontaggio, la pulizia e la sostituzione dei componenti, riducendo al minimo i tempi di inattività.
Componenti durevoli: Includono parti usurabili sostituibili per ridurre i costi di manutenzione a lungo termine.
10. Simulazione e test:
Simulazione CFD: Utilizzate un software di simulazione avanzato per analizzare i modelli di flusso, ottimizzare le geometrie e prevedere le prestazioni.
② Test dei prototipi: Eseguire test approfonditi per identificare e correggere potenziali problemi prima della produzione su larga scala.
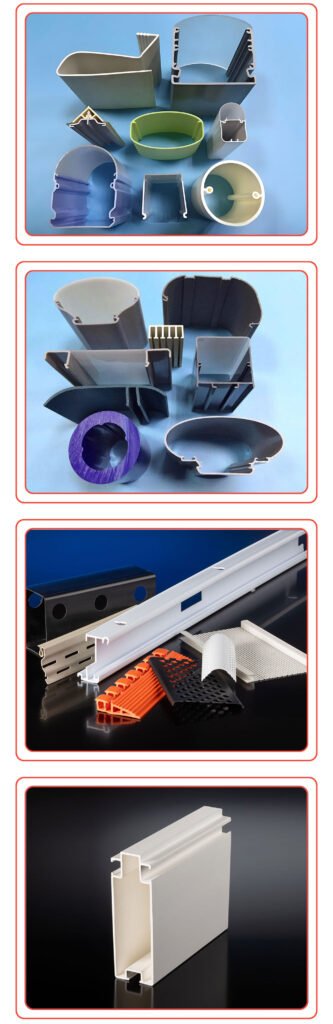
11. Allineamento degli stampi:
Allineamento di precisione: Garantire il corretto allineamento tra la matrice, l'estrusore e le apparecchiature a valle per evitare sprechi di materiale, flussi irregolari e difetti del prodotto.
12. Progettazione per la producibilità:
① Design semplificato: Evitare geometrie troppo complesse che complicano l'assemblaggio e la calibrazione. I progetti semplici migliorano la producibilità e l'affidabilità.
Adattamento e integrazione: Testate le estrusioni personalizzate per verificare la compatibilità con gli altri componenti e garantire un'integrazione perfetta.
13. Considerazioni sulla pulizia e la manutenzione:
① Sistemi di pulizia facili: Le matrici devono includere meccanismi di pulizia accessibili per rimuovere i residui e prevenire la contaminazione.
Manutenzione programmata: Stabilire programmi regolari di ispezione e pulizia per garantire prestazioni ottimali dello stampo e qualità del prodotto.
14. Pratiche di progettazione avanzate:
① Filosofia di design chiara: Concentrarsi sulla semplicità, sull'efficienza e sulla riduzione al minimo degli sprechi.
② Utilizzo del software: Sfruttare un software specializzato per soddisfare i requisiti specifici del prodotto e simulare le prestazioni in diverse condizioni.
Quali sono i materiali comunemente utilizzati per gli stampi per estrusione?
Lo stampaggio per estrusione è un processo produttivo versatile per la realizzazione di prodotti termoplastici. I materiali degli stampi utilizzati in questo processo svolgono un ruolo importante nel determinare la qualità del prodotto finale. Ecco una panoramica dei materiali più comuni utilizzati per gli stampi per estrusione di materie plastiche e di cosa bisogna tenere conto quando si sceglie il materiale migliore per la propria applicazione.
1. Acciaio:
L'acciaio è il materiale più utilizzato per gli stampi per estrusione, noto per la sua eccezionale forza, durata e resistenza all'usura. L'acciaio per lavorazioni a freddo di alta qualità offre un'eccellente durezza, che lo rende ideale per stampi di produzione ad alto volume, mentre l'acciaio per lavorazioni a caldo è in grado di resistere a temperature estreme, garantendo una lunga durata in ambienti sottoposti a stress termico. Gli acciai per utensili legati offrono un equilibrio tra tenacità, resistenza all'usura e lavorabilità, rendendoli versatili per varie applicazioni, tra cui stampi per PVC, HDPE e ABS.
2. Leghe di alluminio:
Le leghe di alluminio sono un'opzione leggera ed economica, ampiamente utilizzata per la prototipazione e le piccole produzioni. La loro eccellente conducibilità termica contribuisce a ridurre i tempi di raffreddamento e a migliorare l'efficienza. Sebbene l'alluminio sia più facile da lavorare rispetto all'acciaio, ha una durezza e una resistenza all'usura inferiori, che ne limitano l'uso ad applicazioni a bassa sollecitazione. È più adatto agli stampi con geometrie semplici e alla produzione di bassi volumi.
3. Rame e leghe di rame:
Il rame e le sue leghe, in particolare il berillio-rame, sono apprezzati per la loro superiore conducibilità termica e resistenza alla corrosione. Questi materiali sono particolarmente efficaci per gli stampi che richiedono un controllo preciso della temperatura, aiutando a prevenire deformazioni e difetti nei profili di estrusione complessi. Gli stampi a base di rame sono spesso utilizzati in applicazioni che richiedono finiture di alta qualità e una gestione costante della temperatura.
4. Leghe di titanio:
Le leghe di titanio sono note per l'impressionante rapporto forza-peso e l'eccellente resistenza alla corrosione. Sono particolarmente adatte per stampi di alta precisione e per applicazioni specializzate in cui sono essenziali tolleranze rigorose. La leggerezza del titanio lo rende anche una buona scelta per gli stampi utilizzati in settori come la produzione medica e aerospaziale.
5. Materiali ceramici:
I materiali ceramici sono scelti per la loro eccezionale durezza e resistenza alle alte temperature. Queste caratteristiche li rendono ideali per gli stampi utilizzati in condizioni estreme, come le applicazioni ad alta pressione o ad alta temperatura. Tuttavia, le ceramiche sono fragili, il che può limitarne l'uso in applicazioni che richiedono una resistenza meccanica agli urti.
6. Plastiche e materiali compositi:
Le materie plastiche e i compositi speciali sono occasionalmente utilizzati come materiali per stampi quando sono richieste strutture leggere o resistenza chimica. Il PTFE (Teflon) viene spesso scelto per le sue proprietà antiaderenti, che facilitano lo stampaggio nelle applicazioni a bassa produzione. Questi materiali sono convenienti e offrono vantaggi unici per casi d'uso specifici, ma sono generalmente limitati ad ambienti a bassa sollecitazione.
7. Ottone e altre leghe di rame:
L'ottone, una lega di rame e zinco, è spesso scelto per la sua lavorabilità e resistenza alla corrosione. Offre una finitura superficiale di alta qualità ed è adatto a stampi utilizzati in volumi di produzione medio-bassi. La combinazione di precisione e convenienza lo rende un'opzione interessante per alcune applicazioni.
8. Vetro e silicone:
Il vetro e il silicone sono materiali specializzati utilizzati in applicazioni di nicchia che richiedono alti livelli di precisione, flessibilità o finiture superficiali uniche. Gli stampi in silicone sono ideali per i progetti più complessi e offrono un'eccellente flessibilità, mentre gli stampi in vetro offrono una precisione dimensionale superiore, ma sono costosi e fragili, il che ne limita la diffusione.
Fattori da considerare nella scelta dei materiali per stampi
① Volume di produzione:
Gli stampi per la produzione di alti volumi richiedono materiali come gli acciai per utensili per garantire la durata, mentre per la produzione di bassi volumi si possono utilizzare alluminio o materiali compositi.
② Prestazioni termiche:
Materiali come l'alluminio o le leghe di rame sono preferiti per la loro conducibilità termica, garantendo cicli di raffreddamento efficienti.
③ Finitura superficiale:
L'ottone o l'acciaio inossidabile sono eccellenti per finiture di alta qualità, mentre la ceramica è ideale per la precisione.
④ Resistenza alla corrosione:
Gli acciai inossidabili, il titanio e le leghe di rame resistono alla corrosione, caratteristica essenziale per le applicazioni mediche o alimentari.
⑤ Costi e manutenzione:
L'alluminio è conveniente per la prototipazione, mentre gli acciai preinduriti riducono i tempi e i costi di lavorazione per stampi di produzione durevoli.
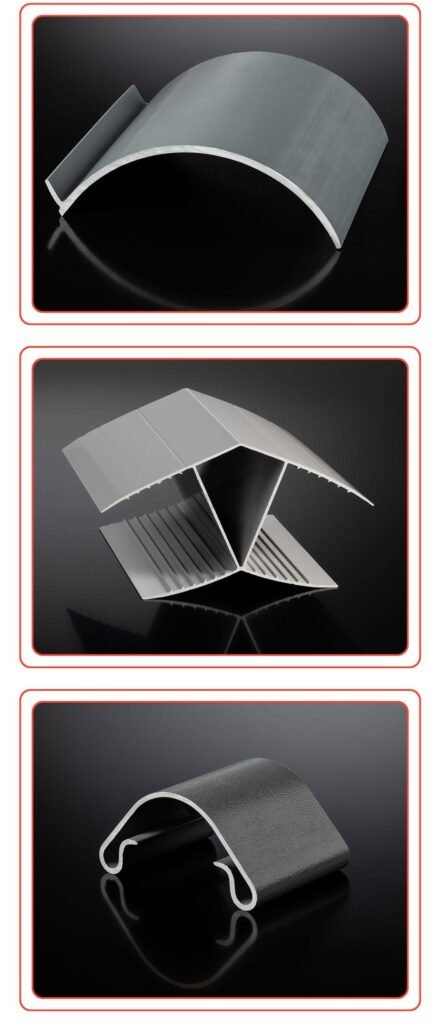
In che modo le proprietà del materiale dello stampo influiscono sulla progettazione dello stampo?
Le proprietà dei materiali degli stampi sono fondamentali per la progettazione, le prestazioni e la durata degli stampi utilizzati nei processi di iniezione ed estrusione. Esse influenzano fattori quali la gestione termica, la durata, la qualità del prodotto e l'efficienza della produzione. Ecco una guida completa su come queste proprietà influiscono sulla progettazione degli stampi:
1. Conducibilità termica:
① Impatto: I materiali ad alta conducibilità termica (ad esempio, alluminio e rame) dissipano efficacemente il calore, riducendo i tempi di raffreddamento e prevenendo problemi come la deformazione dei pezzi stampati. Al contrario, materiali come l'acciaio, con una conducibilità termica inferiore, possono richiedere sistemi di raffreddamento aggiuntivi.
② Considerazioni sulla progettazione: Utilizzare materiali ad alta conduttività per gli stampi, privilegiando la velocità e il raffreddamento uniforme, ma bilanciando il tutto con un rinforzo strutturale per la durata.
2. Espansione termica:
Impatto: Le variazioni dei tassi di espansione termica possono portare a imprecisioni dimensionali durante le variazioni di temperatura. Materiali come l'acciaio o la ceramica, a bassa espansione termica, garantiscono una maggiore stabilità dimensionale.
② Considerazioni sulla progettazione: Per i processi ad alta temperatura o con tolleranze ristrette, selezionare materiali con espansione minima per mantenere la precisione.
3. Resistenza e durata:
① Impatto: i materiali ad alta resistenza (ad esempio, acciaio temprato, titanio) resistono alle alte pressioni e temperature dello stampaggio a iniezione o dell'estrusione. Questi materiali resistono alla deformazione, garantendo una qualità costante dei pezzi per cicli di produzione prolungati.
② Considerazioni sulla progettazione: Utilizzare materiali durevoli per stampi con geometrie complesse o per la produzione di grandi volumi. Considerare acciai per utensili come il P20 o l'H13 per il loro equilibrio tra resistenza e lavorabilità.
4. Resistenza all'usura:
① Impatto: L'uso continuo e i materiali abrasivi possono degradare le superfici degli stampi. I materiali resistenti all'usura riducono la frequenza di manutenzione e prolungano la vita dello stampo.
② Considerazioni sulla progettazione: Scegliere rivestimenti (ad es. nitrurazione, cromatura) o materiali più duri quando si stampano plastiche abrasive o cariche di vetro.
5. Resistenza alla corrosione:
Impatto: L'esposizione all'umidità, alle sostanze chimiche o agli additivi corrosivi di alcune materie plastiche può degradare gli stampi, compromettendo la qualità del prodotto. Gli stampi in acciaio inox e rivestiti offrono una maggiore resistenza.
② Considerazioni sulla progettazione: Utilizzare materiali resistenti alla corrosione per gli stampi esposti ad ambienti reattivi o applicare trattamenti superficiali protettivi per una maggiore durata.
6. Lavorabilità:
① Impatto: I materiali più facili da lavorare, come l'alluminio, riducono i tempi e i costi di produzione, ma possono non avere la durata dell'acciaio o del titanio.
② Considerazioni sulla progettazione: Per gli stampi prototipo o per i volumi ridotti, i materiali lavorabili fanno risparmiare tempo. Gli stampi di produzione possono giustificare i maggiori costi di lavorazione dei materiali durevoli.
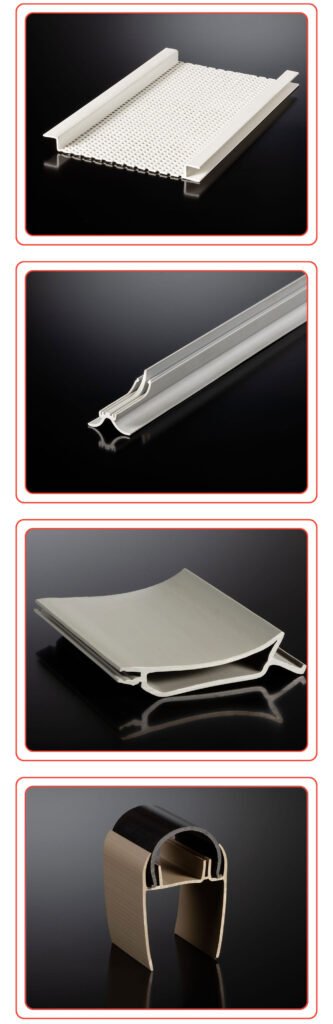
7. Finitura superficiale:
① Impatto: La qualità della superficie dello stampo influisce sull'estetica e sulla facilità di rilascio del prodotto finale. Finiture di alta qualità minimizzano i difetti e riducono i tempi di ciclo.
② Considerazioni sulla progettazione: Selezionare materiali in grado di ottenere finiture lisce, come l'acciaio per utensili, per i pezzi con requisiti estetici o funzionali critici.
8. Resistenza chimica:
① Impatto: Alcune materie plastiche o additivi possono degradare le superfici degli stampi. Materiali come l'acciaio inossidabile o il titanio resistono all'esposizione chimica, preservando l'integrità dello stampo.
② Considerazioni sulla progettazione: Per gli stampi utilizzati con resine chimicamente aggressive, privilegiare materiali resistenti o rivestimenti protettivi.
9. Costo:
① Impatto: Materiali pregiati come l'acciaio temprato o il titanio aumentano i costi iniziali ma riducono le spese di manutenzione e sostituzione nel tempo.
② Considerazioni sulla progettazione: Bilanciare i costi dei materiali con il volume di produzione previsto e le esigenze operative per ottimizzare il ritorno sull'investimento.
Tecniche di produzione di stampi per estrusione di plastica
Gli stampi per estrusione di plastica, noti anche come matrici per estrusione, vengono creati utilizzando un'ampia gamma di tecniche per ottenere la forma, le dimensioni e la funzionalità desiderate. Di seguito viene fornita una panoramica completa delle tecniche di produzione più comunemente utilizzate, combinando i dettagli chiave per una migliore comprensione:
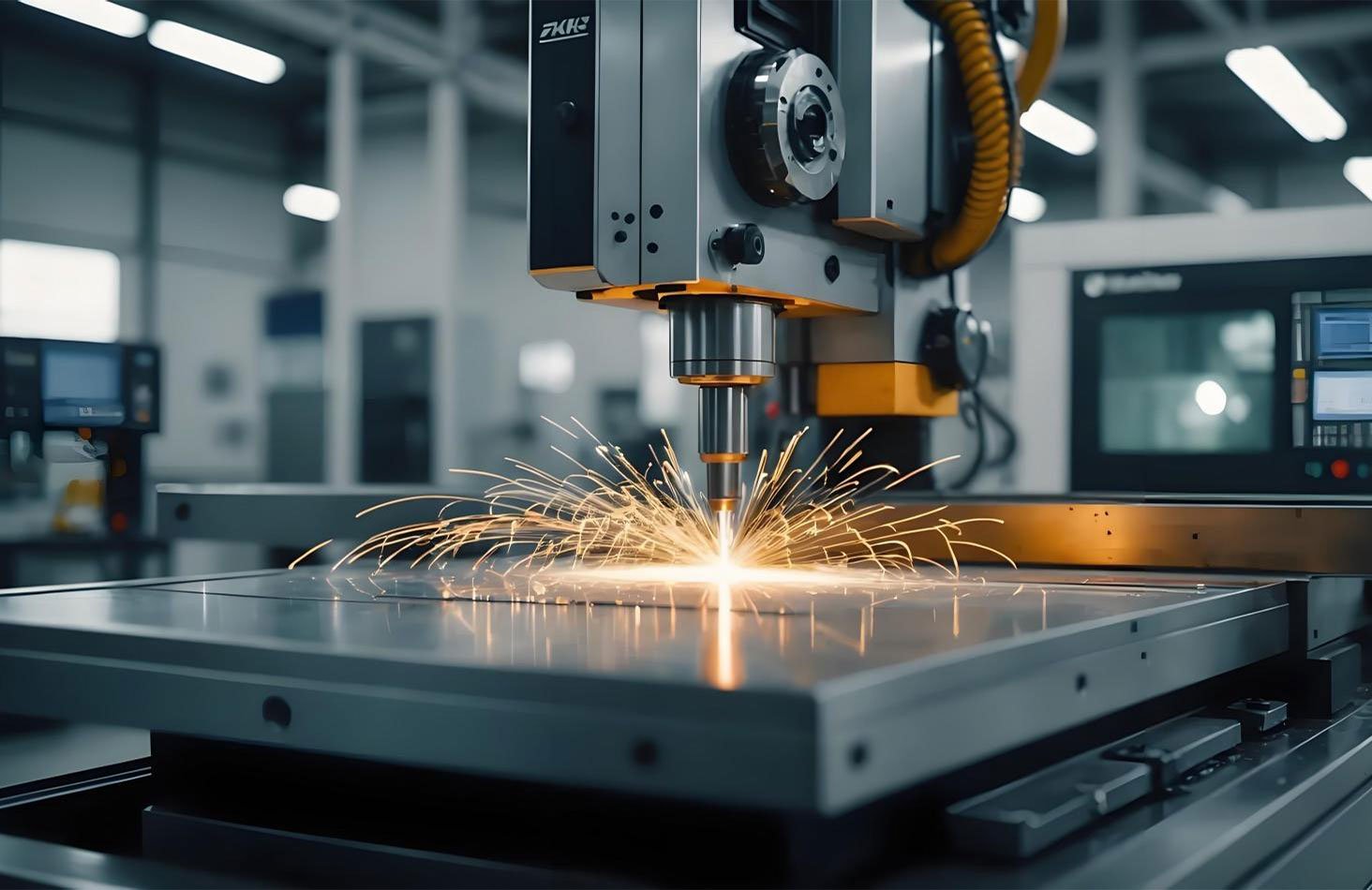
1. Lavorazione CNC:
La lavorazione CNC utilizza strumenti di taglio controllati dal computer per modellare con precisione materiali di stampo come l'acciaio o l'alluminio. È altamente accurata e in grado di raggiungere tolleranze ristrette, il che la rende ideale per creare componenti primari di stampi e geometrie esterne con precisione e coerenza.
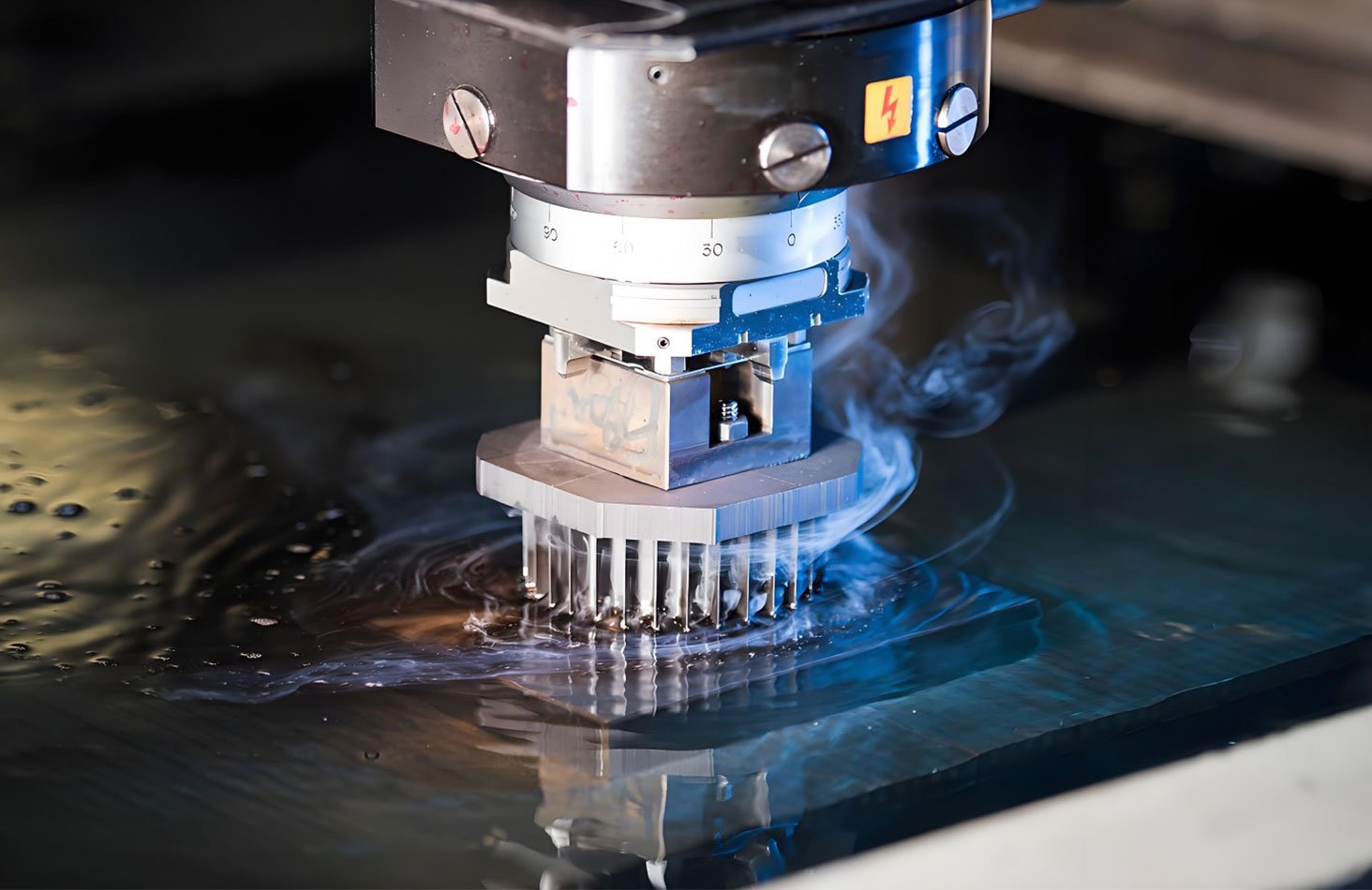
2. EDM:
L'elettroerosione utilizza scariche elettriche per erodere il materiale, consentendo la creazione di forme complesse, cavità profonde e geometrie interne intricate. Comprende varianti come l'elettroerosione a tuffo per cavità dettagliate e l'elettroerosione a filo per tagli precisi, che la rendono adatta a canali di flusso stretti e angoli acuti.
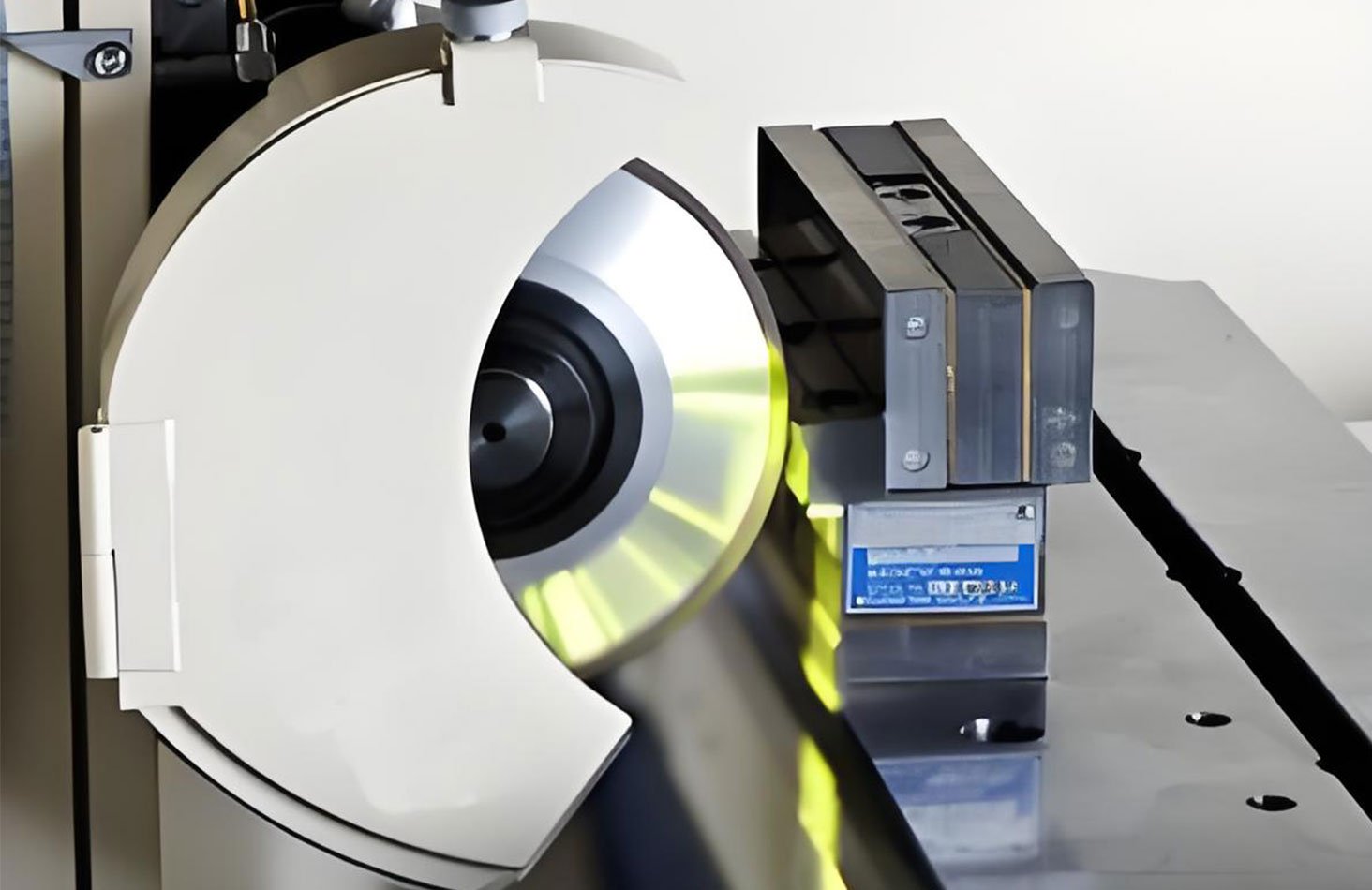
3. Rettifica:
La rettifica viene utilizzata per migliorare la finitura superficiale e la precisione dei componenti dello stampo rimuovendo piccole quantità di materiale attraverso l'azione abrasiva. Viene comunemente impiegata nelle fasi finali della produzione di stampi per ottenere superfici lisce e rispettare tolleranze dimensionali ristrette.
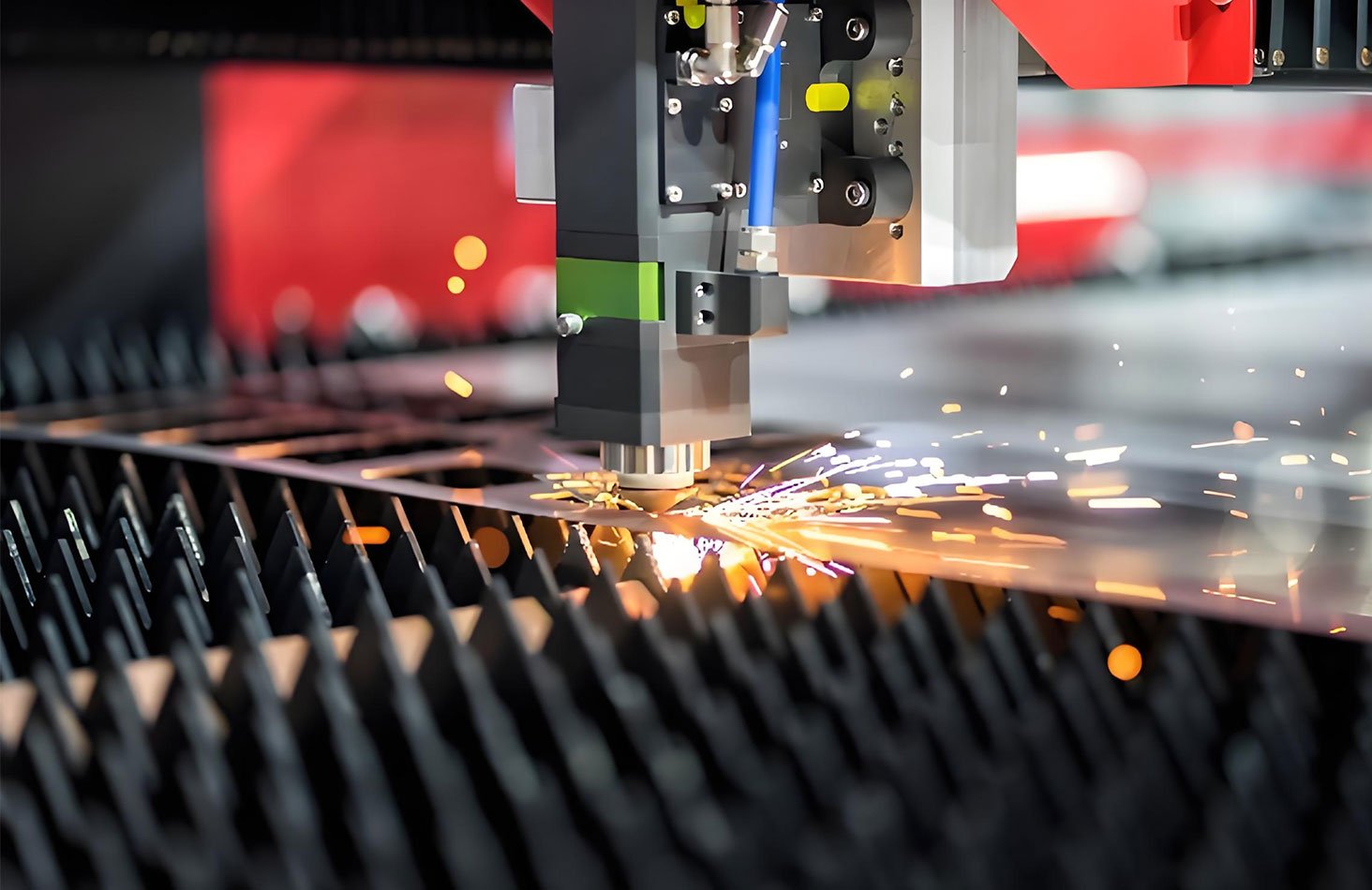
4. Taglio laser:
Il taglio laser utilizza un raggio laser ad alta potenza per tagliare e modellare il materiale dello stampo con eccellente precisione. Viene comunemente utilizzato per lastre sottili o per creare modelli intricati nei componenti dello stampo, offrendo una soluzione di taglio rapida ed efficiente.
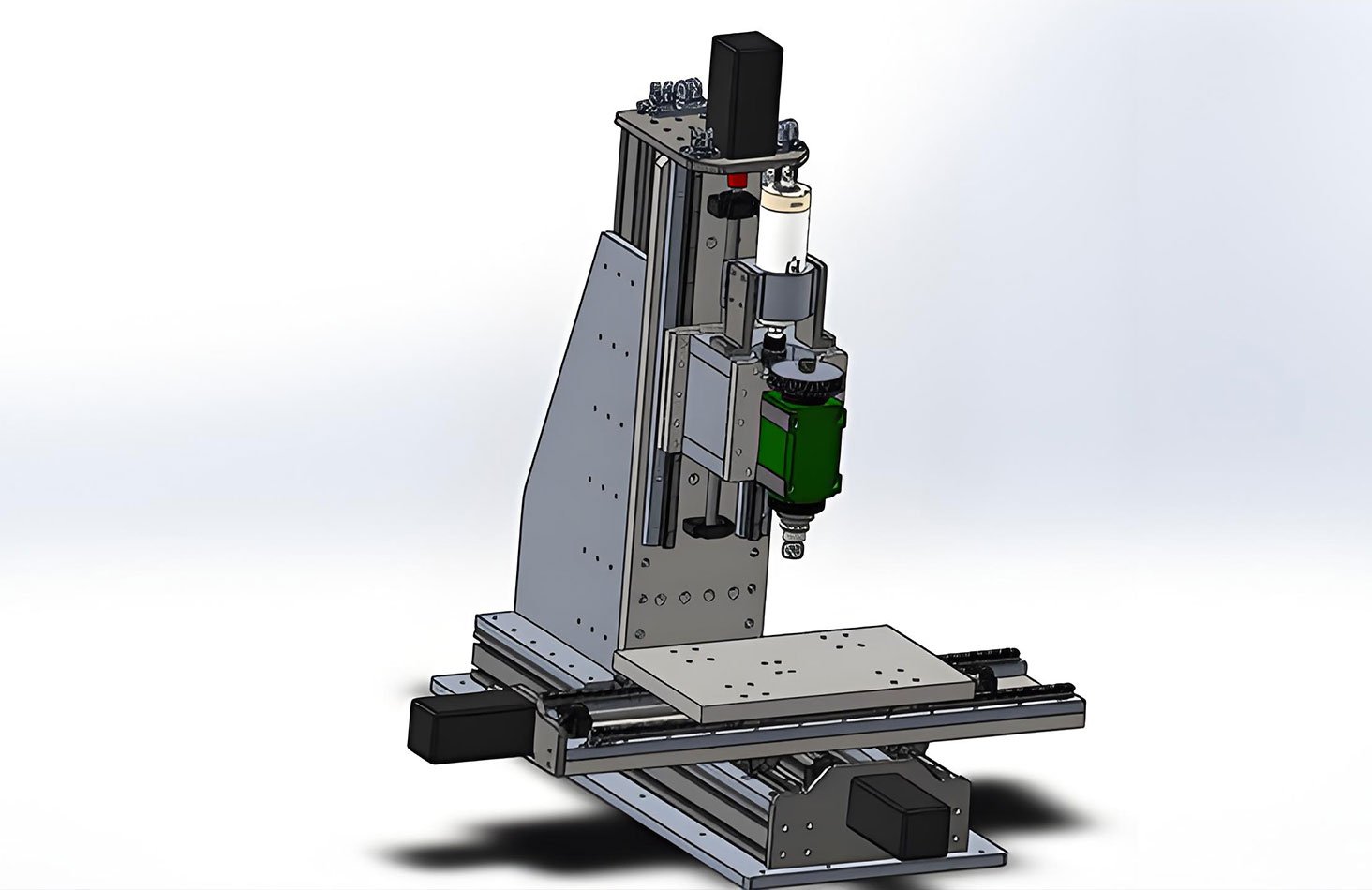
5. Fresatura:
La fresatura prevede l'uso di un utensile da taglio rotante, o fresa, per rimuovere il materiale da un pezzo. Questa tecnica è ideale per la lavorazione di grandi superfici piane con un'elevata precisione, nonché per la creazione di scanalature, contorni e altre caratteristiche complesse nei componenti degli stampi.
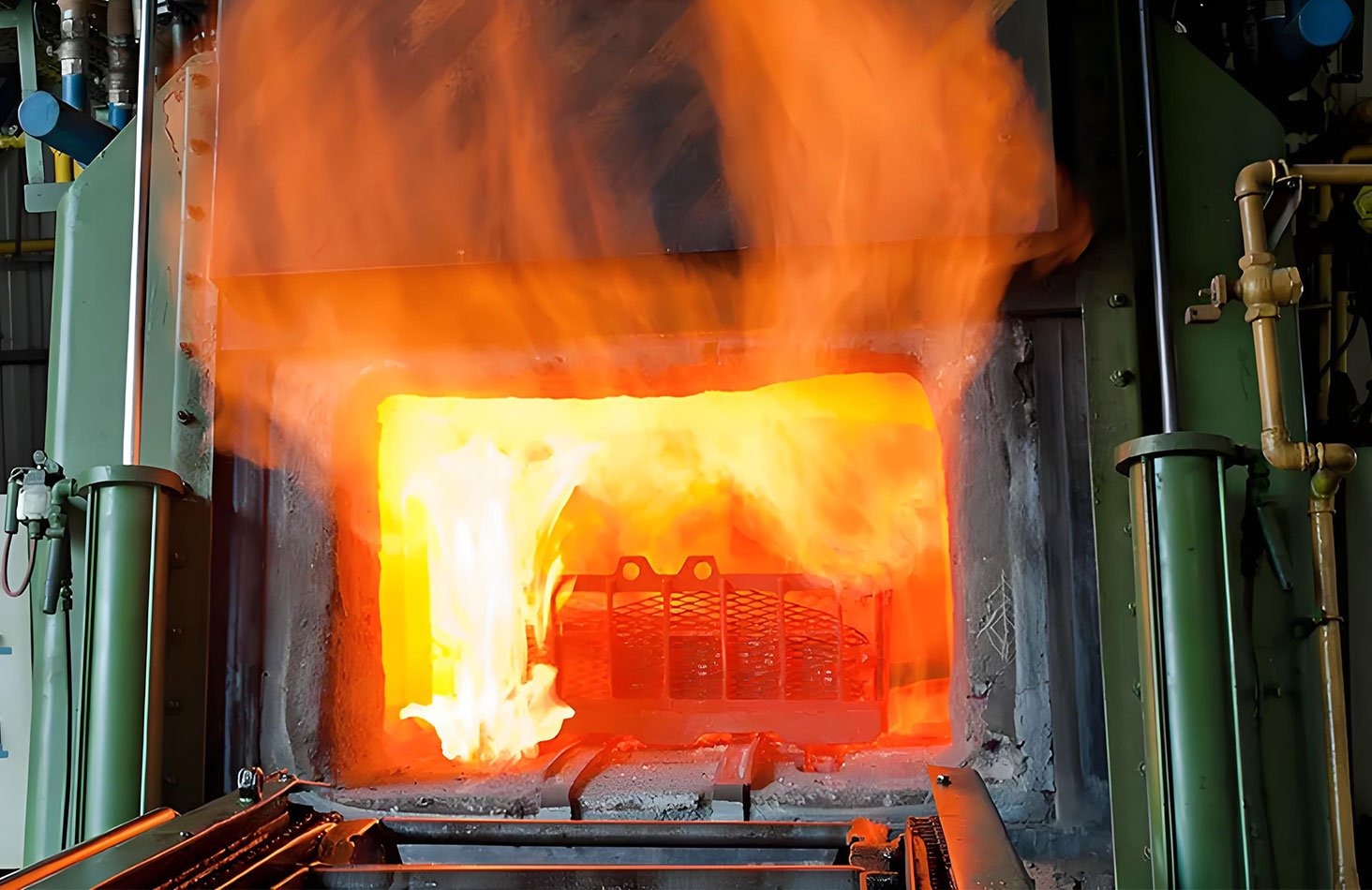
6. Trattamento termico:
I processi di trattamento termico, come la tempra, il rinvenimento e l'indurimento superficiale, sono utilizzati per migliorare le proprietà dei materiali degli stampi. Questi trattamenti migliorano la durata, la resistenza all'usura e la forza degli stampi, garantendo che soddisfino le esigenze di applicazioni ad alte prestazioni.
Quali sono i processi di produzione degli stampi per estrusione di plastica?
La produzione di stampi per estrusione di materie plastiche coinvolge diversi processi chiave che trasformano le materie prime in stampi funzionali per l'estrusione di materie plastiche. Di seguito è riportata una ripartizione dettagliata di questi processi, che combina fasi generali e considerazioni specifiche per garantire la massima qualità e le migliori prestazioni:
Fase 1: progettazione e ingegnerizzazione:
La fase di progettazione e ingegnerizzazione è il primo passo nella produzione di stampi per estrusione di plastica. Vengono creati progetti dettagliati con l'ausilio di software CAD (Computer-Aided Design) e vengono effettuate simulazioni per garantire che lo stampo sia in grado di soddisfare le specifiche del prodotto e di gestire il flusso del materiale e le sollecitazioni termiche. In questa fase si tiene conto del tipo di plastica, della sua viscosità, delle dimensioni del prodotto, delle tolleranze e della compatibilità con la macchina di estrusione. Il progetto definitivo deve ridurre al minimo i difetti e ottimizzare il processo produttivo, garantendo una produzione efficiente e senza intoppi.
Fase 2: selezione del materiale:
La scelta del materiale giusto per lo stampo è fondamentale per garantire la durata, la resistenza all'usura e la capacità di sopportare le elevate pressioni e temperature che si incontrano durante l'estrusione. I materiali più comunemente utilizzati includono acciai per utensili come il P20, l'H13 o l'acciaio inossidabile. Nella scelta dei materiali si devono considerare fattori quali la temperatura e la pressione di esercizio, il tipo di plastica utilizzata e l'equilibrio tra costo e prestazioni. I materiali di alta qualità garantiscono la longevità e la stabilità dello stampo in condizioni difficili.
Fase 3: lavorazione:
Dopo aver completato la progettazione e la selezione dei materiali, lo stampo entra nella fase di lavorazione. Per produrre i componenti dello stampo si utilizzano tecniche di lavorazione ad alta precisione, tra cui fresatura, tornitura, foratura ed elettroerosione (Electrical Discharge Machining). Questi metodi assicurano che lo stampo soddisfi i requisiti di precisione dimensionale, con l'elettroerosione particolarmente utile per i dettagli più complessi. È essenziale ottenere finiture superficiali lisce per ridurre al minimo l'adesione della plastica durante l'estrusione e garantire una produzione efficiente.
Fase 4: trattamento termico:
Il trattamento termico è una fase cruciale per migliorare la forza e la resistenza all'usura dello stampo. I trattamenti termici più comuni comprendono la tempra, il rinvenimento e la nitrurazione, che migliorano la durezza dello stampo e gli consentono di resistere a pressioni e temperature elevate durante il processo di estrusione. È essenziale bilanciare la durezza con la tenacità per evitare la fragilità. Ridurre al minimo la distorsione durante il processo di trattamento è fondamentale per mantenere la precisione dello stampo.
Fase 5: lucidatura e finitura:
Dopo il trattamento termico, lo stampo viene sottoposto a lucidatura e finitura superficiale. Le superfici interne vengono lucidate per migliorare il flusso della plastica e la qualità della superficie del prodotto. Possono essere applicati anche rivestimenti come il cromo o il nichel per aumentare la resistenza alla corrosione e all'usura. La levigatezza della superficie dello stampo influisce direttamente sulle sue prestazioni e sulla sua durata, mentre il rivestimento aiuta a prevenire la corrosione e l'abrasione, assicurando che lo stampo rimanga durevole per tutto il suo ciclo di vita.
Fase 6: Montaggio:
Una volta che tutti i componenti sono stati lavorati e rifiniti, lo stampo viene assemblato con cura. Questo include l'allineamento delle cavità dello stampo, degli inserti e delle altre parti per garantire che tutto si incastri correttamente. Vengono applicati elementi di fissaggio e guarnizioni per garantire che lo stampo sia a prova di perdite e mantenga l'integrità dei percorsi di flusso durante l'estrusione. È importante attenersi a tolleranze ristrette durante l'assemblaggio per evitare problemi in produzione, assicurando che lo stampo funzioni correttamente in condizioni operative.
Fase 7: Test e convalida:
Dopo l'assemblaggio, lo stampo viene sottoposto a test in condizioni reali di estrusione utilizzando materiali campione. Lo scopo del test è quello di identificare eventuali problemi come flusso irregolare, perdite o imprecisioni dimensionali. Se vengono rilevati problemi, il progetto dello stampo o i parametri di processo vengono modificati per risolverli. Grazie a test e perfezionamenti rigorosi, lo stampo viene convalidato per soddisfare i requisiti di produzione, garantendo una produzione costante e di alta qualità.
Fase 8: Manutenzione e documentazione:
Per garantire che lo stampo funzioni in modo affidabile nel tempo, viene sviluppato un programma di manutenzione. La pulizia, la lubrificazione e le ispezioni regolari sono essenziali e i componenti usurati devono essere sostituiti tempestivamente. È inoltre necessario conservare una documentazione dettagliata dei file di progettazione, dei parametri di lavorazione e dei registri di manutenzione per poterli consultare in futuro. Le buone pratiche di manutenzione aiutano a ridurre al minimo i tempi di inattività e a prolungare la durata di vita dello stampo, garantendo una produzione efficiente a lungo termine.
Come vengono utilizzati gli stampi per estrusione in diversi settori?
Gli stampi per estrusione sono uno strumento versatile ed essenziale in molti settori industriali per la creazione di un'ampia gamma di prodotti. Modellando i materiali attraverso uno stampo, gli stampi per estrusione consentono la produzione efficiente e continua di articoli con profili trasversali complessi. Di seguito viene illustrato nel dettaglio l'utilizzo degli stampi per estrusione in vari settori.
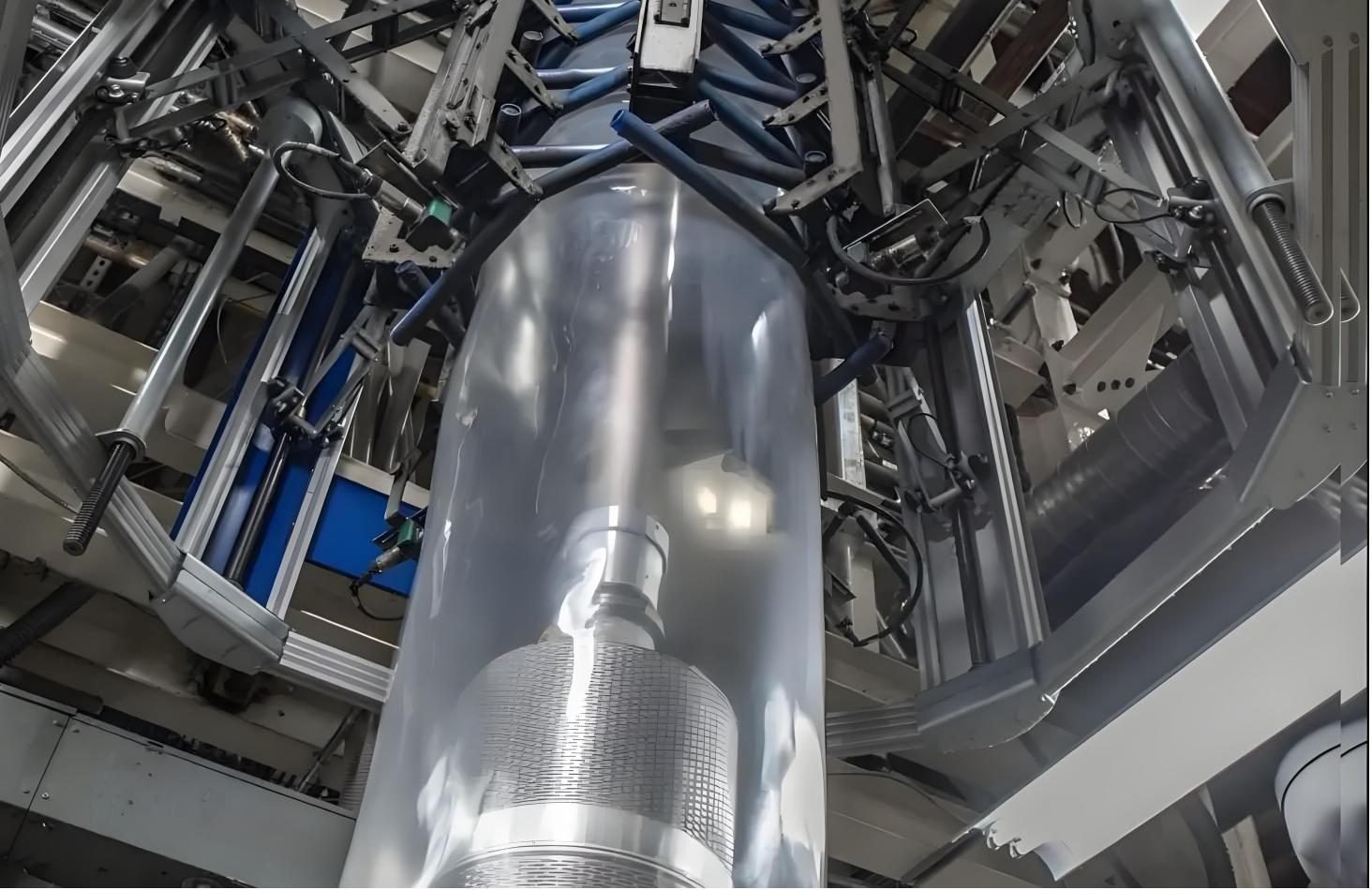
1. Industria dell'imballaggio:
Nell'industria dell'imballaggio, gli stampi per estrusione sono utilizzati per produrre vari materiali di imballaggio in plastica, tra cui bottiglie, contenitori e tubi per alimenti, bevande e prodotti per la cura personale. I materiali più comuni sono il polietilene (PE), il polipropilene (PP) e il PET, ideali per creare soluzioni di imballaggio leggere, flessibili ed economiche. Il processo di estrusione garantisce una produzione in grandi volumi con scarti minimi, soddisfacendo la domanda del settore di articoli prodotti in serie con qualità costante.
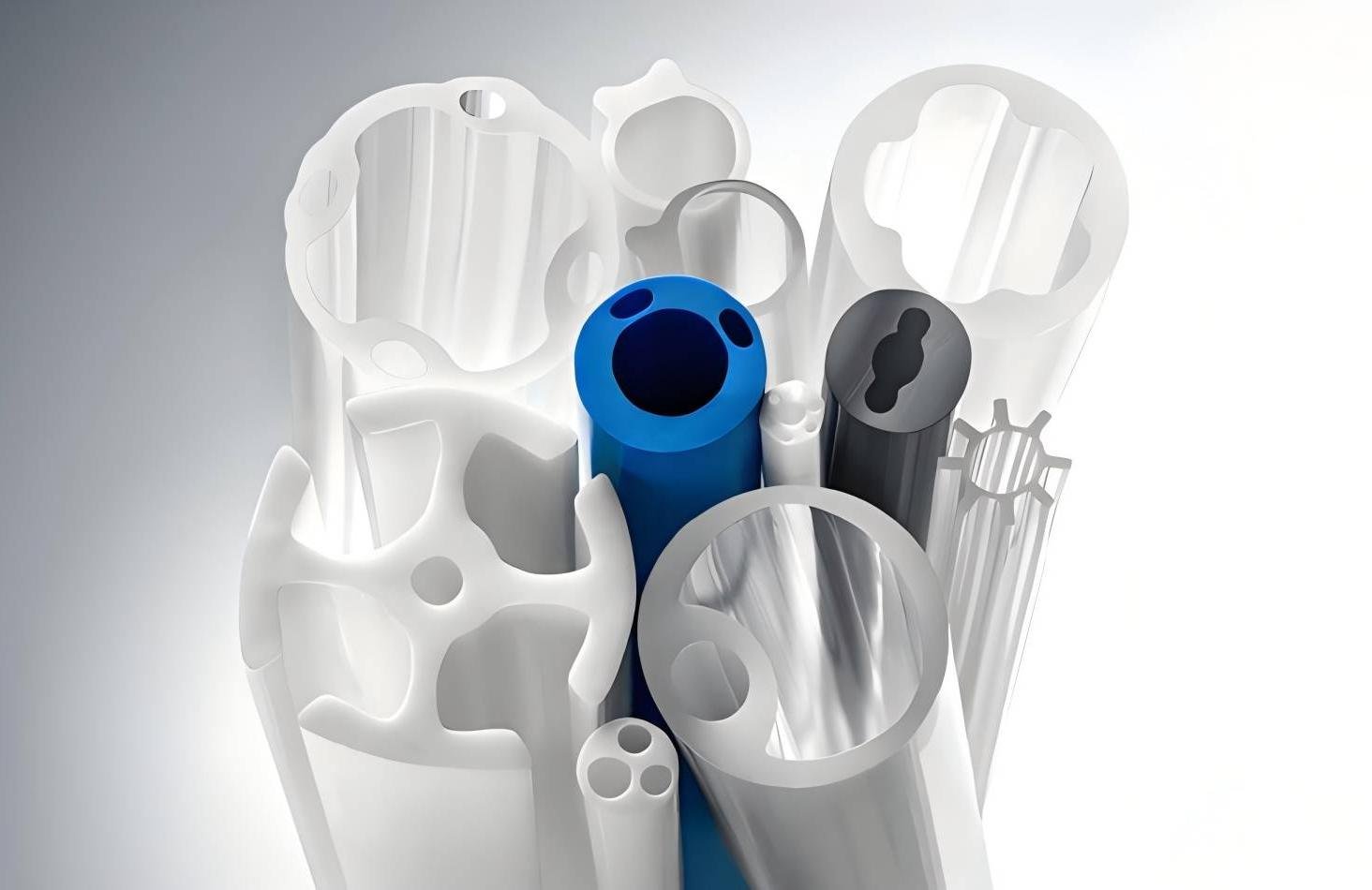
2. Industria medica:
Gli stampi per estrusione sono essenziali nell'industria medica per la produzione di dispositivi come cateteri, fili guida, tubi chirurgici e dispositivi impiantabili. Materiali come PVC, polietilene (PE) e polipropilene (PP) sono comunemente utilizzati per la loro biocompatibilità e durata. La precisione dell'estrusione garantisce la conformità dei componenti medicali ai severi standard normativi in materia di sicurezza, igiene e prestazioni, rendendoli fondamentali per la produzione di prodotti medicali affidabili e di alta qualità.
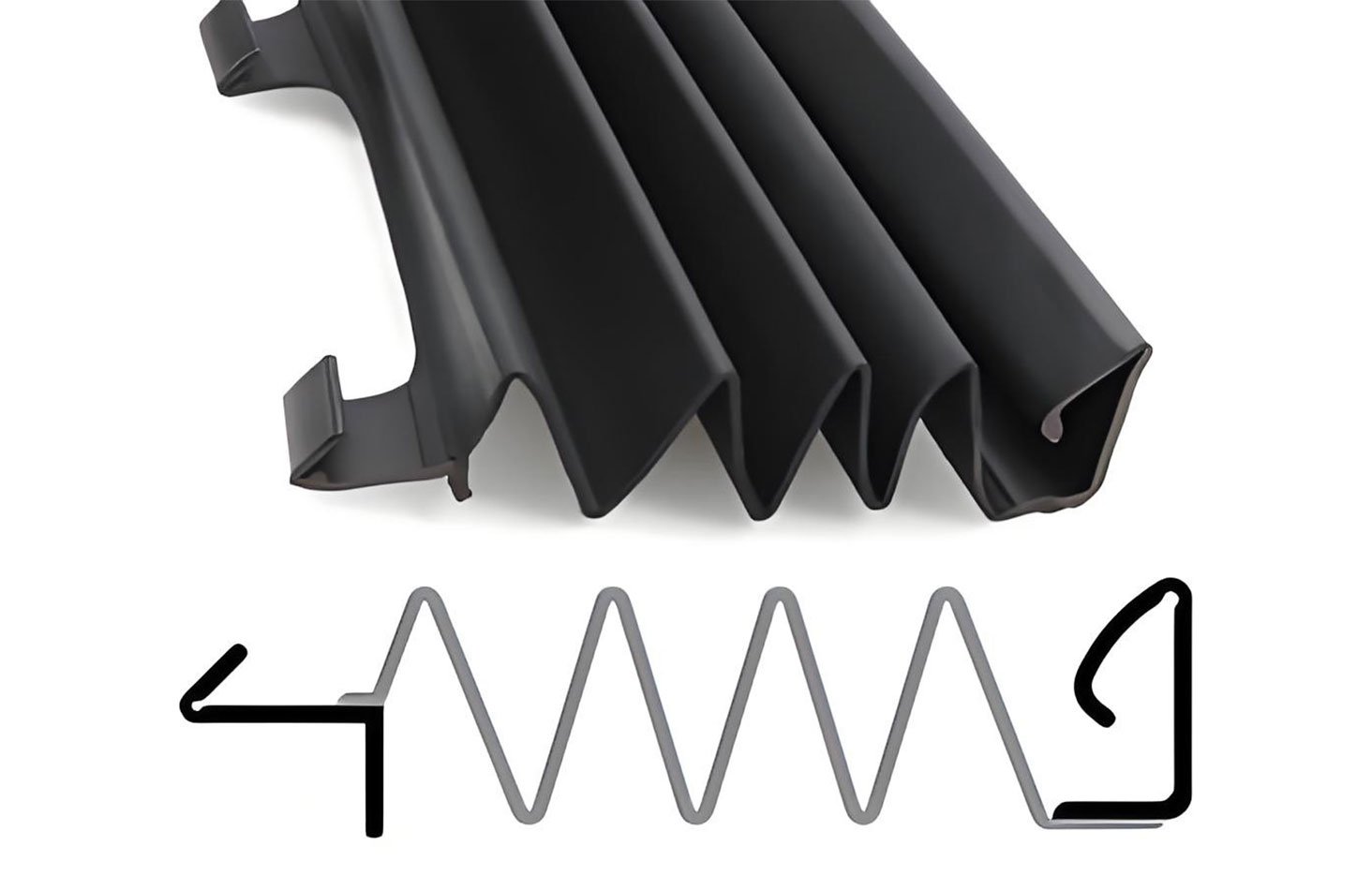
3. Industria automobilistica:
Nel settore automobilistico, gli stampi per estrusione sono utilizzati per produrre componenti leggeri ma resistenti, come tubi del carburante, tubi dei freni, condotti dell'aria, cornici dei finestrini e guarnizioni per gli agenti atmosferici. I materiali utilizzati sono alluminio, PVC e vari materiali termoplastici. Questi materiali offrono resistenza pur mantenendo un peso ridotto, che migliora le prestazioni del veicolo e l'efficienza dei consumi. Il processo di estrusione consente di produrre pezzi con forme e profili intricati, fondamentali per i moderni progetti automobilistici.
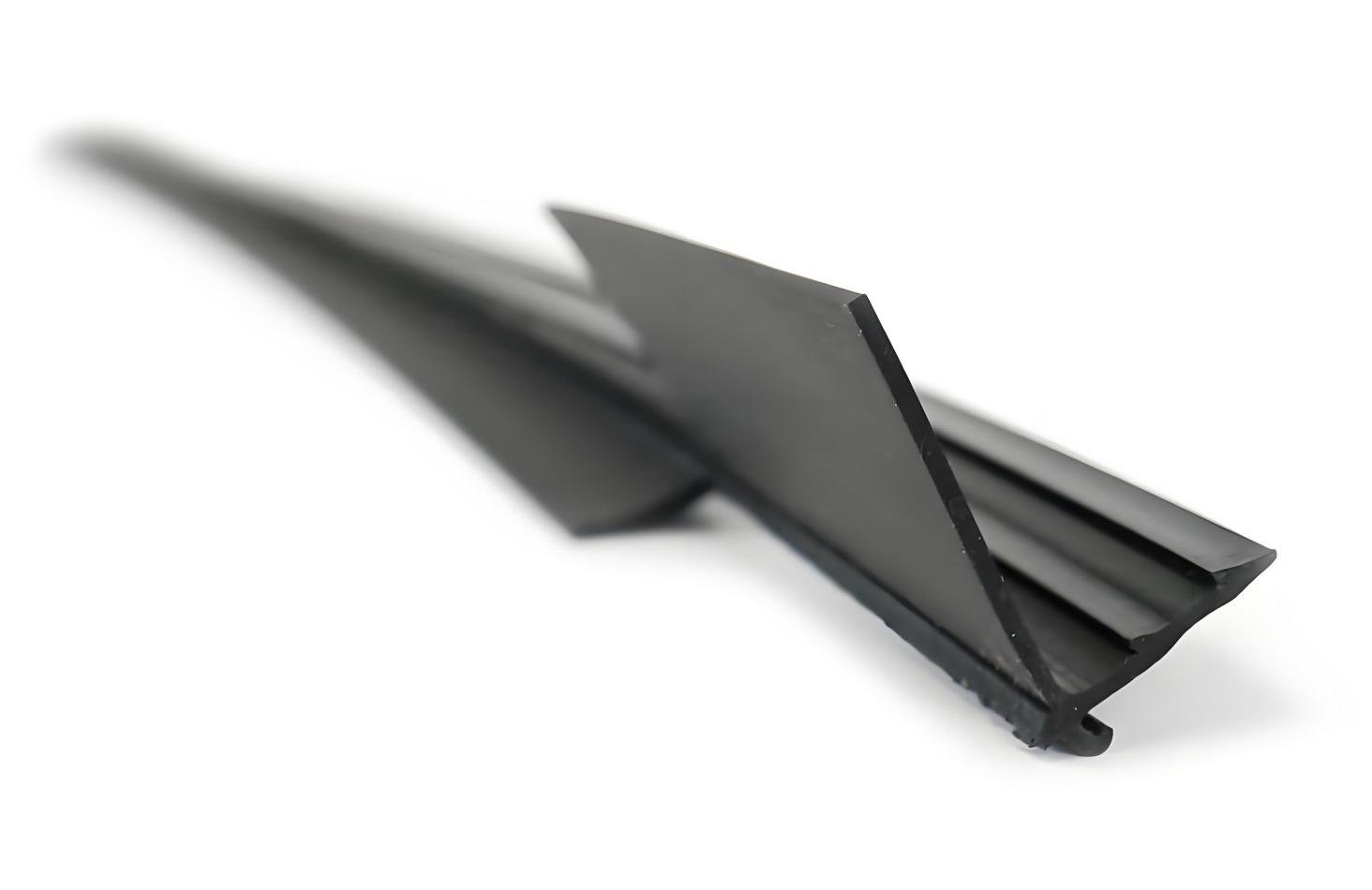
4. Industria aerospaziale:
Gli stampi per estrusione nell'industria aerospaziale sono utilizzati per creare componenti leggeri e ad alta resistenza come linee di alimentazione, linee idrauliche ed elementi strutturali. Materiali come l'alluminio, le leghe di titanio e i polimeri specializzati vengono utilizzati per soddisfare i severi requisiti di prestazione delle applicazioni aerospaziali. La precisione e l'affidabilità del processo di estrusione assicurano che i componenti aerospaziali siano leggeri e durevoli, contribuendo a migliorare l'efficienza e la sicurezza nella progettazione degli aerei.

5. Industria dei beni di consumo:
Gli stampi per estrusione sono ampiamente utilizzati nell'industria dei beni di consumo per produrre prodotti di uso quotidiano come giocattoli, articoli per la casa, componenti per mobili e pellicole per imballaggi. In genere si utilizzano materiali come il PVC, il PET e il polistirene (PS), che offrono un equilibrio tra durata, flessibilità ed economicità. Il processo di estrusione consente la produzione di massa di beni di consumo leggeri, durevoli ed esteticamente diversi, soddisfacendo l'elevata richiesta di qualità e design costanti.
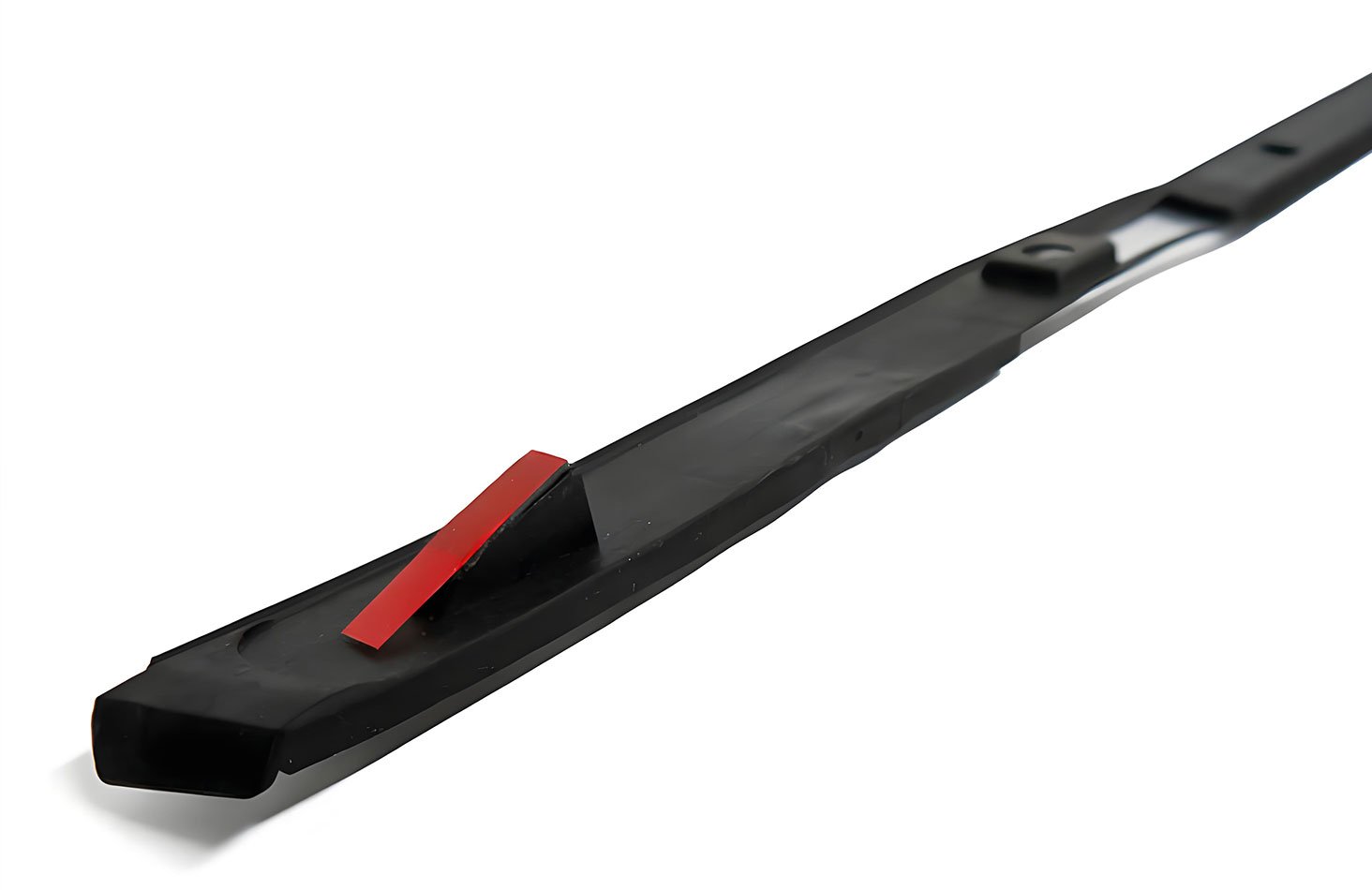
6. Industria tessile:
Nel settore tessile, gli stampi per estrusione creano fibre sintetiche, filati e tessuti utilizzati nell'abbigliamento, nella tappezzeria e nei tessuti industriali. Materiali come il polietilene tereftalato (PET), il nylon e l'acrilico sono comunemente utilizzati per la loro resistenza, flessibilità e capacità di essere filati in fili sottili. Il processo di estrusione garantisce una produzione continua di fibre e tessuti, che possono essere tessuti o lavorati a maglia per creare prodotti tessili versatili e durevoli.
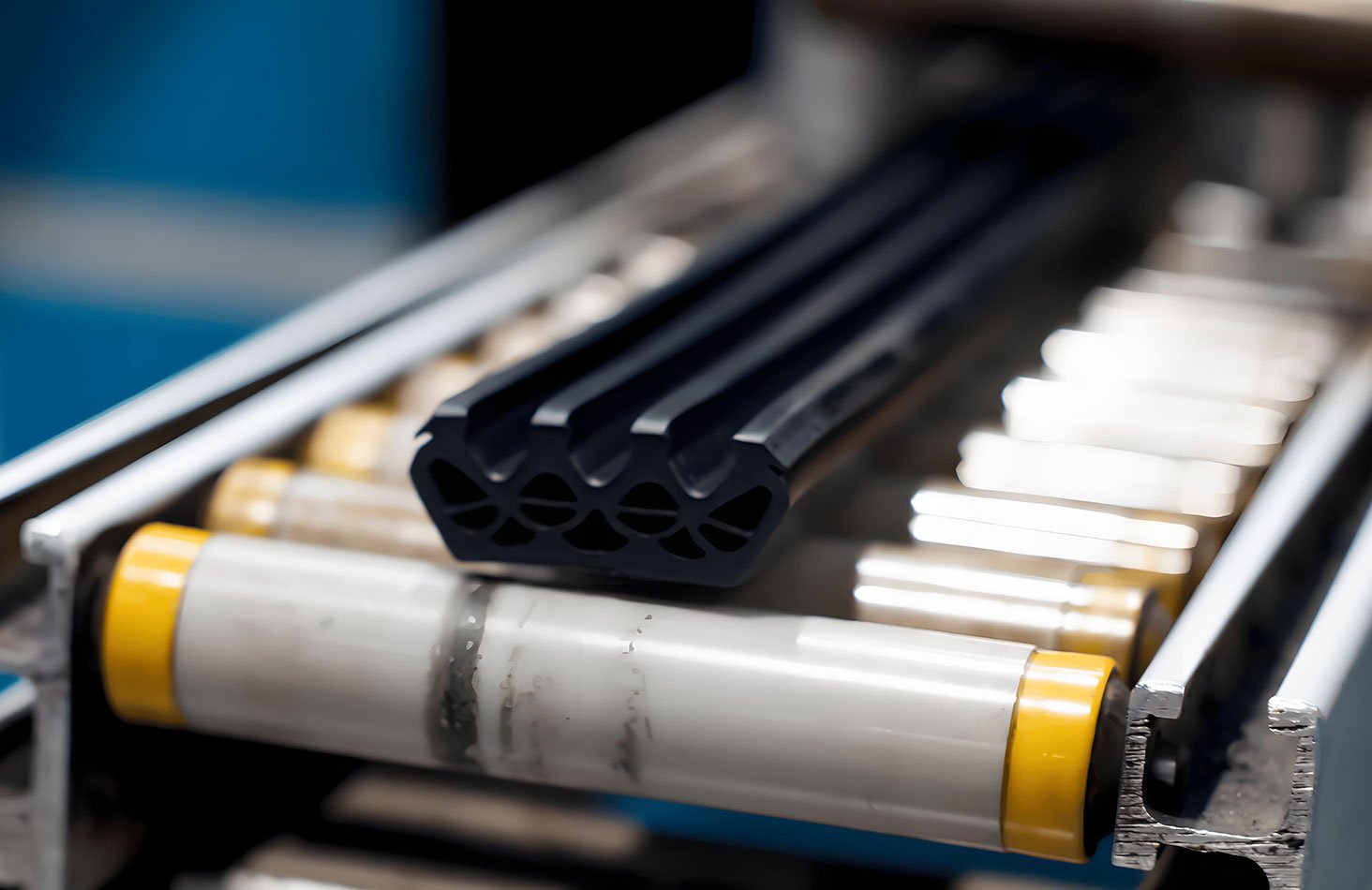
7. Industria marina:
Nell'industria nautica, gli stampi per estrusione sono utilizzati per creare componenti come impianti idraulici, sistemi di ventilazione e parti strutturali per barche e navi. Materiali come l'alluminio resistente alla corrosione sono comunemente utilizzati per resistere al duro ambiente marino. Il processo di estrusione offre una soluzione durevole e leggera per la creazione di componenti che devono sopportare l'esposizione all'acqua e ad altre condizioni difficili.
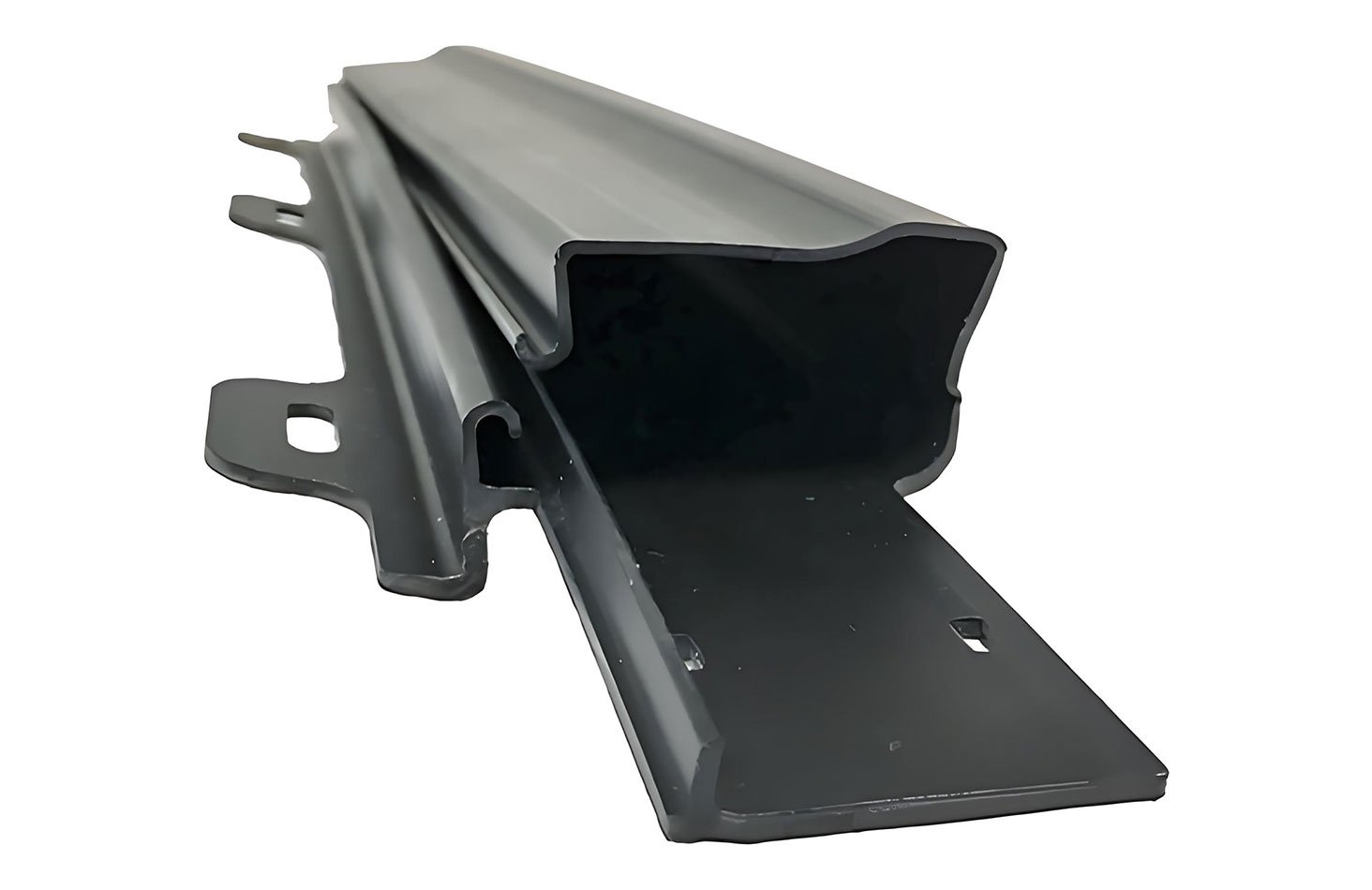
8. Industria delle costruzioni:
Nel settore delle costruzioni, gli stampi per estrusione sono utilizzati per produrre materiali come tubi, telai di finestre e porte e componenti strutturali, tra cui travi e canali. I materiali più comuni sono il PVC, l'alluminio e l'acciaio. Il processo di estrusione consente di produrre sezioni lunghe e continue con profili personalizzati, il che lo rende ideale per la creazione di componenti edilizi che richiedono resistenza e durata, oltre a ridurre al minimo gli scarti di materiale durante la produzione.
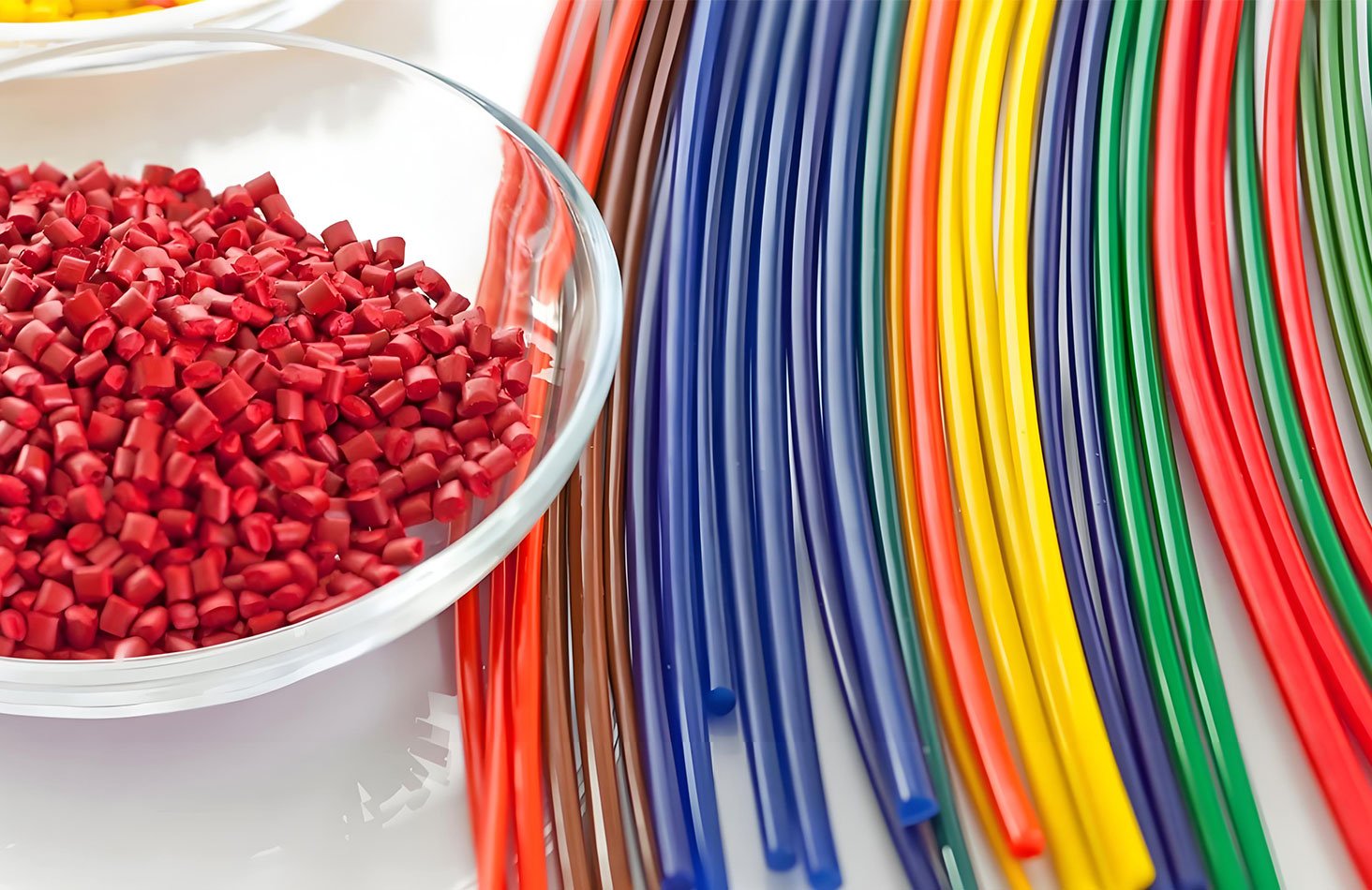
9. Industria elettrica ed elettronica:
Gli stampi per estrusione svolgono un ruolo fondamentale nell'industria elettrica ed elettronica, dove vengono utilizzati per creare componenti come dissipatori di calore, isolanti per fili, guaine per cavi e involucri per dispositivi elettronici. Materiali come la termoplastica e l'alluminio sono comunemente utilizzati per garantire durata, flessibilità e isolamento elettrico. La precisione dell'estrusione assicura che questi componenti siano prodotti con uniformità e soddisfino le specifiche richieste per le prestazioni e la sicurezza dei sistemi elettrici.

10. Industria farmaceutica:
Nell'industria farmaceutica, gli stampi per estrusione sono utilizzati per produrre prodotti come involucri di compresse, capsule e siringhe. I materiali utilizzati comprendono materiali termoplastici come il PVC, che forniscono le proprietà necessarie per la produzione di prodotti di grado medico. Il processo di estrusione è essenziale per garantire che i componenti farmaceutici siano prodotti con elevata precisione e soddisfino i rigorosi standard di igiene e sicurezza, assicurando che ogni prodotto sia affidabile e sicuro per l'uso medico.
Domande frequenti per i clienti
Come iniziare con Uplastech
Avete domande? Abbiamo le risposte.
Siamo specializzati nei processi di estrusione e nella costruzione di stampi di precisione, offrendo soluzioni personalizzate per soddisfare le vostre esigenze di produzione.
Lavoriamo con diversi settori, tra cui quello automobilistico, elettronico e dei beni di consumo, concentrandoci sulle partnership B2B.
Sì, personalizziamo le nostre soluzioni per adattarle alle vostre esigenze specifiche.
Entrare in contatto
Inviateci un'e-mail o compilate il modulo sottostante per ottenere un preventivo.
Email: uplastech@gmail.com