Fabricant de profilés PP sur mesure
Découvrez les profils PP personnalisés pour l'extrusion de plastiques solides, résistants à la chaleur et aux chocs. Idéal pour l'automobile, la construction et bien plus encore. Demandez un devis !
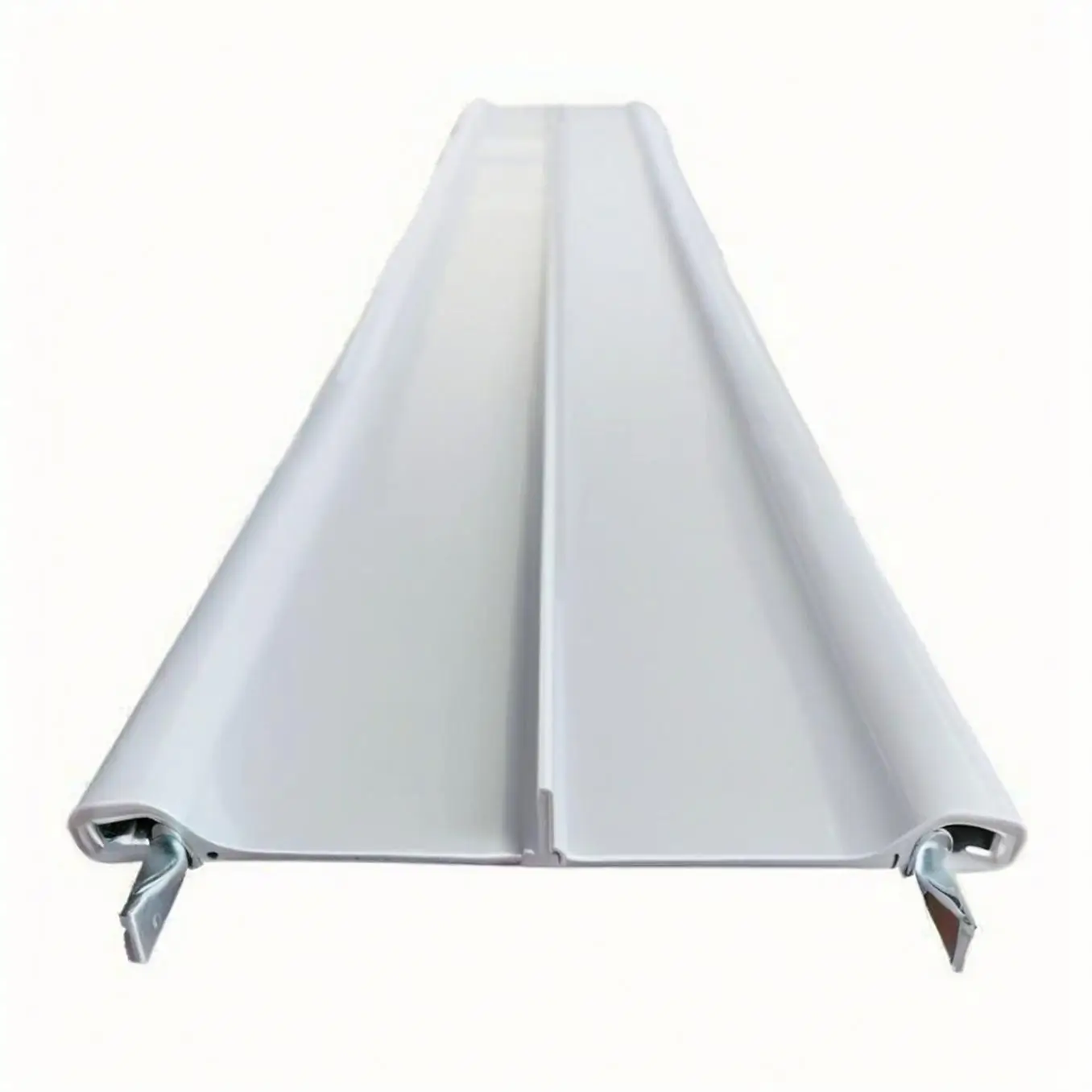
Profil de couverture en PP
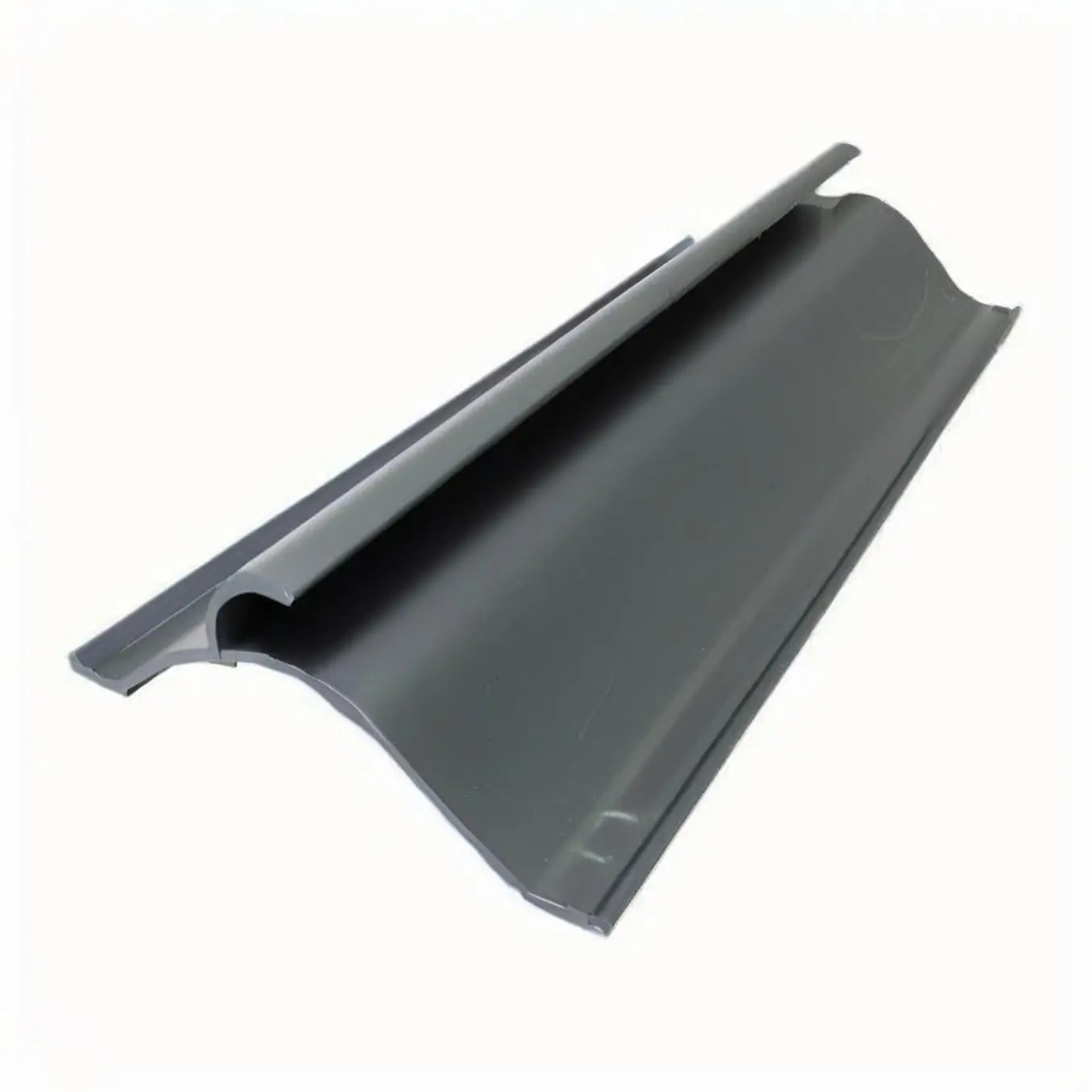
Profil de barrière à l'eau en PP
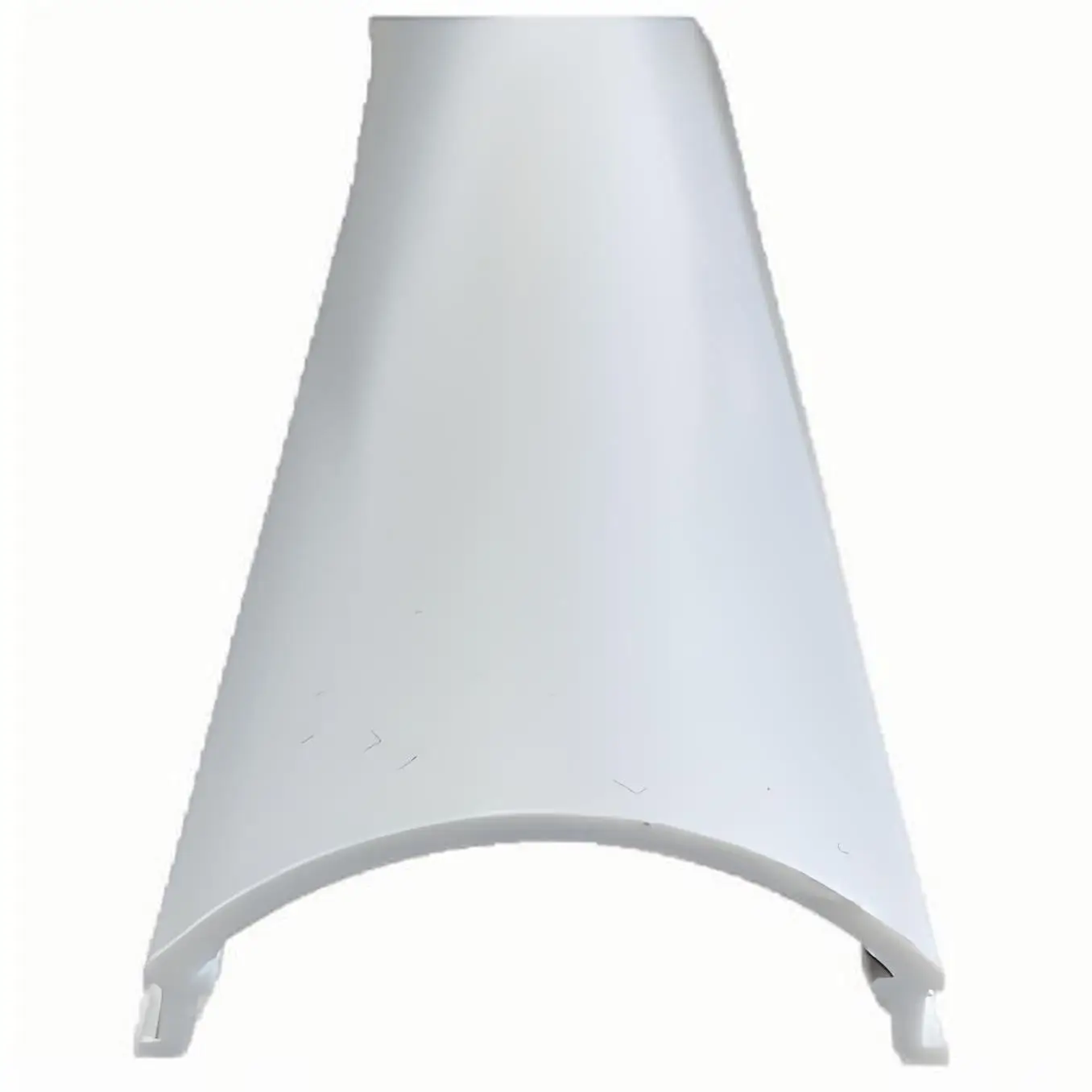
Profil anticollision en PP
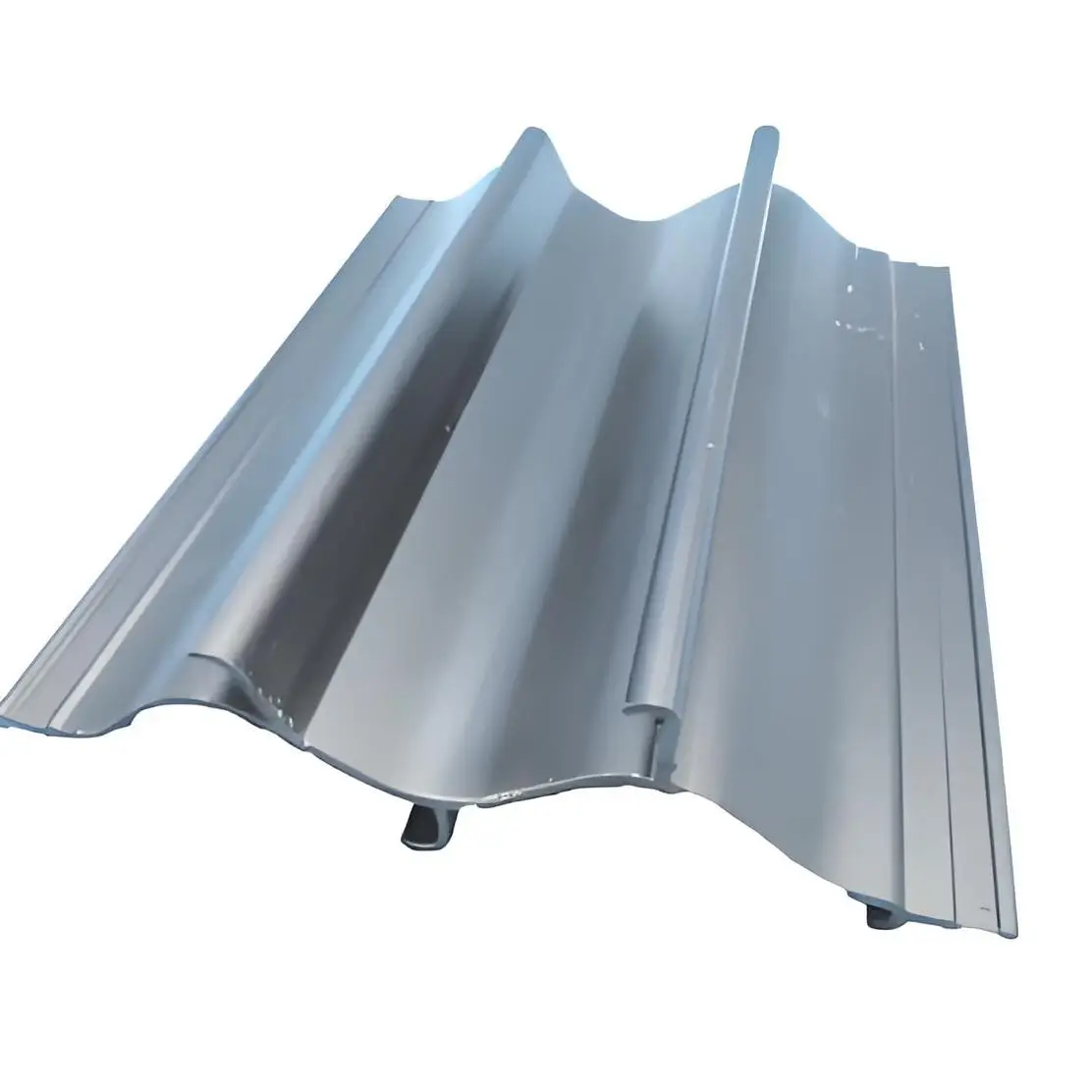
Lame de désembuage en PP
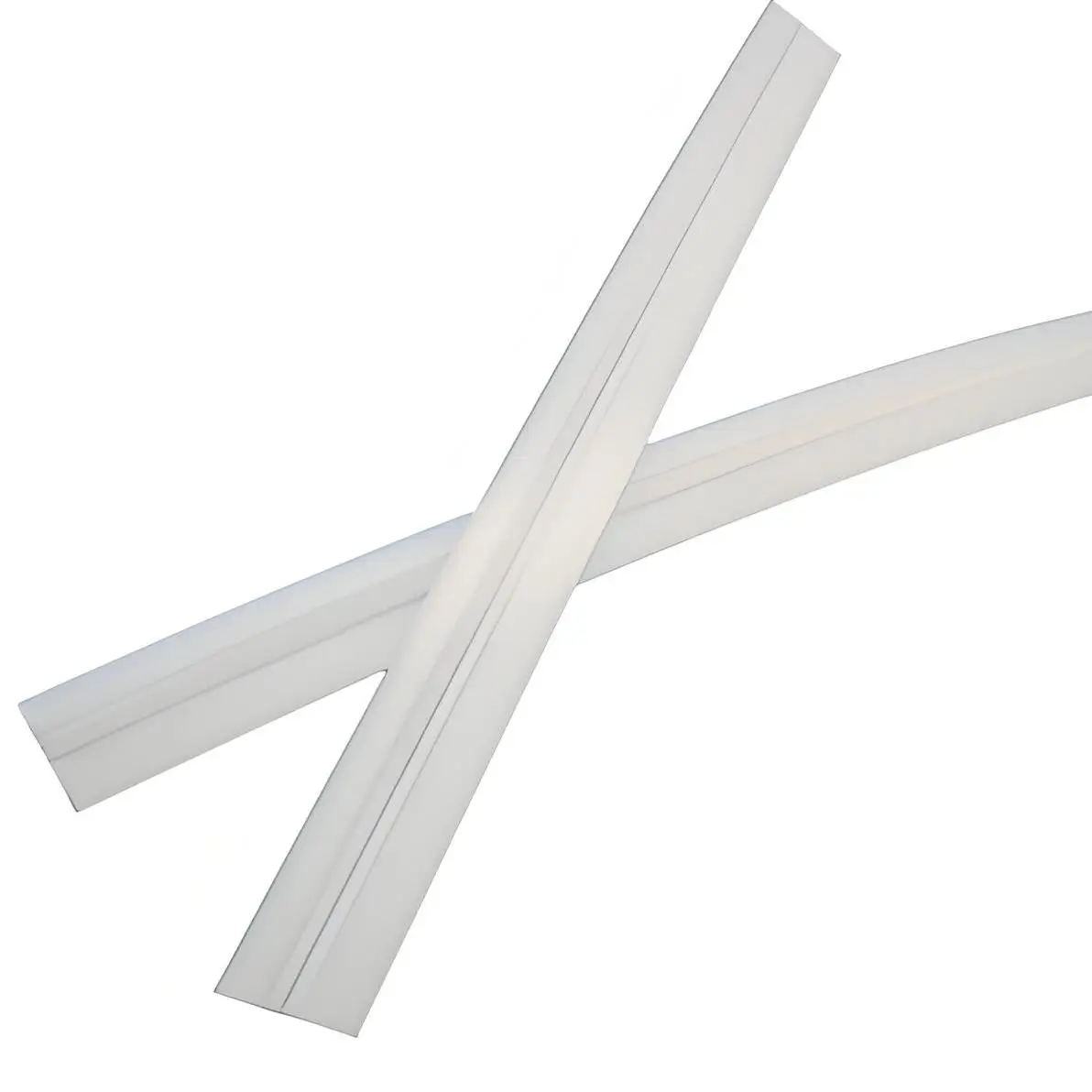
Bande de serrage en PP
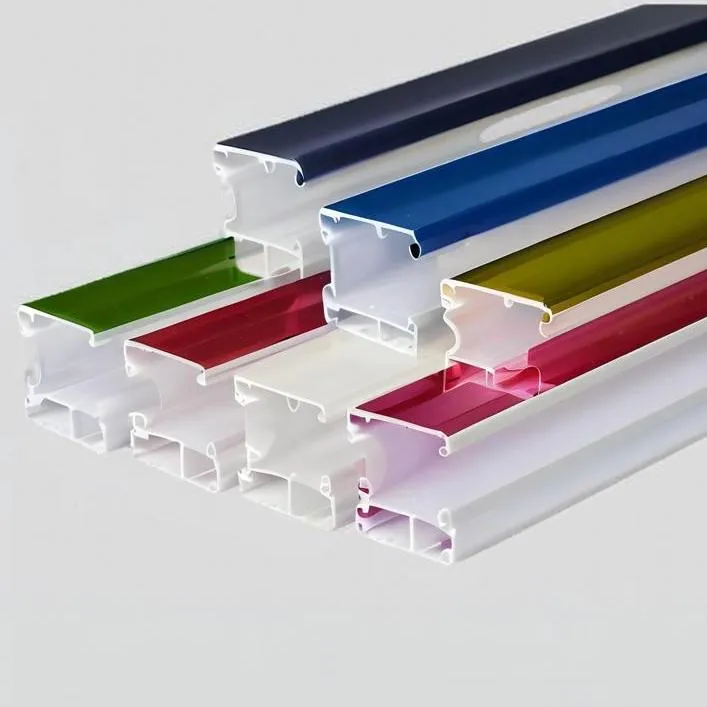
Guide pour la fabrication de profilés d'extrusion en PP sur mesure
Qu'est-ce qu'un profil PP ?
Les profilés PP (profilés en polypropylène) sont des profilés en plastique fabriqués par des procédés d'extrusion de plastique, à partir de polypropylène (PP). Les principales caractéristiques et applications sont les suivantes
1. Caractéristiques principales et traitement :
① Processus d'extrusion :
- Les granulés de PP sont fondus à 170-240℃ dans une extrudeuse à vis, puis mis en forme dans des moules et rapidement refroidis.
Permet la personnalisation de petites séries pour des conceptions transversales complexes.
② Avantages des matériaux :
- Résistance à la corrosion : Stable aux acides, aux alcalis et aux solvants organiques, idéal pour les revêtements d'équipements chimiques.
- Léger : Densité de 0,90-0,91 g/cm³, réduisant les coûts de transport et d'installation.
- Conformité aux normes médicales : Conforme aux normes de biocompatibilité pour les dispositifs médicaux et les emballages.
③ Applications :
- Industrie : Tuyaux résistants à la corrosion, gaines de câbles, châssis d'équipement.
- Médical : tubes de perfusion, composants d'instruments chirurgicaux.
- Construction : Cloisons légères, joints étanches.
2. Fabrication sur mesure :
Les fabricants professionnels de profilés PP personnalisés optimisent les performances en ajustant la conception du moule et en ajoutant des additifs (par exemple, des fibres de verre). Le traitement typique de l'extrusion du PP comprend le séchage, la fusion, le refroidissement et le post-traitement.
Où les profils PP sont-ils le plus souvent utilisés ?
Les profilés en PP (polypropylène) sont largement utilisés dans diverses industries en raison de leur résistance à la corrosion, de leur légèreté, de leur adaptabilité et de leur rentabilité. Vous trouverez ci-dessous les principaux scénarios d'application et les caractéristiques correspondantes du processus d'extrusion plastique, analysés en fonction des besoins de l'industrie :
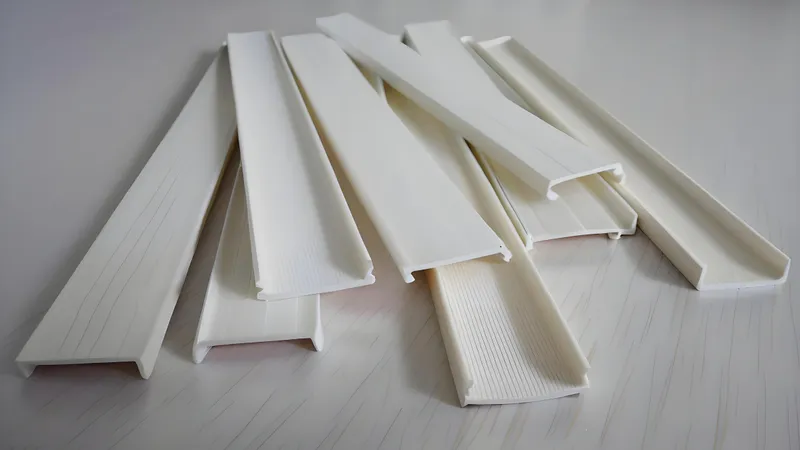
1. Construction et ameublement :
① Systèmes d'étanchéité:Les profilés en PP excellent dans les joints de fenêtre/porte et les protections d'angle en raison de leur adaptabilité aux conditions météorologiques et de leur flexibilité thermique. La co-extrusion avec le TPE améliore l'étanchéité à l'air et la durée de vie, tandis que les garnitures décoratives maintiennent l'intégrité structurelle au fil des saisons. La conception des moules permet l'intégration de plusieurs matériaux pour des géométries complexes.
② Systèmes de conduits de ventilation:Les grilles en PP antimicrobien optimisent la circulation de l'air à l'intérieur et sont conçues de manière modulaire pour une installation rapide. Les sections transversales personnalisées obtenues grâce à des moules de précision garantissent la compatibilité avec les plans architecturaux. Les propriétés de légèreté réduisent les contraintes de charge tout en maintenant la stabilité chimique dans les environnements humides.
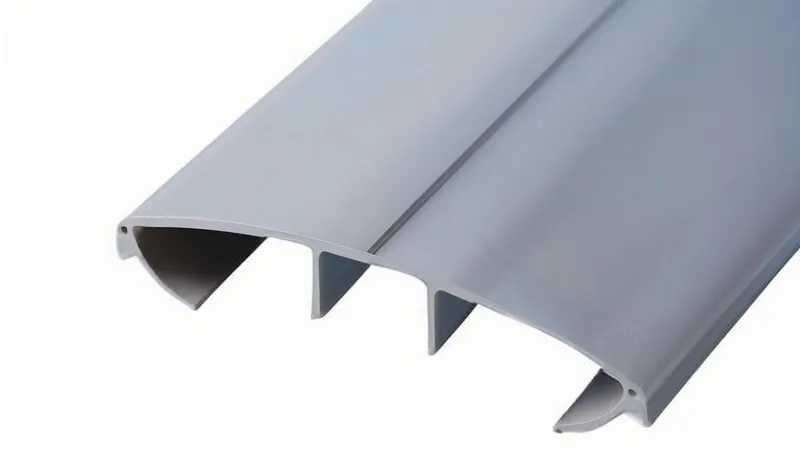
2. Appareils ménagers et électroniques :
① Joints pour réfrigérateur/congélateur:L'extrusion hybride TPE-PP équilibre l'élasticité et la résistance au gel, empêchant les fuites de condensation. Les structures multicouches résistent aux mouvements fréquents de la porte, tandis que la stabilisation aux UV préserve l'intégrité du joint dans divers climats. Des gradients de dureté personnalisés répondent aux exigences d'étanchéité spécifiques à chaque compartiment.
② Boîtiers électroniques:Les boîtiers en PP à paroi mince protègent les composants de l'humidité et de la corrosion grâce à des traitements de surface à l'échelle nanométrique. L'extrusion de haute précision garantit une tolérance de ±0,1 mm pour les assemblages sensibles à la chaleur. Les formulations ignifuges répondent aux normes IEC sans compromettre la recyclabilité.
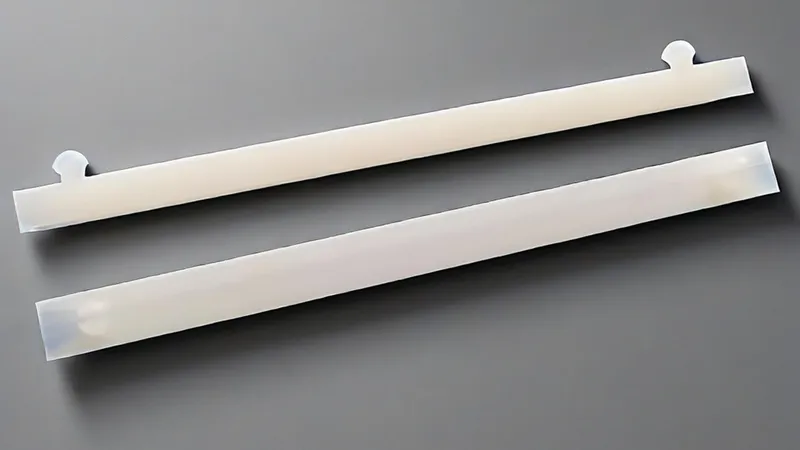
3. Équipement médical et sanitaire:
① Composants d'instruments de qualité médicale : Les profilés en PP sont utilisés dans les mains courantes et les rails des armoires à pharmacie. Ils doivent répondre à des normes de non-toxicité et de résistance chimique afin de garantir la sécurité et la fiabilité.
② Matériel de laboratoire : Les profilés en PP résistent aux acides et aux bases, ce qui les rend idéaux pour les environnements de laboratoire. Le processus d'extrusion peut intégrer des modificateurs antistatiques pour garantir la sécurité et le respect des normes.
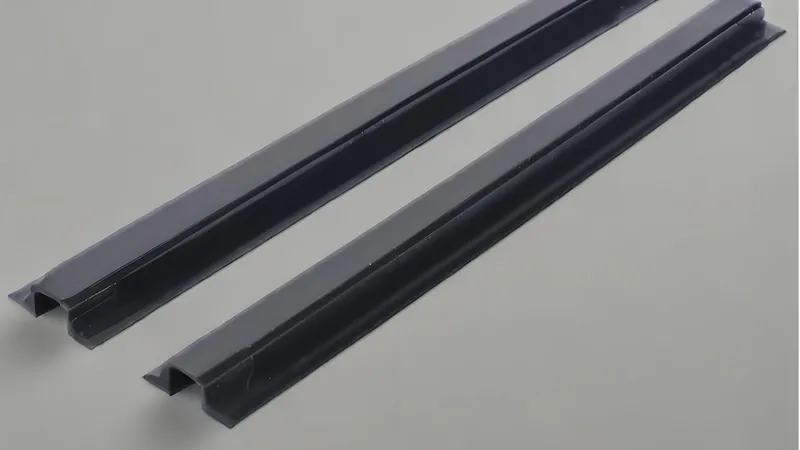
4. Automobile et transports :
① Pièces intérieures et fonctionnelles : Les profilés en PP sont utilisés dans les supports de tableaux de bord et les gaines de faisceaux électriques. Le procédé de moulage par extrusion-injection permet d'intégrer des pièces complexes dans un seul moule.
② Pièces structurelles légères : Les propriétés de faible densité du PP lui permettent de remplacer les pièces métalliques, telles que les supports de bacs à batterie. Le processus d'extrusion permet d'optimiser la répartition de l'épaisseur des parois, ce qui améliore la résistance et la durabilité.
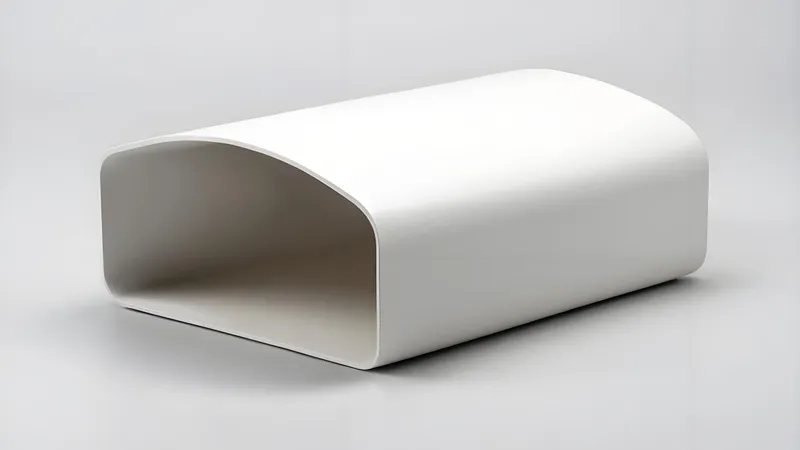
5. Tech: industrielle et environnementale
① Tuyaux et réservoirs résistants à la corrosion : Les profilés en PP sont utilisés dans les réservoirs de stockage de produits chimiques et de galvanoplastie, les techniques d'extrusion à paroi épaisse améliorant la résistance chimique dans les environnements difficiles.
② Composants de l'équipement environnemental : Les profilés en PP sont idéaux pour les supports de remplissage des tours de traitement des gaz résiduaires. Le processus d'extrusion permet de personnaliser les structures poreuses, en augmentant la surface pour améliorer les performances.
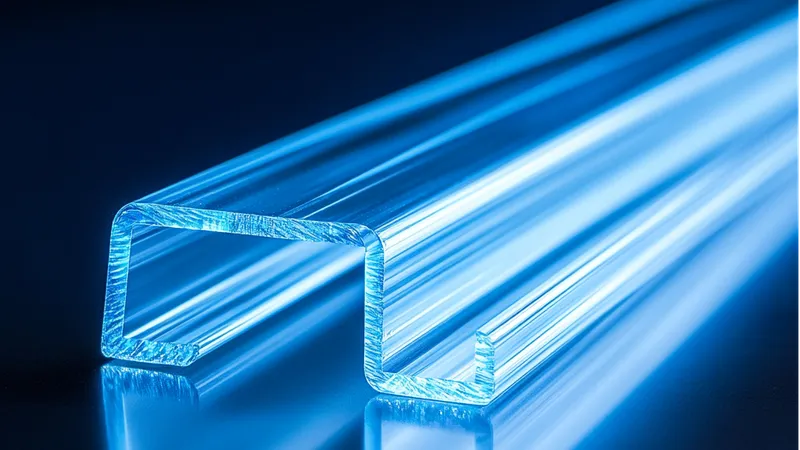
6. Avantages de la personnalisation:
① Personnalisation par petits lots : Des sections transversales personnalisées, telles que des bandes médicales anti-morsure ou des abat-jour à LED, peuvent être développées à la demande, la technologie de changement rapide des moules contribuant à réduire les coûts.
② Formulations améliorées:Les composites GF-PP 30% atteignent une résistance à la traction de 120MPa pour les rubans de construction sismique. Les systèmes FR sans halogène sont conformes à la norme UL94 V-0 à une épaisseur de 1,5 mm. Les mélanges carbone-noir conducteurs atteignent 10³Ω-cm pour les revêtements de sol industriels sécurisés contre les décharges électrostatiques (ESD).
Comment sont fabriqués les profilés en PP ? Un guide pas à pas
Les profilés en polypropylène (PP) sont largement utilisés dans diverses industries en raison de leur excellente durabilité, de leur résistance aux produits chimiques et de leur polyvalence. La fabrication des profilés en PP fait appel au processus d'extrusion du plastique, qui est une méthode efficace et rentable pour produire des profilés personnalisés en vrac. Vous trouverez ci-dessous un guide étape par étape sur la façon dont les profilés en PP sont généralement fabriqués :
1. Sélection et préparation des matériaux :
La première étape de la fabrication des profilés en PP consiste à sélectionner la qualité de polypropylène appropriée. Ce choix peut varier en fonction de l'utilisation prévue du profilé, qu'il s'agisse d'applications industrielles, médicales ou grand public. Pour les profilés en polypropylène de qualité médicale, le matériau doit répondre à des normes de qualité et de sécurité strictes.
Une fois le matériau choisi, il est préparé en ajoutant tous les additifs nécessaires, tels que des stabilisateurs UV, des antioxydants ou des colorants, afin d'améliorer les performances ou les qualités esthétiques du profilé.
2. Processus d'extrusion plastique :
Le cœur de la production de profilés en PP est l'extrusion du plastique, qui consiste à faire fondre les granulés de polypropylène et à forcer le matériau fondu à travers une filière pour créer un profilé continu. Le processus d'extrusion comprend les étapes clés suivantes :
① Alimentation : Les granulés de polypropylène sont chargés dans la trémie d'une extrudeuse, où ils sont transportés vers le cylindre.
② Chauffage et fusion : La matière est chauffée dans le cylindre de l'extrudeuse, où elle est progressivement fondue jusqu'à devenir visqueuse.
③ Extrusion : Le PP fondu est poussé à travers une matrice spécialement conçue pour donner la forme souhaitée au profilé. Il peut s'agir de formes simples ou de modèles plus complexes, en fonction de l'application. Les profils sont personnalisés en ajustant la matrice en conséquence.
④ Refroidissement : Une fois le profilé sorti de la matrice, il est refroidi à l'air ou à l'eau pour solidifier la forme.
Le traitement des profilés d'extrusion en PP nécessite un contrôle précis de la température, de la pression et de la conception de la filière afin de garantir une production de haute qualité et une grande régularité.
3. Refroidissement et découpe après extrusion :
Une fois le profilé en PP extrudé et refroidi, il passe généralement par une filière de calibrage ou un ensemble de rouleaux pour s'assurer que le profilé conserve les dimensions voulues. Les profilés extrudés sont ensuite coupés aux longueurs requises.
Pour les profils PP personnalisés en petites séries, chaque lot est soigneusement mesuré et coupé pour répondre aux exigences spécifiques du client. La personnalisation peut inclure des ajustements d'épaisseur, de largeur ou d'autres caractéristiques de conception.
4. Contrôle de la qualité et inspection :
Pour s'assurer que les profilés PP finis répondent aux spécifications requises, des contrôles de qualité sont effectués à différents stades du processus de production. Ces contrôles peuvent comprendre
① Contrôle dimensionnel : Veiller à ce que les profilés répondent exactement aux spécifications de taille et de forme.
② Inspection visuelle : Contrôler les défauts de surface, tels que les fissures, les décolorations ou les bulles.
③ Tests de performance : Tester la durabilité, la résistance chimique et d'autres propriétés fonctionnelles du profilé, en particulier pour les applications exigeantes telles que les utilisations médicales ou industrielles.
5. Emballage et livraison :
Une fois que les profilés ont passé l'inspection, ils sont soigneusement emballés pour être livrés. L'emballage peut inclure des revêtements protecteurs ou des emballages pour éviter les dommages pendant le transport. Les profilés PP personnalisés sont alors prêts à être expédiés aux clients, que ce soit en vrac ou dans le cadre de commandes personnalisées pour des projets spécifiques.
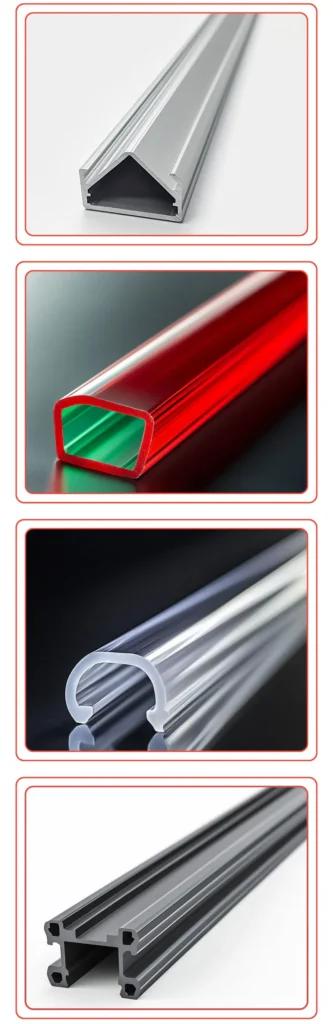
PP ou métal/PVC : quel matériau offre la meilleure rentabilité ?
Lorsqu'il s'agit de sélectionner des matériaux pour la fabrication, la rentabilité est toujours une priorité absolue. Le choix entre le PP (polypropylène), le métal et le PVC (chlorure de polyvinyle) peut avoir un impact significatif sur le coût de production et les performances de vos produits. Nous analyserons ici la comparaison entre le PP et le métal et le PVC, en nous concentrant sur les avantages que le PP offre en termes de coût et de performance des matériaux. En outre, nous montrerons comment l'extrusion plastique peut être un processus efficace pour produire des profilés en PP.
1. Coût-efficacité du PP :
Le polypropylène (PP) est souvent considéré comme l'un des matériaux les plus rentables pour la production de profilés sur mesure. En tant que fabricant de profilés en polypropylène sur mesure, le PP offre des avantages significatifs en termes de coût de la matière première, de vitesse de fabrication et de flexibilité. Le coût inférieur du PP, combiné au fait qu'il peut être facilement transformé à l'aide de profilés d'extrusion en PP, en fait un matériau de choix pour les applications sensibles aux coûts.
Pour une production à plus petite échelle, la personnalisation de profilés en PP en petites séries est également possible. Grâce à la technologie de l'extrusion plastique, le PP peut être efficacement façonné en profils personnalisés en petites séries, ce qui en fait un choix idéal pour les industries qui ont besoin de composants spécialisés en petites séries. Qu'il s'agisse d'applications industrielles, médicales ou grand public, le PP constitue une barrière d'entrée moins importante que les métaux ou le PVC.
2. Durabilité et résistance à la corrosion :
Le PP est intrinsèquement résistant à la corrosion, ce qui le rend adapté aux environnements qui exigent que les matériaux résistent à des conditions difficiles. En revanche, les métaux nécessitent souvent des revêtements supplémentaires pour prévenir la corrosion, ce qui peut entraîner des coûts supplémentaires au fil du temps. Par rapport aux profilés métalliques, le PP est plus léger et ne nécessite pas d'entretien régulier ni de remplacement pour cause de rouille, ce qui en fait une solution rentable à long terme.
Pour les industries confrontées à des environnements corrosifs, le PP est le matériau de prédilection. Qu'il s'agisse de profilés en polypropylène de qualité médicale ou d'autres applications très demandées, la durabilité du PP est inégalée par rapport à son prix.
3. Considérations relatives au poids :
Un autre domaine dans lequel l'extrusion du PP se distingue est celui des économies de poids. Comparé aux métaux, le PP est nettement plus léger, ce qui réduit les coûts de transport et la nécessité de structures lourdes. Cet avantage est particulièrement visible dans des secteurs tels que l'automobile et la construction, où les économies de poids contribuent directement à la réduction des coûts globaux.
4. Flexibilité de traitement :
L'extrusion plastique du PP permet une production de masse rapide et efficace de profils personnalisés avec des tolérances serrées. La polyvalence du PP signifie qu'il peut être extrudé dans une grande variété de formes et de tailles, avec un contrôle précis des dimensions et de la consistance du matériau. Cela contraste avec la complexité accrue du traitement des métaux, qui nécessite souvent des méthodes plus longues et plus coûteuses, telles que le moulage ou l'usinage.
En outre, les profilés en PP peuvent être facilement intégrés à d'autres matériaux, ce qui permet d'obtenir des solutions hybrides efficaces. La personnalisation des profilés pour des besoins spécifiques, par exemple en polypropylène de qualité médicale, est une autre façon pour le PP de surpasser le PVC et le métal.
5. PVC vs. PP : Principales différences :
Bien que le PVC soit un autre plastique populaire, il a tendance à être plus rigide et moins résistant chimiquement que le PP. Le PVC nécessite souvent des stabilisants ou des plastifiants pour améliorer ses propriétés, ce qui peut augmenter les coûts de production. En revanche, le PP est plus résistant à la fatigue et présente une résistance chimique supérieure sans nécessiter d'additifs supplémentaires.
Bien que les profilés extrudés en PVC soient largement utilisés, en particulier dans le secteur de la construction, l'extrusion de PP offre des performances supérieures en termes de coût et de durabilité pour de nombreuses applications, en particulier lorsque la résistance à la corrosion et la personnalisation sont des facteurs clés.
6. Conclusion : Pourquoi choisir le PP ?
Si l'on considère le rapport coût-efficacité, le PP s'impose comme le choix optimal pour toute une série d'applications. Le faible coût du matériau, associé à la facilité de transformation par extrusion du plastique, permet de réaliser des économies significatives au niveau de la fabrication. Qu'il s'agisse de créer des profilés en polypropylène sur mesure à usage industriel, des profilés en polypropylène de qualité médicale ou d'autres applications spécialisées, le PP offre une solution durable et rentable avec des frais généraux inférieurs à ceux du métal ou du PVC.
En résumé, pour les entreprises qui cherchent à optimiser les coûts sans compromettre les performances des matériaux, l'extrusion du PP offre un avantage certain, en particulier lorsqu'il s'agit de personnaliser des profils en PP en petites séries et de créer des profils en plastique résistants à la corrosion.
Comment choisir la bonne qualité de PP pour votre projet ?
Le choix de la bonne qualité de polypropylène (PP) est essentiel pour la réussite de votre projet d'extrusion plastique. Le PP est un thermoplastique polyvalent utilisé dans un large éventail d'industries, de l'emballage à l'automobile en passant par les applications médicales. Que vous travailliez avec des fabricants de profilés en polypropylène sur mesure, que vous envisagiez de transformer des profilés en PP par extrusion ou que vous ayez besoin de profilés en plastique résistants à la corrosion, le choix du bon grade garantit la performance, la durabilité et la rentabilité de votre produit.
1. Comprendre les propriétés des matériaux PP :
Le polypropylène se décline en plusieurs qualités, chacune adaptée à des applications différentes. Les propriétés mécaniques, la résistance chimique et la stabilité thermique du matériau sont des facteurs cruciaux à prendre en compte. Pour les projets nécessitant des profilés en polypropylène de qualité médicale, il convient de s'assurer que le grade PP répond aux réglementations strictes en matière de sécurité et de biocompatibilité.
① Résistance mécanique : La charge que le matériau peut supporter sans se déformer.
② Résistance chimique : Idéal pour les applications exposées à des substances corrosives.
③ Stabilité thermique : Pour une utilisation dans des environnements à haute température.
2. Réfléchissez à votre procédé d'extrusion :
Le processus d'extrusion du plastique joue un rôle important dans les performances du matériau PP. Si vous devez produire des profils PP personnalisés en petites séries, il est essentiel de sélectionner un grade qui assure une extrusion en douceur. Certains grades sont plus adaptés à l'extrusion que d'autres, offrant un flux et une stabilité optimaux.
① Vitesse d'extrusion : Choisissez une qualité qui offre un débit constant pour une production efficace.
② Compatibilité des matériaux : S'assurer que la qualité correspond aux spécifications de l'équipement et de l'outillage d'extrusion.
3. Adaptation à vos besoins spécifiques :
Les différents secteurs d'activité exigent des propriétés spécifiques. Par exemple, si vous produisez des profilés en plastique résistants à la corrosion pour des applications extérieures ou marines, un PP de qualité supérieure présentant une résistance chimique accrue est essentiel. De même, les profilés en polypropylène de qualité médicale doivent répondre aux normes de sécurité, en particulier s'ils sont en contact direct avec le corps humain.
Personnalisation : Travaillez avec des fabricants de profilés PP personnalisés pour créer des matériaux aux propriétés adaptées aux besoins de votre projet.
4. Équilibrer les coûts et les performances :
Pour choisir la bonne qualité de matériau PP, il faut trouver un équilibre entre le coût et la performance. Pour la personnalisation de profils PP en petites séries, vous pouvez envisager d'utiliser des qualités moins coûteuses sans compromettre les propriétés essentielles. En revanche, les qualités à haute performance peuvent être nécessaires pour des applications critiques, mais leur prix est plus élevé.
5. Testez le matériau pour votre application spécifique :
Avant de s'engager dans une production en grande série, il est essentiel de tester la qualité du PP dans votre application spécifique. Cela permet d'identifier rapidement tout problème potentiel, tel que le gauchissement ou la fragilité. Les tests garantissent que votre matériau fonctionnera comme prévu, qu'il s'agisse de profils résistants à la corrosion ou d'utilisations médicales.
6. Consulter des experts :
Travaillez en étroite collaboration avec les fabricants et les fournisseurs de profilés d'extrusion en PP pour obtenir des conseils sur le type de matériau le mieux adapté à vos besoins. Ils peuvent vous recommander des matériaux sur la base de leurs années d'expérience et vous aider à optimiser votre processus d'extrusion pour obtenir de meilleurs résultats.
Les profilés en PP peuvent-ils être entièrement personnalisés ?
Oui, les profilés en PP (polypropylène) peuvent être entièrement personnalisés, et le processus d'extrusion du plastique joue un rôle crucial dans cette personnalisation. Les profilés en PP sont connus pour leur polyvalence, qui permet aux fabricants de créer une large gamme de formes, de tailles et de spécifications en fonction des besoins des clients. Le processus d'extrusion consiste à forcer le polypropylène fondu à travers une filière pour former des profilés continus, qui peuvent ensuite être coupés à la longueur souhaitée.
Les options de personnalisation des profils PP comprennent
① Forme et taille : Les profilés peuvent être fabriqués pour répondre à des exigences spécifiques, qu'il s'agisse de formes géométriques simples ou de formes complexes et personnalisées.
② Épaisseur et résistance : Le processus d'extrusion permet d'ajuster l'épaisseur des parois, ce qui a un impact sur la résistance et la durabilité du produit final.
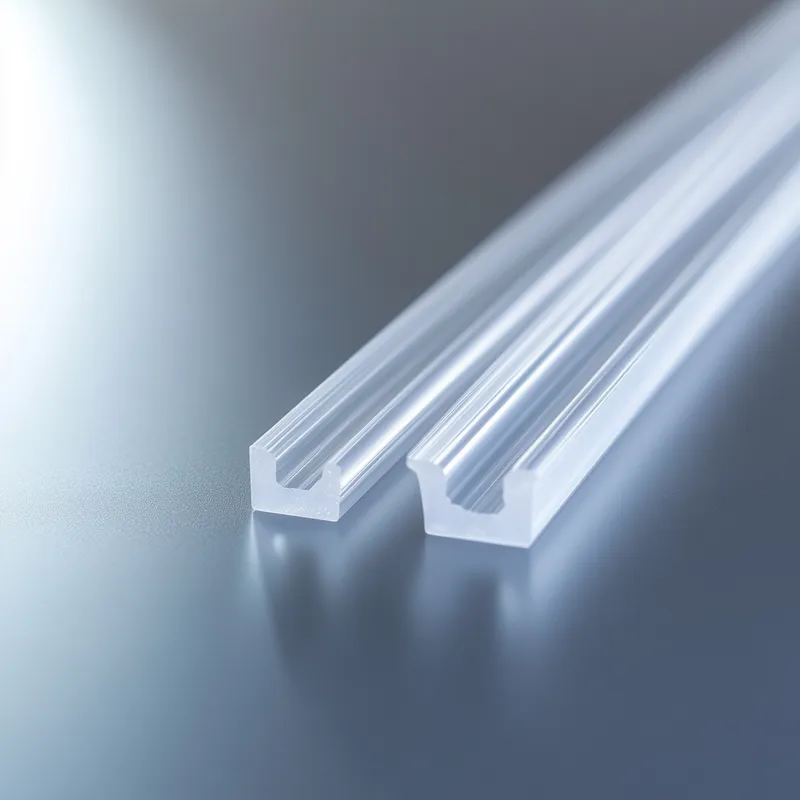
③ Finition de la surface : La finition de la surface des profilés en PP peut être modifiée pour répondre à des exigences esthétiques ou fonctionnelles (par exemple, surfaces lisses, texturées ou à motifs).
④ Additifs et modifications : Des formulations personnalisées peuvent être ajoutées pendant l'extrusion pour améliorer des propriétés spécifiques, telles que la résistance à la corrosion, la stabilité aux UV ou la conformité aux normes médicales.
⑤ Production en petites séries : Les profilés en PP peuvent être produits en petites quantités, ce qui les rend appropriés pour les petits volumes ou les prototypes, ce qui est idéal pour les marchés de niche ou les applications spécialisées.
Fabricant de profilés PP sur mesure
Vous recherchez un fabricant fiable de profilés PP personnalisés ? Nous sommes spécialisés dans les profilés en polypropylène de haute qualité, conçus avec précision et adaptés à vos besoins.
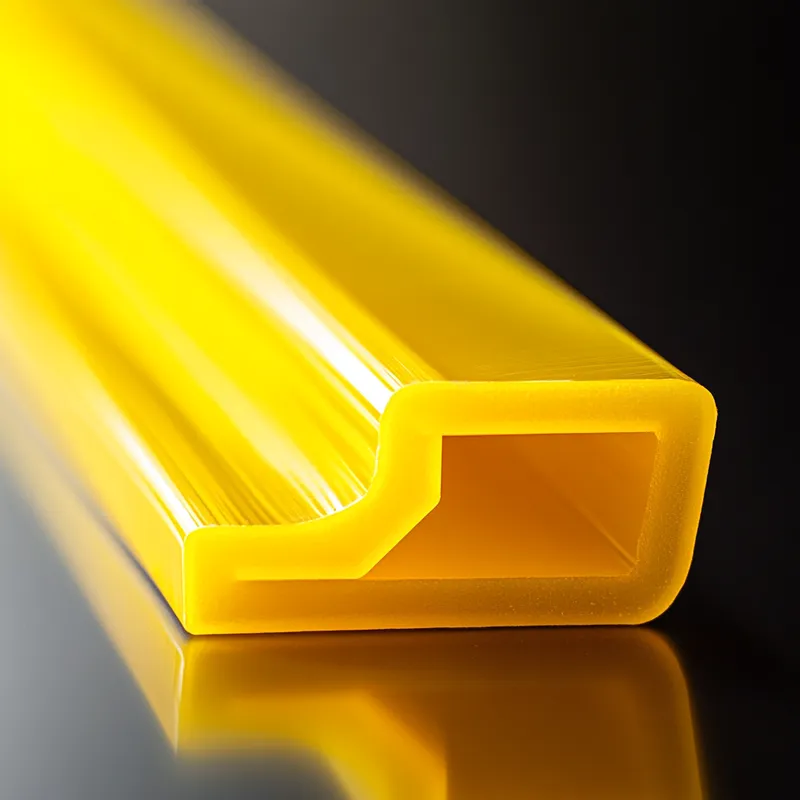
Guide pour la fabrication de profilés d'extrusion en PP sur mesure
- Qu'est-ce qui rend les profils PP durables ?
- Comment les profils PP se comportent-ils dans des conditions extrêmes ?
- Quels sont les défis à relever dans le traitement des profils PP ?
- Comment améliorer les propriétés des profilés en PP ?
- Quels sont les principaux avantages et limites de l'utilisation des profils PP ?
- Quelles sont les idées fausses à éviter dans les profils de PP ?
Qu'est-ce qui rend les profils PP durables ?
Les profilés en polypropylène (PP) sont de plus en plus reconnus pour leur durabilité, en particulier dans le cadre des processus d'extrusion des matières plastiques. Ces profilés sont non seulement durables, mais aussi respectueux de l'environnement lorsqu'ils sont produits de manière responsable. Voyons pourquoi les profilés en PP se distinguent en tant qu'option durable :
1. Durabilité et longévité :
Les profilés en PP sont très résistants à la corrosion, ce qui les rend idéaux pour les applications nécessitant des solutions durables. Leur durabilité exceptionnelle réduit le besoin de remplacements fréquents, ce qui diminue les déchets et l'empreinte carbone au fil du temps. Cette caractéristique est particulièrement importante dans les secteurs de l'automobile, de la construction et des soins de santé, où la longévité est essentielle.
2. Production économe en énergie :
Le processus d'extrusion du plastique utilisé pour créer les profilés en PP est économe en énergie, car il nécessite moins d'énergie que les autres méthodes de fabrication. Cela contribue à réduire l'impact global sur l'environnement pendant la production. Le processus consiste à faire fondre le plastique et à le façonner en profilés à l'aide d'une filière, ce qui permet une production précise et personnalisée avec un minimum de déchets.
3. Recyclabilité :
Le PP est l'un des plastiques les plus recyclables, et les profilés fabriqués à partir de ce matériau peuvent être réutilisés pour produire de nouveaux articles sans dégradation significative de la qualité. Cela permet de réduire le volume des déchets qui finissent dans les décharges et de promouvoir une économie circulaire. Les fabricants de profilés en PP sur mesure utilisent souvent du PP recyclé pour créer des produits durables.
4. Résistance aux produits chimiques et à la corrosion :
Les profilés en PP présentent une excellente résistance aux produits chimiques, à l'humidité et aux environnements corrosifs. Ils sont donc idéaux pour une utilisation dans des secteurs tels que l'agriculture, le traitement chimique et la marine, où l'exposition à des conditions difficiles est fréquente. Leur capacité à résister à la corrosion prolonge encore leur cycle de vie, contribuant ainsi au développement durable.
5. Biocompatibilité :
Pour les applications médicales, les profilés en PP peuvent être produits dans un format de qualité médicale, ce qui garantit qu'ils répondent à des normes d'hygiène strictes tout en conservant la même durabilité et la même résistance. Ils constituent donc une option durable dans le domaine médical, où les produits doivent être à la fois fiables et sûrs pour une utilisation répétée.
6. Personnalisation en petites séries :
La personnalisation des profils PP en petites séries permet aux fabricants de ne créer que ce dont ils ont besoin, ce qui réduit les déchets et minimise la surproduction. Cette flexibilité est particulièrement bénéfique pour les industries nécessitant des solutions spécialisées, telles que les applications médicales ou automobiles.
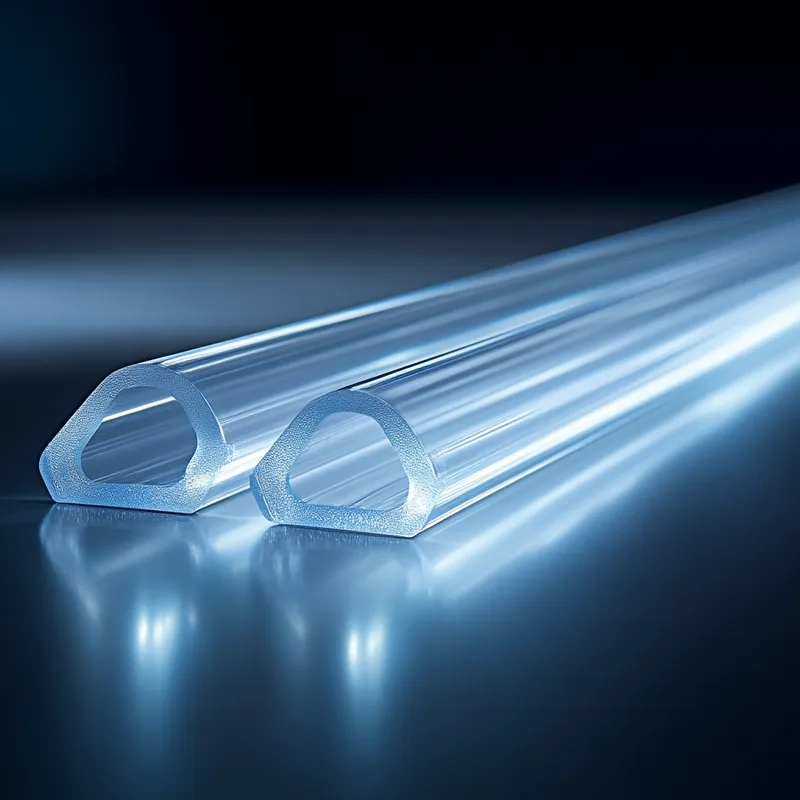
Comment les profils PP se comportent-ils dans des conditions extrêmes ?
Les profilés en polypropylène (PP), lorsqu'ils sont fabriqués par extrusion plastique, sont réputés pour leur polyvalence et leurs excellentes performances dans toute une série d'environnements, y compris les températures extrêmes et les conditions difficiles. Le processus d'extrusion lui-même permet un contrôle précis de la forme, de la taille et des propriétés des profilés en PP, garantissant qu'ils répondent à des exigences spécifiques.
1. Performance à des températures extrêmes :
Les profilés en PP présentent une bonne stabilité thermique, supportant généralement des températures allant de -20°C à 100°C. Ils peuvent donc être utilisés dans des environnements froids ou chauds, où ils conservent leur intégrité structurelle sans déformation importante. Toutefois, à des températures plus élevées, le PP peut se ramollir et perdre de sa rigidité, ce qui doit être pris en compte lors de la conception d'applications impliquant une exposition à la chaleur sur de longues périodes.
Dans les climats plus froids, les profilés en PP conservent leur flexibilité, évitant ainsi la fragilité que peuvent présenter d'autres matériaux comme le PVC. Cette résilience leur permet d'être performants même à des températures négatives, ce qui les rend idéaux pour les industries telles que l'automobile et la construction, où les fluctuations de température sont fréquentes.
2. Performance dans les environnements difficiles :
Le PP est connu pour son excellente résistance aux produits chimiques, aux huiles et aux solvants, ce qui le rend particulièrement utile dans les environnements industriels difficiles. Par exemple, les profilés en PP peuvent être utilisés dans les secteurs du traitement chimique, de l'automobile et de l'agriculture, où l'exposition à des substances corrosives est un problème.
Le processus d'extrusion permet aux fabricants de créer des profilés en polypropylène sur mesure qui répondent à des exigences spécifiques, telles qu'une résistance chimique accrue ou la capacité de résister à l'exposition aux UV dans les applications extérieures. En outre, les profilés extrudés en PP sont légers tout en étant durables, ce qui peut constituer un avantage significatif pour les industries qui cherchent à réduire le poids total sans compromettre la résistance.
3. Résistance à la corrosion :
L'un des principaux avantages des profilés en plastique résistants à la corrosion fabriqués en PP est leur capacité à résister à la dégradation lorsqu'ils sont exposés à l'humidité, aux sels et à de nombreux produits chimiques. Les profilés en PP conviennent donc aux applications marines, au traitement de l'eau et à d'autres environnements corrosifs. Le processus d'extrusion permet d'obtenir des finitions de surface précises qui améliorent la résistance à la corrosion du produit final.
4. Profilés PP de qualité médicale :
En ce qui concerne les profilés en polypropylène de qualité médicale, le processus d'extrusion garantit des niveaux élevés de précision et de propreté, qui sont essentiels dans les applications médicales. Le PP est non toxique et peut être stérilisé, ce qui en fait un choix privilégié pour les appareils et équipements médicaux. La personnalisation est également possible pour les petits lots, afin de répondre aux exigences médicales spécifiques.
5. Personnalisation en petites séries :
Pour les entreprises qui ont besoin de personnaliser des profils PP en petites séries, le processus d'extrusion du plastique permet de réduire les volumes de production sans compromettre la qualité. Cette flexibilité est idéale pour les industries qui ont besoin de formes spécialisées ou personnalisées mais qui n'ont pas besoin de grandes quantités, comme le prototypage ou les applications de niche.
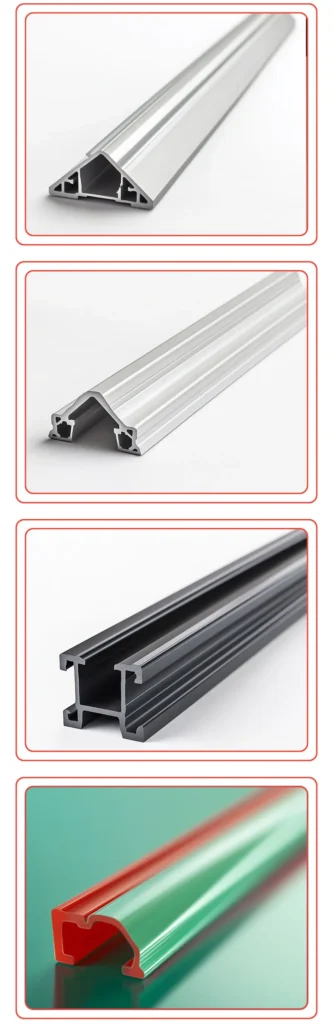
Quels sont les défis à relever dans le traitement des profils PP ?
Le polypropylène (PP) est un plastique polyvalent utilisé dans diverses industries pour la fabrication de profilés tels que des tuyaux, des feuilles et des composants sur mesure. Cependant, la transformation des profilés en PP par extrusion plastique peut poser plusieurs problèmes. Voici quelques-uns des défis les plus courants et leurs solutions :
1. Mauvais état de surface :
Problème : L'un des défis les plus courants de l'extrusion de profilés en PP est d'obtenir une finition de surface lisse et sans défaut. Des problèmes tels que des stries, des marques ou des textures rugueuses peuvent apparaître en raison de réglages d'extrusion ou de processus de refroidissement inadéquats.
Solution :
① Paramètres de l'extrudeuse : Veillez à ce que la température d'extrusion soit optimisée (généralement autour de 200-240°C pour le PP). Si elle est trop élevée, elle peut entraîner une dégradation ; si elle est trop basse, elle peut affecter le flux.
② Système de refroidissement : Contrôler la vitesse de refroidissement pour éviter les déformations ou les irrégularités de surface. Utiliser des techniques de refroidissement appropriées telles que le refroidissement à l'air ou à l'eau pour assurer un refroidissement uniforme sur l'ensemble du profilé.
③ Entretien des moules : Nettoyer et entretenir régulièrement les moules pour éviter l'accumulation de matière, qui peut également affecter la qualité de la surface.
2. Épaisseur irrégulière :
Problème : Des variations dans l'épaisseur des parois ou des incohérences dimensionnelles peuvent se produire en raison d'une mauvaise configuration de l'extrusion ou de la filière.
Solution :
① Conception de la filière : Optimiser la conception de la filière pour assurer une distribution uniforme du matériau. Une filière bien conçue permet de contrôler le débit et l'épaisseur du profilé en PP.
② Vitesse de l'extrudeuse : Ajustez la vitesse de l'extrudeuse en fonction de la capacité de la filière et assurez un flux de matière régulier.
3. La houle :
Problème : Le PP a tendance à se dilater à la sortie de la filière d'extrusion, un phénomène connu sous le nom de "gonflement de la filière". Ce phénomène peut entraîner des difficultés pour obtenir des dimensions de profil précises, en particulier dans les applications personnalisées.
Solution :
① Compensation du gonflement des moules : Tenir compte à l'avance du gonflement des moules en concevant des moules et des matrices capables de supporter le taux de gonflement prévu.
② Paramètres de traitement : Ajuster soigneusement la température et la pression d'extrusion pour réduire l'ampleur du gonflement de la filière.
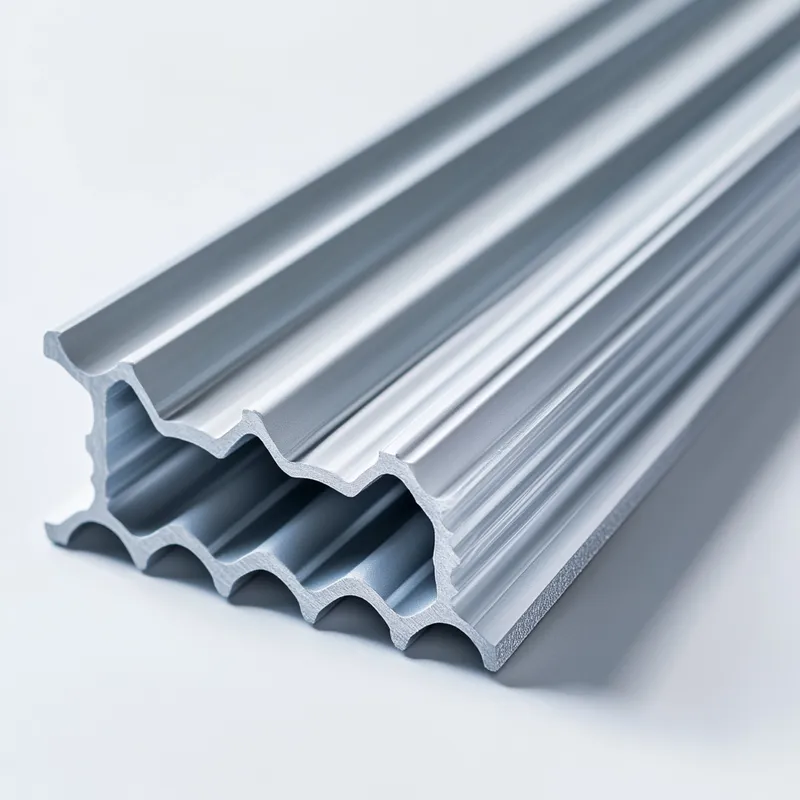
4. Dégradation des matériaux :
Problème : Une chaleur excessive ou une exposition prolongée à des températures élevées peut dégrader le PP, entraînant une décoloration, une réduction des propriétés mécaniques et le dégagement de fumées nocives.
Solution :
① Contrôle de la température : Utiliser des contrôles de température précis pendant l'extrusion pour éviter la surchauffe.
② Additifs : Incorporer des stabilisants ou des antioxydants dans le matériau PP pour améliorer sa résistance à la chaleur et à la dégradation.
5. Rétrécissement important :
Problème : Le PP peut subir un retrait important après le refroidissement, ce qui peut affecter les dimensions et la forme finales du profilé et entraîner des défauts.
Solution :
① Conception du moule : Tenez compte du retrait lors de la conception du moule. Des moules plus grands ou de légères modifications de la conception peuvent contribuer à réduire les effets du retrait.
② Formulation du matériau : Utiliser des qualités de PP à faible retrait ou modifier la formulation du matériau pour atténuer le retrait.
6. Fragilité et fissuration :
Problème : Bien que le PP soit généralement connu pour sa ténacité, il peut devenir cassant dans certaines conditions, en particulier dans des environnements froids ou lorsqu'il est exposé à des contraintes chimiques.
Solution :
① Additifs de durcissement : Utiliser des qualités de PP modifiées par impact ou des additifs qui améliorent la ténacité du matériau et sa résistance à la fissuration.
② Post-traitement : Envisager des techniques de post-traitement telles que le recuit ou le traitement thermique pour améliorer les propriétés mécaniques du matériau et réduire sa fragilité.
7. Contamination et pureté :
Problème : Les impuretés dans le matériau, telles que la poussière ou les particules étrangères, peuvent affecter la qualité et la résistance du profilé PP.
Solution :
① Propreté : Maintenir un environnement propre pendant le processus d'extrusion et veiller à ce que la matière première PP soit exempte de contaminants.
② Contrôle de la qualité : Mettre en œuvre des procédures strictes de contrôle de la qualité afin de détecter et d'éliminer toute impureté avant que le matériau ne soit traité.
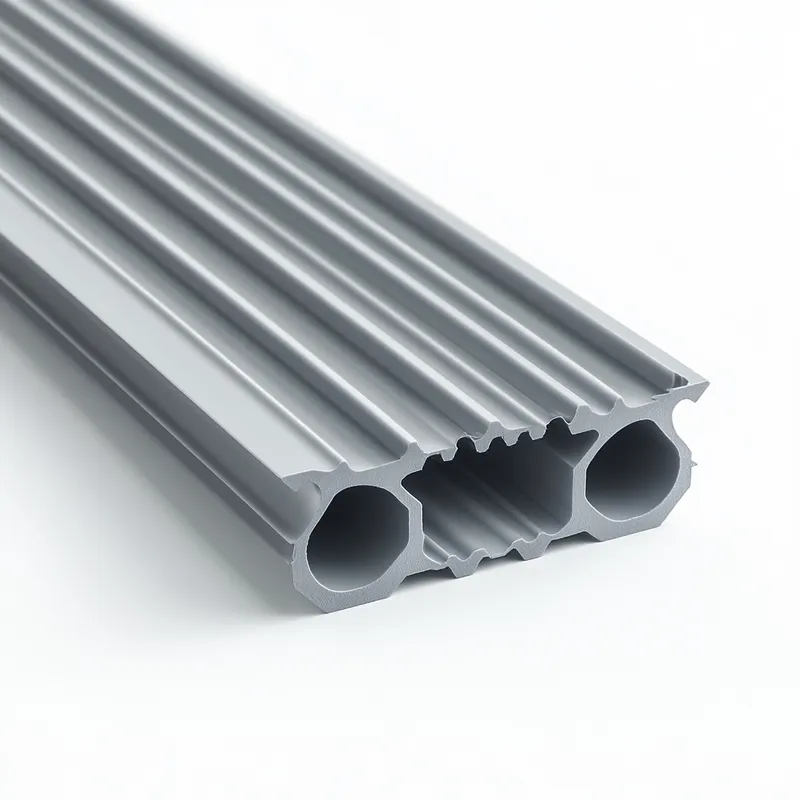
Comment améliorer les propriétés des profilés en PP ?
Le processus d'extrusion joue un rôle essentiel dans l'amélioration des propriétés des profilés en PP. Le processus d'extrusion permet un contrôle précis des propriétés du matériau, ce qui le rend idéal pour adapter les profilés en PP afin de répondre à des exigences de performance spécifiques. Voici quelques stratégies pour améliorer les performances des profilés en PP :
1. Résistance aux UV :
① Incorporation de stabilisateurs d'UV : L'ajout de stabilisateurs ou d'absorbeurs d'UV pendant le processus d'extrusion peut améliorer de manière significative la résistance aux UV des profilés en PP. Ces additifs protègent le matériau de la dégradation due à une exposition prolongée à la lumière du soleil, prolongeant ainsi la durée de vie des profilés dans les environnements extérieurs.
② Revêtement : Une autre approche consiste à appliquer un revêtement résistant aux UV sur la surface des profilés en PP après l'extrusion. Ce revêtement apporte une protection supplémentaire contre les rayons UV nocifs et améliore la durabilité du matériau.
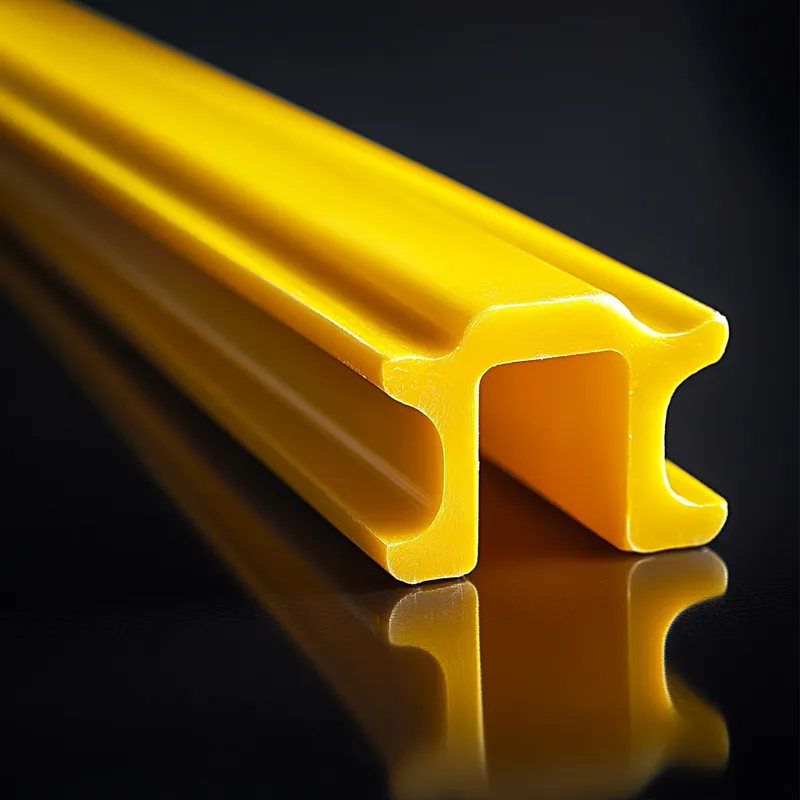
2. Retardateur de flamme :
① Additifs ignifuges : En incorporant des retardateurs de flamme pendant l'extrusion, les profilés en PP peuvent être rendus résistants au feu. Ces additifs agissent en formant une couche de charbon protectrice ou en interférant chimiquement avec le processus de combustion, réduisant ainsi l'inflammabilité du matériau.
② Mélanges de polymères : Le mélange de PP avec des polymères ignifuges peut également améliorer la résistance au feu. Le processus d'extrusion peut être ajusté pour obtenir le bon rapport de mélange, ce qui permet d'obtenir des profils présentant à la fois les propriétés inhérentes du PP et une résistance accrue aux flammes.
3. Renforcement :
① Incorporer des produits de remplissage : Le renforcement des profilés en PP avec des charges telles que des fibres de verre ou des fibres de carbone pendant l'extrusion permet d'accroître leur résistance et leur rigidité. Le renforcement par des fibres de verre est particulièrement courant dans les applications exigeant des performances mécaniques plus élevées, comme dans l'automobile ou l'industrie.
② Charges minérales : L'ajout de charges minérales, comme le talc ou le carbonate de calcium, peut améliorer la stabilité dimensionnelle et la résistance à la chaleur des profilés en PP tout en réduisant les coûts. Ces charges améliorent également la rigidité globale du profilé sans en affecter le poids de manière significative.
4. Personnalisation en petites séries :
Flexibilité de la production : Le procédé d'extrusion permet de fabriquer des profilés en PP en petites séries, ce qui est idéal pour les commandes personnalisées. La production à petite échelle permet de modifier avec souplesse la composition du matériau pour répondre aux besoins spécifiques du client tout en maintenant la rentabilité.
5. Personnalisation et applications spécifiques :
① Profilés en PP de qualité médicale : Pour les applications médicales, les profilés en PP peuvent être extrudés à l'aide de résines de qualité médicale qui répondent à des normes réglementaires strictes. Ces résines peuvent également être modifiées pour obtenir des propriétés telles que la biocompatibilité et la résistance à la stérilisation.
② Résistance à la corrosion : En améliorant le matériau PP avec des additifs résistants à la corrosion, il est possible de fabriquer des profilés destinés à être utilisés dans des environnements difficiles, par exemple dans les industries chimiques ou marines.
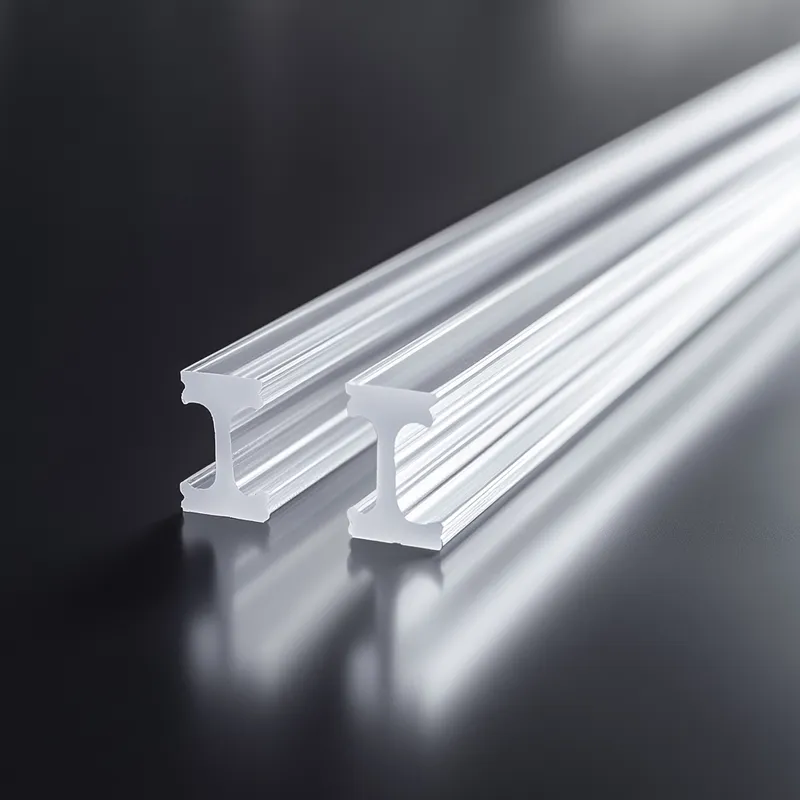
Quels sont les principaux avantages et limites de l'utilisation des profils PP ?
Les profilés en PP (polypropylène), produits par le processus d'extrusion du plastique, offrent plusieurs avantages, notamment une excellente résistance à la corrosion, une conception légère et un bon rapport coût-efficacité. Ils peuvent être facilement personnalisés pour diverses industries, qu'il s'agisse de profilés en polypropylène de qualité médicale ou de profilés en PP personnalisés en petites séries. Ils présentent toutefois certaines limites, telles qu'une faible résistance aux UV et une plage de températures relativement étroite. Comprendre les avantages et les inconvénients des profilés en PP aide les fabricants à prendre des décisions éclairées pour des applications dans les secteurs de l'automobile, de la construction et autres.
1. Principaux avantages de l'utilisation de profilés en PP :
① Excellente résistance à la corrosion : Les profilés en PP sont très résistants à de nombreux produits chimiques, acides et bases. Ils sont donc idéaux pour les applications dans les industries qui traitent des substances agressives, telles que le traitement chimique et le traitement des eaux usées. La résistance à la corrosion garantit une longue durée de vie, même dans des environnements difficiles.
② Polyvalent et personnalisable : Les profilés en PP peuvent être facilement extrudés en différentes formes et tailles, ce qui offre une grande souplesse en matière de conception et de personnalisation. Qu'il s'agisse de profils standard ou de formes complexes et personnalisées, le processus d'extrusion permet une production rapide et précise. Les profilés en PP constituent donc une option attrayante pour les fabricants des secteurs de l'automobile, de la construction et de l'emballage.
③ Léger et durable : Le polypropylène est un matériau léger qui ne fait aucun compromis sur la solidité ou la durabilité. Les profilés en PP présentent une résistance élevée aux chocs et peuvent supporter des contraintes importantes, ce qui les rend idéaux pour une utilisation à long terme dans diverses applications.
④ Rentabilité : Le processus d'extrusion du plastique est efficace, ce qui rend les profilés en PP plus abordables par rapport à d'autres matériaux. En outre, le PP est moins cher que beaucoup d'autres plastiques techniques, ce qui permet de maintenir les coûts de production à un niveau bas sans sacrifier les performances.
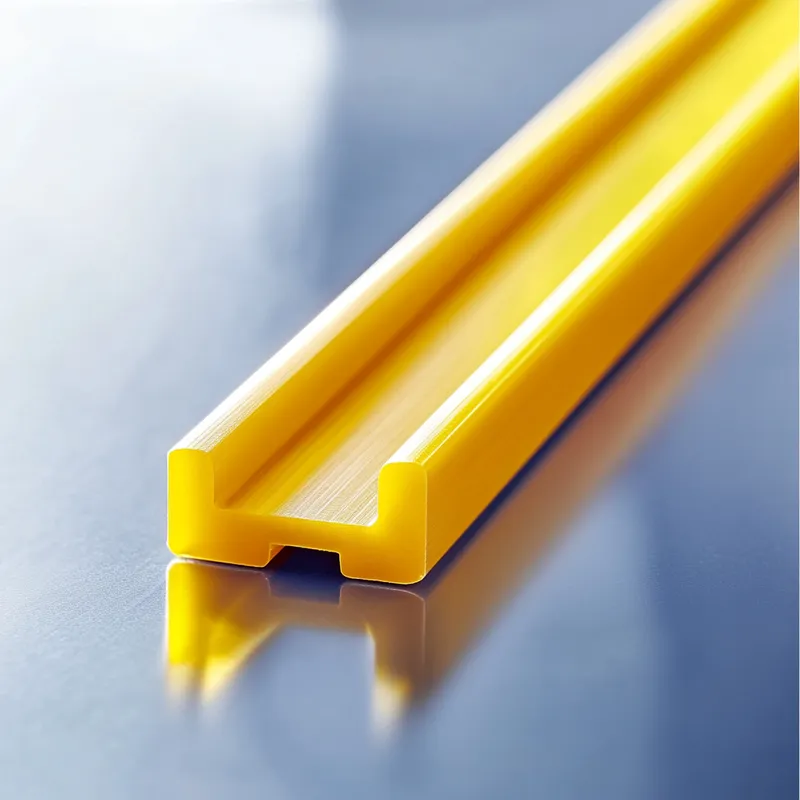
⑤ Options de qualité médicale : Les profilés en PP peuvent être fabriqués pour répondre aux normes strictes des applications médicales, telles que la stérilisation et la biocompatibilité. Pour les profilés de qualité médicale, le PP est un choix idéal en raison de sa non-toxicité et de sa facilité de stérilisation, ce qui permet de répondre aux réglementations strictes du secteur de la santé.
⑥ Avantages pour l'environnement : Le polypropylène est un matériau recyclable, ce qui fait des profilés en PP une option plus durable que les autres plastiques. Cet aspect est particulièrement important pour les entreprises qui cherchent à réduire leur empreinte écologique.
2. Limites de l'utilisation des profils PP :
① Faible résistance aux UV : Le PP n'est pas très résistant aux rayons ultraviolets (UV). Une exposition prolongée à la lumière UV peut entraîner la dégradation du matériau, ce qui se traduit par une décoloration et une perte des propriétés mécaniques. Cela peut limiter son utilisation dans les applications extérieures, à moins que des mesures de protection supplémentaires ne soient prises, telles que des stabilisateurs UV ou des revêtements.
② Plage de température limitée : Le polypropylène a un point de fusion relativement bas (160-170°C), ce qui limite son utilisation dans les environnements à haute température. Les profilés en PP ne conviennent pas aux applications impliquant une exposition à des températures élevées ou à des liquides chauds, car ils peuvent se déformer ou fondre.
③ La fragilité à froid : Bien que les profilés en PP soient généralement résistants, ils peuvent devenir cassants à très basse température. Ils ne conviennent donc pas aux applications où le matériau est exposé au gel ou à des conditions inférieures à zéro, à moins d'utiliser des formulations spéciales.
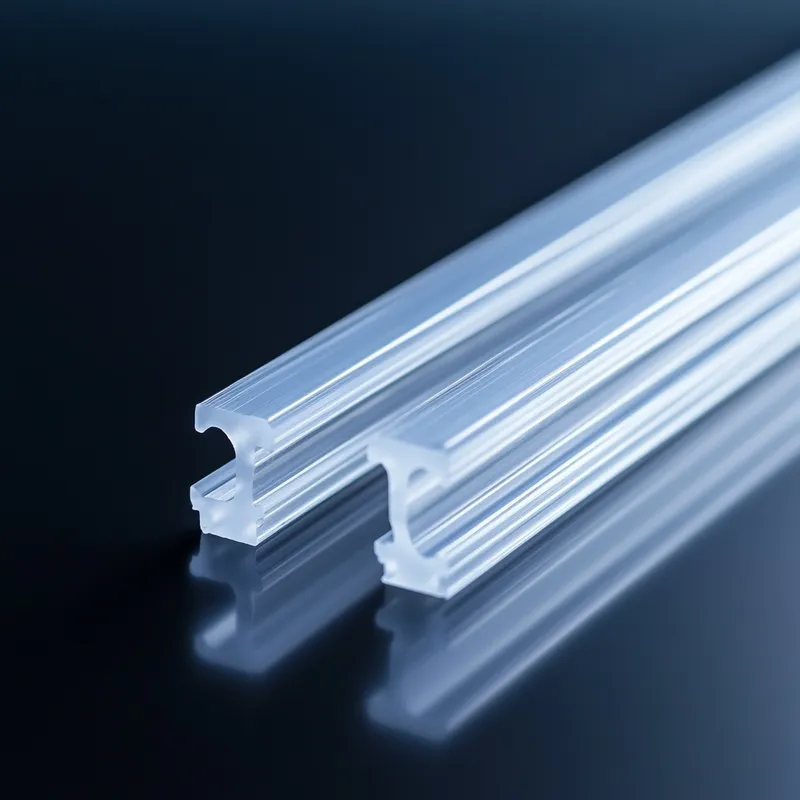
④ Potentiel de fissuration sous contrainte : Dans certaines conditions, les profilés en PP peuvent être sujets à la fissuration sous contrainte, en particulier s'ils sont exposés à des produits chimiques agressifs ou à des contraintes mécaniques au fil du temps. Il est possible de remédier à cette limitation en sélectionnant soigneusement les matériaux ou en utilisant des additifs, mais il s'agit d'un élément important à prendre en compte lors de la phase de conception.
⑤ Finition de la surface : Bien que les profilés en PP puissent avoir une finition lisse, l'obtention de surfaces de haute qualité et esthétiquement agréables peut nécessiter des étapes supplémentaires de post-traitement. Dans les applications où l'aspect du produit est crucial, des traitements de finition supplémentaires peuvent s'avérer nécessaires.
Quelles sont les idées fausses à éviter dans les profils de PP ?
Lors de la mise en œuvre de profilés en PP (polypropylène), il existe plusieurs idées fausses qu'il convient d'éviter, notamment en ce qui concerne le processus d'extrusion plastique, qui joue un rôle essentiel dans la mise en forme de ces matériaux. En voici quelques-unes :
1. Sous-estimation de la compatibilité des matériaux :
Une idée fausse consiste à supposer que tous les profils en PP ont les mêmes performances dans toutes les applications. Bien que le PP soit connu pour sa polyvalence, il est essentiel de choisir la bonne qualité de PP en fonction de l'utilisation prévue. Par exemple, les profilés PP de qualité médicale, utilisés dans le secteur de la santé, exigent un degré de pureté plus élevé et des certifications spécifiques par rapport aux profilés PP industriels généraux. Les fabricants d'extrusion de PP sur mesure doivent être consultés pour choisir le bon matériau.
2. Ignorer les variables de traitement dans l'extrusion :
Le processus d'extrusion est très sensible à la température, à la pression et à la vitesse d'extrusion. Une erreur fréquente consiste à ne pas contrôler soigneusement ces facteurs pendant la production. Des températures et des niveaux de pression incohérents peuvent conduire à des profils irréguliers, affectant à la fois l'apparence et la fonctionnalité du produit fini. Il est important de choisir un transformateur d'extrusion de profilés en PP compétent, capable d'ajuster ces variables pour garantir des résultats cohérents et de haute qualité.
3. Non prise en compte de la résistance à la corrosion :
Le PP est connu pour son excellente résistance à la corrosion, mais cela ne signifie pas qu'il s'agit du meilleur matériau pour tous les environnements. Il est essentiel d'évaluer les facteurs environnementaux spécifiques, tels que l'exposition à des produits chimiques ou à des conditions extrêmes. Si votre application nécessite une résistance accrue à la corrosion, un processus d'extrusion spécialisé avec un PP de qualité supérieure peut s'avérer nécessaire. En veillant à ce que votre profilé PP soit personnalisé pour résister à ces conditions, vous augmenterez la durée de vie de votre produit.
4. Négliger les besoins en matière de production de petits lots :
Certaines entreprises pensent à tort que les procédés d'extrusion plastique ne sont efficaces que pour la fabrication à grande échelle. Cependant, la personnalisation de profils PP en petites séries est tout à fait possible avec les technologies d'extrusion modernes. De nombreux fabricants proposent désormais des solutions flexibles pour les commandes de petits volumes, ce qui permet aux entreprises d'accéder à des profils PP personnalisés pour des applications de niche sans avoir à supporter des coûts de production à grande échelle.
5. Supposer que tous les profils de PP sont identiques :
Chaque profilé en PP est unique en termes d'épaisseur, de forme et de texture de surface, et ces variations peuvent affecter le processus d'extrusion. Tous les profils ne peuvent pas être traités de la même manière, c'est pourquoi il est important de consulter votre partenaire d'extrusion sur les exigences spécifiques de votre profil. Que vous recherchiez des profils durables et résistants à la corrosion ou des conceptions complexes pour des applications spécialisées, votre fournisseur doit adapter le processus d'extrusion à ces besoins.
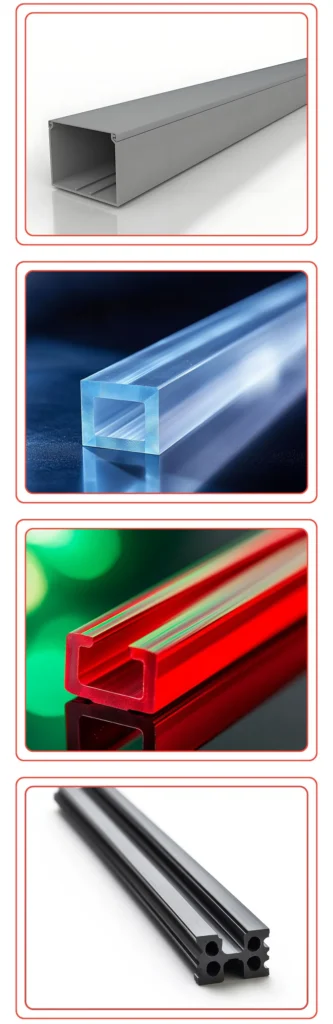
FAQ POUR LE CLIENT
Démarrer avec Uplastech
Vous avez des questions ? Nous avons les réponses.
Nous sommes spécialisés dans les processus d'extrusion et la fabrication de moules de précision, offrant des solutions personnalisées pour répondre à vos besoins de fabrication.
Nous travaillons avec différents secteurs, notamment l'automobile, l'électronique et les biens de consommation, en nous concentrant sur les partenariats B2B.
Oui, nous adaptons nos solutions à vos besoins spécifiques.
Prendre contact
N'hésitez pas à nous envoyer un courriel ou à remplir le formulaire ci-dessous pour obtenir un devis.
Courriel : uplastech@gmail.com