Solutions de formage sous vide pour parois minces
Découvrez des solutions efficaces de moulage sous vide de parois minces. Débloquez l'innovation et la précision pour vos besoins en matière d'injection plastique.
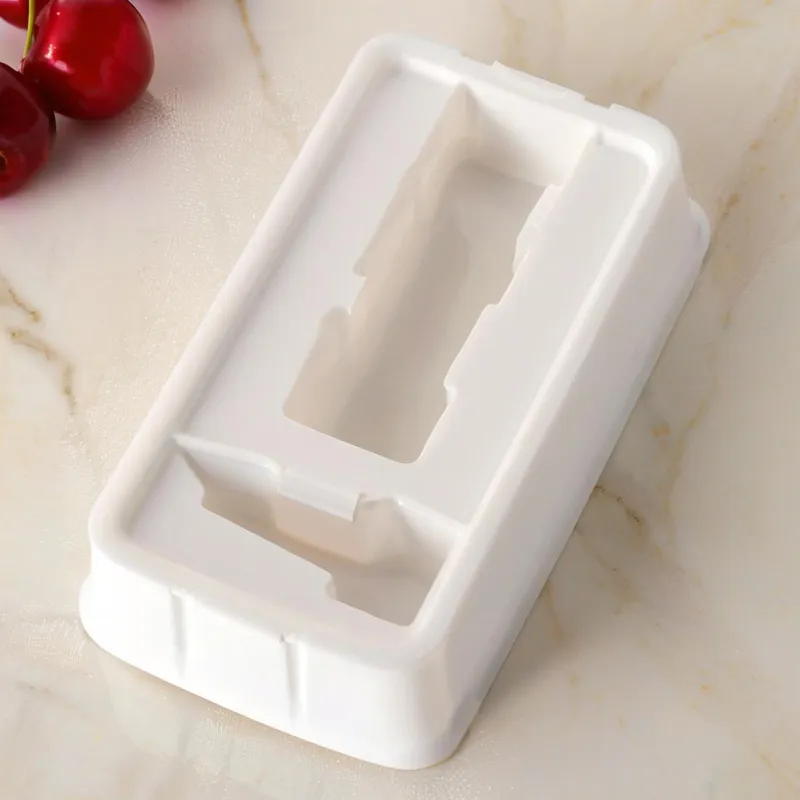
Guide du formage sous vide à paroi mince (jauge mince) sur mesure
Introduction au formage sous vide de parois minces
Le formage sous vide de parois minces est un processus de fabrication dans lequel une feuille de plastique chauffée est mise en forme sur un moule par pression sous vide, ce qui permet d'obtenir des pièces aux parois relativement minces. Cette méthode est particulièrement adaptée au prototypage et à la production de volumes faibles à moyens, offrant un équilibre entre coût et rapidité.
Le formage sous vide, souvent appelé formage sous vide de parois minces lorsqu'il s'agit de produire des pièces aux parois plus fines, est une technique de thermoformage qui consiste à chauffer une feuille de plastique jusqu'à ce qu'elle devienne souple, puis à utiliser un vide pour la tirer fermement contre la surface d'un moule. Ce procédé est apprécié pour sa simplicité et son coût abordable. Il permet de créer des composants légers d'une épaisseur généralement uniforme, qui peuvent être transparents ou opaques en fonction du matériau. C'est un excellent choix pour les fabricants qui ont besoin d'une production efficace d'articles à parois minces tels que des plateaux d'emballage, des panneaux automobiles ou des couvercles d'appareils médicaux, en particulier lorsque des machines complexes ou des outils à haute pression ne sont pas envisageables.
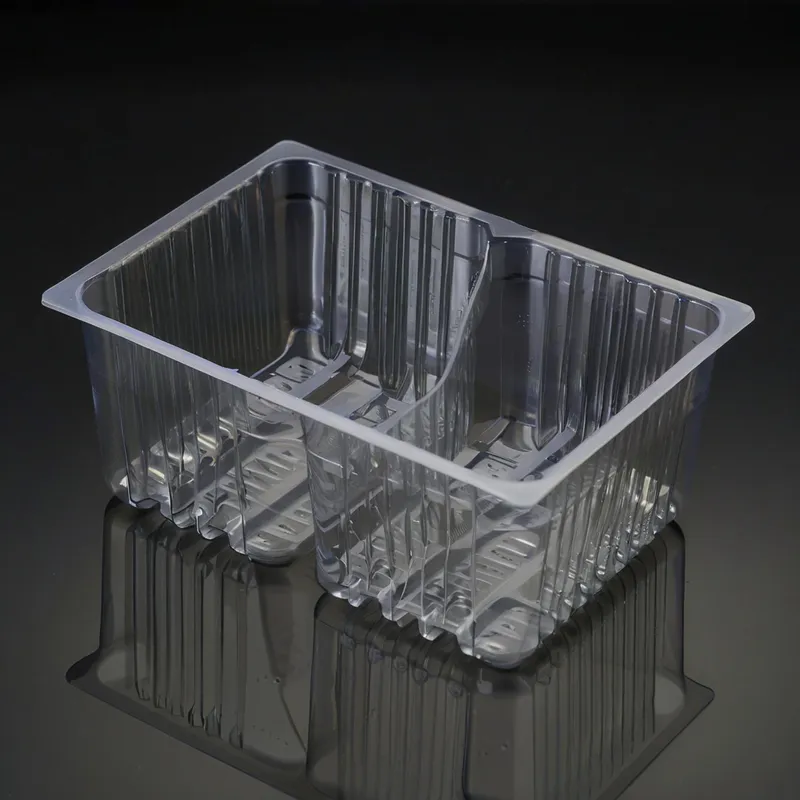
Contrairement à des méthodes plus complexes telles que le moulage par injection, le formage sous vide se distingue par des barrières d'entrée moins élevées, nécessitant un outillage moins coûteux et un équipement plus simple. Il est donc idéal pour les petites entreprises, les startups et tous ceux qui souhaitent prototyper de nouveaux modèles sans s'engager d'emblée dans des coûts de production à grande échelle.
Comment procéder au formage sous vide de parois minces, étape par étape ?
Le processus de formage sous vide de parois minces est une séquence d'étapes à la fois rationnelle et précise, conçue pour produire des pièces aux parois minces et uniformes. Voici une description détaillée :
1. Le chauffage :
Une fine feuille de plastique, telle que l'ABS ou le polystyrène, est chauffée entre 120°C et 180°C, ce qui la rend souple et flexible.
2. Positionnement du moule :
La feuille chauffée est soigneusement placée sur un moule en aluminium ou en polymères imprimés en 3D, ce qui garantit la précision.
3. Application sous vide :
Un vide tire le plastique fermement sur le moule, le façonnant tout en évitant un étirement excessif qui pourrait affaiblir la pièce.
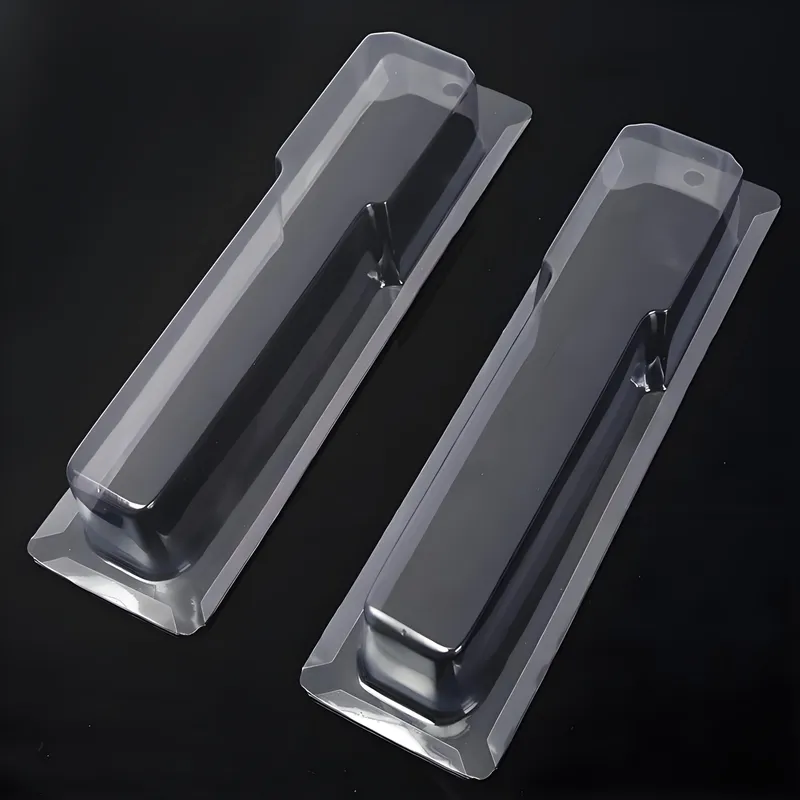
5. Parage :
L'excès de matière est enlevé à l'aide de défonceuses à commande numérique ou par découpage manuel, puis poncé pour obtenir une finition lisse et polie.
4. Refroidissement :
Les ventilateurs ou le brouillard refroidissent rapidement le plastique, ce qui garantit une bonne prise de la forme formée tout en minimisant les problèmes de déformation.
Ce processus est efficace, puisqu'il ne prend souvent que quelques minutes par cycle, mais il exige une attention particulière aux étapes de chauffage et de mise sous vide afin de maintenir la finesse et la résistance souhaitées. Voici un tableau récapitulatif des étapes :
Étape | Description |
---|---|
Chauffage | Une fine feuille de plastique est chauffée jusqu'à ce qu'elle devienne souple (120°C-180°C). |
Positionnement du moule | La feuille chauffée est alignée sur un moule (en aluminium ou imprimé en 3D). |
Application du vide | Le vide tire la feuille contre le moule pour former des parois minces (0,5 mm-2 mm). |
Refroidissement | La pièce est refroidie à l'aide de ventilateurs ou de brouillard pour solidifier la structure à parois minces. |
Parage | L'excédent de matière est enlevé et les bords sont finis pour obtenir la pièce finale à parois minces. |
Avantages et limites du formage sous vide de parois minces
Le formage sous vide de parois minces offre des avantages indéniables, mais il s'accompagne également de difficultés qu'il convient de prendre en compte. Voici un aperçu approfondi :
1. Avantages :
① Coût-efficacité : Les coûts d'outillage sont relativement faibles, ce qui le rend abordable pour la production de pièces à parois minces en petites et moyennes quantités (250-3000 unités).
② Pièces légères : En utilisant un minimum de matériau, ce procédé permet de créer des composants exceptionnellement légers, idéaux pour les applications où la réduction du poids améliore l'efficacité, telles que les tableaux de bord automobiles ou les pièces de la cabine aérospatiale.
③ Production rapide : Les cycles sont rapides - souvent moins de 10 minutes entre le chauffage et l'ébarbage - ce qui permet des délais d'exécution rapides pour les prototypes ou les besoins de production urgents.
④ Efficacité matérielle : Le formage sous vide de parois minces minimise l'utilisation du plastique, réduisant à la fois les coûts et les déchets, les matériaux de rebut étant souvent recyclables.
2. Limites :
① Cohérence de l'épaisseur de la paroi : Il peut être difficile de maintenir une épaisseur uniforme sur des sections plus profondes, ce qui peut entraîner des zones minces ou des faiblesses structurelles si l'on n'y prend pas garde.
② Géométries simples uniquement : Ce procédé est excellent pour les formes de base, mais il a du mal avec les dessins complexes, tels que ceux qui comportent des contre-dépouilles ou des détails compliqués, ce qui limite sa polyvalence.
③ Pas pour les gros volumes : Bien qu'elle soit économique pour les petites séries, elle devient moins compétitive pour la production à grande échelle par rapport à des méthodes comme le moulage par injection en raison des besoins de finition manuelle.
④ Finition secondaire : L'ébarbage et le lissage des pièces à parois minces nécessitent souvent une main-d'œuvre supplémentaire, ce qui augmente les délais et les coûts.
3. Comparaison :
Avantages | Limites |
---|---|
Faibles coûts d'outillage | Difficulté de garantir une épaisseur de paroi uniforme |
Composants légers | Limité aux formes simples |
Cycles de production rapides | Moins efficace pour les gros volumes |
Réduction des déchets de matériaux | Nécessite des opérations supplémentaires d'ébarbage et de finition |
Quels sont les matériaux utilisés dans le formage sous vide de parois minces ?
Dans le domaine du formage sous vide de parois minces, divers matériaux thermoplastiques sont couramment utilisés en raison de leur capacité à être chauffés, étirés et façonnés dans des formes précises. Les principaux matériaux sont les suivants
Matériaux | Propriétés et applications |
---|---|
ABS (Acrylonitrile Butadiène Styrène) | Durable, résistant aux chocs et facile à former. Idéal pour les pièces automobiles, les biens de consommation et les boîtiers électroniques. |
HIPS (polystyrène à haut impact) | Léger, économique et adapté aux emballages, aux récipients jetables et aux prototypes. Moins résistant à la chaleur que l'ABS. |
PVC (chlorure de polyvinyle) | Options rigides ou flexibles. Résistant aux produits chimiques et retardateur de flamme ; utilisé dans l'équipement médical, la signalisation et la construction. |
PETG (polyéthylène téréphtalate glycol) | Combine clarté, ténacité et résistance chimique. Courant dans les emballages alimentaires, les appareils médicaux et les présentoirs. |
Polycarbonate (PC) | Grande solidité, transparence et résistance à la chaleur. Utilisé pour les couvertures de protection, l'éclairage et les composants aérospatiaux. |
Polypropylène (PP) | Flexible, résistant aux produits chimiques et à la fatigue. Convient pour les charnières, les conteneurs et les pièces automobiles. |
Acrylique (PMMA) | Excellente clarté optique et résistance aux UV. Idéal pour les présentoirs, les lentilles et les objets décoratifs. |
PEHD (polyéthylène haute densité) | Rigide, résistant aux produits chimiques et à l'humidité. Utilisé pour les conteneurs industriels et les pièces techniques. |
Facteurs de sélection :
Le choix du matériau dépend des exigences de l'application telles que la solidité, la flexibilité, la stabilité thermique, la résistance chimique et le coût. Le formage de parois minces privilégie souvent les matériaux présentant de bonnes caractéristiques d'écoulement (par exemple, PETG, ABS) pour obtenir des pièces précises et légères sans déchirure.
Principales considérations de conception pour le formage sous vide de parois minces
La conception pour le formage sous vide de parois minces nécessite des directives spécifiques pour garantir que les pièces à parois minces sont à la fois fonctionnelles et fabricables :
① Angles d'ébauche : Incorporer des angles de 5°-10° pour les moules femelles et de 3°-5° pour les moules mâles afin de permettre un retrait facile sans endommager les parois minces.
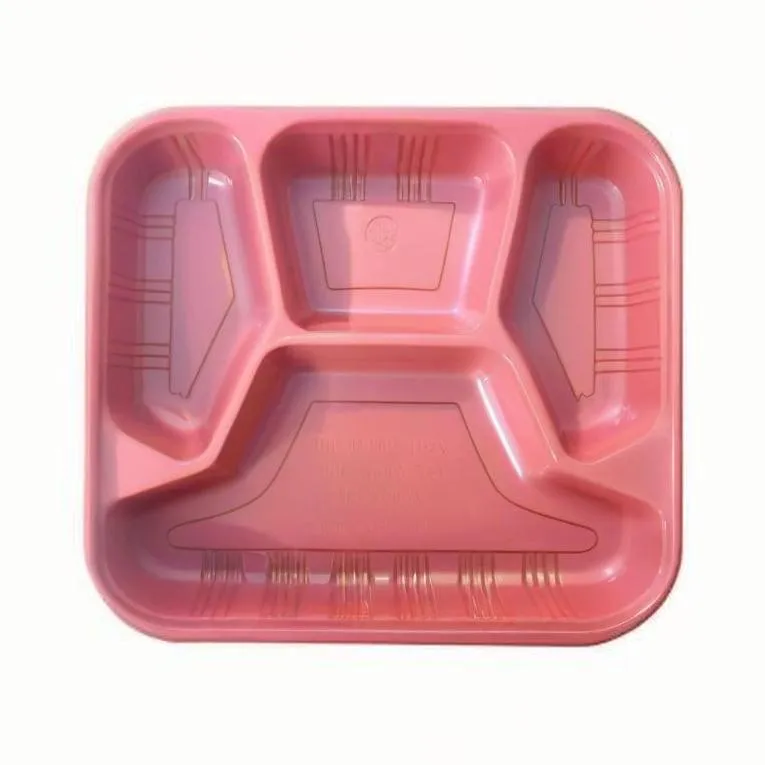
② Épaisseur de la paroi : Viser une épaisseur uniforme (0,5 mm-2 mm) afin d'éviter les points faibles ; un étirement irrégulier peut se produire s'il n'est pas planifié avec soin.
③ Éviter les étirements profonds : Les profondeurs d'étirage doivent être faibles - idéalement inférieures à 75% de la plus petite largeur supérieure de la pièce - afin d'éviter un amincissement ou une déchirure excessifs.
④ Caractéristiques arrondies : Utiliser de grands rayons (minimum 3 mm) et des angles lisses pour réduire les tensions et les fissures dans les parois minces.
⑤ Limiter les contre-dépouilles : Réduire au minimum les contre-dépouilles et les surplombs, car ils compliquent le démoulage et peuvent nécessiter un outillage supplémentaire.
Applications du formage sous vide de parois minces
Le formage sous vide de parois minces est un procédé de fabrication polyvalent et rentable utilisé pour produire des composants en plastique légers, durables et précis. Ses applications s'étendent à diverses industries en raison de son efficacité à créer des formes complexes avec un minimum de pertes de matériaux. Les principales applications sont les suivantes
1. Emballage :
① Emballages alimentaires : Plateaux, récipients à claire-voie et gobelets jetables.
② Plaquettes thermoformées : Pour les produits pharmaceutiques, électroniques ou de consommation.
③ Emballage de détail : Conteneurs de forme personnalisée pour les cosmétiques, les jouets ou l'électronique.
2. Biens de consommation :
① Vaisselle jetable : Assiettes, bols et couverts.
② Articles ménagers : Conteneurs de stockage, revêtements de réfrigérateur ou panneaux de douche.
③ Contenants pour cosmétiques : Pots à paroi mince, couvercles et poudriers.
3. Médecine et soins de santé :
① Plateaux stériles : Pour l'emballage des instruments chirurgicaux ou des dispositifs médicaux.
② Composants à usage unique : Coupes à spécimen, piluliers ou couvercles de protection.
4. L'agriculture :
① Plateaux de semis : Plateaux de multiplication de plantes à parois minces et réutilisables.
② Couvertures de protection : Pour le matériel ou les cultures.
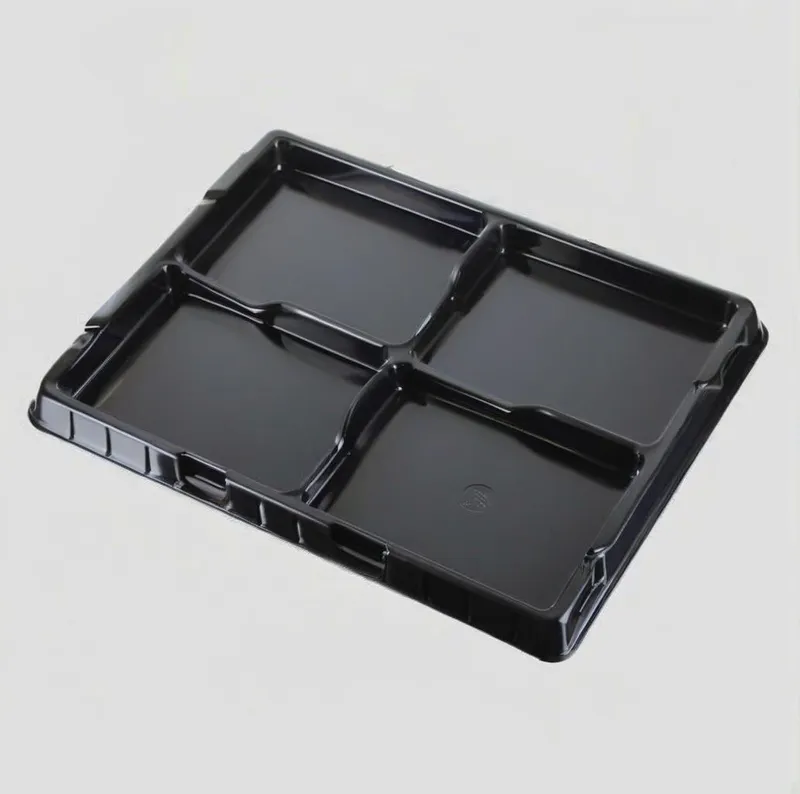
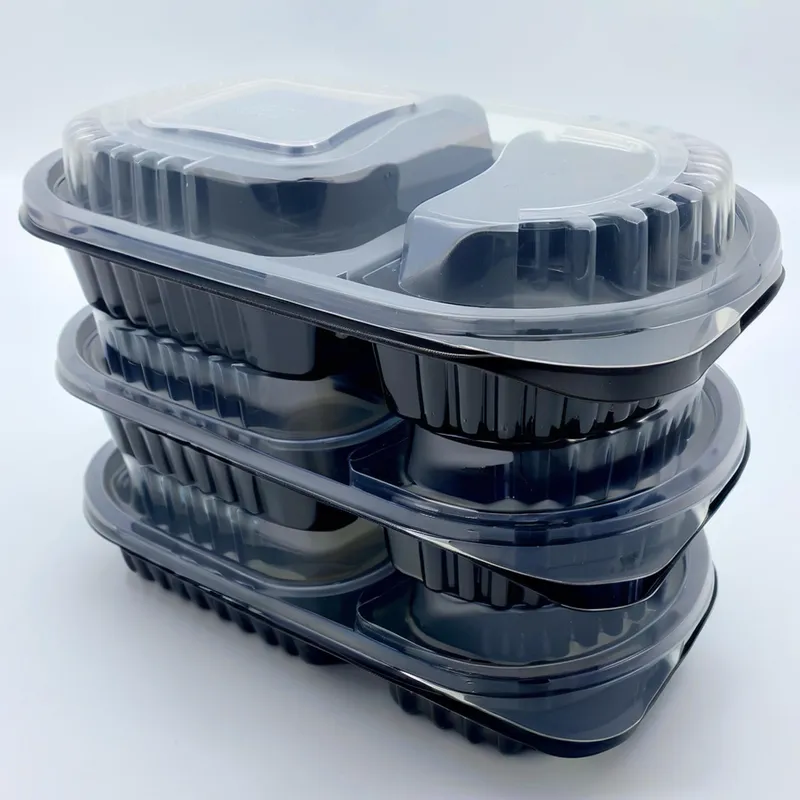
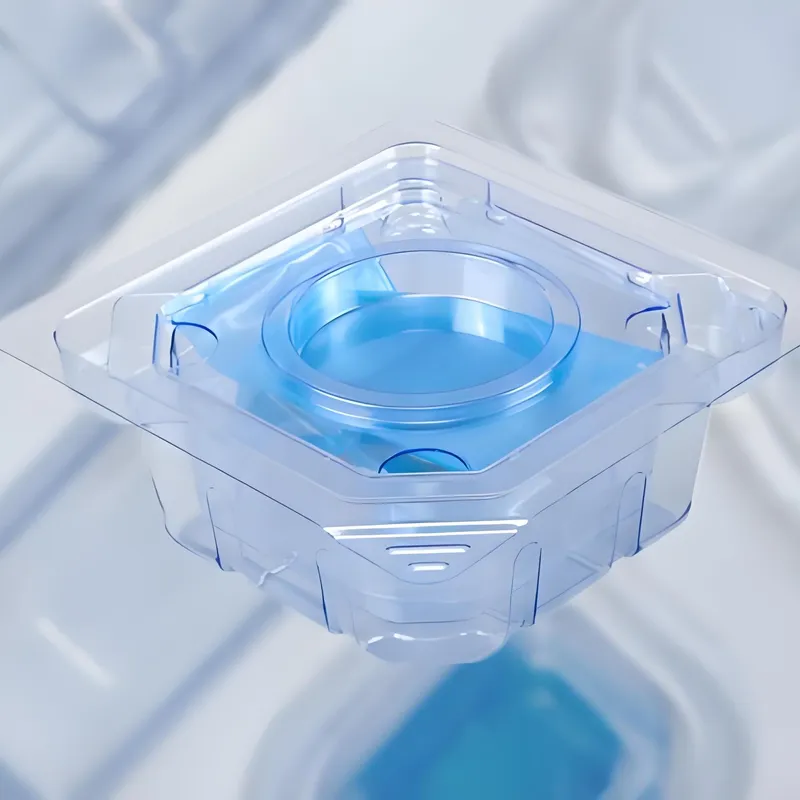

Solutions de formage sous vide pour parois minces
Découvrez des solutions de thermoformage durables et de haute précision, avec une assistance à la conception personnalisée et une polyvalence des matériaux. Demandez un devis dès aujourd'hui !
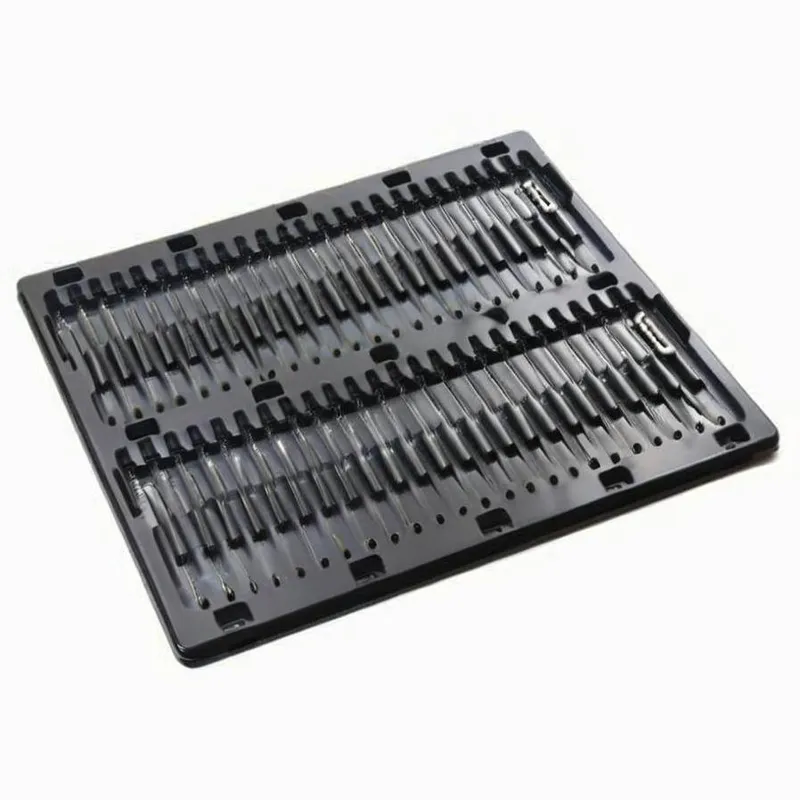
Guide du formage sous vide à paroi mince (jauge mince) sur mesure
- Automatisation du formage sous vide de parois minces
- Défis et solutions dans le domaine du formage sous vide de parois minces
- Comment augmenter la production avec le formage sous vide de parois minces ?
- Formage sous vide de faible épaisseur et formage sous vide d'épaisseur importante
- Moules de thermoformage de haute qualité et de calibre fin constant
- Quels sont les différents types de moules de thermoformage à faible épaisseur ?
Automatisation du formage sous vide de parois minces
L'automatisation transforme le formage sous vide des parois minces, en améliorant l'efficacité et la cohérence. Voici comment la technologie moderne est intégrée au processus :
① Manutention robotisée : Les robots chargent les feuilles de plastique dans la machine et en retirent les pièces finies, ce qui réduit le travail manuel et accélère les temps de cycle.
② Découpage CNC : Après le formage, des machines à commande numérique par ordinateur (CNC) découpent avec précision l'excédent de matière des pièces à parois minces, garantissant ainsi des bords nets et une bonne répétabilité.
③ Contrôles de qualité en ligne : Des capteurs automatisés contrôlent la température de la feuille, la pression du vide et les dimensions de la pièce en temps réel, signalant les problèmes avant qu'ils ne s'aggravent.
④ Contrôleurs logiques programmables (PLC) : Ces systèmes gèrent l'ensemble du processus de chauffage, de formage et de refroidissement à l'aide de paramètres prédéfinis, ce qui minimise les erreurs humaines.
Pour une série moyenne de 1 000 pièces, l'automatisation peut réduire le temps de production de 20 à 30% tout en améliorant l'uniformité, ce qui change la donne pour les industries à forte demande.
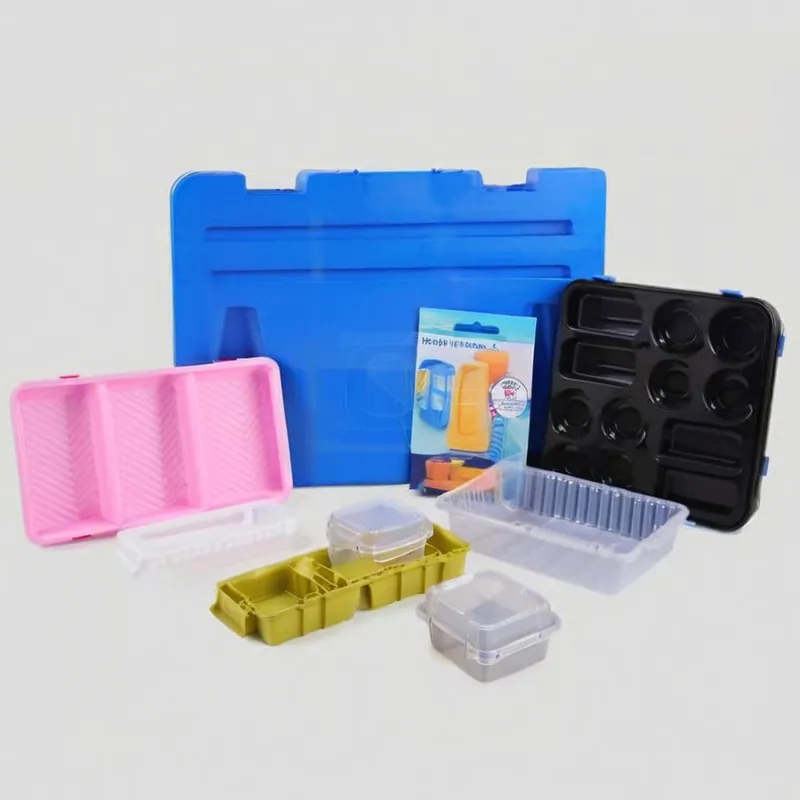
Défis et solutions dans le domaine du formage sous vide de parois minces
Si le formage sous vide de parois minces offre de nombreux avantages, il s'accompagne de défis que les fabricants doivent relever :
1. Éclaircie irrégulière :
① Défi : Les emboutissages profonds peuvent étirer excessivement le matériau, ce qui affaiblit certaines zones.
② Solution : Utiliser des outils d'assistance au bouchage qui pré-étirent uniformément la feuille avant que le vide ne la tire dans le moule.
2. Déformation :
① Défi : Les pièces minces peuvent se déformer lorsqu'elles refroidissent en raison de contraintes internes.
② Solution : Optimiser les taux de refroidissement à l'aide de ventilateurs ou de brouillard d'eau et utiliser des dispositifs de fixation pour maintenir la forme de la pièce pendant le refroidissement.
3. Détails limités :
① Défi : Par rapport au moulage par injection, le formage sous vide se heurte à des difficultés liées à la complexité des caractéristiques.
② Solution : Combinez avec le formage sous pression ou l'usinage post-processus pour obtenir des détails plus fins.
Comment augmenter la production avec le formage sous vide de parois minces ?
Le passage du prototype à la production complète dans le domaine du formage sous vide de parois minces nécessite une planification stratégique. Voici comment les fabricants peuvent effectuer cette transition en douceur :
① Prototypage : Commencez par des moules en bois ou imprimés en 3D à faible coût pour tester les modèles. Un seul moule prototype peut coûter aussi peu que $150.
② Petites séries : Passez aux moules en aluminium pour les lots de 100 à 500 unités. Ces moules sont durables tout en étant abordables, ce qui permet d'équilibrer le coût et la qualité.
③ Production en grande série : À partir de 1 000 unités, les moules multi-empreintes (qui forment plusieurs pièces à la fois) augmentent la production. Les coûts d'outillage augmentent, mais les coûts par pièce diminuent considérablement.
④ Optimisation des processus : Réglez avec précision les temps de chauffage, la force du vide et le découpage pour maximiser le rendement sans sacrifier la qualité.
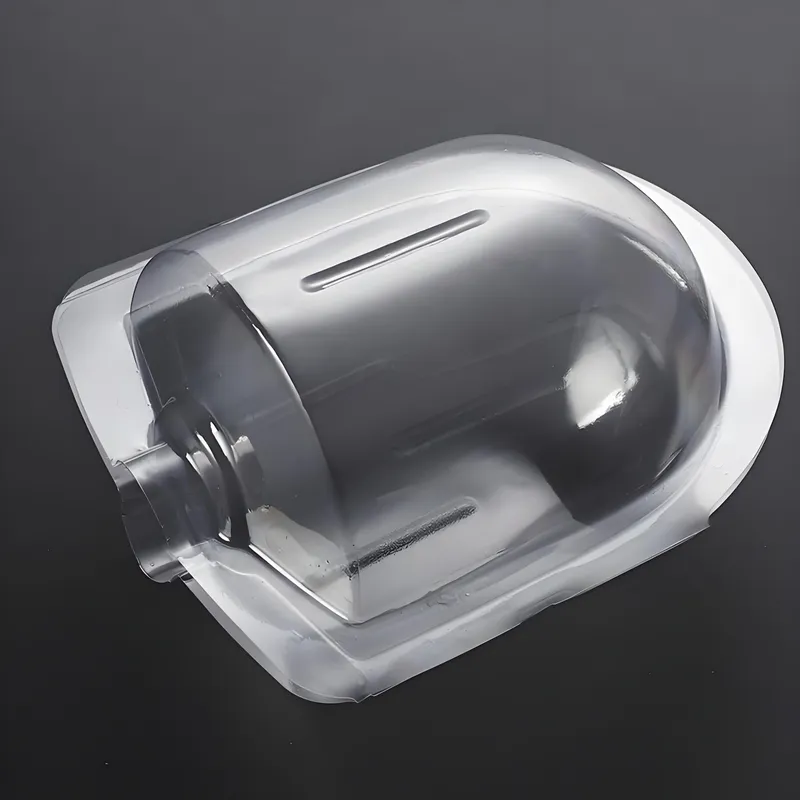
Formage sous vide de faible épaisseur et formage sous vide d'épaisseur importante
Le formage sous vide en couche mince et le formage sous vide en couche épaisse sont deux variantes du processus de thermoformage, qui se distinguent principalement par l'épaisseur des feuilles de plastique utilisées et par leurs applications.
1. Épaisseur du matériau :
① Thin Gauge : Il s'agit de feuilles de plastique d'une épaisseur inférieure à 0,060 pouce (1,5 mm), souvent fournies en rouleaux pour un traitement en continu.
② Jauge lourde : Utilise des feuilles allant de 0,060 pouce (1,5 mm) à 0,500 pouce (12,7 mm) ou plus épaisses, généralement coupées à la taille et alimentées individuellement.
2. Applications :
① Thin Gauge : Couramment utilisés pour les produits jetables légers et de grand volume, tels que les plateaux d'emballage, les coquilles, les blisters et les récipients alimentaires.
② Jauge lourde : Utilisé pour les pièces structurelles durables telles que les composants automobiles (par exemple, les tableaux de bord), les boîtiers d'appareils médicaux et les couvercles industriels.
3. Caractéristiques du processus :
① Thin Gauge : Les temps de cycle sont plus courts grâce aux propriétés de chauffage et de refroidissement rapides du matériau fin. Il intègre souvent un système automatisé de découpage et d'empilage pour plus d'efficacité.
② Jauge lourde : Nécessite des périodes de chauffage et de refroidissement plus longues, ce qui ralentit la production mais permet d'obtenir des formes plus complexes et une plus grande résistance des pièces.
4. Avantages et inconvénients :
① Thin Gauge :
- Avantages : Rentable pour la production de masse, léger et générant peu de déchets.
- Inconvénients : Limités à des conceptions plus simples et à des pièces moins durables.
② Jauge lourde :
- Avantages : Permet de produire des pièces robustes et durables avec une plus grande souplesse de conception (par exemple, contre-dépouilles, textures détaillées).
- Inconvénients : Coûts plus élevés des matériaux et de l'outillage, cadences de production plus lentes.
Moules de thermoformage de haute qualité et de calibre fin constant
Il est essentiel d'obtenir des moules de thermoformage de haute qualité et homogènes pour produire des pièces uniformes, en particulier dans les grands volumes. Les principaux facteurs contribuant à la qualité des moules sont les suivants
1. Sélection des matériaux :
① Aluminium : Préféré pour les moules de production en raison de sa durabilité, de son excellente conductivité thermique et de sa capacité à maintenir des tolérances serrées sur des milliers de cycles.
② Composite/Epoxy : Utilisé pour les prototypes ou les petites séries, il offre une alternative moins durable mais plus abordable.
2. Précision de la conception :
① Outils CAD/CAM : Les moules sont conçus à l'aide de la conception assistée par ordinateur (CAO) et usinés à l'aide de la fabrication assistée par ordinateur (FAO) pour garantir l'exactitude et la répétabilité.
② Draft Angles & Radii : L'incorporation d'angles de dépouille (3-5 degrés) et de rayons lisses facilite la libération des pièces et évite l'amincissement du matériau.
3. Systèmes de refroidissement :
① Canaux de refroidissement : Les canaux intégrés assurent un contrôle uniforme de la température, réduisant ainsi les temps de cycle et garantissant une qualité constante des pièces.
② Gestion thermique : Un refroidissement efficace empêche le gauchissement et maintient la stabilité dimensionnelle des pièces de faible épaisseur.
4. Finition de la surface :
① Poli/Texturé : Un moule poli donne des pièces brillantes, tandis que les surfaces texturées créent des finitions mates ou à motifs.
② Ventilation : Des trous d'aération stratégiquement placés permettent à l'air de s'échapper, ce qui garantit que le plastique se conforme entièrement au moule sans défaut.
5. Techniques de fabrication :
① Usinage CNC : L'usinage de haute précision garantit la précision des caractéristiques des moules, ce qui est essentiel pour assurer la cohérence des grandes séries.
② Conception modulaire : Les inserts interchangeables permettent de modifier rapidement la conception sans avoir à remplacer l'ensemble du moule.
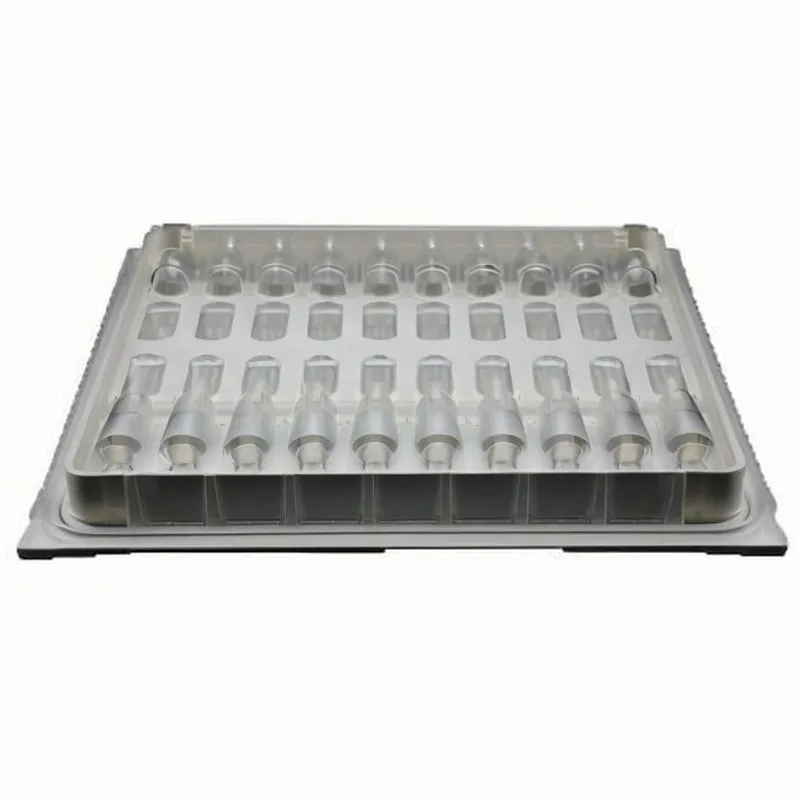
Quels sont les différents types de moules de thermoformage à faible épaisseur ?
Il existe plusieurs types de moules de thermoformage de faible épaisseur, chacun étant adapté aux besoins de production spécifiques, aux budgets et aux exigences des pièces :
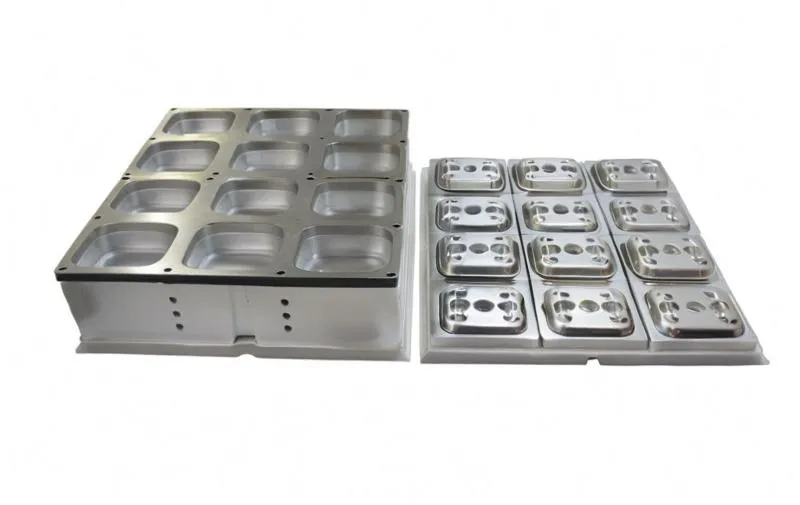
1. Moules en aluminium :
Fabriqués en aluminium de haute qualité, ils constituent le choix idéal pour les moules de production.
- Utilisation : production en grande quantité d'emballages, de plateaux et de conteneurs.
- Avantages : Durable, excellent transfert de chaleur et capable de réaliser des détails fins.
- Inconvénients : coût initial plus élevé.
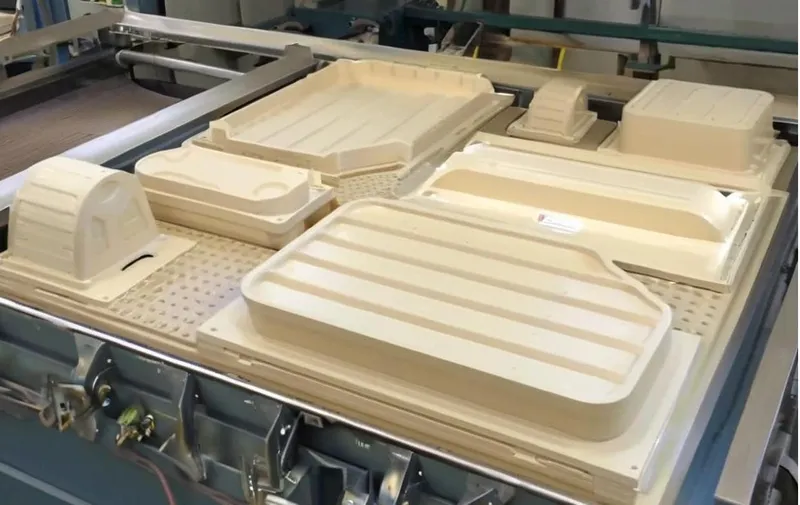
2. Moules composites :
Fabriqués en résine époxy ou en fibre de verre, ces moules sont plus légers et moins coûteux.
- Utilisations : Prototypage ou production en petite série.
- Avantages : Abordable et rapide à produire.
- Inconvénients : moins durable, avec une durée de vie de 100 à 500 cycles.
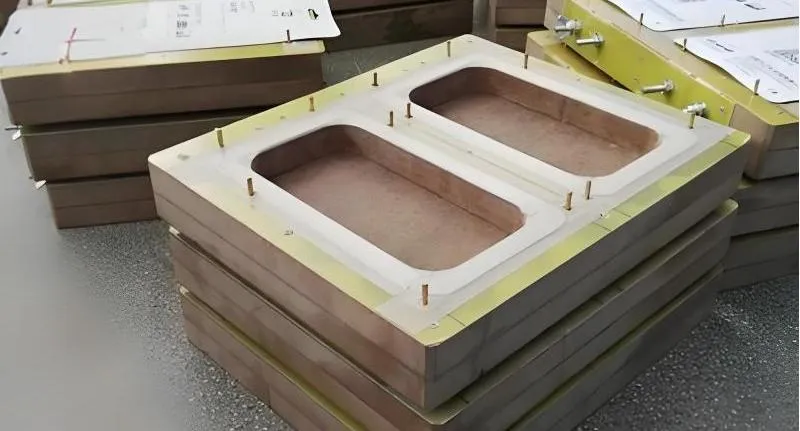
3. Moules en bois :
Construit en bois dur ou en contreplaqué pour les besoins de formage de base.
- Utilisations : Pièces uniques ou premiers prototypes.
- Avantages : Peu coûteux et rapide à créer.
- Inconvénients : sujet à l'usure et ne convient pas à la production.
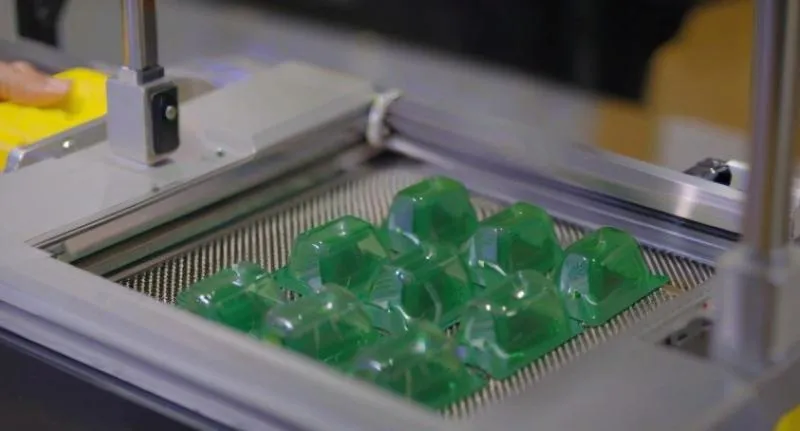
4. Moules imprimés en 3D :
Fabriqués à partir de polymères ou de résines résistants à la chaleur via l'impression 3D.
- Utilisations : Prototypage rapide ou pièces personnalisées de faible volume.
- Avantages : Production rapide et souplesse de conception.
- Inconvénients : durabilité et résistance à la chaleur limitées.
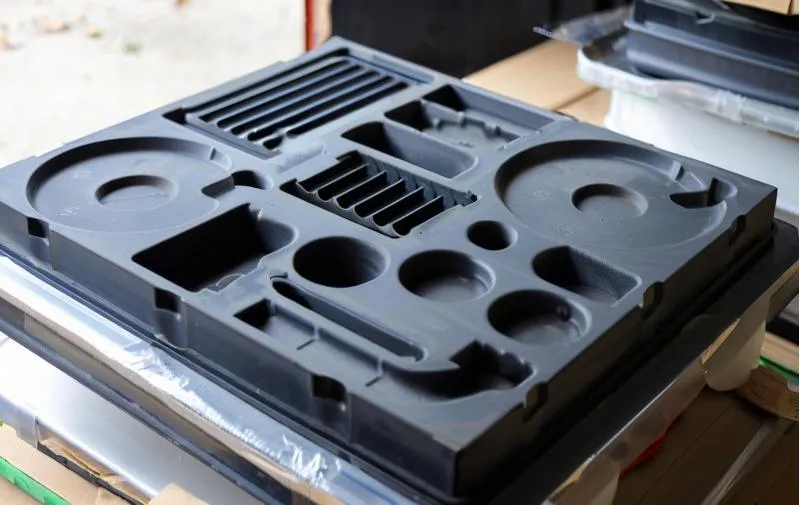
5. Moules à cavités multiples :
Les cavités multiples permettent de former plusieurs pièces simultanément à partir d'une seule feuille.
- Utilisations : production en grande quantité pour des raisons d'efficacité.
- Avantages : Augmente le rendement et réduit les coûts par pièce.
- Inconvénients : conception complexe et coûteuse.
FAQ POUR LE CLIENT
Démarrer avec Uplastech
Vous avez des questions ? Nous avons les réponses.
Nous sommes spécialisés dans l'extrusion, le formage sous vide, le moulage par soufflage et la fabrication de moules de précision, offrant des solutions personnalisées pour répondre à vos divers besoins de fabrication.
Nous travaillons avec diverses industries, notamment l'automobile, l'électronique, les biens de consommation et l'emballage, en nous concentrant sur les partenariats B2B et en fournissant des solutions dans les domaines de l'extrusion, du thermoformage, du moulage par soufflage et de la fabrication de moules de précision.
Oui, nous adaptons nos solutions à vos besoins spécifiques.
Prendre contact
N'hésitez pas à nous envoyer un courriel ou à remplir le formulaire ci-dessous pour obtenir un devis.
Courriel : uplastech@gmail.com