Conception et fabrication de moules pour l'extrusion de matières plastiques
Découvrez des services experts de conception et de fabrication de moules d'extrusion plastique adaptés à vos besoins. Nous fournissons des moules durables et de haute qualité pour diverses industries, en garantissant la précision et l'efficacité de chaque projet. Contactez-nous dès aujourd'hui pour une consultation !
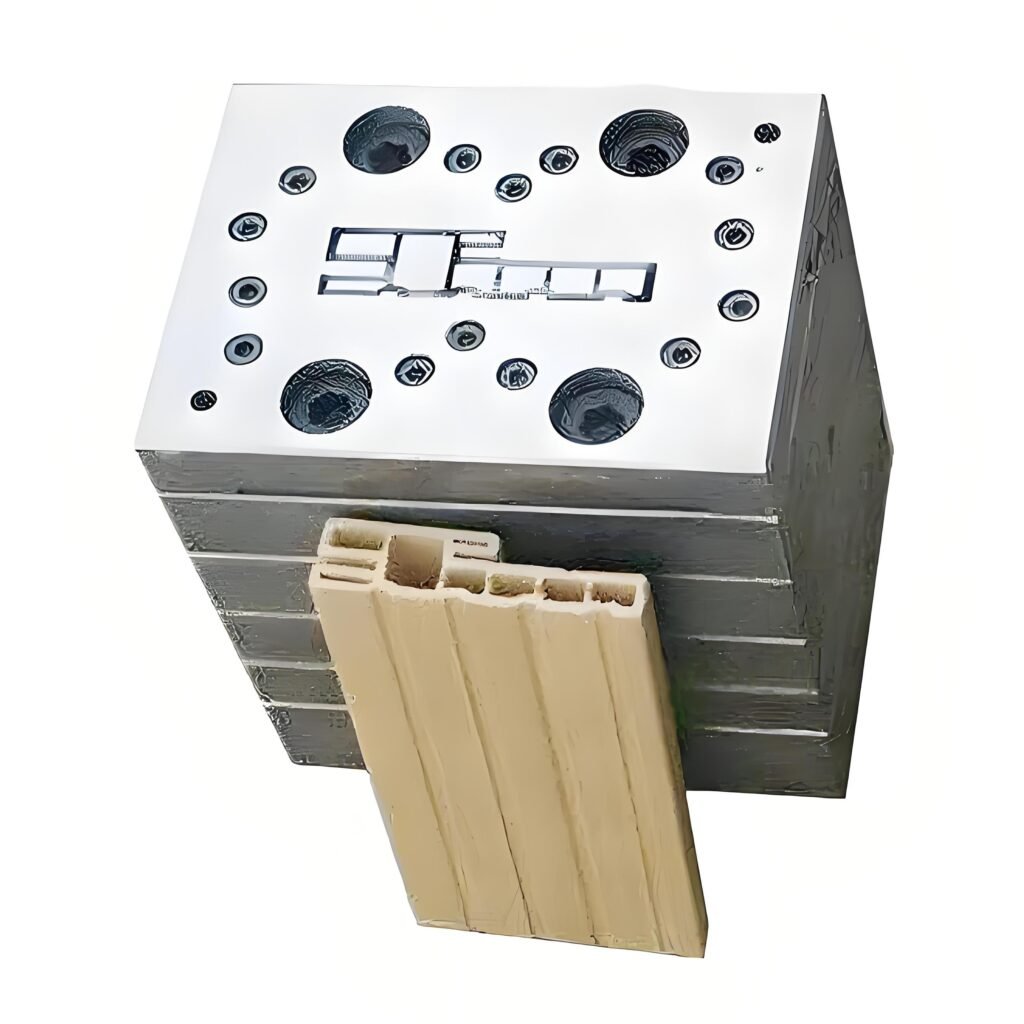
Le guide complet de la conception et de la fabrication des moules d'extrusion
Qu'est-ce qu'un moule d'extrusion et comment fonctionne-t-il ?
Les moules d'extrusion plastique, également appelés filières, sont très importants dans le processus d'extrusion plastique. L'extrusion du plastique est un moyen de fabriquer des formes longues à partir du plastique. Elle est utilisée pour fabriquer des tuyaux, des feuilles et des formes personnalisées. Les gens l'utilisent dans la construction, l'emballage et les voitures.
Qu'est-ce qu'un moule d'extrusion ?
Un moule d'extrusion plastique est un outil métallique qui façonne le plastique fondu en un profil transversal spécifique. Ces moules sont fabriqués en acier ou en aluminium et peuvent supporter les températures et les pressions élevées du processus d'extrusion.
La conception du moule, ou filière, détermine la forme finale du produit extrudé, ce qui en fait un facteur essentiel pour obtenir les dimensions et la qualité souhaitées.
Composants des moules d'extrusion plastique
L'efficacité d'un système d'extrusion dépend de plusieurs éléments essentiels :
① Trémie : Elle alimente l'extrudeuse en matières premières.
② Vis : Elle tourne pour transporter et faire fondre la matière plastique à l'intérieur du tonneau.
③ Barrel : Chauffe le plastique jusqu'à son point de fusion et le maintient à l'état fondu.
④ Filière (moule d'extrusion) : Forme le plastique fondu en un profil continu à la sortie de l'extrudeuse.
⑤ Système de refroidissement : Assure une bonne solidification de la matière extrudée.
⑥ Système d'extraction ou de convoyage : Maintient une vitesse constante pour éviter les déformations pendant le refroidissement.
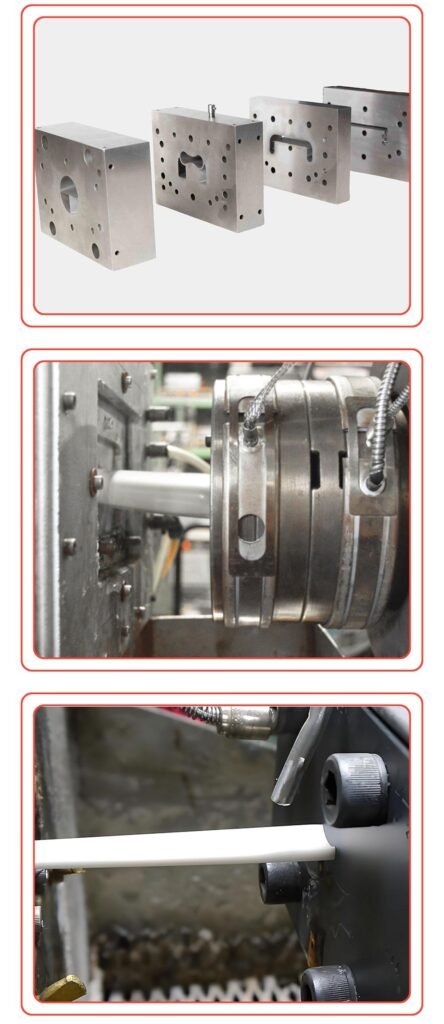
Comment fonctionnent les moules d'extrusion plastique ?
Le processus d'extrusion du plastique prend des matières plastiques brutes et les transforme en produits finis en les chauffant, en les façonnant et en les refroidissant. Voici comment cela fonctionne :
1. Alimentation en matériaux :
Le plastique brut, généralement sous forme de boulettes ou de granulés, est chargé dans une trémie. À ce stade, des additifs tels que des colorants, des stabilisants ou des charges peuvent être mélangés pour améliorer les propriétés telles que la couleur, la solidité ou la résistance aux UV.
2. La fusion :
La matière plastique est ensuite introduite dans un tonneau chauffé, où une vis rotative la fait fondre. La chaleur est générée à la fois par le frottement de la vis et par des éléments chauffants externes. La température du tonneau est généralement comprise entre 200 et 275 degrés Celsius, en fonction du type de plastique.
3. Mise en forme :
Le plastique fondu est poussé à travers une filière, également appelée moule d'extrusion. Cette filière donne au matériau la forme souhaitée. Le processus d'extrusion offre une grande flexibilité et permet d'obtenir des formes variées, telles que des tuyaux, des feuilles ou des conceptions personnalisées.
4. Refroidissement :
Une fois le plastique sorti de la matrice, il est rapidement refroidi par de l'air, des bains d'eau ou des rouleaux de refroidissement. Ce processus de refroidissement rapide solidifie le matériau et lui donne la forme voulue.
5. Découpage :
Le matériau extrudé refroidi et solidifié est ensuite coupé à la longueur requise. Il peut être coupé dans des dimensions spécifiques ou enroulé en rouleaux, en fonction de l'application.
6. Finition :
Après la découpe, des processus supplémentaires tels que le traitement de surface, l'ébarbage ou la mise en forme peuvent être effectués, en fonction de l'utilisation et des spécifications prévues pour le produit.
Quels sont les différents types de moules d'extrusion ?
Il existe de nombreux types de moules d'extrusion plastique, chacun étant conçu pour répondre à des besoins industriels et de produits spécifiques. Ces moules sont essentiels pour façonner le plastique brut en profils, feuilles ou films précis. Voici un résumé des différents types de moules d'extrusion plastique :
1. Matrices à vis unique :
Les filières à vis unique sont les moules d'extrusion les plus courants. Ils sont parfaits pour fabriquer des tuyaux, des tubes et des profilés. Elles sont bon marché et peuvent être utilisées pour extruder de nombreux plastiques différents tels que le PVC, le PE, le PP et l'ABS. Ils sont donc parfaits pour les grandes séries.
2. Matrices à double vis :
Les matrices à double vis utilisent deux vis pour un mélange et une fusion intenses, ce qui les rend adaptées à la fabrication de formes complexes ou de produits contenant beaucoup de matière de remplissage. Ces filières sont souvent utilisées dans des applications telles que les tubes multi-lumières ou les dispositifs médicaux tels que les cathéters, pour lesquels il est nécessaire de bien contrôler le matériau.
3. Matrices de coextrusion :
Les filières de co-extrusion sont conçues pour extruder plusieurs couches de plastique en même temps. Cela permet de fabriquer des produits présentant des caractéristiques particulières, comme des couches de protection ou d'isolation. Ces moules sont très utilisés pour les matériaux d'emballage. Ils peuvent assembler des plastiques ayant des points de fusion ou des propriétés différents pour améliorer le fonctionnement des produits.
4. Matrices de micro-extrusion :
Les matrices de micro-extrusion sont conçues pour fabriquer des pièces petites et précises telles que des appareils médicaux et électroniques. Elles produisent des pièces très précises et sont souvent utilisées avec des plastiques spéciaux comme le PEEK et le Téflon. Elles sont idéales pour fabriquer des pièces de très petite taille et de très petite forme.
5. Filières pour films plats et feuilles :
Les moules pour films plats et feuilles permettent de fabriquer des feuilles ou des films larges et minces, souvent utilisés dans l'emballage, les stratifiés et le thermoformage. Ces moules permettent d'obtenir une épaisseur uniforme grâce à des canaux d'écoulement réglables et fonctionnent avec des matériaux tels que le PET, le PE et le PVC.
6. Matrices à film soufflé :
Les filières de films soufflés sont utilisées pour fabriquer des films tubulaires qui sont soufflés avec de l'air. Elles sont idéales pour la fabrication de sacs en plastique, d'emballages rétractables et de films étirables. Comme elles sont rondes, elles donnent au film la même épaisseur sur tout le pourtour. Elles peuvent produire du LDPE, du HDPE et du PP.
7. Matrices pour tubes et tuyaux :
Les filières pour tubes et tuyaux sont conçues pour fabriquer des profils cylindriques creux tels que les tuyaux de plomberie et les tubes médicaux. Elles ont des interstices réglables pour modifier l'épaisseur de la paroi. Elles fonctionnent avec des matériaux tels que le PVC, le PEHD et le PP.
8. Matrices d'extrusion de profilés :
Les filières d'extrusion de profilés sont utilisées pour fabriquer des formes complexes telles que des cadres de fenêtres et des garnitures automobiles. Elles permettent de réaliser des moules précis de sections complexes et fonctionnent bien avec des matériaux tels que l'ABS, le PVC et le TPE, qui sont utilisés dans les applications industrielles et de construction.
9. Filières d'enrobage de fils et de câbles :
Les moules d'enrobage de fils et de câbles sont utilisés pour envelopper les fils ou les câbles dans des couches de plastique protectrices, qui assurent l'isolation des fils électriques et des fibres optiques. Ces moules sont conçus pour traiter des matériaux à haute température tels que le PVC et le XLPE, tout en garantissant des finitions lisses et durables.
10. Moules d'extrusion-soufflage :
Les moules d'extrusion-soufflage fabriquent des récipients creux tels que des bouteilles et des réservoirs de carburant en formant et en soufflant une paraison de plastique fondu. Avec un contrôle précis de la température pour s'assurer que les parois ont la même épaisseur tout autour, ils fonctionnent très bien avec le PET, le PEHD et le PP.
11. Matrices annulaires :
Les matrices annulaires produisent des formes circulaires telles que des anneaux et des tubes creux. Elles sont utiles pour les joints et les garnitures d'étanchéité. Elles permettent de fabriquer des produits de la bonne taille. Elles conviennent aux plastiques résistants tels que le nylon et le PP renforcé.
12. Matrices d'enduction de feuilles :
Les matrices d'enduction de feuilles sont utilisées pour appliquer de fines couches de plastique à des fins de laminage ou d'enduction. Elles sont utilisées dans les films décoratifs et les applications de barrière. Ces filières sont très précises et compatibles avec des matériaux tels que le TPU, l'EVA et le PE. Elles garantissent que les revêtements sont uniformes et durables.
13. Filières d'extrusion multicouches :
Les filières d'extrusion multicouches sont utilisées pour combiner plusieurs matériaux en un seul processus, créant ainsi des produits aux propriétés améliorées, tels que des films d'emballage ou des panneaux automobiles. Ces filières sont excellentes pour combiner des matériaux avancés tels que l'EVOH, le nylon et le PE, garantissant ainsi de meilleures performances pour des applications spécialisées.
Lignes directrices pour la conception des filières d'extrusion
Une conception efficace des filières d'extrusion est essentielle pour fabriquer des produits plastiques de haute qualité avec régularité et efficacité. Vous trouverez ci-dessous un ensemble consolidé et détaillé de lignes directrices couvrant tous les aspects de la conception des filières d'extrusion :
1. Principes de conception des matrices :
① Cohérence et efficacité : Veiller à ce que la filière produise un produit uniforme et cohérent, minimiser le gaspillage de matériaux et réduire les temps d'arrêt de la production.
② Durabilité : Conception pour résister aux contraintes opérationnelles, y compris les températures et les pressions élevées, garantissant la longévité et la fiabilité.
2. Sélection des matériaux :
① Durabilité et résistance : Utiliser des matériaux de haute qualité comme l'acier trempé ou le carbure de tungstène pour la résistance à l'usure et la stabilité thermique.
② Résistance à la corrosion : Choisissez des matériaux résistants aux environnements corrosifs, en particulier pour le traitement de matières plastiques agressives comme le PVC.
3. Géométrie des filières et conception des canaux d'écoulement :
① Conception rationalisée : Les canaux d'écoulement doivent être symétriques et lisses, en évitant les zones stagnantes afin de garantir une distribution uniforme du matériau et de réduire les défauts tels que le gauchissement ou l'épaisseur inégale.
② Transitions graduelles : Incorporer des transitions graduelles dans la forme de la filière afin de minimiser les contraintes sur le matériau et d'éviter les défauts dans le produit extrudé.
4. Longueur du terrain et dégagement :
① Longueur optimale du terrain : Maintenir une longueur de terrain d'environ 10 fois la hauteur libre du terrain afin de stabiliser l'écoulement et de garantir des dimensions cohérentes.
② Section transversale uniforme : La filière doit avoir une section constante pour éviter les variations d'épaisseur de l'extrudat.
5. Réglage de l'écartement des filières :
Conception réglable : L'espacement réglable permet d'ajuster avec précision l'épaisseur du matériau en cours de fonctionnement et de s'adapter aux différentes viscosités et exigences de production.
6. Gestion thermique et systèmes de refroidissement :
① Contrôle de la température : Des zones de chauffage et de refroidissement uniformes évitent les gradients thermiques et les déformations, préservant ainsi l'intégrité du produit.
② Refroidissement intégré : Utilisez des systèmes de refroidissement à l'eau ou à l'air pour stabiliser la température de la matrice et éviter la surchauffe.
7. Systèmes de ventilation :
Élimination de l'air : Ajouter des canaux de ventilation pour éliminer l'air emprisonné, assurer une finition de surface lisse et prévenir les défauts tels que les vides ou les poches d'air.
8. Finition de la surface et revêtement :
Surfaces intérieures lisses : Appliquer des traitements de surface (par exemple, chromage ou revêtement de nitrure) et obtenir une finition de type miroir pour réduire les frottements, améliorer l'écoulement des matériaux et prolonger la durée de vie des matrices.
9. Conception modulaire et facile à entretenir :
① Facilité d'entretien : Utiliser des conceptions modulaires pour faciliter le démontage, le nettoyage et le remplacement des composants, afin de minimiser les temps d'arrêt.
② Composants durables : Comprennent des pièces d'usure remplaçables pour réduire les coûts d'entretien à long terme.
10. Simulation et essais :
① Simulation CFD : Utilisez un logiciel de simulation avancé pour analyser les schémas d'écoulement, optimiser les géométries et prédire les performances.
② Essais de prototypes : Procéder à des essais approfondis afin d'identifier et de rectifier les problèmes potentiels avant la production à grande échelle.
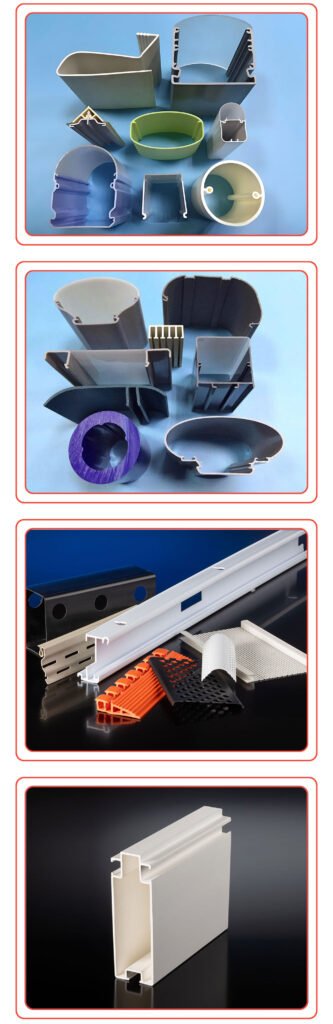
11. Alignement des matrices :
Alignement de précision : Assurer un alignement correct entre la filière, l'extrudeuse et l'équipement en aval afin d'éviter les pertes de matière, les flux irréguliers et les défauts de produit.
12. Conception pour la fabrication :
① Conception simplifiée : Évitez les géométries trop complexes qui compliquent l'assemblage et l'étalonnage. Les conceptions simples améliorent la fabricabilité et la fiabilité.
② Ajustement et intégration : Testez la compatibilité des extrusions personnalisées avec d'autres composants afin de garantir une intégration parfaite.
13. Considérations relatives au nettoyage et à l'entretien :
① Systèmes de nettoyage faciles : Les matrices doivent être conçues de manière à inclure des mécanismes de nettoyage accessibles afin d'éliminer les résidus et de prévenir la contamination.
② Maintenance programmée : Établir des calendriers d'inspection et de nettoyage réguliers pour garantir des performances optimales des matrices et la qualité des produits.
14. Pratiques de conception avancées :
① Une philosophie de conception claire : Privilégier la simplicité, l'efficacité et la réduction des déchets.
② Utilisation de logiciels : Utiliser des logiciels spécialisés pour répondre aux exigences spécifiques des produits et simuler les performances dans différentes conditions.
Quels sont les matériaux couramment utilisés pour les moules d'extrusion ?
Le moulage par extrusion est un procédé de fabrication polyvalent qui permet de fabriquer des produits thermoplastiques. Les matériaux utilisés pour les moules jouent un rôle important dans la qualité du produit final. Voici un aperçu des matériaux les plus couramment utilisés pour les moules d'extrusion plastique et des éléments à prendre en compte pour choisir le matériau le mieux adapté à votre application.
1. L'acier :
L'acier est le matériau le plus utilisé pour les moules d'extrusion. Il est connu pour sa solidité, sa durabilité et sa résistance à l'usure exceptionnelles. L'acier pour travail à froid de haute qualité offre une excellente dureté, ce qui le rend idéal pour les moules de production en grande quantité, tandis que l'acier pour travail à chaud peut supporter des températures extrêmes, ce qui garantit sa longévité dans les environnements soumis à des contraintes thermiques. Les aciers à outils alliés offrent un équilibre entre la ténacité, la résistance à l'usure et l'usinabilité, ce qui les rend polyvalents pour diverses applications, notamment les moules pour PVC, PEHD et ABS.
2. Alliages d'aluminium :
Les alliages d'aluminium sont une option légère et rentable, largement utilisée pour le prototypage et les petites séries. Leur excellente conductivité thermique permet de réduire les temps de refroidissement et d'améliorer l'efficacité. Si l'aluminium est plus facile à usiner que l'acier, sa dureté et sa résistance à l'usure sont moindres, ce qui limite son utilisation à des applications peu contraignantes. Il convient mieux aux moules à géométrie simple et à la production de faibles volumes.
3. Cuivre et alliages de cuivre :
Le cuivre et ses alliages, en particulier le béryllium-cuivre, sont appréciés pour leur conductivité thermique et leur résistance à la corrosion supérieures. Ces matériaux sont particulièrement efficaces pour les moules nécessitant un contrôle précis de la température, ce qui permet d'éviter les déformations et les défauts dans les profils d'extrusion complexes. Les moules à base de cuivre sont souvent utilisés dans des applications exigeant des finitions de haute qualité et une gestion cohérente de la température.
4. Alliages de titane :
Les alliages de titane sont connus pour leur rapport poids/résistance impressionnant et leur excellente résistance à la corrosion. Ils sont particulièrement adaptés aux moules de haute précision et aux applications spécialisées où des tolérances strictes sont essentielles. La légèreté du titane en fait également un bon choix pour les moules utilisés dans des secteurs tels que la fabrication médicale et aérospatiale.
5. Matériaux céramiques :
Les matériaux céramiques sont choisis pour leur dureté exceptionnelle et leur résistance aux températures élevées. Ces caractéristiques les rendent idéales pour les moules utilisés dans des conditions extrêmes, telles que les applications à haute pression ou à haute température. Toutefois, les céramiques sont fragiles, ce qui peut limiter leur utilisation dans les applications nécessitant une résistance aux chocs mécaniques.
6. Plastiques et matériaux composites :
Des plastiques spécialisés et des composites sont parfois utilisés comme matériaux de moulage lorsque des structures légères ou une résistance chimique sont requises. Le PTFE (téflon) est souvent choisi pour ses propriétés anti-adhérentes, facilitant le démoulage dans les applications à faible production. Ces matériaux sont rentables et offrent des avantages uniques pour des cas d'utilisation spécifiques, mais ils sont généralement limités à des environnements peu contraignants.
7. Laiton et autres alliages de cuivre :
Le laiton, un alliage de cuivre et de zinc, est souvent choisi pour sa facilité d'usinage et sa résistance à la corrosion. Il offre une finition de surface de haute qualité et convient aux moules utilisés dans des volumes de production faibles à modérés. La combinaison de sa précision et de son prix abordable en fait une option intéressante pour certaines applications.
8. Verre et silicone :
Le verre et le silicone sont des matériaux spécialisés utilisés dans des applications de niche exigeant des niveaux élevés de précision, de flexibilité ou des finitions de surface uniques. Les moules en silicone sont idéaux pour les conceptions complexes et offrent une excellente flexibilité, tandis que les moules en verre offrent une précision dimensionnelle supérieure, mais sont coûteux et fragiles, ce qui limite leur utilisation à grande échelle.
Facteurs à prendre en compte lors du choix des matériaux de moulage
① Volume de production :
Les moules de production à haut volume nécessitent des matériaux tels que des aciers à outils pour leur durabilité, tandis que les moules de production à faible volume peuvent utiliser de l'aluminium ou des matériaux composites.
② Performance thermique :
Les matériaux tels que l'aluminium ou les alliages de cuivre sont préférés pour leur conductivité thermique, ce qui garantit des cycles de refroidissement efficaces.
③ Finition de la surface :
Le laiton ou l'acier inoxydable sont excellents pour les finitions de haute qualité, tandis que les céramiques sont idéales pour la précision.
④ Résistance à la corrosion :
Les aciers inoxydables, le titane et les alliages de cuivre résistent à la corrosion, ce qui est essentiel pour les applications médicales ou alimentaires.
⑤ Coût et entretien :
L'aluminium est rentable pour le prototypage, tandis que les aciers prétrempés réduisent le temps d'usinage et les coûts pour les moules de production durables.
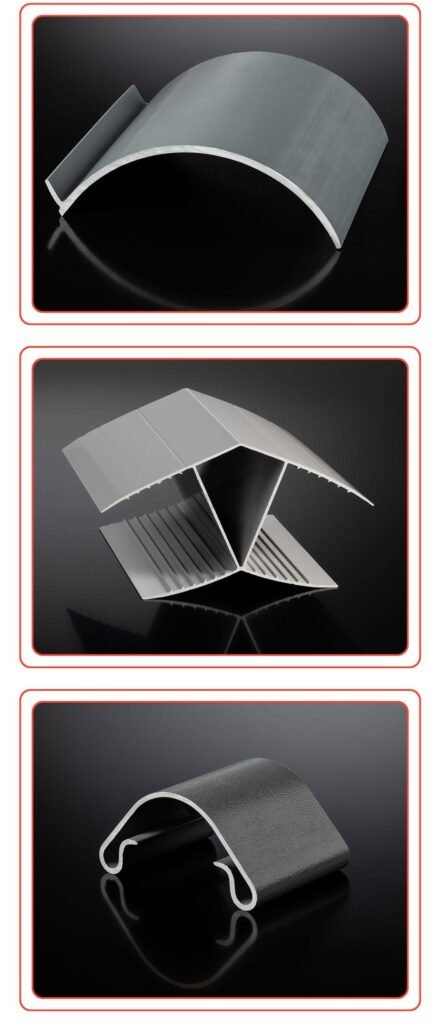
Comment les propriétés des matériaux des moules influencent-elles la conception des moules ?
Les propriétés des matériaux de moulage sont fondamentales pour la conception, les performances et la longévité des moules utilisés dans les processus d'injection et d'extrusion. Elles influencent des facteurs tels que la gestion thermique, la durabilité, la qualité du produit et l'efficacité de la fabrication. Voici un guide complet sur l'impact de ces propriétés sur la conception des moules :
1. Conductivité thermique :
① Impact : Les matériaux à forte conductivité thermique (aluminium, cuivre, etc.) dissipent efficacement la chaleur, réduisant ainsi les temps de refroidissement et évitant des problèmes tels que le gauchissement ou la déformation des pièces moulées. À l'inverse, des matériaux comme l'acier, dont la conductivité thermique est plus faible, peuvent nécessiter des systèmes de refroidissement supplémentaires.
② Considérations relatives à la conception : Utiliser des matériaux à haute conductivité pour les moules en donnant la priorité à la vitesse et au refroidissement uniforme, mais les équilibrer avec un renforcement structurel pour la durabilité.
2. Dilatation thermique :
① Impact : Les variations des taux de dilatation thermique peuvent entraîner des imprécisions dimensionnelles lors des changements de température. Les matériaux tels que l'acier ou la céramique, dont la dilatation thermique est faible, offrent une plus grande stabilité dimensionnelle.
② Considérations relatives à la conception : Pour les procédés à haute température ou les tolérances serrées, choisir des matériaux dont la dilatation est minimale pour maintenir la précision.
3. Solidité et durabilité :
① Impact : les matériaux à haute résistance (par exemple, l'acier trempé, le titane) supportent les pressions et les températures élevées du moulage par injection ou de l'extrusion. Ces matériaux résistent à la déformation, ce qui garantit une qualité constante des pièces sur des cycles de production prolongés.
② Considérations relatives à la conception : Utilisez des matériaux durables pour les moules à géométrie complexe ou pour la production de grandes quantités. Pensez à des aciers à outils comme le P20 ou le H13 pour leur équilibre entre résistance et usinabilité.
4. Résistance à l'usure :
① Impact : L'utilisation continue et les matériaux abrasifs peuvent dégrader les surfaces des moules. Les matériaux résistants à l'usure réduisent la fréquence des entretiens et prolongent la durée de vie des moules.
② Considérations relatives à la conception : Optez pour des revêtements (par exemple, nitruration, chromage) ou des matériaux plus durs lorsque vous moulez des matières plastiques abrasives ou remplies de verre.
5. Résistance à la corrosion :
① Impact : L'exposition à l'humidité, aux produits chimiques ou aux additifs corrosifs contenus dans certains plastiques peut dégrader les moules et affecter la qualité du produit. L'acier inoxydable et les moules revêtus offrent une meilleure résistance.
② Considérations relatives à la conception : Utiliser des matériaux résistants à la corrosion pour les moules exposés à des environnements réactifs, ou appliquer des traitements de surface protecteurs pour une plus grande longévité.
6. Usinabilité :
① Impact : Les matériaux plus faciles à usiner, comme l'aluminium, réduisent les délais et les coûts de production, mais peuvent ne pas avoir la durabilité de l'acier ou du titane.
② Considérations relatives à la conception : Pour les moules prototypes ou les petites séries, les matériaux usinables permettent de gagner du temps. Les moules de production peuvent justifier les coûts d'usinage plus élevés des matériaux durables.
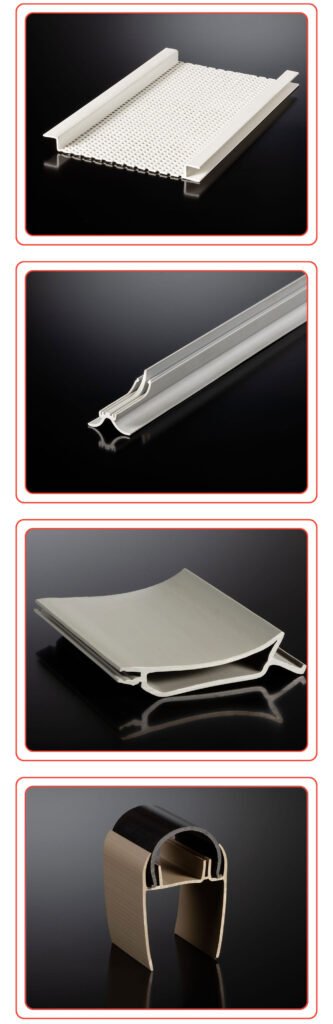
7. Finition de la surface :
① Impact : La qualité de la surface du moule influe sur l'esthétique du produit final et sur la facilité de démoulage. Des finitions de haute qualité minimisent les défauts et réduisent les temps de cycle.
② Considérations relatives à la conception : Choisissez des matériaux permettant d'obtenir des finitions lisses, comme l'acier à outils, pour les pièces présentant des exigences esthétiques ou fonctionnelles critiques.
8. Résistance chimique :
① Impact : Certains plastiques ou additifs peuvent dégrader les surfaces des moules. Des matériaux comme l'acier inoxydable ou le titane résistent à l'exposition aux produits chimiques et préservent l'intégrité du moule.
② Considérations relatives à la conception : Pour les moules utilisés avec des résines chimiquement agressives, privilégier les matériaux résistants ou les revêtements protecteurs.
9. Le coût :
① Impact : Les matériaux haut de gamme comme l'acier trempé ou le titane augmentent les coûts initiaux mais réduisent les dépenses d'entretien et de remplacement au fil du temps.
② Considérations relatives à la conception : Équilibrer les coûts des matériaux avec le volume de production prévu et les exigences opérationnelles afin d'optimiser le retour sur investissement.
Techniques de fabrication des moules d'extrusion plastique
Les moules d'extrusion plastique, également connus sous le nom de matrices d'extrusion, sont créés à l'aide d'un large éventail de techniques afin d'obtenir la forme, la taille et la fonctionnalité souhaitées. Vous trouverez ci-dessous un aperçu complet des techniques de fabrication les plus couramment utilisées, combinant des détails clés pour une meilleure compréhension :
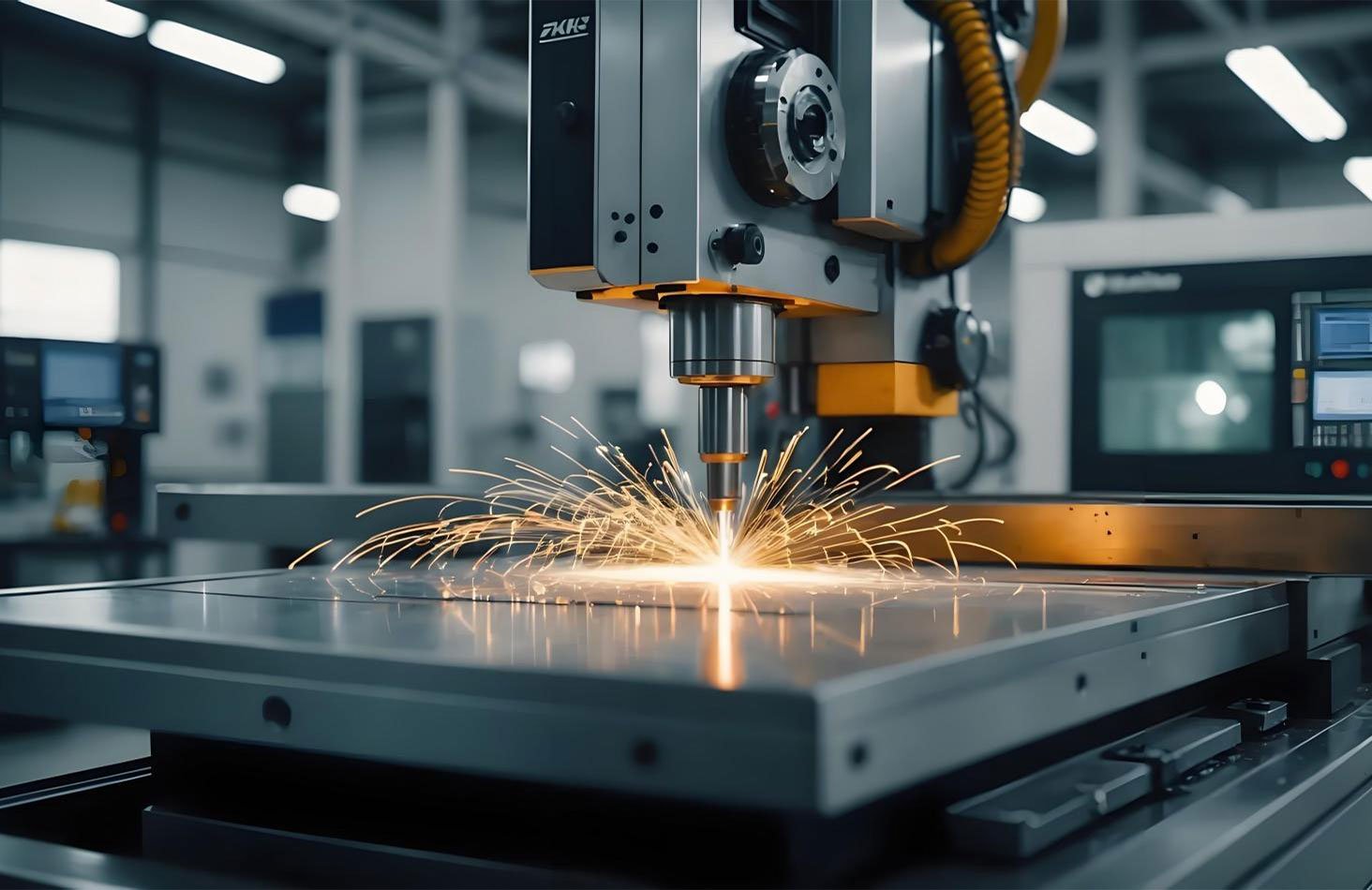
1. Usinage CNC :
L'usinage CNC utilise des outils de coupe commandés par ordinateur pour façonner avec précision des matériaux de moulage tels que l'acier ou l'aluminium. Il est très précis et permet d'obtenir des tolérances serrées, ce qui le rend idéal pour créer des composants de moules primaires et des géométries externes avec précision et cohérence.
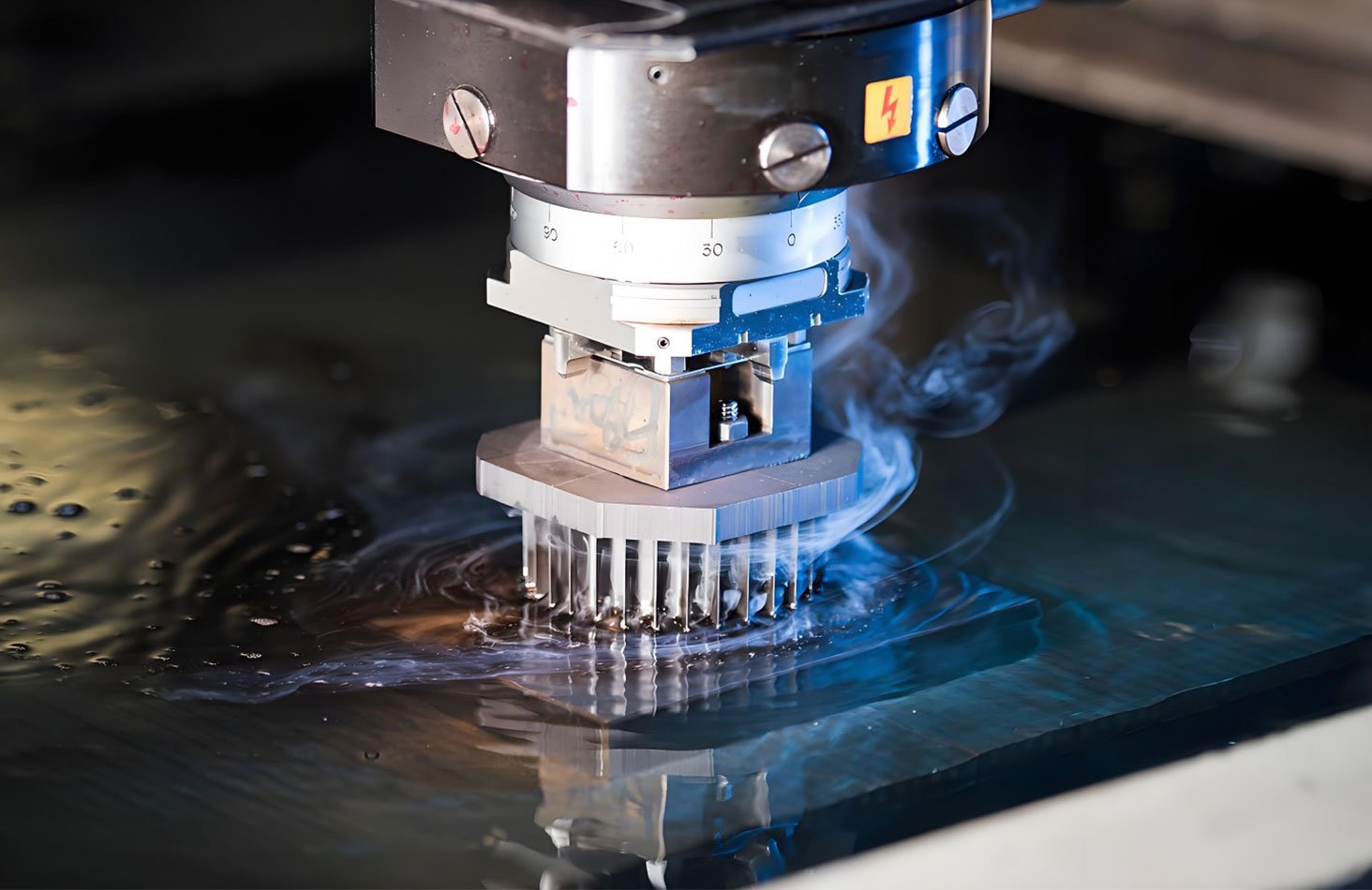
2. EDM :
L'électroérosion utilise des décharges électriques pour éroder la matière, ce qui permet de créer des formes complexes, des cavités profondes et des géométries internes compliquées. Elle comprend des variantes telles que l'électroérosion par enfonçage pour les cavités détaillées et l'électroérosion par fil pour les coupes précises, ce qui la rend adaptée aux canaux d'écoulement étroits et aux angles vifs.
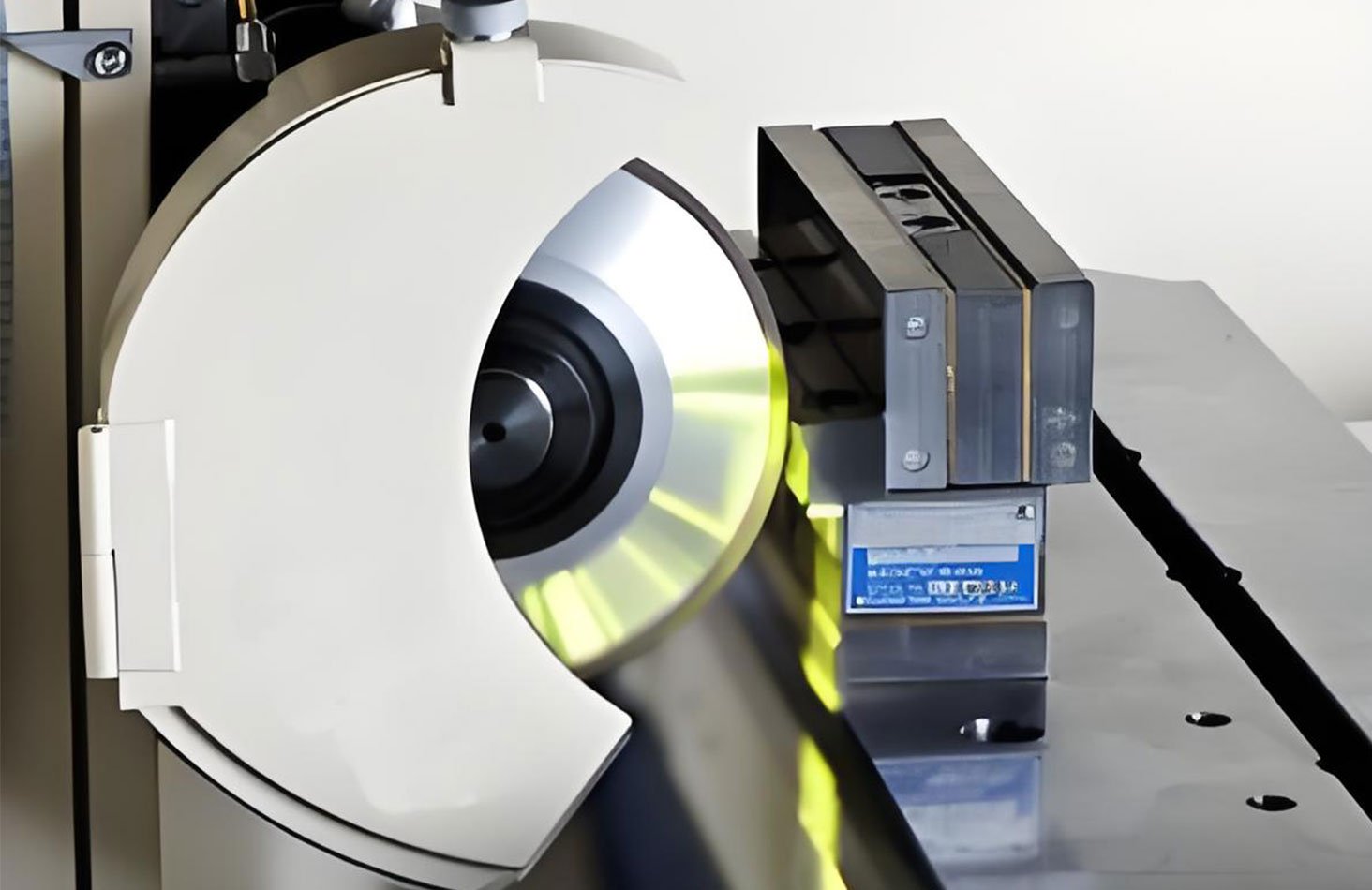
3. Broyage :
La rectification est utilisée pour améliorer l'état de surface et la précision des composants des moules en enlevant de petites quantités de matière par action abrasive. Elle est couramment employée dans les étapes finales de la fabrication des moules pour obtenir des surfaces lisses et respecter des tolérances dimensionnelles serrées.
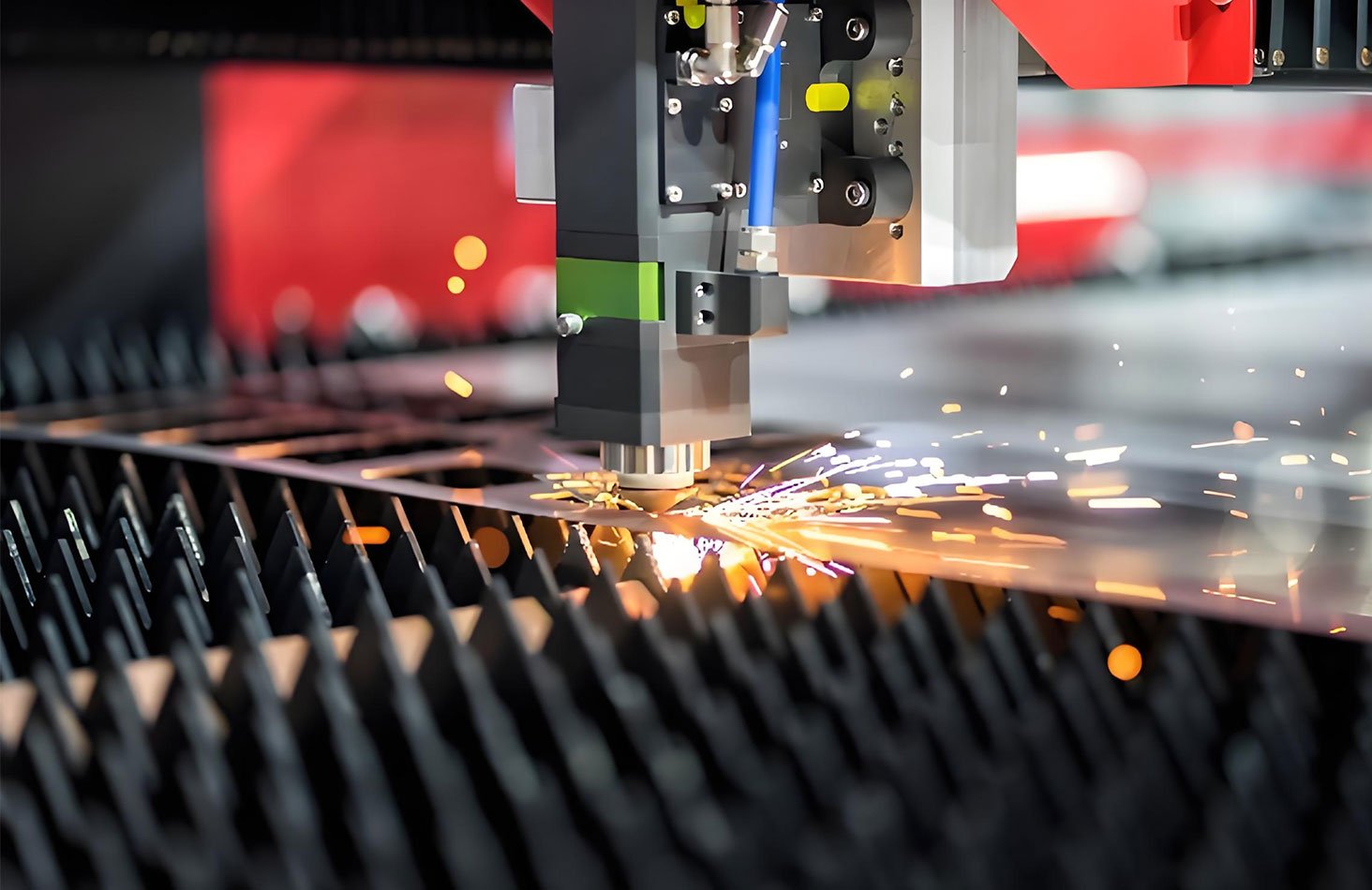
4. Découpe au laser :
La découpe laser utilise un faisceau laser de haute puissance pour découper et façonner les matériaux de moulage avec une excellente précision. Elle est couramment utilisée pour les plaques minces ou pour créer des motifs complexes dans les composants des moules, offrant ainsi une solution de découpe rapide et efficace.
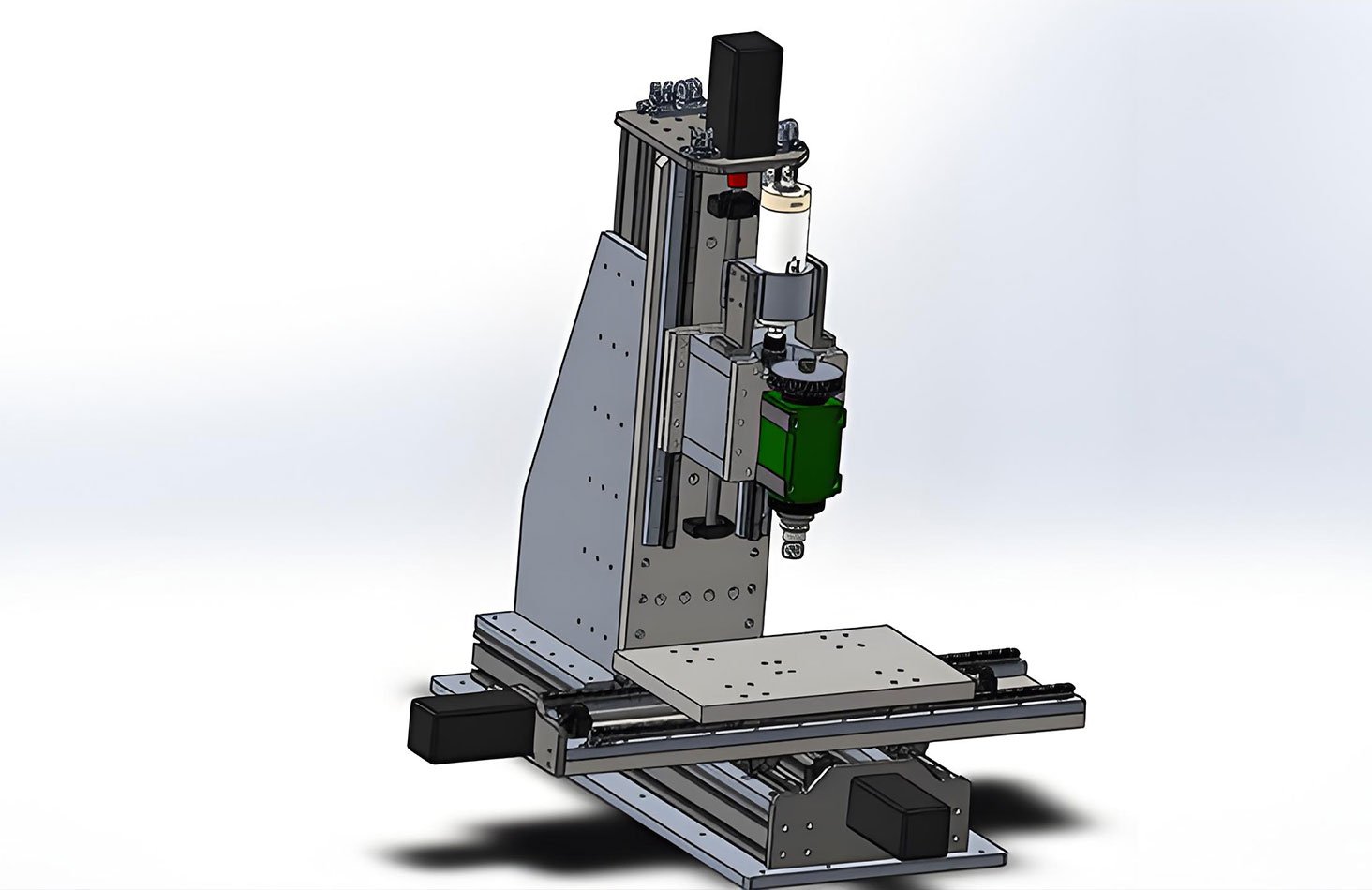
5. Fraisage :
Le fraisage consiste à utiliser un outil de coupe rotatif, ou fraise, pour enlever de la matière d'une pièce. Cette technique est idéale pour l'usinage de grandes surfaces planes avec une grande précision, ainsi que pour la création de fentes, de contours et d'autres caractéristiques complexes dans les composants de moules.
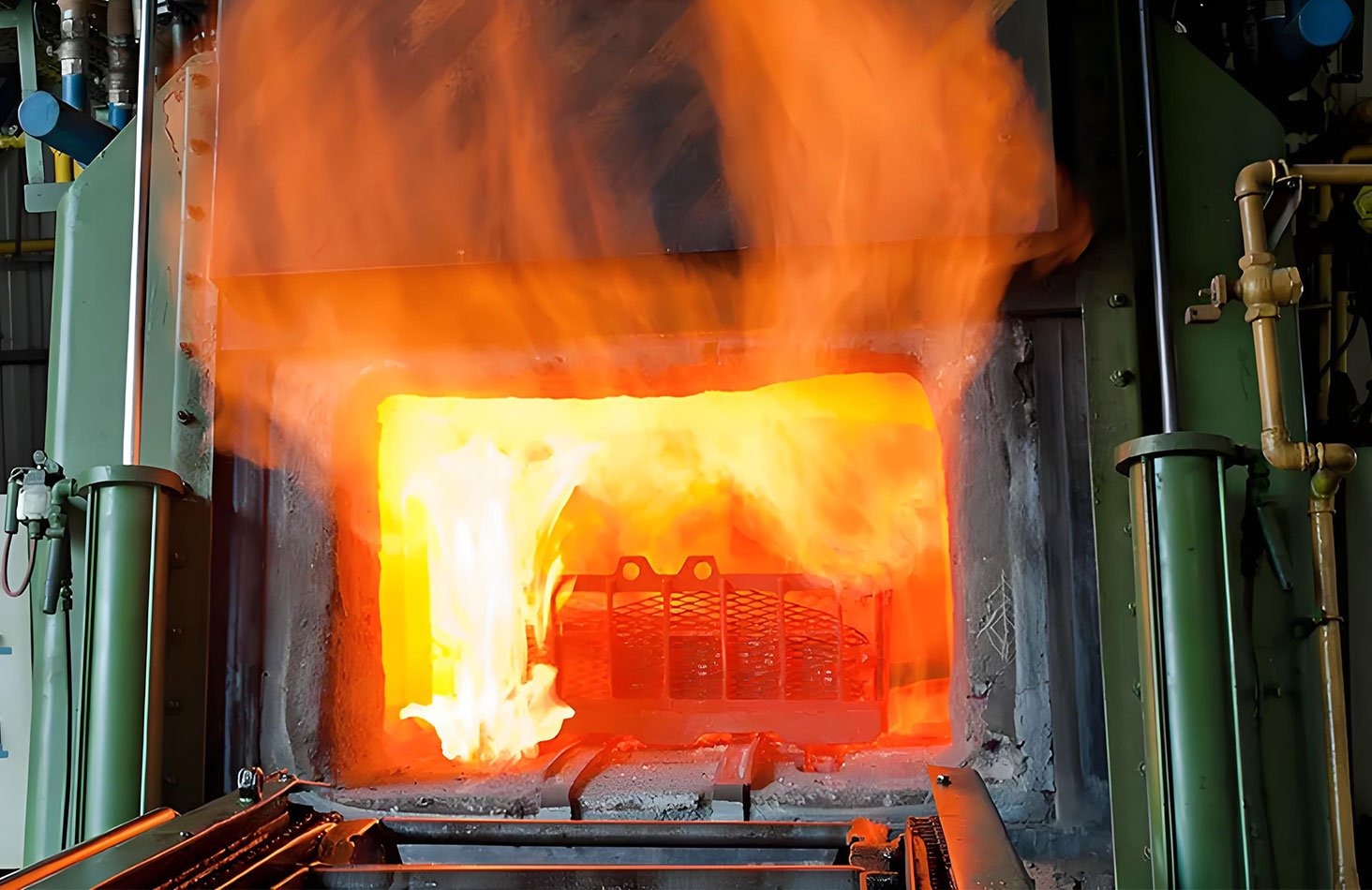
6. Traitement thermique :
Les processus de traitement thermique, tels que la trempe, le revenu et le durcissement superficiel, sont utilisés pour améliorer les propriétés des matériaux des moules. Ces traitements améliorent la durabilité, la résistance à l'usure et la solidité des moules, garantissant ainsi qu'ils répondent aux exigences des applications à hautes performances.
Quels sont les processus de fabrication des moules d'extrusion plastique ?
La fabrication de moules d'extrusion plastique implique plusieurs processus clés qui transforment les matières premières en moules fonctionnels pour l'extrusion plastique. Vous trouverez ci-dessous une analyse détaillée de ces processus, combinant à la fois des étapes générales et des considérations spécifiques pour garantir une qualité et des performances optimales :
Étape 1 : Conception et ingénierie :
La phase de conception et d'ingénierie est la première étape de la fabrication d'un moule d'extrusion plastique. Des dessins détaillés sont créés à l'aide de logiciels de CAO (conception assistée par ordinateur) et des simulations sont effectuées pour s'assurer que le moule peut répondre aux spécifications du produit et gérer l'écoulement du matériau et les contraintes thermiques. Au cours de cette phase, on tient compte du type de plastique, de sa viscosité, des dimensions du produit, des tolérances et de la compatibilité avec la machine d'extrusion. La conception finale doit minimiser les défauts et optimiser le processus de production, afin de garantir une fabrication efficace et sans heurts.
Étape 2 : Sélection des matériaux :
Le choix du bon matériau pour le moule est crucial pour garantir la durabilité, la résistance à l'usure et la capacité à supporter les pressions et les températures élevées rencontrées lors de l'extrusion. Les matériaux couramment utilisés sont les aciers à outils tels que le P20, le H13 ou l'acier inoxydable. Lors de la sélection des matériaux, des facteurs tels que la température et la pression de fonctionnement, le type de plastique utilisé et l'équilibre entre le coût et la performance doivent être pris en compte. Des matériaux de haute qualité garantissent la longévité et la stabilité du moule dans des conditions difficiles.
Étape 3 : Usinage :
Une fois la conception et la sélection des matériaux terminées, le moule entre dans la phase d'usinage. Des techniques d'usinage de haute précision, notamment le fraisage, le tournage, le perçage et l'électroérosion (EDM) à commande numérique, sont utilisées pour fabriquer les composants du moule. Ces méthodes permettent de s'assurer que le moule répond aux exigences de précision dimensionnelle, l'EDM étant particulièrement utile pour les détails complexes. Il est essentiel d'obtenir des finitions de surface lisses pour minimiser l'adhérence du plastique pendant l'extrusion et garantir une production efficace.
Étape 4 : Traitement thermique :
Le traitement thermique est une étape cruciale pour améliorer la solidité et la résistance à l'usure du moule. Les traitements thermiques courants comprennent la trempe, le revenu et la nitruration, qui améliorent la dureté du moule et lui permettent de supporter des pressions et des températures élevées pendant le processus d'extrusion. Il est essentiel d'équilibrer la dureté et la ténacité pour éviter la fragilité. Il est essentiel de minimiser les déformations au cours du processus de traitement pour maintenir la précision du moule.
Étape 5 : Polissage et finition :
Après le traitement thermique, le moule subit un polissage et une finition de surface. Les surfaces internes sont polies pour améliorer l'écoulement du plastique et la qualité de la surface du produit. Des revêtements tels que le chrome ou le nickel peuvent également être appliqués pour améliorer la résistance à la corrosion et à l'usure. La douceur de la surface du moule influe directement sur ses performances et sa longévité, tandis que le revêtement aide à prévenir la corrosion et l'abrasion, garantissant ainsi la durabilité du moule tout au long de son cycle de vie.
Étape 6 : Assemblage :
Une fois tous les composants usinés et finis, le moule est soigneusement assemblé. Il s'agit d'aligner les cavités du moule, les inserts et les autres pièces pour s'assurer que tout s'emboîte correctement. Les fixations et les joints sont appliqués pour garantir l'étanchéité du moule et maintenir l'intégrité des voies d'écoulement pendant l'extrusion. Il est important de respecter des tolérances strictes lors de l'assemblage afin d'éviter les problèmes de production et de garantir que le moule fonctionnera correctement dans les conditions opérationnelles.
Étape 7 : Essais et validation :
Après l'assemblage, le moule est testé dans des conditions réelles d'extrusion en utilisant des échantillons de matériaux. L'objectif de ces essais est d'identifier tout problème tel qu'un écoulement irrégulier, des fuites ou des imprécisions dimensionnelles. Si des problèmes sont détectés, la conception du moule ou les paramètres du processus sont ajustés pour les résoudre. Grâce à des essais et à des perfectionnements rigoureux, le moule est validé pour répondre aux exigences de la production, ce qui garantit une production constante et de haute qualité.
Étape 8 : Maintenance et documentation :
Pour garantir la fiabilité du moule au fil du temps, un programme d'entretien est mis au point. Un nettoyage, une lubrification et des inspections régulières sont essentiels, et les composants usés doivent être remplacés rapidement. Une documentation détaillée des fichiers de conception, des paramètres d'usinage et des dossiers d'entretien est également conservée pour référence ultérieure. De bonnes pratiques d'entretien permettent de minimiser les temps d'arrêt et d'allonger la durée de vie du moule, garantissant ainsi une production efficace à long terme.
Comment les moules d'extrusion sont-ils utilisés dans les différentes industries ?
Les moules d'extrusion sont un outil polyvalent et essentiel dans de nombreuses industries pour la création d'une large gamme de produits. En façonnant les matériaux à travers une filière, les moules d'extrusion permettent la production efficace et continue d'articles aux profils transversaux complexes. Voici un aperçu détaillé de l'utilisation des moules d'extrusion dans différents secteurs.
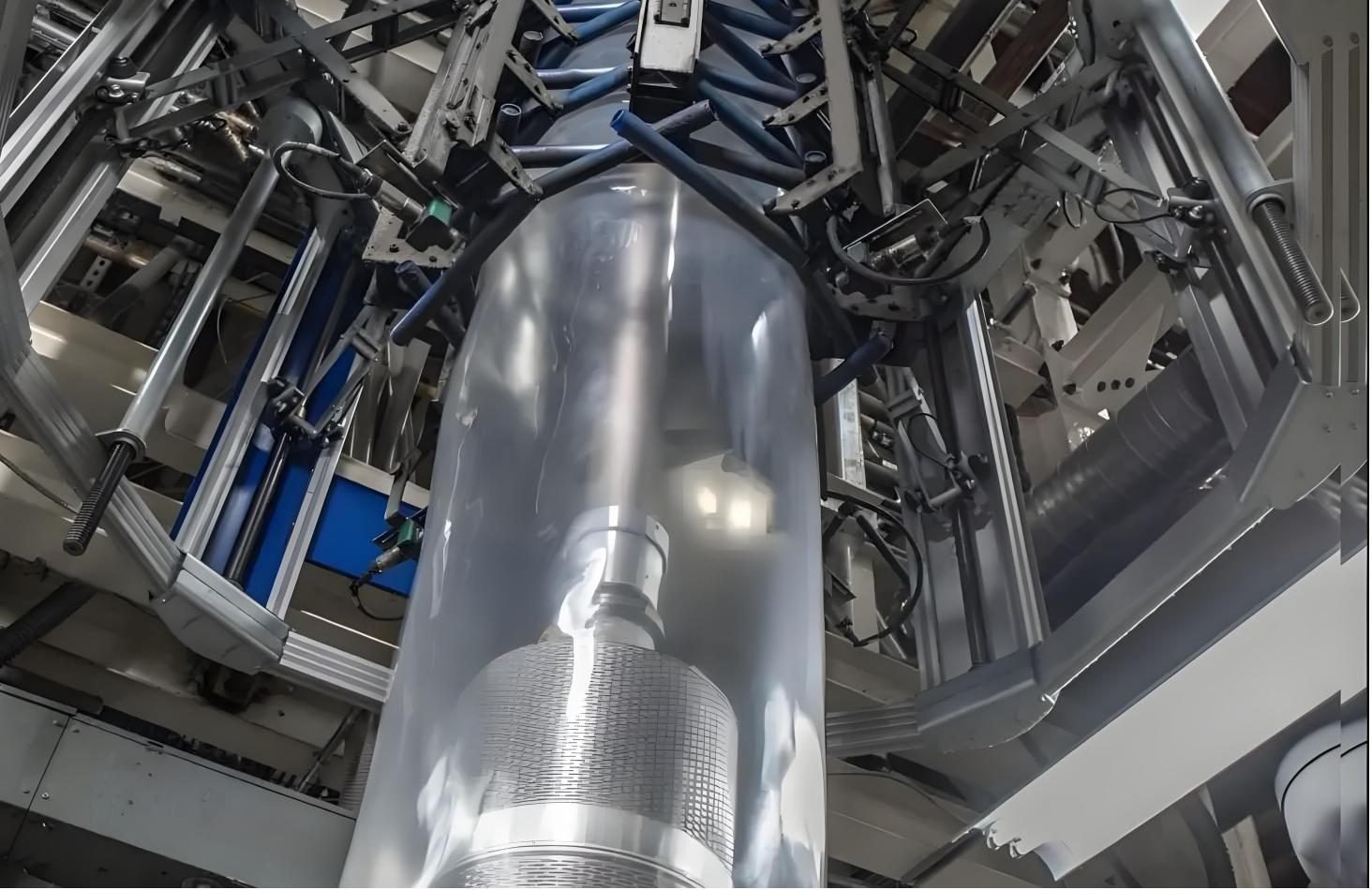
1. Industrie de l'emballage :
Dans l'industrie de l'emballage, les moules d'extrusion sont utilisés pour produire divers matériaux d'emballage en plastique, notamment des bouteilles, des conteneurs et des tubes pour les aliments, les boissons et les produits de soins personnels. Les matériaux les plus courants sont le polyéthylène (PE), le polypropylène (PP) et le PET, qui sont idéaux pour créer des solutions d'emballage légères, flexibles et rentables. Le processus d'extrusion garantit une production en grande quantité avec un minimum de déchets, répondant ainsi à la demande de l'industrie pour des articles produits en masse avec une qualité constante.
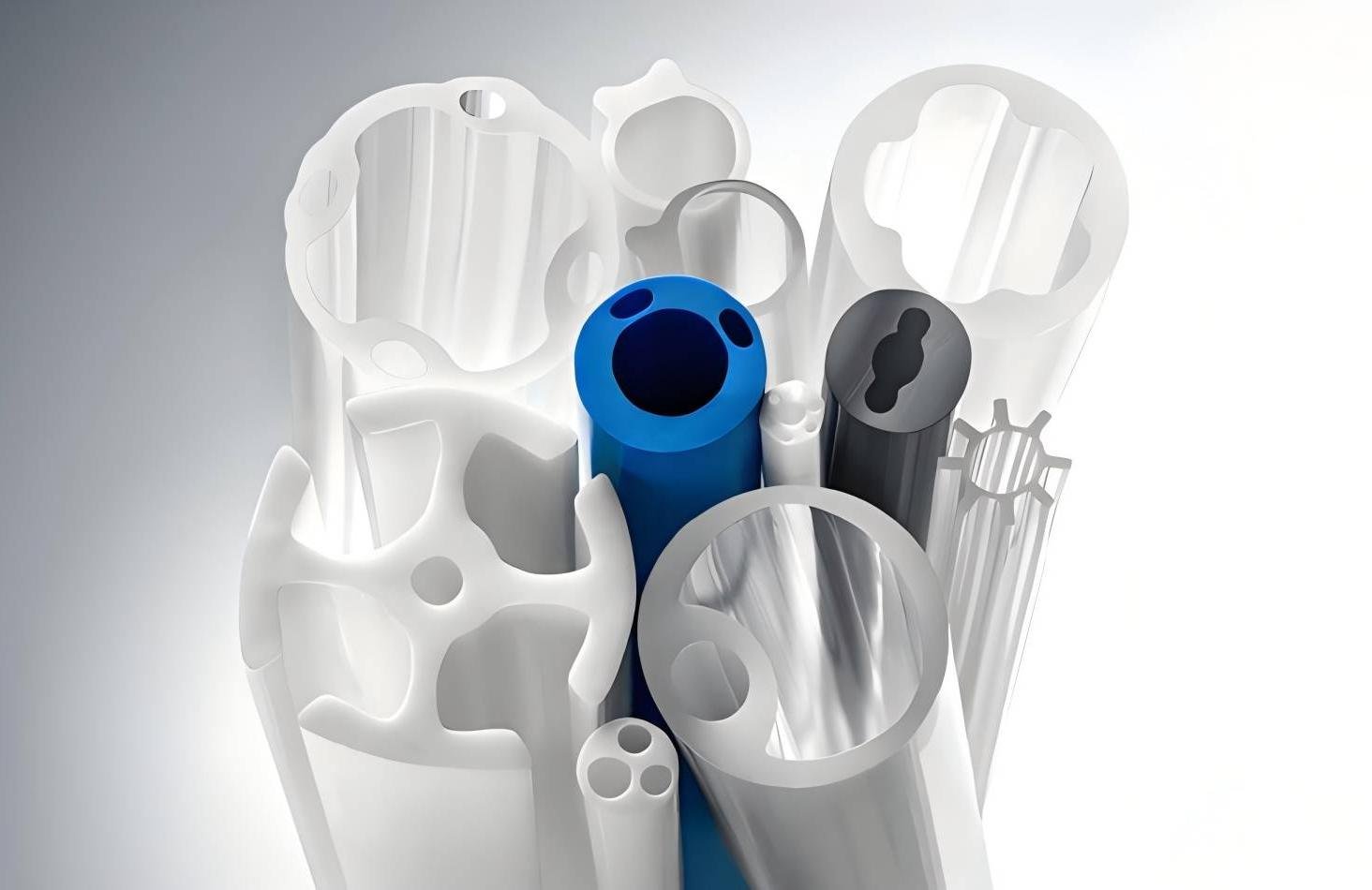
2. Industrie médicale :
Les moules d'extrusion sont essentiels dans l'industrie médicale pour la production de dispositifs tels que les cathéters, les fils-guides, les tubes chirurgicaux et les dispositifs implantables. Des matériaux tels que le PVC, le polyéthylène (PE) et le polypropylène (PP) sont couramment utilisés en raison de leur biocompatibilité et de leur durabilité. La précision de l'extrusion garantit que les composants médicaux répondent aux normes réglementaires strictes en matière de sécurité, d'hygiène et de performance, ce qui les rend indispensables à la production de produits médicaux fiables et de haute qualité.
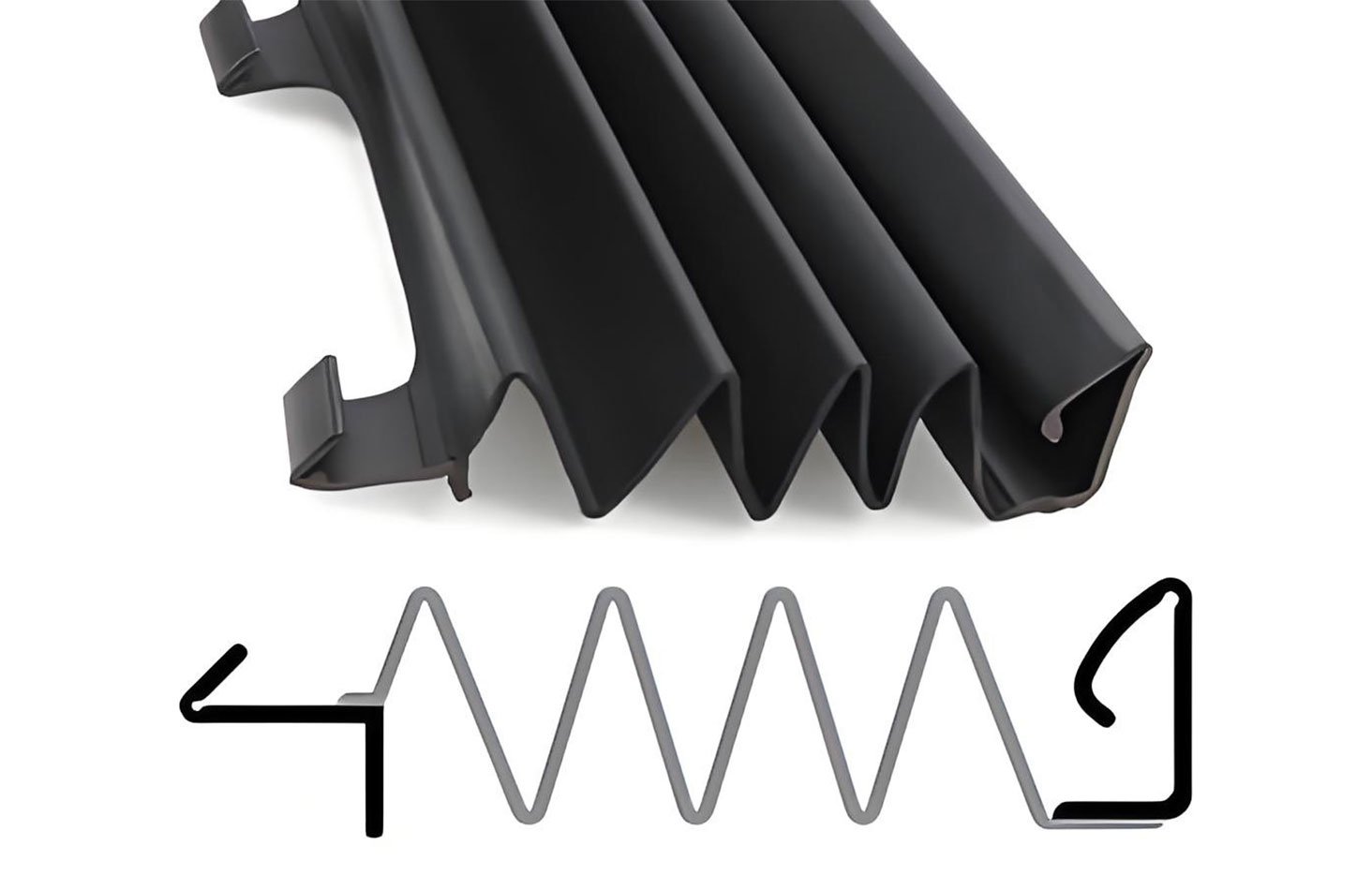
3. Industrie automobile :
Dans le secteur automobile, les moules d'extrusion sont utilisés pour fabriquer des composants légers mais durables tels que les conduites de carburant, les conduites de frein, les conduits d'air, les cadres de fenêtres et les joints d'étanchéité. Les matériaux utilisés sont l'aluminium, le PVC et divers thermoplastiques. Ces matériaux sont résistants tout en conservant un faible poids, ce qui améliore les performances des véhicules et le rendement énergétique. Le processus d'extrusion permet de produire des pièces aux formes et profils complexes, ce qui est essentiel pour les conceptions automobiles modernes.
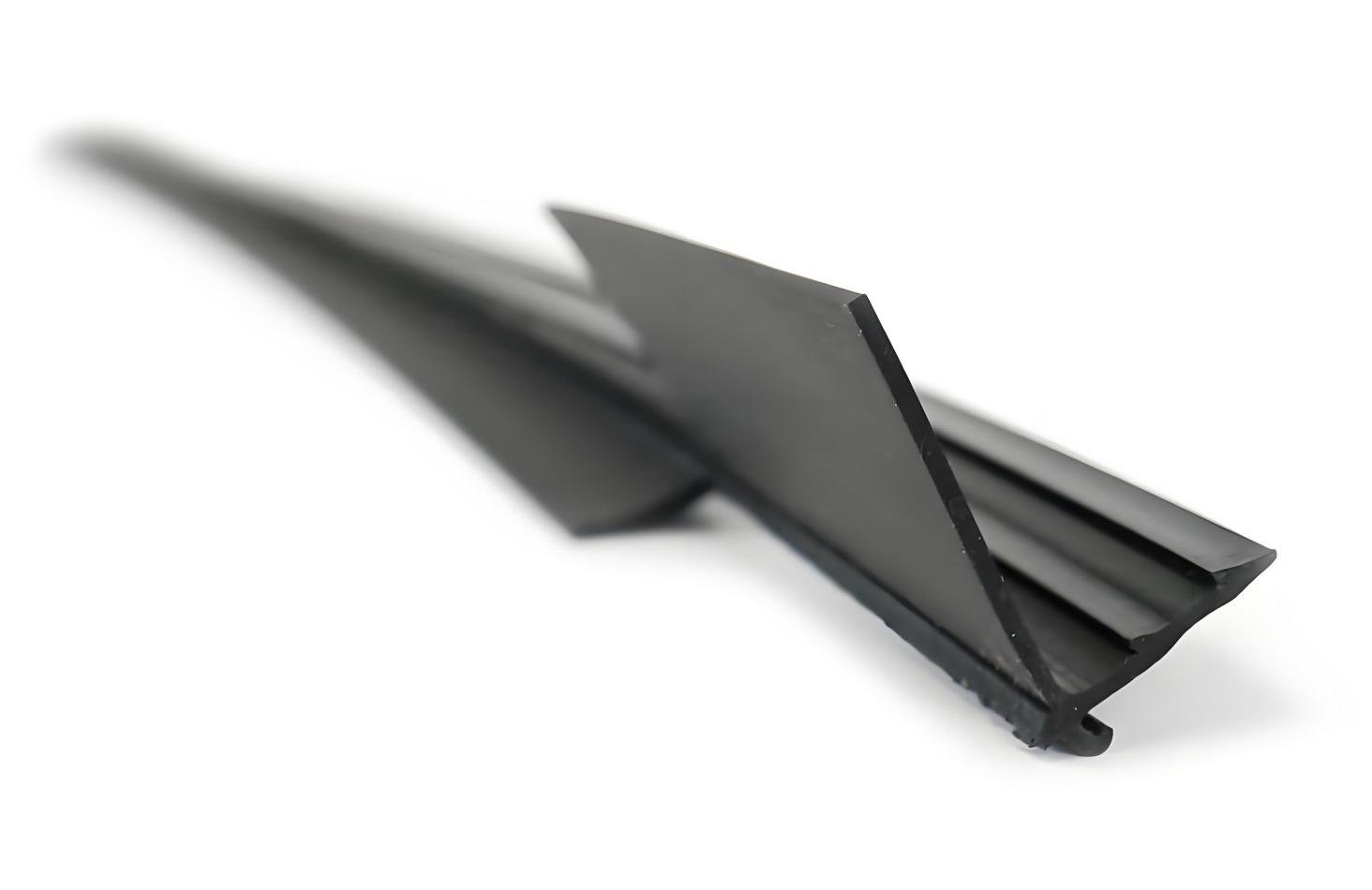
4. Industrie aérospatiale :
Dans l'industrie aérospatiale, les moules d'extrusion sont utilisés pour créer des composants légers et très résistants tels que des conduites de carburant, des conduites hydrauliques et des éléments structurels. Des matériaux tels que l'aluminium, les alliages de titane et les polymères spécialisés sont utilisés pour répondre aux exigences de performance rigoureuses des applications aérospatiales. La précision et la fiabilité du processus d'extrusion garantissent que les composants aérospatiaux sont à la fois légers et durables, contribuant ainsi à améliorer l'efficacité et la sécurité de la conception des aéronefs.

5. Industrie des biens de consommation :
Les moules d'extrusion sont largement utilisés dans l'industrie des biens de consommation pour fabriquer des produits de tous les jours tels que des jouets, des articles ménagers, des composants de meubles et des films d'emballage. Des matériaux tels que le PVC, le PET et le polystyrène (PS) sont généralement utilisés, offrant un équilibre entre durabilité, flexibilité et rentabilité. Le processus d'extrusion permet la production en masse de biens de consommation légers, durables et esthétiquement diversifiés, répondant ainsi à la forte demande de qualité et de design constants.
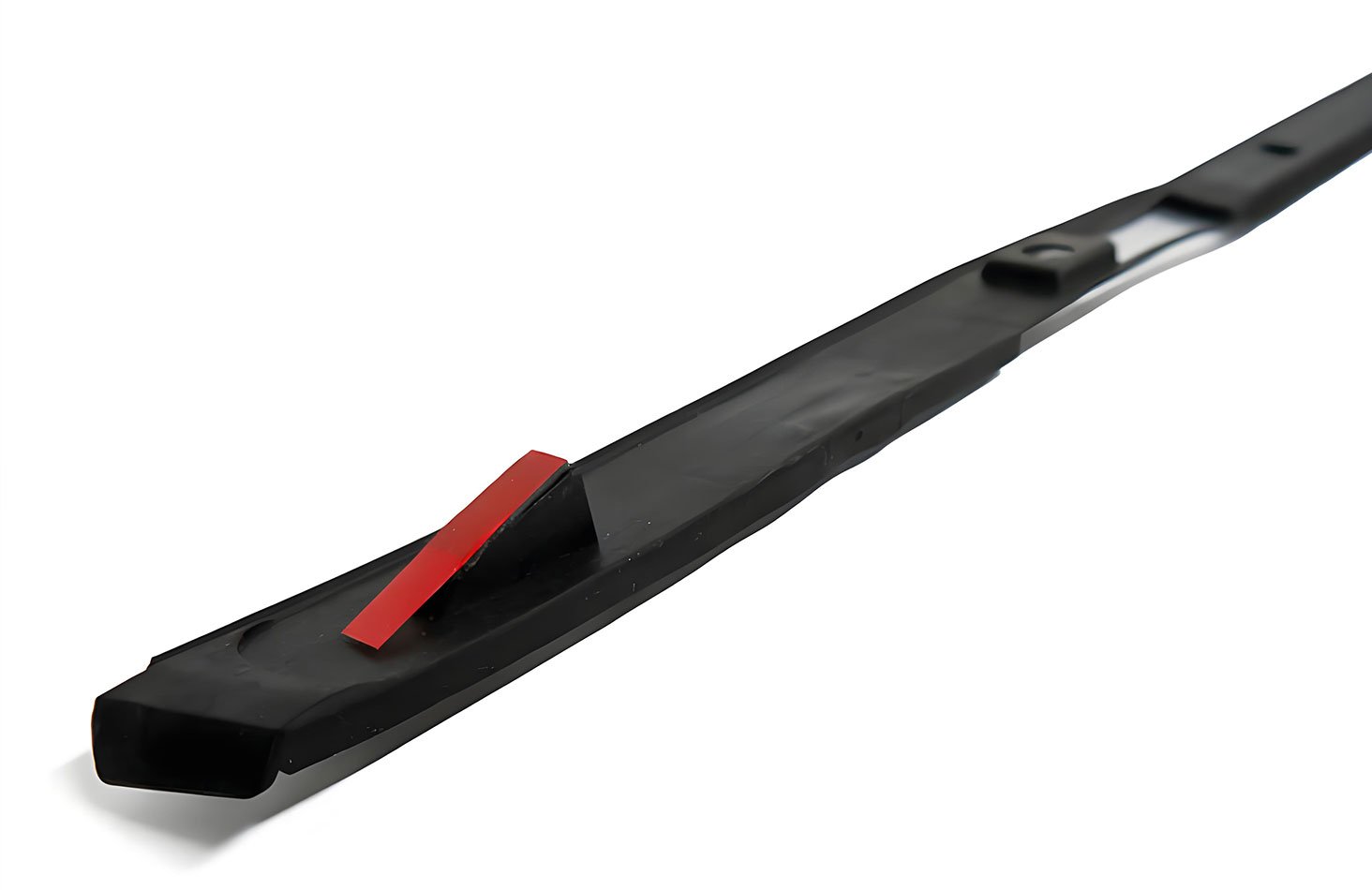
6. Industrie textile :
Dans le domaine du textile, les moules d'extrusion créent des fibres, des fils et des tissus synthétiques utilisés dans l'habillement, l'ameublement et les textiles industriels. Des matériaux tels que le polyéthylène téréphtalate (PET), le nylon et l'acrylique sont couramment utilisés en raison de leur résistance, de leur souplesse et de leur capacité à être filés en fils fins. Le processus d'extrusion assure une production continue de fibres et de tissus, qui peuvent être tissés ou tricotés pour créer des produits textiles polyvalents et durables.
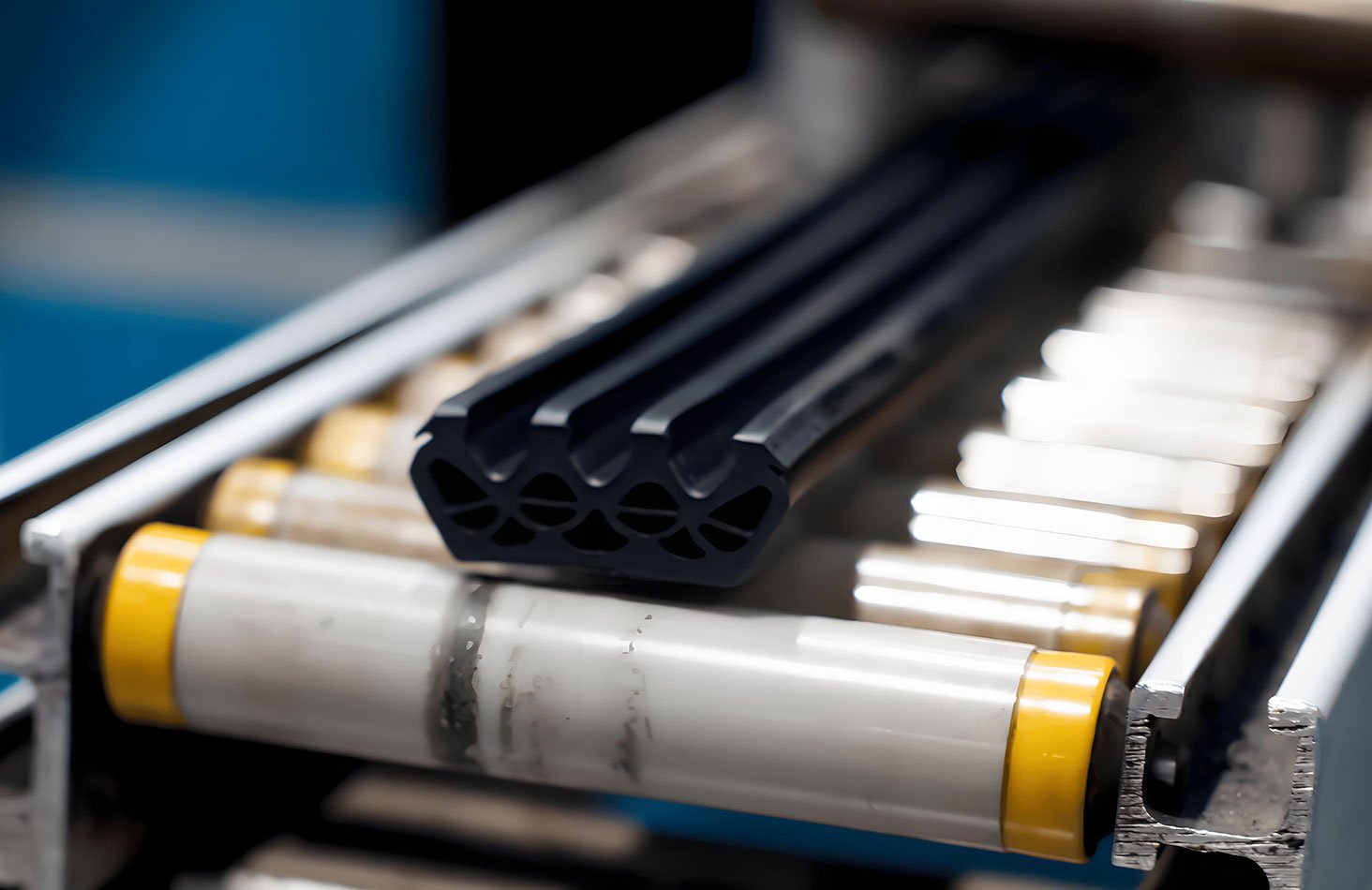
7. Industrie maritime :
Dans l'industrie maritime, les moules d'extrusion sont utilisés pour créer des composants tels que des accessoires de plomberie, des systèmes de ventilation et des pièces structurelles pour les bateaux et les navires. Des matériaux tels que l'aluminium résistant à la corrosion sont couramment utilisés pour résister aux conditions difficiles de l'environnement marin. Le processus d'extrusion offre une solution durable et légère pour créer des pièces qui doivent être exposées à l'eau et à d'autres conditions difficiles.
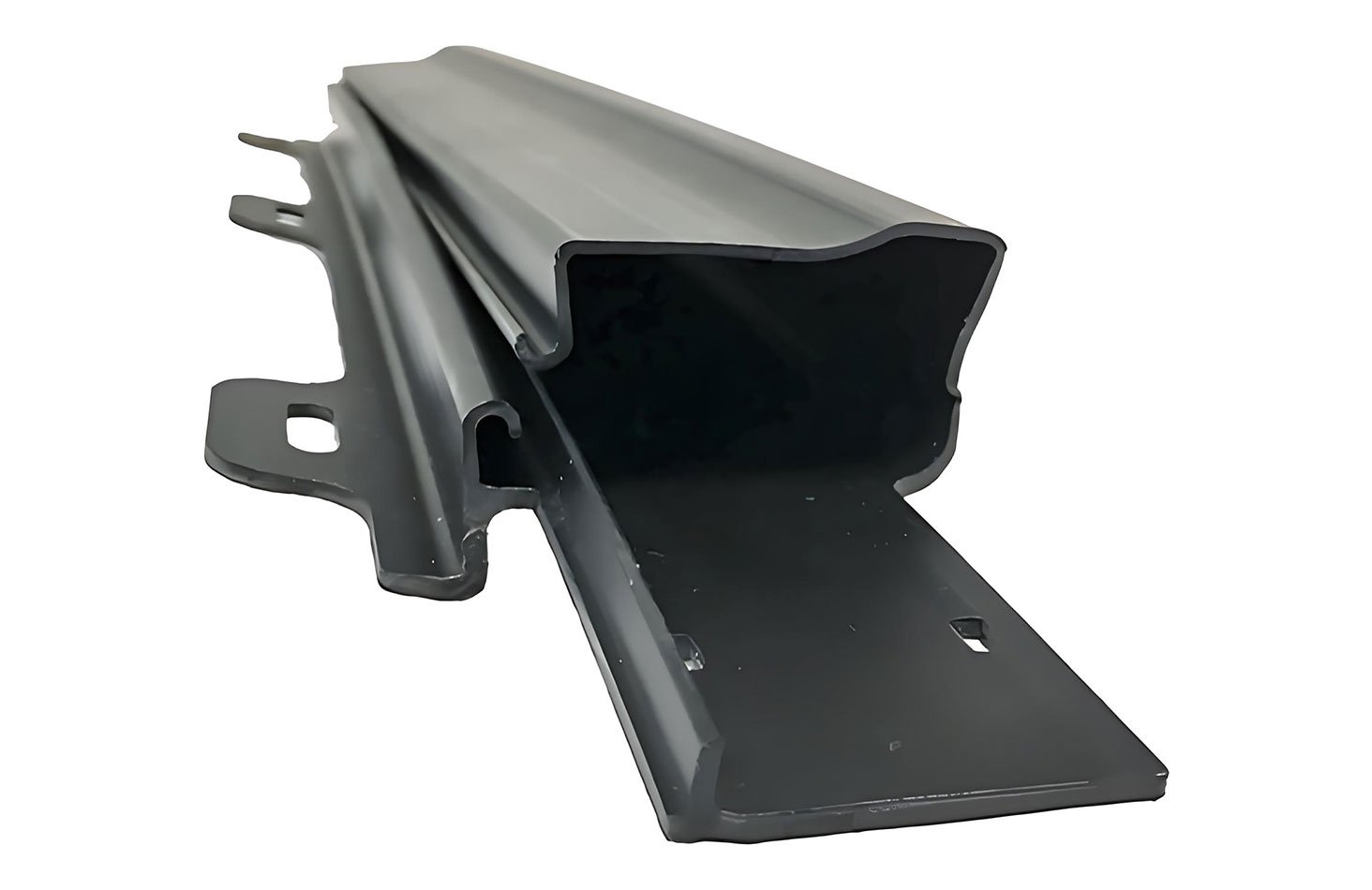
8. Industrie de la construction :
Dans le secteur de la construction, les moules d'extrusion sont utilisés pour produire des matériaux tels que des tuyaux, des cadres de fenêtres, des cadres de portes et des composants structurels, notamment des poutres et des canaux. Les matériaux couramment utilisés sont le PVC, l'aluminium et l'acier. Le processus d'extrusion permet de produire de longues sections continues avec des profils personnalisés, ce qui le rend idéal pour créer des éléments de construction qui requièrent à la fois résistance et durabilité, ainsi que pour minimiser les déchets de matériaux pendant la fabrication.
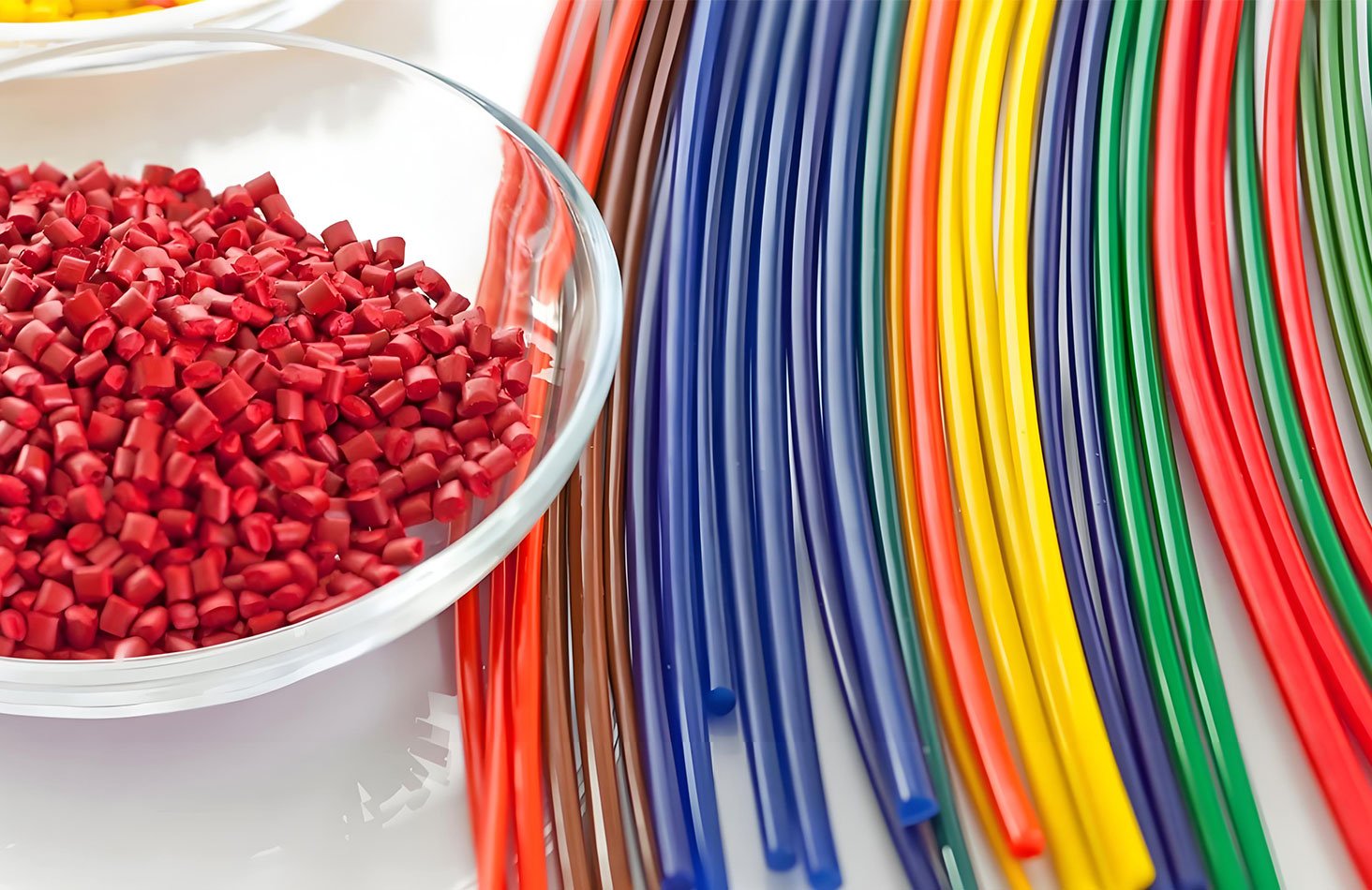
9. Industrie électrique et électronique :
Les moules d'extrusion jouent un rôle essentiel dans l'industrie électrique et électronique, où ils sont utilisés pour créer des composants tels que des dissipateurs thermiques, des isolants pour fils, des gaines de câbles et des boîtiers pour appareils électroniques. Des matériaux tels que les thermoplastiques et l'aluminium sont couramment utilisés pour garantir la durabilité, la flexibilité et l'isolation électrique. La précision de l'extrusion garantit que ces composants sont produits avec uniformité et répondent aux spécifications requises pour la performance et la sécurité des systèmes électriques.

10. Industrie pharmaceutique :
Dans l'industrie pharmaceutique, les moules d'extrusion sont utilisés pour fabriquer des produits tels que des boîtiers de comprimés, des capsules et des seringues. Les matériaux utilisés comprennent des thermoplastiques comme le PVC, qui offrent les propriétés nécessaires à la fabrication de produits de qualité médicale. Le processus d'extrusion est essentiel pour garantir que les composants pharmaceutiques sont produits avec une grande précision et qu'ils répondent à des normes d'hygiène et de sécurité strictes, afin que chaque produit soit fiable et sûr pour un usage médical.
FAQ POUR LE CLIENT
Démarrer avec Uplastech
Vous avez des questions ? Nous avons les réponses.
Nous sommes spécialisés dans les processus d'extrusion et la fabrication de moules de précision, offrant des solutions personnalisées pour répondre à vos besoins de fabrication.
Nous travaillons avec différents secteurs, notamment l'automobile, l'électronique et les biens de consommation, en nous concentrant sur les partenariats B2B.
Oui, nous adaptons nos solutions à vos besoins spécifiques.
Prendre contact
N'hésitez pas à nous envoyer un courriel ou à remplir le formulaire ci-dessous pour obtenir un devis.
Courriel : uplastech@gmail.com