Custom ASA Profiles Manufacturer
Professional custom ASA profiles manufacturer offering weather-resistant, UV-stable, and color-consistent solutions for outdoor and industrial applications. Fast delivery & OEM service.
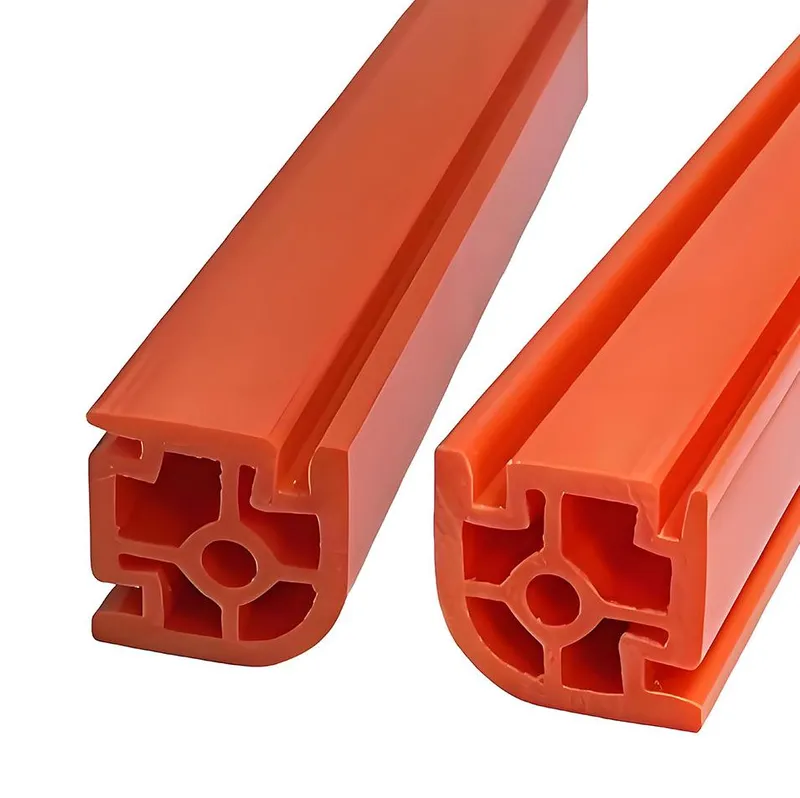
Guide to Custom ASA Extrusion Profiles Manufacturing
What are Custom ASA Extrusion Profiles?
Custom ASA Extrusion Profiles are specialized plastic components made from Acrylonitrile Styrene Acrylate (ASA), a durable thermoplastic valued for its excellent resistance to UV light, weather, and chemicals. These profiles are manufactured through an extrusion process, where molten ASA is forced through a custom-designed die to create continuous shapes with specific cross-sections, such as tubes, channels, or intricate geometries.
The extrusion process ensures high precision and consistency, allowing manufacturers to meet exact design requirements. Customization options can include co-extrusion, where ASA is combined with materials like ABS or PVC to improve properties such as flexibility or strength. This versatility makes custom ASA extrusion profiles a reliable and adaptable solution for projects requiring both durability and design flexibility.
1. Key Characteristics of ASA:
① UV Resistance: Retains color and properties despite prolonged sunlight exposure.
② Weather Resistance: Withstands rain, temperature extremes, and other environmental factors.
③ Impact Strength: Offers durability for demanding applications.
These qualities make custom ASA extrusion profiles ideal for a wide range of uses, particularly where components need to endure harsh conditions while maintaining both performance and aesthetic appeal.
2. Applications:
① Automotive: Exterior trims, such as bumper parts and mirror housings.
② Construction: Ventilation system components like grilles and ducts.
③ Marine: Equipment resistant to saltwater and UV damage.
④ Outdoor Furniture: Weather-resistant frames and fittings.
What is ASA and Why is It Used in Extrusion?
ASA is a copolymer composed of three key components:
- Acrylonitrile: Contributes chemical resistance and rigidity.
- Styrene: Enhances processability and provides a glossy finish.
- Acrylate: Improves weather resistance, especially against UV light.
This combination results in a material that balances strength, durability, and aesthetic appeal. Unlike ABS (Acrylonitrile Butadiene Styrene), which uses butadiene for impact resistance, ASA incorporates acrylate instead. This substitution makes ASA highly resistant to UV degradation, allowing it to retain its color and mechanical properties over time, even in harsh outdoor conditions.
Why is ASA Used in Extrusion?
Extrusion is a process where molten plastic is forced through a die to create continuous shapes like profiles, sheets, or tubes. ASA is particularly well-suited for this process due to the following reasons:
① Excellent Weather Resistance: ASA excels in resisting UV radiation, moisture, and temperature fluctuations. This makes it ideal for outdoor applications where materials face prolonged exposure to sunlight and weather. Unlike other plastics that may fade, crack, or weaken, ASA maintains its appearance and strength over time.
② Durability and Impact Strength: ASA provides high impact resistance, even in cold conditions, ensuring toughness and reliability. This is essential for products like automotive parts, outdoor furniture, and construction components that need to withstand physical stress.
③ Ease of Processing: ASA melts and flows smoothly during extrusion, enabling manufacturers to create complex profiles with precision. Its consistent processing characteristics ensure high-quality output and minimal production issues.
④ Aesthetic Flexibility: Available in various colors and finishes (glossy or matte), ASA also supports co-extrusion with materials like PVC or ABS. This allows for enhanced functionality or cost savings while maintaining an attractive appearance, making it suitable for both practical and decorative uses.
⑤ Chemical Resistance: ASA resists diluted acids, alkalis, and oils, making it a strong candidate for industrial and automotive applications where chemical exposure is a concern.
⑥ Long-Term Performance: Thanks to its resistance to degradation, ASA delivers long-lasting performance with minimal maintenance. This reduces lifecycle costs for products like signage, cladding, and exterior trims.
What are the Key Properties and Advantages of ASA for Extrusion?
ASA (Acrylonitrile Styrene Acrylate) is a thermoplastic material widely recognized for its suitability in extrusion, a process where material is shaped by being forced through a die. Below are its key properties and the advantages they provide for extrusion applications.
1. Key Properties of ASA for Extrusion:
① Superior Weather and UV Resistance: ASA excels in harsh outdoor conditions, resisting degradation and discoloration from sunlight and weather exposure. This is due to its acrylate component, which outperforms materials like ABS (Acrylonitrile Butadiene Styrene) that contain UV-sensitive butadiene.
② High Impact and Thermal Stability: It withstands physical shocks and maintains its shape across a range of temperatures, ensuring durability during both processing and end-use.
③ Chemical Resistance and Ease of Processing: ASA resists damage from many chemicals and flows smoothly during extrusion, enabling the production of precise and complex shapes.
2. Advantages of ASA in Extrusion:
① Extended Product Life: Its resistance to environmental factors reduces the need for maintenance or replacement, making it cost-effective over time, especially for outdoor applications.
② Consistent Aesthetics: ASA retains its color and finish under prolonged exposure, making it ideal for visible components such as automotive trims, signage, or outdoor furniture.
③ Versatility Across Industries: From construction profiles to consumer goods, ASA’s balanced properties meet diverse manufacturing needs.
④ Manufacturing Efficiency: Its excellent melt flow and compatibility with co-extrusion (layering with other materials) enhance production flexibility and allow for innovative, high-performance designs.
3. Why ASA Stands Out?
ASA is often preferred over ABS for extrusion in outdoor settings due to its superior UV resistance, offering a combination of resilience, processability, and visual appeal that few materials match. This makes it a top choice for extruded products requiring durability and design versatility.
Where are ASA Extrusion Profiles Commonly Used?
ASA (Acrylonitrile Styrene Acrylate) extrusion profiles are widely used in applications where durability, weather resistance, and UV stability are essential. Below are the key areas where these profiles are commonly applied:
① Automotive Industry: ASA profiles are frequently used for exterior trims, grilles, and other components. These parts need to endure prolonged exposure to sunlight, rain, and temperature changes while maintaining both their functionality and appearance.
② Construction Sector: In construction, ASA profiles are ideal for window frames, door frames, and siding. Their resistance to fading, cracking, and environmental wear makes them a reliable choice for these structural elements.
③ Signage and Advertising: Outdoor signs and displays often utilize ASA profiles due to their ability to withstand harsh weather conditions without losing structural integrity or aesthetic appeal.
④ Outdoor Furniture and Equipment: ASA is also employed in items like garden furniture and playground equipment, where it resists degradation from constant exposure to the elements.
Which Industries Benefit from Custom ASA Profiles?
Custom ASA (Acrylonitrile Styrene Acrylate) profiles are widely used across multiple industries due to their exceptional durability, weather resistance, and UV stability. These properties make them an ideal material for applications requiring long-lasting performance under harsh environmental conditions. Below is a comprehensive list of industries that benefit from custom ASA profiles, along with their specific applications and advantages:
1. Automotive Industry:
Applications: Exterior trims, grilles, mirror housings, and bumper components.
Benefits: ASA profiles resist UV exposure, temperature changes, and weathering, ensuring automotive parts maintain their appearance and functionality over time. Their impact resistance also enhances durability.
2. Construction Sector:
Applications: Window frames, door frames, siding, and roofing elements.
Benefits: ASA's resistance to fading, cracking, and environmental wear makes it a low-maintenance, durable choice for construction, reducing long-term costs and upkeep.
3. Signage and Advertising:
Applications: Outdoor signs, billboards, and display panels.
Benefits: ASA profiles withstand prolonged sunlight and weather exposure without losing color or structural integrity, keeping signage vibrant and effective.
4. Outdoor Furniture and Equipment:
Applications: Garden furniture, playground equipment, and outdoor fixtures.
Benefits: ASA resists degradation from rain, UV rays, and temperature fluctuations, making it perfect for outdoor products that face constant exposure.
5. Telecommunications:
Applications: Housings for antennas, satellite dishes, and other outdoor equipment.
Benefits: ASA provides reliable protection against weather and UV damage, ensuring the longevity of telecommunications infrastructure.
6. Marine Industry:
Applications: Boat components, dock edging, and marine fixtures.
Benefits: ASA's resistance to saltwater corrosion and UV damage makes it a durable option for marine environments.
7. Electrical and Consumer Products:
Applications: Appliance casings, electrical enclosures, and outdoor lighting.
Benefits: ASA offers durability, chemical resistance, and aesthetic flexibility, balancing functionality with design in consumer goods.
8. Aerospace:
Applications: Aircraft interior and exterior components, such as trim panels and covers.
Benefits: ASA's lightweight yet durable nature, combined with environmental resistance, meets the stringent demands of aerospace applications.
9. Medical Devices:
Applications: Casings for medical equipment, diagnostic devices, and mobility aids.
Benefits: ASA's chemical resistance and durability ensure medical devices remain safe and operational, even with exposure to cleaning agents.
10. Industrial Applications:
Applications: Protective covers, machine guards, and industrial enclosures.
Benefits: ASA's resistance to chemicals, impact, and wear suits it for demanding industrial environments.
How to Design a Custom ASA Extrusion Profile?
Designing a custom ASA (Acrylonitrile Styrene Acrylate) extrusion profile involves a systematic process to ensure the final product meets your specific functional, aesthetic, and environmental needs. ASA is an excellent material choice, particularly for outdoor applications, due to its UV resistance, durability, and color retention. Below is a step-by-step guide to help you design a custom ASA extrusion profile that is tailored to your requirements.
1. Define the Purpose and Requirements:
The first step is to clearly outline what the profile is intended to do and the conditions it will face. This ensures the design is optimized for its specific application.
① Functionality: Identify the profile's role. Will it provide structural support, serve as decorative trim, act as a protective casing, or fulfill another purpose?
② Environmental Conditions: Consider factors like exposure to UV light, weather (rain, temperature extremes), chemicals, or mechanical stress. ASA excels in outdoor settings due to its weather and UV resistance.
③ Aesthetic Needs: Decide on the color, surface finish (glossy, matte, or textured), and any branding elements, such as logos or specific color matching.
④ Dimensions and Tolerances: Specify the size, shape, and precision required. Think about how the profile will integrate with other components or assemblies.
2. Select the Right Material:
While ASA is a strong starting point, confirm it suits your needs and explore any enhancements.
① ASA Properties: Verify that ASA's UV resistance, impact strength, and chemical resistance meet your project's demands. It's ideal for applications requiring durability and color stability outdoors.
② Co-Extrusion Options: If you need additional properties—like flexibility, cost savings, or enhanced strength—consider co-extruding ASA with materials such as ABS, PVC, or TPU. This creates a multi-layered profile with customized characteristics.
3. Design the Profile:
Next, create a detailed design of the profile's cross-section, keeping manufacturing feasibility in mind.
① Cross-Sectional Design: Use CAD (Computer-Aided Design) software to develop a precise 2D or 3D model of the profile's cross-section. Focus on achieving the desired shape while aligning with extrusion capabilities.
② Complexity vs. Manufacturability: Keep the design as simple as possible to reduce production costs and challenges. Complex shapes may increase tooling expenses or lead to manufacturing difficulties.
③ Tolerances: Define tight tolerances for critical dimensions to ensure the profile fits its intended application perfectly. Consult with manufacturers to understand realistic tolerance limits for ASA extrusion.
4. Prototype and Test:
Prototyping allows you to test and refine the design before committing to full production.
① Prototype Production: Collaborate with a manufacturer to produce a small batch of prototypes. This helps identify any issues early in the process.
② Testing: Assess the prototypes for:
- Fit and function within the intended assembly.
- Performance under expected conditions (e.g., UV exposure, temperature changes).
- Aesthetic quality, such as color consistency and surface finish.
③ Refinement: Adjust the design based on test results. This could mean tweaking dimensions, altering the cross-section, or modifying material choices.
5. Collaborate with Manufacturers:
Working closely with extrusion experts ensures your design is practical and cost-effective.
① Expert Consultation: Engage manufacturers early to confirm your design is feasible and optimized for production. Their input can save time and money.
② Tooling and Die Design: The manufacturer will create a custom die based on your design. Ensure it meets your specifications and can produce consistent, high-quality profiles.
③ Production Planning: Discuss:
- Production volumes and lead times.
- Quality control processes (e.g., in-process checks, post-production testing).
- Cost factors, including tooling expenses and potential savings for large orders.
6. Finalize and Approve the Design:
Before launching full-scale production, ensure everything is in place.
① Review and Approve: Conduct a final review of the design, prototypes, and production plan. Confirm that all functional, aesthetic, and performance requirements are met.
② Documentation: Keep detailed records of the design process, including CAD files, test results, and production specs. This is useful for future reference or iterations.
Custom ASA Profiles Manufacturer
Leading manufacturer of custom ASA profiles with precision extrusion, excellent durability, and full customization. Ideal for automotive, construction & outdoor products.
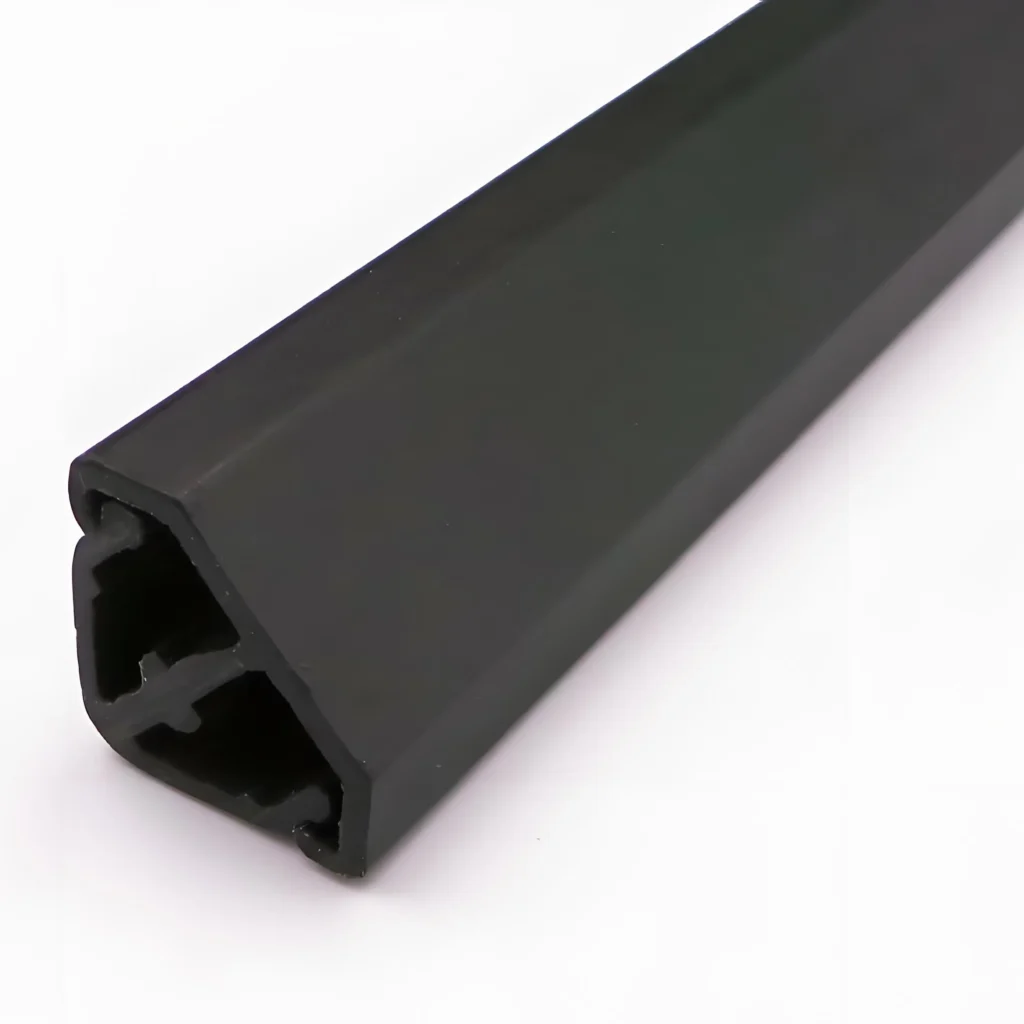
Guide to Custom ASA Extrusion Profiles Manufacturing
- What Customization Options are Available for ASA Profiles?
- How is the Extrusion Process for ASA Profiles Performed?
- Technical Specifications and Tolerances for ASA Profiles
- How is Quality Control Ensured in ASA Extrusion?
- How Does ASA Compare to Other Extrusion Materials?
- How to Choose the Right Manufacturer for Custom ASA Profiles?
What Customization Options are Available for ASA Profiles?
ASA (Acrylonitrile Styrene Acrylate) profiles, commonly used in extrusion processes for their durability and weather resistance, offer a wide range of customization options to meet specific functional and aesthetic needs. Below is a detailed breakdown of the available customization options:
1. Shape and Design:
The cross-sectional shape of ASA profiles can be fully customized by designing the extrusion mold. This allows for:
- Simple shapes like tubes, rectangles, or circles.
- Complex profiles such as channels, trims, seals, or gaskets tailored to specific applications.
2. Dimensions and Tolerances:
ASA profiles can be tailored in terms of size and precision:
- Dimensions: Width, height, wall thickness, and length can be specified based on the intended use.
- Tolerances: Tighter tolerances can be applied for applications requiring high precision, ensuring the profiles meet exact specifications.
3. Color and Appearance:
Color customization is a key feature of ASA profiles:
- A wide range of colors is available, including custom matching to standards like Pantone or RAL codes.
- This is ideal for branding, aesthetic consistency, or functional purposes (e.g., visibility).
4. Surface Finish:
The surface texture of ASA profiles can be adjusted to suit different needs:
- Options include smooth, matte, glossy, or textured finishes.
- Textures can enhance functionality, such as improving grip or diffusing light.
5. Material Properties and Additives:
The properties of ASA can be enhanced through additives or grade selection:
- Additives: UV stabilizers (beyond ASA’s inherent weatherability), flame retardants, or impact modifiers can be incorporated.
- ASA Grades: Different grades with varying characteristics, such as higher impact resistance or better flow, can be selected.
6. Co-Extrusion and Multi-Material Options:
Co-extrusion allows ASA to be combined with other materials in a single profile:
- Examples include an ASA outer layer for weather resistance paired with a cost-effective or rigid core (e.g., PVC or ABS).
- Profiles can also feature flexible sections (e.g., with TPE) for soft-touch surfaces or improved functionality.
7. Secondary Processing:
Post-extrusion processes can further customize ASA profiles:
- Cutting: Profiles can be cut to specific lengths.
- Drilling or Punching: Holes or notches can be added for mounting or assembly.
- Attachments: Features like adhesive tapes or magnetic strips may be applied, depending on the manufacturer.
8. Printing and Surface Decoration:
ASA profiles can be decorated for branding or identification:
- Printing logos, text, or patterns directly onto the surface.
- Painting or coating for additional protection or visual appeal.
How is the Extrusion Process for ASA Profiles Performed?
The extrusion process for ASA (Acrylonitrile Styrene Acrylate) profiles is a precise manufacturing technique that transforms ASA resin into custom-shaped profiles with consistent cross-sections. ASA is a thermoplastic valued for its durability, UV resistance, and weatherability, making it ideal for outdoor applications. Below is a detailed, step-by-step explanation of how this process is performed.
Step 1: Material Preparation:
① Drying the Resin: ASA resin, typically supplied as pellets, is mildly hygroscopic and can absorb moisture from the air. Before extrusion, the pellets are dried in a dehumidifying dryer to eliminate moisture, which could otherwise cause bubbles, surface defects, or weak spots in the final profile.
② Additive Mixing (Optional): Depending on the application, additives like UV stabilizers, flame retardants, or colorants may be blended with the ASA pellets to enhance specific properties or achieve desired colors.
Step 2: Feeding the Extruder:
① Hopper Loading: The dried ASA pellets are loaded into the hopper of an extruder, a machine designed to melt and shape the plastic.
② Gravity Feed: The pellets flow from the hopper into the extruder’s barrel via gravity, initiating the processing sequence.
Step 3: Melting and Mixing:
① Heating Zones: Inside the extruder barrel, the ASA pellets pass through multiple temperature-controlled zones, typically heated to 180°C–220°C (356°F–428°F), depending on the ASA grade. This gradual heating melts the pellets into a molten state.
② Screw Rotation: A rotating screw within the barrel pushes the material forward while thoroughly mixing it, ensuring a uniform consistency and even distribution of any additives or colorants.
Step 4: Extrusion Through the Die:
① Die Shaping: The molten ASA is forced through a custom-designed die at the end of the extruder. The die defines the profile’s cross-sectional shape, which can vary from simple tubes to complex geometries like channels or trims.
② Pressure Control: The extruder applies precise pressure to ensure the molten ASA flows evenly through the die, avoiding defects or inconsistencies in the profile.
Step 5: Cooling and Solidification:
① Cooling System: Upon exiting the die, the profile is still soft and must be cooled to solidify its shape. Common cooling methods include:
- Water Baths: The profile passes through water-filled tanks for rapid cooling.
- Air Cooling: Air systems may be used for gradual cooling, depending on the profile’s requirements.
② Calibration Tools: Calibration devices or vacuum sizing equipment may be employed to maintain precise dimensions as the profile cools.
Step 6: Cutting and Finishing:
① Haul-Off Unit: A haul-off machine pulls the cooled profile at a controlled speed, maintaining consistent tension to ensure uniform thickness and shape.
② Cutting to Length: The continuous profile is cut into specified lengths using saws or automated cutters.
③ Secondary Operations (Optional): Additional processes, such as drilling, punching, notching, or surface treatments (e.g., printing or coating), may be applied based on the profile’s intended use.
Step 7: Quality Control:
① Dimensional Checks: The profiles are measured to ensure they meet specified tolerances for size and shape.
② Surface Inspection: Visual and tactile checks identify defects like bubbles, streaks, or roughness.
③ Performance Testing: Samples may be tested for properties like impact resistance, UV stability, or color consistency to confirm they meet application standards.
Additional Notes:
① Co-Extrusion (Optional): ASA can be co-extruded with materials like PVC or ABS to create profiles with combined properties, such as a rigid ASA core with a flexible outer layer.
② Tooling Precision: The die’s design is critical for shaping the profile accurately and must be tailored to the specific application.
What are the Technical Specifications and Tolerances for ASA Profiles?
ASA (Acrylonitrile-Styrene-Acrylate) profiles are thermoplastic products made by extrusion. They are widely used in automotive decoration, building components and outdoor facilities due to their excellent weather resistance, UV resistance and durability. The following is a summary of its technical specifications and tolerances.
1. Technical Specifications:
① Dimensions:
ASA profiles are highly customizable to suit specific applications, but there are common dimensional ranges:
- Cross-Sectional Dimensions:
a. Profiles can range from simple shapes (e.g., tubes, rectangles) to complex designs (e.g., multi-chambered structures).
b. Width and Height: Typically between 5 mm and 200 mm, depending on the profile’s complexity and intended use.
c. Wall Thickness: Generally rangesrom 1 mm to 5 mm, with thicker walls used for structural purposes.
- Length: Extruded continuously and cut to length, often up to 6 meters for practical handling and shipping.
- Custom Features: Profiles may include holes, slots, or other features added during or after extrusion, tailored to the application.
② Mechanical Properties:
ASA’s mechanical properties make it a robust and versatile material:
- Tensile Strength: Approximately 40–50 MPa, providing good structural integrity for load-bearing applications.
- Flexural Modulus: Between 2,000 and 2,500 MPa, indicating sufficient stiffness for various uses.
- Impact Resistance: Notched Izod impact values of 10–15 kJ/m², maintaining strength even at low temperatures.
- Hardness: Shore D hardness of 80–85, offering resistance to scratches and surface damage.
- Thermal Stability: Suitable for continuous use up to 80°C, with short-term exposure up to 100°C without significant degradation.
2. Tolerances:
Tolerances define the allowable variation in dimensions and characteristics, ensuring ASA profiles fit and function correctly:
① Dimensional Tolerances:
- Width and Height: ±0.5 mm for profiles up to 50 mm; up to ±1.0 mm for larger profiles.
- Wall Thickness: ±0.2 mm for thin walls (1–2 mm), increasing to ±0.5 mm for thicker walls.
② Straightness: Profiles should deviate no more than 1 mm per meter to ensure proper alignment and fit.
③ Surface Finish: A smooth finish is typical, with surface roughness (Ra) less than 1.6 µm for aesthetic or functional surfaces.
④ Color Consistency: For colored profiles, color variation is controlled within a Delta E value of less than 1.0, ensuring uniformity.
3. Relevant Industry Standards:
ASA profiles may need to meet specific standards depending on their use:
① ISO 9001: Ensures consistent manufacturing quality.
② ASTM D4673: Defines material properties for ASA, including mechanical and physical characteristics.
③ UL 94: Applies to flame-retardant grades for fire safety compliance.
④ RoHS and REACH: Ensures compliance with environmental regulations regarding restricted substances.
4. How Specifications and Tolerances Are Ensured?
Manufacturers employ various methods to verify ASA profiles meet these standards:
① In-Line Monitoring: Real-time measurement of dimensions and surface quality during extrusion.
② Mechanical Testing: Samples are tested for tensile strength, impact resistance, and other properties.
③ Visual Inspection: Checks for surface defects, color consistency, and finish quality.
④ Dimensional Verification: Tools like calipers or laser gauges ensure tolerances are maintained.
How is Quality Control Ensured in ASA Extrusion?
Quality control in ASA (Acrylonitrile Styrene Acrylate) extrusion is a systematic process designed to ensure that the final extruded profiles meet strict standards for dimensions, material properties, and performance. Given ASA’s use in demanding applications such as automotive parts, construction materials, and outdoor products, maintaining high quality is essential.
1. Material Inspection:
The process begins with a thorough inspection of the raw materials, particularly the ASA resin. Key steps include:
① Purity Check: The resin is examined for contaminants or impurities that could compromise the extrusion process.
② Moisture Content: Since ASA can absorb moisture, it is tested and dried to a specified level (e.g., <0.1%) to prevent defects like bubbles or weak spots in the final product.
③ Additive Verification: If additives like colorants or UV stabilizers are used, their consistency and proportions are confirmed to ensure uniformity.
2. Extrusion Process Monitoring:
During extrusion, critical parameters are closely monitored to maintain consistency and prevent defects:
① Temperature: The barrel and die temperatures (typically 180°C–220°C) are controlled to ensure proper melting and flow of the ASA material.
② Pressure: Extrusion pressure is regulated to achieve a steady material flow through the die.
③ Screw Speed: The extruder screw speed is adjusted to control the output rate and ensure a uniform profile. Real-time adjustments, often supported by automated systems, help maintain process stability.
3. Dimensional Checks:
After extrusion, the profiles are inspected for dimensional accuracy:
① In-Line Monitoring: Tools like laser gauges or ultrasonic sensors measure dimensions during production to ensure they align with specifications.
② Post-Extrusion Inspection: Key measurements include:
- Cross-Sectional Dimensions: Width, height, and wall thickness are checked against tolerances (e.g., ±0.5 mm).
- Length: Cut lengths are verified for accuracy.
- Straightness: Profiles are assessed for deviations (e.g., ≤1 mm per meter).
4. Surface Quality Inspection:
The surface of the extruded profiles is carefully examined for both aesthetic and functional quality:
① Defect Detection: Operators or automated systems check for scratches, bubbles, streaks, or uneven textures.
② Finish Consistency: The surface is verified to match the required finish, such as smooth, matte, or textured.
5. Mechanical Testing:
Samples from each batch are tested to ensure the profiles meet performance standards:
① Tensile Strength: Measured to confirm the profile can withstand pulling forces (typically 40–50 MPa for ASA).
② Impact Resistance: Tested to verify toughness, critical for outdoor or high-stress applications.
③ Flexural Strength: Assessed to ensure resistance to bending under load. Additional tests, such as heat resistance, may be conducted depending on the application.
6. Color and Appearance Checks:
For applications where aesthetics matter, the profiles are evaluated for:
① Color Consistency: Tools like spectrophotometers ensure color variations stay within acceptable limits (e.g., Delta E <1.0).
② Gloss Level: The surface gloss is measured and compared to specifications if required.
7. Packaging and Handling:
To prevent damage after production:
① Protective Packaging: Profiles are wrapped in film or supported with spacers to avoid scratches or bending during transport.
② Labeling: Packages are marked with production details for traceability.
8. Documentation and Traceability:
Quality control activities are thoroughly documented:
① Records: Include material lot numbers, process parameters, and inspection results.
② Traceability: Enables manufacturers to track each batch’s production history, aiding in troubleshooting and quality assurance.
9. Continuous Improvement:
Feedback from quality control is analyzed to:
① Identify trends or recurring issues.
② Optimize the extrusion process, update procedures, or enhance training, ensuring ongoing quality enhancements.
How Does ASA Compare to Other Extrusion Materials?
ASA (Acrylonitrile Styrene Acrylate) is a popular material in extrusion processes, valued for its durability and resistance to environmental factors. To understand how it compares to other common extrusion materials like PVC (Polyvinyl Chloride), ABS (Acrylonitrile Butadiene Styrene), and PMMA (Polymethyl Methacrylate), let’s examine their key properties, applications, and trade-offs.
1. Key Properties Comparison:
Here’s a detailed breakdown of how ASA stacks up against PVC, ABS, and PMMA across several important characteristics:
Property | ASA | PVC | ABS | PMMA |
---|---|---|---|---|
UV Resistance | Excellent | Moderate | Poor | Good |
Weather Resistance | Excellent | Good | Moderate | Good |
Impact Strength | High | Moderate | High | Low |
Cost | Moderate to High | Low | Moderate | High |
Processing Ease | Good | Excellent | Excellent | Good |
Color Retention | Excellent | Good | Poor | Good |
Chemical Resistance | Good | Excellent | Moderate | Moderate |
① UV and Weather Resistance: ASA excels in resisting sunlight and harsh weather, outperforming ABS (which degrades under UV exposure) and PVC (which has moderate resistance). PMMA also handles weather well but doesn’t match ASA’s overall durability.
② Impact Strength: ASA and ABS both offer high impact resistance, making them tougher than the more brittle PVC and PMMA.
③ Cost: PVC is the most budget-friendly option, while ASA and PMMA are pricier due to their specialized properties.
④ Processing Ease: PVC and ABS are easier to extrude than ASA, which requires precise temperature control (typically 180°C–220°C) and pre-drying to prevent defects.
2. Unique Strengths of ASA:
ASA stands out for its:
① UV Resistance: It maintains strength and appearance under prolonged sunlight exposure.
② Weatherability: It resists cracking, fading, and brittleness in extreme conditions.
③ Color Retention: It keeps vibrant colors over time, unlike ABS, which fades quickly outdoors.
3. Application Suitability:
ASA’s properties align it with specific uses, often outperforming other materials in outdoor settings:
① Automotive: Exterior parts like trims and grilles benefit from ASA’s UV resistance and color stability.
② Construction: Window frames, siding, and roofing leverage its weatherability and durability.
③ Outdoor Signage and Furniture: ASA ensures long-lasting appearance and strength.
④ In Comparison:
- PVC: Commonly used for indoor applications like pipes and fittings due to its low cost and chemical resistance.
- ABS: Suited for indoor products like appliance housings or toys, where UV exposure isn’t a concern.
- PMMA: Ideal for transparent applications like light covers or displays, thanks to its optical clarity.
4. Limitations of ASA:
① Higher Cost: It’s more expensive than PVC and ABS, which can limit its use in budget-driven projects.
② Processing Challenges: It demands careful handling during extrusion, unlike the more forgiving PVC and ABS.
③ Not for Transparency: Unlike PMMA, ASA lacks optical clarity, making it unsuitable for see-through applications.
5. Why Choose ASA?
ASA is a top choice for extrusion when outdoor performance is critical. Its superior UV resistance, weatherability, and color retention make it ideal for products exposed to sunlight and weather, often justifying its higher cost and processing needs. For indoor or cost-sensitive applications, PVC or ABS might be better options, while PMMA shines in scenarios requiring transparency. Ultimately, ASA’s balance of durability and aesthetic stability sets it apart where longevity and appearance matter most.
How to Choose the Right Manufacturer for Custom ASA Profiles?
ASA is a top choice for extrusion when outdoor performance is critical. Its superior UV resistance, weatherability, and color retention make it ideal for products exposed to sunlight and weather, often justifying its higher cost and processing needs. For indoor or cost-sensitive applications, PVC or ABS might be better options, while PMMA shines in scenarios requiring transparency. Ultimately, ASA’s balance of durability and aesthetic stability sets it apart where longevity and appearance matter most.
1. Evaluate Expertise and Experience:
① Why it matters: Producing ASA profiles requires advanced extrusion techniques and a thorough understanding of the material’s properties. A manufacturer with extensive experience will be better equipped to handle ASA’s unique challenges and deliver reliable results.
② What to look for: Investigate how long the manufacturer has been in the extrusion industry and whether they have specific experience with ASA. Request examples of past projects or case studies to confirm their expertise.
2. Assess Customization Capabilities:
① Why it matters: Custom ASA profiles often require specific shapes, sizes, or performance characteristics to meet project needs. A manufacturer with strong customization capabilities can adapt to your unique requirements.
② What to look for: Ask about their ability to design custom dies, perform co-extrusion with materials like PVC or ABS, and offer additional services such as cutting, drilling, or finishing.
3. Check Quality Control Processes:
① Why it matters: ASA profiles must meet precise standards for dimensions, durability, and performance, especially in demanding environments. Robust quality control ensures consistency and reliability.
② What to look for: Look for evidence of in-line monitoring, mechanical testing, and adherence to recognized standards like ISO 9001.
4. Review Material Sourcing and Handling:
① Why it matters: The quality of ASA resin and proper handling (e.g., pre-drying to avoid defects) directly impact the final product’s performance.
② What to look for: Confirm that the manufacturer uses high-grade ASA resin and follows best practices for material preparation and storage.
5. Consider Production Capacity and Lead Times:
① Why it matters: Meeting deadlines is essential, particularly for large-scale or time-sensitive projects. The manufacturer’s capacity and efficiency will determine their ability to deliver on time.
② What to look for: Assess their production capabilities and ask about typical lead times for custom orders.
6. Look for Industry Certifications and Compliance:
① Why it matters: Certifications demonstrate a manufacturer’s commitment to quality, safety, and environmental responsibility, which are especially important for regulated industries.
② What to look for: Check for certifications like ISO 9001, as well as compliance with standards such as RoHS or REACH.
7. Evaluate Customer Support and Collaboration:
① Why it matters: A manufacturer that provides support during design, prototyping, and production can help refine your project and address potential issues early.
② What to look for: Ensure they offer design assistance, prototyping services, and responsive communication throughout the process.
Why Choose Uplastech?
When it comes to custom ASA profiles, Uplastech stands out as a premier choice. With over 20 years of expertise in the extrusion industry, we bring a wealth of experience and professionalism to every project. Our state-of-the-art facilities, rigorous quality control processes, and dedication to customer collaboration ensure that we deliver high-quality, tailored ASA profiles that meet the toughest standards. Whether your application is in automotive, construction, or beyond, Uplastech is your trusted partner for durable, precision-engineered solutions.
FAQs FÜR KUNDEN
Erste Schritte mit Uplastech
Sie haben Fragen? Wir haben Antworten.
Wir sind auf Extrusion, Vakuumformung, Blasformen und Präzisionsformenbau spezialisiert und bieten maßgeschneiderte Lösungen für Ihre vielfältigen Fertigungsanforderungen.
Wir arbeiten mit verschiedenen Branchen zusammen, darunter die Automobil-, Elektronik-, Konsumgüter- und Verpackungsindustrie, wobei wir uns auf B2B-Partnerschaften konzentrieren und Lösungen in den Bereichen Extrusion, Thermoformung, Blasformen und Präzisionsformenbau anbieten.
Ja, wir schneidern unsere Lösungen auf Ihre individuellen Anforderungen zu.
Kontakt aufnehmen
Senden Sie uns eine E-Mail oder füllen Sie das unten stehende Formular aus, um ein Angebot zu erhalten.
E-Mail: uplastech@gmail.com