Twin Sheet Forming Innovations | Uplastech
Discover Uplastech advanced twin sheet forming technology for efficient, high-quality plastic fabrication. Explore our solutions today!
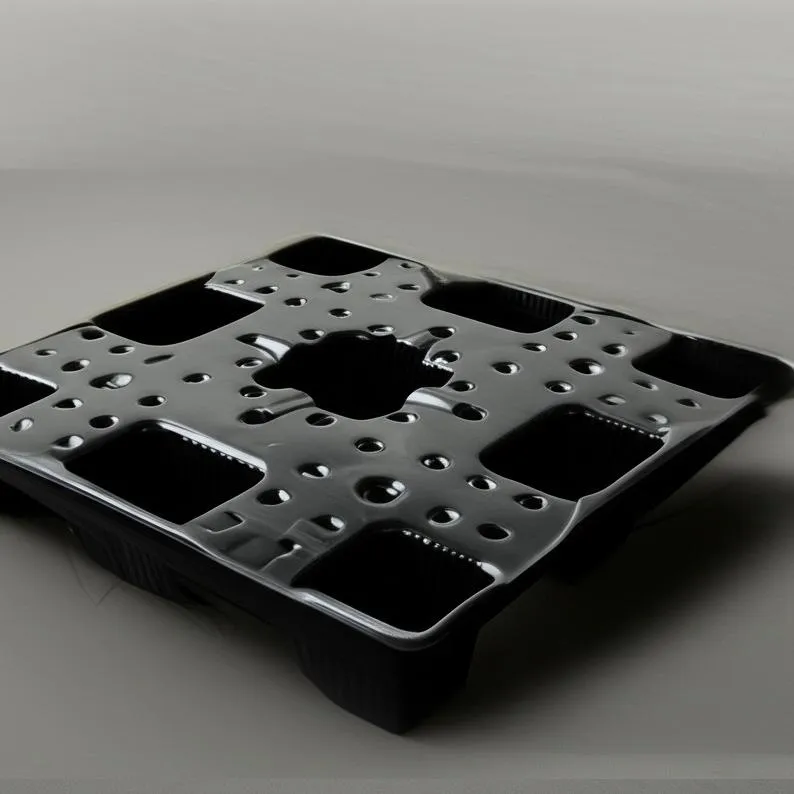
Resources for The Complete Guide to Twin Sheet Forming
What is Twin Sheet Forming? A Comprehensive Definition
Twin Sheet Forming, also known as Twin Sheet Thermoforming, is an advanced plastic manufacturing process that simultaneously heats and forms two separate plastic sheets. These sheets are then precisely brought together and fused at designated points, typically around their perimeters and at internal contact locations, while still in their malleable, heated state. This fusion creates a single, integrated component with a hollow or multi-wall structure.
Full Technical Name: Twin Sheet ThermoformingCommon Aliases: Double Sheet Forming, Twin Wall Forming.
1. Core Principles:
① Dual Sheet Heating: Two distinct thermoplastic sheets are independently heated to their optimal forming temperature.
② Simultaneous or Sequential Forming: Each heated sheet is drawn into or over a mold (or mold halves) using vacuum, pressure, or a combination of both. This can happen simultaneously or in rapid succession.
③ Precise Alignment and Compression: The two formed sheets, while still hot and held in their respective molds, are brought together under significant pressure. This pressure, combined with the residual heat, causes the contact areas of the sheets to weld or fuse, creating a strong, hermetic bond.
④ Hollow Structure Creation: The space between the two sheets, where they are not welded, forms the hollow interior of the part.
2. Basic Concepts:
① Thermoplastics: The process is exclusively used for thermoplastic materials, which can be repeatedly softened by heating and hardened by cooling.
② Tooling: Requires two distinct molds (male or female, or a combination) that define the shape of each half of the final part. The precision of these tools is critical for proper alignment and sealing.
③ Weld Seam: The area where the two sheets are fused is known as the weld seam or pinch-off. The integrity of this seam is paramount to the part’s structural performance.
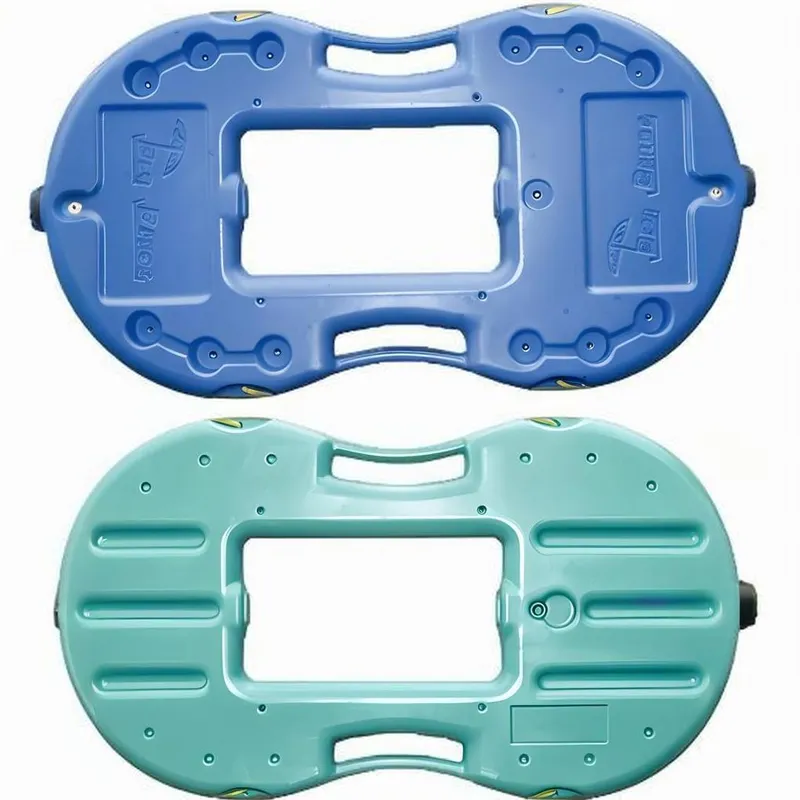
Core Principles and Basic Concepts of Twin Sheet Forming
The ingenuity of twin sheet forming lies in its ability to produce complex, hollow parts with high structural integrity and potentially different characteristics on each side. Several core principles govern its success:
1. Material Compatibility and Selection:
① Both sheets must be compatible for welding, typically meaning they are of the same material or highly compatible co-polymers.
② Materials must possess good melt strength and sag resistance to withstand heating without excessive thinning or tearing before forming.
③ Common materials include High-Density Polyethylene (HDPE), Polypropylene (PP), Acrylonitrile Butadiene Styrene (ABS), High Impact Polystyrene (HIPS), Polycarbonate (PC), and Thermoplastic Olefins (TPO).
2. Independent Sheet Control:
① Modern twin sheet forming machines often allow for independent temperature control for each sheet. This is crucial if using sheets of different thicknesses, colors, or even slightly different material formulations (though challenging).
② This control ensures both sheets reach their ideal forming temperatures simultaneously.
3. Pressure and Vacuum Application:
① Vacuum is typically used to draw the heated sheets into the mold cavities, ensuring good definition.
② Air pressure may be applied between the sheets (pre-blow) or behind the sheets (pressure forming) to assist in material distribution and achieve sharper detail.
③ The final compression (pressing) stage is critical for achieving a strong weld.
4. Tooling Design and Engineering:
① Tooling must be robust to withstand forming and pressing forces.
② Precise alignment mechanisms are essential to ensure the two halves meet correctly.
③ Venting is crucial to evacuate air trapped between the sheet and the mold.
④ Cooling channels within the molds help solidify the part and reduce cycle times.
⑤ Shut-off or pinch-off areas in the tooling define the weld lines and must be designed for optimal material flow and fusion.
5. Cycle Time Optimization:
① The overall cycle time includes sheet loading, heating, forming, pressing/welding, cooling, and part ejection.
② Efficient heating and cooling are key to minimizing cycle times.
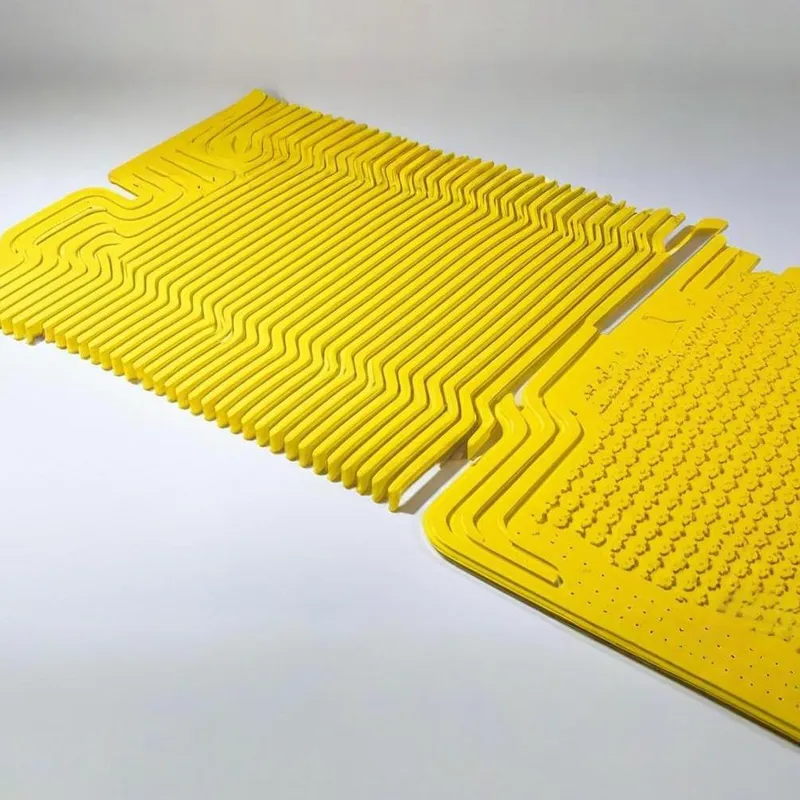
Classifications and Types of Twin Sheet Forming Processes
Twin sheet forming can be classified based on several factors, offering different capabilities:
1. Based on Machine Configuration:
① Shuttle Machines: Sheets are loaded, heated in an oven station, and then "shuttled" to a forming station. Suitable for medium-volume production and larger parts.
② Rotary Machines (Carousel): Feature multiple stations (e.g., loading, heating, forming, cooling/unloading) arranged in a circular carousel. As the carousel rotates, sheets progress through each stage. Ideal for higher volume production and improved efficiency.
③ In-line Machines: Sheets are fed from rolls or pre-cut stacks, moving linearly through heating, forming, and trimming stages. Suited for very high-volume production of smaller parts.
2. Based on Forming Pressure:
① Vacuum Twin Sheet Forming: Relies primarily on vacuum to draw sheets into molds. Simpler, but may have limitations on detail and draw depth.
② Pressure Twin Sheet Forming: Uses air pressure in addition to or instead of vacuum to force the sheets against the molds. Allows for sharper details, textured surfaces, and forming of more complex shapes.
③ Matched Tool Twin Sheet Forming: While all twin sheet forming involves matched tools for pressing, this can refer to processes where both mold halves contribute significantly to shaping complex internal and external features through precise cavity/core interactions during the forming stage itself, not just the pressing/welding.
3. Based on Part Complexity and Features:
① Basic Hollow Parts: Simple sealed structures like tanks or floats.
② Parts with Internal Reinforcement: By designing specific internal contact points, ribs or reinforcing structures can be formed within the hollow cavity.
③ Parts with Encapsulated Components: Items like foam for insulation, metal reinforcements, or mounting hardware can be placed between the sheets before they are welded together.
④ Multi-Material Parts (Challenging): While typically using the same material, it's theoretically possible to form parts with different materials for each sheet if they are weld-compatible. This is complex and less common.
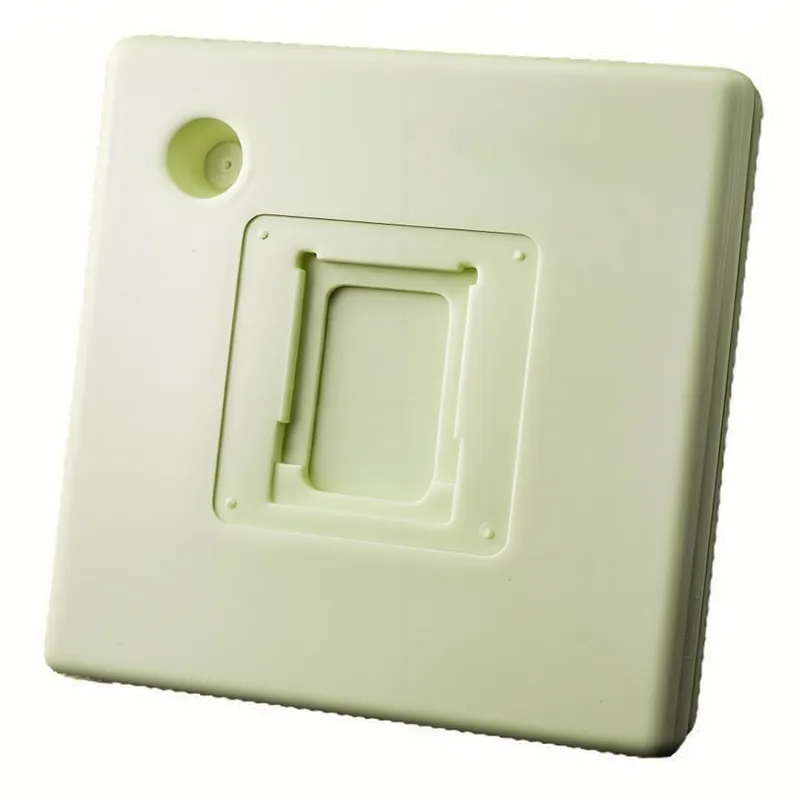
Diverse Applications: Where is Twin Sheet Forming Used?
The versatility of twin sheet forming allows it to serve numerous industries:
① Automotive: Air ducts, plenums, fluid reservoirs (coolant, washer fluid), interior trim components, load floors, seat backs, underbody shields, truck bed liners.
② Industrial & Material Handling: Pallets, shipping containers, dunnage trays, machinery housings, equipment enclosures, chemical tanks, chutes, hoppers.
③ Medical: Medical equipment enclosures, trays, housings for diagnostic machines, mobility aid components.
④ Recreational & Consumer Goods: Kayak hulls, cooler lids, vehicle cargo carriers, playground equipment, furniture components (e.g., chair shells), sleds.
⑤ Building & Construction: Concrete forms, ventilation components, drainage products, portable sanitation units.
⑥ Aerospace: Ducting, interior components, cargo containers (where lightweight and strength are critical).
Twin Sheet Forming in Action (Manufacturing Focus)
1. Automotive Air Ducts:
HVAC ducts in vehicles are often complex, hollow shapes designed to route air efficiently. Twin sheet forming allows for smooth internal surfaces for airflow and the integration of mounting points, all in a lightweight component. This is often more cost-effective than blow molding for moderate volumes.
2. Heavy-Duty Pallets:
Plastic pallets manufactured via twin sheet forming can be designed with internal reinforcing ribs, making them exceptionally strong, durable, and resistant to impact and chemicals. They offer a hygienic and long-lasting alternative to wooden pallets.
3. Industrial Equipment Enclosures:
Housings for pumps, generators, or electronic systems benefit from the robust, double-walled construction. Twin sheet forming can create aesthetically pleasing, impact-resistant enclosures with molded-in features like handles or vents. Tooling costs are significantly lower than injection molding for such large parts.
4. Kayak Hulls:
Many modern kayaks utilize twin sheet formed HDPE. This process creates a buoyant, impact-resistant hull that is seamless (except for the central weld line, which is very strong). The ability to have different colors on the deck and hull (if sheets are loaded accordingly before forming) is also an advantage.
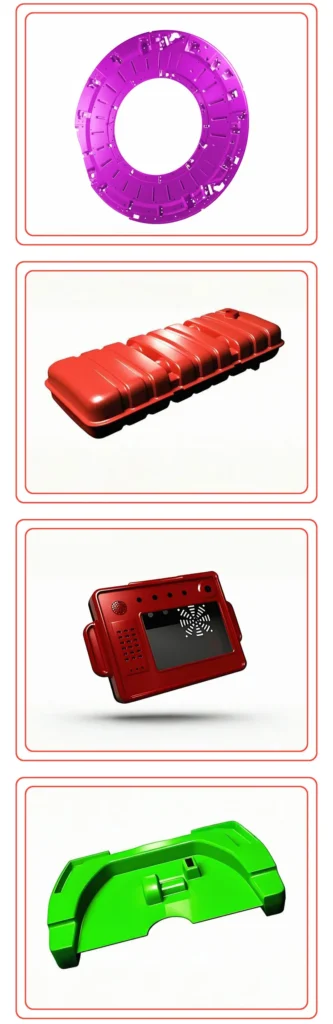
Twin Sheet Forming vs. Alternative Processes: A Comparative Overview
Feature | Twin Sheet Forming | Single Sheet Thermoforming | Blow Molding | Rotational Molding | Injection Molding |
---|---|---|---|---|---|
Hollow Parts | Yes (primary strength) | No (open-faced parts) | Yes (excellent for hollow) | Yes (excellent for hollow) | Possible (gas-assist, etc.), but complex |
Tooling Cost | Moderate | Low | Moderate to High | Low to Moderate | Very High |
Piece Part Cost | Moderate | Low | Moderate (can be low at high vol.) | Moderate to High (long cycles) | Low (at very high vol.) |
Cycle Time | Moderate | Fast | Fast (for extrusion blow) | Very Slow | Very Fast |
Strength | Good to Excellent | Fair to Good | Good to Excellent | Excellent (uniform walls) | Excellent |
Design Detail | Good | Fair to Good | Fair (external only well-defined) | Fair (less sharp detail) | Excellent |
Wall Thickness | Variable, some control | Variable (thinning on draw) | Variable (can be controlled somewhat) | Very Uniform | Excellent Control |
Materials | Thermoplastics | Thermoplastics | Thermoplastics (esp. PE, PP, PET) | Thermoplastics (esp. PE), some thermosets | Wide range of Thermoplastics, Thermosets |
Ideal Volume | Low to Medium (hundreds to thousands) | Low to High | Medium to Very High | Low to Medium | Very High (tens of thousands to millions) |
Part Size | Small to Very Large | Small to Large | Small to Large | Small to Very Large | Small to Large (very large is expensive) |
Note on Silicone Products: Twin sheet forming is not typically used for silicone products. Silicones are thermosetting elastomers (or liquid silicone rubber – LSR), requiring different processing methods like compression molding, transfer molding, or liquid injection molding. The “thermoforming” aspect is specific to thermoplastics that soften upon heating and reharden.
Custom High-Strength Hollow Plastic Part Solutions
Discover how twin sheet forming brings innovation to your products. We offer high-strength, lightweight, flexibly designed hollow plastic parts for automotive, medical, industrial equipment, and more.
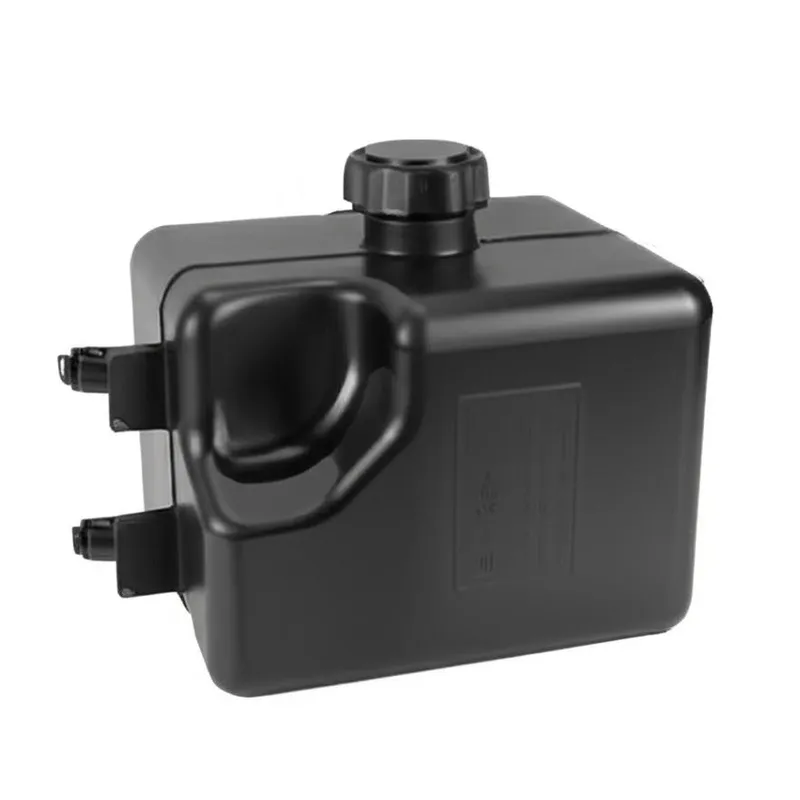
Resources for The Complete Guide to Twin Sheet Forming
- Weighing the Options: Advantages of Twin Sheet Forming
- Understanding Limitations: Disadvantages of Twin Sheet Forming
- Key Characteristics and Material Properties in Twin Sheet Forming
- The Twin Sheet Forming Process: A Step-by-Step Breakdown
- Critical Parameters and Influencing Factors in Twin Sheet Forming
- Essential Design Considerations for Successful Twin Sheet Forming
Weighing the Options: Advantages of Twin Sheet Forming
Twin sheet forming offers several compelling advantages over other plastic manufacturing processes:
1. Hollow, Double-Walled Structures: The primary advantage, allowing for lightweight yet strong parts.
2. High Strength-to-Weight Ratio: Ideal for applications requiring structural integrity without excessive mass.
3. Lower Tooling Costs (Compared to Injection/Blow Molding): Tooling is typically made from aluminum, which is less expensive and faster to produce than the steel molds required for injection molding or most blow molding, especially for large parts. This makes it economical for low to medium production volumes.
4. Design Flexibility:
- Ability to form complex geometries and varying wall thicknesses in different areas.
- Different colors or materials can be used for each sheet (if compatible).
- Different textures can be applied to each side of the part.
- Internal features like ribs and bosses can be integrated.
5. Encapsulation Capability: Reinforcements (metal, wood), insulation (foam), or other components can be placed between the sheets before welding.
6. Seamless Appearance (Largely): Parts have a clean appearance with a single, well-controlled weld line.
7. Good Impact Resistance: The double-wall structure can absorb impact energy effectively.
8. Large Part Capability: The process is well-suited for producing very large parts that would be prohibitively expensive or technically challenging with injection molding.
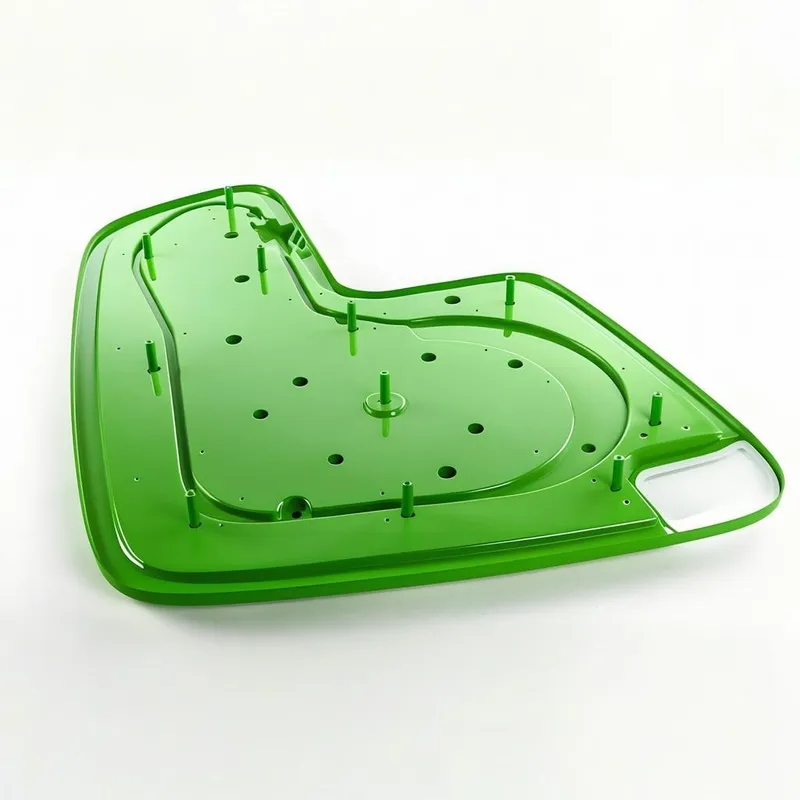
Understanding Limitations: Disadvantages of Twin Sheet Forming
Despite its benefits, twin sheet forming also has limitations:
① Higher Piece Part Cost (Compared to Single Sheet Thermoforming): Uses twice the material and involves a more complex process.
② Slower Cycle Times (Compared to Injection Molding): Heating, forming two sheets, pressing, and cooling take longer, making it less suitable for extremely high-volume production runs where injection molding excels.
③ Material Limitations: Primarily restricted to thermoplastics. Some materials may not have sufficient melt strength for deep draws or complex geometries.
④ Design Constraints:
- Sharp internal corners can be difficult to achieve without thinning.
- Maintaining perfectly uniform wall thickness throughout complex geometries is challenging.
- The weld flange (pinch-off) is a necessary feature and must be accommodated in the design (and often trimmed).
⑤ Weld Integrity is Critical: The strength of the part relies heavily on the quality of the weld between the two sheets. Process control is crucial.
⑥ Secondary Operations Often Required: Trimming of the weld flange is almost always necessary. Other operations like drilling or assembly may also be needed.
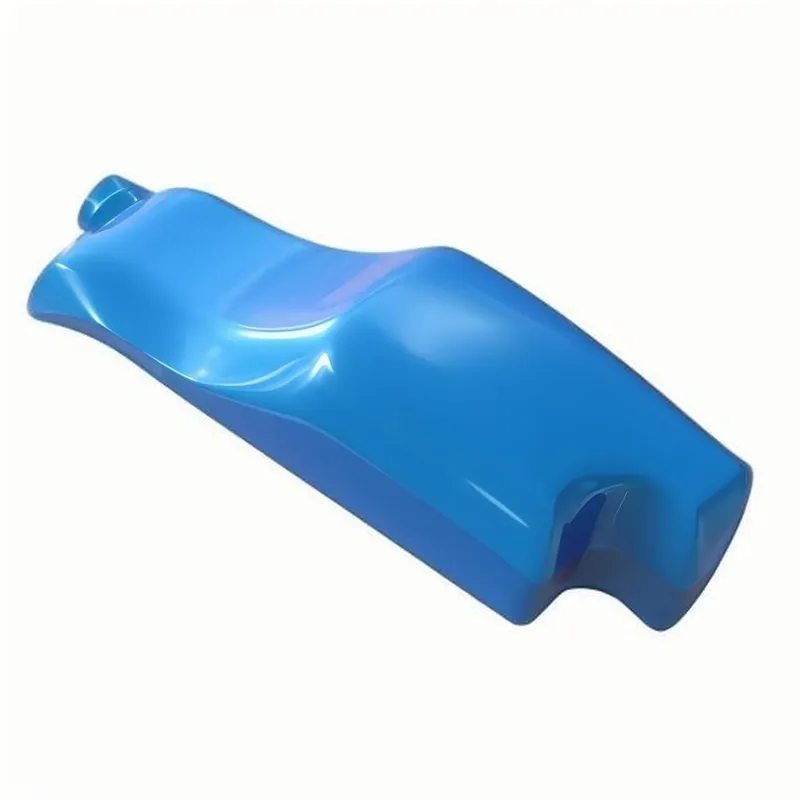
Key Characteristics and Material Properties in Twin Sheet Forming
The success of a twin sheet formed part is intrinsically linked to the properties of the chosen material and the characteristics imparted by the process itself.
1. Key Part Characteristics Achieved:
① Structural Rigidity: The I-beam effect created by the two walls and the enclosed air space provides excellent stiffness.
② Watertight/Airtight Seals: Properly executed welds create hermetically sealed components, essential for tanks and containers.
③ Thermal and Acoustic Insulation: The air gap between the sheets provides natural insulation. This can be enhanced by encapsulating foam.
④ Aesthetic Options: Ability to use pre-colored sheets, apply different textures to each mold half, or even use sheets with different finishes (e.g., high gloss on one side, matte on the other).
⑤ Internal Features: Complex internal ribbing or kiss-off points (where the two sheets touch and weld internally) can be designed to enhance strength or create separate compartments.
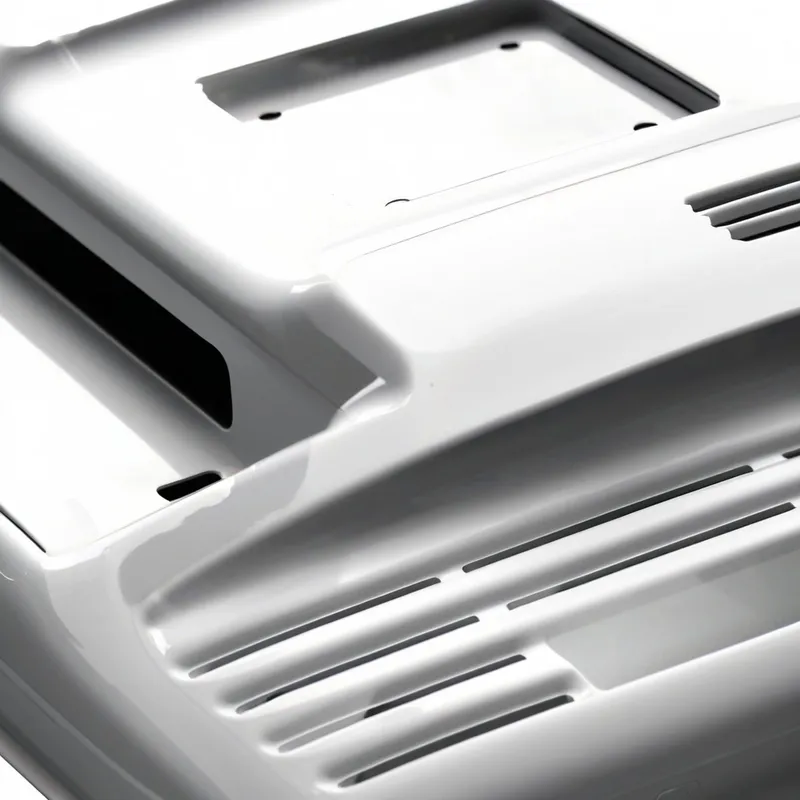
2. Critical Material Properties for Twin Sheet Forming:
① Melt Strength: The ability of the heated plastic sheet to resist sagging or tearing under its own weight before and during forming. Crucial for large parts or deep draws.
② Drawability/Formability: The extent to which a material can be stretched and shaped without excessive thinning, tearing, or other defects.
③ Impact Strength: Especially important for materials like HDPE, TPO, and PC used in applications requiring durability (e.g., pallets, automotive components).
④ Weldability: The material must readily fuse to itself under heat and pressure to create a strong, permanent bond.
⑤ Thermal Stability: Resistance to degradation at forming temperatures.
⑥ Sag Resistance: Critical during the heating phase to prevent the sheet from drooping excessively and touching heating elements or becoming too thin.
⑦ Coefficient of Thermal Expansion: Influences shrinkage and potential warpage as the part cools. Consistent material properties are key.
⑧ Chemical Resistance: Important for tanks, containers, or parts exposed to various fluids or environments.
⑨ UV Stability: For outdoor applications, materials often require UV inhibitors to prevent degradation.
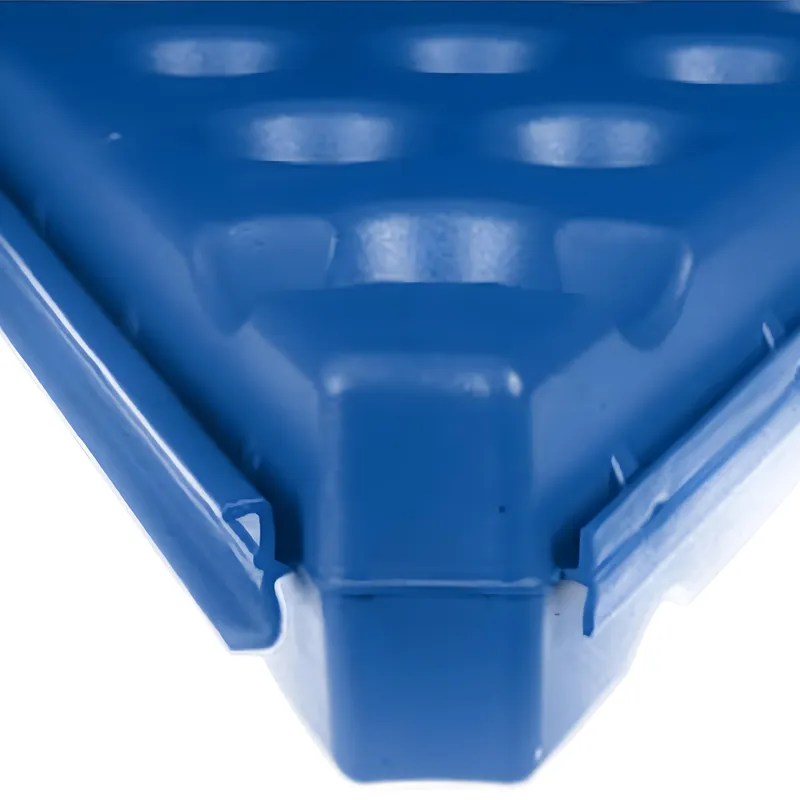
The Twin Sheet Forming Process: A Step-by-Step Breakdown
Understanding the sequential steps of the twin sheet forming process is vital for appreciating its complexities and control points:
1. Sheet Loading:
- Two separate thermoplastic sheets are clamped into individual frames or carriers. Sheets can be pre-cut or fed from rolls for smaller parts.
- Proper clamping is essential to prevent slippage and ensure even tension during heating and forming.
2. Heating:
- Both sheets are transported to an oven station (or heated in place on some machines).
- Heating is typically done using radiant heaters (e.g., ceramic, quartz, or halogen).
- Precise temperature control is critical. Sheets must reach their specific, uniform forming temperature. Overheating can cause degradation or excessive sag; underheating results in poor forming and weak welds.
- Often, non-contact infrared (IR) pyrometers monitor sheet temperature. Zone heating may be employed to selectively heat areas of the sheet more or less, aiding material distribution.
3. (Optional) Pre-Stretching / Pre-Blow:
- To improve material distribution for deep or complex parts, a slight air pressure (pre-blow) might be introduced between the sheet and the mold to dome the sheet upwards, or a plug assist (mechanical plunger) might be used to pre-stretch the material into deeper cavities. This helps prevent excessive thinning in critical areas.
4. Forming:
- The heated, pliable sheets are transferred over their respective molds (male, female, or a combination).
- Vacuum is applied through small holes in the molds, drawing the sheets down to conform to the mold contours.
- Simultaneously or alternatively, air pressure can be applied to the non-mold side of the sheets to force them tightly against the mold surfaces, achieving better detail (pressure forming).
5. Pressing and Welding (Fusion):
- While the formed sheets are still hot and held in their respective molds by vacuum/pressure, the two mold halves (platens) are brought together under high force.
- The edges of the two sheets (and any internal contact points designed into the molds) are pressed together. The combination of residual heat and pressure causes the thermoplastic material to fuse, creating a permanent weld.
- The design of the “pinch-off” or “shut-off” area on the molds is critical here. It must allow material to flow and weld effectively while also cleanly severing excess material or creating a defined flange.
6. Cooling:
- The newly formed and welded part is held in the closed molds under pressure while it cools and solidifies.
- Cooling is often accelerated by circulating water through channels within the aluminum molds.
- Sufficient and uniform cooling is essential to maintain dimensional stability and prevent warpage. The cooling time is a significant portion of the overall cycle.
7. Demolding / Part Removal:
- Once the part has cooled sufficiently and solidified, the molds open.
- Air ejectors or mechanical knockouts may assist in releasing the part from the molds.
- Robots or operators remove the finished part.
8. Trimming and Finishing:
- Excess material around the weld flange (flash or pinch-off trim) must be removed. This is typically done using CNC routers, die cutting, or manual methods.
- Additional secondary operations like drilling holes, installing inserts (if not encapsulated), or assembly may follow.
Critical Parameters and Influencing Factors in Twin Sheet Forming
Numerous parameters can influence the quality and consistency of twin sheet formed parts:
1. Sheet Temperature: The most critical parameter. Must be uniform across each sheet and optimal for the specific material.
2. Heating Time: Directly related to sheet temperature; too short leads to underheating, too long to overheating/sagging.
3. Mold Temperature: Affects cooling rate, surface finish, and potential for warpage. Consistent mold temperature is key.
4. Vacuum Level and Timing: Insufficient vacuum results in poor definition; applied too late or too early can cause issues.
5. Air Pressure (if used): Level and timing for pressure forming or pre-blow.
6. Pressing Force (Tonnage): Sufficient force is needed for a strong weld without crushing the part.
7. Pressing/Weld Time: Duration the sheets are held under pressure at welding temperature.
8. Cooling Time: Must be adequate for the part to solidify and maintain its shape upon demolding.
9. Material Properties: Melt flow index, melt strength, sag resistance, thickness tolerance of the raw sheets.
10. Tooling Design: Venting, pinch-off design, cooling channel layout, alignment accuracy.
11. Ambient Conditions: Extreme changes in temperature or humidity in the plant can affect material behavior and heating.
Essential Design Considerations for Successful Twin Sheet Forming
Designing parts specifically for the twin sheet forming process is crucial for manufacturability, performance, and cost-effectiveness:
1. Draft Angles:
Generous draft angles (typically 3-5 degrees or more per side) are essential on all vertical walls to facilitate part release from the molds.
2. Radii and Fillets:
Avoid sharp corners. Use generous radii on all internal and external corners to prevent material thinning, stress concentrations, and cracking.
3. Wall Thickness Variation:
Understand that wall thickness will vary. Areas stretched more will be thinner. Design to ensure minimum critical wall thicknesses are met. Consider ribbing or kiss-offs for strength if thinning is a concern.
4. Weld Flange / Pinch-Off Design:
- Allow space for the weld flange.
- The design of the pinch-off area in the tool determines the quality of the weld and ease of trimming.
- Ensure sufficient material for a robust weld.
5. Draw Ratio:
The ratio of the depth of the draw to the opening. Deeper draws lead to more thinning. Keep draw ratios reasonable for the chosen material. (e.g., a 1:1 draw ratio means the depth is equal to the width/length). Higher draw ratios (e.g., 3:1 or 4:1) become increasingly challenging.
6. Internal "Kiss-Off" Features:
These are points or ribs where the two sheets touch and weld internally. They significantly increase rigidity and strength. Design their placement and size carefully.
7. Undercuts:
Possible with collapsible cores, cams, or other moving tool components, but they add complexity and cost to tooling.
8. Surface Finish and Texture:
Textures can be applied to the mold surfaces to impart them onto the plastic part. This can hide minor imperfections and improve aesthetics.
9. Tolerances:
Twin sheet forming typically has looser tolerances than injection molding. Design with this in mind. Typical tolerances might be ±0.5mm to ±1.5mm or more, depending on part size and complexity.
10. Material Selection:
Choose materials based on end-use requirements (strength, chemical resistance, temperature exposure, UV stability) and their suitability for twin sheet forming (melt strength, drawability).
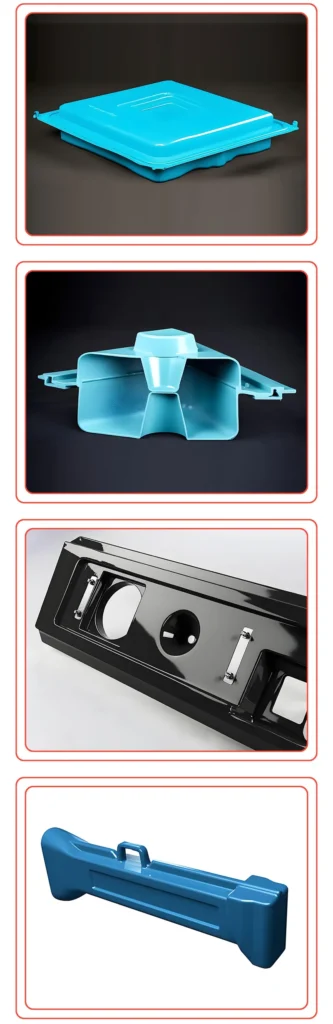
Unlocking Design & Cost-Effectiveness for Complex Hollow Structures
Explore the possibilities of twin sheet thermoforming. By simultaneously forming and fusing two plastic sheets, we create parts with complex internal structures, double walls, and high integration, while optimizing production costs.
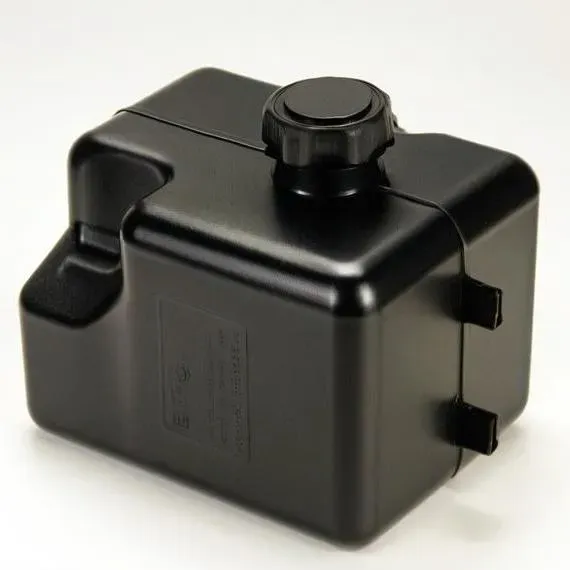
Resources for The Complete Guide to Twin Sheet Forming
- Design for Manufacturability: Best Practices for Twin Sheet Forming
- Troubleshooting Common Issues in Twin Sheet Forming
- Quality Control and Inspection in Twin Sheet Formed Parts
- Decision Aid: Is Twin Sheet Forming Right for Your Project?
- Related Manufacturing Technologies and Concepts
- Future Trends and Innovations in Twin Sheet Forming
Design for Manufacturability: Best Practices for Twin Sheet Forming
Adhering to Design for Manufacturability (DFM) principles is key to producing high-quality, cost-effective twin sheet parts:
1. Simplify Geometry Where Possible:
Complex shapes increase tooling cost and processing challenges.
2. Maintain Uniform Nominal Wall Thickness:
While variations are inevitable, start with a consistent nominal sheet thickness and design features that minimize excessive localized thinning.
3. Maximize Radii:
Generous radii (minimum 3x material thickness, ideally more) improve material flow, reduce stress, and prevent tearing.
4. Incorporate Adequate Draft:
At least 3° per side is a good starting point; more is better, especially for textured surfaces or deep draws.
5. Clearly Define Weld Locations:
Ensure weld lines are in areas that can tolerate the pinch-off and provide structural integrity. Avoid critical functional features too close to weld lines.
6. Design Effective Kiss-Offs:
- Ensure sufficient surface area for a strong internal weld.
- Avoid kiss-offs that create trapped air pockets.
- Consider their impact on material flow from both sheets.
7. Account for Shrinkage:
All plastics shrink upon cooling. Factor in material-specific shrinkage rates when designing tooling.
8. Consider Trimming Requirements:
Design parts so that trimming is straightforward and doesn't compromise part integrity. Ensure easy access for trimming tools.
9. Plan for Encapsulation Early:
If inserts or other components are to be encapsulated, design features in the molds to locate and hold them accurately during forming.
10. Specify Tolerances Realistically:
Understand the process capability and don't over-specify tolerances, as this increases costs.
11. Communicate with the Manufacturer:
Early collaboration between the designer and the twin sheet forming specialist is crucial to optimize the design for the process.
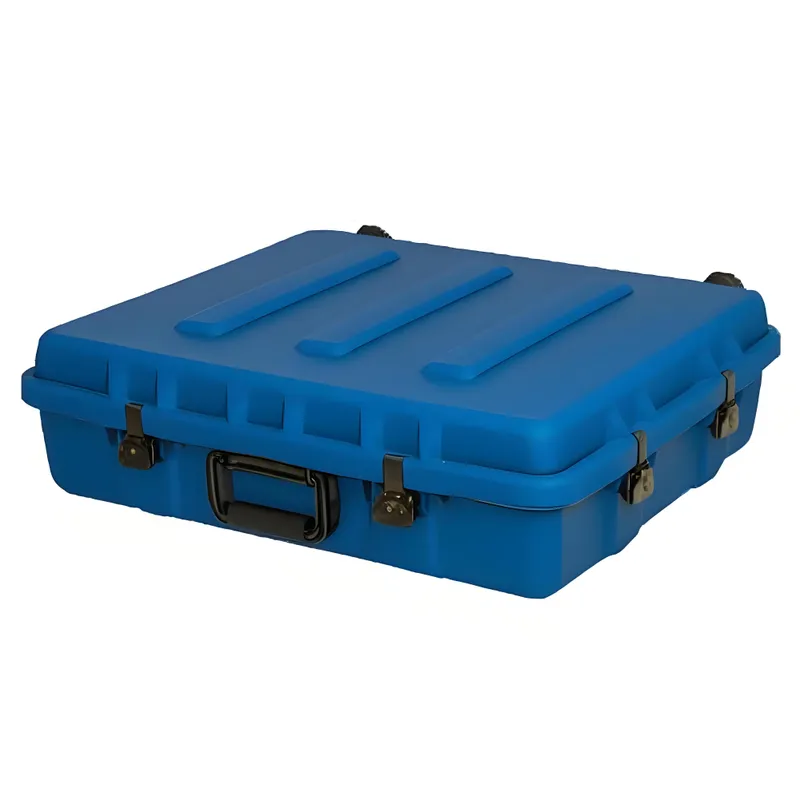
Troubleshooting Common Issues in Twin Sheet Forming
Problem | Potential Causes | Solutions |
---|---|---|
Poor Weld / Delamination | Insufficient sheet temperature, insufficient press tonnage, incorrect weld time, contaminated sheet surfaces, incompatible materials, poor pinch-off design. | Increase sheet/mold temperature, increase press tonnage, optimize weld time, clean sheets, verify material compatibility, redesign pinch-off. |
Excessive Thinning / Holes | Overheating, sharp corners in mold, excessive draw ratio, insufficient material thickness, poor pre-stretching. | Reduce sheet temperature, increase radii, reduce draw depth, use thicker sheet material, optimize pre-blow or plug assist. |
Webbing / Bridging | Insufficient vacuum, trapped air, premature cooling of material before full forming, sheet too cool. | Increase vacuum, improve mold venting, ensure sheet is at optimal forming temperature, optimize heating cycle. |
Warpage / Distortion | Uneven cooling, insufficient cooling time, internal stresses, poor part design (e.g., large flat areas without support). | Optimize mold cooling (uniformity and rate), increase cooling time, anneal parts (if applicable), add ribs or kiss-offs to improve stiffness, adjust sheet temperature. |
Surface Blemishes / Chill Marks | Mold too cold, sheet too cold, moisture in material, contamination on mold or sheet. | Increase mold/sheet temperature, pre-dry hygroscopic materials, clean molds and sheets thoroughly. |
Inconsistent Part Quality | Fluctuations in sheet temperature, material inconsistencies, variations in cycle timing, worn tooling. | Implement tighter process controls, verify material quality, automate cycles where possible, inspect and maintain tooling regularly. |
Difficulty in Demolding | Insufficient draft angles, undercuts without proper tooling, part sticking due to over-packing or too hot mold. | Increase draft angles, redesign for undercuts or use appropriate tooling, optimize cooling, apply mold release if necessary (though generally avoided). |
Quality Control and Inspection in Twin Sheet Formed Parts
Maintaining high quality requires a systematic approach to inspection:
1. Raw Material Inspection:
Verify sheet thickness, color, material type, and absence of contaminants or damage.
2. First-Off Inspection:
Thoroughly inspect the first part produced after setup or any process change. Check all critical dimensions, weld integrity, wall thickness, and cosmetic appearance.
3. In-Process Checks:
Regularly monitor:
- Sheet temperatures (using pyrometers).
- Cycle times (heating, forming, cooling).
- Vacuum and pressure levels.
- Visual inspection of parts for defects (short shots, webbing, warpage, surface blemishes).
- Weld integrity (e.g., destructive testing of sample parts by cutting open welds, or non-destructive methods if applicable).
4. Dimensional Checks:
Use calipers, gauges, CMM (Coordinate Measuring Machine) for critical dimensions on a sampling basis.
5. Functional Testing:
If applicable, test parts for their intended function (e.g., leak testing for tanks, load testing for pallets).
6. Cosmetic Inspection:
Check for color consistency, surface finish, and absence of scratches or marks.
7. Documentation:
Maintain records of process parameters, inspection results, and any corrective actions taken.
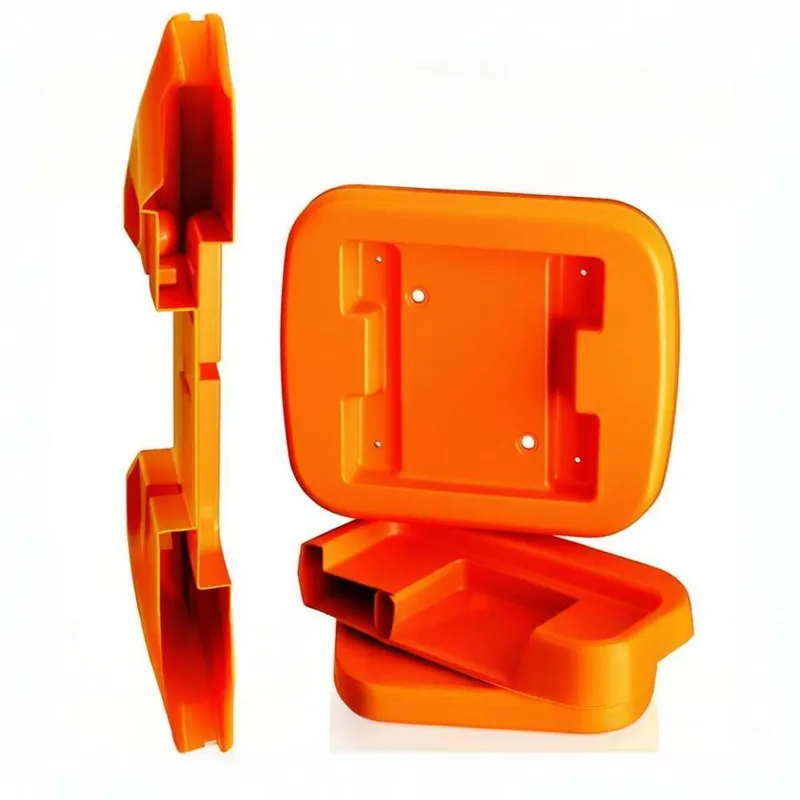
Decision Aid: Is Twin Sheet Forming Right for Your Project?
Consider these questions to help decide if twin sheet forming is a suitable process:
1. Is a hollow or double-walled structure essential or highly beneficial for the part’s function (e.g., strength, buoyancy, insulation, ducting)? (YES points to twin sheet)
2. What is the anticipated annual production volume? (Hundreds to tens of thousands often fits. Very low might be prototypes/other methods; very high might favor injection/blow molding).
3. What is the part size? (Twin sheet excels at medium to very large parts where injection mold tooling would be excessively expensive).
4. Are tooling costs a significant constraint? (Twin sheet tooling is generally less than injection/blow molding).
5. Are there requirements for different colors or materials on opposite sides of the part? (Possible with twin sheet, though can be complex).
6. Is there a need to encapsulate other components (e.g., foam, metal reinforcements) within the part? (A key strength of twin sheet).
7. What are the structural requirements? (Twin sheet offers good strength-to-weight).
8. Are the tolerances very tight (e.g., sub-millimeter)? (Injection molding might be better; twin sheet has wider tolerances).
9. Does the part have extremely complex external and internal details that need high precision? (Injection molding may offer higher fidelity for very intricate details).
10. What is the primary material requirement? (Must be a formable thermoplastic).
If many answers lean towards the advantages offered by twin sheet forming, it’s a strong candidate for further investigation.
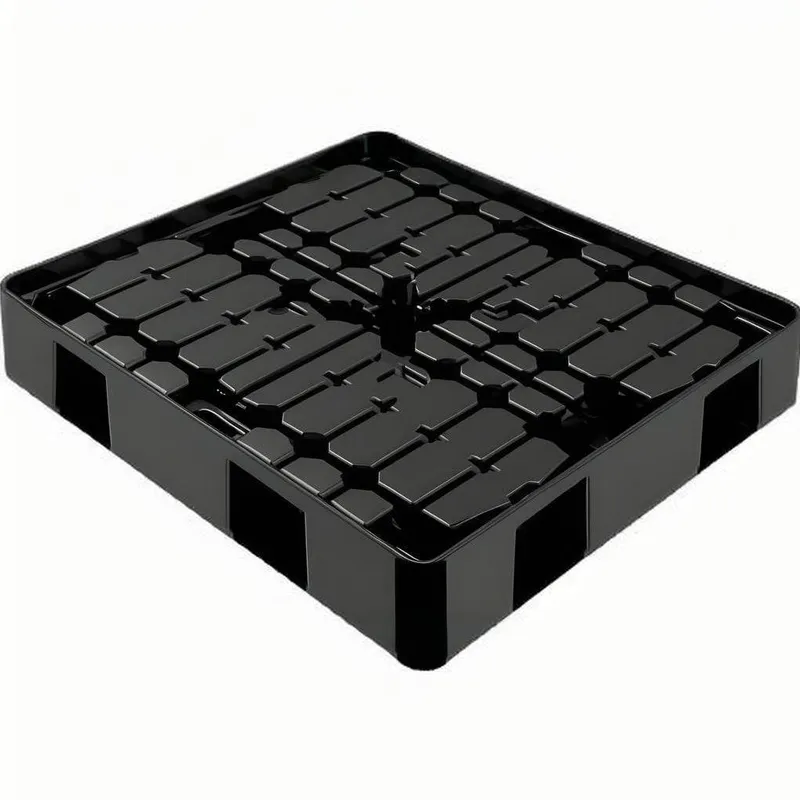
The Broader Context: Related Manufacturing Technologies and Concepts
1. Single Sheet Thermoforming (Vacuum Forming, Pressure Forming, Drape Forming):
Upstream/Simpler: Twin sheet forming is an evolution of these processes. Single sheet forming creates open-faced parts from one sheet of plastic. It's simpler and generally has lower tooling/part costs but cannot create enclosed hollow structures in one step.
2. Blow Molding (Extrusion Blow Molding, Injection Blow Molding, Stretch Blow Molding):
Alternative for Hollow Parts: Blow molding is excellent for high-volume production of hollow parts like bottles and tanks. It typically involves extruding a parison (tube of molten plastic) or injection molding a preform, then inflating it within a mold. Tooling can be more expensive than twin sheet for comparable part sizes, but piece part costs can be lower at very high volumes.
3. Rotational Molding (Rotomolding):
Alternative for Large, Complex Hollow Parts: Plastic powder is loaded into a mold, which is then heated and rotated on multiple axes. The powder melts and coats the inside of the mold. Produces stress-free parts with uniform wall thickness, ideal for very large tanks and complex hollow shapes. Cycle times are long, and piece part costs can be higher, but tooling is relatively inexpensive.
4. Injection Molding:
High-Volume, Precision Alternative: Molten plastic is injected under high pressure into a steel mold. Excellent for complex, high-precision parts in very high volumes. Tooling is very expensive. Can create hollow parts via gas-assist or by molding two halves and then assembling/welding them, which adds steps and cost compared to integral twin sheet forming.
5. Structural Foam Molding:
Alternative for Rigid, Lightweight Parts: A type of injection molding where a foaming agent is introduced, creating a cellular core and solid skin. Results in lightweight, stiff parts. Not inherently hollow in the same way as twin sheet.
6. Plastic Extrusion:
Upstream Process: Produces continuous profiles, sheets, tubes, and films. The plastic sheets used in twin sheet forming are themselves products of an extrusion process.
7. Joining and Assembly Processes:
Downstream/Alternative: If twin sheet isn't used, two separately formed or molded parts might be joined using ultrasonic welding, hot plate welding, adhesives, or mechanical fasteners to create a hollow assembly. Twin sheet integrates this joining step into the forming process.
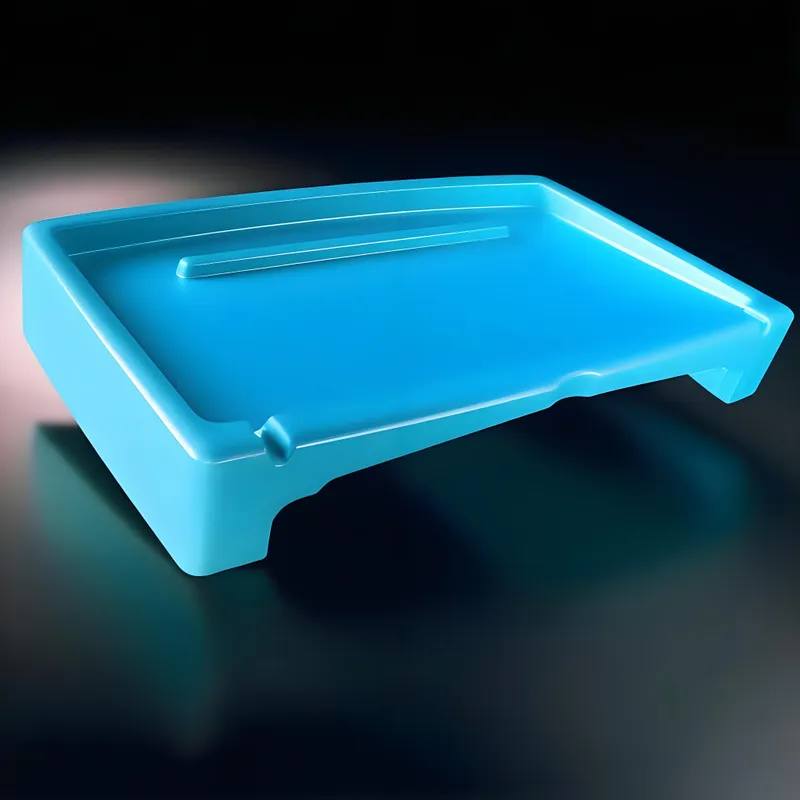
Future Trends and Innovations in Twin Sheet Forming
The twin sheet forming industry continues to evolve, driven by demands for higher efficiency, better quality, and expanded capabilities:
1. Advanced Material Formulations:
Development of thermoplastics with enhanced melt strength, better drawability, and specific properties (e.g., higher heat resistance, improved impact strength, sustainable/recycled content) suitable for demanding twin sheet applications.
2. Improved Machine Control and Automation:
- More sophisticated PLC controls for precise management of heating, pressure, vacuum, and timing.
- Increased use of robotics for sheet loading, part removal, and secondary operations like trimming.
- Real-time process monitoring and data logging for quality assurance and predictive maintenance.
3. Enhanced Heating Technologies:
More efficient and precise heating systems, such as advanced IR heaters with finer zone control, to optimize sheet temperature uniformity and reduce energy consumption.
4. Simulation Software:
Wider adoption of CAE (Computer-Aided Engineering) tools to simulate the twin sheet forming process. This helps predict material behavior, identify potential thinning or webbing issues, and optimize tool design before physical tooling is made, reducing development time and cost.
5. Larger and More Complex Parts:
Push towards machinery capable of handling even larger sheets and forming more intricate geometries, including those with complex internal structures.
6. Integration of In-Mold Labeling/Decoration (IML/IMD):
While more common in injection molding, there's interest in adapting similar technologies for thermoforming to create decorated parts directly in the mold.
7. Sustainable Practices:
Increased focus on using recycled and recyclable materials, reducing energy consumption per part, and minimizing scrap.
8. Hybrid Processes:
Exploration of combining twin sheet forming with other technologies to achieve unique part characteristics or efficiencies.
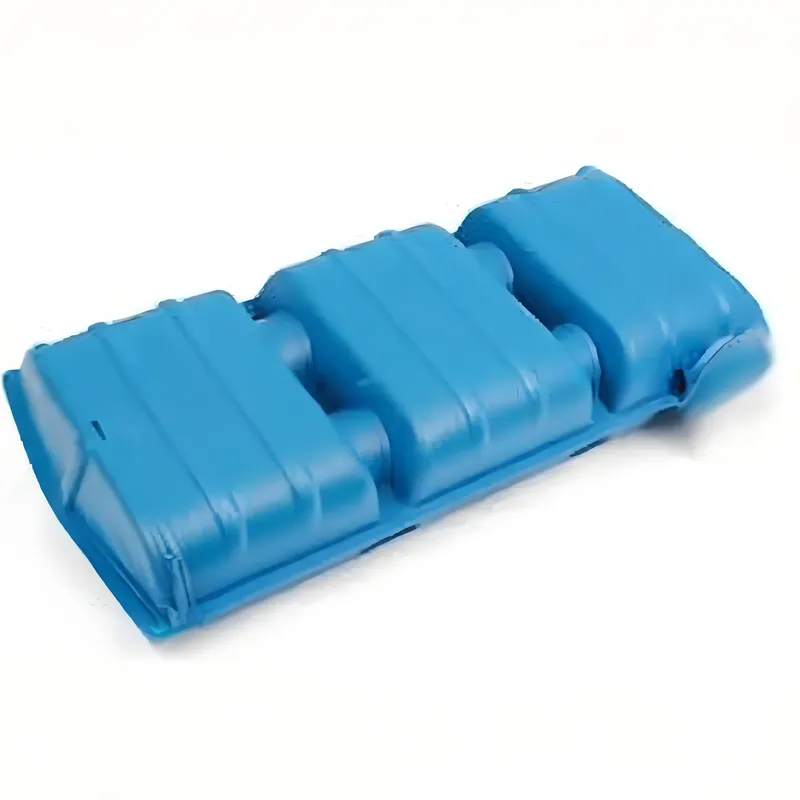
FAQs FOR CLIENT
Getting Started with Uplastech
Have questions? We have answers.
We specialize in extrusion, vacuum forming, blow molding, and precision mold-making, offering customized solutions to meet your diverse manufacturing needs.
We work with various industries, including automotive, electronics, consumer goods, and packaging, focusing on B2B partnerships and delivering solutions across extrusion, thermoforming, blow molding, and precision mold-making.
Yes, we tailor our solutions to fit your unique requirements.
Get In Touch
Feel free to email us or fill out the form below to get a quote.
Email: uplastech@gmail.com